Jogando com inteligência. Mude o foco de custo para valor.
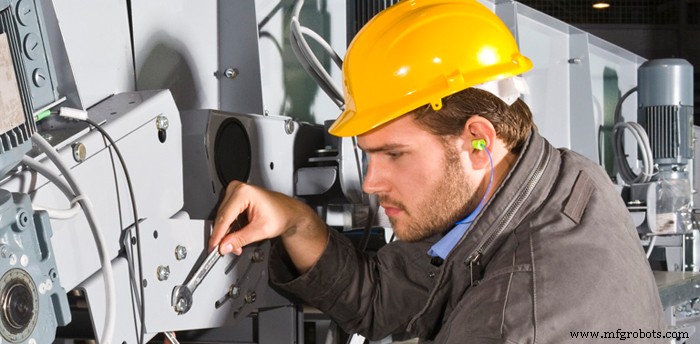
Por Steve Gahbauer
Um dos principais princípios do pensamento de manutenção japonês é que o desempenho de uma máquina é pior quando é nova. A tarefa da equipe de manutenção é melhorá-lo. E um guru americano da manutenção disse uma vez que a melhor manutenção é sem manutenção, mas esse não é o mundo em que vivemos, então a próxima melhor coisa a fazer é ser esperto. Felizmente, temos especialistas que nos orientam e nos incentivam a implementar e praticar a manutenção inteligente.
Um deles é Ben Stevens, ex-presidente da OMDEC (Optimal Maintenance Decisions Inc.), que agora se concentra em treinamento e consultoria em gerenciamento de manutenção e confiabilidade. Ele acredita que os profissionais de manutenção devem ser gerentes de negócios que mudam o foco do custo para o valor.
O gerenciamento do backlog, por exemplo, é uma forma eficaz de garantir que o trabalho realizado acompanhe o trabalho necessário. Consiste em trabalhos iniciados e dentro do prazo, mas ainda não concluídos; não concluído e atrasado; planejado e programado, mas não iniciado; e esperando para ser iniciado, mas não planejado ou programado.
As melhores práticas incluem:revisar o trabalho semanalmente com base na prioridade; examinar as razões dos atrasos; mudar as prioridades de trabalho que exige uma resposta mais oportuna; e iniciar a ação para uma prioridade principal, mas ordens de serviço atrasadas.
A falta de peças sobressalentes interrompe a boa execução das tarefas de manutenção e é uma das principais razões para estouros de tempo e custos, falhas inesperadas e operação do equipamento abaixo da média.
Stevens afirma que o gerenciamento de peças sobressalentes deve ser aplicado de forma diferente às peças comumente usadas e de custo relativamente baixo, além de peças de movimento lento e alto custo.
A primeira categoria é melhor gerenciada usando o módulo de peças sobressalentes de um CMMS. Os principais dados para cada peça estocada (número da peça, descrição, fornecedor preferencial, custo e condições de entrega) devem ser registrados. Estabeleça os níveis mínimo e máximo de estoque, juntamente com uma quantidade de pedido econômica. Registre recebimentos, emissões e devoluções para manter os níveis atuais. Quando os problemas reduzem os níveis abaixo do mínimo, o CMMS emite automaticamente as requisições de compra. Reserve peças para pedidos de alta prioridade para que não sejam usadas em outros trabalhos.
Peças críticas de alto custo requerem uma abordagem diferente. Os prazos de entrega são normalmente longos e o alto custo das peças sobressalentes sugere que não é econômico manter muitos disponíveis. A melhor prática é estabelecer o nível de confiabilidade necessário do equipamento e da peça sobressalente, fatorar a frequência de falha, prazos de entrega e custo de reposição e calcular o número de peças sobressalentes necessárias para atender à confiabilidade desejada.
O controle de custos de manutenção é outro dos assuntos favoritos de Stevens. Ele diz que o processo de ordem de trabalho do CMMS é capaz de acumular custos em cada ordem de trabalho e acumular o custo total para os níveis de equipamento, sistema e planta. Com pequenos ajustes, o CMMS também rastreia o custo da falha. Essas práticas recomendadas identificam onde os custos foram incorridos:
• Incluir mão de obra e taxas de contratados na configuração do CMMS.
• Faça o mesmo com os custos de materiais, consumíveis e peças de reposição. • Carregar ferramentas especiais para as ordens de serviço.
• Preparar relatórios mensais mostrando despesas para cada tipo de atividade de manutenção aplicada aos principais equipamentos, sistema, planta ou local. Esses relatórios identificam variações do orçamento.
O equipamento é crítico
Equipamentos não críticos ocupam uma parte significativa do esforço de manutenção. A prioridade é menor do que o equipamento crítico e deve ser tratada como tal. As melhores práticas incluem:revisões periódicas da criticidade e ordens de serviço de manutenção preventiva para otimizar tarefas; ordens de serviço frequentes e precisas; e revisões periódicas de qualquer trabalho de reparo de alto custo para ver se as táticas de baixo custo são eficazes.
Os pensamentos finais de Stevens são sobre a manutenção baseada na condição (CBM):um conceito simples repleto de muitas complexidades práticas e algumas desvantagens. Seu princípio básico é:“Se as condições do equipamento exigirem, faça a manutenção; se não exigir, não faça nada. ”
Aqui estão as etapas principais para um regime de CBM de sucesso:
• Faça uma inspeção para descobrir a condição do equipamento. • Identificar condições mensuráveis para os principais tipos de falhas.
• Decida quais níveis de medição identificam uma faixa operacional normal de um estágio de alerta a um estágio de alarme. Cada alerta deve determinar o tipo de manutenção preventiva necessária para evitar uma maior deterioração. Para cada alarme, escolha a ação corretiva, de reparo ou de emergência necessária, investigue a causa raiz e determine a ação necessária. Parece bastante simples, mas existem alguns problemas com CBM que Stevens resume da seguinte forma:
• Muitos dados. A automação nos permite coletar mais dados do que podemos analisar, o que pode mascarar tendências e obscurecer problemas. Amarre os dados a uma falha funcional e modo de falha.
• Sistemas de manutenção preventiva executando automaticamente tarefas que não são necessárias. • Captura de dados de condição como "ok" ou "não está bom". Isso evita a análise de tendências, de modo que as falhas parecem ser repentinas, uma vez que a degradação gradual não é aparente.
• Não reconhecer o status de alerta com antecedência suficiente para planejar e executar tarefas de PM antes que ocorra uma falha.
• Gravação de dados de baixa qualidade e inconsistente. As etapas para corrigir isso incluem o treinamento de coletores de dados; atribuição de tempo na ordem de serviço; atribuir responsabilidade pela coleta de dados e verificação de qualidade; e acompanhamento por meio do processo de gerenciamento de backlog e gerenciamento de desempenho.
CBM não é uma bala de prata, há muitos danos colaterais. Como em todas as tarefas de manutenção, aplique o teste padrão:ele agrega valor? Se a resposta for “não”, não o faça.
Steve Gahbauer é um engenheiro e redator freelance baseado em Toronto, o ex-editor de engenharia da PLANT e um editor colaborador regular. Envie um e-mail para [email protected]
Encontre o artigo original no site da PLANT
Manutenção e reparo de equipamentos
- O valor em tempo real da manutenção preditiva
- Por que o gerenciamento da execução do trabalho é a base de todas as atividades de manutenção
- O Gerente de Manutenção Profissional:Um Trabalho em Andamento
- A necessidade de programação de manutenção
- Posso interromper o cronograma de manutenção?
- Custo e valor de substituição estimado
- Os benefícios da gestão estratégica de ativos
- O Supervisor de Manutenção Enigma
- O valor da confiabilidade como um serviço
- Como justificar o custo de um CMMS