Existe uma melhor estratégia de manutenção? 5 estratégias de manutenção comparadas
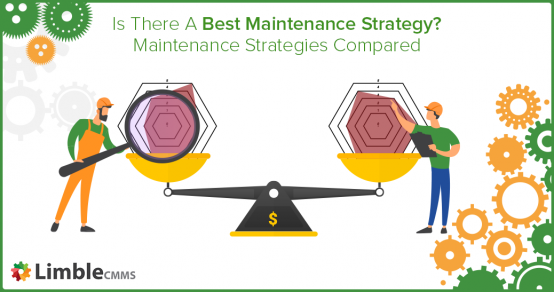
Ao selecionar uma estratégia de manutenção, podemos dizer com segurança que ser proativo é melhor do que ser reativo. No entanto, é uma grande decisão e há um punhado de estratégias viáveis de manutenção proativa para escolher.
Eles variam em complexidade, eficácia e custo de implementação - portanto, você não quer tomar essa decisão sem entender o que cada um traz para a mesa.
Existe a melhor estratégia de manutenção? A resposta curta é não. A resposta longa é dada abaixo enquanto comparamos as principais características, diferenças e cenários de aplicação .
Você pode usar a tabela de conteúdo no lado esquerdo da tela para navegar rapidamente para as partes do artigo de seu interesse.
Onde está seu departamento de manutenção agora?
Se olharmos para as estratégias de manutenção isoladamente, poderíamos dizer objetivamente que a manutenção prescritiva é o caminho a percorrer. É a estratégia mais precisa, requer o mínimo de pessoal para funcionar e oferece os melhores resultados em termos de desempenho, disponibilidade e tempo de atividade do equipamento.
Infelizmente, não é assim que o mundo real funciona. As empresas têm orçamentos de manutenção diferentes, usam ativos diferentes, têm trabalhadores com conjuntos de habilidades diferentes e têm posições iniciais diferentes . Vamos nos concentrar no último por um minuto como o fator mais negligenciado.
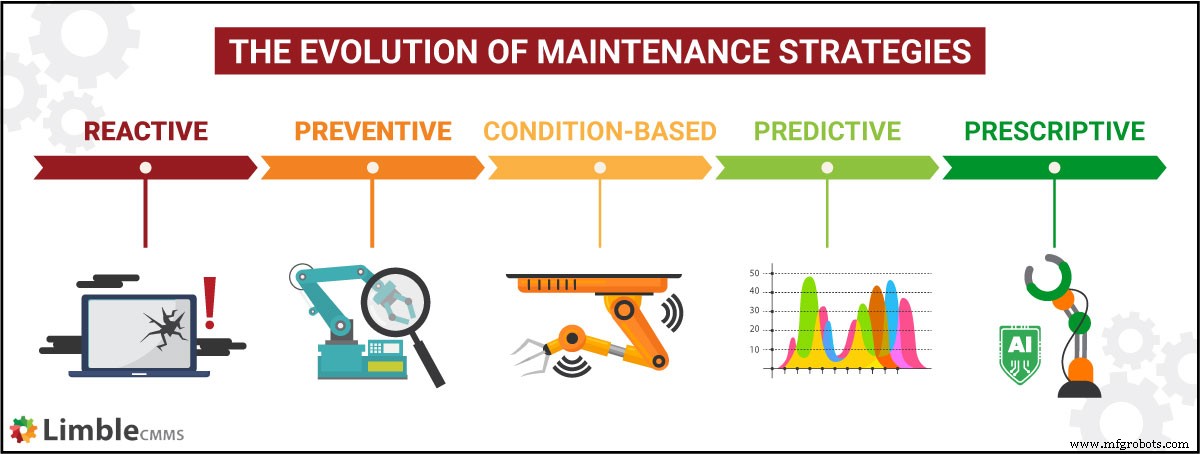
Com o passar dos anos, os avanços na tecnologia de sensores e IIoT facilitaram a evolução das estratégias de manutenção.
Indo da esquerda para a direita, cada estratégia de manutenção subsequente traz benefícios adicionais. Da mesma forma, também acarreta custos e complexidade adicionais. Por causa disso, é difícil pular dois ou três passos à frente. Se você está preso em um modo reativo, é muito desafiador fazer uma transição bem-sucedida para a manutenção preditiva.
A jornada será muito mais tranquila se você seguir a evolução natural dessas estratégias. Antes de tomar uma decisão, cada departamento de manutenção deve considerar onde está agora - quais são suas limitações e capacidades atuais.
Para aqueles que estão determinados a dar um salto maior - faça um favor a si mesmo e comece com um projeto piloto.
Critérios para escolher a estratégia de manutenção mais eficaz
Acreditamos que a melhor abordagem para o gerenciamento de manutenção é aplicar uma combinação de estratégias de manutenção, com base na criticidade dos ativos usados.
Podemos encontrar uma organização onde a manutenção preventiva seja uma estratégia ideal para todos os seus ativos? Certamente, mas isso é incomum - e a razão pela qual uma estratégia de manutenção universalmente melhor não pode existir.
Aplicar a estratégia certa para cada ativo requer um entendimento completo de:
- seus ativos (seus modos de falha e requisitos de manutenção)
- suas capacidades (orçamento, habilidades, acesso a ferramentas e tecnologia)
- estratégias de manutenção (como funcionam, seus prós e contras, custos e requisitos de implementação)
Na próxima seção, vamos nos concentrar no terceiro ponto. Explicaremos resumidamente como cada estratégia funciona e procederemos para avaliá-las com base nos seguintes fatores:
- conjunto de nossos fatores pré-selecionados (confiabilidade de ativos, automação do trabalho, capacidade de controlar custos, utilização de ativos, capacidade de otimizar recursos de manutenção, variedade de ativos aplicáveis)
- prós e contras
- custo para implementar e executar
- requisitos de implementação (em termos de habilidades, hardware e software)
- melhor usado para (quais tipos de ativos)
Incluiremos alguns gráficos personalizados para ajudá-lo a visualizar a diferença relativa entre esses fatores.
Cada seção terminará com um link para um guia detalhado que discute a respectiva estratégia de manutenção em mais detalhes.
Comparação de cinco tipos principais de estratégias de manutenção
Vamos excluir a manutenção produtiva total, a manutenção autônoma e a manutenção corretiva desta comparação, pois são conceitos que podem ser aplicados em qualquer estratégia de manutenção que você decida executar.
1) Manutenção de execução até a falha
Manutenção run-to-fail (também conhecida como manutenção reativa) frequentemente representa a falta de uma estratégia de manutenção real. Isso sugere que o departamento de manutenção não tem um plano - ele espera até que algo parta e, em seguida, envia uma equipe para consertá-lo. Enxague e repita.
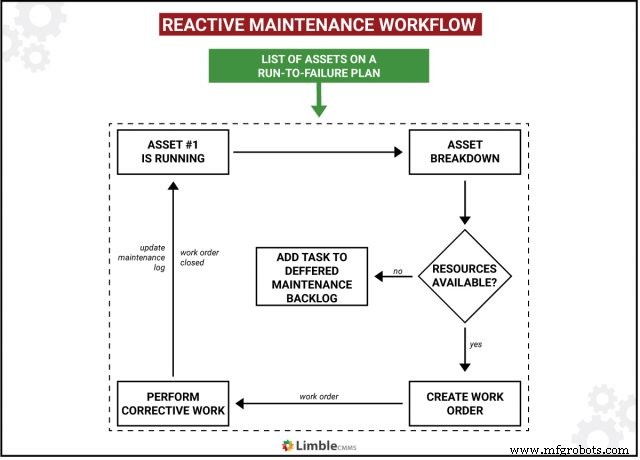
Essa abordagem, quando aplicada a todos os ativos físicos, pode literalmente arruinar um negócio. As coisas começam a quebrar a torto e a direito. As equipes de manutenção não podem estar em todos os lugares ao mesmo tempo. A carteira de manutenção adiada começa a crescer e os problemas operacionais tornam-se insuportáveis.
Não é uma visão bonita. Embora a organização possa implementar um CMMS (ou um sistema alternativo de tíquetes de manutenção gratuita) para ser mais eficiente, a abordagem reativa para manutenção é uma solução ruim de longo prazo.
Acabamos de pintar uma imagem bastante sombria. No entanto, uma estratégia de manutenção run-to-fail não deve ser completamente descartada .
Ativos irrecuperáveis, como lâmpadas e ativos que estão perto do fim de seu ciclo de vida, podem ser substituídos apenas depois de quebrados. Eles podem estar em um plano de manutenção executado até a falha .
Além disso, os departamentos de manutenção operam com orçamentos limitados. Muitas vezes, eles não têm recursos suficientes para fazer a manutenção proativa de toda a instalação. Ainda assim, eles devem ter cuidado ao escolher quais ativos estarão no programa de manutenção executar até a falha.
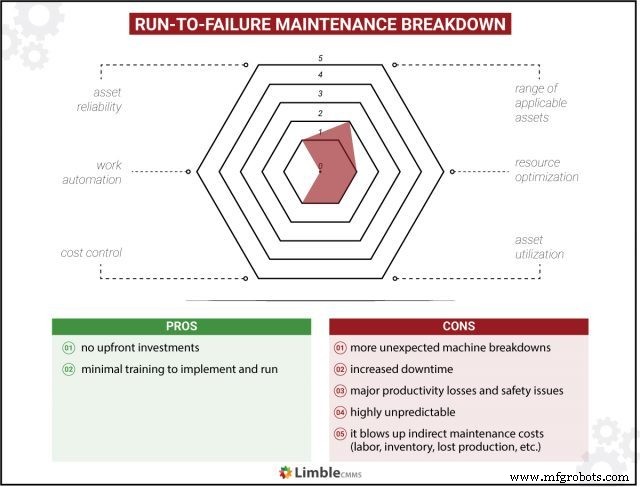
Fatores adicionais a serem considerados:
- Custo de implementação e execução: sem custos iniciais, muito barato de executar.
- Requisitos de implementação: não há requisitos notáveis (embora ainda possa se beneficiar do uso de um sistema de gerenciamento de manutenção computadorizado).
- Melhor usado para: ativos não reparáveis, ativos de baixa prioridade que são baratos e fáceis de reparar ou substituir, ativos simples que você planeja substituir após a próxima falha.
2) Estratégia de manutenção preventiva
De acordo com nosso relatório de manutenção de 2021, a manutenção preventiva é a estratégia de gerenciamento de ativos mais popular.

Manutenção preventiva (também conhecida como manutenção preventiva) é a estratégia de manutenção proativa mais simples e econômica. Ele ganhou destaque à medida que as empresas perceberam que é mais econômico investir em manutenção regular do que esperar que os ativos quebrem - e lidar com todas as consequências negativas que vêm com o tempo de inatividade não planejado.
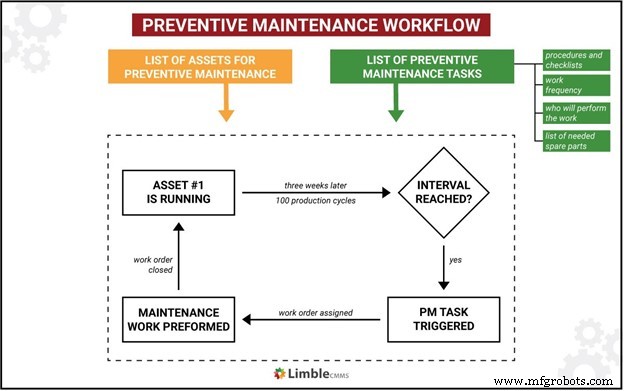
Existem dois tipos de manutenção preventiva, com base em como as atividades de manutenção são programadas:
- manutenção baseada em calendário ( troca do filtro a cada dois meses; troca do óleo a cada três semanas )
- manutenção baseada no uso ( após X quantidade de horas de trabalho; a cada X ciclos de produção )
Esses dois tipos representam simultaneamente os lados mais fortes e mais fracos dos programas de manutenção preventiva.
A manutenção regular garante que os ativos sejam mantidos íntegros. No entanto, isso pode levar a uma manutenção excessiva - como a substituição de peças que ainda podem ser usadas por um tempo. Felizmente, as organizações podem aproveitar o histórico de ativos, logs de manutenção e outros dados do CMMS para manter a manutenção excessiva em níveis aceitáveis.
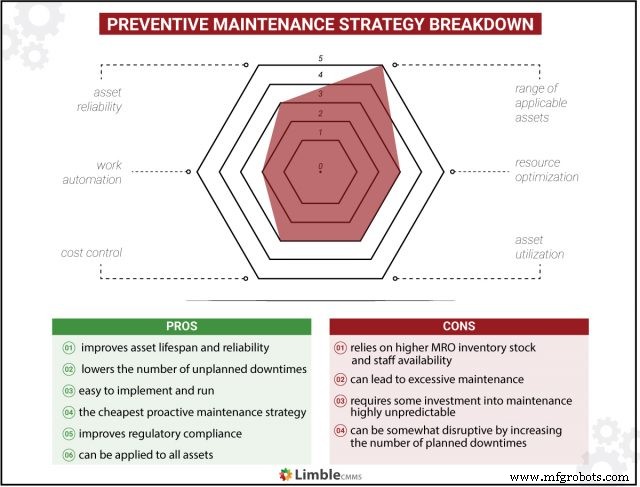
Fatores adicionais a serem considerados:
- Custo de implementação e execução: custo baixo a médio; a estratégia de manutenção proativa mais barata.
- Requisitos de implementação: cultura de manutenção pró-ativa, CMMS ou sistema equivalente para gerenciar o trabalho de manutenção e garantir a disponibilidade de peças de reposição, trabalhadores treinados para realizar tarefas de manutenção preventiva.
- Melhor usado para: qualquer ativo que pode causar problemas operacionais se falhar; quaisquer ativos de baixa e média prioridade que sejam caros para consertar ou substituir.
Para mais informações, leia nosso guia completo sobre manutenção preventiva. Você também pode verificar esta peça sobre como criar um plano de manutenção preventiva do zero.
3) Manutenção baseada em condição (CBM)
Manutenção baseada em condição (CBM) dá um passo à frente, introduzindo tecnologia de monitoramento de condição na mistura. Ele usa análise de vibração, teste ultrassônico, teste infravermelho e outras técnicas para avaliar a condição atual de um ativo e seus componentes.
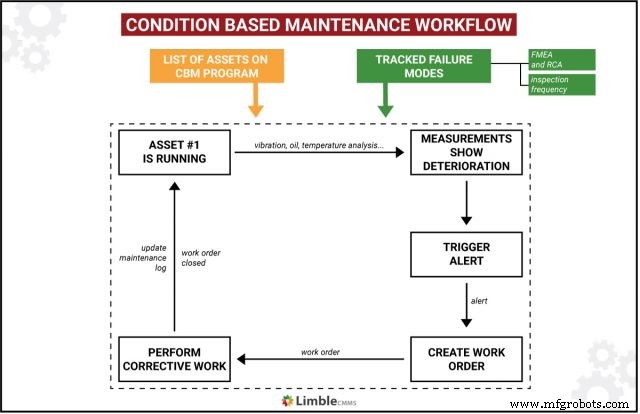
Essa informação é então usada para criar programações de manutenção mais eficientes.
O problema que a CBM tenta resolver está relacionado à maneira como o desgaste se acumula. Dependendo de coisas como materiais de entrada, condições ambientais e comportamento do operador da máquina, o mesmo tipo de ativos se deteriorará em um ritmo diferente.
Em vez de seguir um cronograma fixo, os gerentes de manutenção podem confiar nos dados de monitoramento da condição e nos intervalos P-F para programar o trabalho com base na condição atual do ativo.
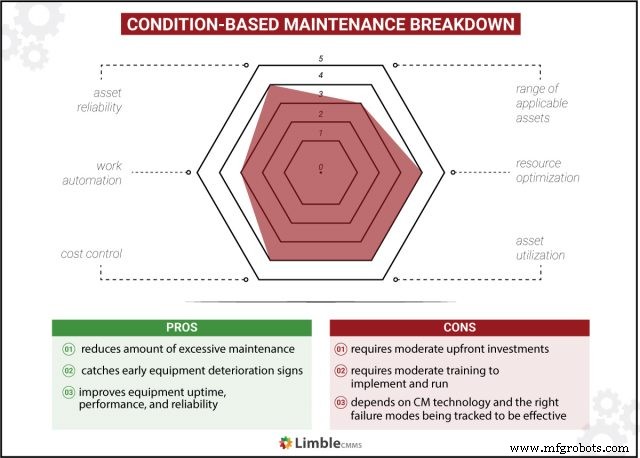
Fatores adicionais a serem considerados:
- Custo de implementação e execução: custo médio; depende do tipo de tecnologia de monitoramento de condição que a organização deve adquirir.
- Requisitos de implementação: equipamento de monitoramento de condição, CMMS, trabalhadores treinados que sabem como utilizar a tecnologia de monitoramento de condição.
- Melhor usado para: qualquer ativo de média ou alta prioridade cujos modos de falha podem ser facilmente rastreados com equipamento CBM.
Para obter mais informações, leia nosso guia detalhado sobre manutenção baseada em condições.
4) Estratégia de manutenção preditiva (PdM)
Uma estratégia de manutenção preditiva é uma versão mais precisa da manutenção baseada na condição. Ele usa dados de monitoramento de condição, recomendações de OEM, registros de manutenção e outros dados para construir algoritmos que podem prever falhas de equipamento.
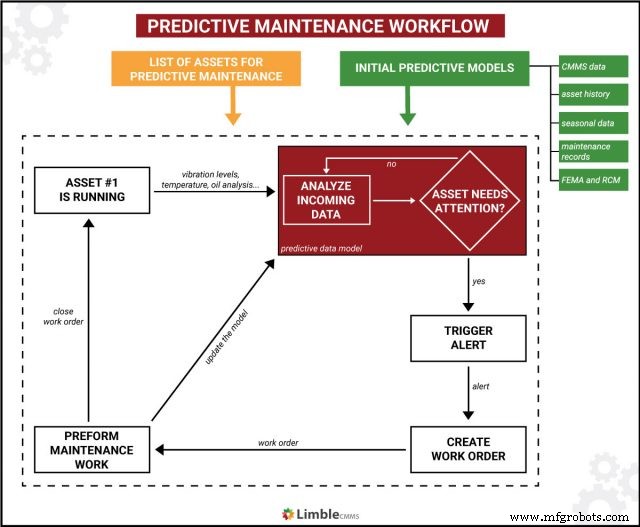
O modelo é baseado em algoritmos preditivos suportados por aprendizado de máquina. Quanto mais dados ele tiver, mais preciso será o modelo na previsão de falhas. É por isso que precisa ser atualizado continuamente.
O objetivo final da manutenção preditiva é otimizar o uso dos recursos de manutenção. Sabendo exatamente quando uma determinada peça irá falhar, os trabalhos de manutenção podem ser programados e planejados com bastante antecedência, evitando simultaneamente manutenções excessivas e paralisações inesperadas do equipamento.
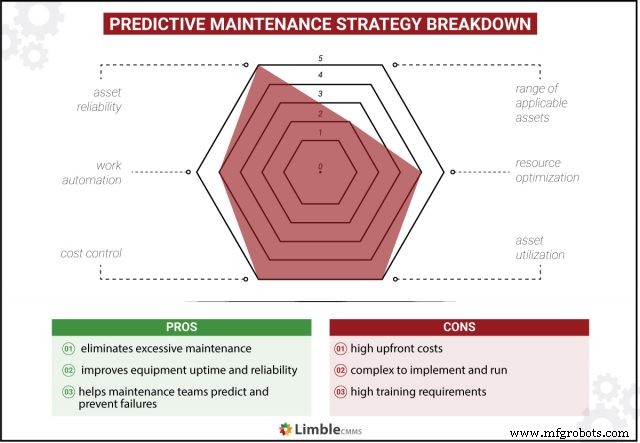
Fatores adicionais a serem considerados:
- Custo de implementação e execução: altos custos iniciais com alto potencial de ROI ao longo do tempo.
- Requisitos de implementação: várias soluções de software e hardware, sensores de monitoramento de condição, análise preditiva, treinamento especializado em ciência de dados e modelagem preditiva.
- Melhor usado para: ativos críticos.
Para mais informações, leia nosso guia completo de manutenção preditiva.
5) Estratégia de manutenção prescritiva (RxM)
A estratégia de manutenção prescritiva representa a abordagem mais avançada para manutenção de ativos.
RxM não para na previsão de falhas potenciais. Ele se baseia em aprendizado de máquina e inteligência artificial para construir algoritmos prescritivos. Esses algoritmos não apenas prevêem falhas - eles oferecem soluções potenciais para os problemas potenciais que identificaram.
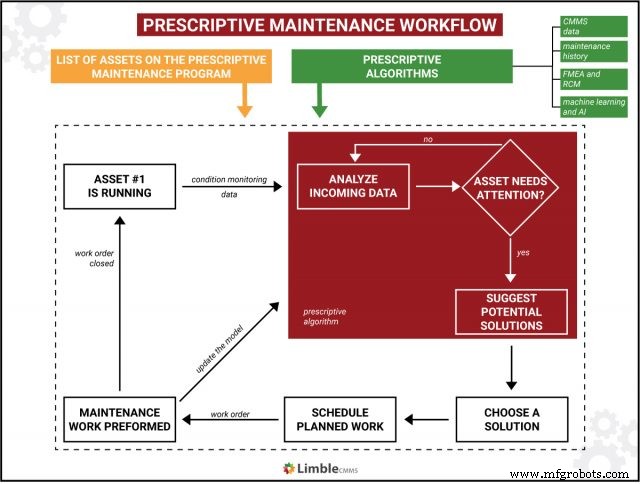
Dan Miklovic da pesquisa LNS explicou isso muito bem em sua postagem:
Digamos que um equipamento esteja apresentando um aumento na temperatura do mancal. A análise preditiva examina o perfil de temperatura e informa que é provável que falhe em X quantidade de tempo. Por outro lado, a análise prescritiva informa que, se você reduzir a velocidade do equipamento em Y%, o tempo até a falha pode ser duplicado, colocando-o dentro da janela de manutenção já programada e revelando se você ainda pode atender aos requisitos de produção planejados.
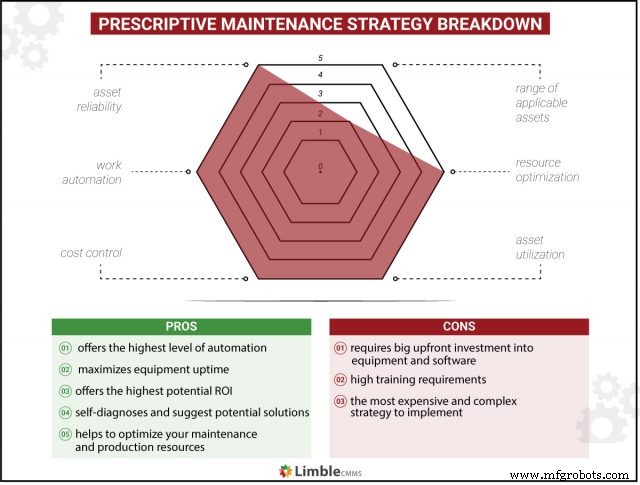
Fatores adicionais a serem considerados:
- Custo de implementação e execução: custos iniciais muito altos com o maior ROI potencial ao longo do tempo.
- Requisitos de implementação: igual à manutenção preditiva, mas com uma camada adicional de complexidade.
- Melhor usado para: ativos críticos; sistemas altamente automatizados com muitos dados de condição e desempenho.
Para obter mais informações, leia este guia perspicaz sobre manutenção prescritiva.
Comparação da estratégia de manutenção resumida
Jogamos muitas informações para você até agora. Sabemos que é difícil conciliar tudo em sua cabeça ao mesmo tempo. Abaixo estão algumas comparações lado a lado para remediar isso.
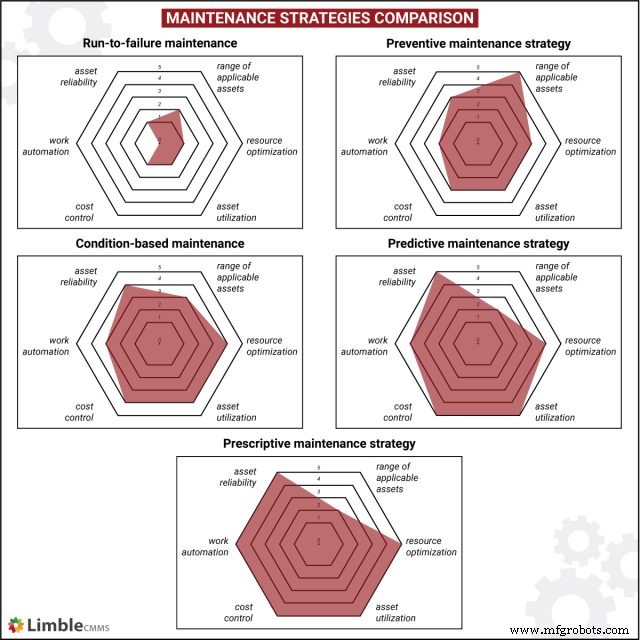
O objetivo da imagem acima é mostrar a diferença relativa entre as diferentes estratégias de manutenção em termos de fatores específicos.
Por exemplo, a otimização de recursos mostra como a manutenção preditiva permite que planejadores e gerentes de manutenção aloquem e usem seus recursos de manutenção com mais eficiência do que se estivessem executando manutenção reativa ou preventiva.
Lembre-se de que os gráficos não incluem outros fatores importantes, como custo e requisitos de implementação. Discutimos isso nas seções anteriores.
Aplicando a estratégia de manutenção certa para cada ativo
Então, qual é a melhor estratégia de manutenção para o ativo X? É uma pergunta comum e muitas vezes leva a conversa na direção errada.
Uma pergunta muito melhor seria: Como podemos resolver esses modos de falha específicos que o ativo X possui?
Cada ativo complexo pode falhar de várias maneiras. Risca isso. Cada componente de cada ativo complexo pode ter vários modos de falha.
Vamos pegar uma esteira rolante, por exemplo. O motor de acionamento pode superaquecer devido ao ventilador inoperante. A caixa de engrenagens pode falhar quando os danos nos dentes da engrenagem se acumulam devido à abrasão ou corrosão. O rolamento do eixo de transmissão pode funcionar mal devido a carga excessiva, corrosão, falta de lubrificação ou vários outros motivos. A própria correia pode escorregar devido à tensão insuficiente.
Nem todos os modos de falha são criados iguais. Eles variam no nível de dano que podem causar, na rapidez com que podem ser resolvidos, no quão caros são e quais são suas chances de ocorrer em primeiro lugar.
Selecionar os métodos de prevenção corretos para modos de falha identificados (ou tecnologia para predizê-los) é mais fácil falar do que fazer. Uma solução potencial vem na forma de manutenção centrada na confiabilidade.
Executando manutenção centrada na confiabilidade (RCM)
A manutenção centrada na confiabilidade é um processo de manutenção estruturado que ajuda a identificar quais métodos de manutenção funcionarão melhor para cada peça do maquinário. Ele está focado em melhorar a confiabilidade e a funcionalidade de ativos críticos de uma maneira eficiente e econômica.
A análise RCM é baseada na identificação de falhas funcionais em potencial, as causas raiz das falhas e a gravidade de seus efeitos posteriores (que é basicamente uma análise FMEA). Mas não para por aqui . Sua estrutura o ajuda a selecionar os métodos de prevenção mais adequados.
Em última análise, ajuda a construir o cronograma de manutenção mais eficaz para o equipamento analisado.
Cada falha pode ter uma infinidade de efeitos negativos, como aumento dos custos de mão de obra, danos ao equipamento, diminuição da produtividade, etc., que podem ser quantificados em termos de perda de $$. Quando você sabe o quanto pode perder com uma falha específica, é muito mais fácil decidir a quantidade de recursos que deve investir para evitá-la.
The solution can be applying any of the maintenance strategies we discussed above – from using sensors and analytics to track deterioration to actually letting the failure happen and being ready to fix it.
Keep in mind that RCM is a complex process that feeds on maintenance data. If you are purely reactive, don’t have a CMMS, and your maintenance logs are a mess, your organization is probably not ready to run RCM. Start with preventative maintenance and move your way up.
Performing Risk-based maintenance (RbM)
Risk-based maintenance is a maintenance process that helps you determine the most economical use of your maintenance resources. It helps divert resources from non-critical to critical assets. This is especially helpful when working with a limited budget, something most maintenance and facility managers can identify with.
The criticality of an asset is determined using a risk (a.k.a criticality) matrix. Each asset is assigned a Probability of Failure (PoF) and Consequence of Failure (CoF) factor. You can use these to map each asset on the criticality matrix. You should get something like this:
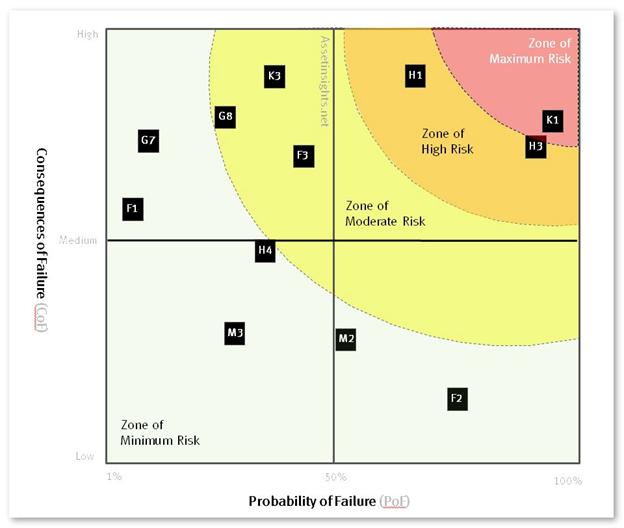
A representation of a criticality matrix
Same as RCM, RbM also relies on relevant maintenance data to ensure each asset is assigned the right PoF and CoF factors.
Naturally, the most critical assets ought to get the most attention. As such, it is easier to justify the investment into condition monitoring and predictive technology to keep an eye on your highest-priority assets.
While in some cases that might be redundant, you can technically use RbM to identify your critical assets, and then pull those assets through the RCM process to select prevention methods and create the maintenance schedule.
To learn more, check out our guide on how to use risk-based maintenance.
Taking into account available internal resources
Choosing between different prevention methods and maintenance strategies has to be made with available internal resources in mind. Maintenance departments are faced with all kinds of limitations like:
- limited budget
- weak support from top management
- lack of manpower
- no access to required condition monitoring devices and other maintenance tools
- no access to required technology (CMMS, predictive/prescriptive analytics)
- old assets that are hard and expensive to retrofit with specific sensors
- lack of intra-organizational knowledge to use new technologies (or even perform complex reliability techniques like FMECA, RCA, and RCM)
- poor organizational culture that is stuck in a reactive mindset
Most (if not all) of these challenges stem from tight maintenance budgets. Top management is not going to have a sudden change of heart. Maintenance managers need to work with what they have.
As a low-cost option, preventive maintenance is still the best strategy for moving away from reactive maintenance. It is fairly easy to set up and doesn’t require a lot of training. Most importantly, the implementation can be spread out in small increments. This allows the organization to adjust the speed of transition according to its capabilities.
The best maintenance strategy is NOT the one that’s best on paper. It is the one you can successfully implement and run.
Use Limble CMMS to create a single maintenance calendar for all assets
Regardless of the strategy, everyone needs a clean maintenance calendar to plan and schedule maintenance work. There are too many moving parts to do everything manually.
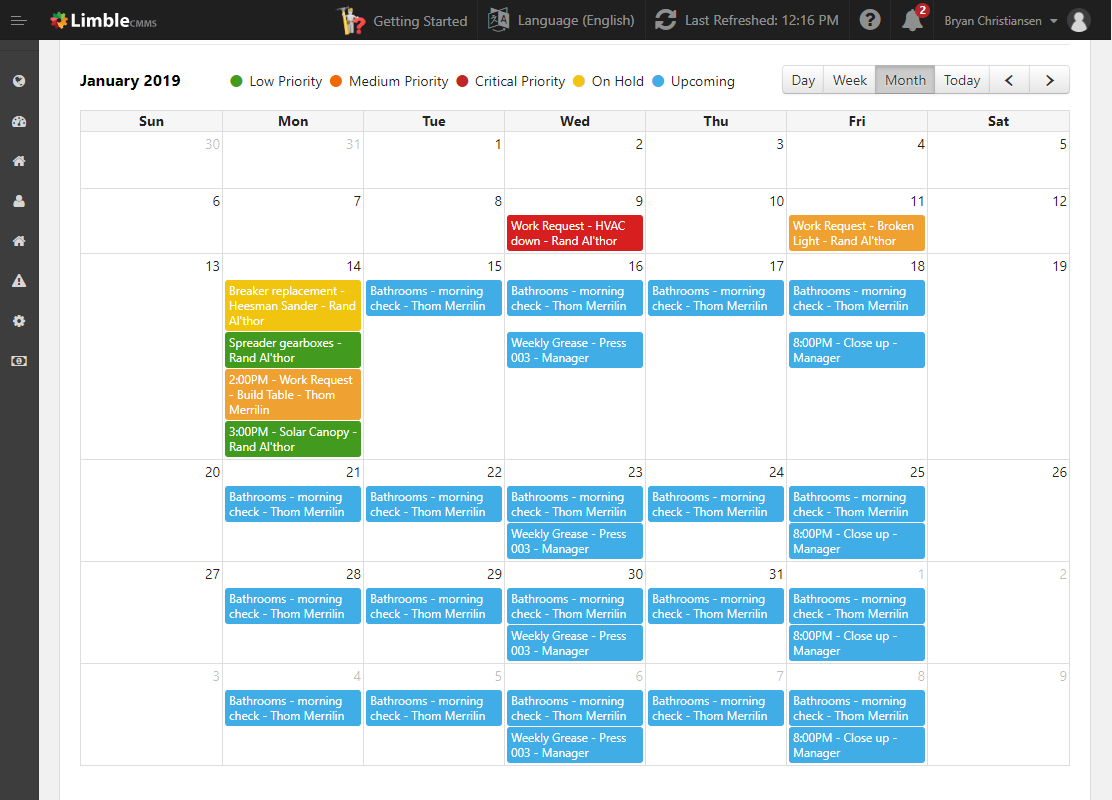
A sample of a maintenance calendar inside of a Limble CMMS
When the assets you want to track are entered into its database, you can use CMMS software to quickly set up all preventive tasks. You will also be able to manage incoming work requests, change task priorities, reschedule and reassign specific tasks, and track exactly how much maintenance resources are you spending on each asset.
With all of that data readily available, you’ll be able to improve upon initial maintenance schedules. You might even consider switching maintenance approaches for specific assets and failure modes.
If you already have the software implemented, the basic steps to create the maintenance calendar are:
- Ensure all assets you want to track are entered into the CMMS database.
- Double-check that basic asset information is correct and up-to-date (like installation date, location, and attached manuals).
- Create the preventive schedule for each asset based on its maintenance history, identified failure modes you want to prevent, and other data you were able to gather.
- If you are using CBM or predictive analytics, you will have to integrate the incoming data with your CMMS software (older CMMS solutions usually do not support that). After that, you will have to play around a little to set up alerts and the automatic triggering of work orders.
- Occasionally review available maintenance data to see if your maintenance schedules can be improved and if everyone is following outlined procedures.
When all of that is done, you can open the maintenance calendar to overview the maintenance schedule. You can just drag and drop tasks to quickly change due dates and reschedule work. Technicians assigned to affected tasks will immediately get an email and push notification informing them about the change in priority. Likewise, they’ll be notified about any new work that was just assigned to them.
If some of the work at your facility is outsourced to vendors and OEMs, you can give them limited access to Limble CMMS and send them PMs and work requests throughout the software. This means you can keep everything in a single maintenance calendar, as well as track maintenance costs associated with each vendor.
You can check Limble’s pricing plans and start a trial here .
Do the best with what you have
Don’t let the fear of failure be the reason why you can’t move forward. One great thing about all of these maintenance strategies is that they can be rolled out in stages. And it is much easier to stay on top of expenses when you can control the pace of implementation.
World-class production needs a world-class maintenance team equipped with the right tools and technology. This doesn’t happen overnight. Still, most organizations that commit to a proactive maintenance culture and follow the natural evolution of maintenance strategies can eventually get there.
1 Comments
-
aviationinfra September 21, 2021, 9:14 am
Thanks for sharing this blog. When conducting maintenance tasks, there are a few things to keep in mind. You should always make sure you have the approved manuals, tools, and parts on hand and practice thorough documentation.
Reply
Manutenção e reparo de equipamentos
- Consertando uma estratégia de manutenção quebrada:Otimização de PM e FMEA
- A manutenção reativa deve fazer parte de sua estratégia de manutenção?
- Parte do infravermelho da estratégia PM eficaz em Weyerhaeuser
- Ivara contrata Smith como líder da estratégia de confiabilidade
- Melhor desempenho em manutenção e confiabilidade
- R&M na UPM-Kymmene:Uma jornada educacional
- AFE oferece Webinars de estratégia de manutenção Wireman
- Nova estratégia de manutenção oferece muitos benefícios
- A revisão da estratégia de manutenção de ativos deve ser um programa vivo
- TOTAL desenvolve estratégia de manutenção e inspeção