Fabricação de nanocompósitos Yolk-Shell Cu @ C como catalisadores de alto desempenho na carbonilação oxidativa de metanol em carbonato de dimetil
Resumo
Uma maneira fácil foi desenvolvida para fabricar compósitos de casca de gema com núcleos de Cu sintonizáveis encapsulados em esferas ocas de carbono (Cu @ C) com um diâmetro médio de cerca de 210 nm e tamanho de cavidade de cerca de 80 nm. Durante a pirólise, o nanoespaço confinado da cavidade oca garante que o processo de nucleação e crescimento dos nanocristais de Cu ocorra exclusivamente dentro das cavidades. O tamanho dos núcleos de Cu pode ser facilmente ajustado de 30 a 55 nm, variando a concentração de sal de cobre. Ao criar deliberadamente porosidade de casca por meio da ativação química KOH, em uma proporção de massa KOH / HCS otimizada de 1/4, o desempenho catalítico para a carbonilação oxidativa de metanol em carbonato de dimetila (DMC) da amostra ativada é aprimorado notavelmente com TOF até 8,6 h −1 na conversão de metanol de 17,1%. O catalisador de casca de gema ativada mostra propriedades catalíticas promissoras envolvendo a reutilização com leve perda de atividade catalítica e lixiviação insignificante de componentes ativados, mesmo após sete reciclagens, o que é benéfico para a implementação de produção limpa para o produto químico ecológico DMC completamente.
Histórico
Carbonato de dimetila (DMC) tem atraído muita atenção como um bloco de construção amplamente utilizado devido à sua excelente biodegradabilidade (por exemplo, baixa bioacumulação e persistência) e baixa toxicidade [1]. As potenciais aplicações industriais do DMC abrangem diversos campos, como solvente não tóxico, substituto alternativo para fosgênio, aditivo para combustível e intermediário para síntese de policarbonatos e isocianatos [2,3,4,5]. Em vista de vários métodos sintéticos de DMC, a carbonilação oxidativa de metanol (MeOH) usando CO, O 2 , e MeOH como matéria-prima tem representado um dos processos propostos favoráveis devido à alta taxa de utilização da fonte de carbono e benefícios ambientais. Os catalisadores usados nesta reação podem ser classificados principalmente em dois tipos:catalisadores contendo cloro e catalisadores sem cloro. Uma vez que existem alguns problemas, como problemas corrosivos graves, deterioração da qualidade do produto e desativação do catalisador, que resultam da perda de cloro dos catalisadores contendo cloro, os catalisadores sem cloro têm sido extensivamente estudados [6, 7]. Cobre ou óxido de cobre com suporte de carbono ativado (AC) têm demonstrado atividade catalítica promissora para a síntese de DMC [8,9,10], e os pesquisadores sugeriram que o Cu é o centro ativo para esta reação [10,11,12,13]. No entanto, a desativação de catalisadores de cobre suportados é geralmente atribuída à aglomeração de partículas de cobre, perda de espécies ativas e mudança do estado químico do cobre, entre os quais, o primeiro é mais sério. A fim de superar tais desvantagens, o projeto e a fabricação de nanopartículas encapsuladas em uma casca protetora são benéficos para reforçar a atividade catalítica e a estabilidade dos centros reativos na carbonilação oxidativa do metanol para DMC do ponto de vista tecnológico.
Ao longo desta linha, nanoestruturas de casca de gema (YSNs) ou nanocompósitos do tipo chocalho, em que nanopartículas de núcleo (NPs) são encapsuladas por uma camada externa com um espaço livre intersticial entre eles, têm sido particularmente populares devido às suas nanoestruturas hierárquicas / multiníveis únicas. , e acompanhando propriedades ópticas e elétricas e grande potencial na aplicação catalítica [14]. A casca protetora em YSNs pode efetivamente manter o elemento central estável, mesmo sob condições adversas e suficientemente expor sua superfície ativa [15]. Espera-se que o espaço vazio fechado seja útil para armazenamento químico, compartimentação e confinamento de interações hospedeiro-hóspede e, mais importante, fornecendo um ambiente único para a criação de ações combinadas entre o núcleo e uma casca permeável [16]. Essas características texturais notáveis permitem que os YSNs funcionem como candidatos promissores para satisfazer as demandas como estabilidade de sinterização e capacidade de reutilização para aplicações em catálise. Entre eles, nanoestruturas de casca de gema de carbono têm imediatamente atraído considerável interesse devido à condutividade inerente, bem como excelente estabilidade química e térmica do revestimento de carbono [17,18,19,20,21].
Recentemente, Lu e co-trabalhos relataram a preparação de esferas ocas através da montagem induzida por interação ácido-base fraca com o uso de ácido oleico um molde macio e ácido diidroxibenzoico funcional (DA) como precursor [22]. Aqui, estendemos seu trabalho para desenvolver uma abordagem fácil para os YSNs com tamanho de núcleo de Cu ajustável encapsulado dentro de esferas ocas de carbono (HCSs) (Cu @ C), empregando uma estratégia de envio em garrafa. A porosidade da casca de catalisadores heterogêneos de Cu @ C pode ser ajustada pela ativação de KOH, e seus efeitos no desempenho catalítico e na estabilidade na síntese de DMC também são investigados.
Métodos
Químicos
O ácido 2,4-di-hidroxibenzoico (DA) foi obtido na J&K Scientific Ltd. Ácido oleico, solução de amônia (25%), formaldeído, nitrato de cobre (Cu (NO 3 ) 2 · 3H 2 O), hidróxido de potássio (KOH) e metanol (MeOH) foram obtidos da Sinopharm Chemical Reagent Co. Ltd. Todos os produtos químicos eram de grau analítico e usados sem qualquer purificação adicional. Água desionizada obtida do sistema Milli-Q (Millipore, Bedford, MA) foi usada em todas as experiências. O 2 (> 99,99%) e CO (> 99,99%) foram fornecidos pela Beijing ZG Special Gases Science &Technology Co. Ltd.
Síntese de esferas ocas de carbono (HCS)
As esferas ocas de polímero (HPSs) com um núcleo oco e uma concha de polímero foram primeiro preparadas usando ácido oleico como molde macio e resina fenólica como precursor de carbono seguindo o procedimento relatado por Lu et al. [22]. Em um procedimento típico, 2,5 mmol de ácido 2,4-di-hidroxibenzoico e 7,5 mmol de formaldeído foram dissolvidos em 95 mL de água desionizada. Um volume de 5 mL de uma solução aquosa contendo 56 μL de ácido oleico e 180 μL de solução de amônia (25%) foi adicionado à solução preparada acima a 30 ° C sob agitação lenta por 30 min. Em seguida, a mistura foi transferida para uma autoclave hidrotermicamente envelhecida por 4 h a 140 ° C. Após centrifugação, lavado com água desionizada e etanol, seco a 50 ° C durante a noite e depois pirolisado a 700 ° C por 2 h sob fluxo de nitrogênio, o HCS foi obtido.
Síntese de materiais nanocompósitos Cu @ C
Normalmente, 0,3 g do HCSs como preparado foi primeiro disperso em 30 mL de solução de nitrato de cobre com faixa de concentração diferente de 0,03 a 0,24 M. Em seguida, a mistura foi transferida para uma autoclave para sofrer uma impregnação hidrotérmica a 100 ° C por 10 h. A amostra impregnada resultante, denotada como HCS-Cu 2+ , foi recuperado pelo mesmo método do HPS. Depois de calcinado a 400 ° C por 2 h sob H 2 / N 2 (10% / 90%), finalmente, obtiveram-se os nanocompósitos de casca de gema Cu @ C-X (X =0,03, 0,06, 0,12, 0,24).
Síntese do catalisador Cu @ A-HCS com a esfera de carbono ativado por KOH como suporte
O tratamento de HCS com KOH é tentado, com a intenção de modificar as características do suporte de carbono e afetar ainda mais o desempenho do catalisador de Cu. Normalmente, 0,3 g de HCSs foram misturados com 0,15 g de KOH fisicamente na ausência de água. Após o pré-tratamento, a amostra foi aquecida em corrente de nitrogênio de 80 mL / min com uma taxa de rampa de 10 ° C / min até 700 ° C por 2 h e, em seguida, resfriada à temperatura ambiente. Os carbonos pós-tratados com KOH foram lavados repetidamente com HCl diluído e subsequentemente com água destilada até que nenhum íon cloro foi detectado (AgNO 3 teste). Depois de seco a 60 ° C durante a noite, solução de nitrato de cobre 0,12 M foi usada durante a impregnação hidrotérmica e outros procedimentos foram idênticos aos de Cu @ C-0,12, finalmente rendendo as amostras modificadas denotadas como Cu @ A-HCS.
O desempenho catalítico de Cu @ C-X (X =0,03, 0,06, 0,12, 0,24) e Cu @ A-HCS
A carbonilação oxidativa do metanol foi realizada em autoclave de aço inoxidável de 25 mL forrada com Teflon e equipada com agitador magnético. Em um experimento típico, 0,2 g de catalisador e 10 mL de metanol foram carregados na autoclave, que foi então bem vedada, purgada três vezes com CO e a seguir pressurizada a 3,0 MPa com CO e O 2 (P CO :P O2 =2:1) à temperatura ambiente. A reação prosseguiu a 120 ° C com agitação contínua a 750 rpm durante 1,5 h. Após a reação, o reator foi resfriado à temperatura ambiente e despressurizado. Os catalisadores foram separados por filtração. As concentrações dos produtos no filtrado foram determinadas por cromatografia gasosa (GC) usando um detector FID. A reciclabilidade do catalisador usado foi estudada realizando uma série de execuções consecutivas.
A principal reação da carbonilação oxidativa de metanol a carbonato de dimetila foi mostrada a seguir:
2CH 3 OH + 1/2 CO + O 2 =(CH 3 O) 2 CO + H 2 O.
A concentração de cobre, conversão de MeOH (C MeOH ), Seletividade DMC (S DMC ), e a frequência de rotação (TOF) foram calculadas pelas seguintes equações:
A concentração de cobre (C Cu , mmol / g) =conteúdo de Cu (% em peso) / 63,55 × 1000.
Conversão de MeOH (C MeOH ,%) =metanol reagido / metanol introduzido × 100%.
Seletividade DMC (S DMC ,%) =2 DMC produzido / metanol reagido x 100%.
Frequência de rotação =DMC produzido / (quantidade molar de cobre × tempo de reação).
Caracterização
Os padrões de difração de raios-X (XRD) foram registrados em um difratômetro Rigaku D-Max 2500, usando Cu K radiação α ( λ =0,154 nm) a 40 kV e 100 mA, com uma taxa de varredura de 4 ° min −1 em 2 θ de 5 ° –85 °. A análise de microscopia eletrônica de transmissão (TEM) foi realizada em um microscópio eletrônico de transmissão de emissão de campo JEM 2100F (JEOL, Tóquio, Japão) operando a 200 KeV. As amostras de TEM foram preparadas por imersão de grades de Cu revestidas com C em soluções de etanol de amostras e secagem em temperatura ambiente. A análise termogravimétrica (TG) foi conduzida em um analisador termogravimétrico, STA 449 F3 Júpiter (NETZSCH), com um N 2 ou taxa de fluxo de ar de 50 mL / min. As áreas de superfície e os volumes de poro foram determinados a partir de isotermas de adsorção de nitrogênio a 77 K usando o analisador de área de superfície 3H-2000PS2 (Beishide). As áreas de superfície específicas de Brunauer-Emmett-Teller (BET) foram calculadas usando dados de adsorção na faixa de pressão relativa de P / P 0 =0,04–0,3. As curvas de distribuição do tamanho dos poros do mesóporo foram calculadas pelo método BJH (Barrett-Joyner-Halenda) a partir do ramo de adsorção. Os volumes totais dos poros foram estimados a partir da quantidade de nitrogênio adsorvido a uma pressão relativa ( P / P 0 ) de 0,99. O teor de cobre é determinado pela dissolução do catalisador em uma mistura de ácido forte seguida pela análise de espectrometria de adsorção atômica (AAS) usando equipamento SpectrAA-220 AAS. A análise do produto da reação foi realizada por cromatografia gasosa (GC; Agilent 6890) usando um detector FID.
Resultados e discussão
Parâmetros de textura e estabilidade térmica do suporte conforme preparado
A área de superfície BET e o volume de poro das amostras envolvidas em diferentes estágios de preparação estão resumidos na Tabela 1. Como visto na Fig. 1a e Tabela 1, o HPS obtido tem áreas de superfície BET baixas (~ 23 m 2 g −1 ) Portanto, dificilmente se pretende introduzir os precursores do catalisador através do método de impregnação convencional. Assim, utilizamos o processo de impregnação hidrotérmica para aumentar a capacidade de difusão de modo que o precursor de cobre possa ser puxado com sucesso para a cavidade do HPS. A área de superfície BET de HPS e HPS-Cu mudou de 23 para 15 m 2 g −1 certificou a declaração. Além disso, as imagens TEM na Fig. 2 confirmam ainda as nanopartículas de Cu formadas exclusivamente dentro dos limites do invólucro de carbono.
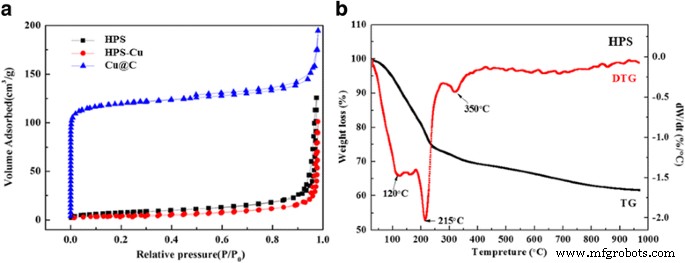
a N 2 isoterma de adsorção-dessorção dos produtos obtidos após cada etapa:HPS, HPS-Cu 2+ e Cu @ C. b Perfis TG-DTG de HPS
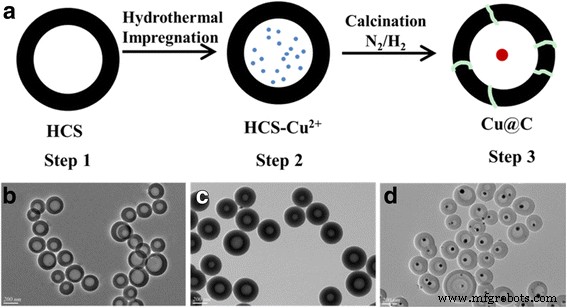
a Ilustração esquemática para a síntese de nanocompósitos de Cu @ C em condições de impregnação hidrotérmica. Imagens TEM dos produtos obtidas após cada etapa: b HCS, c HCS-Cu 2+ , e d Cu @ C
O processo de carbonização do HPS é investigado por TG. A Figura 1b mostra o resultado de TG-DTG em N 2 . Ao longo de todo esse intervalo, a maior perda de HPS aparece perto de 215 ° C e completa-se em torno de 350 ° C. Isso pode ser atribuído à decomposição do ácido oleico embutido no HPS e carbonização da estrutura do polímero [22]. Assim, em comparação com as curvas TG dos catalisadores Cu @ C (ver na Fig. 5b), para garantir a carbonatação completa do HPS e evitar a agregação das nanopartículas de Cu, 400 ° C foi determinado como a temperatura de preparação ideal.
Propriedades estruturais de nanocompósitos Cu @ C
Tomado [email protected] nanocompósito de casca de gema como exemplo, o procedimento de síntese para a preparação de estruturas de casca de gema com NPs de Cu encapsulados por casca de carbono, seguindo uma estratégia de envio em uma garrafa, é ilustrado na Fig. 2a. A Figura 2b, c mostra imagens TEM típicas do produto resultante obtido em cada etapa. Como visto, HCSs com tamanho uniforme de cerca de 210 nm foram sintetizados com sucesso (Fig. 2b). Durante o processo de impregnação hidrotérmica, nenhuma diferença óbvia pode ser observada entre HCSs e HCS-Cu 2+ (Fig. 2c). Porém, após a calcinação, a morfologia oca é mantida, mas NPs de Cu podem ser observados devido à decomposição dos sais de cobre. Finalmente, o Cu @ C estruturado em casca de gema (Fig. 2d) com um diâmetro de ~ 200 nm e tamanho de cavidade de ~ 80 nm é obtido. A microscopia eletrônica de transmissão de alta resolução (HRTEM) (Fig. 3b) mostra que as partículas do núcleo têm um espaço de 0,18 nm indexado ao plano de Cu (2 0 0). Isso é consistente com os resultados de XRD (Fig. 3c), onde a difração atinge o pico em 2 θ =43,3 °, 50,4 ° e 74,1 ° tornaram-se observáveis porque Cu 2+ espécies no precursor (HCS-Cu 2+ ) são reduzidos ao metal Cu sob uma atmosfera redutora, correspondendo aos planos cristalinos específicos (1 1 1), (2 0 0) e (2 2 0) de Cu, respectivamente, que é baseado no cartão JCPDS 04-0836 . O N 2 A isoterma de adsorção-dessorção do [email protected] resultante apresenta uma isoterma do tipo I, demonstrando que existem microporos abundantes nas conchas de carbono de [email protected] (Fig. 3d). Esta amostra tem uma área de superfície BET de 365 m 2 / g acompanhado por um volume de poro de 0,23 cm 3 / g. A baixa área superficial específica junto com a microporosidade estreita são normalmente apontadas como as principais desvantagens, limitando suas aplicações, que serão discutidas a seguir. Os parâmetros de textura detalhados das amostras estão resumidos na Tabela 2.
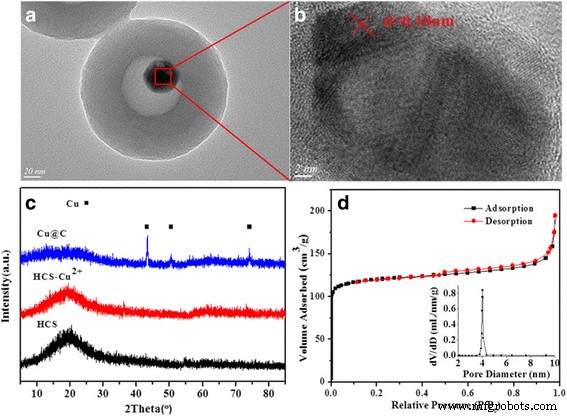
a , b Imagens TEM do núcleo de cobre em [email protected]. c Padrões de XRD dos produtos obtidos após cada etapa:HCS, HCS-Cu 2+ , e [email protected]. d N 2 isoterma de adsorção-dessorção e distribuição de tamanho de poro de [email protected]
O caminho mecanístico para a formação de um único Cu NPs dentro da camada de carbono pode ser explicado pelo processo de nucleação e crescimento confinado. No progresso da pirólise, muitos núcleos minúsculos de CuO iniciais se formaram e se distribuíram completamente dentro da cavidade oca devido à decomposição do Cu incorporado (NO 3 ) 2 moléculas. Quando o agente redutor H 2 difunde-se na cavidade, os núcleos CuO formados são posteriormente reduzidos a núcleos Cu metálico, que tendem a migrar e agregar para formar partículas maiores. Uma vez que os maiores se formem, os núcleos de Cu remanescentes dentro da cavidade serão sucessivamente absorvidos pela superfície das partículas pré-formadas, o que resulta no crescimento do nanocristal de Cu. Mecanismo semelhante também foi proposto em outro lugar [23]. Com base no processo de nucleação e crescimento, pode-se inferir que o tamanho do núcleo de Cu resultante pode ser controlado ajustando a quantidade de precursor de sal de cobre acomodado na cavidade confinada.
Controle de tamanho do núcleo de cobre
Variando Cu (NÃO 3 ) 2 concentrações de 0,03 a 0,24 M, uma série de nanocompósitos de casca de gema, denotados como Cu @ C-X (X =0,03, 0,06, 0,12, 0,24), foram obtidos. A morfologia e o tamanho dos produtos foram examinados por TEM. Como visto na Fig. 4a-d, quase todas as nanoesferas ocas consistem em uma única partícula em seu interior. No entanto, o tamanho do núcleo de Cu das nanoesferas resultantes aumenta de 30 ± 1,3 para 55 ± 2,5 nm (Fig. 4e-h) com um aumento de Cu (NO 3 ) 2 concentrações, conforme determinado a partir de imagens TEM, levando em consideração pelo menos 150 partículas. Notavelmente, uma fração de esferas ocas de carbono (HCSs) são coexistentes com YSNs para o baixo Cu (NO 3 ) 2 concentração (Fig. 4a). Além disso, alguns pequenos NPs de Cu decorados na superfície externa da casca de carbono (Fig. 4d), que podem ser causados pela decomposição e agregação do Cu residual (NO 3 ) 2 fora da casca.
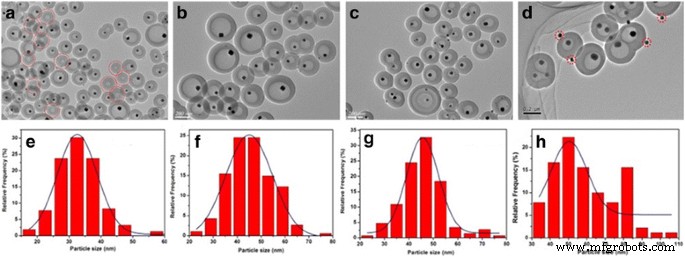
Imagens TEM e histogramas de distribuição de tamanho correspondentes de Cu NPs em amostras: a , e [email protected], b , f [email protected], c , g [email protected] e d , h [email protected]
A Figura 5a mostra os padrões de XRD de Cu @ C-X conforme preparado (X =0,03, 0,06, 0,12, 0,24). Todas as amostras apresentam três picos de reflexão típicos indexados a cristais de Cu (Cartão JCPDS nº 04-0836). Conforme a concentração de sal de cobre aumenta, os picos de difração são muito mais fortes e nítidos, enquanto o tamanho do Cu NP aumenta de 26,6 para 52,2 nm usando a equação de Scherrer com base no pico mais forte dos padrões, que está bem de acordo com os resultados do TEM . Além disso, a análise de TG foi conduzida para determinar o conteúdo de Cu das nanoesferas na Fig. 5b. Assumindo que os resíduos consistem completamente em CuO, as quantidades de carga de Cu de Cu @ CX (X =0,03, 0,06, 0,12, 0,24) são calculadas em aproximadamente 5,9, 7,5, 8,0 e 9,9% em peso, respectivamente, que é idêntico a os valores determinados a partir da análise AAS.
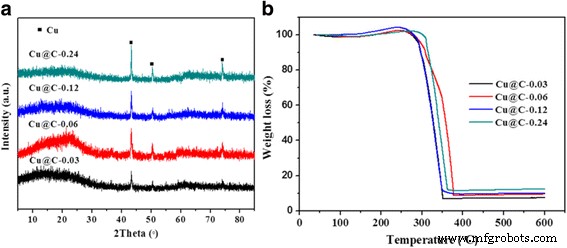
a Padrões de XRD e b Curvas TG das amostras:[email protected], [email protected], [email protected], [email protected]
Desempenho catalítico de Cu @ C-X (X =0,03, 0,06, 0,12, 0,24)
O catalisador Cu @ C preparado foi testado para a carbonilação oxidativa em fase líquida de metanol em DMC (Tabela 2). Inesperadamente, embora seja melhor do que os outros, o catalisador [email protected] apenas deu uma conversão de metanol extremamente ineficiente de 0,82%. A baixa atividade catalítica pode estar associada à falta de porosidade suficiente e grande volume de poro na casca. Até onde sabemos, poros localizados na casca atuam como canais que conectam o vazio das esferas com o ambiente externo [24]. Embora a espessura da casca de [email protected] seja de ~ 15 nm, a falta de porosidade suficiente (o volume do poro estrutural é de 0,23 cm 3 / g com uma área de superfície específica baixa de 365 m 2 / g) restringe a quantidade de moléculas de reagente para se difundir nas cavidades e ainda entrar em contato com o componente ativo enterrado dos núcleos de Cu. Assim, é fundamental criar mais porosidade nas cascas para facilitar o transporte de massa. Como se sabe, a ativação de KOH é um método bem estabelecido no ajuste da porosidade de materiais de carbono [25,26,27]. Com este método, microporos e mesoporos podem ser introduzidos no carbono, juntamente com um aumento significativo na área de superfície específica e volume de poro [28]. Durante o procedimento de ativação, a quantidade de KOH é geralmente considerada como um fator crítico para influenciar a estrutura porosa; assim, diferentes proporções de massa de KOH / HCS foram feitas para otimizar o [email protected] ativado.
Propriedades físico-químicas de Cu @ A-HCS
A imagem TEM (Fig. 6a) mostra que a amostra Cu @ A-HCS ativada mantém a morfologia esférica na proporção de massa inferior de KOH / HCS (1/4), mas parcialmente ou severamente atacada com proporção de massa KOH / HCS superior a 1 / 2 (Consulte as informações de apoio Fig. 2a, b). Este resultado está de acordo com relatórios anteriores de que uma quantidade excessiva de KOH levará a mais queima de carbono e destruirá a morfologia [29]. Curiosamente, para os nanocompósitos de Cu @ A-HCS, após a ativação, partículas de cobre altamente dispersas são predominantemente incorporadas na casca das esferas ocas, que coexistem com várias outras encapsuladas nas cavidades. Quando comparados com [email protected], os NPs de Cu inseridos na casca exibem o tamanho de partícula relativamente menor centrado em 18 ± 2 nm (Fig. 6b) porque a matriz da casca impede que os pequenos aglomerados de Cu cresçam. A existência de pontos brancos na casca sugere a existência de micrósporos desordenados. A Figura 6c mostra o N 2 -isotermas de dessorção-dessorção do Cu @ C-HCS, que exibem curvas representativas do tipo IV associadas à característica mesoporosa, revelando que as amostras ativadas possuem estruturas hierarquicamente micro- / mesoporosas. Além disso, pode ser verificado que após a ativação de KOH a 700 ° C por 2 h, a área de superfície de A-HCS aumentou de 471 para 989 m 2 / g, ainda maior do que o carvão ativado (812 m 2 / g), e o volume do micropore (V mic ), o volume mesopore (V mes ), e o volume total (V T ) também aumentou, mas a proporção de V mic para V T tende a diminuir. Esse resultado indica que mais mesoporos são criados após a ativação de KOH, o que possivelmente está relacionado ao alargamento dos microporos ou à criação de mesoporos pela presença de KOH [30]. A grande área superficial típica e a porosidade desenvolvida dos catalisadores Cu @ A-HCS favorecem a dispersão da fase ativa sobre o suporte, garantem a transferência rápida de matéria entre o catalisador confinado e o ambiente externo (reagentes), e aumentam sua resistência à sinterização em alta carga de metal [31]. Como confirmado pelo padrão de XRD na Fig. 6d de Cu @ A-HCS, todos os picos podem ser indexados indiscutivelmente a Cu cúbico (JCPDS 04-0836); entretanto, o alargamento dos picos característicos implica a formação dos Cu NPs de pequeno tamanho. Na verdade, o tamanho médio dos Cu NPs em Cu @ A-HCS é estimado em 15 nm de acordo com a equação de Scherrer, o que está de acordo com o resultado obtido por TEM. Como previsto, os catalisadores Cu @ A-HCS com 11% em peso de Cu determinado por AAS foram obtidos usando o mesmo método, maior que Cu@C-0,12. Mais importante ainda, durante o processo de ativação, grupos funcionais contendo oxigênio possivelmente originados da ativação de KOH são inevitavelmente introduzidos em HCSs [27]. No geral, a geração de grupos de superfície, o aumento da área de superfície e do volume dos poros, resultam sinergicamente na alta dispersão de NPs de Cu, o que é benéfico para a promoção da atividade catalítica [32,33,34]. As propriedades texturais detalhadas estão resumidas na Tabela 3.
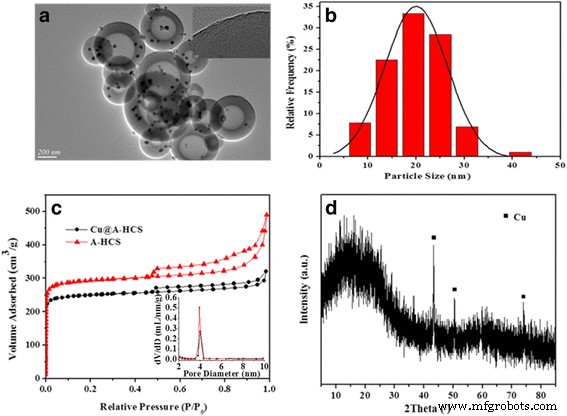
a Imagem TEM de Cu @ A-HCS e b seu tamanho de partícula de Cu correspondente. c N 2 isotermas de adsorção-dessorção e distribuições de tamanho de poro de A-HCS e Cu @ A-HCS. d Padrões de XRD do catalisador Cu @ A-HCS
Desempenho catalítico de Cu @ A-HCS
Os desempenhos catalíticos de A-HCS e Cu @ A-HCS estão resumidos na Tabela 4. Como mostrado na Tabela 4, é claro que o suporte A-HCS não exibiu atividade catalítica na síntese de DMC. Como esperado, as propriedades catalíticas da amostra ativada melhoraram dramaticamente em comparação com as não ativadas. É digno de nota que em comparação com 2.04 h −1 e 4,38% para [email protected], a atividade incipiente de Cu @ A-HCS exibe um aumento próximo de quatro vezes no TOF de 8,6 h −1 acompanhado por um aumento correspondentemente dramático em C MeOH de 17,1%, respectivamente nas mesmas condições. Esses resultados notáveis são razoáveis ao considerar o aumento na área de superfície e os volumes de poros das conchas de carbono podem adsorver positivamente mais moléculas de reagente da solução a granel, facilitar as taxas de difusão através dos canais significativamente e enriquecê-los no espaço vazio do catalisadores, resultando em uma concentração de reagente mais alta para catálise confinada acessível. Um catalisador com vida útil razoavelmente longa é fundamental para sua aplicação na indústria. O catalisador escolhido é uma amostra de Cu @ A-HCS ativado com uma atividade promissora para testar a durabilidade em um sistema descontínuo descrito acima. Catalisadores heterogêneos freqüentemente sofrem com uma diminuição da atividade como uma extensa lixiviação de espécies de metal ativo durante as reações [35]. E igualmente importante é a estabilidade contra coalescência para catalisadores baseados em nanocristais [36]. Em nosso caso, conforme resumido na Tabela 3, o catalisador Cu @ A-HCS recuperado (separado por filtração) mantém uma atividade catalítica muito maior do que CuCl, mesmo após sete execuções (entradas 2-8), e a lixiviação média de Cu, que é o constituinte ativo do catalisador é em torno de 0,004%, permanecendo quase o mesmo com o catalisador fresco. Enquanto isso, a estrutura cristalina e a morfologia dos catalisadores dificilmente não mudaram após ciclos sucessivos (Arquivo adicional 1:Figura S2). Aparentemente, a presença do invólucro de carbono poroso é suficiente para estabilizar as espécies metálicas ativas, evitando sua agregação e lixiviação; ao mesmo tempo, as conchas são permeáveis o suficiente para que as superfícies catalíticas permaneçam acessíveis e vantajosas para os reagentes e produtos [12]. Portanto, os catalisadores YSN são sistemas catalíticos eficazes e não corrosivos, em que os Cu NPs como materiais do núcleo encapsulados na cavidade dos HCSs fornecem centros reativos e o invólucro de carbono poroso evita que o núcleo se agregue e lixivie sob as condições de reação.
Conclusões
Em resumo, apresentamos uma estratégia de envio na garrafa fácil para a fabricação de nanoestruturas de casca de gema de carbono compostas de NPs de Cu com tamanho personalizado em distribuições estreitas, ajustando a concentração de sais de cobre. Como demonstrado, as propriedades catalíticas deste sistema do tipo chocalho na carbonilação oxidativa do metanol em DMC são altamente dependentes da porosidade. Amostra ativada com área de superfície extremamente alta permite a criação de nanorreatores confinados altamente eficientes para reações catalíticas com conversão consideravelmente mais alta (17,1%) e TOF (8,6 h −1 ), longa vida útil e lixiviação insignificante em cada ciclo, que inquestionavelmente satisfazem a produção limpa do produto químico verde DMC. Além disso, a rota de síntese descrita neste artigo pode abrir novas oportunidades para a preparação de nanoestruturas de casca de gema com várias composições confinadas dentro da casca de carbono.
Nanomateriais
- Nanocups podem dobrar luz
- Síntese fácil de WS2 / Bi2MoO6 heteroestruturado como fotocatalisadores acionados por luz visível de alto desempenho
- Novos nanocompósitos de poliestireno com polianilina dopada com ácido lauril sulfúrico
- Fabricação de alto rendimento de nanofibras de qualidade usando eletrofiação de superfície livre modificada
- Desempenho fotocatalítico acionado por luz visível de nanocompósitos N-dopados com ZnO / g-C3N4
- Fabricação e caracterização de novo composto de suporte de catalisador anódico de nanofibra de carbono Tio2 para célula de combustível de metanol direto via método de eletrofiação
- Nanocompósitos de poli (N-isopropilacrilamida) magnético:efeito do método de preparação nas propriedades antibacterianas
- Fabricação, caracterização e citotoxicidade de nanopartículas de carbonato de cálcio derivadas de casca de ouro conjugada em forma esférica para aplicações biomédicas
- A Fabricação e Desempenho de Absorção de Ondas Eletromagnéticas de Alta Eficiência de Nanocompósitos Estruturados com CoFe / C Core – Shell
- Fabricação e caracterização de Nano-Clips de ZnO pelo processo mediado por poliol