50 ideias para um programa de manutenção eficaz
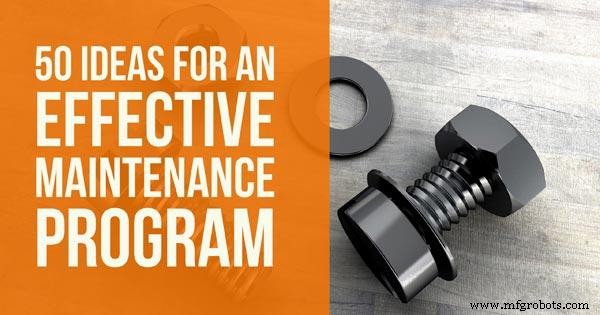
Quando um programa de manutenção é bem-sucedido, todas as áreas da empresa são afetadas positivamente. Hoje, as principais organizações estão colhendo os benefícios da implementação de programas de confiabilidade bem projetados e gerenciados. Você está pronto para levar seu programa de confiabilidade para o próximo nível? Aqui estão 50 ideias para você começar:
Aprenda os 12 elementos de um gerenciamento de confiabilidade eficaz. Certifique-se de que sua organização entende esses elementos importantes e o impacto que eles têm no desempenho - começando pelo topo. Sem esse foco de liderança para seu programa de manutenção, nada mais importa.
Rastreie as métricas de manutenção. Usando métricas e KPIs, as organizações de manutenção podem gerenciar com eficiência as atividades de manutenção e concentrar as iniciativas de melhoria na geração de valor.
Empregue planejamento e programação de manutenção. Com um planejamento eficaz, o trabalho pode ser concluído com o mínimo de interrupção das operações e o uso mais eficiente dos recursos de manutenção.
Considere um programa de confiabilidade orientado pelo operador. Sem a propriedade de seu equipamento nas mãos do operador, é difícil ser confiável. Usando uma abordagem bem planejada envolvendo todos os funcionários, a confiabilidade do equipamento terá um impacto direto e positivo em seus resultados financeiros.
Melhore os sistemas básicos de trabalho. Muitas organizações gastam muito tempo procurando por novos conceitos de confiabilidade e manutenção, e muito pouco tempo implementando e melhorando o que acabaram de começar.
Use sistemas de recompensa conjunta para gerar resultados. Se uma organização leva a sério uma integração mais estreita entre os departamentos, os sistemas de recompensas devem ser projetados para direcionar as ações e desempenho de todos em direção ao mesmo objetivo e recompensas.
Elabore seu plano de manutenção. Criar um plano de manutenção geralmente não é difícil de fazer. Mas a criação de um programa de manutenção abrangente e eficaz apresenta alguns desafios interessantes. o que faz a diferença entre um plano de manutenção normal e um programa de manutenção preventiva bom e eficaz.
Ouça seu equipamento. Você ouve seus motores reclamando de sobrecarga? Você vê suas embalagens de bomba anunciando uma enchente? Você ouve seus rolamentos reclamar de lubrificantes contaminados? Você percebe que seu sistema de vapor está tossindo condensado excessivo e reclamando de cotovelos tensos?
Pare de recompensar o fracasso. Os gerentes podem falar o dia todo sobre o desejo da organização de ser proativa, melhorar a confiabilidade, reduzir custos, etc. Mas as pessoas não prestam atenção ao que você diz; eles prestam atenção ao que você faz. Se você fala de “confiabilidade”, mas paga e reconhece o fracasso, adivinhe o que você receberá? O que é recompensado é feito, ponto final.
Almeje os 60 por cento. Em média, 30% de todas as atividades de manutenção preventiva não agregam valor e devem ser eliminadas. Outros 30 por cento dessas atividades poderiam ser substituídos por tecnologias de monitoramento de condição e uma abordagem de manutenção preditiva.
Vá all-in com monitoramento baseado em condições. Há pouco ou nenhum retorno em usar uma ou duas tecnologias de monitoramento de condição - ou aplicar CBM a uma pequena quantidade de seus ativos e esperar que evolua para um programa de sucesso.
Estime as horas de trabalho com mais precisão. A experiência mostra que as melhores estimativas de mão de obra estão rotineiramente erradas em até 100%. Um trabalho estimado em cinco horas de trabalho pode levar até 10 horas ou apenas duas.
Envolva os líderes certos. Os líderes de confiabilidade corporativa dizem que, se pudessem fazer tudo de novo, gastariam mais tempo escolhendo as pessoas certas para as principais posições de liderança. Com a liderança certa nas áreas certas promovendo as coisas certas, você tem sucesso.
Empregue uma abordagem multiferramenta para mais economia. A equipe de manutenção preventiva da American Axle and Manufacturing abordou um problema encontrado durante uma ordem de trabalho de manutenção preventiva de rotina usando várias ferramentas de monitoramento de condição.
Crie uma lista de equipamentos detalhada e precisa. Apesar do que você pode ter ouvido, a base de um programa de confiabilidade de sucesso é uma lista - uma lista de equipamentos detalhada e precisa, idealmente registrada em seu software CMMS. Ele contém as informações vitais de que você precisa para projetar, desenvolver e projetar seu programa de manutenção do zero.
Nunca aceite “bom o suficiente”. Em um processo de melhoria de manutenção, há várias áreas onde sempre há um desejo ou tendência de atuar o processo. Uma das ações mais importantes da liderança de manutenção e confiabilidade é esperar e definir o ambiente para permitir que toda a organização pratique “Good Enough Never Is” todos os dias.
Melhore os processos de trabalho. As práticas operacionais são uma parte vital de qualquer programa de manutenção preventiva. Boas práticas evitam falhas. Práticas inadequadas encorajam o fracasso. Este artigo discute exemplos de práticas de negócios que devem ser implementadas para melhorar a confiabilidade geral da planta.
Use as métricas corretas de manutenção preditiva. O que é medido é melhorado. Ou, inversamente, o que não é medido nunca será melhorado. O rastreamento e a geração de relatórios sobre as principais métricas permitem que você se concentre diretamente nas mudanças de comportamento que deseja.
Crie uma visão clara e concisa. Uma das primeiras responsabilidades da liderança é fornecer uma visão simples e clara de como o futuro pode e deve ser. Ter uma visão clara e concisa para melhorar sua planta é importante. Essa visão deve ser simples e visível.
Aprenda técnicas de análise de causa raiz. Quando surge um problema de confiabilidade, a maioria das organizações o aborda no nível sintomático ou procura imediatamente colocar a culpa em uma pessoa ou grupo. A análise da causa raiz é um processo sistemático para compreender e abordar as causas subjacentes de um problema.
Olhe, ouça, sinta, cheire. Independentemente de você estar fazendo inspeções com computadores portáteis ou um sistema de papel, pode tendências de dados ou não, ou ter indicadores-chave de desempenho ou não, você não terá sucesso a menos que seu pessoal possa fazer inspeções de qualidade nos equipamentos.
Decida sobre um modelo de equipe de lubrificação. A questão de quem em uma organização deve ser responsável pelas tarefas diárias de lubrificação do maquinário é comum. Aprenda as três estruturas organizacionais mais comuns e crie a sua própria.
Crie uma lista de pendências planejada. O primeiro princípio de programação de manutenção é o pré-requisito para ter uma carteira de pedidos planejada. Aprenda a preparar e usar um cronograma como padrão de controle para melhorar a produtividade da manutenção.
Use a análise de manutenção centrada na confiabilidade. Uma análise de manutenção centrada na confiabilidade deve ser vista como um exercício sério para o seu negócio. Uma análise RCM é um investimento que leva tempo, recursos e dinheiro para ser concluído, mas vale o esforço.
Implemente a manutenção produtiva total em 12 etapas. Implementar o TPM usando essas 12 etapas irá colocá-lo no caminho para “zero avarias” e “zero defeitos”. Alcançar 100% de confiabilidade exige disciplina e trabalho em equipe.
Saia da prisão do orçamento de manutenção. Se você está na prisão econômica e tentou escapar pregando confiabilidade para as pessoas acima de você, mas não fez muito progresso, aqui está um plano para ajudá-lo.
Aprenda o valor de “P”. O ponto P na curva P-F é onde um defeito entra na máquina. Em algum momento no futuro, isso causará algum tipo de perda funcional. À medida que um defeito persiste em uma máquina, a funcionalidade da máquina diminui com o tempo. Em algum momento no futuro, Ponto F, ocorre a falha total da máquina.
Crie uma lista de materiais do equipamento. Uma lista de materiais de equipamento lista todos os componentes de um ativo, incluindo seus conjuntos e subconjuntos. Com uma lista de materiais de equipamentos confiável, um planejador pode determinar exatamente quais peças são necessárias. E em uma emergência, ele fornece informações valiosas para artesãos e outros para garantir que as peças certas sejam identificadas e adquiridas.
Use intervalos P-F para mapear e evitar falhas. O intervalo P-F é uma informação valiosa para qualquer equipe de manutenção e você não precisa de educação especial para usá-lo. O uso de intervalos P-F para determinar a manutenção certa a ser realizada no momento certo não precisa ser confinado ao RCM.
Considere um sistema de monitoramento contínuo. O monitoramento contínuo é a aplicação de dispositivos dedicados para coletar dados de estilo de manutenção preditiva para auxiliar em um programa de monitoramento de condição. A cada ano que passa, essa tecnologia fica mais barata e o desejo por um monitoramento mais complexo e robusto fica maior.
Construa um forte relacionamento com as operações. Para melhorar a manutenção, você deve melhorar a construção de um relacionamento positivo com as operações. Para alcançar a excelência em manutenção, você deve ter um relacionamento excelente. Isso significa ter uma manutenção em total alinhamento com os objetivos maiores de suas operações e de sua empresa.
Quantifique o custo de um modo de falha funcional. Qual é o custo real de uma falha? Infelizmente, não sabemos até depois que a falha ocorreu - e confiabilidade significa evitar a falha.
Desenvolva procedimentos de manutenção padrão. As plantas freqüentemente deixam de ver a importância de ter procedimentos bem escritos para a maioria das tarefas. Este artigo discute a importância de ter bons procedimentos e apresenta os detalhes necessários para desenvolver procedimentos de manutenção padrão bem escritos.
Gerenciar ativos por criticidade. Por meio da construção adequada do modelo de análise de criticidade, a engenharia de confiabilidade será capaz de ilustrar quais aprimoramentos de confiabilidade devem ser feitos para gerenciar a criticidade, melhorando assim sua capacidade de gerenciar ativos por criticidade.
Ensine aos operadores o método “Deveria ser real dos cinco porquês”. Os operadores em uma cultura focada na confiabilidade devem ter uma atitude questionadora e ser muito observadores. A inclusão da ferramenta S-A-5Whys em seu conjunto de habilidades beneficiará a organização pela identificação e resolução antecipada de problemas, levando ao aumento da confiabilidade dos ativos.
Obtenha mais do seu EAM. Todos os sistemas EAM contêm os mesmos recursos básicos de suporte ao seu programa de manutenção. Eles são como qualquer outro pacote de software - seu sucesso depende de como são implementados e, mais importante, de como são usados.
Otimize interrupções com planejamento de tarefas eficaz. As interrupções podem ter cronogramas elaborados, mas geralmente não são bem-sucedidos devido ao planejamento avançado ineficaz, o que resulta em execução de trabalho ineficiente e atrasos no cronograma de interrupções. As interrupções só podem ser bem-sucedidas quando o trabalho de interrupção é planejado com eficácia antes de o trabalho ser agendado e / ou iniciado.
Coloque várias ferramentas CBM em uso. É essencial entender como o equipamento funciona em uma instalação e ser capaz de prever e prevenir falhas antes que elas aconteçam. Os resultados da combinação de tecnologias de monitoramento com base na condição darão ao engenheiro de confiabilidade uma confiança ainda maior ao se comunicar com a gerência quando um ativo estiver se aproximando de uma falha iminente.
Aplique as estratégias de manutenção corretas. A verdadeira confiabilidade é alcançada quando os métodos mais econômicos são aplicados aos ativos em sua planta, maximizando assim a confiabilidade com o mínimo custo total para o negócio.
Compare seu programa de lubrificação. O benchmarking fornece um scorecard muito necessário para áreas de lubrificação que podem não ser óbvias ou muitas vezes consideradas para melhorias. É verdade que “não sabemos o que não sabemos”.
Detecte problemas na máquina com antecedência. Essa lista enorme de itens de inspeção permitirá que você detecte problemas antecipadamente e, com sorte, elimine o tempo de inatividade e / ou reduza os custos de manutenção.
Remova os gargalos do processo. Se os gargalos do seu processo estão intimamente ligados à manutenção e confiabilidade do seu equipamento, é mais provável que você tenha uma organização de manutenção altamente reativa. Para sair de um regime basicamente reativo, um foco significativo deve ser colocado no desenvolvimento e implantação de sistemas que movam a organização em direção à proatividade.
Otimize as tarefas de PM. Infelizmente, a maioria das tarefas de manutenção preventiva não possui os detalhes que fornecerão dados quantitativos para o histórico do equipamento e são gravadas sem considerar os modos de falha. A solução é praticar a Otimização de Manutenção Preventiva (PMO), usando todos os aspectos para escrever procedimentos de PM que sejam de valor agregado, abrangentes, repetíveis, organizados e especifiquem uma duração e intervalo de execução corretos.
Crie um programa de análise de óleo enxuto e eficaz. A análise de óleo é uma ferramenta poderosa em um programa de manutenção. Este estudo de caso apresenta alternativas para equipamentos de teste internos caros, boa utilização de laboratórios externos, soluções de armazenamento de óleo, métodos de relatar descobertas para promover o programa e vender o programa para a alta gerência, bem como para operações e manutenção.
Use listas de verificação de manutenção. Embora a maioria dos grupos diga que tem listas de verificação, exigir seu uso e a responsabilização costumam ser os principais fatores para o sucesso. Em sua organização, quais processos você possui para garantir que as pessoas usem procedimentos de manutenção e listas de verificação?
Evite os 5 maiores riscos. O gerenciamento de ativos é uma abordagem integrada para otimizar o ciclo de vida de seus ativos, desde o projeto conceitual até o uso, descomissionamento e descarte. Ao reconhecer e prestar atenção a esses cinco riscos principais para o gerenciamento eficaz de ativos, você pode colocar em prática planos para mitigar os efeitos que eles podem ter em seu programa.
Conceda aos técnicos de manutenção a propriedade do equipamento. Como você consegue um equilíbrio entre propriedade de equipamento e desenvolvimento de habilidades por meio de treinamento cruzado, e ter a capacidade de fazer o trabalho o tempo todo? É baseado na cultura da organização?
Seja esperto quanto ao kit. Kitting para embarcações de manutenção para realizar suas tarefas é uma das maneiras mais fáceis e eficazes de permitir a conclusão de qualidade do trabalho com o mínimo de impacto na produtividade, especialmente quando acompanhado por um trabalho bem planejado e funcionalmente programado.
Trabalhe para zero falhas. Experiências e dados mostram que zero falhas são possíveis em um programa de manutenção. Como alguém disse uma vez:“Se você acha que não pode, provavelmente está certo. Se você acha que pode, provavelmente está certo. ”
Gerenciar o processo de mudança. O aspecto mais difícil, mas mais benéfico, de liderar um esforço de melhoria de manutenção e confiabilidade é gerenciar o processo de mudança nas organizações. O processo de mudança de comportamento de um estado reativo para um estado proativo é uma transição desafiadora para qualquer programa de manutenção.
Manutenção e reparo de equipamentos
- Cinco etapas para configurar um programa de manutenção preventiva eficaz
- Medindo o sucesso do programa de manutenção preditiva
- Hamilton Sundstrand fornecerá manutenção para a companhia aérea
- SMRP é valioso para profissionais de M&R
- Perguntas de manutenção preditiva respondidas
- Penske reconhecida pelo programa de treinamento de manutenção
- Como construir um programa de manutenção elétrica
- Gerenciamento de códigos QR para gerenciamento de instalações
- IoT para manutenção preditiva
- Como elaborar um programa de manutenção preventiva para seu equipamento