Os 6 erros de armazenamento mais caros (e como evitá-los)
Os armazéns continuam sendo um componente crucial das redes globais da cadeia de suprimentos, pois os consumidores esperam entregas mais rápidas. A configuração de um armazém requer um planejamento cuidadoso e vários sistemas exclusivos devem ser integrados com equipamentos e softwares. Além disso, a alta prioridade dada à rotatividade rápida e ao atendimento rápido e preciso de pedidos exige que a administração remova quaisquer gargalos que possam causar atrasos.
Neste post, exploraremos seis erros caros no armazém e como você pode evitá-los. Esses erros comuns podem ser facilmente ignorados durante os estágios de planejamento de um projeto de armazém. Mas, como discutiremos, muitos desses problemas podem levar a interrupções no piso do armazém e exigir soluções caras para corrigi-los. Compreender esses erros pode ajudá-lo a evitar dificuldades semelhantes durante a configuração do armazém e os projetos de melhoria.
1. Um layout de armazém ruim

O layout de um armazém define toda a estrutura de como o trabalho será realizado em toda a instalação. Criar um design otimizado desde o início é fundamental, pois pode ser difícil fazer alterações após a instalação de racks, estantes e equipamentos. Além de escolher um layout eficiente, também é importante evitar erros comuns que podem causar problemas posteriormente. Alguns dos erros mais comuns de layout de armazém incluem:
- Ter áreas de envio e recebimento sobrepostas
- Não criar espaços para devoluções de produtos e excesso de estoque
- Projetar caminhos e áreas de trabalho muito pequenos
- Falha em manter os espaços de trabalho do armazém limpos e arrumados
Um armazém organizado deve ter zonas claramente marcadas e dedicadas para vários tipos de trabalho e caminhos de deslocamento identificados para pessoas, empilhadeiras e outros equipamentos móveis. Sinais de armazém personalizados, como sinais de corredor de armazém, sinais de portas e docas internas, placas de portas e docas externas e sinais de segurança de armazém fornecem dicas direcionais e ajudam os trabalhadores a identificar as várias áreas do armazém para facilitar a navegação. As soluções de sinalização de armazém transmitem informações cruciais para ajudar a manter o tráfego fluindo sem problemas. Um fluxo de tráfego ideal não apenas melhora a produtividade, mas também aumenta a segurança do armazém.
2. Previsões imprecisas
Mesmo o armazém mais eficiente não será capaz de gerenciar o estoque sem previsões precisas. Isso inclui o planejamento de estoque local, suprimentos e atendimento de pedidos. Ter previsões precisas dá ao gerenciamento a capacidade de definir níveis ideais de estoque de estoque e direcionar os recursos do armazém para coordenar as ordens de serviço. Essas informações também são úteis ao realizar contagens de estoque e podem ajudar a otimizar o atendimento e outras funções essenciais do armazém.
3. Acompanhamento manual
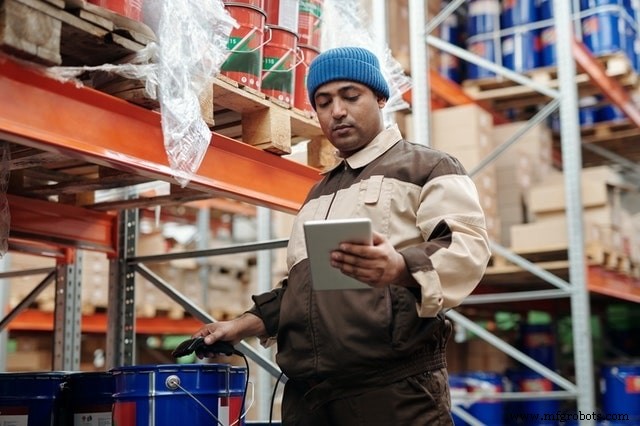
A tecnologia de automação de armazém tornou-se verdadeiramente popular e é um excelente recurso para melhorar os fluxos de trabalho do site. O uso de procedimentos que exigem excesso de papelada e entrada manual de dados pode adicionar tempo significativo e exigir mais esforço. Uma das etapas mais críticas para eliminar o trabalho manual é investir em software de gerenciamento de armazém (WMS) que pode ser usado para centralizar todos os fluxos de trabalho críticos do armazém.
Essas plataformas também podem ser integradas com códigos de barras e scanners para automatizar diversas funções do armazém, como separação, embalagem e expedição. Um WMS totalmente integrado é a espinha dorsal de um armazém que funciona bem e pode ser continuamente aprimorado com futuras integrações e complementos.
4. Escolhendo Ineficiências
O processo de separação é uma área crítica de foco para a gerência e a equipe encarregada do atendimento de pedidos em um depósito. Muitos armazéns modernos incluem esteiras transportadoras, empacotadores e outros equipamentos para ajudar a movimentar o estoque, o que pode tornar a coleta mais eficiente, mas também pode criar gargalos se essas ferramentas não forem cuidadosamente integradas aos fluxos de trabalho do armazém. A separação otimizada requer caminhos de viagem cuidadosamente definidos e um layout que priorize o fluxo de estoque. Também é recomendável ter sinalização clara e etiquetas de rack em todo o armazém para facilitar a identificação do estoque.
Com uma variedade de etiquetas e sinais de código de barras de armazém disponíveis, como etiquetas de rack de armazém, etiquetas de piso de armazém, placas de armazém suspensas, etiquetas de rack de armazém de armazenamento a frio e cartazes de rack de armazém de armazenamento a frio, etiquetas e etiquetas de código de barras de paletes e etiquetas de código de barras para recipientes retornáveis, bandejas e sacolas, você pode rotular facilmente todas as áreas do armazém para garantir a digitalização e o rastreamento contínuos e eliminar a entrada manual de dados para maior precisão.
5. Gerenciando todo o inventário igualmente
Outro erro comum no armazém é tratar todo o estoque da mesma forma. Cada peça de inventário pode ter diferentes requisitos de armazenamento, demanda e manuseio. O estoque de alta rotatividade deve ser colocado em locais de armazenamento e separação dentro do armazém que facilitem o acesso dos catadores e empilhadeiras.
Também é recomendado armazenar estoques com menor demanda longe de áreas de alto tráfego para maximizar a eficiência. O estoque sazonal e perecível deve ser cuidadosamente considerado, e pode ser benéfico ter um plano de posicionamento de estoque rotativo que aproveite as tendências sazonais ao longo do ano. Também é importante não sobrecarregar o estoque a ponto de prejudicar a eficiência. Não só o excesso de estoque pode tornar a utilização do espaço um desafio significativo, mas também aumenta seus custos indiretos – especialmente se você acabar mantendo estoque em excesso por um longo tempo.
6. Planejamento de curto prazo
Não se preparar para o futuro é um grande risco para qualquer negócio. É impossível levar em conta todas as tendências do setor ou do cliente, mas adotar um foco de planejamento de longo prazo pode ajudar muito. O crescimento futuro pode exigir um investimento significativo em novos equipamentos, sistemas e tecnologia de automação. A criação de um plano formal fornece um ponto focal e uma linha de base que pode ser revisada periodicamente e atualizada para refletir as informações mais recentes disponíveis. Esses períodos de revisão também servem como um excelente momento para coletar feedback dos funcionários sobre o que está funcionando bem e onde melhorias podem ser necessárias.
Armazéns modernos provaram que um layout eficiente, planejamento adequado e as práticas recomendadas do setor podem ser combinados para criar um centro de atendimento de alta qualidade. O gerenciamento do armazém e outros funcionários devem estar atentos aos erros comuns que muitas vezes podem ser superados com um planejamento cuidadoso durante os estágios iniciais da configuração ou reforma do armazém. Evitar esses erros dá a toda a sua equipe mais energia para gastar em trabalho de valor agregado e criar uma operação eficiente.
Tecnologia industrial
- 6 Riscos da exportação de bens manufaturados - e como evitá-los
- Seis erros comuns de logística e como evitá-los
- Três armadilhas da entrega na última milha - e como evitá-las
- Sete erros comuns de remessa e como evitá-los
- Como obter o máximo do seu sistema de digitalização de depósito
- 4 principais causas de falha de aparelhagem e como evitá-las
- O que é a cavitação da bomba e como evitá-la?
- 3 principais processos de depósito (e como melhorá-los)
- 5 perigos comuns do guindaste e como evitá-los
- Como funcionam os freios, que tipos de freios industriais existem e como tirar o máximo proveito deles