Injeção de gás de forno de coque em um alto-forno
Injeção de gás de forno de coque em um alto-forno
A indústria siderúrgica é uma das principais consumidoras de energia e, portanto, responsável por altas emissões de dióxido de carbono (CO2). Apesar da notável diminuição nas emissões específicas de CO2 pela maioria das siderúrgicas, a quantidade total de emissões de CO2 está crescendo em todo o mundo devido ao contínuo aumento da produção de aço, que atingiu um nível de 1606 milhões de toneladas em 2013. Atualmente a indústria do aço é enfrentando uma demanda crescente para minimizar o consumo de energia e as emissões de gases, especialmente dos processos de fabricação de ferro. O uso eficiente de gases de subprodutos é essencialmente importante para a rentabilidade da operação da siderurgia devido aos altos volumes de energia e aos custos envolvidos. A injeção de gás de coqueria (COG) no alto-forno moderno é uma das medidas eficazes para a indústria siderúrgica alcançar a produção de ferro de baixo carbono, economia de energia e redução de emissões.
O coque é um insumo essencial para o processo de fabricação do ferro e é produzido pelo aquecimento do carvão em fornos de coque. Para fazer coque, o carvão é aquecido na ausência de oxigênio para expulsar a matéria volátil dele. O COG é produzido como subproduto do processo no caso de subprodutos das baterias de fornos de coque normalmente instaladas em siderúrgicas. A quantidade específica de COG gerada durante a fabricação de coque nos fornos de coque de subprodutos está na faixa de 290 a 340 N cum/t de carga de carvão, dependendo das matérias voláteis na carga de carvão.
O COG é usado atualmente após sua limpeza de alcatrão, naftaleno, benzeno bruto, amônia e enxofre para aquecimento de fornos de alto-forno, fornos de ignição em planta de sinterização, forno de aquecimento em laminadores e geração de energia elétrica em usina.
O COG tem uma composição que consiste em cerca de 55%-58% H2, 25%-27% CH4, 6%-7% CO e uma pequena porcentagem de CO2, N2, hidrocarbonetos e outros elementos. Como a composição do COG é rica em hidrogênio, tem atraído muita atenção nos últimos anos para sua utilização nos processos de redução.
O COG também pode ser um redutor em alto-forno. A injeção de COG é um processo que envolve a injeção de grandes volumes de gás de coqueria na pista de um alto-forno (BF). Isso fornece não apenas uma fonte suplementar de carbono, mas também acelera a produção de ferro líquido, além de reduzir a necessidade de coque metalúrgico para reações no alto-forno. A tecnologia de injeção de COG também reduz as emissões absolutas de CO2, bem como as emissões de SO2 do alto-forno.
Ensaios com injeção de gás no alto-forno foram feitos nos EUA em meados da década de 1990.
Em um esforço para economizar energia e reduzir custos, a USS (US Steels) desenvolveu um sistema em suas fábricas de Mon Valley localizadas nos arredores de Pittsburgh, Pensilvânia, que lhes permitiu usar COG em seus altos-fornos. Embora outras siderúrgicas da América do Norte tenham tentado isso, a USS é a primeira a usar com sucesso o COG em altos-fornos. Para conseguir isso, o USS limpa completamente o gás, aumenta sua pressão e usa ventaneiras de alto-forno modificadas. A implementação deste projeto custou cerca de US$ 6 milhões e resultou em uma economia anual de US$ 6,1 milhões, dando um retorno simples de pouco menos de um ano. Além da redução de custos, a injeção de COG no alto-forno também contribuiu para a diminuição do consumo de energia e das emissões de CO2.
A injeção de COG no alto-forno tem influência nas condições da pista e na redução do minério de ferro. A combustão de hidrocarbonetos COG na frente das ventaneiras pelo oxigênio da explosão resulta em um desenvolvimento de monóxido de carbono e gases de hidrogênio que aumentam o potencial de gás redutor por conta do N2. Os cálculos teóricos e os ensaios comerciais realizados sobre a substituição do gás natural por COG no BF mostraram menor consumo de coque e maior produção de gusa. A alta eficiência do COG se deve ao fato de conter 3,5 a 4 vezes menos hidrocarbonetos em comparação com o gás natural. Isso melhora a combustão na fornalha, ativa a coluna de coque e aumenta a utilização de gases no forno. Foi observado que maior volume e maior poder calorífico do gás de topo BF podem ser gerados através da injeção de COG no alto-forno. Também a temperatura média devido à injeção de COG aumenta com a distância da ponta da lança.
Ressalta-se que as condições da pista são muito complexas e também influenciam as condições da ventaneira e, portanto, a combustão dos gases redutores. Além disso, o aumento da temperatura é maior no caso de injeção de COG devido a uma combustão mais completa e devido ao alto poder calorífico do gás (cerca de 4.000 a 4.400 kcal por metro cúbico normal).
O COG injetado no nível da ventaneira é normalmente acompanhado pelo enriquecimento de oxigênio do jato de ar quente. O COG precisa ser comprimido para injeção e, portanto, requer uma unidade de compressor, o que significa um aumento no consumo de energia. A injeção de oxigênio no jato de ar reduz a vazão específica do gás causando uma redução na temperatura de topo e um aumento na temperatura de chama adiabática da pista (RAFT) nas ventaneiras. Esses efeitos são compensados pela injeção de COG. Assim, uma injeção combinada de oxigênio e COG no nível da ventaneira aumenta a produtividade do alto-forno. Cada 1% de enriquecimento de oxigênio do jato quente melhora a produtividade em 2-0% a 2,5%. Um diagrama esquemático típico de injeção de COG em alto-forno é dado na Fig. 1.
Fig 1 Diagrama esquemático da injeção de COG no alto-forno
A injeção de COG no alto-forno é praticada em alguns países com diferentes taxas de injeção variando de cerca de 30 a 280 N cum/tHM. Em alguns altos-fornos, o COG é injetado apenas ocasionalmente devido à sua disponibilidade gratuita na planta integrada ser limitada. A flexibilidade da utilização do COG pode ser aprimorada, pois o gás pode ser movido entre o alto-forno e algum outro usuário do gás disponível, dependendo da necessidade no momento. Assim, o gás injetado no alto-forno substitui os agentes redutores alternativos que devem ser adquiridos de fontes externas.
Além disso, foi relatado que o nível máximo de injeção de COG na ventaneira do alto-forno é considerado de 0,1 ton COG/tHM de acordo com as condições termoquímicas. A relação de substituição coque/COG alcançada normalmente é de 0,4-0,45 kg/N Cum (cerca de 0,98 ton de coque/ton de COG) em comparação com 0,8-0,85 kg/N cum para o gás natural (GN).
Um modelo matemático foi desenvolvido pela MEFOS, Suécia, para uma ventaneira de injeção em um alto-forno para simular a combustão, ao injetar gás redutor. A modelagem matemática da injeção de COG nas ventaneiras do alto-forno indicou que melhores condições de combustão e maior taxa de injeção são alcançadas com o uso de duas lanças de injeção em comparação com uma lança. A injeção de COG com lança única resultou em (i) visão muito heterogênea de temperatura e velocidade, (ii) o fluxo atinge o final da pista com alta velocidade, (iii) temperaturas mais altas no final da pista e ( iv) nenhum superaquecimento da ventaneira. A injeção de COG com duas lanças resultou em (i) diminuição significativa da profundidade de penetração, (ii) distribuições mais homogêneas de temperatura, velocidade e concentração de gás, (iii) combustão mais uniforme semelhante à injeção de óleo pesado e (iv) nenhum superaquecimento do a ventania. Outros pontos relacionados ao uso de uma ou duas lanças em um alto-forno típico são apresentados a seguir.
- Ao usar uma lança de injeção, a quantidade máxima de injeção é de 10.000 N cum/h. Se a quantidade de injeção for maior, parte do gás não entrará em combustão na ventaneira, mas entrará no alto-forno não queimado.
- Para duas lanças de injeção, a quantidade máxima de injeção é aumentada para 15.000 N cum/h, devido às melhores condições de combustão. As condições são melhores, pois a velocidade de entrada do gás é menor, a turbulência no tubo da ventaneira é aumentada e também mais gás da coqueria está em contato com a explosão, ou seja, a área de reação é maior.
- O efeito da variação dos ângulos de injeção das lanças nos resultados previstos não é óbvio.
Um esquema de um sistema típico de lança de ventaneira é mostrado na Fig 2. Ele inclui duas lanças de injeção para injeção de COG, que são inseridas no tubo de explosão, um tubo de explosão e uma ventaneira de cobre.
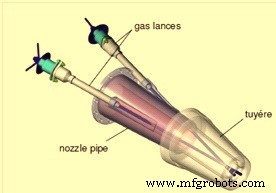
Fig 2 Sistema típico de lança de ventaneira com duas lanças.
Processo de manufatura
- Geração e uso de gás de alto-forno
- Uso de Nut Coke em um Alto Forno
- Geração e uso de gás de forno de coque
- Bateria de forno de coque sem recuperação
- Injeção de carvão pulverizado em um alto-forno
- Irregularidades do alto-forno durante a operação
- Sistema de resfriamento do alto-forno
- Fábrica de Subprodutos de Forno de Coque
- Revestimento refratário do alto-forno
- Produção de DRI com gás de coqueria como redutor