Práticas recomendadas de operações de depósito:55 dicas e táticas incríveis para melhorar o gerenciamento, a organização e as operações de depósito
Os gerentes de depósito sabem muito bem que a tarefa de gerenciar as operações de uma instalação de depósito está longe de ser simples. Os gerentes de operações do armazém têm a tarefa de garantir o fluxo eficiente de produtos dentro e fora das instalações, otimizando o layout do edifício, garantindo que os pedidos sejam atendidos e os produtos estejam em estoque, mas não em excesso. Adicione a garantia de lucratividade e a minimização dos custos indiretos e de mão de obra ao mix, e os operadores de armazém terão seu trabalho cortado para eles.
Com tantos fatores para equilibrar, considerações a pesar em cada decisão e pressão das partes interessadas de todos os lados para ser mais produtivo, minimizar despesas e manter um fluxo de cadeia de suprimentos suave, não é surpresa que existam muitos artigos e recursos descrevendo as melhores práticas para operações de armazém.
Para analisar a vasta gama de informações sobre as melhores práticas de operações de armazém, reunimos uma lista relativamente concisa de práticas recomendadas de várias fontes. Vasculhamos os cantos mais distantes da web para identificar essas 51 práticas recomendadas para operações de armazém para fornecer um recurso útil para gerentes de armazém que desejam ter o melhor desempenho em seu campo e produzir os melhores resultados possíveis para suas empresas. Embora categorizado por tópico, observe que as práticas recomendadas a seguir não são classificadas ou classificadas em nenhuma ordem específica de importância. Para pular para uma seção específica, use os links no índice abaixo.
55 práticas recomendadas de operações de depósito
Índice:
- Práticas recomendadas de rastreamento de ativos para operações de depósito
- Práticas recomendadas de logística de operações de armazém
- Gerenciamento de riscos e segurança nas operações de armazém
- Otimização de fluxos de trabalho de operações de depósito
- Práticas recomendadas para melhorar o gerenciamento de inventário
Práticas recomendadas de rastreamento de ativos para operações de depósito
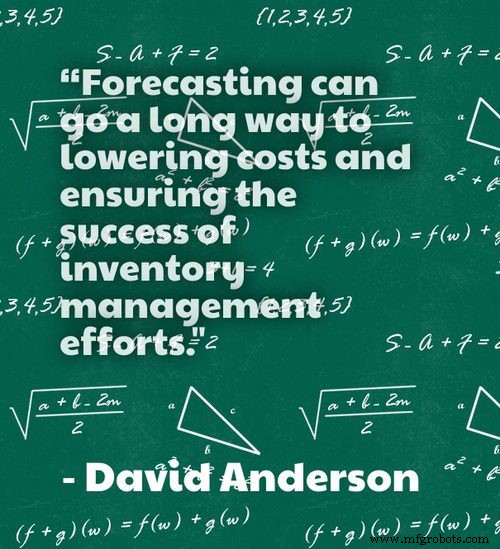
1. Use a coleta automática de dados. “'Pessoas escrevendo números em blocos de papel ou digitando sequências de números em um teclado é um mau sinal', diz McKnight.
Os benefícios da coleta automática de dados – via código de barras e identificação por radiofrequência – estão bem estabelecidos, incluindo maior produtividade e precisão e menores custos de mão de obra. Mas muitas empresas ainda não implementaram a coleta automática de dados.
‘Algumas organizações com 30.000 ou 40.000 números de itens e várias instalações ainda estão convencidas de que estão melhor sem tecnologia’, diz McKnight.” – Denny McKnight, sócio da Tompkins Associates Inc., uma empresa de integração da cadeia de suprimentos com sede em Raleigh, Carolina do Norte, citada por Leslie Hansen Harps em Melhores práticas no centro de distribuição de hoje , InboundLogistics.com
2. Não confie em processos manuais de entrada de dados. “EM VEZ:Use computadores móveis com leitores de código de barras ou leitores RFID na doca de recebimento para identificar imediatamente os produtos na chegada. Isso ajuda a tirar o produto da estação rapidamente e elimina quase todos os erros associados ao recebimento manual:incluindo erros de identificação, contagem e entrada de dados. Com a tecnologia de digitalização e RFID, você evitará os erros que causam estragos na precisão do inventário e consomem tempo e recursos para corrigir. E isso significa que sua equipe de depósito pode se concentrar no processamento de pedidos de clientes mais rapidamente.” – As 10 principais estratégias de perda de armazém e como evitá-las , Soluções Motorola; Twitter:@MotoSolutions
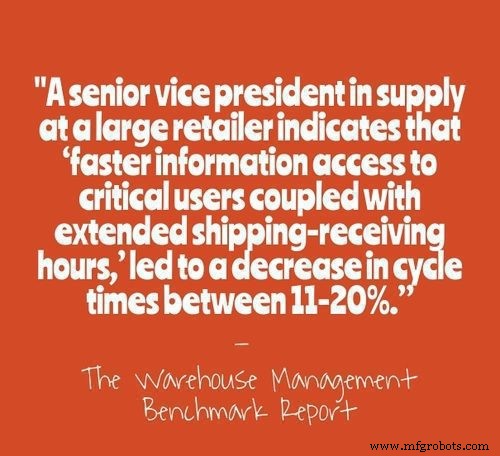
3. Promova a visibilidade das informações em toda a empresa. “Os melhores da categoria apontam para uma infraestrutura de visibilidade de armazém amplamente proliferada que lhes permite compartilhar informações em toda a operação e em toda a empresa. Outro entrevistado aponta a visibilidade como meio de melhoria. Um vice-presidente sênior de suprimentos em um grande varejista indica que “acesso mais rápido às informações para usuários críticos, juntamente com horas estendidas de recebimento de remessa”, levou a uma diminuição nos tempos de ciclo entre 11 e 20%”. – Relatório de referência de gerenciamento de depósito , Grupo Aberdeen; Twitter:@aberdeengroup
4. O rastreamento de ativos combinado com um sistema de gerenciamento de armazém (WMS) fornece a automação necessária para maximizar a produtividade do armazém. “As empresas inteligentes entendem que controlar os custos de estoque, atendimento e envio é essencial para o sucesso. As empresas estão constantemente se esforçando para melhorar suas operações de armazém, aumentando a agilidade, a visibilidade e a eficiência da mão de obra. Isso requer o uso das melhores práticas combinadas com um sofisticado Warehouse Management System (WMS) que gerencia de forma otimizada todos os recursos dentro das operações de distribuição, minimizando o custo total de operação ou propriedade (TCO).” – Depósito e atendimento:simplifique seu processo de atendimento e mantenha seus clientes satisfeitos , NetSuite; Twitter:@NetSuite
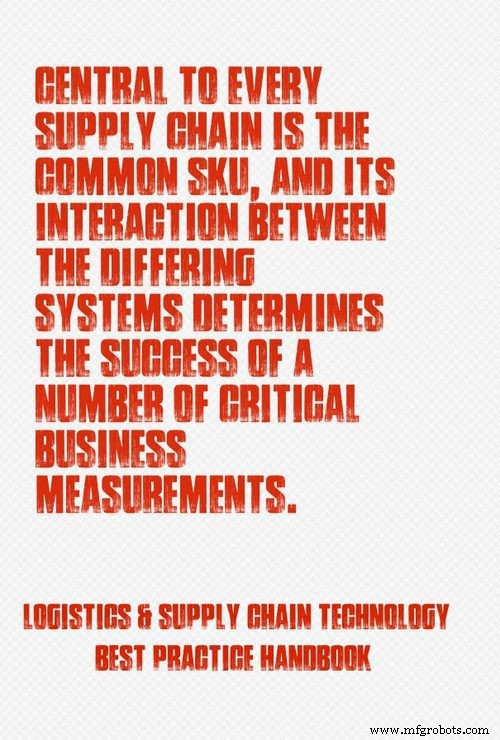
5. A sincronização de dados melhora a visibilidade e simplifica as tarefas de integração de dados normalmente trabalhosas. “Central para toda cadeia de suprimentos é o SKU comum, e sua interação entre os diferentes sistemas determina o sucesso de uma série de medidas críticas de negócios. A chave para harmonizar o fluxo de dados em conjuntos complexos de aplicativos de software em organizações de qualquer tamanho é sincronizar todos os dados relacionados ao SKU comum horizontal ou verticalmente dentro da empresa. Essa abordagem para padronizar dados de produtos comuns no nível do sistema e não ter barreiras para a transformação de dados está substituindo rapidamente as tarefas de integração de dados de trabalho intensivo. O próximo estágio evolutivo no comércio de dados entre organizações é onde os repositórios de dados são atualizados com as informações de SKU mais recentes diretamente dos fornecedores. Essa transferência de dados interoperáveis está agora em um nível global e econômico, atualizando perfeitamente os repositórios de inventário, eliminando a redigitação e reduzindo as transcrepâncias. Está definido para se tornar a melhor prática onde a continuidade das informações de SKU é essencial para investimentos em WMS, BOS e POS. Uma fonte de dados faz sentido. O resultado – varejistas, fornecedores e consumidores se tornam vencedores. Com a maioria das empresas visando eliminar devoluções e re-entregas; reduzir multas ou estornos da cadeia de suprimentos; fornecer uma melhor correspondência de faturas e estoque, podemos um dia estar falando sobre impressões digitais
de carbono em vez de pegadas de carbono.” – Manual de Boas Práticas de Logística e Tecnologia da Cadeia de Suprimentos , BASDA; Twitter:@BASDAUK
6. Use as posições no depósito para localizar produtos rapidamente. “Você está usando locais de depósito para localizar seu produto? A grande maioria dos pacotes de software de distribuição disponíveis hoje utiliza posições no depósito. Isso permite a localização imediata e precisa de produtos dentro de seu showroom e zonas de armazém. Muitos distribuidores desconfiam de aproveitar essa ferramenta devido à necessidade percebida de manter as linhas de fornecedores unidas. Os locais de depósito, na verdade, permitem que você localize o produto com base no volume de vendas, reduzindo assim o número de passos necessários para selecionar os principais itens que tendem a aparecer na maioria dos pedidos. Eu chamo isso de localizar seu produto por classificação de velocidade.
“Você pode passar no 'Teste Temp'? Você é capaz de trazer um novo contratado ou funcionário temporário e ter certeza de que esse indivíduo é produtivo dentro de duas a três horas? A utilização de locais no depósito fornece um mapa para o novo recruta seguir. Isso permite que você procure alguém especializado na área de manuseio de materiais. Sem locais de depósito, você precisará procurar alguém com experiência nas linhas de produtos que você carrega para encontrar o produto para atender aos pedidos. Eles vão precisar de mais mão para aprender onde essas diferentes linhas de produtos são mantidas dentro de suas quatro paredes.” – Dan Belanger, O que fazer e o que não fazer de operações de armazém eficientes (e seguras) , Associação dos Distribuidores de Gases e Soldagem (GAWDA); Twitter:@GasWeldEdge
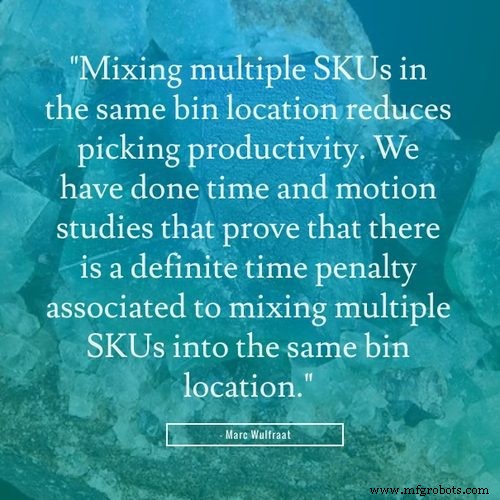
7. Não misture vários SKUs em um único local de depósito. “Misturar vários SKUs no mesmo local da caixa reduz a produtividade de separação. Fizemos estudos de tempo e movimento que provam que há uma penalidade de tempo definida associada à mistura de vários SKUs no mesmo local de depósito.
“Vemos isso em muitos depósitos onde um local de depósito pode representar um nível de prateleira que contém 5 – 10 revestimentos de seleção de SKU. O operador é direcionado para o nível da prateleira e, em seguida, precisa pesquisar nos diferentes SKUs para encontrar o item a ser coletado.
“Isso não apenas reduz a precisão, mas também reduz a velocidade do operador em até 15+ segundos por transação de escolha. Ter um local de separação discreto para cada SKU é a regra nº 1.” – Marc Wulfraat, presidente, MWPVL, 5 maneiras de melhorar a produtividade de separação de pedidos , Cadeia de Suprimentos247; Twitter:@SupplyChain247
8. Registre o número de vezes que o inventário é selecionado durante períodos de tempo específicos usando um sistema de rastreamento de ativos. “Há momentos em que pode não fazer sentido estocar um produto. Por exemplo, se um item é retirado apenas cinco vezes por ano, o custo de armazenamento pode ser eliminado pelo envio direto do fabricante. Ao registrar o número de vezes que um produto é retirado, você pode determinar o valor do espaço onde o estoque reside.” – Práticas recomendadas – Gerenciamento de estoque , Centro de Cumprimento de Promoção; Twitter:@PFCFulfillment
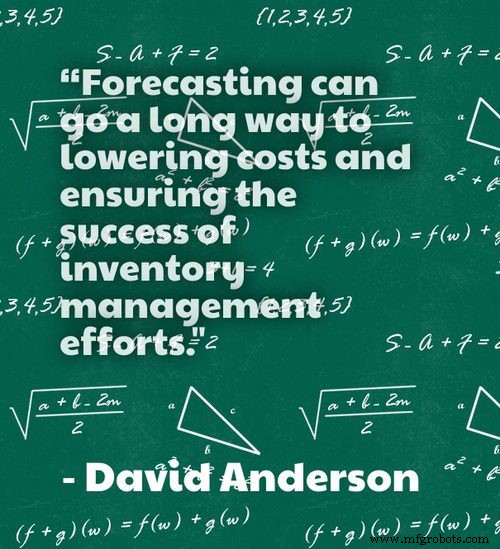
9. O rastreamento de ativos permite previsões mais precisas, essenciais para reduzir custos e melhorar o gerenciamento de estoque. “A previsão pode ajudar muito a reduzir custos e garantir o sucesso dos esforços de gerenciamento de estoque. Quando os varejistas são capazes de prever com precisão quais itens eles precisam e a quantidade correta, eles estarão mais adequados para atender às expectativas de seus clientes sem ter estoque excedente. Uma melhor previsão requer observação hábil de pesquisa de mercado, modelos de demanda de mercado, padrões de demanda, níveis mínimos de estoque e técnicas históricas e pode desempenhar um papel importante no gerenciamento de estoque bem-sucedido. ” – David Anderson, Três práticas recomendadas de gerenciamento de inventário , SalesWarp; Twitter:@SalesWarp
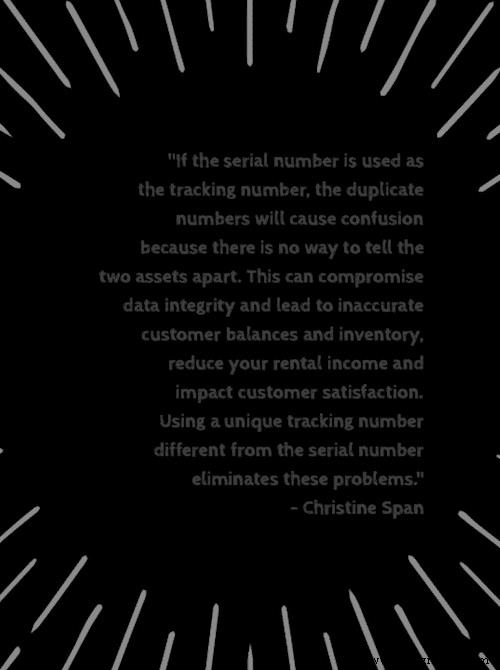
10. Use um número de rastreamento exclusivo, não o número de série do ativo. “É possível que o número de série de um ativo seja idêntico ao de outro ativo. Se o número de série for usado como número de rastreamento, os números duplicados causarão confusão porque não há como diferenciar os dois ativos. Isso pode comprometer a integridade dos dados e levar a saldos e inventários imprecisos do cliente, reduzir sua receita de aluguel e afetar a satisfação do cliente. O uso de um número de rastreamento exclusivo diferente do número de série elimina esses problemas. No caso raro de perda de um número de rastreamento, o ativo ainda pode ser pesquisado usando seu número de série e rotulado corretamente para reter o histórico do ativo.” – Christine Span, Cinco principais práticas recomendadas de rastreamento de ativos , TrackSobre; Twitter:@trackabout
Melhores práticas de logística de operações de armazém
11. Estabeleça uma notificação de envio avançada. “Isso pode parecer um acéfalo, mas muitos centros de distribuição ainda não implementaram notificações avançadas de envio (ASN) transmitidas eletronicamente. Confiar em uma programação “regular” de envio e recebimento pode resultar em ineficiência em todo o centro de distribuição. Atrasos acontecem, interrupções acontecem – e isso causa desvio do cronograma “regular”. Os problemas resultantes começam com pessoal inadequado na doca de recebimento e se espalham pelo armazém. No entanto, aproveitando as notificações eletrônicas avançadas de remessa dentro do pedido de compra e das funções de gerenciamento de estoque, a mão de obra pode ser planejada com mais certeza. O atendimento de pedidos e as atividades de transporte podem ser ajustados para garantir que os requisitos de tempo de serviço adequados sejam atendidos e os modos de transporte são otimizados para manter os custos baixos.” – 11 práticas recomendadas de armazém e centro de distribuição para sua cadeia de suprimentos , Serviços de Cadeia de Suprimentos Legados
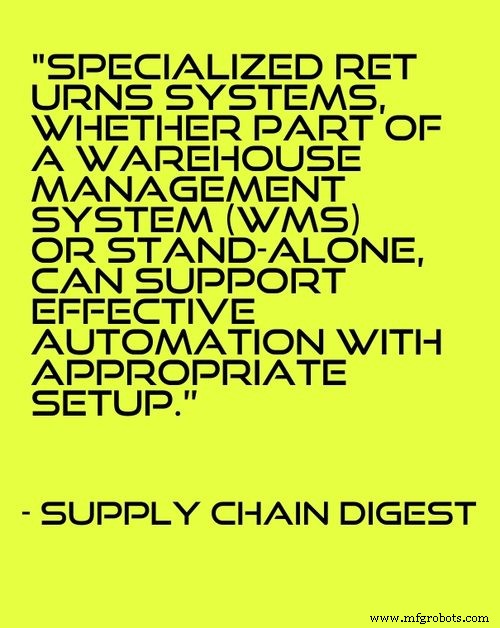
12. Implemente um processo de devolução eficiente. “As devoluções são fundamentalmente complexas devido à forma como impactam o inventário físico, o inventário eletrônico e os sistemas contábeis. Todos os itens devem ser identificados, atribuídos a um cliente ou conta, atribuídos a uma disposição e, em seguida, classificados fisicamente para processamento. Como alguns produtos podem ser descartados ou retidos para estornos do fornecedor, nem todas as mercadorias entram no inventário eletrônico; algumas mercadorias devem ser reembaladas e contabilizadas manualmente versus eletronicamente. Por fim, os créditos geralmente são emitidos posteriormente e geralmente para apenas parte de uma devolução, incluindo mercadorias descartadas ou não vendáveis. Esse processo é difícil de automatizar com um pacote genérico de ERP e muito desafiador com um processo simples em papel. Sistemas de devoluções especializados, sejam parte de um Warehouse Management System (WMS) ou autônomos, podem oferecer suporte a automação eficaz com configuração apropriada.” – Person Insight:Best Practices in Warehouse Returns , Resumo da Cadeia de Suprimentos; Twitter:@scdigest
13. Lide com as tarefas com eficiência e evite a procrastinação. “Às vezes, quando você recebe grandes remessas de fornecedores, é fácil dar o ‘ol, “Eh. Vamos cuidar disso mais tarde.” Acabe com a procrastinação e reserve um tempo para quebrar as caixas, enfiá-las na lixeira, desembalar seus produtos e armazená-los adequadamente. Este é um hábito com o qual você deve se comprometer. Se sua remessa chegar no mesmo horário todos os dias/semanas, agende-a em seu calendário. Adiá-lo só permitirá que ele se torne uma fera ainda maior, esperando por sua atenção.
“Se você não tem tempo para estocá-los em suas prateleiras, outra coisa que eu costumava fazer quando trabalhava no varejo era eu pegava todas as caixas e as alinhava. Abra cada um e veja o que está incluído. A partir daí, faça uma mini pilha de meias em cada caixa. Sabendo onde eles serão alojados, junte os itens próximos, para que você possa puxá-los para o local correto no piso do armazém e armazená-los rapidamente. ” – Breena Fain, 6 maneiras de otimizar seu sistema de gerenciamento de armazém , StitchLabs; Twitter:@StitchLabs
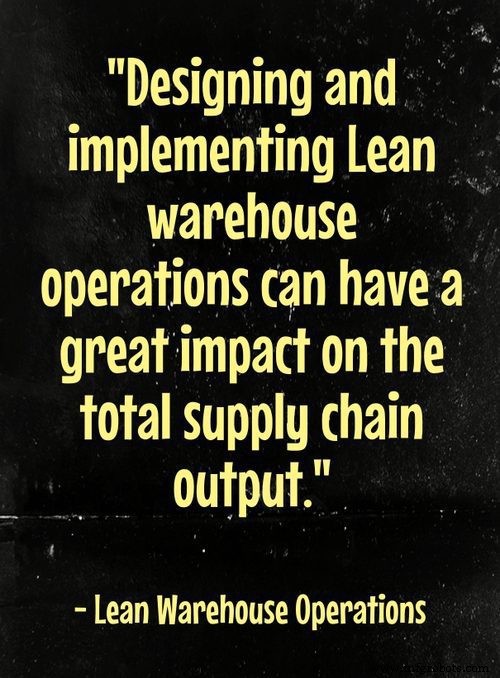
14. Implemente práticas de operações de armazém enxutas. “Projetar e implementar operações de armazém Lean pode ter um grande impacto na produção total da cadeia de suprimentos. Ao abordar as áreas de foco de resíduos mencionadas acima com soluções Lean, algumas das oportunidades que surgem para reduzir os tempos de espera no armazenamento incluem:
- Redução no tempo de manuseio de materiais na separação de pedidos, armazenamento, paletização e expedição.
- Confiabilidade das informações para coordenar o restante da cadeia de suprimentos.
- Redução nos tempos de carga e descarga de caminhões e contêineres.
- Redução no tempo gasto verificando e procurando inventário.
- Aumento da flexibilidade para se adaptar às mudanças nas condições do mercado e nas especificações do cliente.” – Operações de Armazém Lean , Quatro Princípios
15. Controle o frete de entrada e saída para reduzir essa área de custo. “As bibliotecas virtuais estão cheias de artigos sobre como reduzir ou desacelerar essa área de custo. Deve ser seu foco contínuo número um para evitar a erosão dos lucros. Use um consultor para ajudá-lo a fazer lances competitivos. Embora os acordos de transportadora sejam proprietários, consultores experientes ainda podem ajudar a identificar áreas para negociar reduções sem prejudicar os níveis de serviço.” – Curt Barry, 10 maneiras de melhorar a eficiência do depósito e reduzir custos , Comerciante Multicanal; Twitter:@mcmerchant
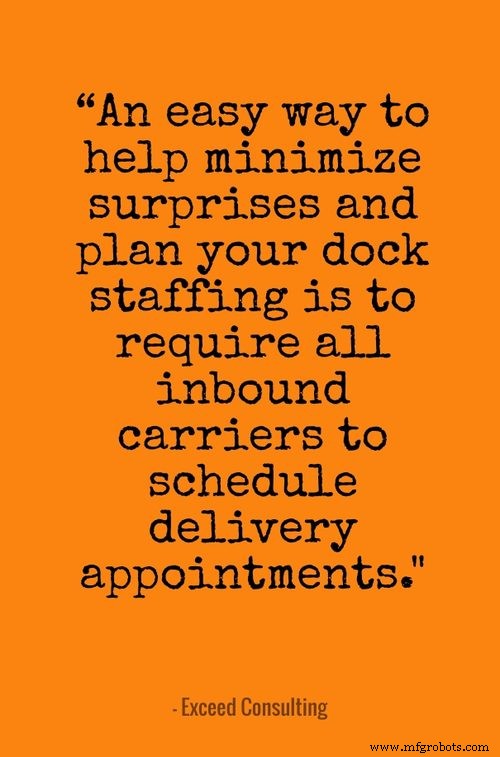
16. Exigir agendamentos de recebimento de fornecedores. “Uma maneira fácil de ajudar a minimizar surpresas e planejar sua equipe de docas é exigir que todas as transportadoras de entrada agendem compromissos de entrega. Existem dois métodos diferentes para agendar e eles podem ser usados simultaneamente. O primeiro método é simplesmente atribuir a cada transportadora ou entrega um horário específico ou janela de tempo para entrega. A segunda é atribuir uma programação diária, semanal ou mensal específica ou recorrente para chegar. Isso permite que você agende a equipe de acordo e faça o melhor uso do seu dock. Os compromissos de recebimento de fornecedores são absolutamente críticos se você compartilha uma doca ou envia tanto de entrada quanto de saída da mesma área. Qualquer papelada ou dados antecipados devem ser fornecidos antes da entrega ser feita. Ao exigir compromissos e informações sobre cargas recebidas, as surpresas são minimizadas.” – De volta ao básico, parte 1:recebimento , Excelência de consultoria
17. Faça uma análise ABC, que é útil para categorizar seu inventário por valor. “ABC é uma hierarquia de seus itens mais valiosos para o mínimo (por valor em dólar). Isso também é chamado de Método de categorização de inventário. Como você pode não valorizar todo o seu estoque da mesma forma, esse controle fará com que você concentre seu tempo e recursos nos itens que geram mais dinheiro.
“Os itens A são caros ou prioritários. Esses produtos exigem controles e monitoramento mais rígidos, pois são seus maiores contribuintes de receita e custo. Devido aos seus custos, você provavelmente estaria carregando volumes menores à mão. Como esses itens são muito procurados, eles devem ser guardados em “cadeado e chave”. Além da segurança, os produtos de primeira linha exigirão frequências mais altas de revisões de estoque e novos pedidos. Isso garante que você tenha um suprimento adequado.
“Por outro lado, os itens C têm valores mais baixos, mas você pode estar carregando grandes volumes deles. Por exemplo, se você possui uma loja de ferragens, pregos a granel podem ser considerados um item C. Os itens B ficam bem no meio do valor, volume, frequência de revisões de estoque e novos pedidos.” – Colleen Rodericks, Técnicas de gerenciamento de estoque e práticas recomendadas , ingresso; Twitter:@inFlowInventory
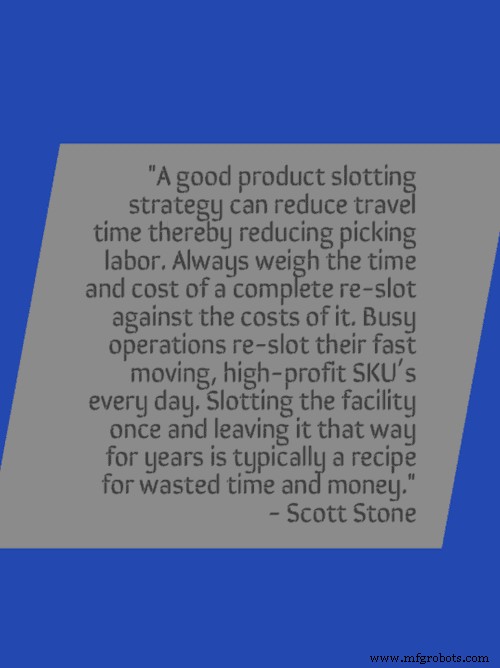
18. Recoloque suas posições de escolha quantas vezes forem necessárias. “Até 60% da atividade diária de um catador pode estar envolvida no tempo de viagem (a pé ou em uma empilhadeira ou walkie), portanto, reduzir esse tempo gasto é uma excelente ideia. Uma boa estratégia de alocação de produtos pode reduzir o tempo de viagem, reduzindo assim o trabalho de separação. Sempre pese o tempo e o custo de um reslot completo em relação aos custos dele. As operações ocupadas reposicionam seus SKUs de alto lucro e movimento rápido todos os dias. Alocar a instalação uma vez e deixá-la assim por anos é tipicamente uma receita para desperdício de tempo e dinheiro.” – Scott Stone, 13 Melhores Práticas para Produtividade de Armazém, Cisco-Águia; Twitter:@CiscoEagle
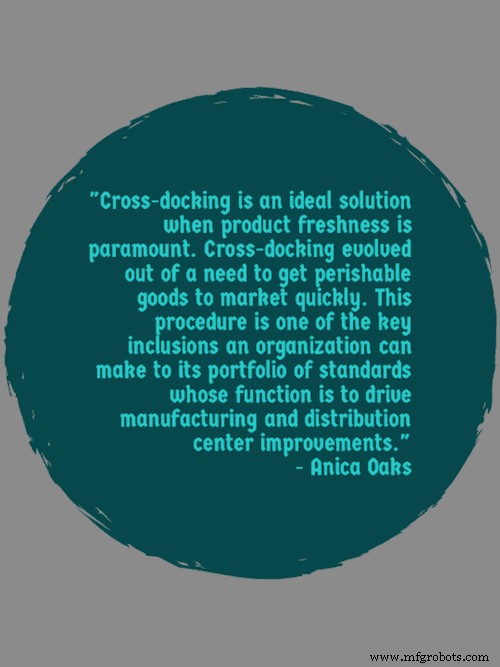
19. Utilize cross-docking sempre que possível. “O planejamento logístico superior inclui cross-docking sempre que possível. Cross-docking é a prática de descarregar materiais de um veículo de entrada e carregar imediatamente esses mesmos materiais diretamente em veículos de saída com intervalo de armazenamento mínimo ou zero entre eles. Pense nisso como um envio “Just-in-Time”. O cross-docking é uma solução ideal quando o frescor do produto é primordial. O cross-docking surgiu de uma necessidade de levar produtos perecíveis ao mercado rapidamente. Esse procedimento é uma das principais inclusões que uma organização pode fazer em seu portfólio de padrões cuja função é impulsionar melhorias de fabricação e centro de distribuição.” – Anica Oaks, 5 Lean Best Practices for the Warehouse, Blog de Transformação da Manufatura Apriso; Twitter:@Apriso
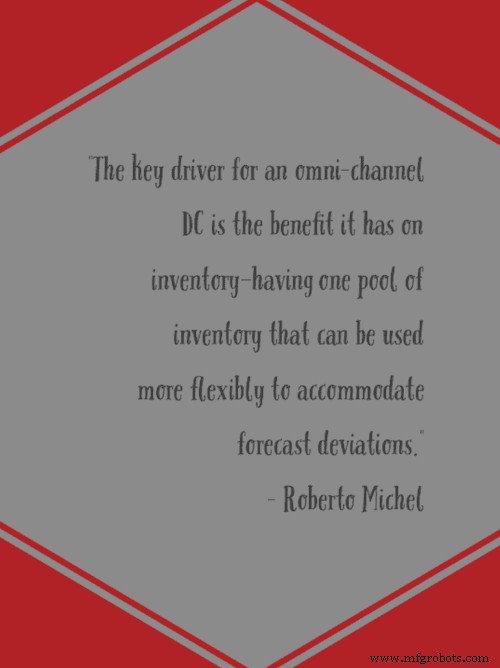
20. Crie DCs que atendam a pedidos para vários canais. “Para algumas empresas que procuram eficiências de atendimento omnicanal, a tendência tem sido se afastar dos CDs dedicados a um único canal e, em vez disso, ter CDs que atendem pedidos para vários canais, diz Ian Hobkirk, fundador e diretor administrativo da Commonwealth Supply Chain Advisors .
“'Há dez anos, quando o comércio eletrônico ainda era relativamente novo, havia muita separação de canais na forma como as empresas configuravam e administravam os CDs, e o atendimento do comércio eletrônico, em muitos casos, era terceirizado para um 3PL', diz Hobkirk. 'Uma das tendências que estamos vendo agora entre os varejistas é ter centros de atendimento multicanal nos quais estoque e atendimento para todos os canais estejam sob o mesmo teto.'
“O principal fator para um DC omnicanal é o benefício que tem no estoque — ter um pool de estoque que pode ser usado com mais flexibilidade para acomodar desvios de previsão. 'Existem outros fatores que impulsionam os centros de atendimento omnicanal, como os custos mais baixos de poder usar um conjunto comum de mão de obra, mas é o fator de estoque que está realmente impulsionando essa tendência', diz Hobkirk.
“O aumento de atendimento omnicanal torna o gerenciamento de estoque mais complexo, o que eleva a necessidade de melhores sistemas para execução, colaboração de previsão e relatórios de gerenciamento, incluindo sistema de gerenciamento de armazém (WMS), planejamento de recursos empresariais (ERP), bem como gerenciamento de demanda e colaboração disciplinar, diz Don Derewecki, consultor sênior da empresa de consultoria em cadeia de suprimentos St. Onge Company.” – Roberto Michel, Gerenciamento de armazém/DC:seis práticas recomendadas para um melhor gerenciamento de estoque , Gestao de logistica; Twitter:@LogisticsMgmt
Gerenciamento de riscos e segurança nas operações de armazém
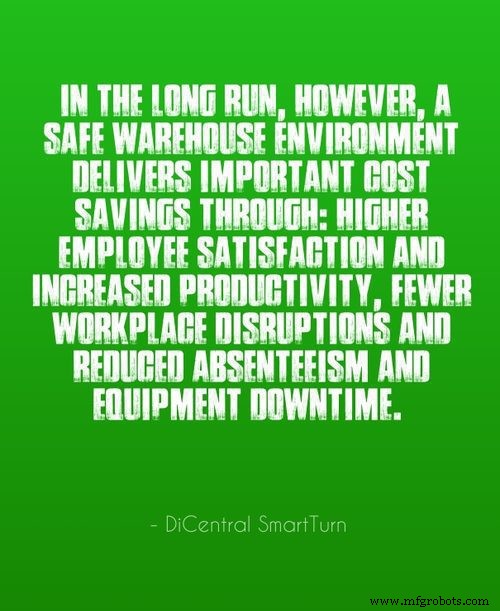
21. Priorize a segurança do armazém. “A segurança do armazém é mais do que a conformidade com os códigos de incêndio e os regulamentos da OSHA. Infelizmente, muitos armazéns e 3PLs consideram a segurança como atendendo ao mínimo exigido por lei ou por sua consciência. Muitas vezes, nem vai longe o suficiente. Neste capítulo, veremos as Melhores Práticas para Segurança de Armazém, discutindo os benefícios e riscos para funcionários, gerentes e empregadores de criar uma cultura de segurança no armazém e não fazê-lo. Para as empresas que não promovem a segurança, muitas vezes isso se deve ao tempo insuficiente, recursos inadequados ou à oportunidade de economizar dinheiro por meio do corte de cantos. A longo prazo, no entanto, um ambiente de armazém seguro oferece importantes economias de custos por meio de:maior satisfação dos funcionários e maior produtividade, menos interrupções no local de trabalho e menos absenteísmo e tempo de inatividade do equipamento. Você pode estender a vida útil de sua infraestrutura de armazém, como equipamentos de armazenamento e manuseio de materiais, além de reduzir os danos ao estoque. Mais importante ainda, não presuma que um local de trabalho seguro tem um preço de cair o queixo.” – Práticas recomendadas de gerenciamento de estoque e armazém , DiCentral SmartTurn; Twitter:@DiCentral_EDI
22. Forme um comitê de segurança. “Embora não sejam particularmente graves, os acidentes em armazéns são numerosos – o setor de armazenamento e armazenamento sofre quase 15.000 lesões e doenças a cada ano, de acordo com o Bureau of Labor Statistics dos EUA.
“Para manter um controle sobre acidentes, os operadores de armazém devem enfatizar treinamento de trabalhadores e estabelecer as melhores práticas de segurança, diz Bob Shaunnessey, diretor executivo do Warehousing Education and Research Council (WERC), uma organização sediada em Oak Brook, Illinois, dedicada ao gerenciamento de armazéns e seu papel na cadeia de suprimentos.
“Para a maioria dos armazéns, formar um comitê de segurança é o primeiro passo para a implementação de procedimentos de segurança aprimorados.
“Os membros de um comitê de segurança geralmente são selecionados de grupos organizacionais específicos—incluindo trabalhadores de chão de armazém, supervisores de turno e gerentes de departamento. Essa abordagem dá voz a todos, mas mantém o tamanho do comitê para um número efetivo de participantes.” – John Edwards, Segurança do Armazém:Não é Acidente , Logística de entrada; Twitter:@ILMagazine
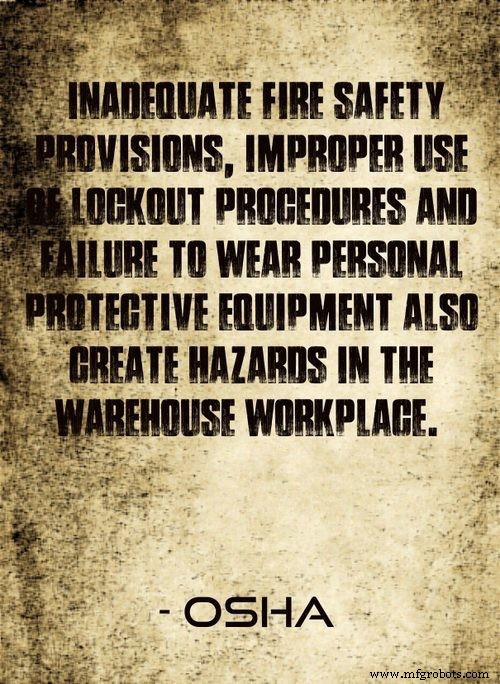
23. Tenha um plano de resposta a emergências. “Disposições inadequadas de segurança contra incêndio, uso inadequado de procedimentos de bloqueio e não uso de equipamentos de proteção individual também criam riscos no local de trabalho do armazém. Os empregadores devem ter um plano de emergência que descreva o que se espera dos funcionários em caso de emergência, incluindo:
• Provisões para locais de saída de emergência e
procedimentos de evacuação;
• Procedimentos de contabilidade para todos os funcionários
e visitantes;
• Localização e uso de extintores de incêndio e
outros equipamentos de emergência.” – Guia de bolso da OSHA, Série de Segurança do Trabalhador:Armazenamento , OSHA.gov; Twitter:@usdol
24. Evite contratempos comuns em docas de carga e áreas de preparação. “Docas de carga ou áreas de preparação são áreas comuns em um armazém onde ocorrem lesões e danos aos produtos. Os perigos comuns incluem:
• Produto caindo na cabeça, pés, braços e pernas dos funcionários;
• Programas de limpeza fracos que resultam em congestionamento;
• Funcionários pulando de um elevação alta para uma elevação mais baixa;
• Elevação das placas de cais e ajuste constante das mesmas; e
• Empilhadeiras ou paleteiras saindo do cais.
“Os controles incluem:
• Fixação das placas de doca para que não capotem;
• Realização de inspeções diárias de cargas e arranjos de armazenamento temporário
;
• Nunca permitir que uma empilhadeira ou porta-paletes recue até a borda da
doca;
• Reforçar as regras de segurança sobre a movimentação de funcionários das elevações
mais altas da doca até a superfície inferior do solo; e
• Monitoramento dos formulários de inspeção de segurança atribuídos West Bend; Twitter:@WBsilverlining
25. Forneça escadas apropriadas para os vários trabalhos em seu depósito e forneça treinamento para que os funcionários possam identificar facilmente a escada mais adequada para as tarefas. “O manuseio de materiais não é a única fonte potencial de lesão dentro de um armazém. Os itens podem ter que ser empilhados para que o espaço seja usado de forma mais eficaz. As escadas podem ser usadas para alcançar o topo das prateleiras ou racks. Escolher a escada certa para o trabalho e usá-la para o uso pretendido minimizará o risco de lesões.” – Segurança do Armazém , KEMI
26. Limpe os derramamentos o mais rápido possível e remova o estoque e os suprimentos dos corredores quando a equipe precisar desocupar a área por um curto período de tempo. “O armazém é um lugar com muitas coisas. Seus corredores estreitos, pilhas altas de mercadorias e pouca iluminação são os ingredientes exatos que podem comprometer a visibilidade. Escorregar e tropeçar em materiais ou líquidos derramados são acidentes comuns que podem ser evitados se o armazém mantiver a iluminação adequada e equipar os cantos escuros com luzes especiais que podem ser facilmente ligadas e desligadas. Remova degraus ou cumes desnecessários e incentive os funcionários a nunca deixar nenhuma carga, caixa e mercadorias sem vigilância no chão.
“Se um funcionário do armazém precisar sair temporariamente do chão, é importante que ele afaste os materiais do centro do corredor mantendo as luzes acesas. Nos casos em que algo é derramado, os funcionários devem tomar as medidas adequadas para fechar a área com sinais visíveis e limpar o mais rápido possível.” – Tom Reddon, 4 maneiras de evitar os incidentes de armazém mais comuns , Conhecimento no Trabalho
27. Somente operadores treinados devem usar equipamentos como empilhadeiras, guindastes e guinchos. “Empilhadeiras e carrinhos de mão não são os únicos equipamentos de armazém que podem ser perigosos. O contato com peças móveis do transportador pode causar ferimentos graves. É por isso que é tão importante manter seus guardas no lugar. Guindastes, guinchos e guindastes podem ser operados apenas por operadores treinados que sabem o suficiente para evitar balançar uma carga sobre pessoas ou remover suas mãos ou pés dos controles enquanto uma carga está suspensa. Além disso, quem trabalha nas proximidades deve ficar atento aos movimentos do guindaste; se você trabalha ou fica embaixo de um guindaste, está procurando problemas. Você também pode identificar perigos na maneira como este equipamento é carregado. Cargas pesadas ou desequilibradas podem cair e causar ferimentos graves, até mesmo fatais.” BLR.com; Twitter:@BLR_INC
28. Use boas práticas de armazenamento para minimizar o risco de incêndios. “O método de armazenamento pode afetar a taxa de propagação do fogo e sua gravidade para o mesmo material. Por exemplo, bobinas de papel armazenadas verticalmente podem dar origem ao efeito de empilhamento. Para armazenamento interno, a altura máxima sugerida da pilha é de 4,5 m. A distância entre o topo da estaca e o ponto mais baixo dos membros do telhado, acessórios elétricos ou detectores de incêndio deve ser de no mínimo 1 m. Uma faixa colorida deve ser pintada na parede para indicar a altura máxima em que os materiais podem ser empilhados.” – N.V. Subba Rao e K. Ramish Ramalingham, Gerenciamento de Riscos em Armazéns , Cholarisk.com
29. O equipamento de segurança deve ser usado sempre. “No armazém, é vital que empilhadeiras ou carrinhos hidráulicos sejam usados para levantar itens muito pesados. Óculos apropriados e capacetes também devem ser usados quando necessário. Employees should be aware of emergency exits and the sprinklers installed in the roof should not be blocked at any time. Safety equipment is implemented in order to minimize workplace injury, so although it may be time consuming to initiate its use, it does pay off in the long run.” – Warehouse Safety Principles:6 key guidelines to keep your workplace safe. , AdaptALift; Twitter:@aalhyster
30. Post safety expectations in highly visible locations and key areas. “Warehouse supervisors should ensure all safety expectations are posted clearly in close proximity to all equipment—forklifts, hydraulic dollies, hand jacks, etc. Doing so assures that employees have constant visual reminders of the inherent dangers of using such equipment, and the safety precautions they should take to avoid injury.” – Warehouse Safety Checklist:8 Things Every Manager Should Review , Legacy Supply Chain Services; Twitter:@legacyscs
31. Establish accountability and give staff a sense of ownership over warehouse safety practices. “Once your staff has been trained and provided the right equipment, they need to be held accountable for working safely. This must apply to everyone in your warehouse. You cannot overlook bad habits of supervisors while reprimanding a dockworker. How you handle safety infractions is up to you, but your employees must own their actions. You will see better results if you offer suggestions for safer operation at the same time you express criticism.
“You do need to document lapses in safety. Without proper records, you may not have the backup you need to take action against an employee that continues to ignore your requirements. Documentation will also help protect you if an employee is injured performing an action after they have been instructed otherwise.” – Jerry Matos, Product Specialist, Cherry’s Industrial Equipment, 6 Ways To Encourage Warehouse Safety , Industrial Distribution; Twitter:@indistwebsite
32. Consider enlisting an outside expert to identify warehouse hazards. “To help improve the safety in the workplace, consider bringing in an outsider. The outsider does not necessarily need to be a consultant or OSHA representative, but may be a business associate, or peer. The point is to have a fresh pair of eyes evaluate the warehouse. Sometimes what is seen in plain sight every day may be an overlooked hazard.” – Best Practices for Warehouse Safety , Labor Law Center
Optimizing Warehouse Operations Workflows

33. Clear aisles make for an efficient flow of inventory. “The movement of inventory throughout the warehouse should be done by experienced materials handlers with certifications or licenses to operate forklifts and boom lifts. These materials handlers should be able to move from one section of the warehouse to another with ease due to aisles that are not full of unstored inventory. Inventory that has not been placed in its proper bin or warehouse location can cause problems with inventory systems, especially under a FIFO, or First In, First Out, inventory system. A FIFO system ensures that the inventory that was received yesterday is moved to the shipping dock before the inventory that was received today. This inventory system reduces the chance of obsolete inventory sitting in warehouse bins.” – Justin Johnson, Best Practices in Warehouse Operations , Chron.com
34. Store the most frequently picked items close to the shipping area. “When considering the level of effort involved in warehouse operations, the greatest expenditure of effort is in the picking process. To gain efficiencies in picking the labor time to pick orders needs to be reduced and this can achieved in a number of ways. Companies with the most efficient warehouses have the most frequently picked items closest to the shipping areas to minimize picking time. These companies achieve their competitive advantage by constantly reviewing their sales data to ensure that the items are stored close to the shipping area are still the most frequently picked.” – Martin Murray, Supply Chain/Logistics Expert, Warehouse Best Practices , About.com
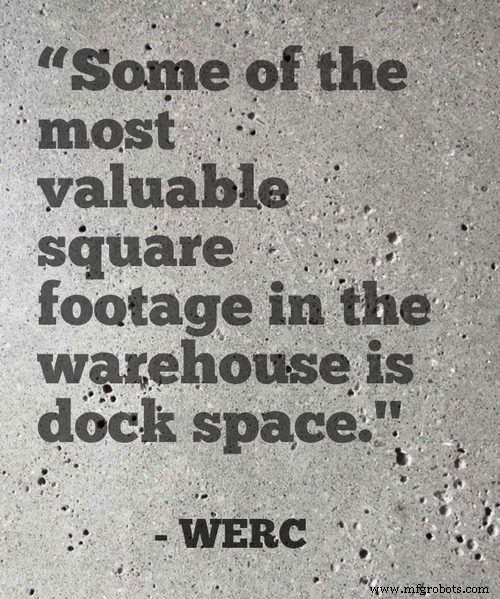
35. Implement efficient dock management practices. “Some of the most valuable square footage in the warehouse is dock space. All material must flow in and out of your docks, and these are limited in number (and not readily added to). Space on the inside and outside of the docks is some of the busiest in your warehouse. Dock best practice depends on the type of inbound you receive and for many companies balancing available dock doors, equipment, and labor is difficult, so the receiving dock becomes a choke point in the supply chain. Docks in today’s warehouses must be more flexible and must support a variety of receipts that are coming in at a faster rate and in greater frequency and with just in-time and VMI programs, smaller quantities and mixed pallets.” – Warehousing &Fulfillment Process Benchmark &Best Practice Guide , Warehouse Education and Research Council (WERC); Twitter:@WERC
36. Calculate resource and space requirements based on expected receipts and current backloads. “Put-away is the process of moving material from the dock and transporting it to a warehouse’s storage, replenishment, or pick area. Best-practice companies manage the put-away area by calculating resource and space requirements based on expected receipts and current backlogs. Best practice is to put away product the same day it’s received, because not doing so affects space, causes congestion, increases transaction errors, and makes product more susceptible to damage. In a busy warehouse, it is easy to let product put-away fall behind other tasks such as picking, replenishment, shipping, and loading. But pulling away resources from put-away tasks can affect fill rates by not having product in pick racks. This can bring about congestion in staging areas that overflow into aisles. Delaying put-away may also result in product damage as the merchandise is moved, again and again, to make way for higher priority receipts. Proper staffing of the put-away team will support down stream processes of picking and shipping, and in the long run lead to better customer order fill rates.” – Kate Vitasek, Best Practices in Material Handling and Put-away , Multi-Channel Merchant; Twitter:@mcmerchant
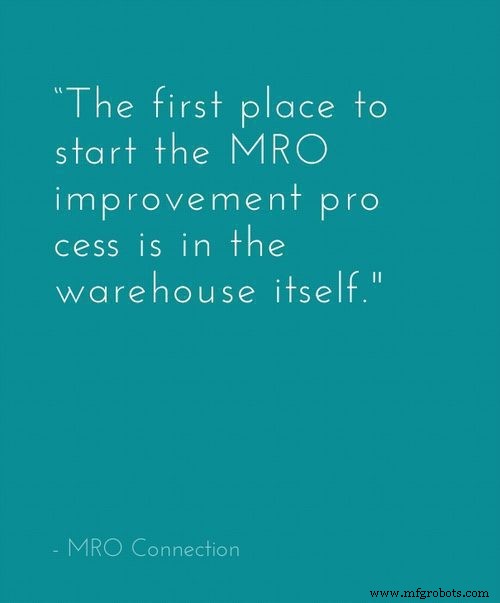
37. Establish stable warehouse operations within the warehouse first, then work to improve pre-planning efforts. “The first place to start the MRO improvement process is in the warehouse itself. Once stable warehouse operations have been established, maintenance and operations can work to improve their pre-planning efforts. At first glance, this appears to be a daunting task. Trying to organize, store, identify and properly manage thousands of disparate inventory items, with different and seemingly unpredictable demand patterns, creates an environment in which it is difficult to succeed. Creating an implementation strategy that is simple, straight forward and thorough, is critical to a successful MRO Warehouse Operation.” – Creating the “Perfect Warehouse,” MRO Connection
38. Maximize vertical space. “On the production floor, where space can be limited, it’s important to take advantage of every inch of available space (floor to ceiling). As noted in an Occupational Health &Safety article, solutions such as pallet racking can lead to safer working conditions as well as increased efficiency in the warehouse. Pallet racking, the most common way of storing pallet loads in the world, is an easy-to-use storage solution; it’s used in the vast majority of warehouses, manufacturing facilities, commercial warehouse operations, and even retail stores.” – Jennie Dannecker, 10 Ideas for More Efficient &Productive Warehouse Operations , Cerasis; Twitter:@Cerasis
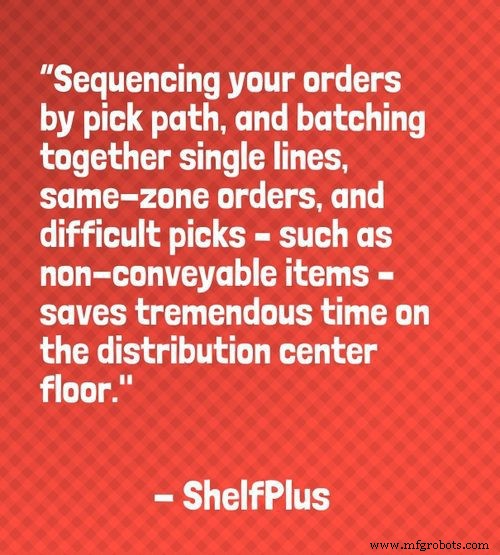
39. Use your WMS software to sequence orders and organize the workflow. “Sequencing your orders by pick path, and batching together single lines, same-zone orders, and difficult picks – such as non-conveyable items – saves tremendous time on the distribution center floor. Again, your WMS software should be able to organize the workflow and optimize sequence performance.” – 10 Ideas for a More Efficient Warehouse Operation , ShelfPlus
40. Communicate effectively — and often. “Clearly communicating to workers your organizational goals and the processes to achieve them is one key to effective warehousing operations. When managers fail to create an environment of open and clear communication, employee productivity suffers, resulting in high turnover and wasted resources.” – Increasing Warehouse Productivity , Inbound Logistics; Twitter:@ILmagazine
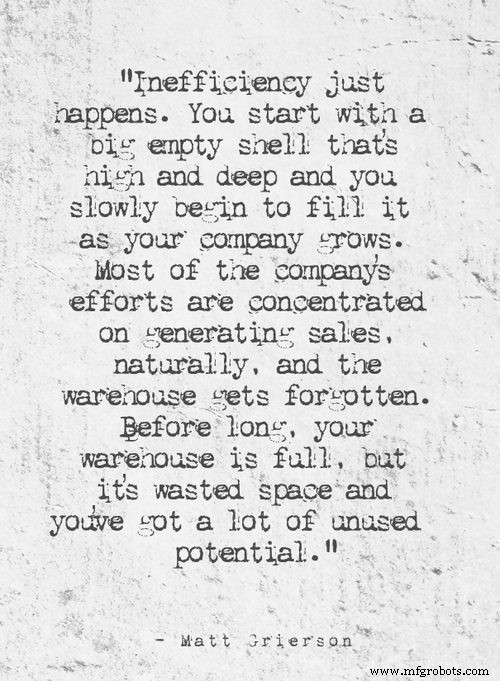
41. Make smart use of floor space. “Matt Grierson is managing director at Dexion, which provides industrial and commercial storage solutions across Europe. He says that only a small fraction of the companies that approach him believing they need to move into larger premises really do need to. The rest have enough space already, they’re just using it badly.
“Grierson says:‘Inefficiency just happens. You start with a big empty shell that’s high and deep and you slowly begin to fill it as your company grows. Most of the company’s efforts are concentrated on generating sales, naturally, and the warehouse gets forgotten. Before long, your warehouse is full, but it’s wasted space and you’ve got a lot of unused potential.’
“By using your space efficiently, your staff can get jobs done quicker and can complete more jobs in a day, you save on purchase or rent by not expanding unnecessarily, and you can go longer before the huge burden of relocating into bigger premises.
“Grierson adds:‘There are a lot of shelving options. Two-tier or mezzanine, fixed or mobile. If you can squeeze your rows of shelving together, and only open them up when access is required, you can save 50% of your floor space.'” – Tim Aldred, How to manage an effective warehouse , The Guardian; Twitter:@tim_aldred
42. Design storage systems to meet the needs of the current and planned mix of storage types. “The layout of a warehouse that supports an adjoining manufacturing facility will have different requirements than a facility supporting product distribution to stores or a facility that supports end-user fulfillment. Some operations place emphasis on replenishment of product to the point of use, others on product picking or order fulfillment.
“Regardless of the ultimate mission of the warehouse, best-practice companies have designed storage systems to meet the needs of the current and planned mix of storage types. They have optimized storage locations and layouts to fit product without the need to restack or repalletize it once received. The warehouse management system will track storage location profiles and properly assign product to the best storage location. As a result, best-practice companies have excellent cube-fill rates.
“In addition to optimizing the cubic fill of storage locations, best practice is to minimize travel time. If a product is in high demand it should be placed closer to its next point of use. In this case demand should be based on the number times the product is required, not on the number of units required. The difficulty of retrieval should also be considered in travel time. Higher-demand product should be placed on the most easily accessed storage space, typically floor level for racking and between waist and shoulder level in pick racks.” – Kate Vitasek, Storage and Inventory Control Best Practices , Multi-Channel Merchant; Twitter:@mcmerchant
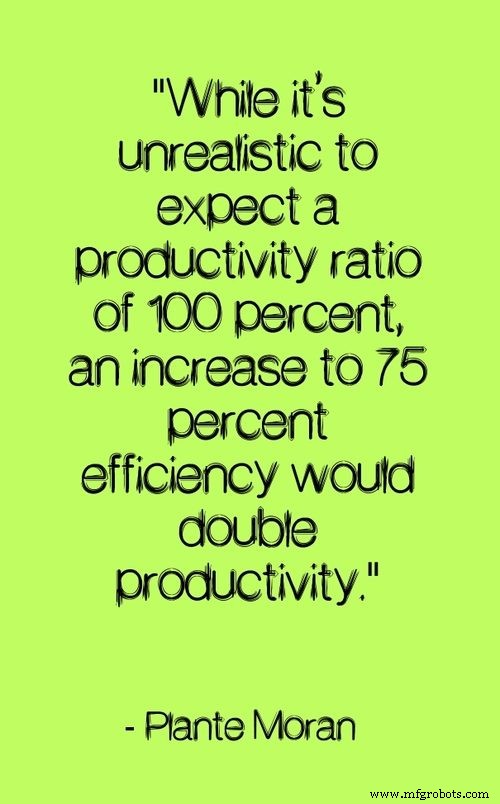
43. Reduce order processing cycle time. “In one analysis of a distribution operation, data revealed that the overall order processing cycle time was extremely inefficient. Of the total order cycle time, it was actually being worked on only 37.9 percent of the time. Six percent of the time was wasted while people dealt with problems such as waiting for lift equipment, computer issues, interruptions, and blocked aisles, and the remaining 56.1 percent of the time orders sat idle. This is a low productivity ratio by any standard. While it’s unrealistic to expect a productivity ratio of 100 percent, an increase to 75 percent efficiency would double productivity. How can this opportunity be captured? ” – Are Your Warehouse Operations Lean? , Plante Moran; Twitter:@PlanteMoran
44. Implement and maintain operational standards in all functional areas. “Maintain and use standards in all major functional areas. This will assist management in identifying systemic bottlenecks such as aisle congestion or other workflow problems.” – Warehouse Workflow Handbook , WERC; Twitter:@WERC
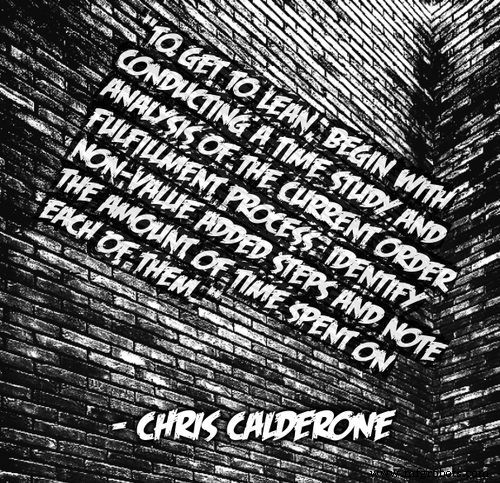
45. Improve cycle time utilization through lean applications. “Lean applications can help improve cycle time utilization, reduce costs, increase productivity, and increase customer satisfaction. To get to lean, begin with conducting a time study and analysis of the current order fulfillment process. Identify non-value added steps and note the amount of time spent on each of them. Then, assess overall workflow in an attempt to reveal inefficient product pick paths, wasted motion, excessive delays, excessive footsteps, aisle and work area congestion, and equipment availability.” – Chris Calderone, Creating a Lean HME Warehouse Operation , Lean Homecare; Twitter:@LeanHomecare
Best Practices for Improving Inventory Management
46. Reduce inventory inefficiencies. “Warehouse management systems are critical to tracking the various stages of the manufacturing process. From production to delivery, officials need to be able to monitor inventory as it makes its way through the supply chain. This is especially relevant during periods of growth, as a sudden influx of inventory may overwhelm employees on the floor, leading to costly errors. Without a robust inventory control system, managers may have difficulties locating materials or finished products, causing them to dedicate more manpower and resources to this process. Officials with Land Rover dealt with this issue on a regular basis, according to Zebra Technologies. When vehicles rolled off the assembly line, they were subject to a number of finalization processes, including testing, setting configurations and addressing any existing errors. Managers had a great deal of difficulty identifying where individual items were located along the supply chain, resulting in a high degree of uncertainty and risk.” – Nancy Master, Identifying Warehouse Management Best Practices , RFgen; Twitter:@RFgenSoftware
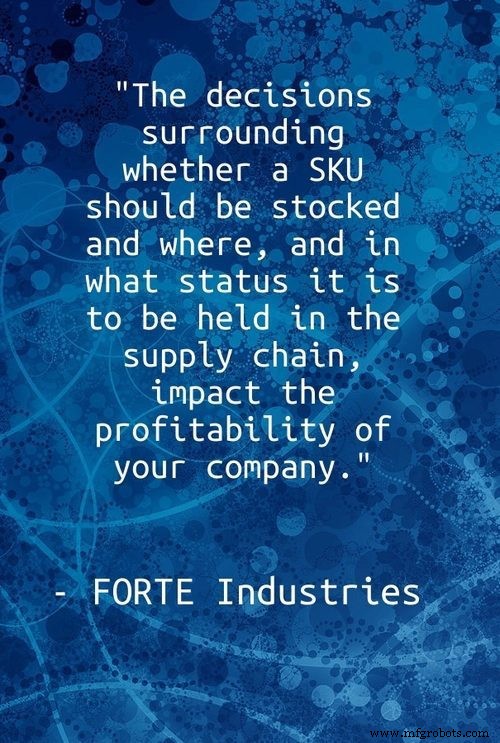
47. SKU profiling can facilitate profitability. “Understanding how every SKU carried in your distribution center (DC) can – and should – contribute to your company’s bottom line – is the best way to design and run DC operations. Here’s why:Each SKU has a potential cost impact that goes well beyond its actual purchase price. The decisions surrounding whether a SKU should be stocked and where, and in what status it is to be held in the supply chain, impact the profitability of your company. And from a selfish standpoint, these same decisions, made without sufficient evaluation, can rob your distribution center of capacity and efficiency.” FORTE Industries
48. Establish minimum holding stocks to cover lead times. “It has been established that the role of inventory management is to ensure that stock is available to meet the needs of the beneficiaries as and when required.
“Inventory represents a large cost to the humanitarian supply chain. This is made up of the cost of the inventory itself, plus the cost of transporting the goods, cost of managing the goods (labor, fumigation, repackaging, etc) and keeping the goods in warehouses. The inventory manager’s job is to make inventory available at the lowest possible cost.
“In order to achieve this, the inventory manager must ensure a balance between supply and demand by establishing minimum holding stocks to cover lead-times. To achieve this, the inventory manager must constantly liaise with the programs to keep abreast of changing needs and priorities. The warehouse must always have sufficient stocks to cover the lead-time for replacement stocks to avoid stock-outs.” – Warehousing and Inventory Management , Logistics Cluster; Twitter:@logcluster
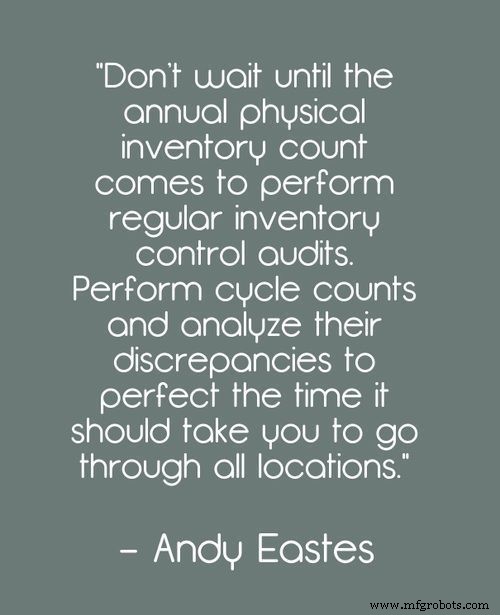
49. Perform cycle counts and analyze discrepancies. “Don’t wait until the annual physical inventory count comes to perform regular inventory control audits. Perform cycle counts and analyze their discrepancies to perfect the time it should take you to go through all locations. It’s good to have cycle counts go through all locations every quarter so that you have a more accurate back-office system.” – Andy Eastes, CEO of Agile Harbor, 10 Ways to improve warehouse efficiency and inventory management without software , SKUVault; Twitter:@skuvault
50. Develop an approved stock list for each location. “When you stock an item you are making a commitment—a commitment that the product will be available in reasonable quantities for immediate shipment or delivery to customers. Most distributors’ warehouses are filled with two things:‘stock’ and ‘stuff.’ Stock is the material you intend to be in the warehouse. That is, the items necessary to meet or exceed customers’ expectations of product availability. Stuff is everything else. You must separate the stock from the stuff in each of your warehouses. Our goal is to liquidate the stuff and arrange the stock items in such a way to minimize the cost of filling customer orders.” – John Schreibfeder, President of Effective Inventory Management, Inc., The First Step to Achieving Effective Inventory Control , via Lanham Associates; Twitter:@LanhamAssoc
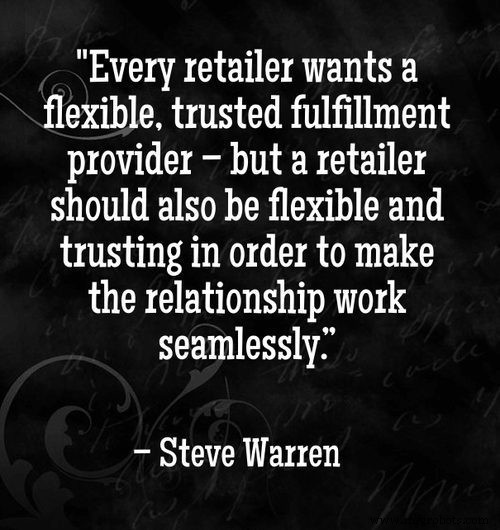
51. Maintain constant, consistent communication with vendors. “A good relationship with your vendors is crucial to your company’s success – especially if you outsource any part of your retail operations. Your fulfillment provider becomes your brand in the eyes of the customer, so it’s important that they understand your plans for your inventory as well as you do.
“This means constant communication of your promotional plans, product information, and upcoming releases. Every retailer wants a flexible, trusted fulfillment provider – but a retailer should also be flexible and trusting in order to make the relationship work seamlessly.” – Steve Warren, 4 Tips for Effective Inventory Management , Multi-Channel Merchant; Twitter:@mcmerchant
52. Achieve inventory analysis efficiency. “With solid inventory analysis, you can ensure that you are investing in the right amount of the right products to remain competitive. By developing and using a comprehensive set of tools to closely monitor the performance of your inventory, you can achieve more of your goals more efficiently.” – Bill Knapp, Socius, Beyond Software:6 Effective Inventory Management Practices , featured on the ERP Software Blog; Twitter:@erpsoftwareblog and @mssocius
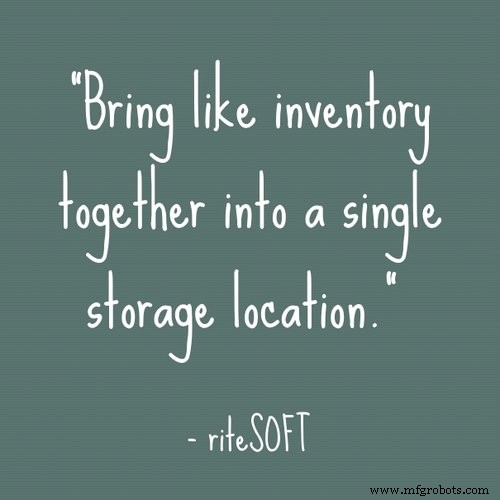
53. Understand the warning signals. “The easiest way to identify that you have too much—or the wrong inventory—is the amount of dust settled on the product in storage. If you see more than ½ inch of dust, then that’s likely a sign of obsolete inventory. However, there are other, more specific indicators that inventory management issues need to be addressed.
“If there are significant discrepancies between the book inventory and physical inventory, this is a direct indicator that there is a problem with inventory management. Another distinct indicator is when your warehouse staff is having trouble locating inventory on a timely basis—an issue that’s particularly critical when FIFO, batch/lot number or serial number controls are involved.
“The issue of locating specific inventory is typically tied to inventory discrepancies. And, of course, if you’ve seen a trend in the increased use of outside storage space, then this can indicate another ongoing inventory management issue.” – Norm Saenz and Don Derewecki of St. Onge, Inventory Management 101:Time to revisit the principles , Logistics Management; Twitter:@LogisticsMgmt
54. Use both fixed and moveable tracking options. “When companies think of warehouse tracking, they think primarily of movable tracking options, tracking the units and pallets that actually get moved around the warehouse and sent up the supply chain. This is only one part of the warehouse management process – do not forget the benefits that come with used fixed trackers, too! By tracking fixed warehouse assets, you are able to assign and manage destinations much more easily, and arrange strategy protocols as needed without mass confusion. It is better to think of warehouse tracking in two different parts, one fixed and one movable.” – Justin Velthoen, 7 Tips for Warehouse Inventory Management , QStock Inventory; Twitter:@QStockInventory
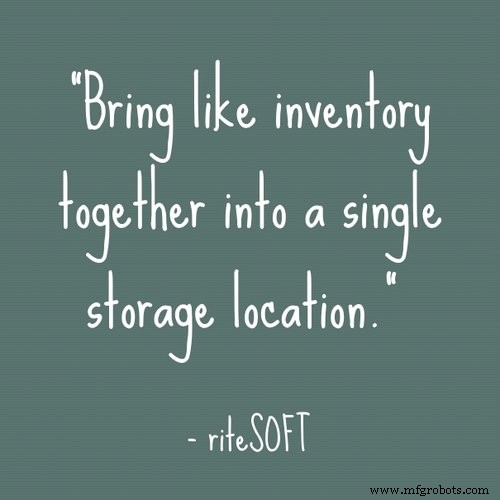
55. For physical count inventory, keep like inventory together in a single location. “Bring like inventory together into a single storage location. The same part shouldn’t be in several storage areas unless physical size dictates a limitation. In that case, keep available quantities to a minimum and move remainder to a location that isn’t part of the easily accessible storage (overstock location).” – Warehouse Management Tips for Physical Count Inventory , riteSOFT; Twitter:@ritesoft
Asset Tracking Solutions from Camcode:
- Inventory Control
- Inventory Management
- Custom Foil Labels
- Sinais de armazém
- Aisle Signs
- Stainless Steel Tags
- Floor Labels
- Security Labels
- Magnetic Labels
- Etiquetas de recursos
Tecnologia industrial
- Como o CMMS pode melhorar o gerenciamento do armazém
- Práticas recomendadas e dicas de manutenção para sistemas hidráulicos
- 25 melhores ferramentas de software de otimização de armazém
- 6 práticas recomendadas para rastreamento de estoque do armazém
- 50 práticas recomendadas em gerenciamento de ativos de TI
- Produtividade do armazém:15 especialistas revelam suas principais dicas para operações de armazém mais eficientes e produtivas
- O melhor guia para gerenciamento de inventário de depósito:80 recursos confiáveis sobre estruturas de gerenciamento de inventário, práticas recomendadas, software, mobilidade e soluções de in…
- Melhores apresentações de gerenciamento de depósito e apresentações de slides:50 recursos detalhados sobre como otimizar operações de depósito, aumentar a produtividade e muito mais
- Principais recursos de treinamento em gerenciamento de depósito:50 cursos, webinars, tutoriais e muito mais para dominar as práticas de gerenciamento de depósito
- Software de gerenciamento de armazém:as 52 melhores ferramentas e sistemas para melhorar a eficiência do armazém, reduzir despesas gerais e aumentar os lucros