Manutenção centrada na confiabilidade:5 fundamentos essenciais de um RCM eficaz
A Manutenção Centrada na Confiabilidade (RCM) é uma abordagem de manutenção avançada que é usada para evitar grandes falhas em equipamentos essenciais e muito utilizados. Diversas indústrias, como petróleo e gás, fazem uso dos princípios RCM para manter suas extensas infraestruturas operando sem problemas. Gerenciar a confiabilidade dos equipamentos das instalações não é um conceito novo, mas existem várias ferramentas modernas disponíveis para apoiar esses esforços.
Um subconjunto da manutenção centrada na confiabilidade é o gerenciamento baseado em condições (CBM), que usa critérios operacionais definidos para cada ferramenta como referência de desempenho. Neste post, exploraremos cinco fundamentos principais para executar um programa RCM eficaz. Essas recomendações podem ser usadas durante as fases de planejamento, execução e melhoria para otimizar sua abordagem ao gerenciamento de manutenção.
O que é manutenção centrada na confiabilidade?
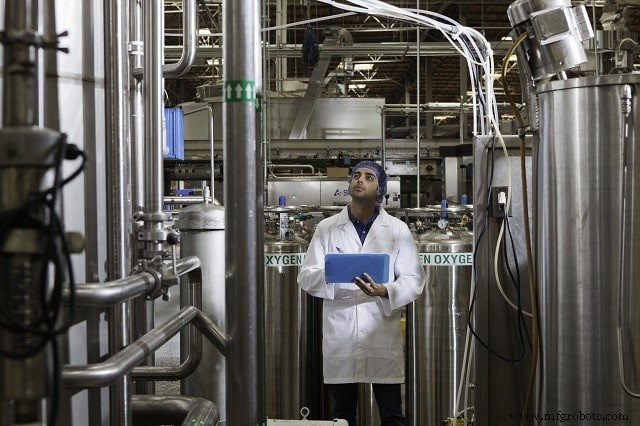
A manutenção centrada na confiabilidade é uma prática que prioriza o trabalho com base na probabilidade de falha do equipamento. O objetivo de um programa RCM é proteger os ativos que podem causar graves interrupções em caso de falha ou interrupção. Essa abordagem ajuda o gerenciamento a priorizar o trabalho de manutenção de acordo e fazer uso eficiente dos recursos. Quatro elementos-chave de um programa RCM são:
- Identificando pontos de falha para cada ativo
- Foco na manutenção da função de ativos
- Classificação de recursos com base nos modos de falha
- Criando uma estratégia de manutenção para cada ativo individual
Um programa RCM é uma abordagem muito focada que é mais frequentemente usada para ativos importantes e de alto valor. A TI pode não ser tão útil para subsistemas e ativos de prioridade mais baixa devido à natureza intensiva da análise de falhas e acompanhamentos. A manutenção centrada na confiabilidade é uma ótima opção para usar com outras abordagens, como manutenção preventiva e manutenção preditiva, como parte de um programa de manutenção em toda a empresa.
1. Definir condições de fronteira para sistemas relacionados
Um equipamento raramente existe em um vácuo completo. Ao revisar os sistemas de suas instalações, sempre vale a pena considerar tanto a função do equipamento quanto as entradas e saídas conectadas. Isso pode incluir linhas de fornecimento de eletricidade, ar, água ou outros materiais. Fazer este exercício o ajudará a decidir como atribuir cada peça do equipamento da instalação a um sistema relacionado. Uma vez que os sistemas são definidos, é possível analisar completamente cada um usando os princípios do RCM.
2. Não se concentre muito em falhas relacionadas à idade
Pode ser surpreendente, mas a causa da falha dos sistemas de equipamentos é aleatória em muitos casos e não causada pelo declínio relacionado à idade. Por exemplo, dados do setor aéreo demonstraram que entre 70-90% dos modos de falha não estão relacionados à idade. Isso é significativo ao planejar atividades de RCM porque essas ferramentas podem se beneficiar do monitoramento baseado em condições. O monitoramento em tempo real indicará um ponto de falha imediatamente e não influencia o potencial de falha com base na idade de um ativo.
3. Identificar potenciais falhas funcionais
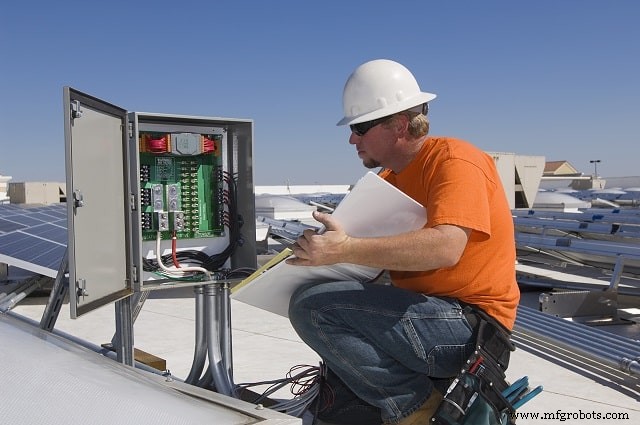
Uma das melhores maneiras de proteger o desempenho dos ativos é determinar os possíveis pontos de falha. Um modo de falha e análise de efeitos (FMEA) é um exemplo de uma ferramenta que pode ser usada para definir vários modos de falha que podem ser mitigados. Ao revisar esses pontos de falha, também é útil definir faixas de operação para parâmetros importantes. Uma faixa de operação fornecerá uma medida tangível que define uma falha potencial quando os valores se movem para fora dessa faixa.
4. Escolha soluções de manutenção com base em modos de falha
Como uma abordagem RCM priorizará os modos de falha para cada sistema de equipamento, ela também pode ser usada para selecionar soluções de manutenção apropriadas. Em alguns casos, um monitor em linha pode ser usado como uma solução baseada em condições ou um cronograma de manutenção preventiva pode ser seguido para substituir os consumíveis comuns e acompanhar as tarefas de manutenção de rotina para manter o equipamento em condições ideais de funcionamento. Um Sistema Computadorizado de Gerenciamento de Manutenção (CMMS) é um excelente recurso para planejar e organizar este trabalho. Juntamente com etiquetas de ativos de gerenciamento de instalações para simplificar a documentação e monitorar o uso e as condições do equipamento, essas ferramentas suportam um programa RCM eficaz.
5. Adote uma estrutura de projeto RCM comprovada
Qualquer programa de manutenção se beneficiará de uma melhor organização. Dada a complexidade de muitos sistemas de instalações, o uso de um CMMS combinado com uma estrutura comprovada pode ajudar a superar vários problemas comuns. Uma estrutura de projeto RMC pode ser descrita em 4 etapas comuns.
- Escolha um plano com base nos resultados desejados
- Analisar dados de equipamentos
- Implementar melhorias de manutenção
- Avalie os benefícios reais e faça as alterações necessárias
Esse processo é melhor entendido como um loop que pode ser repetido regularmente para melhorar as decisões de manutenção com base nos dados disponíveis mais recentes.
A manutenção centrada na confiabilidade é uma excelente abordagem para empresas que gerenciam ativos críticos de alto valor com requisitos de desempenho exigentes. Ao aprender sobre os princípios do RCM, é útil consultar vários recursos para criar um plano abrangente que funcione melhor para sua organização, equipe e equipamento. Esperamos que os fundamentos deste post ajudem você a otimizar suas práticas de gerenciamento de manutenção.
Tecnologia industrial
- O que é cultura de confiabilidade?
- Melhor desempenho em manutenção e confiabilidade
- A chave nº 1 para o sucesso da confiabilidade
- Detalhes são importantes na manutenção e confiabilidade
- Confiabilidade orientada para a família
- 5 Chaves para Manter a Confiabilidade do Equipamento
- Principais benefícios do software de manutenção preventiva
- Simplifique o relatório de falhas na manutenção
- Principais benefícios do software de manutenção preditiva
- Como implementar a manutenção centrada na confiabilidade (RCM)