Uma corrida contra o tempo
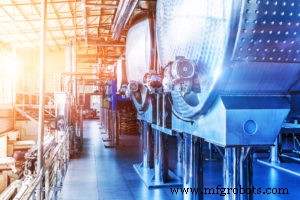
A manutenção é importante, mas o envelhecimento do equipamento pressiona as plantas.
Os sistemas e estratégias de manutenção continuam a fazer uma transição lenta para um processo digital, com maior uso de tecnologia para avaliar a integridade da máquina e desenvolver programas de reparo e manutenção. Mas é uma corrida contra o tempo. O envelhecimento do equipamento é o maior fator no tempo de inatividade não programado, e a falha do equipamento está em segundo lugar.
Essas são as conclusões da Engenharia de Plantas 2019 Relatório de manutenção, uma pesquisa anual patrocinada pela Advanced Technology Services (ATS). Profissionais de manutenção em indústrias de processo, discretas e híbridas responderam à pesquisa e ofereceram suas visões sobre onde suas operações estão hoje - e para onde estão indo.

Cortesia:CFE Media, ATS
Os gerentes de manutenção e líderes de fábrica usam uma variedade de estratégias no chão de fábrica para manter uma operação segura e produtiva. Embora a manutenção preventiva continue a ser a estratégia mais frequentemente empregada (78% dos entrevistados a utilizam de alguma forma), o uso de um sistema de gerenciamento de manutenção computadorizado (CMMS) saltou para o segundo lugar entre as estratégias, suplantando ambas as manutenções reativas (execução até a falha) e manutenção preditiva. Alguma combinação dessas estratégias de manutenção é usada por pelo menos 40% dos entrevistados.
Cada estratégia tem seus próprios méritos:
- Manutenção preventiva é vista como diminuindo o tempo de inatividade, melhorando a segurança e o gerenciamento de energia e sendo uma estratégia mais flexível,
- Manutenção reativa é visto como econômico e fácil de usar
- Manutenção preditiva tem um custo inicial mais baixo
- Um CMMS reduz a probabilidade de falha enquanto diminui o tempo de inatividade e melhora a eficácia geral do equipamento.
Mesmo que a tecnologia desempenhe um papel mais importante na manutenção em particular e na fabricação em geral, ainda existem muitas barreiras para sua adoção. A pesquisa descobriu que 48% dos gerentes de manutenção dizem que a falta de recursos ou equipe os impede de melhorar o sucesso da manutenção e 38% citam a falta de compreensão das novas opções de tecnologia. Outras questões, incluindo treinamento, adesão dos funcionários, financiamento para manutenção e falta de apoio da administração foram citadas por pelo menos 25% dos entrevistados.
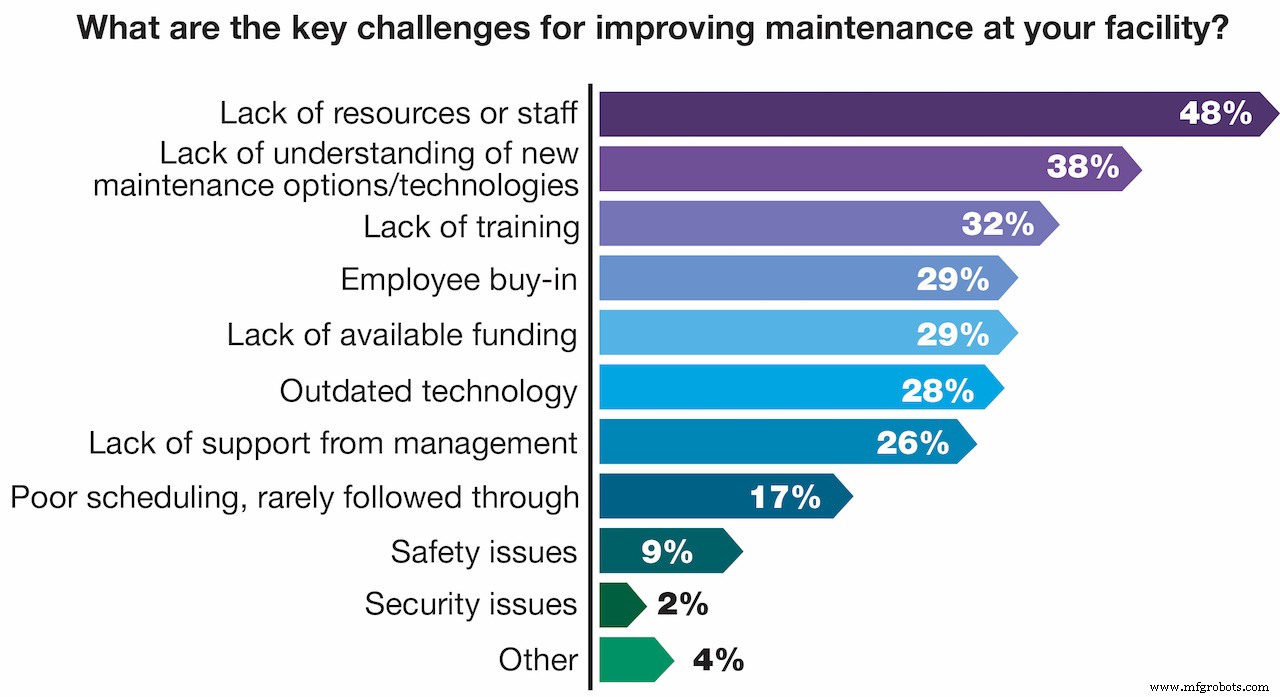
Cortesia:CFE Media, ATS
“Apesar de uma economia favorável, muitos fabricantes continuam adiando investimentos em novos equipamentos de fábrica”, disse Jeff Owens, CEO da ATS. Estender a vida útil de ativos legados está fazendo com que a manutenção desempenhe um papel cada vez mais crítico na eficiência da produção, mas também está tendo um impacto sobre os integradores de tecnologia encarregados de atualizar as máquinas para a era digital.
“Tudo isso mostra a necessidade de indivíduos treinados que tenham as habilidades e a compreensão para sustentar ou aumentar a eficiência em todas as fases do ciclo de vida do equipamento”, acrescentou Owens.
Outra tendência significativa é a terceirização da manutenção para fornecedores terceirizados. Em média, cerca de 20% das funções de manutenção são terceirizadas, e a falta de qualificação da equipe existente é citada como o principal motivo para terceirizar essas funções. Esse problema continuou a aumentar nos últimos três anos do Estudo de Manutenção:foi responsável por mais de 40% das respostas em 2017, mas aumentou para mais de 50% em 2019.
Cortesia:CFE Media, ATS
“Continuamos a ver um futuro brilhante para técnicos, engenheiros de confiabilidade, programadores e integradores de sistema, especialmente aqueles que entendem as tecnologias e sistemas de energia que são comuns na fabricação”, disse Owens. “A lacuna de habilidades industriais e a evolução sem fim da tecnologia digital estão criando enormes oportunidades para os trabalhadores jovens e voltados para o crescimento ver os avanços que uma carreira em manufatura oferece.”
A tecnologia empregada na manutenção é variada - e pode nem mesmo ser tão técnica. Embora o CMMS e as planilhas e cronogramas projetados internamente sejam os dois sistemas mais usados, o papel e a prancheta ainda são usados em 39% das fábricas dos entrevistados. O uso da tecnologia interna caiu no último ano, de 55% em 2018 para 45% em 2019.
Cortesia:CFE Media, ATS
Entre os outros resultados do Estudo de Manutenção de 2019:
- Manutenção programada: A instalação média gasta 20 horas por semana em manutenção programada, com 53% alocando até 10% de seus custos operacionais anuais para processos de manutenção e 30% dedicando mais de 10% deste orçamento à manutenção.
- Atenção aos sistemas: Equipamentos rotativos (motores, transmissão de força, etc.), sistemas de força fluida (ar, hidráulico, etc.) e sistemas de automação de plantas são as três áreas onde as instalações dedicam mais suporte de manutenção, seguidas pelos sistemas internos de distribuição elétrica e equipamentos de manuseio de materiais.
- Treinamento: As equipes de manutenção são em sua maioria treinadas em mecânica básica (73%) e elétrica (72%), além de segurança (72%). Outros tipos de treinamento incluem lubrificação e motores (55%), caixas de engrenagens e rolamentos (52%).
Quer a manutenção seja vista como um centro de custo (59% disseram que os gastos mantêm o equipamento funcionando mesmo enquanto gerencia os custos) ou um centro de lucro (34% disseram que a manutenção oferece maior capacidade para a planta), ela continua sendo crucial para o tempo de atividade, produtividade e excelência operacional da planta.
Confira este infográfico para saber mais sobre as tendências de manutenção e desafios na indústria de manufatura ou entre em contato conosco hoje para uma discussão individual sobre as necessidades exclusivas de manutenção de sua fábrica.
Manutenção e reparo de equipamentos
- O sensor de imagem 3D Tiny usa tecnologia de tempo de voo
- Compreendendo as métricas de manutenção:Tempo médio para reparar
- 7 maneiras de reduzir o tempo de inatividade atualizando sua tecnologia de manutenção
- Por que agora é a hora de obter o software de manutenção e gerenciamento de ativos
- Tecnologia de semicondutor avançada, um nanômetro por vez
- Por que é hora de atualizar a tecnologia móvel nos transportes
- O que é um IMMP:diferenças e vantagens em relação ao CMMS
- Como saber a hora certa para a manutenção dos freios do guindaste
- Manutenção do guindaste:sinais de que é hora de substituir as rodas do guindaste
- 6 etapas para otimizar as práticas de manutenção