Estimule o Trabalho em Equipe para Melhores Resultados de Manutenção
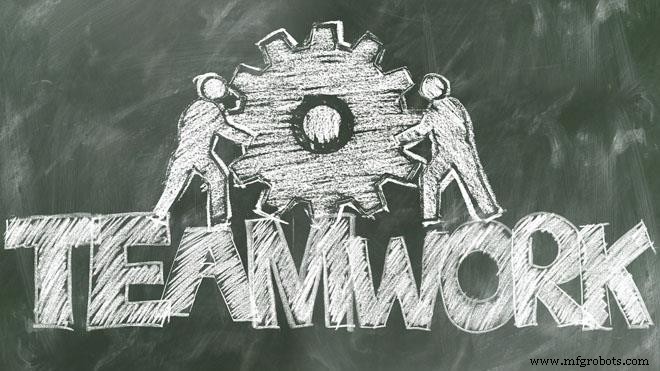
Sua reputação era questionável. Se você caminhasse pelo chão da fábrica, teria problemas para enxergar além de 15 metros.
Você também notaria banheiros deploráveis (não é uma questão de custódia), ausência de supervisão, pintura descascando das paredes e muito material rodante com etiqueta vermelha no chão. Apesar disso, o departamento de manutenção foi muito estimado, pois conseguiu manter o equipamento em funcionamento.
Você pode imaginar a magnitude das queixas sindicais, reclamações da Equal Employment Opportunity Commission (EEO) e cartas para a Administração de Segurança e Saúde Ocupacional (OSHA).
O novo gerente da fábrica, Al LaRiviere, tinha um desafio. Suas primeiras ações foram remover todo o equipamento com etiqueta vermelha, bem como o equipamento que não estava sendo usado. O número de itens colocados no estacionamento chegou a mais de 1.000.
Mais da metade foi sucateada, enquanto os outros foram eventualmente consertados em outra instalação. Em seguida, ele começou um estudo de gerenciamento de processo sobre o que realmente acontecia na fábrica e trabalhou para envolver a gerência como uma equipe.
Esta era uma planta de 24 horas, 365 dias, com três turnos por dia. Havia aproximadamente 350 funcionários na equipe de manutenção para gerenciar os mais de 1 milhão de pés quadrados do prédio, saguões de clientes, 20 acres de terreno, mais de 200 peças de automação, 2 milhas de transporte, todas as necessidades de custódia e as 25 estações ao redor da cidade .
A planta original era um projeto Works Progress Administration (WPA) e havia sido modificada várias vezes.
Os processos do correio de origem (enviado dentro da área de serviço da planta) e do correio de destino (entrando na área de processamento da planta) foram divididos em fluxos (cartas, pacotes, pequenos itens e pacotes). Ele teve um giro de estoque de 365 por ano (incapaz de armazenar correspondência).
As métricas críticas foram medidas em dias desde o envio da correspondência em uma caixa até o dia da entrega (padrões de entrega). Cada tipo de correspondência tinha padrões diferentes. Houve também uma quase métrica de horas de trabalho usadas versus horas de trabalho ganhas (desempenho do orçamento). Essas foram as métricas de resultados nas quais o gerente da fábrica foi avaliado.
Uma avaliação externa das competências da equipe de gestão recomendou o treinamento da equipe, o treinamento individual e o desenvolvimento de todos os supervisores e gerentes em habilidades interpessoais e como supervisionar. Isso foi iniciado simultaneamente com o estudo de gerenciamento de processos.
No estudo, os indicadores de desempenho foram identificados como processos ou resultados. Exemplos de processo são ausência, produção, qualidade da unidade e cumprimento dos tempos de liberação da área de trabalho.
O resultado final foi se a correspondência eliminou as várias operações com classificação de qualidade e fez a correspondência certa chegar ao transporte correto no horário de envio programado. Essas duas últimas questões tornaram-se os indicadores de resultados da planta. Se eles foram atendidos de forma consistente, os padrões de entrega da planta foram atendidos.
Armado com os resultados do estudo de processo, LaRiviere decidiu que só queria que suas equipes de gerenciamento se preocupassem com duas métricas - limpar a correspondência dentro do prazo e a qualidade da classificação.
Ele sentiu que a produtividade era fruto da motivação dos indivíduos e acompanharia o cumprimento dos indicadores. Estes se tornaram os indicadores de resultados para as áreas de processamento de cada supervisor / superintendente.
Os gerentes de turno tinham os indicadores de resultados da correspondência certa nos caminhões certos na hora certa. Todas as reuniões da equipe ou outras discussões de gerenciamento foram limitadas a esses dois conjuntos de métricas.
A LaRiviere até tinha um pequeno estande com três degraus construído para a sala de conferências. Se uma pessoa falhava em suas métricas, ela tinha que subir os degraus para se levantar e ser contada. Não houve discussão de acompanhamento. No entanto, LaRiviere instituiu celebrações por realizações (muitas delas).
Treinamento para todos os funcionários com foco nas duas métricas e no processo dentro de suas áreas de trabalho. Os supervisores não deviam se concentrar nas taxas de ausência, desempenho individual, motivos para a qualidade da correspondência recebida ou ser críticos sobre qualquer outro processo com seus funcionários.
Era responsabilidade do supervisor se preocupar com os problemas anteriores e posteriores e fazer com que seus funcionários se concentrassem em seu trabalho.
Os supervisores também deveriam desenvolver uma equipe. Cada supervisor postou os indicadores de processo de sua equipe a cada dia (quanto foi processado, horas de trabalho, qualidade interna e correio atrasado).
Todos os operadores de máquina foram treinados para usar os relatórios de produção gerados pela máquina, e rudimentos de eficácia geral do equipamento (OEE) foram incorporados ao software.
Para fazer esse trabalho, os funcionários da fábrica foram designados a supervisores específicos. Todos os supervisores aderiram ao plano de jogo e foram mantidos informados sobre o desempenho geral do serviço postal dos EUA, o desempenho de sua fábrica e o efeito de sua própria área no desempenho. Eles estavam se tornando pessoas respeitadas pelos funcionários do artesanato.
LaRiviere acreditava que se os funcionários soubessem que seus gerentes estavam todos no mesmo navio, para onde ele estava indo e o plano de jogo para chegar lá, eles encontrariam a confiança e a motivação para atuar e iriam para casa à noite com um sentimento de realização e orgulho de sua planta.
Os funcionários de manutenção foram treinados para interpretar relatórios de desempenho de equipamentos, entender o relacionamento cliente-fornecedor com os operadores e se relacionar com o pessoal de operações em um modo de resolução de problemas para parar o jogo de culpa. As conversas entre os funcionários e seu supervisor centraram-se nos processos de suas áreas de trabalho.
Eu apenas toquei a superfície dessa notável reviravolta. As ausências não programadas caíram para 3 por cento, a produtividade aumentou 20 por cento e a qualidade da fábrica liderou a região.
Você acreditaria que agora havia muitas pessoas vindo trabalhar todos os dias? Os funcionários passaram a contar com supervisores para supervisioná-los, mantê-los informados e protegê-los. Os supervisores agora erguiam a cabeça e aguardavam ansiosos para trabalhar.
LaRiviere também pintou a planta interna e colocou sinalização significativa para torná-la um local de trabalho visual. Ele reduziu o número e o tamanho dos banheiros (o emprego original era de mais de 4.000 funcionários).
Em seguida, ele trabalhou o mesmo processo com recursos humanos, finanças, manutenção, operações de veículos e equipes de escritório. LaRiviere foi um gerente único que estava no lugar certo na hora certa.
Embora não seja necessariamente uma história de manutenção, ela ilustra o uso de ferramentas de gerenciamento de processos, a compreensão do que motiva as pessoas e o que uma visão pode produzir quando o chefe tem a liberdade de arriscar.
Manutenção e reparo de equipamentos
- Lápide
- Maiô
- Propriedade de equipamento para técnicos de manutenção
- Melhor planejamento de manutenção é a bala de prata da MillerCoors
- Sistema de recompensa conjunto impulsiona resultados e trabalho em equipe
- Planejamento de manutenção:O que você ganha com isso?
- SMRP é valioso para profissionais de M&R
- Gerenciamento de códigos QR para gerenciamento de instalações
- IoT para manutenção preditiva
- 14 dicas para manutenção de miniescavadeiras