Ferro
Antecedentes
O ferro é um dos elementos mais comuns da Terra. Quase toda construção do homem contém pelo menos um pouco de ferro. É também um dos metais mais antigos e foi transformado em objetos úteis e ornamentais há pelo menos 3.500 anos.
O ferro puro é um metal branco acinzentado macio. Embora o ferro seja um elemento comum, o ferro puro quase nunca é encontrado na natureza. O único ferro puro conhecido de existir naturalmente vem de meteoritos caídos. A maior parte do ferro é encontrada em minerais formados pela combinação do ferro com outros elementos. Os óxidos de ferro são os mais comuns. Os minerais próximos à superfície da terra que possuem o maior teor de ferro são conhecidos como minérios de ferro e são extraídos comercialmente.
O minério de ferro é convertido em vários tipos de ferro por meio de diversos processos. O processo mais comum é o uso de um alto-forno para produzir ferro-gusa, que é cerca de 92-94% de ferro e 3-5% de carbono com quantidades menores de outros elementos. O ferro-gusa tem apenas usos limitados, e a maior parte desse ferro vai para uma usina siderúrgica, onde é convertido em várias ligas de aço, reduzindo ainda mais o teor de carbono e adicionando outros elementos, como manganês e níquel, para dar propriedades específicas ao aço.
História
Os historiadores acreditam que os egípcios foram os primeiros a trabalhar com pequenas quantidades de ferro, cerca de cinco ou seis mil anos atrás. O metal que usaram foi aparentemente extraído de meteoritos. A evidência do que se acredita ser o primeiro exemplo de mineração e fundição de ferro aponta para a antiga cultura hitita no que hoje é a Turquia. Como o ferro era um material muito superior para a fabricação de armas e ferramentas do que qualquer outro metal conhecido, sua produção era um segredo bem guardado. No entanto, a técnica básica era simples e o uso do ferro foi se espalhando gradualmente. Por mais útil que fosse em comparação com outros materiais, o ferro tinha desvantagens. A qualidade das ferramentas feitas com ele era muito variável, dependendo da região de onde o minério de ferro foi retirado e do método usado para extrair o ferro. A natureza química das mudanças ocorridas durante a extração não foi compreendida; em particular, a importância do carbono para a dureza do metal. As práticas variam amplamente em diferentes partes do mundo. Há evidências, por exemplo, de que os chineses foram capazes de derreter e fundir implementos de ferro muito cedo, e que os japoneses produziram resultados surpreendentes com aço em pequenas quantidades, como evidenciado por espadas antigas que datam de séculos. Avanços semelhantes foram feitos no Oriente Médio e na Índia, mas os processos nunca surgiram no resto do mundo. Durante séculos, os europeus careceram de métodos para aquecer o ferro até o ponto de fusão. Para produzir ferro, eles queimaram lentamente minério de ferro com madeira em um forno forrado de argila. O ferro separou-se da rocha circundante, mas nunca derreteu totalmente. Em vez disso, formou uma escória crocante que foi removida com martelo. Esse processo de aquecimento e martelamento repetido misturou o oxigênio com o óxido de ferro para produzir ferro e removeu o carbono do metal. O resultado era ferro quase puro, facilmente modelado com martelos e pinças, mas muito macio para segurar e manter uma boa lâmina. Como o metal foi moldado, ou forjado, por martelagem, passou a ser chamado de ferro forjado.
As ferramentas e armas trazidas do Oriente para a Europa eram feitas de ferro fundido e moldado. Retendo mais carbono, o ferro fundido é mais duro do que o ferro forjado e mantém uma aresta de corte. No entanto, também é mais frágil do que o ferro forjado. Os siderúrgicos europeus sabiam que os orientais tinham um ferro melhor, mas não os processos envolvidos na fabricação de produtos de ferro mais fortes. Nações inteiras lançaram esforços para descobrir o processo.
O primeiro avanço europeu conhecido na produção de ferro fundido, que levou rapidamente ao primeiro aço prático, só aconteceu em 1740. Naquele ano, Benjamin Huntsman obteve uma patente para a fusão de material para a produção de molas de aço. usado na relojoaria. Ao longo dos próximos 20 anos ou mais, o procedimento tornou-se mais amplamente adotado. Huntsman usou um alto-forno para derreter ferro forjado em um cadinho de argila. Ele então adicionou quantidades cuidadosamente medidas de carvão puro ao metal derretido. A liga resultante era forte e flexível quando fundida em molas. Como a Huntsman estava originalmente interessado apenas em fazer relógios melhores, seu cadinho de aço levou diretamente ao desenvolvimento de cronômetros náuticos, que, por sua vez, tornaram a navegação global possível ao permitir que os marinheiros determinassem com precisão sua posição leste / oeste. O fato de ele também ter inventado a metalurgia moderna foi um efeito colateral que ele aparentemente não percebeu.
Matérias-primas
As matérias-primas usadas para produzir ferro-gusa em um alto-forno são minério de ferro, coque, sínter e calcário. Os minérios de ferro são principalmente óxidos de ferro e incluem magnetita, hematita, limonita e muitas outras rochas. O teor de ferro desses minérios varia de 70% a 20% ou menos. O coque é uma substância produzida pelo aquecimento do carvão até que se torne carbono quase puro. O sinter é feito de minério de ferro de menor qualidade, finamente dividido, que é torrado com coque e cal para remover uma grande quantidade de impurezas do minério. O calcário ocorre naturalmente e é uma fonte de carbonato de cálcio.
Outros metais às vezes são misturados ao ferro na produção de várias formas de aço, como cromo, níquel, manganês, molibdênio e tungstênio.
O processo de extração e refino de minério
Antes que o minério de ferro possa ser usado em um alto-forno, ele deve ser extraído do solo e parcialmente refinado para remover a maioria das impurezas.
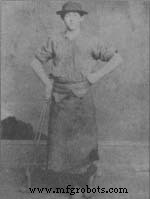
Historicamente, o ferro era produzido pelo método de explosão a quente ou, posteriormente, pelo forno antracítico. De qualquer forma, a atividade fundamental na fabricação do ferro envolvia um trabalhador mexendo pequenos lotes de ferro-gusa e cinzas até que o ferro se separasse da escória. Chamado de "poça", era um trabalho altamente qualificado, mas também quente, extenuante e perigoso. Exigia muita experiência e também uma constituição vigorosa. Puddlers eram orgulhosos, independentes e bem pagos.
Puddlers fundou o primeiro sindicato na indústria de ferro e aço, os Sons of Vulcan, em Pittsburgh, em 1858. Em 1876, esse sindicato se fundiu com três outras organizações trabalhistas para formar a Associação Amalgamada de Trabalhadores do Ferro e do Aço. Este foi o sindicato que Andrew Carnegie derrotou na greve de Homestead de 1892, deixando o sindicato em ruínas e a indústria essencialmente desorganizada até a década de 1930.
William S. Pretzer
Extração
- 1 Grande parte do minério de ferro do mundo é extraído por meio de mineração a céu aberto, na qual o
O ferro puro é um metal branco acinzentado macio. Embora o ferro seja um elemento comum, o ferro puro quase nunca é encontrado na natureza. Os minerais próximos à superfície da terra que possuem o maior conteúdo de ferro são conhecidos como minérios de ferro e são extraídos comercialmente. superfície do solo é removida por máquinas pesadas, geralmente em uma área muito grande, para expor o minério abaixo. Nos casos em que a remoção da superfície não é econômica, são cavados poços no solo, com túneis laterais para acompanhar a camada de minério.
Refino
- 2 O minério extraído é triturado e separado. Os melhores tipos de minério contêm mais de 60% de ferro. Graus menores são tratados, ou refinados, para remover vários contaminantes antes que o minério seja enviado ao alto-forno. Coletivamente, esses métodos de refino são chamados de beneficiamento e incluem mais trituração, lavagem com água para fazer a areia e a argila flutuarem, separação magnética, pelotização e sinterização. À medida que o suprimento mundial de minério com alto teor de ferro se esgota, essas técnicas de refino se tornam cada vez mais importantes.
- 3 O minério refinado é então carregado em trens ou navios e transportado para o local do alto-forno.
O processo de fabricação
Carregando o alto-forno
- 1 Após o beneficiamento, o minério é misturado com outro minério e segue para o alto-forno. Um alto-forno é uma estrutura em forma de torre, feita de aço e revestida com tijolos refratários ou resistentes ao calor. A mistura de matéria-prima, ou carga, entra no topo do alto-forno. No fundo da fornalha, ar muito quente é soprado, ou soprado, através de bicos chamados tuye'res. A coca queima na presença do ar quente. O oxigênio do ar reage com o carbono do coque para formar o monóxido de carbono. O monóxido de carbono
então reage com o minério de ferro para formar dióxido de carbono e ferro puro.
Separando o ferro da escória
- 2 O ferro derretido vai para o fundo da fornalha. O calcário se combina com a rocha e outras impurezas do minério para formar uma escória que é mais leve que o ferro e flutua no topo. À medida que o volume da carga é reduzido, mais é adicionado continuamente no topo do forno. O ferro e a escória são retirados separadamente do fundo do forno. O ferro derretido pode passar por outro processo de liga ou pode ser fundido em lingotes chamados pigs. A escória é transportada para descarte.
Tratamento de gases
- 3 Os gases quentes produzidos nas reações químicas são retirados na parte superior e encaminhados para uma planta de limpeza de gases, onde são limpos ou esfregados e enviados de volta ao forno; o monóxido de carbono restante, em particular, é útil para as reações químicas que ocorrem dentro do forno.
Um alto-forno normalmente funciona dia e noite por vários anos. Eventualmente, o revestimento de tijolos começa a desmoronar e o forno é desligado para manutenção.
Controle de qualidade
A operação do alto-forno é altamente instrumentada e monitorada continuamente. Tempos e temperaturas são verificados e registrados. O conteúdo químico dos minérios de ferro recebidos das várias minas é verificado e o minério é misturado com outro minério de ferro para atingir a carga desejada. Amostras são retiradas de cada vazamento e verificadas quanto ao conteúdo químico e propriedades mecânicas, como resistência e dureza.
Subprodutos / resíduos
Existem muitos efeitos ambientais possíveis da indústria do ferro. O primeiro e mais óbvio é o processo de mineração a céu aberto. Enormes extensões de terra são reduzidas a rocha nua. Hoje, os locais de mineração esgotados são comumente usados como aterros sanitários e, em seguida, cobertos e ajardinados. Alguns desses aterros tornam-se eles próprios problemas ambientais, uma vez que, no passado recente, alguns eram utilizados para a eliminação de substâncias altamente tóxicas que se infiltravam no solo e na água.
O processo de extração do ferro do minério produz grandes quantidades de gases tóxicos e corrosivos. Na prática, esses gases são depurados e reciclados. Inevitavelmente, no entanto, algumas pequenas quantidades de gases tóxicos escapam para a atmosfera.
Um subproduto da purificação do ferro é a escória, produzida em grandes quantidades. Esse material é em grande parte inerte, mas ainda deve ser descartado em aterros.
A fabricação de ferro consome grandes quantidades de carvão. O carvão não é usado diretamente, mas primeiro é reduzido a coque, que consiste em carbono quase puro. Os muitos subprodutos químicos da coqueificação são quase todos tóxicos, mas também são comercialmente úteis. Esses produtos incluem amônia, que é usada em um grande número de produtos; fenol, que é usado para fazer plásticos, óleos de corte e anti-sépticos; cresóis, que entram em herbicidas, pesticidas, produtos farmacêuticos e produtos químicos fotográficos; e tolueno, que é um ingrediente em muitos produtos químicos complexos, como solventes e explosivos.
Sucata de ferro e aço - na forma de carros antigos, eletrodomésticos e até edifícios inteiros com vigas de aço - também são uma preocupação ambiental. A maior parte desse material é reciclada, entretanto, uma vez que a sucata de aço é um recurso essencial na produção de aço. A sucata que não é reciclada eventualmente se transforma em óxido de ferro, ou ferrugem, e retorna ao solo.
O Futuro
Superficialmente, o futuro da produção de ferro - especialmente nos Estados Unidos - parece problemático. As reservas de minério de alta qualidade se esgotaram consideravelmente nas áreas onde ele pode ser extraído economicamente. Muitas siderúrgicas de longa data fecharam.
No entanto, essas aparências enganam. Novas técnicas de enriquecimento de minério tornaram o uso de minério de baixo teor muito mais atraente, e há um vasto suprimento desse minério. Muitas usinas siderúrgicas foram fechadas nas últimas décadas, mas isso ocorre principalmente porque menos são necessárias. A eficiência dos altos-fornos por si só melhorou notavelmente. No início deste século, o maior alto-forno dos Estados Unidos produzia 644 toneladas de ferro-gusa por dia. Acredita-se que em breve a possível produção de um único forno chegará a 4.000 toneladas por dia. Uma vez que muitas dessas fábricas mais modernas foram construídas no exterior, na verdade se tornou mais econômico em alguns casos enviar aço através do oceano do que produzi-lo em fábricas mais antigas dos EUA.
Processo de manufatura