Tecnologias para Melhoria do Processo de Coqueamento em Fornos de Coque de Subprodutos
Tecnologias para Melhoria no Processo de Coqueamento em Fornos de Coque de Subproduto
Os carvões de coque são convertidos em coque em baterias de fornos de coque subprodutos. O processo de coqueificação consiste em aquecer a mistura de carvões de coque triturados na ausência de ar para expulsar os compostos voláteis. O coque resultante é um material de carbono duro, mas poroso, que é usado para a redução de materiais de suporte de ferro em um alto-forno. O forno de coqueria também recupera produtos químicos voláteis na forma de gás de coqueria, sulfato de amônio, alcatrões e óleos. Nas últimas três a quatro décadas, várias tecnologias foram desenvolvidas que resultaram não apenas em (i) uso de carvões inferiores na mistura de carvão, (ii) grandes melhorias no processo de coqueamento, (iii) melhoria da qualidade da produção metalúrgica coque, (iv) melhores rendimentos, (v) recuperação de energia residual e (vi) melhor controle de emissões na bateria. Algumas das principais tecnologias a este respeito são dadas abaixo.
Esmagamento seletivo de carvões
O carvão é um material heterogêneo. Seus diversos componentes possuem uma dureza diferenciada, de modo que durante a quebra por meios mecânicos seja a quebra inevitável na mineração ou a britagem durante a preparação do carvão para coqueificação, os componentes mais fracos tendem a se concentrar nas frações finas e os demais nas frações grossas. Espera-se que essas várias frações tenham diferentes propriedades de coqueificação. Isso desencadeia o conceito de britagem seletiva que visa controlar o grau de britagem dos diferentes constituintes da mistura de carvão. Essa tecnologia é útil quando os carvões são petrograficamente heterogêneos.
Esta tecnologia é uma tecnologia teoricamente sólida e visa controlar o grau de esmagamento dos diferentes constituintes do carvão. Tem como objetivo melhorar a homogeneidade dos componentes reativos e inertes no carvão. Os componentes reativos dos carvões são principalmente vitrinitas e são os constituintes mais macios, enquanto as matérias minerais dos carvões são os componentes mais duros. Em unidades convencionais de britagem de carvão, onde todo o carvão é triturado em conjunto, as vitrinitas são trituradas em um tamanho relativamente mais fino em comparação com os constituintes da matéria mineral. Para a produção de coque de maior qualidade, é desejável triturar a matéria mineral mais fina que o componente de vitrinita do carvão para que durante o processo de coqueificação, quando a carga do carvão amolece, a matéria mineral seja melhor assimilada, levando a uma maior resistência. Isso normalmente é realizado por britagem de cada tipo de carvão separadamente.
A britagem seletiva de carvão é composta pelo silo, estação de britagem, estação de mistura, misturador de carvão e direciona o carvão até a torre de carvão nas baterias do forno de coque. O carvão é transportado por correias transportadoras do pátio de armazenamento de carvão para o silo, que amortece o alto fluxo de massa do pátio de carvão contra o fluxo de massa reduzido para a estação de britagem. Na estação de britagem, os carvões são britados tipo por tipo com configurações individuais do britador. Após o processo de britagem, o carvão britado é transportado para a estação de mistura. Cada tipo de carvão é armazenado em um recipiente de mistura separado. Adaptados ao número de tipos de carvão e sua porcentagem em relação à composição da mistura de carvão, são projetadas diferentes quantidades e tamanhos de silos.
A jusante dos silos de mistura, os diferentes tipos de carvão são alimentados ao transportador de saída por alimentadores de pesagem de esteira. Da estação de mistura, o carvão é transportado para o misturador. Aditivos, como óleo, água e pó de coque, etc., são adicionados ao carvão na calha de transferência a montante antes do misturador. No misturador, a mistura de carvão é homogeneizada. Após o processo de mistura, o carvão é alimentado na torre de carvão. A medição da umidade do carvão ocorre a montante no final da esteira transportadora para a torre de carvão. O conceito básico para britagem seletiva do carvão é mostrado na Figura 1.
Fig 1 Conceito básico de britagem seletiva
No conceito de britagem seletiva de carvão, o ajuste do britador de carvão é alterado automaticamente seguindo pré-ajustes para cada tipo de carvão. Isso oferece a possibilidade de atingir o tamanho de grão ideal de cada tipo de carvão em consideração à composição da mistura de carvão e de reagir às mudanças nas propriedades do carvão a qualquer momento. Por exemplo, os tipos de carvão com fraca capacidade de coqueificação são triturados para um tamanho de grão médio maior para garantir uma superfície específica mais baixa. Carvões de coque macios com uma grande quantidade de inertes podem ser moídos até um tamanho de grão médio menor em relação à composição de mistura de carvão. A mistura de carvão é mais homogeneizada do que no caso de britagem de mistura. Os teores de inertes e reativos dos carvões são distribuídos uniformemente na mistura de carvão e não concentrados em certas frações de grãos. Isso resulta em pontos menos frágeis no coque e evita diferenças em termos de retração por inertes distribuídos de forma não homogênea.
Pré-triagem antes dos britadores
Uma etapa adicional do processo recomendável é a pré-peneiração do carvão antes de ser encaminhado para a estação de britagem de carvão. A maioria dos tipos de carvão bruto tem 30% a 50% de um tamanho de grão menor que 3 mm, que não precisa ser moído mais. A remoção deste tamanho de grão do carvão antes do britador tem o efeito positivo e ajuda a reduzir consideravelmente a capacidade dos britadores. Além disso, a porção de partículas finas pode ser controlada de forma mais eficaz.
A separação do carvão fino pode ser efetuada por classificadores pneumáticos ou por peneiras flip-flop. O investimento adicional neste equipamento é parcialmente compensado pela redução da capacidade dos trituradores de carvão.
Pela redução de partículas finas, o tamanho médio de grão da mistura de carvão é reduzido efetivamente, aumentando a densidade aparente com efeito positivo na produtividade do forno de coque. Além disso, as propriedades de coqueificação da mistura de carvão são melhoradas pela redução da superfície específica. Isso permite o uso de uma porcentagem maior de carvões de coque de baixa qualidade na mistura.
Adição de óleo
É possível ajustar a densidade aparente do carvão pela adição de óleo em quantidades relativamente pequenas de 0,1% a 0,5%. Isso mostra efeitos positivos nas propriedades do coque. Nos casos de adição de óleo para compensar a redução da densidade aparente devido ao aumento da porcentagem de partículas menores que 0,5mm, verificou-se que a pressão do gás do carvão não aumenta simultaneamente. Em casos de distribuição de tamanho de partícula constante, a pressão do gás do carvão diminui ainda que levemente devido à adição de óleo. Além disso, uma melhor característica de fluxo dentro da câmara durante o carregamento foi confirmada em muitos testes por operadores de baterias de fornos de coque. Assim, uma distribuição de carvão mais uniforme dentro da câmara com uma linha de carvão constante pode ser alcançada e há uma redução do arraste. Isso leva a menos carvão derramado e carbonização uniforme do carvão em toda a câmara do forno de coque. Além disso, o consumo de calor também é otimizado e o superaquecimento do espaço de coleta de gás acima do carvão pode ser evitado. Isso reduz a formação de carbono das reações de craqueamento que ocorrem em temperaturas acima de 850 graus C.
Controle de umidade do carvão
O controle da umidade do carvão é realizado pela secagem do carvão a um nível de umidade constante. Agora é uma característica comum. O nível de umidade constante proporciona um funcionamento estável das baterias do forno de coque. A secagem é feita por meio de secadores de tubos rotativos ou secadores de leito fluidizado que ficam dispostos atrás da estação de mistura. O controle de umidade do carvão usa o calor residual do gás do forno de coque para secar o carvão usado na fabricação de coque.
O teor de umidade da mistura de carvão para carregamento em fornos de coque normalmente varia na faixa de 8% a 10%. A secagem da mistura de carvão reduz o teor de umidade na mistura de carvão para um nível de cerca de 6%. Isso, por sua vez, reduz o consumo de combustível nos fornos de coque. O coque é seco usando o conteúdo de calor do gás de coqueria, vapor de baixa pressão ou qualquer outra fonte de calor residual. O fluxograma esquemático do controle de umidade do carvão é dado na Fig 2.
Fig 2 Esquema de controle de umidade do carvão
Os benefícios do controle de umidade do carvão são (i) economia de combustível em cerca de 71.700 kcal/ton, (ii) melhoria na qualidade do coque em 1,7%, (iii) aumento na produção de coque em cerca de 10%, (iv) redução no período de coqueamento, e (v) diminuição da poluição da água.
Outra alternativa favorável, mas ainda não realizada, é a combinação de classificadores pneumáticos para remoção dos finos de carvão e secagem do carvão pela corrente de ar em frente à estação de britagem. Tal sistema combina as vantagens de pré-peneiramento e pré-secagem em uma estação de processo. Os equipamentos básicos necessários para tal processo estão disponíveis no mercado, mas sua aplicação combinada ainda não foi praticamente adotada em estações de tratamento de carvão.
Cobrança de selos de carvão
O uso generalizado de injeções de carvão pulverizado em alto-forno tem como exigência a maior qualidade do coque. Além disso, como os carvões de coque se tornaram mais caros, com preços voláteis e disponibilidade relativa, a introdução de carvões mais baratos na mistura de carvão tornou-se uma necessidade. Isso levou ao uso de carga de selo de carvão, que foi originalmente desenvolvido para o uso de carvões altamente voláteis e pouco coqueificáveis.
A técnica de preparação de carga consiste em preparar um bolo com a mistura de carvão em uma caixa metálica e depois carregá-lo na coqueria. A maior densidade de carga implica em melhor qualidade de coque quando comparada com a carga convencional. Assim, dependendo da situação, pode-se obter uma melhor qualidade de coque ou incluir carvões de coque fracamente na mistura.
A estampagem de carvões aumenta a densidade aparente da carga em 30% a 35% para cerca de 1.150 kg/cum. A trituração de carvões em mais de 90% abaixo do tamanho -3 mm e 40% a 50% abaixo do tamanho -0,5 mm é necessária para uma torta estável. Com carga de selo, carvões de baixa classificação, coqueamento fraco e alta volatilidade podem ser usados na extensão de cerca de 20%, mas como a carga de carvão é compactada para alta densidade aparente, pode haver problemas de pressões de parede aumentadas. A fim de garantir que as paredes do forno refratário não sejam danificadas, a mistura de carvão usada deve ser cuidadosamente escolhida pelo equilíbrio ideal entre carvões de alto e baixo voláteis.
O processo de cobrança de selos era usado desde o início do século 20. Essa tecnologia nasceu na Silésia e na Polônia há mais de 100 anos. Nas fábricas anteriores, a estação de estampagem estava localizada no espaço entre as duas baterias. A palha foi usada como auxiliar na resistência do bolo. A palha foi usada como aglutinante e um carregador de carro / aríete especialmente projetado, construído para carregar a carga no forno pela parte de trás. O coque produzido pelo processo de carregamento de selos era de uma variedade mais densa e maior do que o produzido por outros métodos, tornando-o mais adequado para a fabricação de ferro em fundições onde a resistência é um fator importante. Outra vantagem observada foi que uma gama muito maior de carvões poderia ser usada com os limites de (alta) volatilidade e propriedades de coqueamento muito aumentadas.
O desenvolvimento de processos modernos ocorreu na coqueria de Fuerstenhausen, Volklingen, Alemanha, com foco no uso de carvão de alta volatilidade. Em 1978, após intensa pesquisa e desenvolvimento, foi produzida a primeira torta de 6 metros de altura, superando um gargalo para a implantação econômica desta tecnologia. A primeira fábrica desta dimensão foi inaugurada em 1984 na Alemanha. Tanto os fornos convencionais como os fornos sem recuperação/recuperação de calor fazem uso desta tecnologia.
A tecnologia envolve basicamente a formação de uma torta de carvão estável com o carvão finamente triturado por estampagem mecânica fora do forno para carbonização. No carregamento de selos, a densidade aparente do carvão carregado no forno é aumentada pela estampagem física da carga em um bolo. O bolo, que é quase semelhante em tamanho ao forno, é então inserido no forno. A estampagem é realizada em uma máquina de estampagem cum carregamento cum empurradora que usa martelos de queda para estampagem.
O equipamento de estampagem pode estar localizado num edifício construído para este fim ou na máquina de carregamento/empurrão. O processo de estampagem normalmente consiste em introduzir a mistura de carvão previamente moída em um tamanho específico, dentro de uma caixa de aço, em camadas sucessivas que são compactadas mecanicamente. Pode ser aplicado verticalmente ou horizontalmente. Além disso, a vibração pode ser aplicada para facilitar a acomodação das partículas. Uma caixa horizontal é preenchida com a mistura de carvão, com distribuição granulométrica definida e teor de umidade, em três camadas iguais. A compactação e vibração são aplicadas, através de uma série de placas de martelo que cobrem toda a superfície da torta, por dois minutos para cada camada, para suportar a transferência da caixa para o forno. Diz-se que, neste caso, o tamanho de grão fino não é necessário como na estampagem convencional.
Dois aspectos devem ser levados em consideração. Estas são (i) densificação e (ii) propriedades mecânicas. A densificação é necessária para o processo de coqueificação. Quanto mais densa a torta, melhor é a qualidade do coque, levando em consideração tanto a resistência mecânica a frio quanto o comportamento em alta temperatura. As propriedades mecânicas devem ser suficientes para suportar o transporte da torta para sua carga no forno de coque.
Quando a densificação começa, as partículas de carvão cedem sob o estresse aplicado pela máquina de estampagem, preenchendo os vazios intersticiais com partículas menores. O rearranjo das partículas é suportado pela umidade da superfície, o que reduz o atrito interno. Com mais tensão, ocorre uma deformação elástica-plástica das partículas, resultando em parte na quebra das partículas e no preenchimento de pequenos poros com os fragmentos. Enquanto o volume dos poros diminui, a saturação dos poros com a água aumenta causando um efeito de amortecimento.
Além da influência da água capilar no próprio processo de densificação, as propriedades mecânicas da massa compactada também são determinadas pela água superficial, que atua como agente ligante na formação de forças adesivas. Dentro da sistemática de engenharia de processo, a torta de estampagem pode ser chamada de aglomerado úmido que é caracterizado pelas forças adesivas resultantes de pontes líquidas dentro do sistema de poros capilares.
A densidade do bolo é de 1.100 kg/cum 1.150 kg/cum e depende da umidade e do tamanho do grão da mistura de carvão e da energia de compactação aplicada. As propriedades mecânicas dos carvões também têm influência. A densidade úmida aumenta continuamente quando a umidade aumenta de 6% para 13%. Para maior umidade, a energia aplicada é usada para expelir a água da torta. Normalmente, duas variáveis importantes da mistura de carvão são a umidade e o tamanho do grão para a obtenção da resistência necessária para o transporte e carregamento da torta. A variável de operação é a energia de compactação aplicada e as propriedades mecânicas relevantes são a resistência à compressão e a resistência ao cisalhamento.
Para o carregamento do bolo no forno de coque, são utilizadas diferentes técnicas dependendo do design do forno de coque (forno vertical ou forno de coque horizontal sem recuperação / recuperação de calor. Para fornos de coque verticais, o carregamento do bolo ocorre através do empurrador Este procedimento causa altas emissões, para diminuir essas emissões, vários sistemas foram experimentados durante o carregamento de torta de carvão, principalmente através do uso de molduras de vedação, porém o sistema de controle de emissões reduz apenas parcialmente a emissão sem eliminá-la completamente. A solução adotada recentemente nas novas baterias para diminuir as emissões durante o processo de carregamento do forno é criar uma forte depressão (menos 400 Pa) no coletor principal durante a fase de carregamento. é ajustado para uma pressão nominal negativa A mudança para o ponto de ajuste de depressão mais alto é feita antes de iniciar o processo de empurrar o bolo.
Normalmente, a especificação das misturas de carvão inclui 25% a 32% de matéria volátil (base seca isenta de cinzas) e um índice de dilatação livre de 3 no mínimo. No entanto, as especificações da mistura de carvão mudam de usina para usina, dependendo da disponibilidade e dos custos do carvão. Em algumas usinas, a mistura de carvão inclui coque de petróleo e finos de coque.
As vantagens do carregamento de selos são (i) aumento do rendimento de 8% a 10% devido à maior densidade aparente e (ii) maior resistência do coque (valor micum e CSR) devido ao empacotamento mais próximo das partículas de carvão individuais durante a carbonização. o coque produzido é mais denso, menor e mais uniforme em tamanho.
Fornos de coque carregados no topo de câmara grande
Os fornos de coque de câmara grande têm 7,6 m de altura. O complexo de baterias de fornos de coque de grande câmara representa o estado da arte e tecnologia consolidada para coquerias. A Tabela 1 mostra uma tabela de comparação entre baterias de forno de coque carregadas no topo de câmara grande com baterias de forno de coque de 6,25 m de altura com base em uma produção de coque de 1,9 milhão de toneladas de produção anual.
Guia 1 Comparação de forno de coque de câmara grande com forno de coque de 6,25 m | |||
Assunto | Unidade | Forno de coque de câmara grande | Forno de coque de 6,25 m de altura |
Produção anual | toneladas | 1.900.000 | 1.900.000 |
Altura do forno | m | 7,6 | 6,25 |
Largura do forno | mm | 550 | 410 |
Volume do forno | Goza | Cerca de 79 | Cerca de 40 |
Número de baterias | Nºs | 2 | 4 |
Número de fornos | Nºs | 118 | 160 |
Empurrando por dia | Nºs | 116 | 226 |
Portas de fornos de coque | Nºs | 236 | 320 |
Tampas de carregamento | Nºs | 472 | 640 |
Tampas de tubo de suporte | Nºs | 118 | 160 |
Conjunto de máquinas operacionais | Nºs | 31 | 2 |
Comparação da duração da bateria | |||
Tempo de cozimento | horas | 24,5 | 17 |
Empurrões por dia por forno | Nºs | 0,98 | 1,41 |
Empurrões por forno por ano | Nºs | 358 | 515 |
Vida útil esperada por bateria (16.000 impulsos por forno) | Anos | 44,6 | 31 |
O número reduzido de empurrões por dia das baterias de coqueria de grande câmara permite ter apenas 1 conjunto de máquina operacional em operação em vez de 2 conjuntos para as baterias de coqueria de 6,25 m de altura, com vantagens em termos de (i) custo de investimento do forno de coque máquinas e (ii) custo operacional. A Tab 1 também mostra que, considerando um número médio de empurrões que cada forno pode realizar durante sua vida útil, o resultado é que a vida útil esperada aumenta consideravelmente.
Cada parede de aquecimento é composta por 38 chaminés de aquecimento tendo a configuração composta por (i) chaminé dupla, com recirculação parcial dos gases residuais para baixa produção de NOx, (ii) três níveis de entrada de ar escalonada para minimizar a formação de NOx e manter uma distribuição vertical adequada da temperatura, e (iii) vazão mista de gás e ar facilmente ajustável por meio de placa de regulagem colocada na parte inferior do nível do regenerador.
Sistema de aspiração de licor de amônia de alta pressão
O sistema de aspiração de licor de amônia de alta pressão é eficaz para controlar as emissões de carga em baterias de fornos de coque. Nesse sistema, o licor amoniacal, que é um subproduto, é pressurizado em torno de 35 kg/cm2 a 40 kg/cm2 e injetado através de bicos especiais instalados no pescoço de ganso no momento do carregamento. Isso cria uma sucção suficiente dentro do forno, evitando assim que os poluentes sejam liberados para a atmosfera. O sistema consiste em bombas de reforço multiestágio de alta pressão, tubulação robusta, bicos de pulverização especialmente projetados, válvulas adequadas e instrumentos de controle. Este sistema de controle de emissões resulta em economia na quantidade de vapor de processo e aumento no rendimento de gás bruto.
Extinção a seco de coque
A têmpera seca de coque é uma alternativa à têmpera úmida tradicional. É um processo de economia de energia utilizado durante a produção de coque na bateria do forno de coque. Uma planta de têmpera a seco de coque também é chamada de planta de resfriamento a seco de coque. No processo tradicional de têmpera úmida de coque, o coque incandescente que é empurrado do forno de coque é resfriado por pulverização de água no coque quente. A água utilizada para o resfriamento é vaporizada e liberada na atmosfera. Um problema com este sistema convencional é a perda de energia quando a energia térmica do coque incandescente é convertida em vapor que é vaporizado e liberado sem uso. Outra desvantagem é que o processo de têmpera úmida de coque também produz poeira de coque no ar e, portanto, o processo está associado a altas emissões de dióxido de carbono e perda de energia térmica.
Durante o processo de têmpera úmida do coque para resfriamento do coque de forno, o calor sensível do coque quente é dissipado na atmosfera e é perdido. Além disso, há emissões aéreas (0,5 tonelada de vapor por tonelada de coque, que é carregado com fenol, cianeto, sulfeto e poeira) e uma grande quantidade de água (cerca de 0,6 cum por tonelada de coque) é necessária para a têmpera úmida . Os contaminantes da água também são lançados no meio ambiente.
Em uma planta de têmpera a seco de coque, o coque incandescente é resfriado em câmaras de resfriamento de aço revestidas com refratários especialmente projetadas por meio de gás inerte circulante em um circuito fechado que consiste em uma câmara de resfriamento, uma câmara de coleta de poeira, uma caldeira de calor residual, ciclones de poeira, um ventilador de moinho, um dispositivo de sopro e dutos de circulação. A energia térmica do coque incandescente é recuperada na caldeira de calor residual para uso como vapor, resultando em economia de energia e redução nas emissões de partículas de coque. A Tabela 2 mostra a comparação das propriedades típicas do coque produzido pelos dois processos.
Tab 2 Comparação das propriedades típicas do coque produzido | ||||
Sl. No. | Parâmetros | Unidades | Processo de têmpera úmida de coque | Processo de têmpera a seco de coque |
1 | Conteúdo de água | % | 2-5 | 0,1-0,3 |
2 | Conteúdo de cinzas | % | 11,35 | 11,39 |
3 | Componentes voláteis | % | 0,5 | 0,41 |
4 | Tamanho médio de partícula | mm | 65 | 55 |
5 | Taxa de brisa de coque (após corte em -15 mm) | % | 10 | 13 |
6 | Porosidade | % | 49 | 48 |
7 | Índice de bateria | % | 83,5 | 85 |
8 | Força do coque após reação (CSR) | % | 58 | 60 |
O coque quente depois de empurrado é trazido da bateria do forno de coque para a planta de têmpera a seco de coque no balde de abertura inferior mantido no carro de têmpera. Este balde é levantado na planta de têmpera a seco de coque por um dispositivo de elevação/carregamento até o topo da câmara de têmpera a seco de coque e o coque incandescente é descarregado na pré-câmara pelo dispositivo de carga. O coque quente (temperatura em torno de 1.000 graus C a 1.100 graus C) é resfriado na câmara pelo gás circulante. Na câmara o gás circulante se move em contracorrente ao movimento do coque, ou seja, o gás circulante se move para cima enquanto o coque se move para baixo pela gravidade.
O gás circulante em uma planta de têmpera a seco de coque de funcionamento contínuo é um gás misto que consiste principalmente de nitrogênio juntamente com pequenas quantidades de dióxido de carbono, monóxido de carbono e hidrogênio. O coque quente, enquanto desce na câmara, é resfriado a uma temperatura inferior a 200°C pelo gás circulante soprado da zona inferior da câmara de resfriamento e é descarregado da instalação de descarga na parte inferior da câmara. O tempo de passagem do coque pela câmara é em torno de 5 horas a 6 horas.
O gás de circulação de alta temperatura (em torno de 800 ° C a 850 ° C) após um processo de troca de calor na câmara de resfriamento passa pelo coletor de poeira primário e é fornecido à caldeira. O gás de circulação após um processo de troca de calor na caldeira é resfriado a cerca de 180 graus C. O vapor gerado na caldeira é usado como vapor de processo de uso geral ou convertido em vapor de alta pressão superaquecido para a geração de energia elétrica energia através de um gerador de turbina.
O gás circulante passa pelo coletor de pó secundário para o soprador de circulação de gás, pelo qual sua pressão é aumentada, e sua composição é corrigida pela adição de gás nitrogênio e, em seguida, o gás circulante é injetado no fundo da câmara de têmpera seca de coque. Se necessário, um sub-economizador é instalado para diminuir a temperatura do gás de circulação para cerca de 130 graus C, melhorando a eficiência de resfriamento da câmara de resfriamento.
Existem algumas facilidades auxiliares que incluem dispositivo de corte para cortar o coque da câmara, sistema de despoeiramento para remover o pó do gás inerte circulante e o coletor de pó secundário instalado antes do soprador de circulação. O fluxograma do processo de têmpera a seco de coque é mostrado na Fig 3.
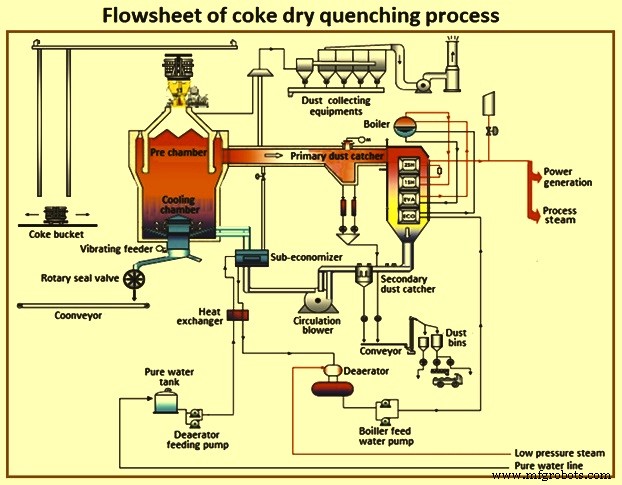
Fig 3 Fluxograma do processo de têmpera a seco
No processo de têmpera a seco de coque, o coque incandescente é resfriado pelo gás que circula em um sistema fechado, evitando assim a liberação de poeira de coque no ar. A energia térmica do coque incandescente, que é perdida no processo de têmpera úmida de coque convencional, é coletada e reutilizada como vapor no processo de têmpera a seco de coque. Essa tecnologia utiliza menos combustível fóssil e resulta em menores emissões de dióxido de carbono, contribuindo assim para a prevenção do aquecimento global. Atualmente, as plantas de têmpera a seco de coque têm atraído muita atenção do mundo devido à sua eficiente recuperação de energia e à característica de reduzir a poluição do meio ambiente. Eles estão sendo considerados como uma facilidade essencial para a contramedida contra problemas ambientais como o aquecimento global por dióxido de carbono e poluição do ar. Em um estudo, no qual o cálculo da economia de energia foi realizado com base na operação de um processo de têmpera a seco de coque existente, foi demonstrado que 85% do calor residual gerado durante a carbonização do carvão está sendo recuperado pelo processo de têmpera a seco de coque .
A têmpera a seco também melhora a resistência do coque. Outras vantagens da têmpera a seco de coque são a redução das emissões de gases de efeito estufa (GEE) e a melhoria da eficiência hídrica.
Portas modernas à prova de vazamentos
As portas vazando de uma bateria de forno de coque são sempre uma importante fonte de poluição. O design das portas dos fornos passou por um processo de evolução, desde as portas cimentadas até a atual geração de portas auto-reguláveis sem vazamento. As características importadas das portas à prova de vazamentos são (i) um diafragma fino de aço inoxidável com uma lâmina de faca como uma moldura de vedação construída entre o corpo da porta e o retentor de tijolos, (ii) regulagem de mola na borda da faca para auto vedação, (iii) provisão para resfriamento de ar do corpo da porta e (iv) canais de gás de grande porte para facilitar a circulação do gás dentro do forno.
A vantagem das portas à prova de vazamentos é a minimização de vazamentos na porta, operação livre de regulamentações, vida útil mais longa devido a menos empenamento do corpo da porta refrigerada a ar e manutenção reduzida.
Sistema de controle de emissões de impulso baseado em terra
As emissões geradas durante a expulsão do coque incandescente contêm uma grande quantidade de pó de coque (cerca de 11 % do total de poluentes nos fornos de coque. Os sistemas de controle de expulsão baseados em terra atenuam essa poluição. É composto por (i) uma grande coifa de sucção fixada no carro guia de coque e movendo-se com a guia de coque, direcionando os fumos para o duto coletor de pó do lado do coque (ii) duto coletor de pó e (iii) e a limpeza do equipamento dos fumos. A grande quantidade de fumos paroxísticos de alta temperatura são coletados sob o ventilador de bóia quente na grande coifa de aspiração de gás instalada no carro guia de coque, e entra no duto de coleta de poeira através dos outros equipamentos. O ar é dissipado na atmosfera após a purificação pelo coletor do duto de pulso e após ser resfriado pelo resfriamento do acumulador. O sistema é controlado por controladores lógicos programáveis (CLP).
Sistema de automação e controle de processos
A automação da coqueria está estruturada nos níveis clássicos, do Nível 0 (Nível de campo) até o Nível 3 (Nível de gestão). O projeto de automação de uma coqueria normalmente é dividido em seis camadas de equipamentos básicos. A Fig. 4 mostra a hierarquia do sistema de automação da coqueria.
Fig 4 Hierarquia da automação da coqueria
O equipamento elétrico, os elementos de controle e a instrumentação são normalmente conectados a unidades de E/S remotas redundantes (entrada/saída) feitas por interfaces padrão 4-20 mA e 24 CC. Os subsistemas inteligentes são normalmente acoplados ao Profibus ou Modbus. Todos os equipamentos de automação são conectados por meio de uma rede de fibra ótica da planta que percorre todos os locais da planta em que o equipamento relevante é colocado. Todos os dados são coletados e distribuídos por meio dessa rede, onde a fonte de dados e o destino de dados podem ser conectados de forma flexível entre si usando conexões físicas por painéis de conexão e switches, bem como conexões lógicas usando um sistema de gerenciamento de rede. Através desta rede, todos os sistemas são capazes de se comunicar entre si.
Na área da coqueria, um “sistema de controle distribuído” integrado (DCS) é usado no nível de controle do processo. Muitas aplicações na coqueria são funções de controle de sequência, que são melhor executadas por PLCs.
A automação e o controle do processo para o aquecimento e as máquinas da bateria do forno de coque são obtidos usando um sistema de controle de nível 2 que realiza vários cálculos de modelo de processo com base nos dados processados coletados de um sistema de automação de nível 1. O sistema de controle de nível 2 fornece aos operadores de fornos de coque uma ferramenta de suporte avançada, precisa e fácil de usar, que pode ser usada com sucesso para melhorar o desempenho operacional e ambiental da planta.
Os benefícios do sistema de automação e controle de processos incluem menor consumo de energia por meio da redução do consumo de gás combustível, estabilização da condição e operação da bateria do forno de coque, qualidade consistente do coque, redução de emissões, aumento da vida útil da bateria e facilidade na geração de relatórios e análise de dados operacionais e dados de manutenção.
Processo de manufatura
- Processo Finex para Produção de Ferro Líquido
- Processo HIsarna para fabricação de ferro
- Bateria de forno de coque sem recuperação
- Tecnologias para Melhoria no Processo de Sinterização
- Processo CONARC para Siderurgia
- Processo de Laminação para Aço
- Fabricação de coque em baterias de forno de coque subproduto
- Processo de Produção para Refratários Moldados
- Processo CLU para Produção de Aço Inoxidável
- Recuperação de amônia durante a produção de coque de carvão de coque