Solução de problemas para manutenção:mais do que apenas tentativa e erro
Um guia completo para solução de problemas para manutenção e dicas para melhorar suas habilidades de solução de problemas para elevar toda a sua operação.
Índice
- O que é solução de problemas?
- Dicas sobre solução de problemas para manutenção
- Uso de software de manutenção para solução de problemas
- O resultado final
A solução de problemas para manutenção pode ser uma arte e uma ciência. O problema é que, embora a arte possa ser bela, não é conhecida por sua eficiência. Quando levado ao próximo nível, a solução de problemas pode abandonar o apelido de tentativa e erro e se tornar um esforço puramente científico. Isso ajuda os técnicos a encontrar os problemas e soluções corretos com mais rapidez. Quando a solução de problemas é feita corretamente, toda a operação de manutenção pode superar o acúmulo, perda de produção e problemas de conformidade com muito mais eficiência.
Vamos dar uma olhada no que realmente é a solução de problemas, por que é importante para os profissionais de manutenção e como sua equipe pode ajustar sua abordagem.
O que é solução de problemas?
Os sistemas quebram - isso é apenas um fato da vida. Quer seja uma correia transportadora ou uma furadeira industrial, todos nós já passamos por um equipamento que não responde, está com defeito ou está agindo de forma anormal sem motivo aparente. Pode ser totalmente frustrante.
A solução de problemas é o processo de identificar o que há de errado com esses sistemas defeituosos quando o problema não é imediatamente óbvio. A solução de problemas geralmente segue uma abordagem sistemática de quatro etapas; identifique o problema, planeje uma resposta, teste a solução e resolva o problema. As etapas de um a três são freqüentemente repetidas várias vezes antes que uma resolução seja alcançada.
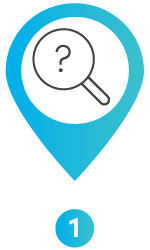
Identifique o problema
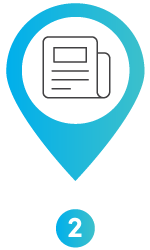
Planeje uma resposta

Teste a solução
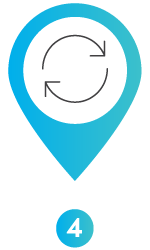
Repita até que o problema seja resolvido
Pense da seguinte maneira:quando uma correia transportadora quebra, você pode tentar alguns métodos diferentes para consertá-la. Primeiro, você identifica qual parte da correia transportadora não está funcionando. Depois de identificar a área do problema, você planeja uma resposta e a testa, como realinhar ou lubrificar uma peça. Se isso não resolver o problema, você pode substituir a peça, o que faz a correia transportadora funcionar novamente. Esta é a solução de problemas.
Como a solução de problemas geralmente é feita na manutenção?
Pare-nos se você já ouviu essa história antes. Um ativo quebra e ninguém sabe por quê. Você conversa com a operadora, lê alguns manuais e verifica suas notas sobre o ativo. Você tenta algumas coisas para colocar a máquina em funcionamento e voltar a funcionar sem sorte. Antes de tentar uma terceira ou quarta solução possível, você é chamado para outra emergência, com o ativo ainda fora de serviço.
Geralmente é assim que o processo acontece ao solucionar problemas de manutenção, especialmente quando uma instalação depende de registros em papel ou planilhas do Excel. O processo baseia-se na coleta do máximo de informações possível do maior número de fontes possível para identificar a causa mais provável da pane. Você nunca pode dar errado ao coletar informações, mas é a maneira como as informações são coletadas que pode transformar a solução de problemas de uma necessidade em um pesadelo.
Por que a solução de problemas é importante na manutenção?
A falha inesperada do equipamento é a razão pela qual a solução de problemas existe. Se os ativos nunca quebrassem sem quaisquer sinais claros de falha iminente, não haveria necessidade de solucionar o problema. Mas sabemos que não é esse o caso.
A falha de ativos nem sempre segue um padrão previsível. Sim, as equipes de manutenção podem usar a manutenção preventiva e a manutenção baseada na condição para reduzir a probabilidade de tempo de inatividade não planejado. No entanto, você nunca pode eliminá-lo totalmente. O que você pode fazer é implementar processos para reduzir ao máximo as falhas e corrigi-las o mais rápido possível quando ocorrerem. É aqui que fortes técnicas de solução de problemas são úteis.
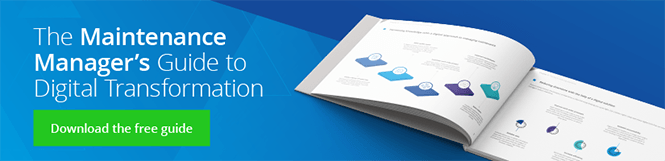
Como a solução de problemas sempre fará parte da equação de manutenção, os humanos também sempre terão uma função. A tecnologia de manutenção não elimina a necessidade de um toque humano na solução de problemas; simplesmente torna o processo muito mais eficiente. Quando a solução de problemas não é refinada, pode levar a perda de tempo rastreando informações, uma perda substancial de produção, um ambiente de trabalho inseguro e falhas mais frequentes. Resumindo, conhecer algumas das práticas recomendadas para a solução de problemas pode ser a diferença entre uma enorme lista de pendências e um programa de manutenção estável.
Dicas para solução de problemas para manutenção
A seguir estão apenas algumas maneiras pelas quais sua operação pode melhorar suas habilidades de solução de problemas para vencer o caos e assumir o controle de sua manutenção.
Quantifique o desempenho dos ativos e entenda como usar os resultados
Provavelmente nem é preciso dizer, mas quanto mais profundamente você conhece um ativo, melhor equipado você estará para diagnosticar um problema. Anos trabalhando com um determinado ativo podem ajudá-lo a reconhecer quando ele não está funcionando muito bem. Mas a solução de problemas excepcional não se trata apenas de conhecer os sons, velocidades ou odores normais de uma máquina específica. Em vez disso, trata-se de saber como analisar o desempenho dos ativos em um nível mais profundo, que é onde os fatores de relatórios avançados entram.
Obtenha as melhores práticas para rastrear e usar dados de ativos
Consulte Mais informação
Quando os operadores e técnicos contam exclusivamente com sua própria experiência anterior com um equipamento, isso deixa com eles enormes lacunas no conhecimento que prejudicam o processo de solução de problemas. Por exemplo, deixa muito espaço para o viés de recência afetar a tomada de decisão, o que significa que os técnicos provavelmente tentarão a última coisa que corrigiu um problema específico sem considerar outras opções ou se aprofundar na causa raiz. Além disso, se a solução de problemas depende do conhecimento proprietário de alguns técnicos, isso significa que os reparos terão que esperar até que esse pessoal específico esteja disponível.
A equipe de manutenção deve ter o know-how para conduzir uma análise aprofundada do desempenho de um ativo. Por exemplo, os técnicos devem compreender como executar relatórios e compreender os KPIs para equipamentos críticos, como o tempo médio entre a falha e a eficácia geral do equipamento. Se estiver usando a manutenção baseada na condição, a equipe de manutenção também deve saber a curva P-F para cada ativo e o que significam as diferentes leituras do sensor. Quando os técnicos estão equipados com um conhecimento mais profundo de um ativo, será mais fácil para eles identificar onde ocorreu um problema e como corrigi-lo, tanto a curto quanto a longo prazo.
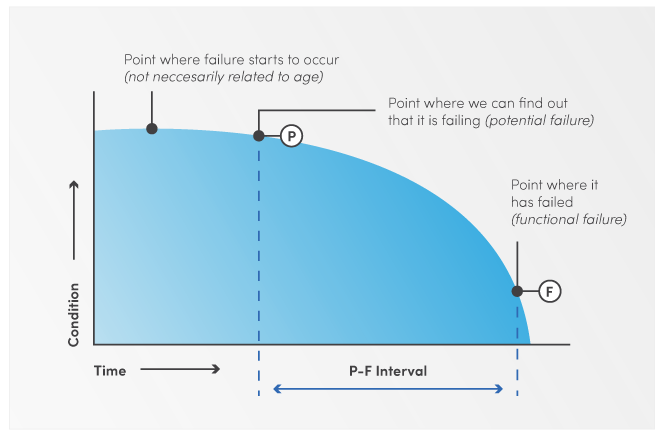
Crie históricos de ativos detalhados
A informação é o combustível que impulsiona a solução de problemas excepcionais para manutenção. Saber como um determinado ativo funcionou e falhou para centenas de outros é um bom lugar para começar um reparo. É por isso que os manuais são uma ferramenta útil na solução de problemas. No entanto, cada ativo, instalação e operação são diferentes, o que significa que a falha do ativo nem sempre segue o script. Notas detalhadas sobre o histórico de um ativo podem abrir um beco sem saída e levar você a uma solução muito mais rápida.
Um histórico detalhado de ativos pode lhe dar uma vantagem na solução de problemas de várias maneiras. Ele oferece um método simples para fazer referência cruzada de sintomas do problema atual com elementos de problemas anteriores. Por exemplo, um técnico pode ver se um determinado tipo de material estava sendo manuseado por uma máquina ou se havia algum sinal de alerta identificado para uma falha anterior. Quanto mais uma situação presente se alinha com um cenário passado, mais provável é que precise da mesma correção. As soluções podem ser priorizadas dessa forma, levando a menos perdas, menos tempo de inatividade, menos peças sobressalentes desnecessárias sendo usadas e muito mais.
Quando a solução de problemas é feita corretamente, toda a operação de manutenção pode superar o acúmulo, perda de produção e problemas de conformidade com muito mais eficiência.
Ao criar históricos de ativos detalhados para ajudar na solução de problemas (bem como na manutenção preventiva), é importante incluir o máximo de informações possível. Certifique-se de registrar a hora e as datas de quaisquer ações notáveis tomadas em um ativo ou peça de equipamento. Isso pode incluir avarias, PMs, inspeções, substituição de peças, programações de produção e comportamento anormal, como fumaça ou sons incomuns. Em seguida, documente as etapas executadas durante a manutenção, incluindo PMs ou reparos. Por fim, destaque a solução bem-sucedida e o que foi necessário para realizá-la, como peças, mão de obra e equipamentos de segurança necessários. Certifique-se de adicionar quaisquer métricas e relatórios relevantes ao histórico de ativos também.
Uma maneira de capturar todas essas informações em um só lugar é criar um registro de manutenção de equipamentos bem construído, como este:
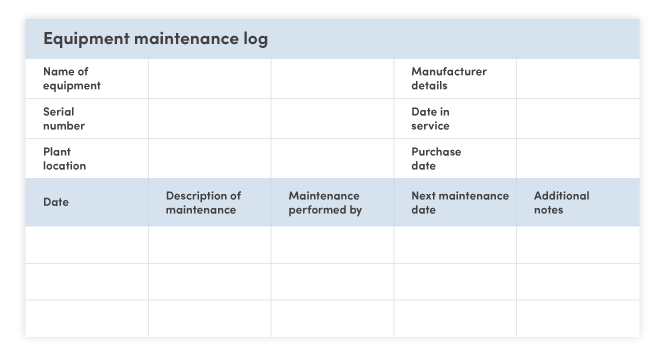
Baixe seu próprio modelo de registro de manutenção de equipamento aqui
Use análise de causa raiz e códigos de falha
A solução de problemas eficaz para manutenção começa com a eliminação de ambiguidades e soluções de curto prazo. Encontrar a raiz de um problema rapidamente, resolvê-lo com eficácia e garantir que continue resolvido é uma fórmula vencedora. A análise de causa raiz e os códigos de falha são algumas ferramentas que o ajudarão a atingir esse objetivo.
A análise de causa raiz é uma técnica que permite identificar o motivo de uma falha. O método consiste em perguntar “por que” até chegar ao cerne do problema. Por exemplo:
- Por que o equipamento falhou ?:Porque um rolamento se desgastou
- Por que o rolamento se desgastou ?:Porque um acoplamento estava desalinhado
- Por que o acoplamento estava desalinhado ?:Porque não foi reparado recentemente.
- Por que o acoplamento não foi reparado ?:Porque a manutenção não foi agendada.
- Por que a manutenção não foi programada ?:Porque não tínhamos certeza de com que frequência ela deveria ser programada.
Crie sua próxima análise de causa raiz com este modelo de RCA
Esse processo tem dois benefícios ao solucionar problemas de manutenção. Primeiro, permite identificar a causa imediata da falha e corrigi-la rapidamente. Em segundo lugar, leva você ao cerne da questão e a uma solução de longo prazo. No exemplo acima, está claro que um melhor programa de manutenção preventiva é necessário para melhorar o gerenciamento de ativos e reduzir o tempo de inatividade não planejado.
Os códigos de falha fornecem um método consistente para descrever por que um ativo falhou. Os códigos de falha são baseados em três ações:Listar todos os problemas possíveis, todas as causas possíveis e todas as soluções possíveis. Este processo registra os principais aspectos de uma falha de acordo com categorias predefinidas, como desalinhamento ou corrosão.
Os códigos de falha são úteis ao solucionar problemas de manutenção porque os técnicos podem ver imediatamente os códigos de falha comuns, determinar a melhor solução e implementá-la rapidamente. Os códigos de falha também podem ser usados para descobrir um problema comum entre um grupo de ativos e determinar uma solução de longo prazo.
Crie códigos de falha incríveis com este modelo FMEA gratuito
Crie listas de tarefas detalhadas
A solução de problemas excepcional requer planejamento e previsão sólidos. Processos claros fornecem um plano para os técnicos, para que eles possam identificar rapidamente os problemas e implementar soluções mais eficazes. Criar listas de tarefas detalhadas é uma forma de reforçar seu planejamento e evitar dores de cabeça no futuro.
Uma lista de tarefas descreve uma série de tarefas que precisam ser concluídas para terminar um trabalho maior. Eles garantem que etapas cruciais não sejam perdidas durante a realização de inspeções, auditorias ou PMs. Por exemplo, o trabalho maior pode ser a realização de uma inspeção de rotina dos desfibriladores de sua instalação. Este trabalho é dividido em uma lista de tarefas menores, como "Verificar a instalação da bateria" e "Inspecionar os componentes externos em busca de rachaduras".
A tecnologia de manutenção não elimina a necessidade de um toque humano na solução de problemas; simplesmente torna o processo muito mais eficiente.
Listas de tarefas detalhadas são extremamente importantes ao solucionar problemas para manutenção. Eles atuam como um guia ao testar as soluções possíveis para que os técnicos possam corrigir o problema ou desqualificar um diagnóstico o mais rápido possível. Quanto mais explícita a lista de tarefas, mais completo será o trabalho e menos provável que o técnico cometa um erro. Listas de tarefas abrangentes também podem oferecer dados valiosos quando ocorre uma falha. Eles fornecem uma visão sobre o tipo de trabalho realizado recentemente em um ativo para que você possa determinar se alguma ação foi perdida e se esta foi a origem do problema.
Existem algumas práticas recomendadas para a construção de listas de tarefas detalhadas. Primeiro, inclua todas as ações individuais que constituem uma tarefa. Por exemplo, em vez de instruir alguém para “inspecionar o ventilador de resfriamento”, inclua as etapas que compõem essa inspeção, como “Verifique se há rachaduras visíveis” e “Inspecione se há peças soltas”. Organize todas as etapas na ordem em que devem ser realizadas. Por último, inclua qualquer informação adicional que possa ser útil para completar as tarefas, incluindo suprimentos, recursos (ou seja, manuais) e EPI necessários.
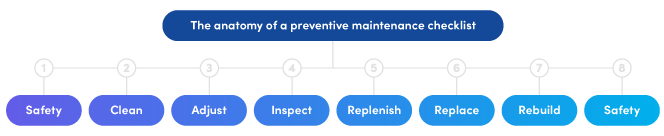
Crie listas de verificação de PM de classe mundial com este modelo gratuito
Torne as informações adicionais acessíveis
Já dissemos isso antes e vamos dizer de novo; Uma boa solução de problemas geralmente é o resultado de ótimas informações. No entanto, se essas informações forem de difícil acesso, você perderá todas as vantagens que elas proporcionam. É por isso que é crucial para sua operação não apenas criar um grande centro de recursos, mas também torná-lo altamente acessível. Isso aumentará sua capacidade de resolução de problemas e colocará seus ativos online de volta mais rápido quando ocorrer um tempo de inatividade não planejado.
Vamos começar com os elementos de um grande centro de informações. Já falamos sobre a importância dos relatórios, históricos de ativos, códigos de falha e listas de tarefas ao solucionar problemas de manutenção. Alguns outros recursos importantes incluem diagramas, procedimentos operacionais padrão (SOPs), vídeos de treinamento e manuais. Todos eles devem ser incluídos e organizados por ativo. Se um técnico chegar a um beco sem saída ao solucionar um problema, essas ferramentas podem oferecer uma solução que pode ter sido perdida na análise inicial.
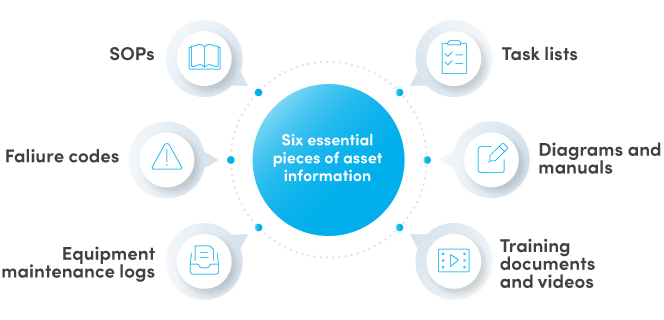
Agora que você reuniu todos os seus documentos, é hora de torná-los facilmente acessíveis para toda a equipe de manutenção. Se os recursos estão presos em um arquivo, em uma planilha ou na mente de uma única pessoa, eles não fazem muito bem para o técnico. Eles podem ser perdidos, perdidos e difíceis de encontrar - sem mencionar a ineficiência envolvida na necessidade de ir de um ativo ao escritório apenas para pegar um manual. Uma maneira de contornar esse obstáculo é criar um hub de conhecimento digital com software de manutenção. Ao disponibilizar todos os seus recursos por meio de um dispositivo móvel, os técnicos podem acessar qualquer ferramenta necessária para solucionar um problema. Em vez de vasculhar os arquivos de papel para encontrar um histórico ou diagrama de ativos, eles podem acessar as mesmas informações em qualquer lugar, a qualquer hora.
Tudo o que você precisa saber sobre métricas de manutenção
Consulte Mais informação
Usando o software de manutenção para solucionar problemas
Se parece muito trabalhoso reunir, organizar, analisar e divulgar todas as informações necessárias para ter sucesso na solução de problemas, você não está errado. Sem as ferramentas adequadas, esse processo pode ser um trabalho pesado para equipes de manutenção sobrecarregadas. O software de manutenção é uma ferramenta que pode ajudar a aliviar a carga em cada etapa do processo. Uma plataforma digital, como um CMMS, se encarrega de processar os números, organizar os dados e disponibilizá-los onde e quando quiser, para que você possa se concentrar no uso dessas informações para tomar grandes decisões e solucionar problemas de maneira mais eficaz.
Por exemplo, ao construir um histórico de ativos detalhado, é importante documentar cada encontro com uma peça do equipamento. É muito trabalho para um técnico que corre de um trabalho para outro e é difícil de controlar depois do fato. Um investimento em software de manutenção o ajudará a navegar por esses obstáculos. Ele faz isso permitindo que os técnicos usem um conjunto predeterminado de perguntas para fazer e recuperar anotações em tempo real com alguns cliques.
O mesmo vale para códigos de falha. A chave para usá-los com eficácia é a organização adequada e a acessibilidade. Sem esses dois ingredientes principais, os códigos de falha tornam-se mais um obstáculo do que uma ajuda. Uma maneira de fazer isso é usar um software de manutenção. Uma plataforma digital pode organizar os códigos de falha melhor do que qualquer armário de arquivo ou planilha do Excel e tornar mais fácil para os técnicos classificá-los rapidamente e identificar os relevantes no local da falha.
Os resultados
A solução de problemas sempre existirá na manutenção. Você nunca terá 100 por cento de certeza 100 por cento das vezes ao diagnosticar a causa da falha. O que você pode fazer é tomar medidas em direção a um processo de solução de problemas mais eficiente para garantir que o equipamento seja reparado de forma rápida e eficaz. Combinando um bom entendimento das métricas de manutenção com históricos detalhados de ativos, códigos de falha, listas de tarefas e outros recursos de ativos, e tornando todas essas informações acessíveis, você pode mover sua solução de problemas além da tentativa e erro para uma abordagem mais científica.
Manutenção e reparo de equipamentos
- Manutenção móvel:mais do que apenas uma tendência do setor (PODCAST)
- Está quebrado, ligue para manutenção:Um processo de solicitação de trabalho que é mais do que apenas tíquetes
- Uma lição de direção para operações e manutenção
- Novo livro ajuda a transformar a manufatura e a manutenção
- Estratégia e soluções do Exército para manutenção baseada em condições
- O esforço multi-habilidades para manutenção
- 5 Regras para operações e manutenção de parceria
- Melhorar a disponibilidade é muito mais do que manutenção
- Extensão de controle para planejadores de manutenção e outros
- Estratégias para componentes de transmissão de energia mais confiáveis