Uma maneira melhor de alocar e analisar o tempo de inatividade
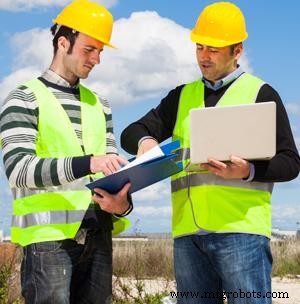
Lembro-me da seguinte discussão em uma reunião matinal em uma fábrica de celulose. Cerca de 50 toneladas de produção foram perdidas por causa de um vazamento em um cotovelo de um tubo de rejeição do atador secundário. O atador secundário é o último estágio da remoção de detritos grossos depois que a polpa deixa os digestores, onde os cavacos de madeira são transformados em polpa crua.
Superintendente de operações:"O tubo de rejeição é uma peça de equipamento mecânico, portanto, é um tempo de inatividade mecânico."
Superintendente de manutenção:"Desculpe, mas o cano se desgastou porque seus operadores têm trabalhado com as pilhas de cavacos muito baixas e colocado muito cascalho no sistema. Não foi projetado para isso. É falha de operação."
Operações:"Mas a razão para isso é que o transportador de cavacos para a pilha de cavacos continua quebrando, então a pilha ficou tão baixa que eles estão raspando o fundo e o problema do transportador de cavacos é definitivamente mecânico."
Manutenção:"O transportador quebra porque os operadores não estão mantendo a galeria do transportador limpa, e os fragmentos ficam presos sob os tambores e escorrem a correia. Isso é um problema de operação."
Operações:"Mas não podemos limpá-lo porque a linha de ar que fornece as lanças para soprar sob o transportador está enferrujada e não temos ar lá. Isso é mecânico."
Manutenção:"OK, qual é a ordem de serviço para consertar a linha de ar? Faremos isso amanhã."
Operações:"Ainda não enviamos uma ordem de serviço. Vou fazer isso agora."
A questão é que o tempo de inatividade é o tempo de inatividade, e o foco deve ser evitar que os problemas se repitam, não quem é o culpado. Discutir a culpa é um obstáculo à parceria de operações / manutenção. Esses argumentos são um resultado inevitável do processo de atribuição de culpa e serão muito mais frequentes (e barulhentos) se uma medição de "tempo de inatividade departamental" for um componente de um programa de incentivo, o que geralmente é.
Neste exemplo, um gerente prudente teria reconhecido que a causa raiz do problema era a falta de comunicação entre as operações e a manutenção, e uma falha em seguir a ordem de serviço / carteira / definição de prioridade / agendamento do processo. Se houver um programa de inspeção mecânica em vigor, ele também deve ser revisado, especialmente se estiver faltando problemas fundamentais como tubulação de serviço corroída.
Felizmente, existe uma maneira melhor. Em vez de atribuir culpas, uma abordagem muito mais positiva e produtiva é sempre tratar o tempo de inatividade como uma responsabilidade conjunta da parceria de operações / manutenção. Registre todas as perdas contra o equipamento ou evento que resultou no tempo de inatividade (por exemplo, Eq. No. 23-4567, No. 3 bomba de óleo quente ou entrega de matéria-prima atrasada por colisão ferroviária). Em seguida, atribua a responsabilidade pela ação ao departamento na melhor posição para iniciar e prosseguir para que o problema não ocorra novamente. Este departamento pode nem estar diretamente envolvido na operação do dia-a-dia.
Por exemplo, em uma fábrica de celulose onde um grande tubo de fibra de vidro falhou durante a inicialização, a causa raiz foi determinada como a falta de treinamento do operador no procedimento de inicialização correto. A responsabilidade foi atribuída ao departamento de engenharia para treinar os operadores nos fundamentos dos sistemas de bomba e tubulação e para desenvolver um procedimento operacional padrão para dar partida em cada bomba.
Após um grande evento de tempo de inatividade, freqüentemente a primeira ação necessária é conduzir uma análise de causa raiz. Isso pode envolver algumas pessoas com conhecimento ou exigir uma investigação extensa. Obviamente, os gerentes precisam garantir que as pessoas com responsabilidades de prevenção de problemas tomem as medidas necessárias. Se parte dessa ação for iniciar uma ordem de serviço para alguma manutenção preventiva ou corretiva ou redesenho, então também é necessário ter certeza de que o trabalho seja executado.
Se sua operação for qualificada sob a ISO 9000, incluindo manutenção fornece uma ferramenta para rastrear solicitações de ações corretivas (CARs) e solicitações de ações preventivas (PARs). Caso contrário, o uso de um campo "como iniciado" no banco de dados de ordens de serviço, onde um dos valores na lista suspensa é "investigação", permitirá que os gerentes se concentrem em todas essas ordens de serviço. O campo "motivo" pode ser usado para separar ainda mais as ordens de trabalho de "investigação" em segurança, operações, meio ambiente, etc.
Lembre-se de que nada de bom vem em atribuir culpas. Há valor em abordar problemas individuais, mas o melhor valor pode ser alcançado melhorando sistemas, como processos de negócios, de forma que a filosofia de prevenção de problemas se enraíze na cultura da organização.
Manutenção e reparo de equipamentos
- Software de planejamento de capacidade - planejar, analisar e preparar a capacidade
- Melhores maneiras de solucionar problemas de automação e loops de controle de processo
- Por que sua instalação precisa de um CMMS para aumentar a produtividade e evitar o tempo de inatividade
- Planejamento e execução da cadeia de suprimentos funcionam melhor juntos
- Oito dicas para manter sua máquina CNC funcionando melhor e por mais tempo
- 8 maneiras de prevenir o tempo de inatividade e ainda economizar dinheiro
- VFDs - Redução de ruído e conservação de energia
- Um design inspirado na aranha abre caminho para melhores fotodetectores
- Como reduzir o tempo de inatividade e aumentar a produtividade
- Circuito do amplificador do subwoofer:uma maneira completa de melhorar a qualidade do som