Compósitos 4.0:Transformação digital, produção adaptativa, novos paradigmas
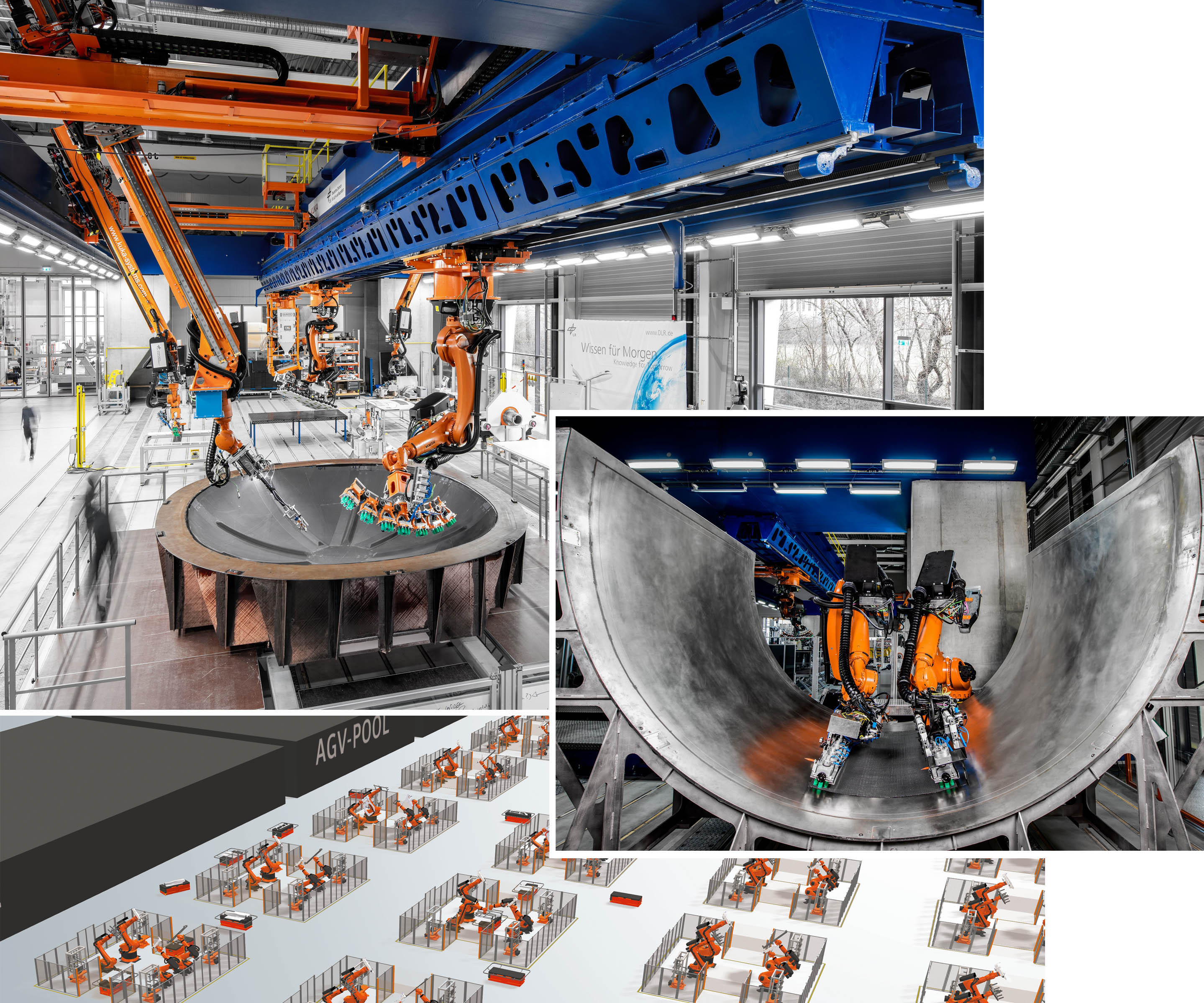
Composites 4.0 é uma pequena galáxia no universo da Indústria 4.0, que é a transformação digital em como bens e serviços são projetados, produzidos, entregues, operados, mantidos e desativados. Para a fabricação de compósitos, o objetivo é usar automação, sensores e dados, comunicações 5G, software e outras tecnologias digitais em constante evolução para tornar os produtos e processos mais eficientes, inteligentes e adaptáveis.
Os fabricantes de compósitos estão passando por essa transformação digital ao longo de um espectro. As etapas iniciais incluem inspeção em linha e processos otimizados que reduzem o desperdício e o custo, enquanto aumentam a qualidade e o rendimento das peças. Soluções mais avançadas trabalham em direção à produção autônoma e inteligente que não é apenas ágil, mas responde e até antecipa mudanças nos mercados e nas demandas dos clientes.
"Composites 4.0 não é um fim, mas uma ferramenta", explica o Dr. Michael Emonts, diretor administrativo do Centro AZL Aachen para Produção Integrativa Leve da RWTH Aachen University (Aachen, Alemanha), cujo projeto iComposite 4.0 demonstrou uma cadeia de processo adaptável com potencial para reduzir o custo de um piso automotivo em 50-64%.
“Há uma diferença entre apenas tornar as coisas digitais e a transformação digital que realmente muda os processos por trás do seu negócio e abre novas oportunidades e modelos de negócios”, afirma Christian Koppenberg, diretor administrativo da produtora de peças compostas Dynexa (Laudenbach, Alemanha).
“O Composites 4.0 não usa apenas robôs”, afirma o Dr. Michael Kupke, chefe do Centro de Tecnologia de Produção Leve do Centro Aeroespacial Alemão (DLR) (ZLP, Augsburg), que desenvolveu uma célula de trabalho equipada com inteligência artificial [IA] onde robôs colaborativos podem passar da produção de anteparos de pressão traseira compostos para painéis da fuselagem sem reprogramação ou retreinamento. “É a tecnologia que garante que você não precise ensinar os robôs, porque não há um business case para isso. Composites 4.0 é mais do que apenas aumentar a eficiência e reduzir custos. É uma mudança na forma como as empresas pensam e abordam a produção que determinará quais empresas sobreviverão e quais não ”.
Pré-formação adaptativa, RTM
“A ideia do projeto iComposite 4.0 era criar pré-formas a partir de mechas econômicas e reboques, combinando fibra de vidro longa e seca (25-30 milímetros) pulverizada e posteriormente reforçada com uma grade de fibras de carbono unidirecionais (UD) por meio de colocação automática de fibra (AFP) ”, explica Emonts. “O demonstrador escolhido, um painel traseiro sob o piso do veículo, era feito anteriormente com tecidos mais caros, que também produziam mais de 60% de resíduos.”
A transformação de Compósitos 4.0 exigiu a integração dos processos de pulverização de fibra, deposição de fibra e subsequente moldagem por transferência de resina (RTM) para que reagissem entre si e se adaptassem com base na qualidade da peça medida entre as etapas (Fig. 1). “Usamos um sistema de visão mecânica da Apodius GmbH [Aachen, Alemanha] com um sensor óptico de laser e um módulo de câmera para caracterizar a topologia de superfície da pré-forma pulverizada”, diz Emonts. “A Apodius adaptou o software para analisar a porcentagem de fibras em cada direção. A linha iComposite 4.0 comparou isso ao design digital e decidiu se atendia aos requisitos mecânicos. Em caso afirmativo, aplicou a grade UD padrão para reforço. Se não, ele decidiu onde colocar camadas de fibra UD adicionais. ”
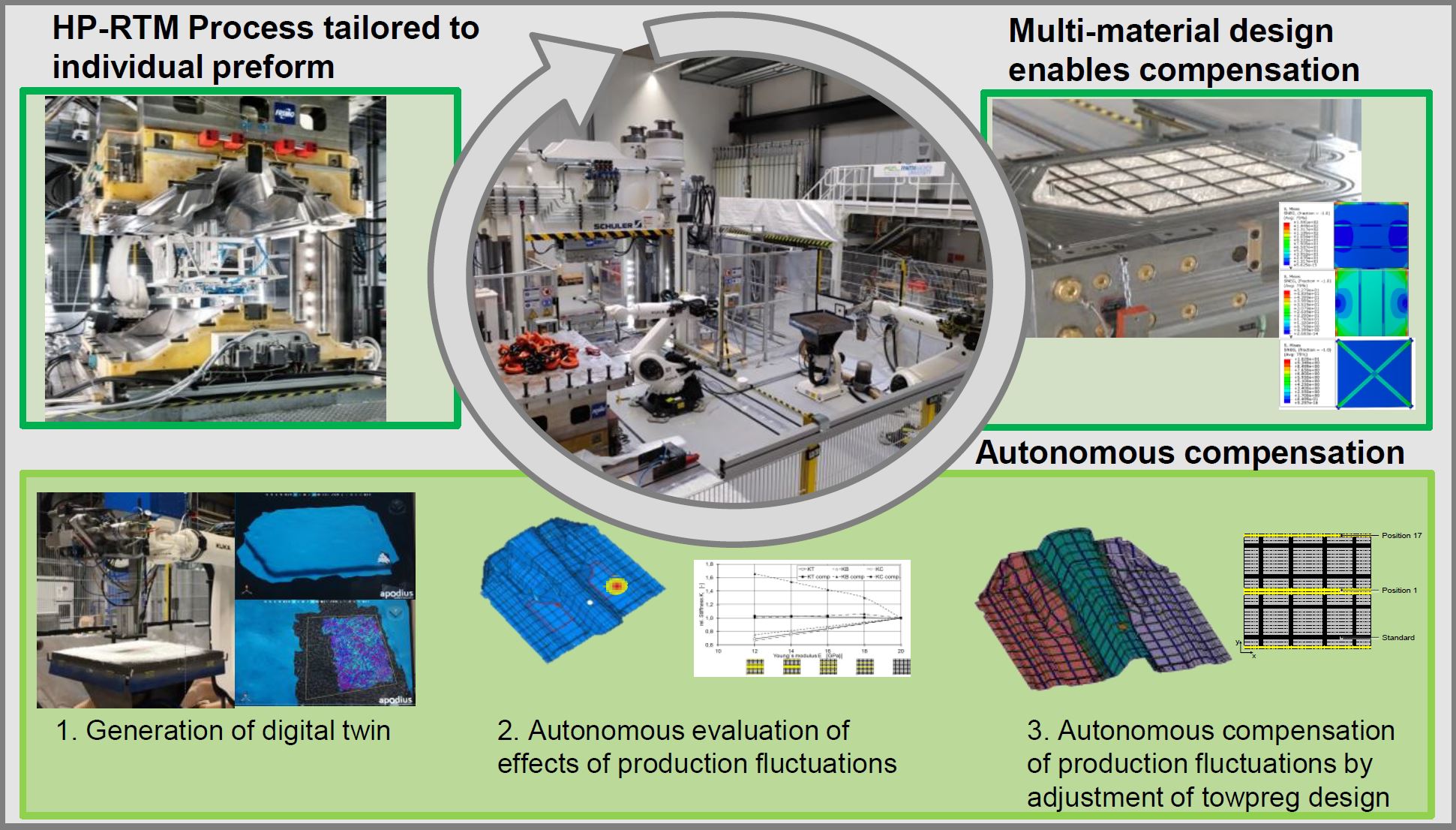
No entanto, essas camadas UD adicionais podem fazer com que a espessura e a geometria da peça excedam as tolerâncias. “Portanto”, explica ele, “combinamos a linha de pré-formação com um processo RTM adaptativo que, se necessário, ajustava a espessura da peça aumentando a pressão em certas partes da prensa”. Isso também foi automatizado, com o objetivo de substituir a intervenção do operador de linha, mas exigia a simulação do desempenho da peça usando dados de medição e software FEA padrão.
“Atualmente, a simulação das propriedades mecânicas da peça é realizada offline”, diz Emonts. “Geramos um banco de dados de variações de processos e peças, criamos algoritmos para reagir a cada variação e os validamos via FEA. Assim, com base nas variações medidas pela linha, os algoritmos a direcionaram para realizar uma mitigação adequada. Para tornar a linha adaptável in-situ, a próxima etapa seria adicionar o aprendizado de máquina. ” Enquanto isso, a AZL está buscando vários projetos de Composto 4.0, incluindo a produção auto-otimizada de compostos termoplásticos híbridos e peças moldadas por injeção com reforço integrado de peças em branco personalizadas baseadas em fita.
Peles de asas CFRP com defeito zero
O projeto ZAero (consulte “Fabricação de peças compostas com zero defeitos”) é outro projeto-chave da Composites 4.0, que começou em 2016. O objetivo era aumentar a produtividade de grandes estruturas de plástico reforçado com fibra de carbono (CFRP), como as asas. Os defeitos seriam reduzidos usando a inspeção automatizada em linha com prepreg AFP ou Danobat (Elgoibar, Espanha) colocação automatizada de material seco (ADMP, consulte "Provando a viabilidade de tecidos secos, infusão para grandes aeroestruturas"). O monitoramento do processo durante a infusão de resina ou cura pré-impregnada poderia prever o estado de cura e reduzir o tempo de ciclo. Os dados de processo e defeito coletados foram usados com a FEA para prever o desempenho da peça. Isso foi então inserido em uma ferramenta de suporte à decisão sobre como lidar com os defeitos identificados. Foi desenvolvida uma simulação de fluxo parcial para wingskins de CFRP que, quando inserida nesta ferramenta, ajudou a otimizar uma estratégia de retrabalho (Fig. 2). Hoje, muitas dessas peças são retrabalhadas durante a fabricação, mas somente após o NDI. Retrabalho anterior e controle de processo aprimorado eram de fato objetivos do projeto ZAero, bem como capacitadores para seu aumento de 15% na taxa de produção e redução de 15-20% em custo de produção e 50% menos desperdício.
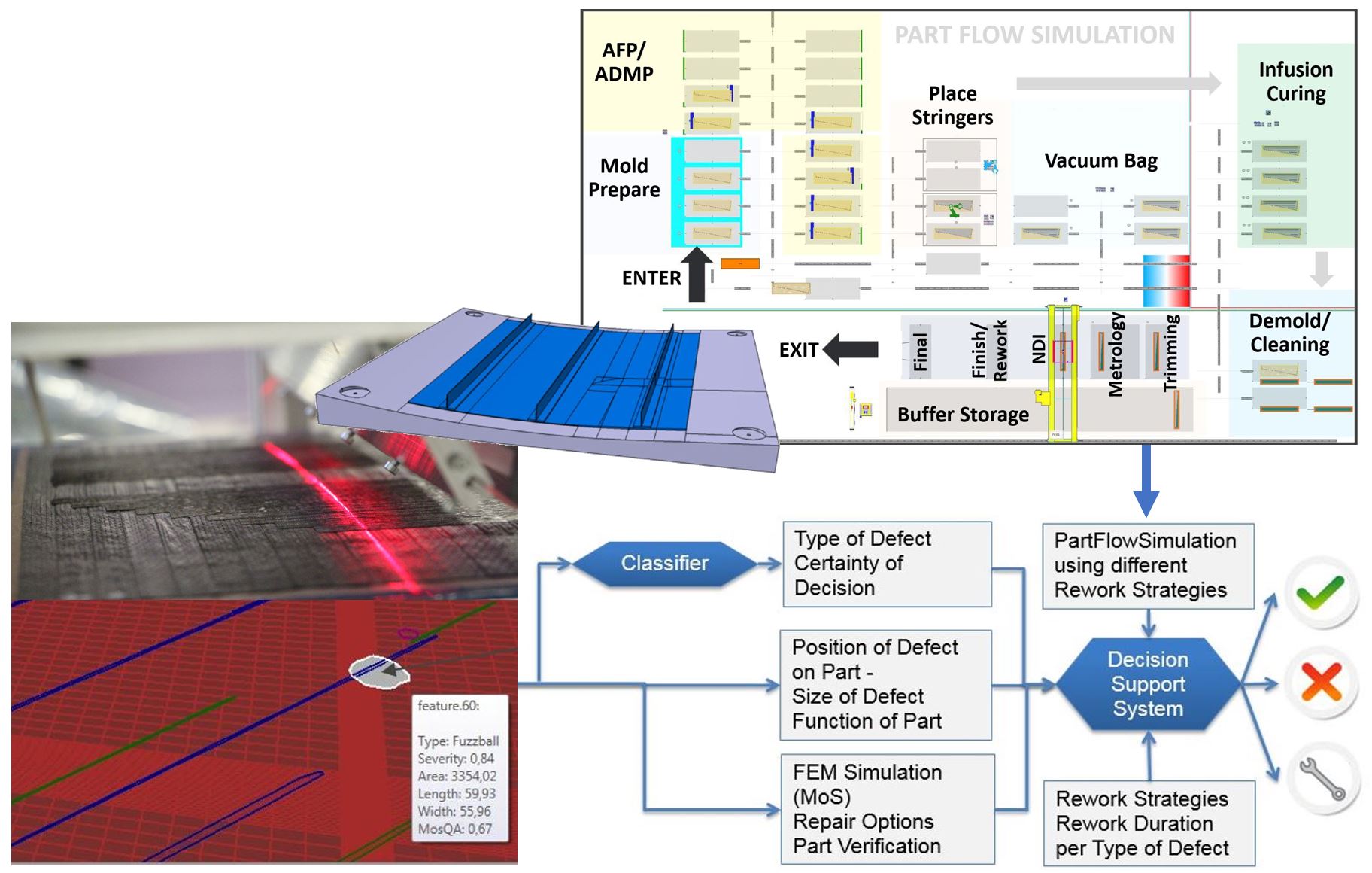
Na revisão final de setembro de 2019, o sensor AFP pré-impregnado desenvolvido pelo líder do projeto Profactor (Steyr, Áustria) não apenas alcançou a inspeção automatizada em linha, mas também pode ser usado para corrigir peças no local. “Este sensor pode detectar os defeitos padrão, como lacunas, sobreposições, FOD, fuzzballs e reboques torcidos, bem como corte antecipado e tardio de cada reboque”, disse o Dr. Christian Eitzinger, chefe de visão mecânica da Profactor. Um reboque ausente pode ser corrigido automaticamente com a colocação de um reboque adicional exatamente onde foi omitido. A máquina deve ser parada, no entanto, para remover bolas de pelo ou um reboque torcido. “Um banco de dados construído usando a experiência 3D da Dassault Systèmes (Paris, França) para CATIA nos permite calcular os efeitos no desempenho da peça com base no tamanho, forma e tipo de defeito. O processamento de todos os defeitos em uma camada leva apenas alguns segundos. O operador da máquina então decide quais defeitos podem ser deixados e o que deve ser retrabalhado. ”
Para monitoramento e controle do processo de infusão, a Airbus (Toulouse, França) trabalhou por meio da subsidiária InFactory Solutions (Taufkirchen, Alemanha) para desenvolver três sensores que medem a temperatura, o estado de cura e a frente de fluxo de resina (consulte “Sensores para monitorar a frente de fluxo de infusão de resina”. ) “Nós os integramos ao CATIA 3D Experience e mostramos que os dados podem ser adquiridos de forma confiável e adicionados à rosca digital de cada peça”, diz Eitzinger. (Consulte a barra lateral online “Compostos 4.0:Digital thread vs. digital twin”.)
O final dos demonstradores de três partes foi uma subseção da cobertura da asa superior com três longarinas (veja a barra lateral online “Atualização do projeto ZAero”). Para esta parte, a ferramenta de suporte à decisão da Profactor foi demonstrada ao vivo no parceiro FIDAMC (Madrid, Espanha), conectada à simulação de fluxo parcial - com base no software Siemens PLM (Plano, Texas, EUA) Tecnomatix Plant Simulation - rodando no servidor Profactor na Áustria. Além de construir um banco de dados de defeitos, a ZAero conduziu experimentos com aprendizado de máquina. Modelos de computador geradores projetados manualmente combinados com redes neurais profundas detectadas e classificadas de defeitos, alcançando uma taxa de 95% de classificação correta de diferentes regiões (lacuna, sobreposição, reboque, bola fuzzball) em dados de monitoramento ADMP reais, mesmo quando dados de defeitos criados artificialmente foram usados para o treinamento de rede profunda (análogo a como os sistemas de teste ultrassônico são calibrados em uma variedade de defeitos deliberados).
“Definitivamente buscaremos algum tipo de próxima fase”, diz Eitzinger. Enquanto isso, a Profactor está comercializando sensores modulares para orientação de fibra e defeitos durante layup automatizado. A InFactory Solutions também está oferecendo seus sensores de infusão de resina e AFP, e os parceiros de colocação de fibra Danobat e MTorres (Torres de Elorz, Navarra, Espanha) estão agora vendendo seus equipamentos com inspeção em linha integrada.
Jornada de transformação digital da Dynexa
Dynexa é um fabricante de peças compostas especializado em tubos e eixos CFRP. “Sempre tentamos digitalizar tudo”, diz o diretor Koppenberg. “Já nos livramos dos processos manuais e analógicos, integrando tudo principalmente em nosso sistema ERP [planejamento de recursos empresariais]. Mas como fazemos isso na manufatura? Entendemos que tudo o que colocamos em um protocolo ou procedimento de trabalho é um código e esta é uma base para a transformação digital. Mas onde está armazenado? Em um servidor local, na nuvem ou dentro da máquina? Perguntaríamos a cinco pessoas e obteríamos sete respostas sobre o que deveríamos fazer. ” (Consulte a barra lateral online, “Compostos 4.0:Por onde começar?”)
Felizmente, o governo alemão criou um programa para as universidades para fornecer consultoria gratuita da Indústria 4.0 para pequenas e médias empresas (PMEs). A Dynexa começou a trabalhar com o Centro de Competência Darmstadt “Mittelstand (SME) 4.0”. “Eles disseram para não se preocupar com a arquitetura digital, mas olhar mais para o que você precisa medir e como fazer isso”, lembra Koppenberg. “Escolhemos um processo que envolvia medição manual significativa, onde sabíamos que tínhamos problemas de qualidade, tempo e custo.”
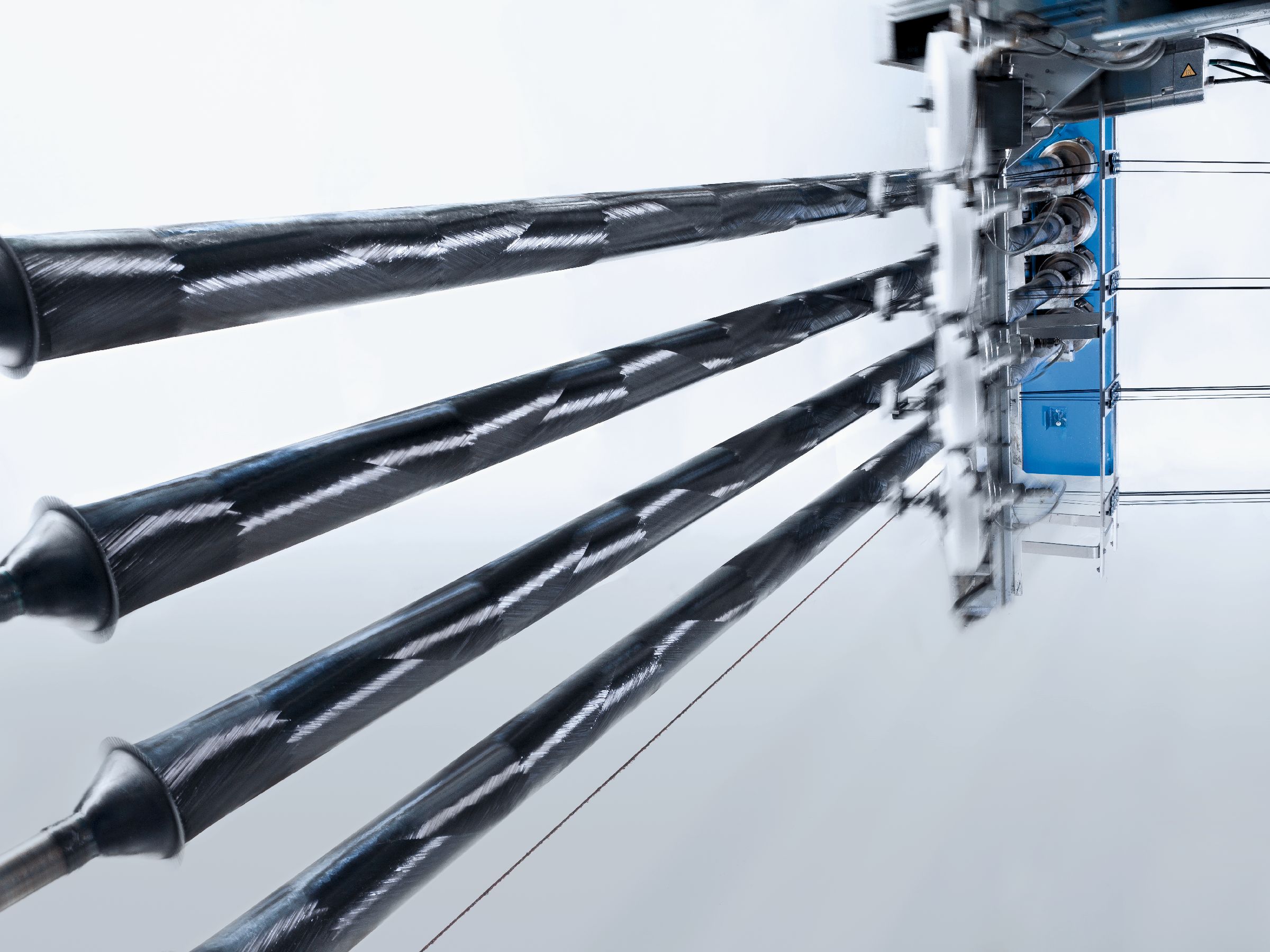
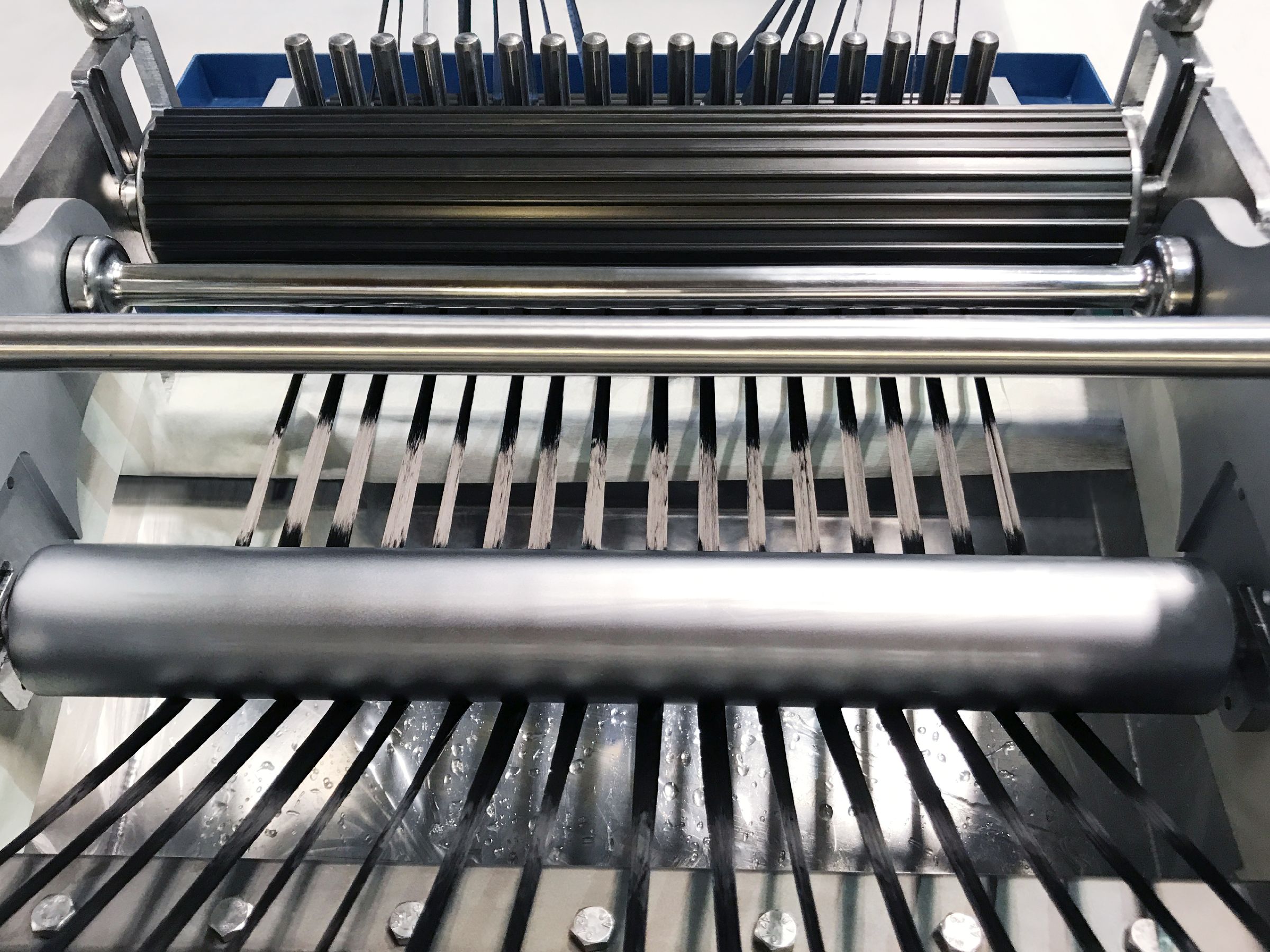
Dynexa usa um processo de enrolamento de filamento úmido. (Consulte “Eixo de saída composto pronto para campo de provas automotivas.)” Uma etapa importante é a coleta da resina, onde a fibra seca é passada para um rolo de compactação que sai do banho de resina. Contra o rolo de compactação está uma lâmina raspadora que determina a quantidade de resina a ser combinada com o filamento seco antes de ser ferido. “Se pegarmos muita resina, podemos exceder o diâmetro do tubo especificado”, diz Koppenberg, “mas com pouca resina, corremos o risco de cair abaixo do diâmetro mínimo permitido.”
“Sem medir, você só sabe o diâmetro final após a cura, quando todo o valor foi investido”, destaca. “Então, o operador deve parar a máquina, medir a peça, anotar e depois reiniciar. Com anos de experiência, sabemos qual deve ser a espessura do laminado em cada estágio do enrolamento. Assim, o operador compara a medição e ajusta a lâmina raspadora para corrigir a coleta de resina conforme necessário, mas isso é muito manual e depende da habilidade e experiência do operador. ”
Para digitalizar isso, a Dynexa conversou com uma miríade de fabricantes de câmeras e laser. “Eles diziam:‘ temos a solução ’, mas ninguém conseguia fazer com que funcionasse”, observa Koppenberg. A equipe da Universidade de Darmstadt, no entanto, permitiu o uso de uma câmera descobrindo as correções necessárias devido a certos fatores físicos, como o reflexo da luz na superfície molhada. “Agora, temos a bobinadeira conectada ao medidor, que funciona de forma bastante padronizada”, acrescenta.
A equipe desenvolveu um banco de dados de tabelas de correção e algoritmos de decisão que permitem à máquina de enrolamento de filamento saber qual deve ser o alvo para cada estágio do tubo específico sendo enrolado. “Se a entrada do dispositivo de medição mostrar que a coleta de resina não está onde deveria estar”, explica Koppenberg, “a máquina de enrolamento de filamento responde ajustando a lâmina raspadora para trazê-la de volta às especificações sem parar o enrolamento para medir.”
Cada bobinadeira agora tem o sistema de medição digital, e uma placa Ethernet. “A parte mais cara foi instalar e passar os cabos para o servidor”, brinca Koppenberg, “mas agora podemos falar com cada máquina e coletar todos os dados”. E há outro benefício. “Antes, os operadores programavam nas máquinas, mas assim que os conectamos ao servidor, podemos programar em qualquer desktop ou laptop. Isso reduziu ainda mais o tempo de inatividade e removeu outro gargalo de produção ”.
Esta primeira etapa digital permitiu à Dynexa melhorar seu controle de processo, qualidade e eficiência, tornando-se mais econômica. Ele também estimulou outras transformações.
Mudança de paradigmas para compostos
“Estamos em um processo gradual de fornecer um novo ecossistema para nossos clientes”, diz Matthias Bruckhoff, chefe de vendas e marketing da Dynexa. Ele dá um exemplo:“Na Amazon, você pode ver o que comprou e quando, além de sugerir novos produtos. Costumávamos pegar os requisitos do cliente e responder em alguns dias usando nossos cálculos e ferramentas de engenharia. Agora, isso estará online. Nossos clientes irão olhar para os produtos e calcular o que precisam, custo e entrega em questão de minutos. Isso não é novo, mas é para a nossa indústria. Assim como liberamos nossos operadores de máquina para se concentrar em mais máquinas e tarefas de nível superior, agora vamos liberar nossa equipe de engenharia para se concentrar em produtos mais especializados e sofisticados. ”
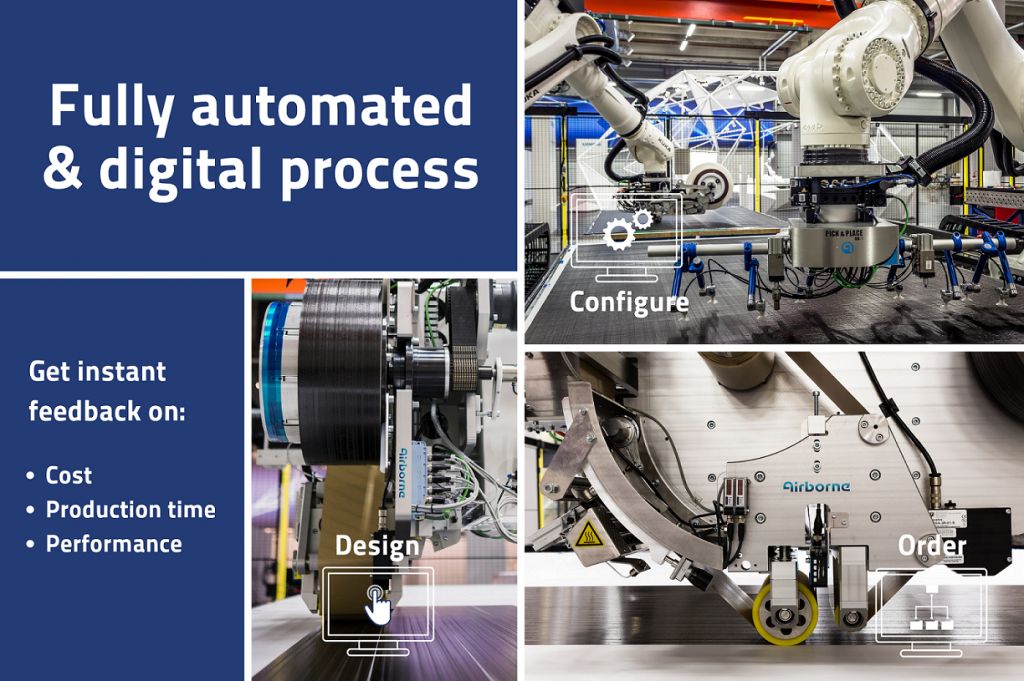
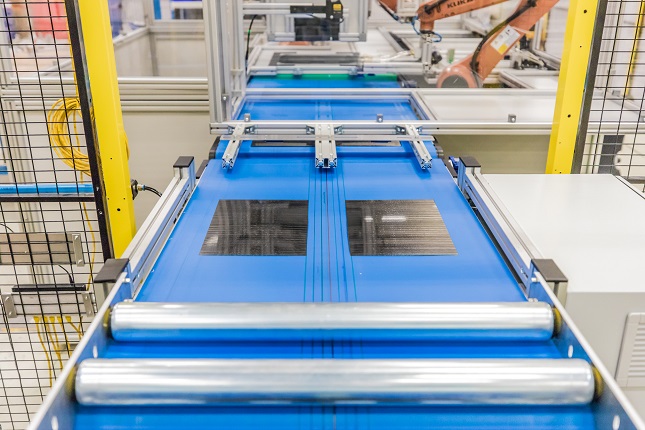
A Airborne (Haia, Holanda) lançou seu Portal de Fabricação sob demanda para fabricação automatizada de compósitos em setembro de 2019 (consulte “Airborne lança portal de impressão de compósitos”). Usando essa ferramenta, os clientes inserem designs na plataforma baseada na web. O sistema então cria o código de máquina em tempo real e determina a duração e o custo da produção. Os produtos podem ser personalizados e, uma vez solicitados, produzidos em uma célula de manufatura automatizada. O portal foi lançado usando o Automated Laminating Cell (ALC) da Airborne para processar prepreg termofixo. Será estendido a outros processos, por exemplo, a linha de produção de compósitos termoplásticos de alto volume (TPC) desenvolvida para a unidade de negócios Especialidades da SABIC (Riade, Arábia Saudita).
“Este portal é um alicerce fundamental de como vemos o futuro digital da manufatura de compostos”, disse Marcus Kremers, diretor de tecnologia da Airborne. “Cinco anos atrás, mudamos de um modelo de negócios de fabricação de peças para ajudar os clientes com automação e digitalização. Estamos desenvolvendo um portfólio de soluções que tornam mais fácil para os clientes construir com compostos. ” Este portfólio inclui o ALC, envasamento automatizado em forma de favo de mel, kit de dobras automatizado e a linha de alto volume usando fitas TPC, denominada Digital Composites Manufacturing Line (DCML) pela SABIC e Falcon pela Airborne. Este último é um exemplo das soluções personalizadas da Airborne. “Estamos incorporando nossos materiais compostos e conhecimento de fabricação de peças nesses sistemas automatizados para que os clientes não precisem ser especialistas”, diz Kremers.
A Airborne possui três modelos de negócios:comprar a automação, alugá-la ou deixá-la com a Airborne para operar via manufatura como serviço (MaaS). As células automatizadas aerotransportadas possuem sensores e sistemas de inspeção em linha que geram alertas com base em um banco de dados de defeitos e tolerâncias definidas pelo cliente. “A linha Falcon tem tolerâncias muito baixas para defeitos de qualidade visual”, observa Kremers, “mas nossa automação para aeroespacial é mais orientada por tolerâncias estruturais. Também estamos continuamente avançando em nossas tecnologias para que sejam de autoaprendizagem e autoadaptação. Por exemplo, nossa próxima versão de software para colocação de fita ALC terá a capacidade de identificar defeitos e corrigir o programa de produção em tempo real. ”
A longo prazo, a visão é expandir o portal sob demanda para coletar a capacidade de produção de peças compostas distribuída por várias empresas e regiões. Kremers cita a Protolabs (Maple Plains, Minn., U.S.), que fornece protótipos moldados por injeção, chapas de metal, usinados em CNC ou impressos em 3D sob demanda em apenas um dia. Da mesma forma, o aplicativo online da Plyable (Oxford, Reino Unido) fornece moldes para a fabricação de compostos, oferecendo materiais que vão desde placas de poliuretano até aço, incluindo ferramentas compostas e impressas em 3D. “Essa é uma maneira diferente de organizar a cadeia de valor”, diz Kremers. “Estamos fazendo as máquinas e o software que tornarão isso possível para peças compostas.”
A AZL Aachen também está buscando esse objetivo com sua Ultra-Fast Consolidator Machine, desenvolvida para produzir laminados TPC multicamadas em menos de cinco segundos. Comercializado em 2019, ele usa aplicadores robóticos AFP assistidos por laser da Conbility (Aachen, Alemanha) e fitas UD de 25 milímetros de largura, bem como um princípio de fluxo de peças - estado da arte na indústria de impressão de alta velocidade - para produzir laminados TPC, simplesmente aderidos ou totalmente consolidados, em diversas espessuras, com reforços locais. “Nossa visão é fornecer máquinas escaláveis que permitirão plataformas online”, diz Emonts. “As linhas podem ter várias estações, cada uma com vários aplicadores AFP. O cliente irá inserir os requisitos e obter opções de plybook, custo e entrega. Uma vez finalizado, os aplicadores se comunicam entre si para organizar a produção, não com o operador. Esta é uma produção completamente inteligente de compostos sob medida. ”
Automatizando a automação
O foco principal do ZLP é a produção automatizada de estruturas CFRP. “A automação para apenas uma peça ou programa é difícil de justificar”, observa Florian Krebs, líder da equipe ZLP para automação flexível. “No entanto, se você ir além das máquinas com tarefas específicas para uma plataforma de automação que é reconfigurável quase sem configuração adicional, agora você tem uma solução de negócios. Quanto mais flexível for a plataforma, mais rápido será o retorno do investimento ”.
A célula de trabalho mostrada nas imagens de abertura foi projetada como parte do projeto ZLP PROTEC NSR para construir uma família de peças que segue a mesma rota de processo:arranjo pick-and-place de tecidos não crimpados e infusão de resina (ver barra lateral online “Não business case para o ensino de robôs ”). “Este processo foi projetado para a antepara de pressão traseira do Airbus A350, mas você também pode fazer um painel da fuselagem ou uma tampa de asa nesta linha porque as etapas são semelhantes”, diz Krebs.
“Alcançar plataformas de automação flexíveis requer certos tijolos de tecnologia, incluindo algoritmos para os robôs, bem como sensores e como entender os dados que eles produzem”, diz Kupke. “Por exemplo, a linha de produção PROTEC NSR é projetada para a modularidade máxima - todos os módulos interconectados entre si para demonstrar um sistema de autoconfiguração, correção e otimização, escalonável em tamanho e complexidade.”
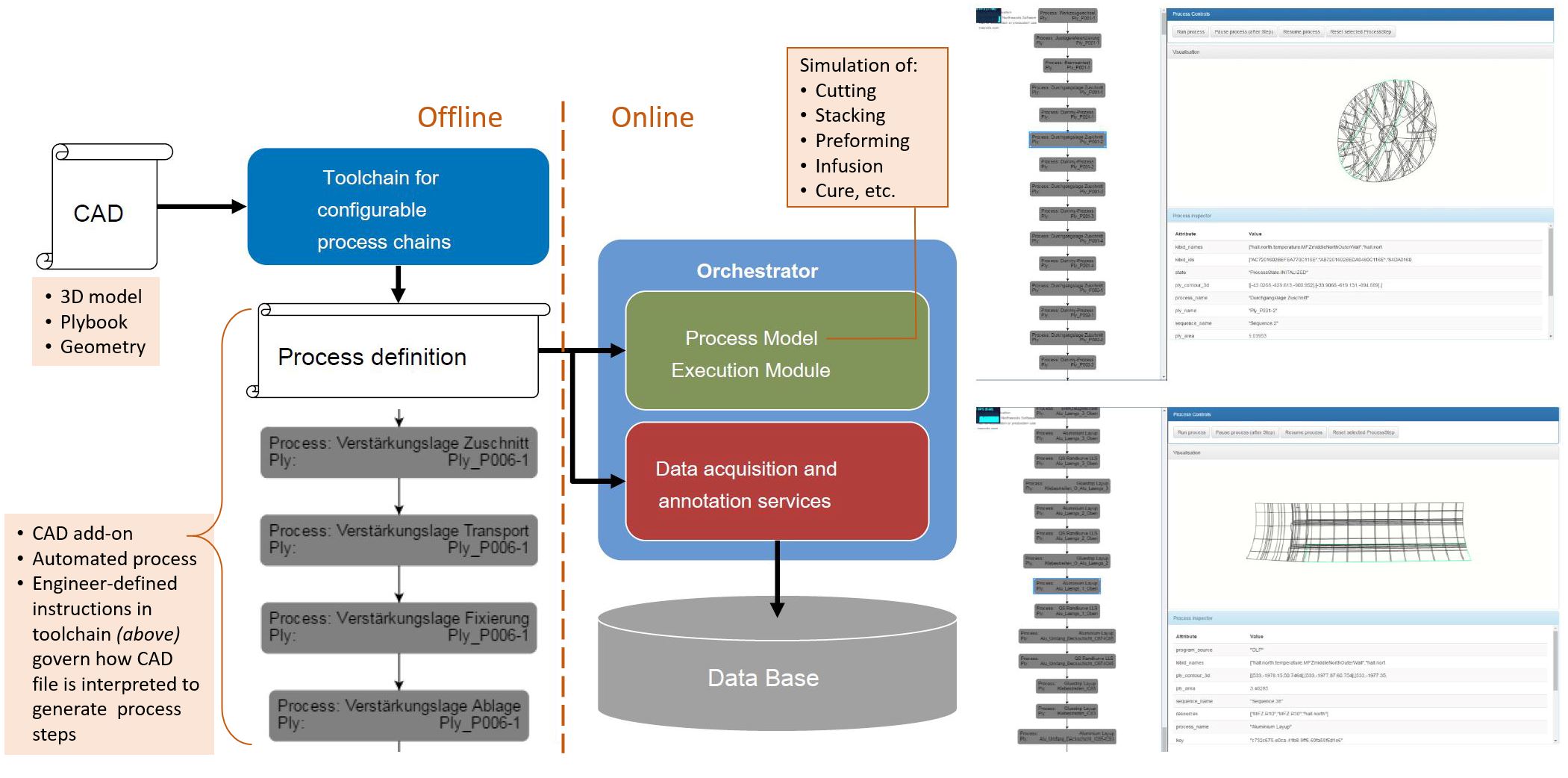
Ele explica os módulos mostrados na Fig. 5, que incluem modelo CAD, definição do processo, modelo do processo que permite a simulação e execução do processo, módulo de execução da manufatura, sensores para adquirir dados, software para anotar os dados e banco de dados para armazenamento.
“No lado esquerdo deste diagrama, você faz um plano. O módulo de execução então implementa esse plano ”, diz Kupke. “Durante as etapas do processo, adquirimos dados de todas as máquinas e processos envolvidos, por exemplo, o cortador, os robôs, o edifício (temperatura, pressão, umidade), as câmeras durante a coleta e colocação, etc. Analisamos os dados em tempo real durante o processo e também anotar os dados coletados automaticamente com metadados para alimentá-los no banco de dados, que forma a base para o gêmeo digital do processo. O ponto mais importante do gêmeo digital é ter um repositório central, uma fonte de verdade. O modelo CAD de cada parte e a definição do processo são parte de sua única fonte de verdade. ”
Com esses módulos instalados, a linha opera de forma autônoma com o toque de um botão. A partir do modelo CAD, plano de produção e câmeras, os robôs inferem qual peça cortada vem a seguir e procuram por ela na mesa (por exemplo, de 100 outras peças cortadas). “Eles decidem como configurar as garras para pegá-lo e colocá-lo na ferramenta e sabem onde colocá-lo.” Com base no plano de produção, os robôs determinam cada caminho inicial / final para todas as etapas do processo e sabem quando cada uma é concluída. “Normalmente, esses caminhos são ensinados por um humano”, observa Kupke. “Mas em nosso sistema, cada caminho é definido automaticamente, sem colisões e em tempo real. Se você alterar o modelo CAD ou a definição do processo, os robôs se adaptarão sem nenhum esforço adicional de ensino. Mas e se você mudar a peça completamente? Com esse tipo de automação, você pode fazer essa mudança muito rapidamente. Este é o caminho para a produção flexível. Nosso papel na ZLP é abrir esse caminho desenvolvendo tijolos de tecnologia e conectando-os. ”
Oportunidade e ontologia
A pandemia COVID-19 destacou o valor da produção flexível. Também criou um ambiente de negócios cada vez mais imprevisível. “Nos últimos dois a três anos, tudo ficou mais volátil”, observa Bruckhoff da Dynexa. “Nossos clientes querem respostas muito rápidas, a fim de responder aos seus clientes. Ao oferecer nosso novo ecossistema online, tornamos toda a cadeia de suprimentos mais competitiva. ”
Isso é bem conhecido pela indústria da aviação. “Precisamos de uma base digital para linhas de produção e sites inteiros que possibilitem a integração horizontal e vertical”, disse Marc Fette, presidente da Divisão Técnica de Tecnologias Aeroespaciais da VDI - Associação Alemã de Engenheiros e COO para Centro de Tecnologia de Compostos (CTC, Stade, Alemanha), uma subsidiária de R&T da Airbus. Os projetos CTC em Composites 4.0 incluem rastreamento de materiais e ativos, robôs colaborativos, cadeias de processos avançados e muito mais. Mas Fette enfatiza a necessidade de ontologia - uma terminologia e protocolo comum para comunicação digital e troca de dados. (Consulte a barra lateral online “Arquitetura e ontologia de compósitos 4.0”.)
“Você precisa de uma rede holística para todas as máquinas e sistemas de produção em uma determinada fábrica”, explica ele, “mas isso também deve se estender a toda a cadeia de criação de valor, incluindo disciplinas como engenharia, compras, logística e certificação de materiais e processos , por um lado. Por outro lado, todos os stakeholders, como os fornecedores, devem ser considerados e envolvidos neste processo de mudança. Vemos muitos projetos-piloto, mas quando você olha em detalhes, ainda falta uma estratégia para uma abordagem holística por empresa ou cadeia de produção. ”
Ele continua:“Temos uma rede global muito grande de fornecedores e eles têm os mesmos requisitos para operar como uma cadeia de suprimentos conectada digitalmente. A maioria de nossos fornecedores são PMEs que trabalham para fabricantes de aeronaves, Airbus e Boeing. Se não houver discussão sobre um padrão comum, você repassa esses desafios aos fornecedores. Eles provavelmente não podem se dar ao luxo de cumprir dois conjuntos de padrões diferentes para todas as suas máquinas, incluindo documentação, avaliação de dados, segurança cibernética, etc. ”
Fette admite que essas são grandes ideias e diz que os OEMs de aeronaves estão criando planos para enfrentar esses desafios. “Mas existem muitos obstáculos como este, e é realmente complexo, envolvendo não apenas tecnologia, mas questões sociais, econômicas, ergonômicas e legais - é um processo de mudança mental. Estamos apenas no começo. Mas para ter sucesso, devemos entender que esses novos sistemas dependem de pessoas e essas pessoas devem estar a bordo, não apenas em OEMs, mas em toda a rede global. ”
“Os mercados estão se tornando mais fragmentados em todas as indústrias e todos estão enfrentando uma mudança de paradigma”, observa Krebs da ZLP. “Muitas pessoas não veem isso como uma oportunidade”, acrescenta Kupke, também da ZLP. Mas aqueles que veem essa oportunidade vislumbram o acesso democratizado aos compósitos habilitado pelo Composites 4.0 e, com isso, um mercado muito mais amplo, incluindo aplicações que estamos apenas começando a conceber.
Resina
- Otimizando a transformação digital na manufatura de CPG
- Estratégia de transformação digital exige abordagem de novos talentos
- Transformação digital orientada por dados impulsiona o Airbus a novas alturas
- Como a nova era da transformação digital está mudando o setor de serviços públicos?
- Evonik construirá nova unidade de produção PA12
- Planeje o sucesso na transformação digital
- O que é transformação digital na manufatura?
- 7 Motores da Transformação Digital
- Desafios da Transformação Digital na Manufatura
- Transformação da manufatura digital:uma resolução de ano novo