Entendendo a injeção de carvão pulverizado em alto-forno
Compreendendo a injeção de carvão pulverizado em alto-forno
A injeção de carvão pulverizado (PCI) é uma tecnologia bem estabelecida para a produção de metal quente (HM) em um alto-forno (BF). É praticado na maioria dos BFs e todos os novos BFs são normalmente construídos com capacidade PCI. A composição e as propriedades do carvão utilizado para injeção podem influenciar a operação, estabilidade e produtividade do BF, a qualidade do HM e a composição do gás BF. Os carvões usados para o PCI estão descritos no artigo no link ‘http://www.ispatguru.com/coal-for-pulverized-coal-injection-in-blast-furnace/’.
Os aspectos críticos dos sistemas PCI incluem a preparação do carvão, seu armazenamento e distribuição para garantir a alimentação uniforme do carvão para cada ventaneira sem flutuações na taxa de entrega do carvão e sua combustão através do projeto da lança e injeção de oxigênio (O2).
Preparação de carvão
A pulverização do carvão é realizada em moinhos únicos ou múltiplos (pulverizadores), dependendo dos requisitos. A moagem e distribuição do carvão para as lanças de injeção constituem um custo operacional importante. O carvão recuperado do armazenamento de carvão é peneirado para a remoção do material estranho e qualquer grande pedaço de carvão é triturado. O carvão é então alimentado no moinho onde é pulverizado e seco. O carvão do tamanho necessário é transportado para fora do moinho pelo fluxo de gás quente, coletado em um filtro de mangas e transportado para as caixas de armazenamento. A moagem e o transporte são realizados em atmosfera inerte para minimizar o risco de ignição das partículas de carvão seco. A distribuição granulométrica resultante do carvão pulverizado afeta sua manuseabilidade em equipamentos de transporte pneumático e, em altas taxas de injeção, sua combustibilidade.
Os pulverizadores trituram o carvão em uma das duas frações de tamanho, a saber (i) carvão pulverizado onde cerca de 70 % a 80 % do carvão está abaixo de 75 mícrons (micrômetros) e o restante está abaixo de 2 mm, e (ii) carvão granular que tem um tamanho de topo de 2 mm a 3 mm com um limite de 2 % de carvão acima de 2 mm e 20 % a 30 % abaixo de 75 mícrons. Os sistemas que injetam esse tamanho de carvão são chamados de injeção de carvão granular (GCI). A moagem mais grossa tem a vantagem de menores custos de moagem e secagem com o carvão moído mais fácil de manusear. A moagem mais fina tem um desgaste maior na pista. PCI é uma tecnologia mais popular que o GCI.
A finura do carvão pode ser variada no pulverizador por uma série de medidas que incluem a variação da taxa de alimentação do carvão, as configurações do classificador ou a taxa de fluxo de ar. Embora os moinhos possam ser ajustados para se adequar a um carvão específico para produzir o tamanho necessário, isso não é prático no caso de uma mistura de carvão onde um grande número de carvões está sendo usado. Nesse caso, alguns dos constituintes do carvão podem não atingir a finura necessária.
Uma das funções do pulverizador é remover o máximo de umidade possível do carvão. A secagem é necessária, pois a umidade causa problemas de fluxo livre tanto no sistema de transporte pneumático quanto nos silos de armazenamento. Além disso, a umidade precisa ser minimizada, pois é necessária energia adicional para sua remoção no BF e a injeção de umidade aumenta a taxa de redutor. Além disso, carvões com maior umidade consomem mais energia nos pulverizadores durante sua moagem e reduzem o rendimento.
A evaporação da umidade da superfície do carvão evita problemas de aglomeração dentro do pulverizador, uma vez que carvões com alto teor de umidade e argila são mais propensos a grudar. Portanto, normalmente é necessário reduzir o teor de umidade total do carvão em torno do nível de umidade de equilíbrio para reduzir os problemas de manuseio dentro do moinho e das caixas de armazenamento. O teor de umidade do carvão que sai do moinho deve ser dois terços do nível de umidade de equilíbrio. A umidade de equilíbrio do carvão varia com sua classificação, composição maceral e teor de cinzas.
É importante garantir que o carvão seja moído até a finura desejada com o mínimo desgaste das peças do pulverizador e com o menor consumo de energia para reduzir os custos operacionais. O desgaste influencia nas paradas e manutenção dos pulverizadores. As propriedades do carvão que influenciam o desgaste incluem o teor e a composição das cinzas, a distribuição do tamanho das partículas, a umidade e a densidade aparente. O maior teor de umidade do carvão acelera o desgaste devido aos efeitos combinados de desgaste e corrosão. Os minerais abrasivos (duros) nas cinzas de carvão incluem sílica (SiO2) e pirita (FeS2). Além do desgaste dos elementos de moagem, os minerais abrasivos também podem erodir os tubos e dutos. O teste mais comumente usado para avaliar as propriedades de abrasão do carvão é o ‘Índice de Abrasão’ (AI). Normalmente, espera-se que carvões com alta IA causem taxas de desgaste mais altas.
A redução no consumo de energia do moinho reduz os custos operacionais. O consumo de energia e a capacidade (rendimento) do moinho dependem de seu projeto, configurações do moinho, a finura necessária e as propriedades do carvão. Quanto maior a redução no tamanho do carvão necessária, maior é o consumo de energia necessário. Um nível mais alto de finura do carvão requer maior capacidade do moinho, o que também pode ser necessário ao moer carvões difíceis.
A principal propriedade do carvão que tem a principal influência no consumo de energia e capacidade do moinho é a dureza, determinada pelo ‘índice de moagem Hardgrove’ (HGI). Normalmente, quanto maior o HGI, mais fácil é a moagem do carvão, com conseqüente menor consumo de energia e maior rendimento. Se a capacidade de projeto do pulverizador estiver limitando a taxa de PCI, é possível aumentar as taxas de injeção mudando para um carvão mais macio. Aumentando a porcentagem de baixa matéria volátil (MV), carvão macio de alto poder calorífico (CV) no alto VM, a mistura de carvão ajuda a aumentar a capacidade do pulverizador, além de diminuir a pressão de explosão no BF e melhorar o consumo de carvão.
A composição maceral também afeta a moagem. Em geral, carvões de vitrinita mais altos tendem a ter menores requisitos de energia de moagem do que carvões de vitrinita mais baixos, uma vez que a vitrinita é mais facilmente moída do que a inertinita e a liptinita. O efeito da classificação diminui acima de uma refletância de cerca de 1,6, onde a energia de quebra necessária para vitrinita e inertinita é aproximadamente a mesma.
Os carvões são geralmente misturados para otimizar as forças relativas. No entanto, blendas não se comportam como uma média de seus componentes, mas podem ser afetadas desproporcionalmente por um carvão com características problemáticas. A moagem preferencial do carvão mais macio ocorre quando misturas de dois carvões cujo HGI difere em mais de 20 são pulverizados. A pulverização de blendas de carvões “duro” e “mole” mostrou que as características ruins dos carvões constituintes tendem a dominar a mistura, com o desempenho do pulverizador mais próximo ao do carvão mais duro. A moagem preferencial dos macerais mais macios também pode ocorrer na moagem de blendas. Carvões contendo argilas expansivas podem absorver a umidade depois de saírem do pulverizador e esfriarem. Mesmo quando presentes como componente de uma mistura, tais carvões podem levar a bloqueios nos sistemas de injeção.
Sistema de injeção de carvão
O sistema de injeção transporta e mede pneumaticamente o carvão pulverizado do silo de armazenamento através do vaso injetor, onde é pressurizado até ou acima da pressão BF, até as lanças de injeção da ventaneira. As lanças injetam o carvão em quantidades iguais através das ventaneiras, que são dispostas simetricamente ao redor da circunferência do BF. Um fator crítico no projeto do sistema de distribuição é garantir uma alimentação uniforme de carvão para cada ventaneira sem flutuações na rota de entrega do carvão. Qualquer interrupção no fornecimento de carvão pode levar rapidamente a sérios problemas. Quanto maior a taxa de injeção, mais graves são as consequências de uma interrupção não planejada.
São necessários pelo menos dois vasos de injeção para fornecer um fluxo contínuo de carvão para o BF. Basicamente, existem dois arranjos diferentes desses vasos a saber:(i) arranjo serial onde o vaso superior reabastece periodicamente o inferior, que é sempre mantido sob pressão, e injeta o carvão, e (ii) arranjo paralelo onde os dois vasos injetam alternadamente com uma operação sobreposta para manter a injeção de carvão durante o período de transição.
É importante controlar a quantidade de carvão injetado. Assim, os recipientes injetores são continuamente pesados e a vazão do carvão é cuidadosamente controlada. Os problemas de manuseio do carvão pulverizado nos silos de armazenamento que alimentam os vasos de injeção e dutos são devidos às quantidades de umidade e partículas ultrafinas e à presença de argilas no carvão. Aquecedores externos e/ou isolamento podem ser necessários para reduzir a probabilidade de bloqueios do silo devido à condensação de umidade que pode ocorrer no interior das paredes do silo. Em alguns lugares, o nitrogênio (N2) é soprado através de almofadas de aeração no fundo do tanque de injeção intermediário para garantir o fluxo livre quando o carvão pulverizado é transferido para o tanque de injeção inferior.
O carvão dos vasos de injeção é geralmente transportado por (i) tubulações individuais para cada ventaneira, caso em que a quantidade de carvão é controlada e carregada independentemente em cada tubulação, (ii) uma tubulação comum para um distribuidor adjacente ao BF, caso em que, o distribuidor divide igualmente o carvão nos tubos individuais que levam a cada ventaneira. Uma vantagem deste sistema é que a distância entre a planta de preparação de carvão e BF pode ser maior do que com o sistema de tubulação individual.
Diferenças no encaminhamento dos tubos para as ventaneiras e a inevitável divisão desigual do carvão nos pontos de divisão podem resultar em uma alimentação desigual nas ventaneiras. Desequilíbrios também podem causar desgaste desigual nas tubulações e no distribuidor.
Dependendo da proporção de carvão para o gás de transporte, o carvão é transportado pneumaticamente do recipiente de injeção para as ventaneiras em fase diluída ou fase densa. O carregamento de gás de transporte no caso de sistema de fase diluída para carvão é tipicamente cerca de 10 kg de carvão por kg de gás de arraste, e a velocidade do gás de arraste é de cerca de 15 metros/segundo (m/s) a 20 m/s. O gás de arraste é normalmente uma mistura de N2 e ar com ar comprimido é adicionado à tubulação abaixo do vaso de injeção. No caso do sistema de fase densa, o carregamento é de cerca de 40 kg a 80 kg de carvão por kg de gás de arraste e a velocidade do gás de arraste é de cerca de 1 m/s a 5 m/s. O gás de arraste é normalmente N2 ou uma mistura de N2 e ar.
A velocidade do gás de arraste deve ser sempre maior que a velocidade mínima de transporte para evitar bloqueios. Esta velocidade mínima depende de vários parâmetros que incluem a pressão do sistema e o diâmetro do tubo. Essas variáveis interagem entre si. A baixa velocidade no sistema de fase densa significa baixo desgaste da tubulação e dos componentes, enquanto a alta velocidade de transporte do sistema de fase diluída pode levar ao desgaste, principalmente nas curvas do tubo. A taxa de desgaste é determinada pela dureza, forma e velocidade das partículas de carvão. As propriedades do carvão também influenciam o desgaste. Revestir as partes dos tubos propensas ao desgaste com, por exemplo, um material elastômero de uretano proporciona resistência à abrasão, além de retardar o acúmulo de finos que podem levar ao bloqueio. As propriedades do carvão que estão relacionadas aos bloqueios da linha de transferência são o teor de umidade e os minerais de argila.
Alta umidade em carvões e misturas pode criar problemas. Assim, limites estritos de umidade nos carvões moídos são aplicados. A presença de argilas, que incham na presença de água, pode causar problemas, principalmente se houver queda de pressão no sistema de transporte e/ou se houver a presença de partículas ultrafinas. À medida que o teor de finos (menor que 5,8 mícrons) do carvão pulverizado aumenta, a queda de pressão no sistema de transporte aumenta. Se a queda de pressão ultrapassar um determinado valor, que está relacionado ao projeto da planta, pode ocorrer o bloqueio. O entupimento dos dutos ocorre devido ao acúmulo de depósitos nas curvas dos tubos, o que normalmente está relacionado à natureza macia do carvão (distribuição de tamanho de partícula mais fina). Ao injetar o carvão, o carvão ultrafino (menos de 10 mícrons) inicia o processo aderindo à parede do cotovelo e, uma vez que uma superfície áspera é formada, as partículas maiores começam a aderir. Além disso, a moagem preferencial do carvão mais macio em uma mistura de carvão pode levar a uma alta proporção de partículas ultrafinas, levando ao bloqueio.
Os bloqueios podem ser evitados por meio de melhorias no layout da tubulação e no sistema de distribuição e, em alguns casos, ajustando o sistema de preparação (como o pulverizador de carvão) para produzir um tamanho de partícula mais grosso. O sistema de injeção geralmente possui procedimento para detectar e eliminar o bloqueio, pois é um fenômeno comum. As linhas de transporte incluem portas de purga onde os bloqueios são removidos, normalmente com ar de alta pressão. Um teste simples e prático é necessário para avaliar a fluidez e manuseio do carvão pulverizado e das misturas de carvão. Isso permite que os materiais difíceis sejam identificados antes de serem usados.
A lança de injeção injeta carvão no maçarico que leva até a ventaneira. As partículas são imediatamente aquecidas pelo jato quente, inflamam, gaseificam e queimam. O design e a colocação da lança influenciam a eficiência de combustão do carvão. Anteriormente, as lanças costumavam ser lanças de aço retas que eram posicionadas na interface ventaneira / maçarico ou perto dela. Projetos que incorporam a injeção de O2 diretamente no fluxo das partículas de carvão (lanças de oxi-carvão) e/ou formas de gerar mais turbulência na ponta da lança foram desenvolvidos para melhorar a eficiência da combustão. Estes incluem (i) lanças coaxiais (onde o carvão é injetado através do tubo interno e O2 através do anel circundante), (ii) lanças de alta dispersão, (iii) lanças chanfradas, (iv) lanças de fenda, (v) excêntricas (não -concêntricas) lanças duplas, e (vi) lanças espiraladas.
O pré-aquecimento do carvão para aumentar a eficiência da combustão também é praticado. Os problemas que ocorreram quando o carvão foi introduzido pela primeira vez, como bloqueios de lança e tuyere e derretimento da ponta da lança, foram amplamente superados. Os bloqueios são principalmente devidos ao aquecimento do carvão a uma temperatura em que se tornam pegajosos e aderem à superfície das lanças de injeção e ventaneiras. A deposição de cinzas é minimizada utilizando carvão com alta temperatura de fusão de cinzas (AFT). Para todos os propósitos práticos, a AFT deve ser 50°C mais alta que a temperatura do jato quente. As lanças também podem obstruir se carvões com uma torta de alta fluidez perto da ponta da ventaneira. Isso pode ser superado evitando carvões com altos índices de aglomeração ou aumentando a vazão.
Posicionar a lança de injeção mais perto da ventaneira reduz a extensão do impacto das cinzas no maçarico. A utilização de lanças coaxiais refrigeradas a ar ajuda a prevenir o bloqueio e a erosão e pode prolongar a vida útil da ponta. A taxa de fluxo do ar de resfriamento deve ser minimizada para diminuir seu efeito de resfriamento na combustão do carvão. No entanto, o bloqueio das lanças ainda pode ser uma ocorrência frequente. Existem procedimentos definidos para detectar e eliminar esses bloqueios antes que possam causar problemas.
O uso de diferentes ligas para as lanças de injeção e a limitação da temperatura do jateamento a quente também influenciaram na fusão da ponta da lança. A durabilidade de uma lança é uma consideração operacional importante, pois ela queima com o tempo.
Combustão de carvão
As pistas são regiões vitais do BF, embora seu volume total geralmente não exceda 1% do volume interno do BF. Eles fornecem o processo com calor e agentes redutores. A injeção de carvão inevitavelmente afeta as condições da pista que, por sua vez, tem consequências fora da pista. Partículas não queimadas que saem da pista podem causar problemas operacionais, como permeabilidade reduzida, distribuição de gases e temperatura indesejáveis, erosão excessiva de coque e aumento do arraste de carvão. A quantidade de carvão não queimado aumenta com o aumento das taxas de injeção. Assim, o comportamento de combustão e gaseificação do carvão injetado na pista é um elemento importante para o funcionamento estável do BF. É muito evidente que o BF pode consumir mais carvão injetado do que o queimado dentro da canaleta, uma vez que o material não queimado é consumido em outra parte do forno.
A combustão de carvão dentro do BF tem sido amplamente estudada. Os estudos foram conduzidos usando equipamentos de escala de bancada como análise gravimétrica térmica (TGA), fornos de tubos de queda (DTFs) e reatores de malha de arame (WMRs). Essas técnicas não simulam totalmente as condições dentro da pista. O tempo de residência de partículas de carvão pulverizado em um DTF, por exemplo, é da ordem de segundos enquanto em um canal de um BF é em torno de milissegundos. Portanto, essas técnicas são normalmente usadas para fornecer uma avaliação comparativa dos diferentes tipos de carvões.
Outra abordagem seguida é o uso de instalações especialmente projetadas para simular as condições da pista. Isso inclui a injeção de uma explosão quente em um leito de coque empacotado, muitas vezes chamado de “modelo quente”. Estes têm a capacidade de simular condições de combustão para tempos de residência curtos de milissegundos, bem como diferentes localizações de pistas. No entanto, as instalações em escala piloto ainda não simulam totalmente as condições da pista em um BF. Como exemplo, eles podem não funcionar em pressões próximas à pressão principal da ventaneira/agitação. Pressões mais altas na pista aumentam a taxa de gaseificação do carvão.
Vários modelos de computador estão disponíveis para avaliar o comportamento do carvão na pista e em outras partes do BF. A validade desses modelos tem sido questionada, uma vez que os mecanismos que eles estão retratando são complexos e não totalmente compreendidos. Sua precisão depende das suposições feitas e da validade das relações construídas nos modelos. Uma vez que o comportamento do carvão é fortemente influenciado pelo projeto do BF e pelas condições de operação, bem como pelas propriedades do carvão, um modelo computacional talvez seja aplicável apenas para um determinado BF, condições de operação e os mesmos tipos de carvões nos quais foi desenvolvido e testado. Estas são as limitações de todas essas técnicas.
A combustão do carvão entre a saída da lança de injeção e a parede traseira da pista (distância física em torno de 0,7 m a 2 m) ocorre em altas temperaturas (1400 graus C a 2200 graus C), pressões elevadas (cerca de 3 kg/ cm2 a 6 kg/cm2 e tempos de residência curtos (10 milissegundos a 40 milissegundos para partículas pulverizadas) É nestas condições severas que é necessário atingir um alto nível de combustão do carvão.
O processo de combustão do carvão pode ser dividido nas seguintes etapas, sendo algumas delas sobrepostas.
- As partículas pulverizadas injetadas (menos de 75 mícrons) são rapidamente aquecidas à medida que entram no jato de ar quente enriquecido com O2. A taxa de aquecimento é determinada pelas condições operacionais, mas é de cerca de 100 graus C por segundo. A temperatura do jato quente é normalmente de 1.000 graus C a 1.200 graus C e a velocidade do gás é de cerca de 180 m/s a 250 m/s.
- A pirólise das partículas ocorre para produzir voláteis não condensáveis (gases), voláteis condensáveis (alcatrões) e um carvão carbonáceo. Demora cerca de 2 milissegundos a 20 milissegundos para concluir a desvolatilização.
- A ignição e a combustão do VM ocorrem para produzir principalmente CO2 (dióxido de carbono) e H2O (vapor de água). Isso leva alguns milissegundos.
- A combustão parcial do carvão residual ocorre pelo O2. A combustão do carvão contribui com a maior parte do calor liberado durante a combustão. Ao contrário da combustão do MV, em que o MV se difunde para a atmosfera rica em O2 (resultando em uma grande área de reação), o O2 para oxidação do carvão deve ser transportado para a superfície relativamente pequena da partícula. Como resultado, a oxidação do carvão é um processo mais lento. Enquanto a VM estiver sendo liberada, o O2 não poderá entrar em contato com a superfície do char devido aos altos requisitos estequiométricos da VM.
- Gaseificação do carvão residual por CO2 e H2O para produzir CO (monóxido de carbono) e H2 (hidrogênio). Esta é a reação mais lenta de todos esses processos e ocorre principalmente fora da pista.
São as características de combustão do carvão, em vez da combustão do coque, que governam a composição do gás e a distribuição de temperatura na pista, uma vez que são queimados preferencialmente. A Fig. 1 ilustra algumas das etapas de combustão do carvão que ocorrem dentro da canaleta e como a composição do gás varia. A maior parte do O2 é consumida perto do nariz da ventaneira, enquanto uma atmosfera rica em CO2 é produzida no meio e uma atmosfera rica em CO no final da pista.
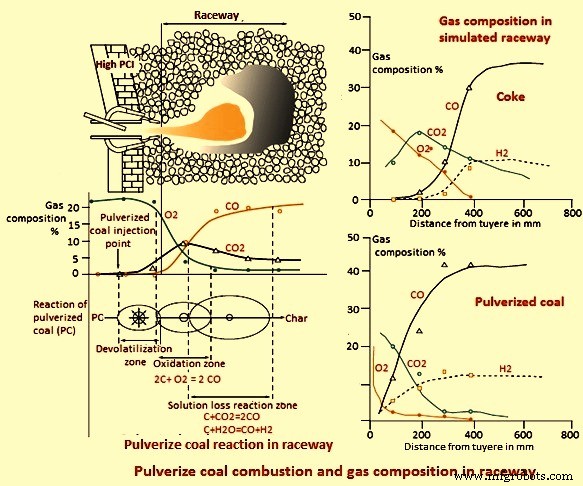
Fig 1 Combustão de carvão pulverizado e composição de gás na pista
A extensão da combustão (eficiência de combustão) e, portanto, a quantidade de material não queimado transportado para fora da pista, depende de vários parâmetros que incluem (i) propriedades do carvão, como teor de VM, tamanho e densidade das partículas e (ii) ) condições de operação, por exemplo, composição e temperatura do gás de explosão e posição e projeto da lança.
O gráfico da Figura 2 mostrando a eficiência de combustão e a taxa de injeção de carvão pulverizado é baseado em estudos feitos ao investigar a taxa máxima para carvão pulverizado a partir de um balanço de carbono no BF usando um modelo de balanço de material e calor.
Fig 2 Eficiência de combustão e taxa de injeção de carvão pulverizado
Com base nas várias investigações realizadas, as medidas para intensificar a combustão de carvão na pista estão resumidas abaixo.
- Enriquecendo a explosão com O2. No entanto, o efeito não linear da explosão de O2 no grau de combustão deve ser levado em consideração. O aumento na taxa de combustão torna-se menor à medida que o teor de O2 aumenta.
- Mistura preliminar de carvão pulverizado com O2 antes da introdução na cavidade da ventaneira.
- Uso de misturas de carvão (geralmente carvões com alto e baixo teor de VM) e misturas de combustível para manter alto grau de combustão e alta taxa de substituição de coque/carvão.
- Injeção de carvão com óxidos de Fe (minério de ferro fino e resíduos contendo Fe, etc.), carbonatos e outros aditivos ricos em O2.
- Uso de fenômenos químicos e físicos, por exemplo. efeitos catalíticos, polarizadores e outros.
- Otimização da moagem de carvão, dependendo das condições operacionais e propriedades do carvão.
Efeito da classificação de carvão
O comportamento de combustão e gaseificação do carvão pulverizado na pista é influenciado por suas propriedades. O efeito das propriedades geralmente na temperatura da chama (FT) e eficiência de combustão (CE) é descrito abaixo.
PCI tem um efeito de resfriamento no FT. O FT é um parâmetro importante, pois afeta a química da escória e do metal, a evaporação e a recirculação dos elementos alcalinos presentes e o fluxo do metal na lareira. É difícil medir o FT e, portanto, geralmente é calculado a partir de um balanço de energia da zona da pista. O valor calculado é conhecido como 'temperatura de chama adiabática da pista' (RAFT), ou FT teórica. Os cálculos do RAFT podem variar de um BF para outro dependendo das suposições feitas e, portanto, os valores podem não ser diretamente comparáveis. Existe um RAFT ideal para cada BF dependendo de fatores como a composição da carga e permeabilidade, qualidade do coque e taxa de sopro. A injeção de carvão reduz o RAFT (em comparação com a operação totalmente a coque), pois promove reações endotérmicas. Carvões de baixa VM e alta VM reduzem a FT nas faixas de 80 graus C a 120 graus C e 150 graus C a 220 graus C por 100 kg/tHM, respectivamente. Em geral, quanto maior a razão H2/C (carbono) no carvão, maior é o efeito de resfriamento. A jangada também diminui com o aumento da taxa de injeção de carvão. Aumentar a temperatura da explosão e/ou enriquecimento de O2 e/ou diminuir a umidade da explosão pode compensar o efeito de resfriamento do carvão.
Experimentos de combustão em condições simulando o ambiente BF indicaram que o CE normalmente aumenta com o aumento do VM do carvão. Carvões HV (alta volátil) são facilmente gaseificados, produzindo maior quantidade de gás, com menor CV e menor quantidade de carvão em comparação com carvões de baixa volátil (LV) e média volátil (MV). Assim, a combustão de gás é mais importante para os carvões de classificação inferior do que a combustão de carvão. Se a combustão do gás for incompleta, pode haver formação de fuligem, o que pode levar à deterioração da permeabilidade do BF ao sair da pista. A fuligem tem uma reatividade menor do que o carvão não queimado.
A extensão da desvolatilização é influenciada pelo tamanho das partículas de carvão, com tamanhos mais finos levando a uma desvolatilização mais completa. À medida que o teor de VM do carvão diminui, o CE final é governado pelas reações do carvão, uma vez que a ignição e a combustão do VM são rápidas. Char com maior reatividade tem maior CE. Tem sido frequentemente debatido que nas altas temperaturas que ocorrem na pista, a reatividade química torna-se menos importante, uma vez que a taxa de combustão é limitada pela taxa de difusão de O2 para a partícula, e o tempo de queima depende mais do tamanho da partícula e da concentração de O2. Combinado com o curto tempo de residência, o efeito da diferença de reatividade do carvão entre os carvões pode não ser muito significativo na pista. Existem outras opiniões que afirmam que, tendo em vista as pequenas granulometrias utilizadas (superiores a 80 % inferiores a 75 mícrons em PCI) e as condições altamente turbulentas que existem na pista, a taxa geral de combustão do carvão é normalmente influenciada pela intrínseca reatividade química do carvão. A reatividade do char é certamente importante fora da pista. Sob as condições do forno superior, a gaseificação do carvão é provavelmente controlada pela velocidade da reação química. Portanto, a taxa geral de reação de gaseificação do carvão é provavelmente influenciada pela reatividade química do carvão ao CO2.
Em geral, a reatividade do carvão aumenta com o carvão VM, ou seja, os carvões HV normalmente produzem carvões mais reativos do que os carvões LV e, portanto, uma melhor queima. Existem exceções, pois a reatividade do carvão é influenciada por vários fatores que incluem (i) sua morfologia (área superficial e porosidade), (ii) sua estrutura resultante, (iii) sua composição e (iv) as condições de operação. A taxa de queima e a reatividade do carvão dependem parcialmente do tamanho da partícula e de sua estrutura de poros. A estrutura de poros controla o fornecimento de gases reativos para o interior da partícula de carvão e fornece uma superfície interna variável para a reação.
A fragmentação do carvão, que é influenciada por sua estrutura, aumenta a área de superfície externa. Uma maior proporção de partículas de carvão com cavidades de paredes finas e maiores áreas de superfície de macroporosidade e macroporos são produzidas em altas taxas de aquecimento. Em geral, esses tipos de carvão tendem a se fragmentar mais do que aqueles com paredes mais espessas e menor porosidade e, portanto, têm uma taxa de reação mais alta. A fragmentação pode ser uma das razões pelas quais alguns operadores acham que o VM tem pouco efeito sobre a combustibilidade dos carvões. Carvões formados a partir de carvões de classificação mais alta (LV) em altas temperaturas são normalmente mais ordenados e, portanto, menos reativos. O desenvolvimento de cenosferas de carvão altamente anisotrópicas com o aumento da temperatura também diminui a reatividade do carvão. Esses carvões se beneficiam, assim, de uma temperatura de explosão mais baixa para melhorar a combustibilidade.
Mudanças na composição maceral de um carvão podem explicar diferenças na reatividade de combustão, particularmente entre carvões de classificação semelhante. Os macerais de inertinita são geralmente considerados “inertes” (não reativos). No entanto, não é tão simples assim. Nem todos os macerais de inertinita são, de fato, não reativos, e nem todos os de vitrinita são reativos. Vitrinita, inertinita e até liptinita podem contribuir para o C não queimado no resíduo carbonáceo. Também foi observado que, embora os carvões de carvão ricos em inertinita sejam basicamente menos reativos do que os carvões de carvão ricos em vitrinita a 500°C, isso não é mais importante em altas temperaturas (1300°C). É provável que a diferença na combustibilidade dos carvões seja bastante reduzida sob as condições de combustão muito intensas na pista.
O desempenho de combustão dos carvões pode ser melhorado devido aos efeitos catalíticos dos minerais constituintes ou retardado pela concentração excessiva de minerais. SiO2 e Al2O3 (alumina) podem diminuir a taxa de reação, enquanto os tipos cálcio (Ca), magnésio (Mg), ferro (Fe) e alcalinos podem melhorá-la, com os efeitos catalíticos mais pronunciados em carvões de classificação inferior. No entanto, a melhor combustibilidade das partículas ricas em minerais tem sido atribuída, não aos efeitos catalíticos, mas à difusão favorável do gás reagente através dos minerais e das interfaces maceral-mineral. A falta de uma correlação clara entre a reatividade do carvão e as fases inorgânicas individuais pode estar relacionada a diferenças na influência da temperatura na transformação do carvão mineral. Embora carvões e carvões com alta reatividade sejam geralmente preferidos, reatividade muito alta pode levar a condições instáveis do forno.
A mistura pode diluir as propriedades de combustão desfavoráveis de um carvão. Mas o desempenho de combustão de uma mistura é mais complexo do que o de um único carvão. Cada um dos componentes do carvão desvolatiliza e entra em combustão em diferentes temperaturas e em diferentes momentos e sua queima pode, portanto, variar consideravelmente. Além disso, podem ocorrer interações entre os vários carvões na mistura, o que complica as previsões do comportamento de combustão da mistura. As interações ocorrem primeiro no pulverizador onde há o potencial de grandes diferenças na distribuição de tamanho dos carvões componentes, especialmente se houver diferenças significativas na dureza de cada carvão. A desproporção também ocorre, influenciando a composição mineral e petrográfica das partículas resultantes, e o comportamento de combustão subsequente.
As interações entre os carvões componentes podem aumentar a combustibilidade da mistura. Como exemplo, a combustibilidade dos carvões de baixa tensão pode ser melhorada pela mistura com carvões de alta tensão. O carvão HV libera mais VM ajudando a formar um campo de temperatura de gás mais alta, que então aquece o carvão LV. Isso promove sua desvolatilização, ignição e combustão. O efeito sinérgico é mais pronunciado quando a fração de carvão HV é maior, até um certo percentual. Sob condições de BF simuladas, uma mistura contendo cerca de 70 % de carvão HV com 32,5 % de VM e 30 % de carvão LV com 20 % de VM deu o maior burnout.
Efeitos de tamanho de partícula
O desempenho de combustão do carvão é influenciado pelo tamanho das partículas. Para a conversão completa e, portanto, a utilização efetiva do carvão injetado, o aquecimento, a desvolatilização, a pirólise e a combustão das partículas precisam ocorrer no período entre sua entrada no jato quente e o limite da pista. Normalmente, maior quantidade de VM é liberada com a redução do tamanho das partículas de carvão. Isso pode facilitar a combustão em fase gasosa.
Partículas mais finas têm áreas de superfície específicas mais altas e, portanto, taxas de aquecimento mais altas. The granular coals releases lower amounts of VM than when they are pulverized. Calculated pyrolysis yields indicate that nearly all the VM from the pulverized coals are released whereas it is incomplete in case of the granular coals. The presence of residual VM in the granular coals affects the subsequent CO2 gasification reactivity of the chars. It has also been shown that the extent of devolatilization in the finer particles (45 microns to 75 microns) is more complete than the larger particles (75 microns to 150 microns). The effect is more pronounced for the LV coal (15 % VM) compared to the HV coal (37 % VM). This is since a higher VM release can result in more soot and tar production, produced from secondary reactions of the volatiles. The reactivity of the soot is lower than that of the unburned char. Thus, the lower is the soot formation; the better is the BF stability.
The CE (or burnout) of coal normally increases with decreasing particle size since a higher surface area is available for reaction. Larger particles require a longer time for burnout. The increase is more pronounced as VM content increases in coals. However, the particle size effect is also dependent on O2 stoichiometry, as well as coal rank (and char reactivity). It has been found that larger particles of coal generally have a higher CE (degree of burnout) at O2/C ratios of greater than 2 (fuel lean conditions) under simulated BF conditions. The smaller particles have higher CE under fuel rich conditions (O2/C ratio less than 2).
Operational factors
The effective use of coal needs operational changes to compensate for alterations in the raceway parameters and their effect elsewhere in the BF (such as the thermal state, slag regime and gas dynamics). Measures to intensify the combustion of coal in the tuyere/raceway region, and hence increase the injection rate include (i) increase the amount of O2 in the tuyeres, and (ii) adjustment in the blast temperature and moisture. There are some other measures taken to improve coal combustion, such as preheating the coal and the use of additives. Further, the choice of particle size, and hence the grinding parameters, can also influence the CE.
Oxygen can be added to the tuyere by (i) enrichment of the hot air blast, (ii) injection through the coal lances, and (iii) separate O2 lances. The addition of O2 results into higher availability of O2 for the participation in the combustion of coal in the raceway. Hence, the CE of the coal increases. However, the influence of O2 enrichment on CE is limited. It has been shown through calculation that the CE increases by around 6.7 % for a HV coal (34.5 % VM) and 3.3 % for a LV coal (14 % VM) when O2 enrichment of the hot air blast is raised from 0 % to 6 % by volume. With higher O2 enrichment, CE can actually decrease due to insufficient mixing. Increasing O2 enrichment increases the diffusion of O2, but diminishes the volume of combustion gas which transfers heat to the coal particles. Thus, there is the non-linear effect of blast O2 content on the degree of coal combustion.
Oxygen enrichment of the hot air blast produces both a reduction in bosh gas flow and a rise in FT. The former effect can help counteract the increase in the burden resistance (lower permeability) and the pressure drop associated with high injection rates. The latter effect can help compensate for the cooling effect of the decomposition of the coal VM. The CO and H2 contents also increase with O2 enrichment, resulting in the improved reduction of the iron ore in the central shaft. The CV of the top BF gas normally improves with O2 enrichment.
The lower limit of O2 enrichment is generally determined by the amount needed to maintain the required RAFT, with more O2 needed as the VM content of the coal increases. If the FT becomes too high, then burden descent can become erratic. Too low a FT hampers coal combustion and melting of the ore burden. The upper limit is dependent on maintaining a sufficient top gas temperature. As O2 is increased, the gas mass flow within the BF decreases, which decreases the heat flow to the upper region of the furnace for drying of the burden. The upper limit of the top gas temperature is also governed by the need to protect the top gas equipment. Other limitations to O2 enrichment include its cost and availability.
The position and design of the injection lance influence the CE and ash deposition in the tuyere. However, oxy-coal lance injection (co-annular injection) can produce an insulating effect around the coal particles, resulting in less coal combustion inside the tuyere. This effect carries over into the raceway, and less combustion is the end result. Lowering the O2 lance injection rate in this case improves the CE.
The key measure for combustion at high injection rate is a high blast temperature. O2 enrichment plays a more important role as a means of controlling gas flow in the BF rather than controlling the coal combustion. Normally, a higher hot blast temperature is a cost effective measure than O2 enrichment since it allows a lower consumption of O2. Increased blast temperature also reduces coke consumption, typically 10 kg/tHM for every increase of 40 deg C with PCI, and lead to a small rise in the raceway depth. A higher blast temperature is normally required as the VM of the coal increases. This is due to the lower char reactivity of the low VM coal.
Lowering of blast moisture can help to compensate for the cooling effects of PCI. If the RAFT becomes excessive, then blast moisture can be increased. Raising the hot blast moisture means more H2 in the bosh gas for iron ore reduction. The optimum RAFT in BF operating with higher H2 content can be lower than the BF operating with lower H2. Also, the blast velocity can be adjusted to not only improve coal combustion, but to maintain the needed length of the raceway zone which is critical for obtaining good conditions in the hearth.
Unburnt char
As the injection rate increases, the combustibility of coal tends to decrease resulting in unburnt material (such as char, fines, and fly ash) leaving the raceway. Some of these materials, along with coke debris, collect at the back of the raceway, in the bird’s nest, obstructing the rising gas flow and entrained solids in this area. The majority are swept upwards where they can accumulate under the cohesive zone, decreasing permeability and hence the productivity of the BF.
Changes in the permeability of the lower furnace zone can further affect the HM quality and slag viscosity. The unburnt material tends to collect at positions where large changes in the gas flow occur. Eventually it is entrained into the gas flow, passing through the cohesive zone coke slits, and up the shaft, where it can influence burden permeability, and is finally emitted with the top BF gas. Higher coal injection rates also increase the volume of combustion gases, and hence the gas flow, and change the heat load in the lower part of the BF. In addition, more slag is produced.
The deposition of unburnt fine material is a complex phenomenon consisting of several generation mechanisms, reactions, multiphase flow, buildup and re-entrainment. Different gas flow models have been developed to understand and predict the behaviour of fine material within the BF. With suitable burden charging patterns (such as central coke charging) and the use of stronger coke many of the problems relating to gas flow can be overcome.
Operating experience has shown that most of the unburnt material (char) is consumed within the furnace by the three mechanisms which are (i) gasification with CO2 and H2O, (ii) reaction with liquid iron (carburization), and (iii) reaction with slag. It is advantageous if the unburnt char participates in the ore reduction reactions, thus replaces more of the coke and lowers the amount of unburnt solids in the top BF gas. The three char consumption mechanisms are described below.
The gasification reaction of char with CO2 and H2O begins in the raceway, but because the residence time for fine particles is too short for appreciable reaction, gasification mainly occurs in the BF shaft. The reactions of char C with CO2 (the solution loss or Boudouard reaction) and H2O are slower than char combustion. The char obtained from coal competes with that from coke for CO2 and H2O. Char from coal is more reactive than the char from coke and hence is preferentially gasified. Therefore coke degradation by the solution loss reaction decreases with increasing PCI rates. In general, high VM coal char has a higher CO2 reactivity than low VM coal char. However the char reactivity in case of low VM coal can be improved by blending it with the high VM coal. The CO2 reactivity of coal blends is non-additive.
The reactivity of C in the unburnt char to CO2 and H2O is dependent not only on its surface area (particle size) but also on its structure and composition, as well as the operating conditions in the BF. It has been shown that the CO2 gasification reactivity of coal char increases with temperature upto 1500 deg C, especially between 1300 deg C and 1500 deg C. Complete char gasification usually requires a contact time of around 10 seconds at 1500 deg C. Since the residence time for particles at such high temperatures is too short in a BF, hence char gasification mainly occurs at decreasing temperatures in the furnace shaft.
The properties of char change as it moves up the BF, and thus its reactivity to CO2 and H2O. The reacting atmosphere is not uniform. As an example, the concentrations of CO, CO2, H2 and H2O vary at different locations within the BF. Injection of coal increases the bosh gas H2 concentration. Since the chemical reaction rate of H2 reduction is higher than that of CO, the extent of solution loss reaction diminishes as the bosh gas H2 rises. CO2 and H2O are present in the upper part of the BF due to the reduction of iron ore. Under the conditions here, char gasification by CO2 is expected to be controlled by the rate of the chemical reactions. In the lower part of the BF, char gasification is partly diffusion controlled. Hence, the overall reaction rate of char gasification is probably influenced by the chemical reactivity of char to CO2 in this region. Char reactivity towards CO2 is also influenced by its chemical structure, with less ordered structures being more reactive.
The presence of certain minerals in the char ash, such as Fe and alkalis, can catalyze the CO2 gasification reaction, whereas other minerals, such as SiO2 and Al2O3, can slow down the reaction. These catalytic effects become more prominent for low rank coals. Depending on its composition, ash can also retard the C conversion due to blockage of char particles as a result of increased proportion slag formation in the char particle. In the lower part of the BF, condensed alkalis from the recirculating gases (derived from coal, coke and iron ore) can have a catalytic effect. The loss of C by gasification increases the char ash content.
Carburization of the HM begins in the solid phase within the cohesive zone of the BF, and continues during descent of the metal droplets through the active coke, deadman and hearth zones. Unburnt char and fine material leaving the raceway can contact the dripping liquid metal in the bosh and hearth zones. C and other elements, such as Fe, Si (silicon) and S (sulphur), dissolve from the char into the liquid iron and hence influence the composition of the HM. The dissolution of C contributes to the carburization of liquid iron, and controls the level of char consumption by the HM. It becomes critical when the CE is low. If the HM is close to saturation when it reaches deadman and hearth, the unburnt material cannot be consumed, thus reduces the permeability in these regions. The C can come from unburnt coal as well as from coke. Since the dissolution rate of C from coal char is a slower process than that from coke, C from coke is preferentially consumed.
Carbon dissolution from unburnt char into liquid metal is influenced by the furnace operating conditions and the following factors.
- Char particle size – Unburnt char which maintains its pulverized form reacts very little with the liquid metal and the slag since it cannot penetrate into the liquid. If, however, the char particles are agglomerated into larger particles or captured by the larger pieces of coke, then they behave like bosh coke and carburize the liquid metal up to saturation. However, a tuyere probe sample taken at a BF in Australia indicated that ultrafine coal char particles can react with the dripping liquid metal, and that they are more readily dissolved than ultrafine coke particles. Experiments, though, have shown that the dissolution rate of C from coal char, though at larger particle sizes, is a slower process than that from coke.
- Char structure – Normally, the rate of dissolution improves as the C structure becomes more ordered.
- Char mineral matter – In general, SiO2, Al2O3 and MgO (magnesia) slow the C dissolution kinetics, whilst CaF2 (calcium fluoride) and Fe oxides increase the rate. The effect of CaO (calcium oxide) is less clear. The reaction of Ca (calcium) with S in the metal produces a layer of CaS (calcium sulphide) which can inhibit C transfer. The AFT is also one of the controlling mechanisms which limit the C dissolution. The formation of an ash layer on the carbonaceous material reduces the surface area available for dissolution, thus retarding C dissolution rates. Low AFT allows easy removal of the ash, in the form of liquid slag. This results in constant exposure of fresh C surface to the liquid iron, permitting the mass transfer of C to the liquid iron.
- Liquid iron composition – It changes over time. The C dissolution rate is typically decreased as the C content of the liquid iron increases. Higher S content also retards the C dissolution. Combustion of coal and coke releases sulphur oxides (SOx) which can react with the descending metal and slag.
Unburnt char, ash, fines and coke can interact with the dripping slag. The slag composition changes as it moves down the BF, with the Fe oxide concentration being continuously reduced. The reactions at the interface between the solid char and liquid slag play a major role in char consumption since they influence the kinetics of the reduction reactions and the contact area between the slag and char available for reaction.
Factors influencing unburnt char interactions with the slag include the slag composition, char C content, and char ash content and composition, as well as the furnace operating conditions. Char consumption by slags basically occurs through the following mechanisms.
- Reduction of the Fe oxides in slags by C in the char – The wetting characteristic has a significant effect on the dominant reduction mechanism taking place. The wetting characteristic of slags varies with slag composition, temperature, time, and carbonaceous material. Wetting varies as a function of time since the reduction of Fe oxide in the slag by char, and the dissolution of the char ash components into the slag, results in continuous variations in the slag and char compositions. An increase in temperature normally results in improved wettability at the slag/C interface. Reduction rate usually increases with increasing slag FeO (2 % to 10 %) content and with increasing reaction temperature (1300 deg C to 1600 deg C). In general, coal chars are poorly wetted by slag containing more than 10 % FeO at 1400 deg C and 1500 deg C. A faster reaction rate for coke suggests that coke fine is preferentially consumed before coal char.
- Reduction of SiO2 in slag by C of the char – It is a function of temperature. At temperatures less than 1500 deg C, only reduction of FeO takes place. At higher temperatures, both SiO2 and FeO in the slag are reduced, thus resulting in increased consumption of the char. SiO2 is reduced by C, through gaseous SiO, to Si or silicon carbide (SiC). Self-reduction of SiO2 in the char ash by C can also occur, resulting in further consumption of the char. The reduction kinetic of SiO2 is influenced by the wettability of char by the slag. Wetting behaviour is improved with an increase in slag SiO2 content, and with an increase in temperature (1500 deg C to 1700 deg C). Greater amounts of SiO2 and FeO in the char ash facilitate the slag/C interaction, leading to improved consumption of these oxides through reduction reactions.
- Interaction between components in the slag and char – This leads to the assimilation of char ash components such as S. In addition, the reduction of MgO in slag by char C can lead to further consumption. Self-reduction of the oxides in the char ash by C can also contribute to char consumption.
Slag viscosity has also a role to play. The presence of unburnt char in the slag can interfere with tapping by increasing slag viscosity, whereas absorption of char usually increases the fluidity of the bosh slag. Changes in slag mobility can affect the position and shape of the fluid and cohesive zones. A high viscosity slag around the tuyeres leads to serious gas flow problems. Slag viscosity is a complex function of slag composition, temperature and partial pressure of O2. Also unburnt char, coke, and unburnt ash from the coal can interact with the slag. All of these carbonaceous materials contribute oxides to the slag. In general, higher amounts of SiO2 or Al2O3 (acidic components) increase slag viscosity, whereas a higher basicity (higher CaO or MgO) lowers slag viscosity because of de-polymerization of the silicate network. Slag viscosity decreases with increasing FeO (0 % to 20 %) content at a fixed basicity. Basicity is normally determined by the CaO/SiO2 ratio. Since the slag does not completely absorb the char and ash in the bosh region, bosh slag usually has a higher basicity than tapped slag. The addition of fluxes can help in solving slag formation problems.
Processo de manufatura
- Geração e uso de gás de alto-forno
- Uso de Nut Coke em um Alto Forno
- Injeção de carvão pulverizado em um alto-forno
- Irregularidades do alto-forno durante a operação
- Sistema de resfriamento do alto-forno
- Sistemas de carregamento de alto-forno
- Entendendo um sistema de injeção direta
- Entendendo um sistema de injeção indireta
- Entendendo um sistema de injeção de combustível multiponto
- Entendendo o sistema de injeção de ar