Aspectos históricos da Fundição Contínua e Tecnologias Relacionadas para o Aço
Aspectos históricos da Fundição Contínua e Tecnologias Relacionadas para o Aço
A tecnologia de lingotamento contínuo (CC) do aço, como método de processamento de solidificação do aço líquido, tem uma história relativamente curta — não muito mais longa do que a fabricação de aço com oxigênio. Diferente de outros processos na produção de aço, o lingotamento contínuo é o elo vital entre a fase líquida e a sólida e tem que conviver com efeitos metalúrgicos e desafios mecânicos ao mesmo tempo.
O lingotamento contínuo transforma o aço líquido em sólido de forma contínua e inclui uma variedade de importantes processos comerciais. Esses processos são a maneira mais eficiente de solidificar grandes volumes de aço líquido em formas simples para processamento posterior. O índice CC para a indústria siderúrgica mundial é agora de cerca de 96% da produção de aço bruto, que era de apenas 4% em 1970.
O lingotamento contínuo se distingue de outros processos de solidificação por sua natureza de estado estacionário. O aço líquido solidifica contra as paredes do molde enquanto é simultaneamente retirado do fundo do molde a uma taxa que mantém a interface sólido/líquido em uma posição constante com o tempo. O processo funciona melhor quando todos os seus aspectos operam dessa maneira de estado estacionário.
Em relação a outros processos de lingotamento, o lingotamento contínuo geralmente tem um custo de capital mais alto, mas um custo operacional mais baixo. É o método mais eficiente em termos de custo e energia para a produção em massa de produtos de aço semi-acabados com qualidade consistente em uma variedade de tamanhos e formas. As seções transversais podem ser retangulares, para laminação posterior em chapa ou chapa, quadradas ou circulares para produtos longos e tubos sem costura, e até mesmo em formato de osso de cachorro, para laminação em vigas I ou H.
Hoje, as máquinas de lingotamento contínuo consistem em pacotes tecnológicos/mecatrônicos modulares para permitir um design rápido e um tempo de execução de projeto curto, bem como um rápido aumento da produção após o primeiro calor ter sido fundido. Do ponto de vista metalúrgico, as máquinas de lingotamento contínuo de última geração possuem características que permitem o tratamento dos fios através de tecnologias especiais de resfriamento e redução suave. Modelos de processo sofisticados permitem simulação de processo on-line e controle de circuito fechado para otimizar ainda mais a qualidade do produto e as metas de produtividade. As unidades robóticas realizam tarefas em áreas perigosas e melhoram a confiabilidade operacional sem intervenção humana. A velocidade da inovação tem se destacado na fundição contínua desde o início da comercialização na década de 1950. Observam-se visões e as primeiras tentativas de desenvolvimento desse processo durante as décadas de 1960 e 1970, bem como benchmarks na década de 1980.
Durante a incubação bastante longa nos períodos precursores, ou seja, antes da década de 1950, importantes estímulos de desenvolvimento vieram da indústria de não ferrosos, que já havia aplicado processos CC - em particular, pelo princípio do molde viajante - usando rodas e/ou correias de fundição para superar atrito do molde. Mais tarde, ideias genuínas emanadas de fabricantes de aço adicionaram vários marcos à condução da aplicação de CC ao aço, embora principalmente por um processo baseado em um molde estacionário e oscilante.
Estágios iniciais no desenvolvimento do lingotamento contínuo
A ideia de tornar o processo de fundição mais produtivo através da continuidade é atribuída a J Laing que em 1843 patenteou nos EUA após testar com sucesso uma máquina para fundição contínua horizontal de tubos e chapas de ligas metálicas de baixo ponto de fusão. Nesta patente, Laing propôs a alimentação do metal líquido de um reservatório vertical através de uma calha para um molde horizontal pré-aquecido com um mandril inserido que girava em torno de seu eixo para evitar a aderência ao fundido. O tubo foi resfriado na saída do molde.
O desenvolvimento da fundição contínua é atribuído a Henry Bessemer que em 1857 sugeriu e patenteou no Reino Unido um dispositivo conhecido como twin roll caster. Neste dispositivo, o aço líquido foi derramado entre dois tambores resfriados a água, e a folha sólida resultante foi extraída através de placas guias curvas onde a folha foi cortada continuamente para medir e posteriormente extraída através de rolos de mola (Fig. 1). No entanto, Bessemer não buscou essa tecnologia presumivelmente dando maior prioridade ao desenvolvimento do processo de fabricação de aço primeiro.
Fig 1 Processo de fundição contínua proposto por Henry Bessemer
Demorou mais de 100 anos para que a fundição contínua de aço se tornasse uma tecnologia de produção em massa, mas com um design diferente da fundição de rolos duplos que foi aplicada em ligas leves em escala industrial.
Em tais desenvolvimentos posteriores, Bessemer implementou então um distribuidor com rolha para retenção de escória. O molde de 250 mm x 250 mm abaixo do distribuidor incorporou um aríete hidráulico para empurrar o lingote para cima para uma laminação direta do lingote sem reaquecimento. Este foi um precursor para fechar a extremidade inferior do molde com uma barra fictícia.
Goeran Fredrik Goeransson da Suécia introduziu uma panela com rolha para a transferência de aço líquido do vaso de sopro para o poço de vazamento através de uma talha em 1858. Este foi substituído por Henry Bessemer em 1859 com um dispositivo do tipo swing que foi a primeira torre de panela. O primeiro portão deslizante de concha foi concebido em 1885 por David D Lewis.
O próximo passo no desenvolvimento do lingotamento contínuo foi feito por Benjamin Atha em 1886. De acordo com seu pedido de patente, o molde alto, refrigerado a água e sem fundo foi conectado diretamente ao distribuidor, enquanto a barra fictícia apresentava uma cabeça em forma de garra e extraía o resultante tarugo de metal intermitentemente com rolos de retirada acionados. O método foi utilizado para a produção semi-comercial de tarugos de 100 mm quadrados no início do século XX, mas não chegou à produção em massa. Independentemente, RM Daelen patenteou em 1889 um aparelho similar (não usado de fato) com corte de cisalhamento em tempo real.
O primeiro rodízio construído por um fabricante de máquinas genuíno, Arthur McKee Co. de Cleveland, Ohio, em 1915 havia sido projetado por John T Rowley dos EUA já com dobra e não dobra e com tamanhos de tarugos de 45 mm x 45 mm a 75 mm x 75 mm em comprimentos que variam de 10 m a 50 m (sem corte em tempo real). Houve um controle errático do comprimento como consequência do atrito excessivo do molde, que causou a aderência e o rasgamento aleatório da casca.
O conceito de reciprocidade de um molde curto para cima e para baixo para reduzir o atrito do molde foi patenteado por Cornelius W. van Ranst dos EUA em 1921. Siegfried Junghans da Alemanha implementou a oscilação do molde pela primeira vez na década de 1930. Sua máquina de fundição contínua foi inicialmente usada em Wieland-Werke para a fundição de latão. O molde consistia em um tubo de cobre aberto em ambos os lados e cercado por uma camisa de água. O metal líquido foi alimentado pela parte superior e o metal solidificado foi retirado por rolos da parte inferior. Por um sistema especial, a alimentação do metal líquido foi ajustada à velocidade de retirada de tal forma que o nível do metal líquido foi mantido constante no molde. Essa foi uma parte importante da tecnologia e um exemplo vívido de que o processo CC oferece uma vantagem de automação e controle. O molde foi lubrificado e recebeu um movimento oscilante para cima e para baixo para evitar a aderência do metal sólido às paredes do molde. Esse recurso acabou sendo adotado para o lingotamento contínuo de aços. Serras voadoras foram posicionadas no poço abaixo da instalação para o corte contínuo dos tarugos no comprimento necessário. Tal esquema foi bem sucedido e foi amplamente utilizado para a fundição contínua de cobre e ligas de alumínio na Alemanha, EUA e na então URSS. O processo Junghan foi aplicado ao magnésio a partir de 1937 para a fundição de tarugos redondos de 200 mm de diâmetro para extrusão e placas de dimensões de até 100 mm x 600 mm. A Fig. 2 mostra o método Junghans de fundição contínua. Mais tarde, a Junghans adicionou pulverização de água diretamente no tarugo e fez muitas inovações em relação ao sistema adequado de alimentação e distribuição de metal líquido.
Fig 2 Método de fundição contínua de Junghan
Em comparação com a fundição em molde permanente usada anteriormente, o método Junghans teve as seguintes vantagens.
- Processo verdadeiramente contínuo com possibilidade de automação avançada que permitiu aumento de produtividade com menos mão de obra
- Regimes de fundição reprodutíveis que permitiram a qualidade reprodutível dos tarugos
- Melhor alimentação das porções centrais dos tarugos com solidez correspondentemente aumentada dos tarugos
- Estrutura mais uniforme em todo o tarugo
- Melhor remoção de gases durante o lingotamento através da porção líquida do tarugo
- Menos materiais descartados
No entanto, o método de Junghans não resolveu todos os problemas da fundição em molde permanente, principalmente devido à extração de calor ser predominante através das paredes do molde. Como resultado, o poço do tarugo era profundo, a casca solidificada estava sujeita a altos gradientes térmicos e a formação do entreferro exigia a manutenção de baixas velocidades de lingotamento ou, em outras palavras, maiores tempos de solidificação. Tarugos maiores (300 mm – 500 mm de diâmetro) foram caracterizados com estrutura e composição química não homogêneas (macrosegregação). Os moldes longos, necessários para o resfriamento adequado, exigiam um acabamento muito fino da superfície interna.
Para eliminar essas deficiências, foi necessário desenvolver uma tecnologia, onde o calor fosse extraído predominantemente pela parte sólida da fundição. Como resultado, o reservatório do fundido precisava ser mais raso com o perfil de solidificação necessário para ser mais plano. A macrossegregação, a falta de homogeneidade da estrutura e as tensões radiais precisavam ser muito menos pronunciadas. Essas necessidades foram atendidas com uma nova tecnologia desenvolvida quase simultaneamente e de forma independente na Alemanha e nos EUA. Esta tecnologia é conhecida como “tecnologia de resfriamento direto (DC)”. Esta tecnologia foi logo comercializada e utilizada em escala industrial. O processo de fundição DC de acordo com a tecnologia foi o seguinte.
O metal líquido foi derramado a partir do topo em um molde refrigerado a água aberto, relativamente curto, que no início foi fechado por baixo por um bloco fictício conectado a um sistema de abaixamento hidráulico ou mecânico. Depois que o nível de fusão no molde atingiu um certo nível, o aríete foi abaixado e a parte sólida do tarugo foi extraída para baixo. A vazão do metal líquido e a velocidade de fundição foram ajustadas de forma que o nível do líquido no molde permanecesse constante. Assim que a casca sólida emergia da parte inferior do molde, a água era aplicada na superfície em forma de spray ou filme de água. O resfriamento do tarugo sólido foi intensificado ainda mais, baixando-o em um poço cheio de água (o que também tornou o processo mais seguro, pois o metal líquido, em caso de sangramento, era resfriado rapidamente em grande quantidade de água). O processo foi semi-contínuo. Assim que o carneiro atingiu sua posição mais baixa no poço, a fundição foi interrompida e o tarugo foi removido do poço. A fundição DC tinha uma característica única que a torna muito distinta das tecnologias de fundição usadas anteriormente.
A solidificação ocorreu em uma estreita camada do fundido dentro e abaixo do molde. Durante o estágio estável de fundição, a forma e as dimensões desta região permaneceram constantes e reprodutíveis de um calor para outro. Ao controlar a distribuição do metal líquido durante a alimentação do molde, o resfriamento direto abaixo do molde e a velocidade de vazamento, a forma e as dimensões das regiões de solidificação podem ser mantidas dentro dos limites ótimos. Como essas formas e dimensões determinam os gradientes térmicos e são responsáveis pela fissuração, macrossegregação e homogeneidade da estrutura, a ocorrência desses defeitos também pode ser controlada. A fundição DC teve as seguintes vantagens sobre o método de fundição de Junghan.
- Segregação da linha central consideravelmente reduzida
- Aumento da densidade da porção central do tarugo
- Estrutura mais fina e homogênea com propriedades mecânicas correspondentemente melhoradas
- Melhor qualidade de superfície
- Menor custo de operação
A primeira máquina CC para metais não ferrosos foi instalada por Rossi, um empresário, em 1937 na Scovill Manufacturing Co. em Waterbury aplicou vários processos CC da época. O lingotamento contínuo (Fig. 3), com molde oscilante mais resfriamento direto com jatos de água abaixo parecia bastante simples, mas foi implementado um sistema elaborado para o fornecimento e alimentação do metal líquido. Estes incluíram (i) transferência de metal líquido totalmente encoberto da panela através de um funil para dois recipientes de retenção aquecidos e inertados por indução, dispostos em paralelo, (ii) a partir daí, transferência de metal líquido encoberto para uma calha de alimentação intermediária pequena e inerte por gás inerte pressão (garantindo a retenção completa da escória) através de dutos aquecidos por resistência, e equipado com um indicador de altura de metal, e (iii) então, alimentação por gravidade de metal líquido através de outro duto aquecido por resistência no molde protegido de gás. A Rossi garantiu uma operação de lingotamento ininterrupto de sete dias, o que foi alcançado desde o início do lingotamento contínuo.
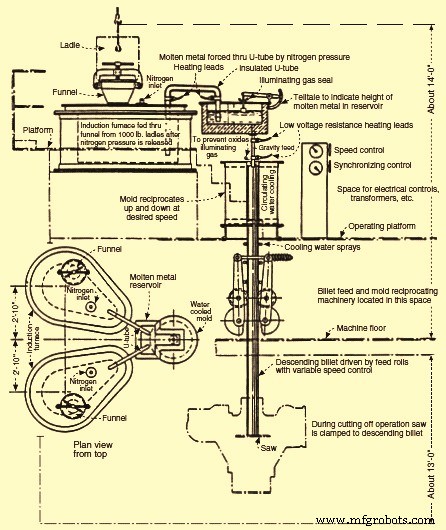
Fig 3 Rodízio Rossi com molde oscilante
Estimulados por esse exemplo bem-sucedido da indústria de não ferrosos, os esforços gradualmente se intensificaram para aplicar a tecnologia CC também ao aço. No entanto, a maioria desses desenvolvimentos foi fortemente restringida nos anos durante e logo após a Segunda Guerra Mundial. Muito poucos detalhes e detalhes operacionais surgiram durante este período devido ao ambiente de sigilo geral durante o período. Edward R. Williams, presidente da 'Vulcan Mold and Iron Co.', optou por um molde longo e estacionário e tentou reduzir o atrito do molde pela retirada intermitente do cordão. Seu pedido de patente incluía um suporte de esteira de rolos necessário na fundição de seções de laje. Ele, juntamente com a Republic Steel, iniciou um grande rodízio piloto em 1942 para tarugos de tamanho 100 mm x 100 mm, bem como mini lajes de tamanho 75 mm x 215 mm. Uma outra unidade piloto foi construída com Babcock e Wilcox em 1948, que foi equipada com recursos avançados como controle automático de nível de molde e supervisão de TV.
Com base em um molde fixo estacionário, muitos esforços contemporâneos semelhantes foram iniciados então nos EUA, na Grã-Bretanha, na Rússia (então URSS), no Japão, na Áustria e na França. Esses esforços de fundição foram prejudicados pelo atrito do molde e, portanto, tiveram menos sucesso do que a primeira fundição piloto de aço com o molde oscilante Junghans-Rossi. Em 1949 Junghans iniciou seu próprio piloto de caster, alimentado por um conversor I ton Bessemer. Depois de iniciar o rodízio, ele entrou em um acordo de cooperação com a Mannesmann, que iniciou seu rodízio piloto em Huckingen em 1950. Em 1952, os desenvolvedores da CC alemã e austríaca uniram forças, posteriormente nomeando a Demag como fabricante de máquinas em 1956, o que levou ao grupo sigla DMB, Demag-Mannesmann-Boehler.
Rossi, que ficou sozinho, forneceu sua primeira máquina de fundição de aço, construída pela Koppers Co., que foi iniciada em Allegheny Ludlum em 1949. Este rodízio era para seção de tarugos de tamanho redondo de 150 mm de diâmetro e mini laje de tamanho 75 mm x 380 milímetros. A Rossi deu garantias de produtividade de lingotamento de 20 toneladas por hora e qualidade do produto. Este rodízio está sendo considerado como a primeira tentativa de um rodízio comercial para aço. O rodízio é mostrado na Fig 4. Além das características vistas na Fig 4, este rodízio tinha proteção de gs inerte de tundish e molde, bem como pré-aquecimento de resistência do tubo de vazamento não submerso. Para eventual aplicação de um bocal de entrada submersa (SEN) na seção de laje fina, Rossi propôs e patenteou uma metade superior do molde em forma de funil, mas não a utilizou.
Fig 4 Primeiro rodízio com garantias de produção
Rossi formou a empresa de engenharia 'Continuous Metalcast Inc. com Allegheny e Koppers entre os acionistas e recebeu mais quatro pedidos de siderúrgicas especiais nos EUA, Inglaterra, Suécia e França. Para lidar com negócios no exterior, a Concast AG, Zurique, Suíça foi fundada por Rossi em 1954. Assim, dois grandes grupos rivais surgiram no projeto e fornecimento de rodízios no início da industrialização da CC, além de muitos esforços de construção de máquinas de menor capacidade. Um certo entendimento entre os dois grupos foi alcançado após a implementação do conceito de molde curvo quando o consórcio DMB e o grupo Concast formaram uma joint venture em 1963 chamada MBC (Mannesmann-Boehler-Concast) em Zurique.
Inicialmente, o desenvolvimento do CC em aço estava focado na fabricação de aços especiais, onde a economia potencial de rendimento acarretava a maior vantagem de custo. Além disso, a capacidade menor da panela foi mais compatível com a taxa de transferência de caster mais baixa. Outro obstáculo para a adoção do lingotamento contínuo por grandes produtores foi por causa das tentativas malsucedidas de produzir aços para aros com qualidades de superfície aceitáveis. Assim, os primeiros esforços na fundição de placas foram restritos à produção de aços de aços mortos de manganês-silício (Mn-Si). Apenas a conversão para aços mortos de alumínio (Al) e paralelamente melhorias nas qualidades da superfície dos fios abriram o caminho para uma aplicação mais ampla de lingotamento contínuo para produtos planos e longos. Nesse sentido, os desenvolvimentos na siderurgia secundária também se tornaram um pré-requisito vital, igualmente importante tanto para a produtividade do fundidor quanto para a qualidade do produto.
No decorrer do desenvolvimento das máquinas de lingotamento contínuo, vários tipos de lingotamentos foram realizados com diferenças significativas nas alturas de projeto (Fig. 5). Alguns desses tipos estavam tendo a produtividade de lingotamento restrita devido ao comprimento limitado do suporte (rodízios verticais) ou devido à velocidade de fundição limitada pelo alto atrito do molde (rodízios horizontais). Além disso, também houve diferenças de características com relação à qualidade do produto.
Fig 5 Tipos de máquinas de lingotamento contínuo
A máquina de fundição vertical foi o projeto da máquina natural, fundindo com gravidade e também garantindo uma macroestrutura simétrica; mas a produtividade do caster foi severamente limitada pela altura da máquina. Assim, vários esforços na história do CC foram notáveis para estender o comprimento da máquina em baixa altura de construção por meio de flexão e endireitamento de cordões, por exemplo. o lançador de tarugos de Rowley e uma proposta mais avançada de Tarquinee e Scovill. Para evitar rachaduras internas, várias regras para o projeto de caster, com base na deformação crítica e na taxa de deformação na interface sólido/líquido, foram desenvolvidas, o que levou a zonas distintas de flexão e endireitamento que se estendem por vários pares de rolos.
Com o advento do princípio de fundição de molde curvo, introduzido simultaneamente pelos testes pioneiros da fábrica de Mannesmann Huckingen e Von Moos Stahl em 1963, a altura necessária do edifício foi substancialmente reduzida. Esse tipo de lingotamento iniciou um rápido crescimento da aplicação de CC no caso de lingotamento contínuo de tarugos e blocos, especialmente em pequenas fundições de tarugos que poderiam usar os edifícios existentes. Na fundição de placas, no entanto, o uso generalizado do projeto de moldes curvos foi claramente interrompido nos últimos anos devido ao acúmulo acentuado de macroinclusões e/ou bolhas de argônio em um quarto de banda. Assim, além das novas máquinas de fundição que agora são construídas exclusivamente como molde reto/dobrador, as máquinas de molde curvo existentes estão sendo cada vez mais renovadas.
Desde o início do desenvolvimento do CC, uma grande preocupação era o controle da temperatura do aço líquido. Este foi um grande obstáculo para pequenas capacidades de panelas com grande relação superfície/volume. Embora os primeiros fundidores piloto fossem alimentados diretamente dos fornos de fusão ou espera, isso não era prático para uma operação em grande escala. Uma abordagem anterior adotada por Halliday na Barrow Steel Works na Inglaterra nessa direção foi o uso de uma concha de despejo de lábios completamente fechada que poderia ser aquecida durante a fundição por um queimador de jato de lata através da tampa da concha, permitindo um tempo de fundição de até 2 horas a partir de uma concha de 7 toneladas. Halliday também insistiu no pré-aquecimento da panela de alta temperatura. Para capacidades maiores, as panelas de derramamento de lábios não eram práticas, então panelas com controle de fluxo de rolha foram introduzidas. No entanto, o uso do controle da rolha não foi bem adequado ao aumento do tempo de residência do metal. Assim, um grande avanço na confiabilidade operacional e na produtividade dos rodízios foi alcançado com a implementação do portão deslizante da panela.
Desde a década de 1980, um grande número de desenvolvimentos ocorreu para melhorar o desempenho da tecnologia de lingotamento contínuo de aços. Essas melhorias ocorreram em tratamentos panela de aços líquidos, transferência panela para distribuidor e distribuidor para molde de metal líquido, no distribuidor (metalurgia do distribuidor), em moldes e resfriamento primário (agitação eletromagnética etc.), em resfriamento secundário e suporte de metal fundido (agitação eletromagnética e resfriamento por névoa de ar etc.), corte e resfriamento do aço fundido (camas de resfriamento tipo turnover) e automação e controle do processo. A Fig. 6 apresenta exemplos típicos de sistema especialista e agitação eletromagnética.
Fig 6 Exemplos típicos de sistema especialista e agitação eletromagnética
Processo de manufatura
- Inclusões em aço fundido contínuo e sua detecção
- Automação, Instrumentação e Modelagem de Lingotamento Contínuo de Aço
- Pós para moldes de fundição contínua
- Tundish e seu papel na fundição contínua de aço
- Fundamentos de Fundição Contínua de Aço
- Papel do Molde na Fundição Contínua de Aço
- Fases no Projeto e Construção de uma Usina Siderúrgica
- Aço inoxidável:os melhores produtos para corte, retificação e acabamento
- Classes de aço ferramenta para punções e matrizes
- Aço doce, aço inoxidável e aço ferramenta:qual é o melhor material para sua aplicação?