Formação de andaime no poço do alto-forno
Formação de andaime no poço do alto-forno
O termo scaffold é utilizado quando há acreção ou formação de crosta na parede do alto-forno (BF) que provoca uma diminuição da área da seção transversal do fuste do BF. O andaime pode ocorrer relativamente no nível mais alto do eixo BF ou relativamente baixo no eixo BF (perto do topo do bosh). É difícil generalizar os tipos de andaimes, pois há muito pouco em comum entre a estrutura e a localização dos andaimes de diferentes BFs. No entanto, os andaimes podem ser geralmente organizados em dois grupos. Esses grupos são (i) andaimes laminados e (ii) andaimes não laminados. Andaimes com estrutura laminada consistem em camada alternada de ferro metálico (Fe) e carga rica em álcalis. A formação típica de um grande andaime em um BF é mostrada na Fig 1.
Fig 1 Formação típica de um grande andaime em um BF
Andaimes podem causar enforcamento no BF. A suspensão se origina quando a carga, ao descer, encontra uma resistência muito alta, resultando na paralisação do movimento da carga. A suspensão pode se romper e, em seguida, o material cai por causa da lacuna que foi criada abaixo da suspensão. Após a ruptura, quando ocorre o deslizamento, normalmente grande quantidade de materiais cai e resulta em funcionamento irregular do BF resultando em uma distribuição não uniforme do gás com suas implicações nos parâmetros do BF.
Os pré-requisitos para a formação de scaffolds estáveis e prejudiciais são (i) presença de material adequado na carga de BF para construir o scaffold (por exemplo, finos, carga mal peneirada, sinter com características de degradação de redução de baixa temperatura inferiores, uso de sinterização por muito tempo armazenada, úmida e fria , ou coque de pequeno porte etc.), (ii) presença de material aglomerante (cimentante) para a aglomeração do material de carga, (iii) presença de mecanismo de fixação (ancoragem) para construir o andaime na parede do eixo do BF que pode ser uma ligação química com o material de revestimento, ancoragem física ao redor das placas de resfriamento, construção de arco em direção às paredes do bosh ou simplesmente condensação do material aglomerante na parede, (iv) fornecimento contínuo dos componentes aderentes e (v) ) o andaime formado é forte o suficiente para suportar as forças de desgaste dos materiais descendentes.
O local onde o andaime está localizado depende do material aglomerante, material aderente, materiais de carga, operação do forno e características de construção do forno, como elementos de resfriamento e material de revestimento. Ele pode estar localizado em vários níveis no BF, como o eixo, o bosh ou a barriga. A Fig 2 dá algumas vistas de andaimes em um BF.
Fig 2 Vistas de andaimes em um BF
A composição química típica da raiz e da crosta dura das amostras de andaime de alguns dos BFs da Europa são fornecidas na Tab 1.
Tab1 Análise típica de andaimes de amostras de BFs europeus | ||||
Sl. No. | Composição | Raiz do andaime | Crosta dura do andaime | |
Amostra 1 | Amostra 2 | |||
% | % | % | ||
1 | C | 4,24 | 1,59 | 8,4 |
2 | Fe (total) | 56 | 33 | 42,6 |
3 | SiO2 | 5.4 | 21 | 5,9 |
4 | Al2O3 | 9,51 | 5.16 | 1,26 |
5 | CaO | 11,9 | 20,6 | 5,35 |
6 | MgO | 4,95 | 6,08 | 1,91 |
7 | ZnO | 0,002 | N.D. | 23,3 |
8 | PbO | 0 | N.D. | 0,26 |
9 | K2O | 0,86 | 1,57 | 3.1 |
10 | Na2O | 0,36 | 0,76 | 1.3 |
11 | S | 4.2 | 0,05 | 0,20 |
Andaimes no bosh e na barriga
Em um BF ideal, a formação e descamação dos scaffolds ocorrem continuamente para que não sejam observadas grandes variações nas perdas por resfriamento ou na química da escória. Em BFs mais antigos com placas de resfriamento e revestimento cerâmico, esse equilíbrio é difícil de alcançar, especialmente quando o revestimento está erodido. Em BFs recentes com revestimento em aduela ou chapa de cobre-grafite, há uma sequência regular de construção e descamação de andaimes alternada. O descascamento dos andaimes normalmente ocorre duas ou mais vezes em uma semana.
O andaime é composto por brisa de coque, componentes de minério reduzido, escórias, componentes de pó como fuligem, álcalis condensados etc. Este tipo de andaime é quebradiço e se desprende com bastante facilidade. Se este tipo de andaime permanecer por mais tempo na parede bosh, especialmente quando cobre a circunferência bosh, é mecanicamente estável e ganha força com o tempo. Os óxidos de ferro são reduzidos a Fe metálico, sinterizados e carbonizados. O carbono de coque (C) é gaseificado por reação de perda de solução deixando espaço para poeira e materiais de condensação, por exemplo. óxido de potássio (K2O). Quando o andaime permanece por mais tempo em temperaturas mais altas no bosh, o andaime é compacto e contém principalmente Fe e escória. Quanto mais tempo o andaime fica, mais ele ganha em dimensões e aumenta o risco de perturbações graves.
Uma típica formação de andaime ocorre devido às razões e às etapas que consistem em (i) estarem presentes na carga muitos finos e sinter mal peneirado com características de degradação de redução de baixa temperatura inferiores, (ii) o material fino é segregado para a parede lado onde o fluxo de gás é fraco, a temperatura baixa e a taxa de redução lenta, (iii) a raiz da zona coesiva está localizada baixa no bosh e também pode ser carga mista, (iv) a descida normal da carga pára devido a uma suspensão ou parada de manutenção, (v) a decrepitação do sínter continua devido à sua redução, (vi) o material amolecido ou semifundido adere a um elemento de resfriamento e solidifica, (vii) quando a carga começa a descer novamente (a suspensão escorrega ou o forno é reiniciado após a parada), este material aderido fica no seu lugar, (viii) zinco (Zn) e compostos alcalinos condensam-se do gás no material estagnado aglomerando os finos juntos, (ix) formação da raiz do andaime dobra, (x) na superfície da camada de material estagnado, em direção à carga, a condensação de compostos aglomerantes e poeira continua construindo uma crosta dura de Fe, ZnO (óxido de zinco), K2O e componentes de escória, (xi) continuação crescimento para cima e ligeiramente para o centro do forno. Se esse tipo de andaime crescer, ele pode crescer por algum tempo sem criar problemas significativos, mas depois disso causa sérios distúrbios na operação do BF, por exemplo, lareira refrigerada, avarias de tuyère, etc.
Andaimes no eixo médio e inferior
Tradicionalmente, os álcalis estão sendo considerados como a razão para a formação de andaimes no eixo BF. Em temperaturas acima de 1100°C, os álcalis são reduzidos e vaporizados da escória fundida e ascendem com o gás. Os cianetos alcalinos são formados em temperaturas que variam de 900°C a 1000°C e em temperaturas de menos de 750°C a 880°C esses vapores são condensados e oxidados por CO2 em carbonatos. Os álcalis também podem reagir com materiais de carga, partículas de poeira e o revestimento se a temperatura for alta o suficiente. No sistema Na2O-K2O-MgO-CaO Al2O3-SiO2, existem muitas composições com baixo ponto de fusão, com algumas delas com ponto de fusão tão baixo quanto 700 graus C. Em temperaturas flutuantes, esses derretimentos podem dissolver mais material sólido quando a temperatura é subindo e aglomeram as partículas juntas quando a temperatura cai novamente. Estas misturas de baixo ponto de fusão decompõem-se em fases mais estáveis durante a solidificação e é difícil fixar uma determinada composição fundida como fase aglomerante. As fases cristalizadas têm geralmente pontos de fusão mais elevados do que a fase fundida inicial. É por isso que por ex. KAlSiO4 (calsilita) é frequentemente encontrado nos andaimes, embora tenha um ponto de fusão muito alto (superior a 1700 graus C). A influência de K na formação do andaime é mostrada na Fig 3.
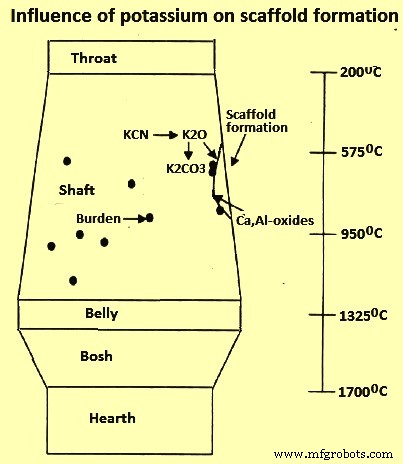
Fig 3 Influência do K na formação do andaime
O zinco é reduzido em cerca de 800 graus C e é evaporado a 907 graus C. É oxidado de volta a ZnO nas partes mais frias da carga, onde a temperatura cai abaixo de 800 graus C e onde a proporção de CO2 / (CO2+CO) é superior a 0,2.
O andaime pode crescer muito rápido se não houver mecanismo de desgaste, como o movimento da carga descendente. Durante o movimento da carga descendente, os torrões de coque com arestas duras atuam como material de moagem. O crescimento do andaime é um equilíbrio entre os fenômenos de aderência e desgaste. Há muitos fatores que contribuem são descritos anteriormente. Geralmente é difícil apontar apenas um fator. Normalmente uma soma de muitos fatores desencadeia o crescimento de um andaime.
Andaimes no eixo superior
Andaimes no eixo superior são muito comuns quando os materiais de carga não são completamente peneirados ou os valores de suas propriedades de ruptura a baixa temperatura são ruins. Os finos na carga são segregados para as paredes ou são formados por decrepitação do sinter. Quantidades excessivas de finos dão origem a uma alta queda de pressão e podem causar os chamados “suspensos de poeira”. O material fino estagnado forma uma base para aglomerar compostos como ZnO e K2CO3. Às vezes, a umidade na carga úmida e fria também pode condensar nos materiais finos do lado da parede.
A raiz do andaime está localizada no meio do eixo, preferencialmente ancorada em torno de placas de resfriamento pendentes. Como a raiz do andaime está localizada tão alta no eixo, é difícil destruí-la derretendo-a com a escória. Além disso, um andaime no eixo superior dificulta ou mesmo impossibilita o controle da distribuição de minério/coque ao longo do raio do forno.
Causas para a formação de andaimes
Existem várias teorias sobre como a formação de andaimes é iniciada, mas todas as teorias aceitam que álcalis e/ou Zn estejam envolvidos no processo de formação de andaimes. A diferença básica entre as teorias é que se álcalis e Zn atuam apenas como iniciadores para a formação de andaimes, ou se são responsáveis por todo o processo. No entanto, não é muito certo se a presença de álcalis e Zn é um pré-requisito para a formação de andaimes, ou se eles apenas agravam todo o processo de formação de andaimes.
Com base nos estudos químicos e mineralógicos realizados nas amostras coletadas para os scaffolds de vários BFs, fica evidente que a formação de scaffolds no BF pode ocorrer por uma causa única ou por múltiplas causas. As várias causas estão resumidas abaixo.
Zinco – Compostos contendo Zn e Zn são encontrados em várias amostras. O acúmulo de Zn ocorre devido à ciclagem de Zn no BF. Compostos contendo Zn, como ZnO, entram no BF com a carga ferrosa. Enquanto o Zn está derretendo a temperaturas de 419,7 graus C e evaporando a 906 graus C, o ponto de fusão do ZnO é 1975 graus C. Dependendo da pressão parcial de Zn e dos teores de CO / CO2 e H2 / H2O, ZnO é reduzido em altas temperaturas e sob condições encontradas no nível da ventaneira conforme as reações reversíveis ZnO + C =Zn + CO, ZnO + CO =Zn + CO2 e ZnO + H2 =Zn + H2O. O Zn gasoso e metálico sobe no eixo, onde as condições mudam e o Zn é oxidado novamente e condensa no material de carga. A precipitação forma uma camada branco-esverdeada sobre o material de carga. Devido à alta temperatura de fusão, o ZnO permanece preso e desce com a carga. Juntamente com o novo Zn, inserido com a carga, o Zn acumula-se no BF desde que não seja retirado.
A oxidação e outras reações produzem vários compostos de Zn que foram estabelecidos durante os estudos mineralógicos das amostras. O ZnO é o mais encontrado. Alguns dos outros compostos encontrados são silicato de zinco (Zn2SiO4), gahnita (ZnAl2O4), hardistonita (Ca2ZnSi2O7) e franklinita (ZnO.Fe2O3). O ZnO pode aglomerar diversos finos e poeiras de carga, formando um andaime no eixo. Tal andaime não precisa necessariamente ser fixado diretamente em toda a parede que cobre.
Em um caso típico de uma operação de BF onde o material de carga tem uma carga de Zn muito alta até 45 kg por tonelada de metal quente (kg/tHM), a quantidade de Zn no BF se acumula mais rapidamente do que os BFs com menores concentrações de Zn do fardo. No entanto, os scaffolds causados pelo Zn não são um problema específico de um determinado BF. As concentrações de Zn podem atingir grandes quantidades em cada BF, se o Zn não for retirado do processo por ação específica, como altas temperaturas do gás de topo.
Sinterização – Se parte da carga ferrosa for mantida acumulada por um longo período de tempo, ela pode ser reduzida mesmo nas temperaturas e atmosfera existentes no eixo. Esse acúmulo torna-se rico em grãos de Fe metálico, encontrados próximos às fases de escória. Devido à pressão da carga e temperaturas acima de 900 graus C, os grãos metálicos de Fe podem ser sinterizados juntos. Um sólido acúmulo de Fe espesso ocorre. Por causa de sua estabilidade, ele só precisa ser fixado na parede na parte inferior do acúmulo no poço causando a formação de andaime.
Álcalis – Os álcalis normalmente entram no BF com o material ferroso e com o coque na forma de silicatos. O acúmulo de álcalis pode ocorrer de forma semelhante ao acúmulo de Zn no BF. Reduzido no nível da ventaneira, os álcalis sobem no poço e condensam a temperaturas de 882 graus C (sódio, Na) e 779 graus C (potássio, K).
Os vapores alcalinos que sobem com o gás circundante condensam-se na parte superior do BF, onde uma parte sai com o gás superior, enquanto o restante condensa nas paredes internas ou no material de alimentação. Devido à volatilização e condensação do álcali nas diferentes zonas térmicas, o álcali tende a circular dentro do BF, levando a um acúmulo e interações com outros materiais de alimentação. Isso pode ter um impacto significativo no processo, mesmo quando o álcali é carregado em pequenas quantidades, geralmente inferiores a 5 kg/tHM. Uma visão simplificada da circulação alcalina no BF é mostrada na Fig 4. Estudos de BFs escavados mostraram que o nível de álcali é mais alto onde a temperatura está acima de 1000 graus C, o que significa que há um aumento da concentração de álcali na parte inferior do o BF.
Fig 4 Visão simplificada da circulação alcalina no BF
Várias reações que estão ocorrendo para formar os óxidos de álcalis com pontos de fusão acima do nível de temperatura do eixo. Os álcalis também podem aglomerar a carga e a poeira. Se precipitados na parede do eixo, os álcalis podem unir as partes da carga e formar um andaime.
Não é essencial que os andaimes compostos principalmente de álcalis sejam formados em cada BF. No entanto, em BFs, camadas finas, contendo calsilita (KAlSiO4) e outros compostos de K2O estão presentes. Eles são formados diretamente na parede. O comportamento do KAlSiO4 é importante. Ele pode unir as peças da carga e formar um andaime. As peças ferrosas são então reduzidas e sinterizadas, formando um andaime sólido. Como o KAlSiO4 não é uma composição estável, ele pode reagir de forma que nenhuma ou muito pouca quantidade de álcalis seja encontrada posteriormente nas amostras de andaime.
Zona mole – Em temperaturas em torno de 1100 graus C, o material de carga ferrosa começa a amolecer. Estruturas moles dentro dessa zona mole são forçadas pelo peso da carga a se unirem. Durante uma paralisação do forno ou uma vez que as paredes mais frias próximas a regiões são atingidas, essa zona pastosa solidifica, adere à parede e forma a camada frontal de um andaime. O andaime perturba o fluxo de gás através do eixo e força o fluxo em outra direção. Se devido ao fluxo de gás alterado, as temperaturas permanecerem abaixo de seus níveis originais, o andaime dificilmente poderá derreter. Os processos de redução e sinterização geram então uma camada de grãos metálicos de Fe em fases de escória que são ainda mais difíceis de remover. Andaimes muito grandes podem ser encontrados em BFs onde as temperaturas atingiram mais de 1100 graus C. Esses andaimes são compostos de fases de escória e grãos metálicos de Fe sinterizados juntos. Quantidades muito pequenas de Zn ou álcalis estão presentes. Assim, nesta área, estima-se que não estes elementos, mas sim um processo de solidificação do material pastoso seja responsável pela aderência inicial. Outros indicadores para este processo de formação são a baixa carburação do Fe e as partículas de coque bem fechadas.
Água – A água entra no BF de diferentes maneiras. Os mais importantes são (i) sinterização úmida e coque, especialmente sinterização recebida do armazenamento a céu aberto que não é protegido por cobertura de condições ambientais como chuva, (ii) injeção de vapor d'água no nível da ventaneira e (iii) injeção de água líquida no topo da carga, caso as temperaturas superiores do gás excedam um determinado valor. Além disso, perto do topo da carga, nas regiões próximas da parede fria, o vapor de água pode condensar. Ao longo da parede do poço, a água líquida pode descer e atingir níveis mais profundos do poço. A água acumula poeira e partículas finas da carga e pode colar esses aglomerados na parede. Durante um longo período de tempo, os processos de sinterização e redução formam um andaime de construção sólido.
A água que flui para baixo na parede do poço reduz a temperatura nas regiões próximas à parede. Devido a esta queda de temperatura, Zn e álcalis condensam muito mais rápido e os processos de formação de andaimes correspondentes são acelerados. Uma vez que a água atinge regiões mais quentes, ela evapora, enquanto a fase de água líquida desce mais abaixo no eixo BF. O vapor de água reduz o teor de H2/H2O nestas áreas. Como resultado, o equilíbrio da reação reversível na equação ZnO + H2 =Zn + H2O é alterado na direção ou mais na direção do ZnO.
No diagrama de área de predominância para o sistema Zn-O-H2 (Fig. 5), três fases diferentes são mostradas em função do teor de H2/H2O e da temperatura. As fases são (i) Zn líquido, Zn(l), (ii) vapores de Zn, Zn(v), e (iii) ZnO sólido, ZnO(s). O diagrama foi calculado a partir de dados termoquímicos para substâncias puras. As linhas sólidas com uma curva no ponto de ebulição são linhas de coexistência onde Zn e ZnO existem em equilíbrio juntos. Zn é estável acima dessas linhas e ZnO é estável abaixo. As linhas de coexistência são uma função da atividade do Zn, a(Zn). Para gases ideais, a atividade dos vapores de Zn, a(Zn) é igual à pressão parcial de Zn(v). Sob condições normalmente encontradas em BF, valores de atividade entre 0,1 e 0,01 são esperados para vapores de Zn. Quanto mais as condições estiverem longe das linhas de coexistência, mais um produto será criado antes que a reação atinja o equilíbrio novamente. Se mais ZnO for formado, as chances de tirar Zn do processo por altas temperaturas de topo do gás diminuem.
Fig 5 Diagrama de área de predominância para o sistema Zn-O-H2
O círculo preto no diagrama caracteriza uma quantidade de H2 que é três vezes a quantidade de vapor de água em temperaturas um pouco acima do ponto de ebulição do Zn. Dependendo da pressão parcial do Zn, o equilíbrio termo-mecânico é próximo, provavelmente até a favor do Zn(v). Se a água for adicionada, ela evapora e o teor de H2/H2O diminui na direção da seta. As condições estão agora mais distantes das linhas de convivência. Como resultado, a quantidade de ZnO formado é aumentada. Após a precipitação, o scaffold se forma muito mais rápido à medida que o processo de formação do scaffold se acelera.
Cal junto com água – Se muito cal queimada for adicionada ao processo de sinterização, pode forçar o sinter a rachar e quebrar, se entrar em contato com a água e reagir. Como resultado, a quantidade de peças de carga fina é aumentada no BF. Em geral, partes finas da carga são muito mais fáceis de aglomerar e favorecem a formação de andaimes. Dentro do BF, cal queimada e água podem reagir para formar cimento. O cimento aglomera a carga e forma um andaime de construção muito estável e sólido. Se as peças de carga ferrosa são reduzidas e sinterizadas, um andaime ainda mais estável é formado.
Processo de formação de andaimes
Os andaimes são normalmente constituídos por uma casca sólida no lado interno do BF e uma camada de material de carga solta entre esta casca e a parede do BF. Estudos mostraram que a casca sólida se desenvolve ao longo de uma isotérmica. Durante a formação, esta isotérmica está localizada na posição da casca sólida. Existem duas estruturas diferentes que formam a casca sólida no lado interno, a saber, (i) grãos de Fe metálico em fases de escória e (ii) carga colada por ZnO. Dois processos de formação parecem possíveis.
No primeiro processo, a carga mole e ferrosa solidifica ao longo de uma isotérmica, se a temperatura dentro do BF cair. O motivo de uma queda de temperatura pode ser uma interrupção ou uma flutuação no processo. Ao longo de um intervalo de tempo suficientemente longo, a carga contendo Fe é reduzida e mais sinteriza junto à temperatura do eixo e atmosfera. Ao final do processo, grãos metálicos de Fe em fases de escória se formaram.
No segundo processo, Zn, álcalis e seus compostos precipitam e se formam quando a temperatura cai abaixo de um certo ponto. Somente a uma certa temperatura, os processos de reação e precipitação criam compostos de Zn ou alcalinos suficientes para unir a carga. As estruturas de coque e sinterização unidas por ZnO são o produto. Durante outros processos de redução e sinterização da carga de Fe, o Zn pode reagir e gaseificar. Neste caso, os grãos metálicos de Fe nas fases de escória são o produto final do scaffold, que no primeiro processo é formado por estruturas de coque e sinter unidas por ZnO.
O andaime formado por qualquer um dos processos acima explica a forma da casca sólida, a camada de material de carga solta e por que o andaime é formado em poucos dias. Uma vez que a casca sólida existe, ela perturba o fluxo de gás através do eixo e força o fluxo em outra direção. Como resultado do fluxo de gás alterado, as temperaturas podem ficar abaixo de seus níveis originais. Neste caso, o andaime dificilmente pode derreter. A condensação e a precipitação na camada de material de carga solta acumulam posteriormente Zn e compostos alcalinos. Esses processos de acumulação também podem levar à formação de uma nova camada na frente da casca já existente. A casca existente é um suporte estrutural para o crescimento de uma nova camada e a protege da abrasão.
Os andaimes são normalmente formados continuamente. Os teores de álcalis e Zn do gás ascendente são depositados na carga ou refratário à medida que a temperatura diminui no eixo. Esse fenômeno cria andaimes de crescimento lento. A velocidade de crescimento da camada de andaime no refratário é geralmente da ordem de alguns milímetros por semana. Este tipo de formação de andaimes é influenciado principalmente pela carga alcalina e Zn da carga e pela distribuição de temperatura no eixo.
Distúrbios ou interrupções do processo no BF podem fazer com que a carga comece a sinterizar. Se isso ocorrer na região inferior do forno, a carga descendente pode remover parte ou todo o material aglomerado. Se a aglomeração ocorrer na parte superior do eixo, a carga parcialmente aglomerada pode ficar estagnada. O material abaixo desta zona também deve ficar estagnado. Todo esse material é reduzido lentamente com o tempo e se torna Fe reduzido. Durante o tempo de redução e dependendo da distribuição de temperatura no BF, os fumos alcalinos e de Zn podem se depositar nas superfícies das partículas de óxido de Fe e formar compostos com silicatos de alumina e magnésia. A velocidade de crescimento deste fenômeno pode ser consideravelmente maior em comparação com a formação do scaffold devido à deposição de álcali e Zn no refratário. A velocidade de crescimento depende de parâmetros como a extensão da zona de carga aglomerada inicial, distribuição de temperatura e a quantidade de partículas finas no gás ascendente.
Medidas para evitar a formação de andaimes
Se os andaimes crescem muito, eles perturbam o processo no BF e reduzem a eficiência do BF. Andaimes de construção sólida às vezes só podem ser removidos por detonação. Essas contramedidas radicais às vezes não podem ser evitadas. No entanto, parece possível intervir com medidas menos extremas para evitar a formação de andaimes. Quando os andaimes ainda são comparativamente pequenos em tamanho, especialmente durante o processo de formação, as etapas contra sua formação são eficazes. Algumas dessas medidas são apresentadas a seguir.
Capacidade de refrigeração – Para iniciar o processo de fusão do material de carga solidificado na parede do eixo e para evitar a solidificação da zona pastosa em regiões frias próximas à parede, a capacidade do sistema de resfriamento do eixo pode ser reduzida. O número de caixas de resfriamento na parte superior do eixo pode ser minimizado. A menor capacidade de refrigeração mantém a temperatura interna alta o suficiente, para evitar que uma possível zona pastosa solidifique durante as paradas do BF. Alternativamente, parece possível carregar grandes quantidades de coque perto da parede, antes de uma paralisação. O coque deve ser colocado de tal forma que, durante a paralisação, fique na região onde a parte inferior do andaime normalmente gruda na parede. Dessa forma, a solidificação e a aderência do material de carga mole podem ser evitadas, porque o coque não fica macio nas temperaturas do eixo.
Perto da parede de carregamento de coque – Grandes quantidades de coque, preferencialmente carregadas em direção à parede, aumentam a temperatura e podem derreter andaimes. O aumento da temperatura também evita ou reduz a condensação de Zn e álcalis e, como resultado, o desenvolvimento de novos andaimes. Os primeiros resultados de um carregamento de coque próximo à parede geralmente são visíveis dois ou três dias após seu início. A desvantagem desta contra-medida é, evidentemente, um maior processo de desgaste do refratário da parede do eixo e menor utilização de gás.
Sílica – A sílica pode reagir com o material do scaffold e pode formar compostos eutéticos de sílica com baixo ponto de fusão. Portanto, a sílica pode ser adicionada às regiões próximas à parede, para derreter os andaimes da parede do eixo.
Cobrança central de partes finas da carga – Partes finas da carga são muito mais fáceis de aglomerar e devem ser reduzidas. Se forem cobrados do BF, estes devem entrar no BF para a região central. Desta forma, as chances de aderência dos aglomerados de carga fina à parede do poço são minimizadas.
Balanceamento de álcalis e escória ácida – O balanço de entrada e saída fornece informações valiosas sobre a quantidade real de álcalis no processo de BF. Os álcalis podem então sair do BF por uma escória ácida. A escória ácida também aumenta a quantidade de enxofre no metal quente (HM). Portanto, o balanceamento é importante para operar o BF com a escória ácida por um período limitado e, portanto, as desvantagens o mínimo possível.
Deslizamento forçado – O deslizamento forçado ocorre quando há uma parada da pressão de jateamento por alguns minutos. Isso força a carga a descer repentinamente no poço e a parte superior da carga afunda. Devido à força repentina iniciada pelo peso da carga, os andaimes podem quebrar. O deslizamento forçado deve ser dado apenas no final do rosqueamento, para evitar perda de qualidade e contaminação do HM pelo deslizamento do material.
Otimização de recursos de construção de BF – Especialmente no topo frio, as caixas de refrigeração funcionam como uma âncora para futuros andaimes. Ao contrário das aduelas, as caixas de resfriamento geram pontos frios distribuídos pela parede do poço. Esses pontos frios são pontos de partida ideais para condensação e solidificação. As aduelas com o mesmo efeito de resfriamento que as caixas de resfriamento produzem um campo de temperatura constante, sem os mínimos extremos de temperatura. Assim, as aduelas são menos propensas a gerar andaimes.
Alta temperatura máxima do gás – O Zn pode ser retirado do processo BF com altas temperaturas do gás de topo, não dando aos vapores de Zn tempo suficiente para condensar ou reagir. Para atingir este objetivo, uma temperatura ótima do gás de topo necessária é de cerca de 350 graus C. Juntamente com as altas quantidades de coque, carregadas na área da parede, quantidades de Zn de 45 kg/tHM podem ser manuseadas no BF.
Processo de manufatura
- Geração e uso de gás de alto-forno
- Uso de Nut Coke em um Alto Forno
- Injeção de carvão pulverizado em um alto-forno
- Irregularidades do alto-forno durante a operação
- Sistema de resfriamento do alto-forno
- Sistemas de carregamento de alto-forno
- Química da Ferragem por Processo de Alto Forno
- Revestimento refratário do alto-forno
- Fatores que afetam a taxa de coque em um alto-forno
- Alto-forno e seu projeto