Pós para moldes de fundição contínua
Pós de molde de fundição contínua
Os pós de molde de lingotamento contínuo são usados principalmente para facilitar a passagem do aço líquido através do molde da máquina de lingotamento contínuo. Também é conhecido por vários outros nomes, como pó de molde, pó de fundição, fluxo de molde, escória de fluxo de molde ou pó de fluxo de molde. O pó de molde desempenha um papel importante no lingotamento contínuo do aço líquido e é um dos fatores mais influentes e críticos na estabilidade do processo de lingotamento e para o lingotamento suave do aço líquido.
O pó de molde melhora o desempenho do processo de fundição e reduz os defeitos de superfície. As principais funções do pó de molde são (i) proteger o aço líquido contra oxidação, (ii) fornecer lubrificação para o aço solidificado, (iii) controlar, otimizar e isolar a transferência de calor do aço líquido para o molde e o ambiente nas direções horizontal e vertical, (iv) para absorver as inclusões do aço líquido para produzir um produto de aço fundido mais limpo, e (v) para fornecer proteção química ao aço líquido contra oxidação e outras reações indesejadas. A alta basicidade do pó de molde aumenta sua capacidade de assimilar inclusões não metálicas.
Quando o lingotamento contínuo de aço líquido começou na década de 1950, a lubrificação e a transferência de calor entre a carcaça de aço e o molde foram fornecidas pelo uso do óleo de semente de colza. Nos primórdios, quando o lingotamento contínuo de aço líquido começou, o aço líquido era fundido em fluxo aberto usando óleos do tipo colza para lubrificar o molde. No entanto, a qualidade da superfície dos produtos fundidos era ruim devido à falha dos óleos do tipo colza em fornecer isolamento térmico adequado, proteção contra a reoxidação do aço e falha em atuar como um fluxo para impurezas como a alumina. Com o advento do bocal de entrada submerso (SEN) no lingotamento contínuo de aço, o uso de óleos apresentou um novo problema adicional, pois nas plaquetas de aço congeladas, os crânios cresceriam ao redor do bocal submerso até se tornarem grandes o suficiente para romper o SEN.
Os pós de molde foram desenvolvidos na tentativa de superar os problemas encontrados com óleos do tipo colza. Este desenvolvimento tem sido considerado por muitos como um desenvolvimento de “tentativa e erro”. Os pós de molde à base de cinzas volantes foram introduzidos em 1968. Inicialmente, os pós de molde eram misturas físicas de materiais como cinzas volantes, escória de alto forno (BF), espatoflúor, carbonatos alcalinos e criolita. Esses pós têm um efeito muito positivo nas perdas de calor e as temperaturas de superaquecimento do aço líquido podem ser reduzidas. Esses pós também "molharam" tanto o molde quanto a casca. Esses pós também tiveram efeito positivo nos parâmetros de fundição que, por sua vez, melhoraram a qualidade do produto fundido. No entanto, os pós à base de cinzas volantes usados para lubrificar e proteger o aço líquido não foram eficientes, pois as cinzas volantes têm composição variável. Portanto, houve a necessidade de misturar cuidadosamente as cinzas volantes com calcário, carbonato de sódio e fluorita (CaF2) para obter uma composição reprodutível do pó de molde. Isso levou ao desenvolvimento de pó de molde sintético por volta do início dos anos 80. O desenvolvimento contínuo do pó de molde desde a sua primeira introdução tornou a fundição contínua de muitas seções de aço como rotina.
Hoje, muitos tipos de pós de molde com diferentes composições e formas (granular, em pó e pós extrudados) são produzidos para atender a fundição de diversos graus e tamanhos de aço. Os fatores que influenciam as propriedades dos pós de molde são (i) composição química, (ii) composição mineralógica, (iii) composição do tamanho de grão, (iv) processo de fabricação, (v) método de secagem ou torrefação e (v) teor de carbono livre . Cada forma e tipo de pó tem suas próprias vantagens e desvantagens, como preço, problemas de saúde, fluidez, isolamento térmico e taxa de fusão. A escolha do pó requer um profundo conhecimento do processo de fundição, composição do aço líquido, preferências desejadas e viáveis, características do processo e do produto.
Pós de molde são misturas mecânicas de vários óxidos metálicos e fluoretos contendo pequenas quantidades de carbono para regular sua taxa de fusão. Durante a fusão do pó, os óxidos e fluoretos reagem para formar um líquido que produz óxidos complexos e oxifluoretos após o resfriamento. A extensão em que essas fases afetam as propriedades de lubrificação e transferência de calor da escória depende da composição química do pó original. Com um número tão grande de componentes químicos no pó de molde, é difícil comparar o desempenho dos diferentes pós com base na composição.
A composição dos pós de molde difere de acordo com a aplicação, grau de aço e produto desejado. No entanto, alguns componentes são considerados os principais constituintes dos pós de molde. Os componentes que caracterizam a composição são (i) uma mistura de CaO e SiO2 que é cerca de 70% da composição com CaO na faixa de 22% a 45% e SiO2 na faixa de 17% a 56%, (ii) A razão CaO/SiO2 normalmente na faixa de 1 a 1,3 com alguns pós tem razão de basicidade como 0,8, (iii) MgO em torno de 0% a 10%, (iv) Fe2O3 em torno de 0% a 6%, (v) Al2O3 em torno de 0% a 13%, (vi) Na2O em torno de 0% a 25%, (vii) K2O em torno de 0% a 2%, (viii) flúor em torno de 2% a 15%, (ix) TiO2, B2O3, ZrO2, Li2O e MnO que são adicionados aos pós de acordo com a necessidade da aplicação e, portanto, a quantidade pode variar muito, e (x) C em torno de 2% a 20%.
O flúor (F) no pó de molde tem uma grande influência nas propriedades do pó de molde e também tem um efeito perigoso no meio ambiente. As vantagens do flúor são (i) reduz o ponto de fusão do pó de molde e, portanto, aumenta a propriedade lubrificante do pó de molde, (ii) diminui a viscosidade do pó de molde e, portanto, ajuda na formação de filme de escória contínuo e estável, e (iii) melhora a cristalização do filme em pó. As desvantagens do flúor são (i) há emissão de componentes voláteis como SiF4 e NaF, e (ii) reage com água de resfriamento levando à formação de HF.
A viscosidade, ponto de solidificação, ponto de fusão e velocidade de escória são consideradas propriedades importantes para os pós de molde. Os pós de molde devem ter baixa viscosidade, baixa temperatura liquidus e taxa de fusão que corresponda à velocidade do lingotamento contínuo. Às vezes, torna-se necessário prestar atenção à densidade e à química do pó do molde durante a fundição de certos tipos de aço. A propriedade de isolamento térmico do pó de molde é controlada através da densidade aparente, tamanho de partícula e tipo de carbono. O efeito da composição química em algumas das principais propriedades do pó de molde é mostrado na Tab 1.
Tab 1 Efeito da composição química na propriedade do pó de molde | ||||
Sl. No. | Composto/elemento | Viscosidade | Ponto de solidificação | Ponto de fusão |
1 | CaO | Diminuir | Aumento | Aumento |
2 | SiO2 | Aumento | Diminuir | Diminuir |
3 | CaO/SiO2 | Diminuir | Aumento | Aumento |
4 | Al2O3 | Aumento | Diminuir | Aumento |
5 | Na2O | Diminuir | Diminuir | Diminuir |
6 | F | Diminuir | Aumento | Diminuir |
7 | Fe2O3 | Diminuir | Diminuir | Diminuir |
8 | MnO | Diminuir | Diminuir | Diminuir |
9 | MgO | Diminuir | Diminuir | Diminuir |
10 | B2O3 | Diminuir | Diminuir | Diminuir |
11 | BaO | Diminuir | Diminuir | Diminuir |
12 | LiO2 | Diminuir | Diminuir | Diminuir |
13 | TiO2 | Sem alteração | Aumento | Aumento |
14 | K2O | Diminuir | Diminuir | Diminuir |
Existem requisitos específicos de pó de molde para se adequar à composição do aço. Esses requisitos são apresentados a seguir.
- Aço morto com alumínio de baixo carbono requer pó de molde que pode absorver a inclusão de Al2O3 sem qualquer efeito adverso na viscosidade. O pó de molde deve ter boas propriedades isolantes, boa absorção de não metálicos e propriedades estáveis. A estabilidade do pó de molde é a capacidade de absorver Al2O3 sem qualquer efeito adverso na viscosidade.
- Aços carbono com carbono na faixa de 0,1% a 0,18% são propensos a trincas. A alta temperatura de solidificação do pó do molde reduz o calor através do molde. Para uma lubrificação adequada, é necessária baixa viscosidade do pó do molde.
- Os aços carbono com teor de carbono superior a 0,18% também precisam de pós de molde de baixa viscosidade, baixa densidade e baixo ponto de fusão. Esses pós devem ter boas propriedades isolantes, teor correto de carbono e boa capacidade de lubrificação.
- Os aços com baixo teor de carbono precisam de pós de molde que possam absorver inclusões não metálicas, melhorar o isolamento, fornecer boa lubrificação e ter propriedades estáveis e aprisionamento mínimo de escória. O pó de fundição não deve causar acúmulo de carbono no aço.
Os pós de mofo hoje são amplamente classificados em três grupos:(i) à base de cinzas volantes, (ii) sintéticos e (iii) material pré-fundido ou fritado. Pós de molde à base de cinzas volantes são misturas mecânicas de matérias-primas como bauxita, cal, espatoflúor etc. com cinzas volantes em pó como o componente principal. Os pós sintéticos são simplesmente misturas de matérias-primas em pó nas proporções desejadas. Os pós de moldes pré-fundidos, normalmente utilizados para a fundição de aços de qualidade de estampagem profunda mortos com alumínio, são misturas que são fundidas e calibradas após a mistura mecânica das matérias-primas. Os pós de molde são fornecidos em diferentes formas, nomeadamente pós, granulados, extrudados e grânulos em expansão. Cada tipo de pó de molde tem suas próprias vantagens e desvantagens relacionadas ao custo, fluidez, isolamento térmico, taxa de medição e riscos à saúde. Os pós são mais baratos que os granulados, mas os pós finos apresentam problemas de saúde. Há também alguma falta de homogeneidade nos suprimentos, uma vez que os finos tendem a se depositar no fundo do contêiner. Diferentes tipos de pós de molde são descritos abaixo.
Pós de cinzas volantes – Esses pós são misturas mecânicas nas quais as cinzas volantes em pó são um componente significativo da mistura. Nesses pós, as cinzas volantes são misturadas com diferentes minerais. Como a composição das cinzas volantes varia muito, isso restringiu a produção e o uso desse tipo de pó.
Pós sintéticos – Esses pós são misturas mecânicas de muitos minerais em pó fino. Estes são feitos com mistura de alto cisalhamento. É desejável usar matérias-primas com pontos de fusão semelhantes. É preferível usar quantidades mínimas de matérias-primas para obter a composição necessária, pois simplifica a garantia de qualidade. Além disso, as matérias-primas que apresentam problemas de saúde não devem ser usadas.
Pós pré-fundidos – Esses pós possuem uma porção considerável de materiais que foram pré-fundidos e dimensionados. A introdução de pós pré-fundidos é feita para melhorar a uniformidade e a composição química.
Pós granulados – Esses pós têm a forma de grânulos esféricos ou extrudados. Esses grânulos têm muito menos poeira do que os pós de molde. Os grânulos esféricos são particularmente adequados para aplicação automática. Os pós de molde granulados são produzidos por secagem por pulverização, enquanto os pós extrudados são produzidos por extrusão. Esses pós têm melhor controle de qualidade e menores problemas de risco à saúde. Os grânulos de expansão contêm um agente de expansão. Durante o aquecimento dos grânulos, o agente de expansão altera a forma dos grânulos e reduz a fluidez do pó no topo do molde.
Pós iniciais – Às vezes são usados no início da fundição para fornecer uma poça de escória rapidamente formada. Esses pós têm baixo ponto de fusão, alto teor de óxido de sódio (Na2O) e frequentemente contêm agentes exotérmicos, como silicato de cálcio e uma pequena quantidade de carbono (menos de 1%). Os pós iniciais devem ser usados apenas quando houver necessidade.
Durante o lingotamento contínuo, o aço líquido é continuamente derramado do distribuidor para o molde oscilante. O molde de cobre é resfriado com água. Para proteger o aço líquido da oxidação e da aderência ao molde, é usado o pó de molde. O pó do molde é adicionado continuamente na superfície superior do aço líquido dentro do molde, o que pode ser feito manualmente ou automaticamente. Este pó de molde forma uma camada com uma profundidade total de 100 mm a 150 mm. Devido à alta temperatura do aço líquido, bem acima do ponto de fusão do pó, forma-se um gradiente de temperatura na direção vertical através do pó. Na parte superior há o pó de molde recém-adicionado, formando uma camada de pó. Na adição do pó de molde, diferentes camadas de pó de molde que são formadas são mostradas esquematicamente na Fig1. O mecanismo de formação dessas camadas é descrito abaixo.
- O pó de molde aquece e perde algum carbono por reação com o oxigênio. A remoção da água ocorre à medida que a temperatura aumenta e o pó do molde forma uma camada sinterizada.
- O pó do molde derrete a uma taxa definida e forma camadas sinterizadas (mole) e líquidas. A camada líquida atua como um reservatório para fornecer pó líquido ao fio. Esta piscina de líquido deve ser mais profunda do que o comprimento do curso para garantir uma boa lubrificação.
- O pó do molde forma um filme de pó sólido através da primeira infiltração do pó líquido no espaço do molde/fio. Este filme de pó sólido é de natureza vítrea e normalmente tem 2 mm a 4 mm de espessura. Este filme sólido cristaliza posteriormente nas regiões de alta temperatura adjacentes à fita.
- O pó de molde forma um filme de pó líquido tipicamente de 0,1 mm de espessura. Esta escória líquida é puxada para dentro da abertura ao longo da carcaça de aço e lubrifica o cordão. Essa lubrificação evita que o aço adira ao molde, eliminando assim a causa da quebra do cordão.
O pó no menisco normalmente consiste em quatro camadas, a saber (i) uma camada de pó escuro não reagida, não derretida na parte superior, (ii) uma camada sinterizada, semirreagida, (iii) uma zona pastosa na qual o pó de molde está derretendo, e (iv) uma camada de escória derretida diretamente no aço líquido. O processo de lubrificação é quase totalmente realizado dentro desta última camada mencionada e depende de muitos fatores. Normalmente os fluxos com menor viscosidade e/ou temperatura de fusão tendem a proporcionar menor atrito, melhores propriedades de lubrificação e, portanto, evitar a aderência.
Fica claro pela Fig 1 que, passando do aço líquido para a superfície externa do pó, existem três camadas diferentes que podem ser definidas de acordo com seu estado de agregação e estado físico. Cada um deles existe para uma determinada faixa de temperatura. Por outro lado, movendo-se do aço líquido para o molde resfriado, surgem outras camadas, que podem ser previstas pela curva de fusão. As propriedades do filme em pó ditam as principais funções de lubrificação do fio e transferência de calor do molde. De acordo com a composição química e as propriedades físicas, dois mecanismos principais podem ocorrer:cristalização e vitrificação. A formação de cristais é favorável para uma transferência de calor homogênea e controlada (horizontal) durante a fundição, o que é necessário para evitar a formação de trincas superficiais.
Mas os pós de molde que são diretamente expostos ao aço líquido também sofrem um aquecimento instantâneo que é capaz de fornecer condições térmicas muito distantes do estado termodinâmico. Os pós normalmente têm um comportamento vítreo neste caso.
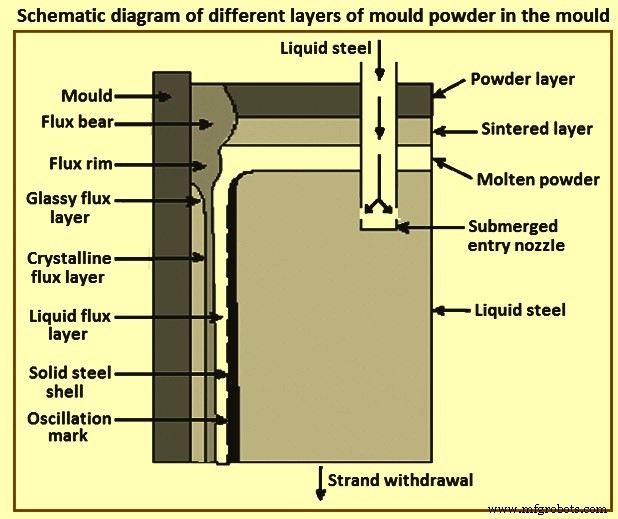
Fig 1 Diagrama esquemático de diferentes camadas de pó de molde no molde
Processo de funcionamento do pó de molde
A parte inferior do pó de molde começa a sinterizar e forma uma camada sinterizada. No entanto, o pó que está em contato mais próximo com o aço líquido derrete devido à alta temperatura e resulta em uma poça de pó líquido no topo do aço líquido dentro do molde. Nas faces estreitas e largas do molde, o pó líquido penetra no espaço estreito entre o menisco de aço e a parede do molde. Uma camada sólida de escória vítrea é formada quando a escória líquida é temperada na parede do molde refrigerada a água. Se mais pó for adicionado a esta camada, ou quando ocorrer o pré-aquecimento, há uma probabilidade de formação de fases cristalinas na camada. Devido à maior taxa de transferência de calor na parte superior do molde, uma camada de escória chamada rim é formada no topo do menisco e ao redor do molde. A estrutura da camada de escória sólida faz parte do controle do fluxo de calor horizontal, ou seja, a taxa de resfriamento do aço, está diretamente relacionada ao número de defeitos superficiais que ocorrem no produto final de aço. A temperatura na superfície do aço sólido está acima do ponto de fusão do pó do molde em todo o comprimento do molde. Como resultado, uma camada de pó líquido está presente entre as camadas de pó sólido e o invólucro de aço (cordão). Esta camada é crucial para manter um baixo atrito entre o cordão e o molde e, portanto, evitar a aderência da carcaça de aço
As camadas de aço líquido mais próximas do molde começam a solidificar. A qualidade e caracterização desta concha é de extrema importância. Portanto, é essencial controlar e otimizar a estabilidade e a qualidade da casca solidificada. Isso pode ser feito ajustando a velocidade de fundição, velocidade de oscilação do molde, transferência de calor e propriedades do pó do molde, como taxa de fusão, composição e viscosidade, etc. O pó do molde que cobre o aço líquido forma uma camada de pó líquido. Acima desta camada está uma camada sinterizada rica em carbono e acima desta o pó não fundido. Espera-se que o pó de molde cumpra várias funções como (i) proteção do metal contra a oxidação pelo ar, (ii) isolamento térmico para evitar a solidificação parcial na superfície, (iii) absorção de inclusões que sobem até a superfície, (iv) lubrificação do contato entre o metal e o molde, e (v) permitir a transferência homogênea de calor entre o cordão e o molde conforme as condições de fundição.
Durante a oscilação do molde, o pó líquido formado na superfície do aço líquido se infiltra entre o cordão de aço e o molde para atuar como lubrificante e também para regular a extração de calor do cordão para o molde. Se o calor é dissipado muito lentamente, uma casca de aço muito fina é formada pelo cordão e pode ocorrer um ‘breakout’, ou seja, a casca de aço se rompe, logo abaixo do molde, pois não pode sustentar a pressão ferro-estática do aço líquido. Por outro lado, se a taxa de remoção de calor for muito alta, trincas longitudinais podem aparecer no produto fundido.
Caracterização do pó do molde
A caracterização física desempenha um papel importante no processo de seleção e na avaliação operacional. Em geral, a composição química, a viscosidade incluindo o início da cristalização e o comportamento de fusão são considerados para a caracterização do pó de molde.
viscosidade – A viscosidade de um pó de molde influencia a infiltração do pó de molde durante a fundição. Em geral, a infiltração aumenta com a diminuição da viscosidade do pó de molde para as mesmas condições de operação. As janelas de operação para a viscosidade são baseadas principalmente em regras práticas, mas outras exigências, como o controle do aprisionamento de pó, também desempenham um papel importante ao definir a viscosidade necessária de um pó de molde.
Comportamento de derretimento – O comportamento de fusão de um pó de molde influencia fortemente tanto a profundidade da poça de líquido quanto a sensibilidade em relação à formação do aro / urso. O comportamento de fusão pode ser descrito pela trajetória de fusão e pela velocidade de fusão. Em ambos os casos, as adições de carbono livre são consideradas um fator principal. O outro parâmetro principal é a condição de fluxo no molde, ou seja, a estabilidade do menisco durante a fundição. A profundidade da poça de líquido resulta dos valores equilibrados da alimentação e da infiltração do pó de molde.
Trajetória de fusão – A trajetória de fusão do pó do molde é determinada usando um microscópio de platina quente. Os resultados são normalmente dados como valores para as temperaturas de amolecimento, fusão e fluxo.
Velocidade de fusão – A velocidade de fusão dos pós de molde é determinada usando o chamado método de amolecimento. Com este método, o deslocamento de um cilindro pré-prensado de pó de molde é medido em função do tempo a uma temperatura fixa (1400°C). O método produz resultados qualitativos que podem estar relacionados com a composição do pó de molde, isto é, o teor de carbono livre de um pó de molde.
Processo de manufatura
- Lã de aço
- Tesoura
- Zinco
- Aço inoxidável
- Inclusões em aço fundido contínuo e sua detecção
- Automação, Instrumentação e Modelagem de Lingotamento Contínuo de Aço
- Resfriamento por névoa de ar em lingotamento contínuo
- Tundish e seu papel na fundição contínua de aço
- Fundamentos de Fundição Contínua de Aço
- Processo de fundição de aço inoxidável