Detecção de falhas e diagnósticos em manutenção de equipamentos
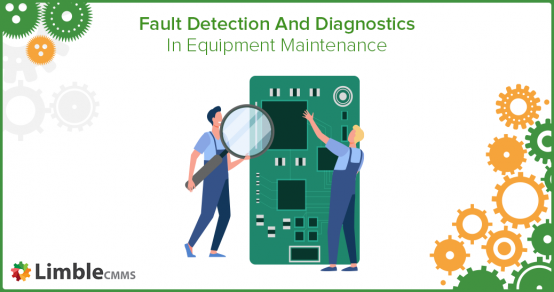
Compreender as falhas do equipamento e desenvolver estratégias para detectá-las e diagnosticá-las é um dos elementos-chave da manutenção do equipamento.
O objetivo deste artigo é apresentar uma visão geral da detecção de falhas e diagnósticos aplicados para melhorar o processo de manutenção de equipamentos e aumentar a confiabilidade dos ativos.
A história por trás da detecção e diagnóstico de falhas
No início, a manutenção do equipamento se restringia ao conserto de ativos defeituosos e à manutenção de rotina básica com base em rígidos intervalos de tempo. Os profissionais de manutenção não poderiam ter sido mais proativos, mesmo se quisessem. Sua capacidade de coletar, armazenar e analisar dados sobre a integridade e o desempenho do equipamento era simplesmente muito limitada.
No entanto, devido aos avanços consistentes em controles baseados em microprocessador, automação, aquisição de dados em tempo real e sistemas como Fault Detection and Diagnostics (FDD), a maneira como realizamos a manutenção do equipamento foi significativamente transformada.
FDD na manutenção de equipamentos
O objetivo da Detecção e Diagnóstico de Falhas no contexto da manutenção de equipamentos é otimizar os custos de manutenção e, ao mesmo tempo, melhorar a confiabilidade, disponibilidade, facilidade de manutenção e segurança (RAMS) do equipamento. O FDD funciona monitorando e analisando continuamente os dados de monitoramento de condição e detectando quaisquer anomalias (se houver). Os conjuntos de dados de condição do equipamento são então processados por algoritmos de diagnóstico de falhas, às vezes embutidos no próprio equipamento, para produzir alertas de falha para os operadores do equipamento e permitir a intervenção de manutenção em tempo hábil.
Em alguns casos, os algoritmos são sofisticados o suficiente para até mesmo iniciar ações de contenção de falhas para autocorrigir a própria falha e restaurar o equipamento à sua condição saudável.
Elementos-chave do sistema de detecção e diagnóstico de falhas
O FDD, como o nome indica, contém a detecção e diagnóstico de falhas de equipamentos. O diagnóstico da falha pode ser dividido em isolamento e identificação da falha.
A avaliação de falhas geralmente é incluída no escopo do FDD, pois ajuda a entender a gravidade da falha no desempenho do sistema - um aspecto importante do gerenciamento de manutenção.
No entanto, o algoritmo de detecção e diagnóstico de falhas para qualquer equipamento deve conter pelo menos os quatro processos-chave listados abaixo (estes também podem constituir um processo não linear, desde que algumas etapas ocorram ao mesmo tempo):
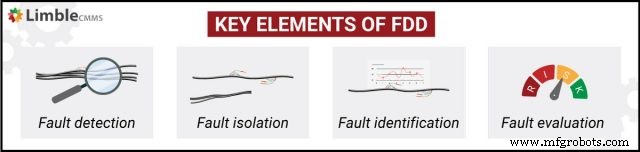
Precisamos discutir cada elemento com mais detalhes para realmente entender como funcionam a detecção e o diagnóstico de falhas.
1. Detecção de falha
A detecção de falhas é o processo de descobrir a presença de uma falha em qualquer equipamento antes que ela se manifeste na forma de uma avaria. É o estágio mais importante do FDD, pois todos os processos downstream dependem de sua precisão.
Se o equipamento não conseguir descobrir o modo de falha correto (ou se a detecção estiver incorreta e disparar alarmes falsos), o isolamento, a identificação e a avaliação também serão ineficazes.
Existem duas abordagens principais para a detecção de falhas:
- Detecção de falha baseada em modelo: É realizado por meio de modelagem matemática de sinais e processos.
- Detecção de falhas baseada em conhecimento: É um método que aproveita os dados históricos sobre o desempenho do equipamento.
Detecção de falha baseada em modelo
Na detecção baseada em modelo, definimos um conjunto de regras de engenharia que são escritas de acordo com as leis físicas que definem as relações dos subsistemas e componentes dentro do equipamento. Sempre que a regra é quebrada, o algoritmo pode detectar a falha e executar o diagnóstico de falha.
Um exemplo de detecção de falha baseada em modelo é o uso de refletometria no domínio do tempo (TDR) para detectar falhas em cabos subterrâneos. No TDR, o sinal é enviado através do cabo de teste e é recebido após ser refletido do ponto de falha.
Se o cabo tiver uma descontinuidade ou alta impedância, a parte do sinal será refletida de volta para o equipamento de teste ou receptor. Ao analisar o tempo de retorno do sinal e a velocidade do sinal refletido, o equipamento de teste pode detectar a natureza das falhas no cabo como uma falha de circuito aberto ou uma falha de curto-circuito.
Outro exemplo simples de detecção baseado em regras vem da operação em série do sistema de enchimento, tampa e embalagem de garrafas em um sistema de correia transportadora. Uma regra simples pode ser estabelecida para indicar a hierarquia de processos como:
- a garrafa não pode ser tampada até que as garrafas estejam cheias com o líquido
- as garrafas não podem ser embaladas a menos que sejam cheias e tampadas
Em caso de falha no mecanismo de tamponamento da garrafa, o algoritmo detectará a interrupção de entrada no sistema de embalagem. Ele notificará o operador de embalagem com bastante antecedência. A preparação necessária pode ser feita para minimizar as perdas operacionais no lado da embalagem da correia transportadora.
Detecção de falhas baseada em conhecimento
Para que a detecção de falhas baseada em conhecimento funcione, primeiro precisamos estabelecer uma linha de base. Isso é feito recuperando os parâmetros de desempenho do equipamento como tensão, corrente, vibração, temperatura, pressão e outras variáveis de processo relevantes - enquanto o equipamento está funcionando em condições normais.
O objetivo é desenvolver a assinatura do equipamento em operações normais.
Depois disso, os mesmos parâmetros são recuperados continuamente e correlacionados com a assinatura “saudável” para capturar o desvio por meio de uma interface de análise estatística - reconhecimento de padrão feito por meio de aprendizado de máquina ou uma rede neural artificial.
Podemos usar essa técnica para prever a falha do rolamento do motor por meio de dados sensoriais coletados do rolamento e do motor em geral.
A grande quantidade de dados obtidos ao longo do tempo - histórico do processo - pode ser analisada usando um algoritmo estatístico. Isso nos ajuda a compreender o impacto das diferentes condições às quais o motor está sujeito, como classificação térmica, estresse mecânico ou algumas outras condições de operação que ocorrem em circunstâncias especiais.
O algoritmo então correlaciona o impacto dessas condições na degradação da integridade do rolamento e prevê a taxa de falha e a condição de integridade do motor em geral.
Com base nessas assinaturas de dados, a análise pode ser feita para prever a saúde futura do equipamento. Além disso, os alarmes necessários podem ser disparados e o diagnóstico de falhas pode ser conduzido, para que o operador / técnico possa tomar as medidas adequadas.
Os mesmos dados podem ser usados para estabelecer uma estratégia de manutenção preditiva ao longo da vida restante do motor.
2. Isolamento de falha
O objetivo do processo de isolamento de falhas é localizar a falha no componente mais baixo que pode ser substituído. Em algumas aplicações, a detecção de falhas e o isolamento andam de mãos dadas; eles podem, é claro, ser módulos separados do processo. Isso ocorre porque os processos de detecção e localização da falha acontecem basicamente ao mesmo tempo, ambos feitos pelo algoritmo Fault Detection and Isolation (FDI).
Por exemplo, considere o exemplo de teste de TDR para cabos subterrâneos. O sinal de pulso retornado do cabo indica simultaneamente a presença e a localização da falha ao longo do tempo e da velocidade do sinal de pulso retornado.
Um aspecto importante do isolamento de falha é que a falha deve estar localizada no componente mais baixo que pode ser substituído . Isso é feito para melhorar a precisão do isolamento e reduzir o impacto do tempo de inatividade.
No caso do exemplo do sistema de transporte de garrafas explicado anteriormente, a detecção deve ser capaz de apontar o local da falha, como a falha do cartão de controle no mecanismo de tampa da garrafa.
Se a detecção apenas apontar uma falha de alto nível na correia transportadora, isso não será realmente útil para o técnico que realiza o diagnóstico - há vários sistemas no mesmo transportador que podem falhar.
A informação que realmente irá acelerar o processo de reparo é saber a localização exata da falha.
3. Identificação de falha
O objetivo da identificação de falhas é entender o modo de falha subjacente, determinar o tamanho da falha e encontrar sua causa raiz. Os métodos de diagnóstico de falhas podem ser diferentes, mas as etapas a seguir geralmente são as mesmas.
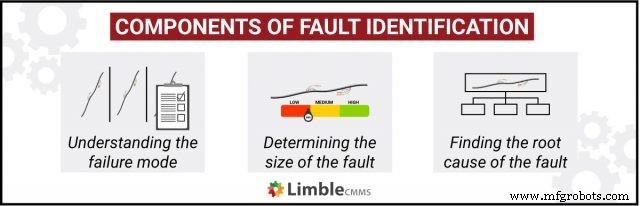
Compreendendo o modo de falha subjacente
A compreensão aprofundada do modo de falha requer trabalho:
- precisamos analisar como a falha se comporta em momentos diferentes
- para que possamos desenvolver a assinatura variante do tempo do modo de falha
- e classifique-o em diferentes categorias
Determinando o tamanho da falha
Independentemente do método de detecção de falhas aplicado, o tamanho ou magnitude da falha desempenha um papel importante na definição de qual é o nível desejado de tolerância a falhas que precisa ser construído no projeto do equipamento.
Se a magnitude da falha for baixa, o sistema só precisa ser capaz de suportar a falha por um tempo extra até que a falha seja eliminada por si mesmo. O exemplo perfeito é permitir a troca temporária de sobrecorrentes em aparelhos elétricos, desde que isso não afete significativamente o desempenho do equipamento.
Agora, se a magnitude da falha for realmente alta, uma metodologia diferente é necessária:os engenheiros precisam usar redundâncias ativas ou passivas para aumentar a tolerância a falhas em seus dispositivos.
Encontrando as causas raízes
O algoritmo de detecção e diagnóstico de falhas é o núcleo de um bom sistema de diagnóstico de falhas. É baseado em princípios de aprendizado de máquina e pode ser usado para identificar anomalias nos fluxos de dados originados do equipamento, determinando a causa raiz por trás disso.
Identificar alguns modos de falha é realmente simples, enquanto outros podem ser desafiadores e requerem cálculos matemáticos extensivos.
Vamos usar um motor de indução CA trifásico de alta tensão e alta potência como exemplo.
Na maioria das vezes, os modos de falha subjacentes são de natureza mecânica e associados à parte rotativa do motor:enrolamentos do rotor em curto, falhas nos rolamentos e quebra do rotor. Como o rotor é um componente de movimento rápido, não se pode instalar um sensor diretamente nele.
Os algoritmos FDD avançados podem ser usados para produzir assinaturas de corrente do terminal do estator do motor saudável e compará-las com as assinaturas de corrente em condições de falha.
Por exemplo, ao quebrar as barras do rotor, o pulso produzido na corrente do estator é duas vezes a frequência da corrente do estator do motor. Existe uma correlação indireta entre a quebra mecânica das barras do rotor e as flutuações da corrente do estator.
Essas tendências emergentes são analisadas por algoritmos de detecção e diagnóstico de falhas e podem ser usadas para encontrar possíveis causas-raiz, que são derivadas e exibidas em tempo real em painéis ao vivo.
O uso de tais algoritmos de identificação de falhas reduziu significativamente a quantidade de tempo que os técnicos precisam para solucionar problemas de equipamentos e chegar à causa raiz das falhas. Os diagnósticos automáticos de causa raiz contribuíram enormemente para reduzir o tempo de inatividade do equipamento, melhorando o tempo médio de reparo e aumentando a confiabilidade geral da planta.
4. Avaliação de falha
Depois que os modos de falha e as causas raiz associadas são identificados, a próxima etapa é avaliar o impacto desse tipo de falha no desempenho geral do sistema.
Precisamos considerar fatores como:
- o impacto da falha no meio ambiente e no resto do sistema
- o impacto da falha na segurança do sistema
- a perda financeira devido ao tempo de inatividade
- a necessidade de tomar decisões de substituição de capital (no caso de a gravidade da falha ser suficiente para justificar a substituição do equipamento em vez de consertá-lo)
via GIPHY
A avaliação de falhas é um elemento significativo do processo geral, uma vez que visa compreender a gravidade da falha . Isso ajuda os engenheiros de confiabilidade a fornecer validação e calcular o risco de falhas, o que terá um grande impacto nos requisitos de manutenção, recomendações e otimização.
Por exemplo, o resultado do FDD para uma peça do equipamento pode implicar no rápido aumento das taxas de falha. No entanto, o impacto dessa falha pode ser mínimo no desempenho geral do sistema, tornando o risco geral moderado. Nesse caso, a estratégia de manutenção menos rigorosa, como operação até a falha ou manutenção preventiva, pode ser suficiente para gerenciar o risco.
A detecção de falhas e diagnósticos para outra peça do equipamento pode indicar o aumento da taxa de falha, junto com o alto impacto da falha no desempenho geral do sistema. Nesse caso, o programa de manutenção preditiva mais rigoroso deve ser adotado, apesar de seu alto custo. Isso ocorre porque o aumento do custo de manutenção é garantido para evitar uma grande precipitação que será muito mais cara.
Otimizando a manutenção com FDD
Em suma, a detecção e o diagnóstico de falhas desempenham um papel decisivo na otimização do regime de manutenção de qualquer equipamento, ao longo de seu ciclo de vida.
Com o advento de tecnologias de computação rápida, processamento de big data e algoritmos de aprendizagem avançados, a detecção de falhas tradicional evoluiu para sistemas de gerenciamento de falhas automáticos que não apenas detectam falhas, mas também identificam a causa raiz e implementam ações corretivas para evitar recorrências futuras.
Essa automação de uma série de processos manuais permitiu aos engenheiros de confiabilidade e manutenção aplicar previsões sobre a integridade do equipamento, derivar o desempenho futuro do equipamento e definir intervalos de manutenção ideais.
A única coisa que resta a fazer é iniciar seu software de gerenciamento de manutenção computadorizado (CMMS), rastrear a condição de seus ativos críticos e programar o trabalho de manutenção adequado.
Manutenção e reparo de equipamentos
- A Evolução da Manutenção Industrial
- Deixe o risco e seu equipamento determinarem sua estratégia de manutenção
- Cuidados com a saúde humana e manutenção de equipamentos:Alguma conexão?
- Melhor desempenho em manutenção e confiabilidade
- Novo livro ajuda a transformar a manufatura e a manutenção
- Detalhes são importantes na manutenção e confiabilidade
- 5 Chaves para Manter a Confiabilidade do Equipamento
- 5 causas de falha do equipamento (e o que você pode fazer para evitá-lo)
- 3 Chaves para aluguel e manutenção de equipamentos industriais
- Dicas de manutenção do motor para proteger seus equipamentos e maquinários pesados