Automatizando Job Shops? Você aposta!
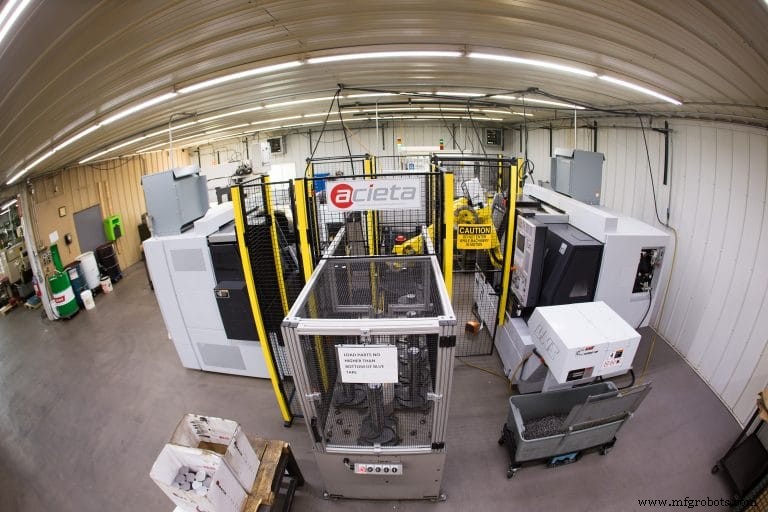
Às vezes, um único operador pode cuidar de vários robôs, cada um dos quais cuidando de várias máquinas. Tudo se soma!
Se “automação” é o zumbido constante que você ouve de praticamente todos na metalurgia hoje em dia, os donos de oficinas podem ser as únicas pessoas gritando “Não!” Ou pelo menos “Espere!” Como, eles perguntam, você pode automatizar de forma econômica peças de baixo volume e alto mix? No entanto, não é apenas factível, mas provavelmente necessário.
Como disse Steve Alexander, vice-presidente de operações da Acieta LLC, um integrador de automação com locais em Waukesha, Wisconsin, e Council Bluffs, Iowa, “Os EUA lideram o mundo em fabricação, mas também têm uma das maiores taxas de fabricação por hora custos trabalhistas. As lojas de empregos não estão apenas competindo com outras lojas locais por negócios, elas também estão competindo com outros países. A automação pode reduzir seus custos para que possam competir melhor.”
Ele acrescentou que a demanda por capacidade de fabricação está superando a oferta de mão de obra disponível e “as oficinas podem achar difícil competir com oficinas maiores e mais estabelecidas” por talentos cada vez mais caros. Mas um robô pode cuidar de várias máquinas e, em alguns casos, um único operador pode cuidar de vários robôs, cada um dos quais cuidando de várias máquinas.
“Isso libera os operadores para realizar operações secundárias, como rebarbar peças, montar ou gastar mais tempo em verificações de qualidade”, disse Alexander. Para citar apenas dois exemplos, a Central United em Newburg, Wisconsin, usa um único robô FANUC M-20iB para cuidar de dois tornos. Outro cliente da Acieta em New Berlin, Wisconsin, usa um único robô FANUC R-2000iB para cuidar de quatro máquinas. “Em ambos os casos, há apenas um único operador responsável por carregar as peças brutas no transportador ou na estação de fila para o robô pegar.”
Alexander acrescentou outro motivo convincente para automatizar:a ergonomia. “As lesões no local de trabalho são uma preocupação para qualquer loja de tamanho. Algo tão simples quanto carregar uma peça em um mandril de torno pode rapidamente se transformar em uma lesão por esforço repetitivo para um operador quando esse processo é repetido centenas de vezes por dia. Entre tempo perdido e reclamações, essas lesões custam às empresas bilhões de dólares a cada ano. Robôs devidamente integrados podem remover um processo repetitivo do operador, melhorando assim o bem-estar dos funcionários.”
Opções e integradores
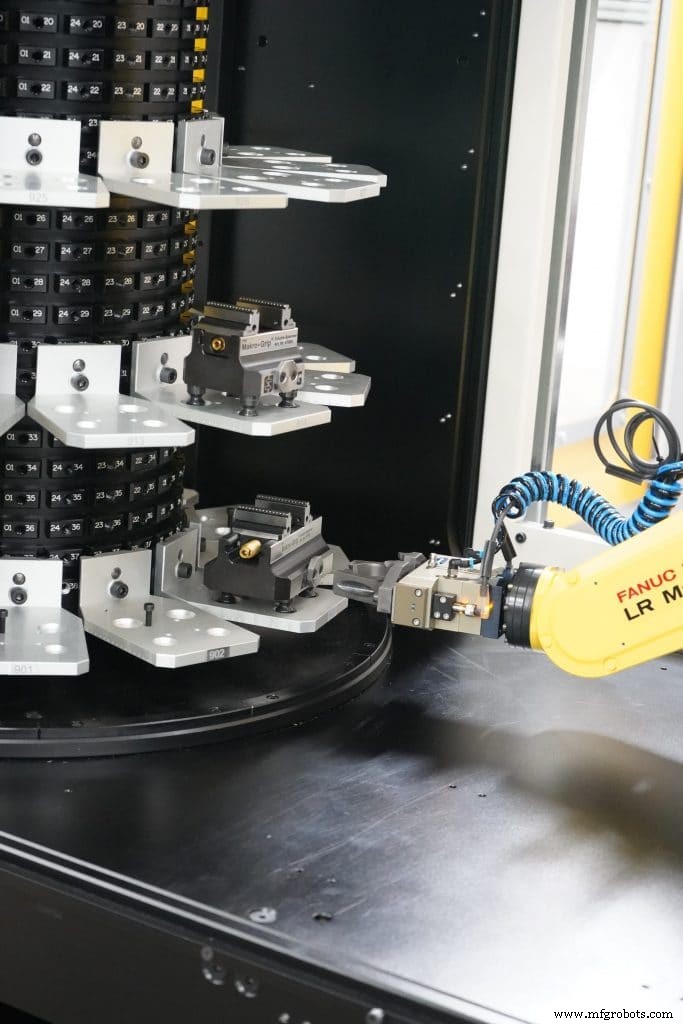
Até agora tudo bem. Mas, como John Lucier, gerente de automação da Methods Machine Tools Inc., Sudbury, Massachusetts, explicou, o simples objetivo de “fazer mais peças com mais eficiência” pode levar a abordagens muito diferentes, dependendo do tipo de trabalho que está sendo produzido e dos volumes envolvidos .
Por exemplo, digamos que uma oficina de médio volume precise mudar algumas vezes por semana. “Com o planejamento adequado, uma célula pode ser trocada no turno tripulado, permitindo uma boa quantidade de produção autônoma no turno seguinte.” E dentro deste contexto, a velocidade requerida do robô dependeria em grande parte do tempo do ciclo de usinagem das peças produzidas. Quanto menor o tempo de ciclo, mais rápido o robô precisa ser e menor a probabilidade de um robô suportar várias máquinas.
Mas as lojas com volumes ainda menores – mesmo tamanhos de lote de um – também podem ser boas candidatas à automação, explicou Lucier. Exceto que “a consideração mais importante é reduzir o tempo de troca ou até mesmo eliminar totalmente o tempo de configuração. As pessoas ficam presas no tempo de ciclo e no tempo de carga/descarga, mas se seus volumes são tão baixos que metade do seu tempo é gasto na troca, atacar o tempo de troca, mesmo às custas do tempo de ciclo, pode fazer sentido.”
Uma maneira de “eliminar” a configuração é automatizá-la, e os robôs de hoje podem ser programados para alterar tanto suas próprias ferramentas de ponta de braço quanto o suporte de trabalho na máquina. Outra abordagem é carregar paletes comuns a partir de um carrossel (ou outro tipo de empilhador), independentemente da peça que está sendo produzida. Isso elimina a necessidade de trocar as ferramentas do robô ou programar diferentes movimentos de carga/descarga para diferentes peças.
O sistema Methods PlusK leva este conceito um passo adiante e também carrega os porta-ferramentas do carrossel. Concebido para suportar as máquinas da série RoboDrill da FANUC, o carrossel da PlusK tem cinco anéis, cada um com 12 estações, num total de 60 estações. Cada estação pode conter um palete de peças ou um porta-ferramentas e o robô pode carregar ambas as peças na mesa de trabalho do RoboDrill e ferramentas na torre de 21 ferramentas integrada da máquina.
Mas, como destacou Lucier, se você deseja automatizar a produção de 30 ou 40 peças completamente diferentes, 21 ferramentas podem não ser suficientes. “Geralmente carregamos peças em pequenas morsas de cinco eixos de fornecedores como a Lang Technovation”, explicou Lucier. “E geralmente misturamos e combinamos peças e ferramentas no carrossel. Digamos que um trabalho exija cinco ferramentas que diferem das ferramentas usadas no trabalho anterior. Posso usar o robô para carregar cada ferramenta conforme necessário ou carregar todas as cinco ferramentas na torre de uma só vez, da mesma forma que um operador faria um trabalho.”
Se essas considerações estão começando a fazer sua cabeça doer, isso é compreensível. Porque, embora tenha ficado muito mais fácil implementar a automação nos últimos anos, ainda é difícil o suficiente para que a maioria das oficinas seja sensata em aproveitar integradores como Acieta e Methods. Do ponto de vista de Lucier, programar o robô é a parte mais fácil. Coisas como lidar com o workholding automático, remoção de cavacos na zona de trabalho e a melhor forma de apresentar as peças ao robô são o maior desafio. É aí que os conselhos de especialistas realmente valem a pena.
Automatizando máquinas legadas
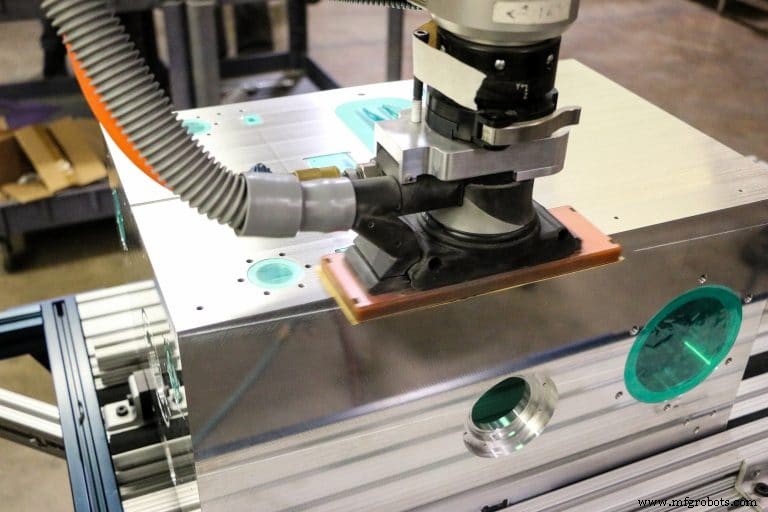
Aqui está um exemplo de como isso pode acontecer. Em meados de 2017, Gary Kuzmin, proprietário da All Axis Machining em Dallas, Texas, era um exemplo clássico de frustração de job shop. Ele tinha mais trabalho potencial do que a força de trabalho disponível poderia suportar e uma loja cheia de centros de usinagem de cinco eixos alemães de ponta, EDMs e outras tecnologias que os OEMs não podiam automatizar economicamente com o tipo de versatilidade que poderia tirá-lo dessa ligar. Sua solução foi investir em um robô colaborativo da Universal Robots (UR), Ann Arbor, Michigan.
Como qualquer proprietário de job shop, o principal requisito de Kuzmin era manter “flexibilidade total” em sua operação. “Faremos uma parte por dois ou três dias e depois partimos para outra. Em um determinado mês, poderíamos produzir de 30 a 40 peças diferentes em uma máquina.” Então ele precisava de um robô que fosse fácil de configurar e trocar. E ele precisava de recursos como garras de controle de força para que o robô pudesse se adaptar a diferentes peças e a mudança de material bruto para uma peça acabada e de paredes mais finas.
UR entregue em todos os aspectos. Seus robôs possuem uma interface de programação em um pingente de mão. Eles operam com segurança lado a lado com humanos porque os robôs param automaticamente ao entrar em contato com um operador (daí o termo robô colaborativo, ou “cobot”). Eles são fáceis de treinar e não intimidam.
Kuzmin explicou que uma das principais razões para a flexibilidade da solução da UR é uma arquitetura aberta que permitiu que terceiros desenvolvessem software, sistemas de visão, atuadores finais e outros acessórios que funcionam com robôs UR. A UR facilita o esforço de integração fornecendo um showroom on-line completo chamado UR+.
Mesmo com isso, Kuzmin descobriu que não havia uma solução pronta para programar o robô para realizar lixamento ou rebarbação, duas funções que ele queria automatizar porque são difíceis para os humanos, e especialmente para os trabalhadores mais velhos. Assim, a All Axis utilizou o kit de desenvolvimento de software gratuito da UR para criar suas próprias rotinas, que seguem a curvatura da peça com base no modelo CAD.
Esses plug-ins integram o controle do aplicativo por meio do próprio teach pendant do cobot. “A Universal Robots fez um trabalho fantástico ao disponibilizar esta solução para lojas como a nossa”, disse Kuzmin. “Não estamos presos a um ambiente proprietário. Em vez disso, recebemos um livro de receitas com uma maneira fácil de expandir a comunicação”, acrescentando que a All Axis usa protocolos como TCP/IP, Ethernet, Modbus e Profinet para conectar cobots e máquinas.
“Outra vantagem é que não precisamos pagar contratos de licença especiais – tudo vem com a compra do cobot UR”, disse Kuzmin. “Nos inscrevemos no site da UR para nos tornarmos desenvolvedores e baixamos os elementos de que precisamos.”
Em outro exemplo, a All Axis decidiu que queria a capacidade de mover um cobot de máquina para máquina o mais rápido possível. O desafio foi criar um sistema que reorientasse o cobot para a próxima máquina e o prendesse ao chão sem fazer furos no concreto. A solução foi colocar epóxi um receptáculo no concreto e prender um pino de indexação.
“Se o robô precisar ser movido ou atendido, você simplesmente destrava e puxa os pinos e move o robô conforme necessário”, disse Kuzmin. “Quando você reposiciona o robô e trava os pinos, tudo ainda está indexado. Também anexamos a bandeja de apresentação ao suporte do robô, para que sua posição em relação ao eixo do robô nunca mude.”
Em apenas alguns meses, Kuzmin e sua equipe ficaram tão bons em integrar cobots (agora eles têm sete) e tão empolgados com os benefícios da automação que criaram uma empresa separada chamada All Axis Robotics. Embora Kuzmin tenha dito que é relativamente fácil automatizar uma nova máquina gastando cerca de US$ 150.000 com o OEM, ele vê um tremendo potencial na automação de máquinas legadas, que é o foco deles.
Para dar um exemplo de como a automação ajudou nos resultados da All Axis Machining, um trabalho que normalmente levava seis meses para ser concluído em 2 meses e meio usando o robô. “Foi fenomenal. O ROI foi de sete a oito meses”, disse Kuzmin.
Talvez em sua inovação mais impressionante, a All Axis combinou um robô UR com um microscópio e câmera prontos para uso, além de inteligência artificial (IA) e aprendizado profundo, para criar um sistema que detecta rebarbas, bordas enroladas ou qualquer anomalia (como hardware ausente) em uma peça.
Isso é importante, porque, como explicou Kuzmin, muitas rebarbas não podem ser identificadas exceto sob ampliação e os olhos de um humano ficarão cansados após apenas 20 a 30 minutos de tal inspeção. Mas também é difícil automatizar.
“Rebarbas são como flocos de neve – não há dois iguais”, disse Kuzmin. “Nosso sistema, que chamamos de Aurora, usa IA para ensinar a si mesmo como é uma rebarba. Quanto mais rebarbas ele vir, melhor será capaz de detectá-las. O sistema irá identificar a rebarba, classificá-la e classificar a peça após rejeitá-la devido à rebarba. Ele também registra a inspeção e a localização da broca para que os operadores possam voltar para corrigir a peça com eficiência e movê-la.”
A All Axis apresentou o Aurora em 2018 e Kuzmin diz que a maior resposta foi:“Estamos procurando algo assim há anos!” Uma próxima versão do sistema incluirá a capacidade de inserir insertos helicoidais (comumente chamados de Heli-Coils) e hardware em peças também.
Os robôs industriais contra-atacam!
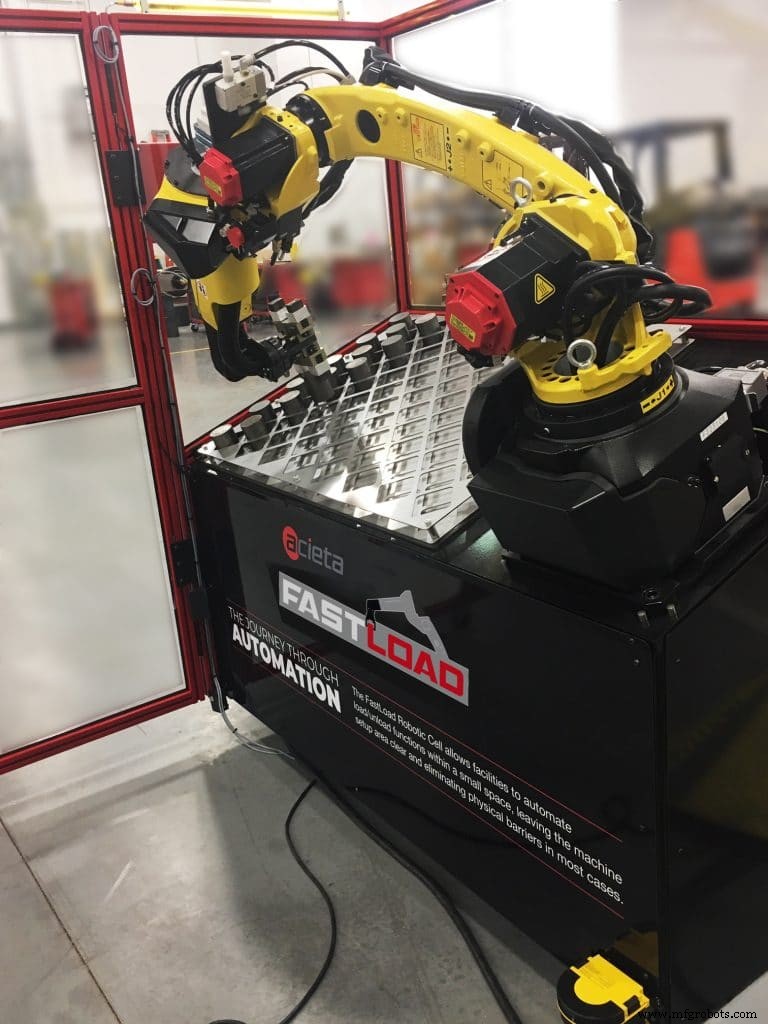
Conforme discutido, os cobots UR são fáceis de configurar e integrar com uma variedade de máquinas e acessórios. Mas fornecedores de robôs industriais, como a FANUC e a KUKA Robotics, tomaram conhecimento de recursos como o pingente de instrução manual intuitivo e introduziram suas próprias versões.
Lucier, da Method, reconheceu que “uma vez era absolutamente verdade que os robôs colaborativos eram mais fáceis de programar. Mas montar um robô industrial não é mais diferente de montar um robô colaborativo.” Mesmo a função de configuração “pegar e arrastar” está disponível em robôs tradicionais, embora Lucier tenha dito que isso é melhor usado para casos em que você simplesmente deseja definir a peça em uma mesa ou em um bloco.
“É perfeito para algo como ensinar o robô a carregar uma CMM, porque a máquina só precisa saber aproximadamente onde a peça está para encontrar a borda e depois realizar as medições”, disse ele. “Mas se estou carregando em um mandril ou torno, tenho mais controle quando ensino com o pingente de programação.”
Há também uma variedade de acessórios para robôs industriais. Por exemplo, disse Lucier, garras de troca rápida e controle de força não são exclusivas dos cobots. “A Schunk tem uma linha de garras com sensor de força que utilizam servomotores, fugindo da pneumática, que é mais difícil de trocar. Você pode realmente ligar a parte elétrica.”
O pessoal do robô industrial também tem soluções que permitem reposicionar rapidamente o robô de máquina para máquina. No caso da FANUC, uma câmera no robô escaneia três decalques na “nova” máquina para se reorientar automaticamente.
Mas em meses de tentativas, Lucier disse que não consegue encontrar uma situação em que tal capacidade seja útil. “Movimentar um robô de máquina para máquina envolve mais do que simplesmente mover o robô. Pense em todas as coisas que você precisa mudar:talvez as ferramentas da extremidade do braço, a entrada, a saída…” A melhor solução é aquela em que cada máquina tem seu próprio robô ou um robô atende várias máquinas, talvez com efetores de extremidade dupla para que possa alternar entre os tipos de peças sem intervenção.
Também é o caso de integradores como Acieta e Methods podem adicionar robôs tradicionais a máquinas legadas, e os robôs custam quase o mesmo que os cobots. Portanto, considerando as ofertas atuais, a maior vantagem dos cobots é sua capacidade de funcionar perto de humanos sem o espaço e as despesas de cercas.
A desvantagem é que eles são mais lentos que os robôs industriais tradicionais e se limitam a peças mais leves. O maior modelo da UR lida com peças de até 10 kg (24 lb). Tempos de carga/descarga mais lentos não são significativos em peças com tempos de ciclo longos, mas podem diminuir a produção em trabalhos de médio a alto volume com tempos de ciclo mais curtos.
Kuzmin da Axis Machining não vê a necessidade de velocidade, “apenas consistência e confiabilidade – especialmente em peças com um longo tempo de ciclo. É melhor ter um cobot para carregar peças em uma velocidade confiável e depois usá-lo para rebarbar outras peças enquanto a máquina funciona. E se você não precisa de velocidade, por que arriscar?”
Lucier e Alexander alertam contra o exagero do benefício de poder trabalhar ao lado do robô. Por um lado, apontou Lucier, você já tem que proteger o operador da área de usinagem. Alexander acrescentou que, se um cobot estiver manuseando uma peça com bordas afiadas (como é comumente o caso na usinagem), “não é colaborativo ou seguro para um operador trabalhar em sua proximidade de qualquer maneira”.
Tanto Lucier quanto Alexander disseram que combinar “técnicas colaborativas” com robôs industriais oferece um compromisso útil. “Para os fabricantes que procuram um piso aberto com o mínimo de cercas, os robôs industriais têm a capacidade de trabalhar em um ambiente sem cercas usando scanners de segurança de área”, explicou Alexander. “E eles podem trabalhar neste ambiente sem cercas sem sacrificar a velocidade. Quando um operador entra na primeira zona de segurança, o robô desacelera. Quando o operador entra na segunda zona de segurança, o robô para completamente.”
Por outro lado, disse Lucier, uma vez que a zona de segurança para esta abordagem é 3-4′, o robô muitas vezes estaria desacelerando se empilhadeiras ou outros tráfegos passassem com frequência.
Como sugerido anteriormente, uma área perfeita para cobots é cuidar de um CMM. “As CMMs são intrinsecamente seguras para começar”, como disse Lucier. “Não há proteção, exceto em torno de componentes móveis. Eles não são rápidos. Você pode ficar bem ao lado deles. E geralmente você não está colocando a peça em um acessório, talvez apenas segurando-o contra um bloco em V ou algo semelhante. Foi aí que vi um robô colaborativo brilhar.”
Ambos os especialistas concordam, como resumiu Alexander, que “os robôs industriais são muito mais aplicáveis do que os cobots na maioria das aplicações de job shop e manufatura”.
Considerações de software
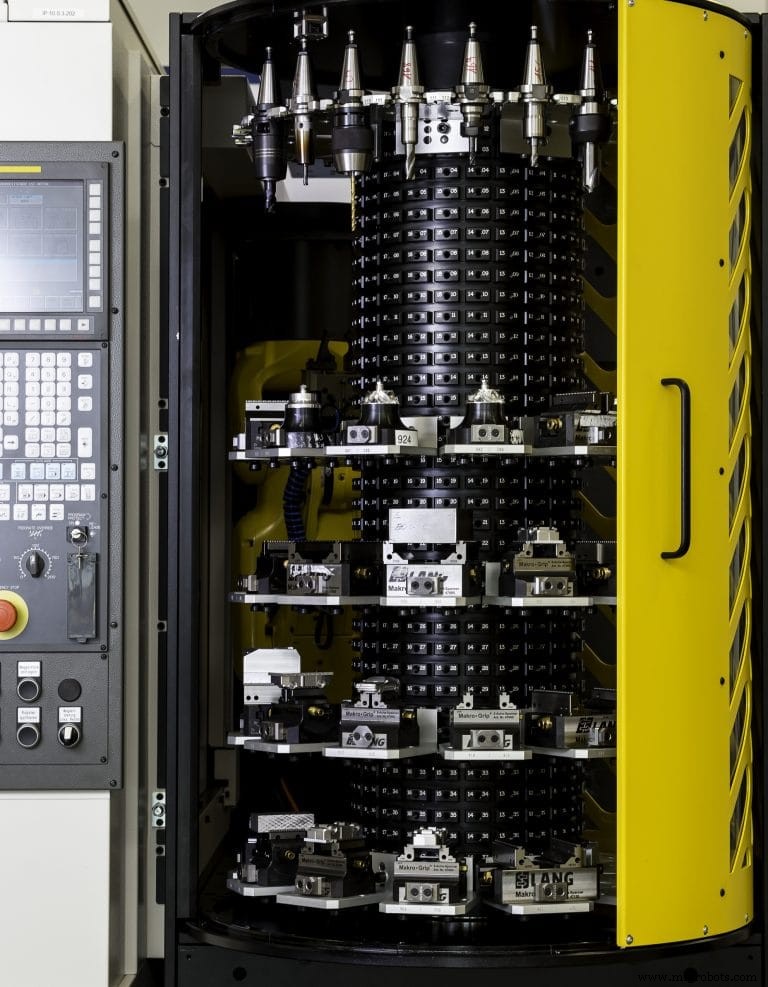
De acordo com Greg Mercurio, presidente da Shop Floor Automations, La Mesa, Califórnia, “software é o componente mais essencial na automação de oficinas”. Ele disse que o software de controle numérico direto (DNC) (também conhecido como software de controle numérico distribuído ou software de “alimentação por gotejamento”) “permite uma comunicação simplificada da máquina, bem como controle de revisão para gerenciar qualidade/sucata e um meio de organizar milhares de programas .”
A principal função do software DNC é enviar programas de usinagem diretamente para a máquina, permitindo que uma máquina com um controle de grau relativamente baixo manipule uma superfície complexa.
Mercurio e todos os especialistas concordam que algum grau de monitoramento da máquina é útil “para aumentar o tempo de atividade e a capacidade da máquina”. Mercurio acrescentou que o software Production Data Management permite que as empresas fiquem sem papel e que “o gerenciamento do berço de ferramentas também é uma necessidade. A melhor parte é que todas essas soluções podem se integrar com CAD/CAM, ERP, MES, CMMS e muito mais.”
Por outro lado, ele apontou que lojas menores podem se beneficiar muito com uma simples adição de hardware antes de gastar milhares em software. Por exemplo, adicionar uma interface RS232 para USB a equipamentos mais antigos facilita os programas de alimentação por gotejamento.
“O hardware é fácil de usar, configurar e manter, por isso é a opção de automação menos demorada
para uma oficina menor. Máquinas RS232 mais antigas podem usar uma unidade USB como máquinas CNC mais novas que possuem essa função integrada de fábrica. É também uma maneira mais acessível de modernizar seu chão de fábrica sem substituir completamente o equipamento. Também permite upgrades de memória acessíveis”, acrescentou Mercurio.
Voltando aos robôs, Alexander disse que existem vários pacotes de software oferecidos por OEMs de robôs e terceiros que permitem a programação de robôs off-line em um PC enquanto o robô continua trabalhando. “Esses pacotes de software permitem que você carregue um arquivo CAD e, em seguida, dê a liberdade de ‘desenhar’ o caminho do seu robô usando uma caneta ou um mouse”, explicou Alexander. “O software converterá seu caminho desenhado em código de robô que pode ser carregado diretamente no robô.”
É apropriado que o proprietário da oficina Kuzmin tenha a última palavra:“Eu queria melhorar a produtividade. Eu fiz isso adicionando robots. E estou muito satisfeito com o que conseguimos. Ao fazer isso, eu disse que deveríamos disponibilizar isso para todos, porque é isso que tornará a fabricação em nosso país muito mais competitiva”.
Sistema de controle de automação
- Aposte na nuvem ideal para você
- Quantos detalhes para planos de trabalho?
- Você não tem tempo para negligenciar a segurança do trabalhador
- Torre de trabalho final reduz o tempo de ciclo
- Se Você Quer Melhorar Algo, Meça
- Automatizar pequenas tarefas de programação NC compensa muito com o tempo
- 5 sinais de que você precisa de reparos de guindaste
- Como saber se você precisa de novas peças de guindaste
- Você precisa de um novo hardware de freio industrial?
- Motivos pelos quais você precisa de usinagem personalizada