O Poder da Programação de Manutenção Certa
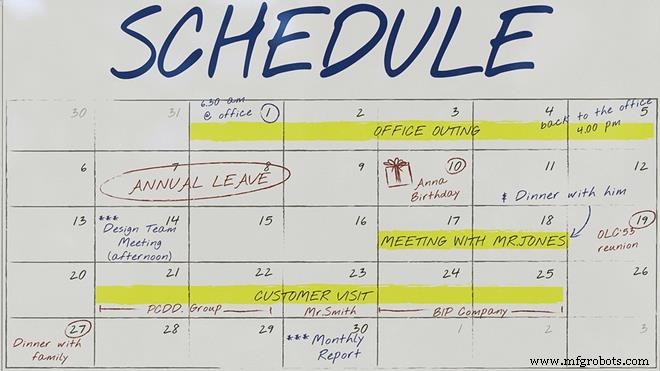
Definindo a programação
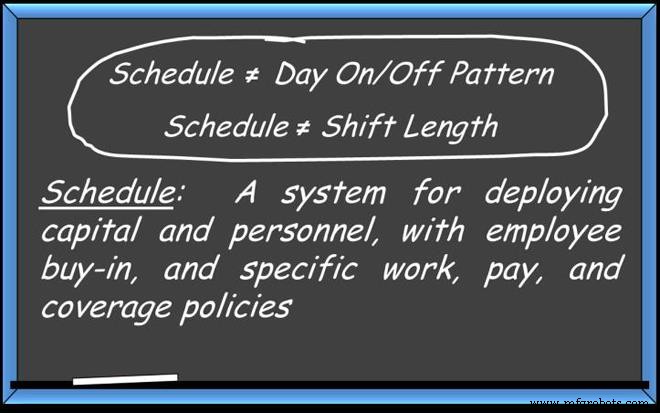
Muitos gerentes acreditam que o cronograma se refere à cobertura de determinados dias usando uma duração de turno. “Você está usando turnos de 8 ou 12 horas?” Embora os dias de cobertura e a duração do turno sejam considerações importantes, eles são apenas parte da solução. Uma programação começa como um sistema para distribuir recursos-chave:capital e pessoal. Mas, para ser eficaz, esse cronograma precisa ter a adesão dos funcionários.
Além disso, o sistema deve incluir todas as regras de trabalho, remuneração e cobertura que tornam o cronograma o que ele realmente é. Por exemplo, a programação de segunda a sexta, em que ninguém trabalha no fim de semana, é muito diferente da programação de segunda a sexta-feira, em que todos são forçados a trabalhar todos os sábados e metade dos domingos. No papel, os dois parecem iguais, mas os horários reais, aqueles que afetam os funcionários, são muito diferentes.
O exemplo de segunda a sexta-feira é aplicável a várias organizações de manutenção. Quantas fábricas têm técnicos de manutenção trabalhando 40 horas durante a semana, apenas para virem trabalhar todo final de semana nas horas extras? É uma prática tão padrão que a maioria das pessoas a considera um estilo de vida.
A pior parte é que normalmente o pessoal de manutenção não consegue chegar ao equipamento em que precisa trabalhar durante a semana porque está sendo usado pelos operadores. Eu até ouvi:“Eu fico em dia direto durante a semana e chego para trabalhar nos fins de semana na hora extra”.
E se a planta trabalha seis dias por semana, a equipe de manutenção está trabalhando todos os domingos. As operações 24 horas por dia e 7 dias por semana têm problemas muito semelhantes. Estou aqui para lhe dizer que não precisa ser assim.
Então, e se as operações precisarem funcionar de segunda a sexta-feira ou 120 horas por semana? Não faria sentido ter uma manutenção programada em uma equipe reduzida durante esse período para cobrir o trabalho emergente não planejado ou, se necessário, para dar suporte com trocas e outro tipo de trabalho de operação? Se for esse o caso, a manutenção deve ser programada para ser totalmente preenchida quando as operações forem encerradas, como nos fins de semana.
No entanto, mesmo essa estratégia tem alguns problemas. Primeiro, embora entregar a planta para manutenção por 48 horas consecutivas possa ser fácil, pode não ser tão eficiente. Como os técnicos só podem trabalhar cerca de 12 horas antes de precisar descansar, qualquer coisa além de um período de 12 horas não ajuda.
Uma opção é configurar a manutenção em duas equipes, mas agora você está distribuindo o trabalho por causa da carga de trabalho ou para combinar as pessoas? Em segundo lugar, você realmente deseja fazer o trabalho mais difícil, crítico e fora do padrão quando há menos gerentes com menos pessoal de suporte? Isso não faz sentido.
Manutenção Pitstop
Vamos pensar um pouco fora da caixa. Você deseja usar a manutenção com mais eficácia e rapidez, para que a planta possa voltar a trabalhar e ganhar dinheiro. Existe algum grupo maximizando o giro da chave no menor período possível para colocar as operações de volta em seu negócio principal?
Pense em stock cars por um segundo. Os pitstops são essenciais para manter o carro na pista, mas nenhuma volta está sendo feita no box, assim como nenhum produto está sendo feito durante a manutenção. Em Daytona, eles lidam com isso concentrando uma equipe altamente treinada no problema em questão e virando o carro rapidamente. Não é isso que a liderança da fábrica quer fazer - voltar à produção e ganhar dinheiro?
Você pode levar o conceito de pitstop para a planta tendo a equipe de manutenção muito focada para que eles possam fazer o trabalho no menor período de tempo. Se a tripulação tiver recursos suficientes, eles podem entrar, sair e seguir para o próximo trabalho. Esta é a essência da manutenção pitstop.
Há alguns anos, uma fábrica de engarrafamento do Meio-Oeste fazia exatamente isso. A fábrica tinha cinco linhas de produção e várias áreas de suporte que precisavam de cerca de um dia de manutenção por semana. Junto com a liderança da fábrica, desenvolvemos um cronograma que tinha uma equipe de manutenção de pitstop focada em cada área um dia por semana, de segunda a sábado. Descobrimos que 10 horas semanais cobririam a maioria dos problemas. Domingos e períodos especiais de inatividade podem ser usados para lidar com eventos maiores e mais difíceis.
Os pitstops foram programados durante o dia. Por exemplo, se a Linha 2 estivesse fora do ar para manutenção na terça-feira, o turno da noite iria desligá-la no início da manhã. A manutenção foi preparada para funcionar assim que a linha estivesse pronta. Os pacotes de trabalho foram pré-preparados, enquanto as ferramentas e peças já haviam sido preparadas para a área.
Como esse era o processo mais difícil e fora do padrão na planta, a gerência e a supervisão estavam disponíveis para garantir que tudo ocorresse sem problemas. Se houvesse algum problema, os fabricantes de equipamento original (OEMs) podiam ser contatados por telefone e o controlador estava lá para aprovar o tempo adicional. Para garantir que a produção não perdesse o ritmo, os principais líderes permaneceram até que a linha estivesse de volta a 100 por cento de operação.
De onde veio a tripulação? Eles foram retirados do turno onde muitos estavam "parados esperando para trabalhar no fim de semana na hora extra". No geral, a instalação tinha 36 técnicos de manutenção nas classificações mecânica, elétrica e de instrumentação.
Calculamos que 18 técnicos espalhados por três turnos poderiam fornecer de forma conservadora a cobertura de produção necessária para dar suporte às operações. Isso permitiu que seis técnicos atendessem a cada turno de segunda a sexta-feira. Essa estratégia permitiu que os outros 18 técnicos formassem uma equipe de pitstop.
É interessante notar que todos os gerentes e supervisores acreditavam que os técnicos de manutenção com foco no equipamento de desligamento eram muito mais eficazes do que aqueles que tentavam fazer a manutenção enquanto o equipamento estava operando. Quando questionados sobre o quão mais produtivo é, suas respostas variaram de 25 a 75 por cento mais eficazes.
Supondo que 18 dos 36 fossem transferidos para a equipe do pitstop, e o salário completo fosse de $ 46,96, essa eficácia aumentada valeria de $ 400.000 a $ 1 milhão anualmente. A economia poderia ser alcançada em uma melhor manutenção ou na redução dos requisitos de pessoal de manutenção. De qualquer forma, a economia para esta planta de engarrafamento foi significativa.
O que isso significa para os funcionários? Envolver a equipe no processo de agendamento permitiu que eles elaborassem sua própria agenda. A decisão foi feita para fazer rodízio de funcionários através da equipe de pitstop em uma base rotativa. Isso permitiu que todos compartilhassem mais dias de folga e fins de semana mais longos.
A realização de pitstops durante o dia permitia que todos os funcionários trabalhassem pelo menos 50% dos turnos diários. A rotação também permitiu que todos treinassem em habilidades básicas, ao mesmo tempo em que fornecia funcionários bem treinados para cobertura nos turnos anteriores.
Para as linhas com restrição de capacidade, o processo ficou ainda mais focado. Diferentes aspectos do processo de engarrafamento foram paralisados sequencialmente. Por exemplo, as garrafas ainda estavam sendo embaladas depois que o enchimento foi fechado. O oposto foi verdadeiro para o início - o equipamento de pré-enchimento ficou online enquanto a manutenção da embalagem ainda estava finalizando. O principal objetivo de executar um pitstop era obter mais tempo de operação de cada linha crítica, e isso foi alcançado.
Outras considerações
Então, que tal turnos mais longos? Eles são mais ou menos eficientes? No papel, a resposta é mais eficiente. A cada dia, sempre se perde algum tempo nas partidas e paradas dos processos. Isso incluiria mudanças de turno, problemas com ferramentas, almoços, limpeza e muito mais. Na verdade, os gerentes costumam admitir que ficam felizes em obter 50% do tempo efetivo de sua força de trabalho.
Portanto, se eu tiver a mesma quantidade de horários de início e término durante cada turno, mas tiver turnos mais longos, posso aumentar minha eficiência de trabalho. Aumentos de eficiência de 15-20 por cento são típicos ao mudar para turnos mais longos. No entanto, é importante garantir que alguma medida de produtividade esteja em vigor antes de fazer a mudança. A falta de tal medida leva invariavelmente à mesma quantidade de trabalho todos os dias durante menos dias.
Outra consideração no projeto de turnos é a parada e início de turnos ou execuções mais longas. Muitas vezes as coisas quebram quando você liga e desliga as máquinas, não quando elas estão apenas funcionando. Quantos carros quebram enquanto circulam em uma rodovia, em comparação com aqueles que não dão partida pela manhã? Ao projetar operações e manutenção, é fundamental levar isso em consideração, tanto na medição quanto na prática.
Também é importante não ser pego programando manutenções em torno do dia, da semana, do mês ou do ano. Por exemplo, se a manutenção do equipamento é necessária a cada 10 dias, realizá-la semanalmente para que possa ocorrer no mesmo dia de todos os anos pode ser muito cara. Um item sendo mantido semanalmente tinha 52 eventos de manutenção por ano. Isso representa 15 ciclos de manutenção a mais do que se fosse feito a cada 10 dias. Conseqüentemente, o custo adicionado seria 15 vezes o custo total de mão de obra e peças para cada ciclo.
Para itens caros, tanto em tempo quanto em materiais, pode valer um pouco mais de análise. A boa notícia é que a matemática por trás desse tipo de análise já foi feita. Se alguém tiver os dados, uma curva Weibull pode ser usada para calcular onde a manutenção deve ser concluída. Uma mina da Southwestern trabalhou com essa análise e, ao mudar conservadoramente seu padrão de manutenção de substituições de revestimento, economizou mais de US $ 600.000 por ano.
No final, bons gerentes de manutenção devem ter mais perguntas do que não. A maioria das programações é realmente uma “bola de band-aids” que foi desenvolvida ao longo do tempo. Imagine que, há alguns anos, houvesse um problema com as horas extras, então a gerência criou uma regra sobre como lidar com isso.
Hoje, as razões por trás dessa regra podem ou não ser válidas, mas a regra permanece, assim como as regras para fins de semana, rodízio de plantões, faltas por doença, absenteísmo e muito mais. Essas regras, que geralmente estão relacionadas a políticas de trabalho, remuneração e cobertura, podem ter efeitos dramáticos na força de trabalho e na capacidade de uma organização de atender à carga de trabalho necessária. Lembre-se de que o objetivo de qualquer bom cronograma é combinar a força de trabalho com a carga de trabalho.
Este artigo foi publicado anteriormente na Reliable Plant 2019 Conference Proceedings.
Manutenção e reparo de equipamentos
- A Evolução da Manutenção Industrial
- Compreendendo os benefícios da manutenção preditiva
- A Evolução da Prática de Manutenção
- A questão da manutenção do contrato - Parte I
- O poder de uma visão clara e concisa
- Posso interromper o cronograma de manutenção?
- Comportamento de sucesso das unidades de programação de manutenção
- Nas mentes da manutenção
- O poder de uma visão clara e concisa para melhorar os resultados de M&R
- O que afeta a frequência de manutenção do gerador a diesel