Revestimento refratário do alto-forno
Revestimento refratário do alto-forno
Um alto-forno moderno (BF) é revestido de refratário para proteger a carcaça do forno das altas temperaturas e materiais abrasivos dentro do forno. O revestimento refratário é resfriado para aumentar ainda mais a proteção contra o envio de excesso de calor que pode destruir o revestimento refratário. A BF possui um sistema refratário complexo para fornecer uma vida longa e segura que é necessária para a disponibilidade do alto-forno e para permitir a operação e fundição quase contínuas do forno.
As condições dentro do alto-forno variam amplamente por região e os refratários estão sujeitos a uma variedade de mecanismos de desgaste. Os detalhes são fornecidos na Tab 1. A condição de aplicação de diferentes regiões de um alto-forno não é a mesma devido à própria natureza de sua geometria e também devido ao processo pirometalúrgico que ocorre em diferentes estágios. Existem diversos mecanismos de desgaste físico e químico nas diferentes regiões do alto-forno e são de natureza complexa. Por exemplo, desgaste mecânico ou abrasão ocorre principalmente na região superior da pilha e é causado pela queda dos materiais de carga e pelos gases carregados de poeira. Altas cargas térmicas são um fator importante na pilha inferior e nas regiões da barriga. Na região da lareira, o fluxo horizontal e vertical de metal quente combinado com tensões térmicas muitas vezes forma cavitação indesejável em forma de pé de elefante. Os materiais refratários nessas regiões devem cuidar desses mecanismos de desgaste para evitar danos decorrentes dos mesmos. Portanto, a pilha BF (média superior e inferior), barriga, bosh, canaleta e região da ventaneira, lareira e furo de drenagem exigem diferentes qualidades de refratários, dependendo das respectivas condições de aplicação.
Aba 1 Mecanismos de ataque em diferentes regiões do alto-forno | ||
Região | Mecanismo de ataque | Dano resultante |
Pilha superior | Abrasão | Desgaste abrasivo |
Flutuações de temperatura média | Descamação | |
Impacto | Perda de tijolos | |
Pilha intermediária | Flutuações de temperatura médias a fortes | Descamação |
Erosão por gás | Desgaste | |
Oxidação e ataque alcalino | Deterioração | |
Pilha inferior | Flutuações de temperaturas intensas | Descamação severa |
Erosão por jatos de gás e abrasão | Desgaste | |
Oxidação e ataque alcalino | Deterioração | |
Fadiga térmica | Dano e rachaduras no casco | |
Barriga | Flutuações de temperatura média | Descamação |
Oxidação e ataque alcalino | Deterioração | |
Abrasão, erosão gasosa e alta temperatura | Desgaste | |
Bosh | Alta temperatura | Ataque de estresse |
Ataque de escória e alcalino | Deterioração e desgaste | |
Flutuações de temperatura média | Descamação | |
Abrasão | Desgaste | |
Pista e | Temperatura muito alta | Fissuras por estresse e desgaste |
Região de Tuyère | Flutuações de temperatura | Descamação |
Oxidação (água e oxigênio) | Deterioração | |
Ataque e erosão de escória | Desgaste | |
Dano de crostas | Perda de elementos de resfriamento e ventaneiras | |
Lareira | Oxidação (água) | Desgaste |
Zinco, escória e ataque alcalino | Deterioração | |
Alta temperatura | Acúmulo de estresse e rachaduras | |
Erosão de líquidos quentes | Risco de ruptura | |
Entalhe de ferro | Flutuações de temperaturas intensas | Descamação |
(orifício da torneira) | Erosão (escória e ferro) | Desgaste do furo da torneira |
Ataque de zinco e álcali | Deterioração | |
Ataque de gás e oxidação (água) | Desgaste e deterioração |
A seleção da combinação de refratários apropriada dependendo do mecanismo de desgaste é muito importante. Uma seleção inadequada dos refratários geralmente leva a uma falha refratária que, posteriormente, se torna um problema complexo de resolver. Os tipos de revestimento refratário necessários em uma região de alto-forno, bem como a tendência no padrão de revestimento refratário, são apresentados na Fig 1.
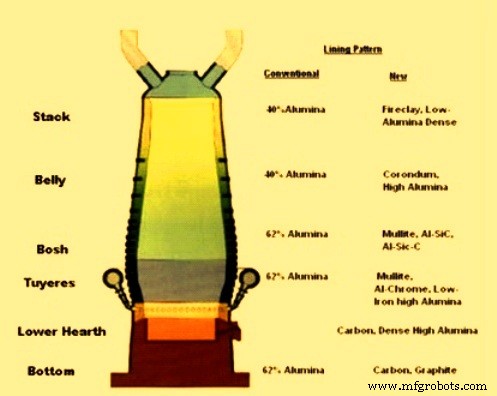
Fig 1 Revestimento refratário em várias regiões de um alto-forno
Atualmente, espera-se que a vida útil da campanha de um BF seja de cerca de 15 anos ou mais. Além disso, há uma tendência para BFs de grande capacidade, que estão sendo submetidos a condições operacionais rigorosas. Para atingir a meta de longa vida útil do revestimento sob condições operacionais rigorosas, é necessário ter uma boa combinação de refratários de alto grau combinados com sistemas de refrigeração altamente eficientes e controle rígido na operação do forno para garantir alta produtividade sem trabalho excessivo de parede e com minimização de grandes 'deslizamentos' no BF que podem causar danos prematuros excessivos aos revestimentos refratários.
Sabe-se que o fundo e uma parte da lareira são corroídos principalmente por ferro-gusa, escória e álcalis. Os tijolos refratários nessas áreas estão sujeitos a altas cargas e temperaturas. Portanto, requer um revestimento refratário que deve ter alta resistência, menor fluência no valor de compressão e valores mais altos de RUL (refratário sob carga) e PCE (equivalente a cone pirométrico). Alguns BFs usam baixo teor de ferro, denso 42% -62% de alumina, tijolos refratários de mulita, blocos de carbono convencionais etc. na parte inferior e inferior da lareira, enquanto a tendência atual é substituí-la por blocos de grafite super micro poros. A vida da lareira BF depende principalmente dos seguintes fatores.
- Fatores operacionais como (i) alta produtividade levando a altas cargas de calor, (ii) alta velocidade do fluido que causa mais erosão e (iii) alta injeção de carvão significa menor permeabilidade. Nenhum desses fatores está sob o controle do operador BF e, portanto, a única solução para isso pode ser um revestimento refratário robusto.
- Projeto do sistema de revestimento refratário - Todo o revestimento refratário também está sujeito a estresse térmico, que também desempenha um papel dominante, especialmente quando o design é inadequado. O sistema ou projeto de revestimento refratário deve (i) otimizar a resistência térmica, (ii) fornecer alívio de expansão, (iii) evitar rachaduras e (iv) eliminar barreiras embutidas.
- Propriedades refratárias:incluem (i) alta condutividade térmica, (ii) resistência alcalina, (iii) baixa permeabilidade, (iv) baixa expansão térmica e (v) baixa elasticidade.
O recente desenvolvimento de tijolos de carbono microporosos e a melhoria da qualidade dos blocos de grafite e semi-grafita levaram a uma maior resistência à infiltração de ferro e escórias e condutividade térmica. O problema da formação de camada frágil em torno de 800 graus C isotérmico por condensação alcalina e tensões térmicas foram resolvidos usando blocos menores, tolerâncias de expansão ótimas etc. Os refratários de carbono são cobertos por tijolos refratários ou mulita para protegê-los contra a oxidação. O design deste 'copo de cerâmica' é importante, pois as isotermas são alteradas dependendo da qualidade e espessura do material do copo.
Os tijolos empilhados são particularmente expostos a alta abrasão e erosão por material de carga do topo, bem como partículas de fumaça e poeira de alta velocidade que saem devido à alta pressão de explosão em um ambiente de CO (monóxido de carbono). Portanto, a condição de aplicação exige materiais refratários que devem ter alta resistência, baixa permeabilidade, alta resistência à abrasão e resistência à desintegração de CO. Tijolo refratário de alta resistência ou tijolo de alumina densa com Al2O3 em torno de 39% - 42% pode conferir essas características necessárias para aplicação em pilha.
O tuyere e bosh são atacados por mudança de temperatura, abrasão e álcalis; e a barriga e o eixo inferior por choque térmico, abrasão e ataque de CO etc. Nas áreas críticas do BF, ou seja, tuyère, bosh, barriga e pilha inferior, carboneto de silício, SiC-Si3N4 e refratários de corindo substituíram o carbono e 62% de Al 2 O3 ou tijolos de mulita. Isso aproveita a alta condutividade térmica do SiC em combinação com os resfriadores de stave. No entanto, devido ao problema de vazamento de água ao redor do furo de drenagem e da área da ventaneira, muitos altos-fornos são revestidos com refratários de corindo de alta alumina ou alumina-cromo. O presente e a tendência nos refratários Bf são dados na Tab 2.
Guia 2 Refratários de alto-forno | ||
Área | Presente | Tendência |
Pilha | 39 % – 42 %% Al2O3 | Argila refratária super útil |
Barriga | 39% – 42% Al2O3 | Corindo, SiC-Si3N4 |
Bosh | 62% Al2O3, mulita | SiC-Si3N4 |
Tuyère | 62% Al2O3, mulita | SiC autoligado, Alumina-cromo (Corindo) |
Lareira inferior | 42%-62% Al2O3, mulita, bloco de carbono convencional | Bloco de carbono/grafite com super microporos |
Orifício de torneira | Aderido ao alcatrão de refratário, com alto teor de alumina/alcatrão de SiC | Aderido ao alcatrão de refratário, com alto teor de alumina/alcatrão de SiC |
Calha principal | Piche / argila ligada à água / Grog / massas de compactação ligadas ao alcatrão, Castables | Concretos de cimento ultrabaixos (ULCC), misturas de SiC/Alumina, técnica de reparo de canhão |
Boca basculante | Alta alumina/massas de compactação SiC/concretos com baixo teor de cimento | Alta alumina / SiC / Carbono / ULCC |
Diferentes tipos de refratários BF
Diferentes tipos de refratários que são usados no revestimento de alto-forno são descritos abaixo.
- Bloco de carbono cozido – Bloco de carbono micro poroso, bloco de carbono semi-grafítico e bloco de silício microporoso de carbono são feitos com antracite eletricamente calcinada de alta temperatura, grafite sintético e carboneto de silício como principais matérias-primas. Eles possuem maior condutividade térmica, menor permeabilidade, boa resistência ao metal quente e alcalino. Blocos de carbono semi-grafíticos são usados como revestimento inferior inferior. Blocos de carbono microporosos são usados como revestimento do fundo superior e inferior de altos-fornos com fundição intensificada. Blocos de silício de carbono microporoso são usados na colocação da lareira, furo de torneira e furo de escória do alto-forno.
- Tijolos de carbono cozidos de pequeno porte – Os tijolos de carbono microporosos moldados e os tijolos de carboneto de silício de carbono são produzidos através de moldagem a quente, cozimento em alta temperatura e moagem acabada com antracito eletricamente calcinado de alta temperatura, grafite sintético e carboneto de silício como principais matérias-primas e o óleos derivados de carvão ou resina de formaldeído fenólico como aglutinante, bem como aditivos ultra micro em pó. Tijolos de carboneto de silício de carbono microporosos moldados podem ser usados para a alvenaria de ventaneira, furo de escória, furo de torneira, lareira e zonas de formação de escória do alto-forno.
- Tijolo de copo cerâmico - Estes são tijolos de corindo compostos ligados em fase plástica. O tijolo é composto de mulita de alta qualidade e corindo fundido de alta pureza como matérias-primas com adição de aglutinante especificado por moldagem em alta pressão e sinterização em alta temperatura. Com características de alta refratariedade sob carga (RUL), estrutura compacta, baixa porosidade e alta resistência à corrosão, os tijolos são utilizados para o fundo BF, revestimento do fundo da taça cerâmica e tijolo combinado de ventaneira, furo de torneira e furo de escória do grande jateamento forno.
- Tijolo de corindo – O tijolo de corindo é feito de corindo marrom fundido e carboneto de silício como materiais de partida, combinados com aditivos especiais, através do processo de prensagem e sinterização antes da usinagem fina. O tijolo é caracterizado por uma boa resistência alcalina e resistência à corrosão por escória, que é adequada para revestir o fundo, o copo de cerâmica da lareira, a ventaneira, o furo de torneira e o furo de escória.
- SiC- Tijolo Si3N4 – Existem muitos tipos diferentes de tijolo SiC com diferentes sistemas de colagem e conteúdo de SiC variável. Em geral, SiC de ligação direta tem alta resistência a álcalis e zinco. Além disso, eles têm alta condutividade térmica, excelente resistência à erosão, propriedades de choque térmico muito boas e são resistentes à corrosão e ao ataque de CO. Geralmente, SiC ligado a nitreto é usado em aplicações, como barriga de BF.
- Tijolo de carbono de alumina microporosa – Esses tijolos são feitos adotando clínquer de bauxita de grau especial, corindo, grafite e alumina média como principais matérias-primas, combinados com vários tipos de aditivos em pó super fino. Possui micro poros, boa resistência alcalina e alta condutividade térmica. É usado para forro de bosh, pilha e parede de resfriamento de BF.
- Tijolos de classe de alumina de 50% – Normalmente, os refratários desta classe são tijolos refratários super resistentes atualizados. Eles são geralmente compostos por uma mistura de bauxita, argila de sílex/chamota e argila plástica. Tijolos com 50% de alumina geralmente têm baixa porosidade, expandem após reaquecimento a 1600°C e têm boa resistência ao ciclo térmico. Um tijolo desta classe contendo materiais de maior pureza apresenta boas qualidades de suporte de carga e excelente resistência ao ataque alcalino.
- Tijolos classe alumina 60% – Os tijolos desta classe são compostos por uma grande variedade de materiais. Os tijolos de alumina média mais comuns e conceituados são compostos de minerais do grupo sillimanita (geralmente combinados com pequenas quantidades de alumina calcinada e argilas plásticas). Outras qualidades de 60% de alumina nesta classe são compostas por uma mistura de chamota sintética, bauxitas, alumina calcinada e argilas plásticas. Altos níveis de formação de mulita permitem que tijolos desta classe (especialmente refratários contendo silimanita) apresentem excelente resistência à fluência. Os tijolos de silimanita podem ser frequentemente fosfatados/quimicamente ligados e curados como um meio de melhorar a resistência ao choque térmico.
- Tijolos de classe de alumina 70% – Esta classe de tijolos é baseada em matérias-primas primárias bauxita ou chamota de alta alumina que é adicionada com argila refratária. Esses tijolos são queimados a cerca de 1400 graus C para evitar a expansão excessiva durante a queima (causada pela reação dos ingredientes siliciosos com a bauxita, formando mulita). Os tijolos de 70% de alumina apresentam altos valores de expansão em serviço, reduzindo assim o dimensionamento das juntas.
- Tijolos classe alumina 80% – São à base de bauxita com adições de alumina calcinada e materiais argilosos. Eles são disparados a cerca de 1420 – 1480 graus C para manter o dimensionamento consistente dos tijolos. Os produtos queimados desta classe têm cerca de 20% de porosidade, boa resistência e resistência ao ciclo térmico. Esses produtos estão associados à ligação fosfato/químico (tanto curado quanto queimado) como forma de conferir maior resistência à abrasão e reduzir a porosidade.
- Firelay tijolos – Os tijolos refratários são compostos de uma mistura de geralmente duas ou mais argilas. O uso de argilas de sílex e caulim confere refratariedade, as argilas calcinadas (chamotas) controlam as retrações de secagem e queima e as argilas plásticas facilitam a formação e a força de união. Os tijolos refratários geralmente são agrupados em (i) tijolos super resistentes (PCE> 33) que possuem um teor típico de alumina de 40 % a 45 % e têm boa refratariedade, resistência ao choque térmico e estabilidade de volume em temperaturas mais altas, (ii) alta tijolos refratários para serviço (PCE 31 ½ a 33) que são semelhantes aos equivalentes para serviço super, mas são normalmente fabricados com argilas/chamotas de sílex de qualidade inferior e argilas plásticas (típico Al2O3 40% a 45%) e são comumente usados como substitutos para tijolos refratários para serviço médio onde a ciclagem térmica é um problema potencial, (iii) tijolos refratários de serviço médio (PCE 29 a 31) (típico Al2O3 38% a 42%) são usados em aplicações menos severas e sua resistência ao choque térmico é menor do que em tijolos refratários de serviço super e alto, (iv) tijolos refratários de baixa carga (PCE 15 a 29) (típico Al2O3 35% a 38%) são usados como revestimentos de apoio e outras aplicações onde prevalecem temperaturas moderadas, e (v) tijolos refratários de semi-sílica que têm teores típicos de alumina de 18 % a 25% com valor de sílica s que variam de 72% a 80% e têm excelente resistência ao suporte de carga e estabilidade de volume em temperaturas relativamente mais altas.
- Massa do furo de macho – As principais características necessárias da massa do furo de macho incluem boa viscosidade e boas propriedades de sinterização combinadas com resistência à corrosão e erosão.
Processo de manufatura
- Revestimento refratário de um forno de oxigênio básico
- Geração e uso de gás de alto-forno
- Uso de Nut Coke em um Alto Forno
- Proteção do Revestimento do Lar do Alto Forno pela Adição de TiO2
- Injeção de carvão pulverizado em um alto-forno
- Irregularidades do alto-forno durante a operação
- Sistema de resfriamento do alto-forno
- Sistemas de carregamento de alto-forno
- Química da Ferragem por Processo de Alto Forno
- Fatores que afetam a taxa de coque em um alto-forno