Manutenção produtiva total:a conexão entre você e o Japão dos anos 70
O que a fabricação de automóveis japonesa na década de 1970 tem a ensinar sobre como administrar um departamento de manutenção hoje? Pode ser muito. A Manutenção Produtiva Total (TPM) é apenas três letras curtas, mas há muito para olhar e considerar.
Antecedentes rápidos
Entre 1950 e 1970, as empresas japonesas investiram muito tempo e atenção no ajuste fino da fabricação. Eles descobriram que a chave era capacitar pequenos grupos de funcionários da linha de frente em projetos de melhoria. Em 1971, Seiichi Nakajima formalizou este e outros insights sobre Manutenção Produtiva Total. A contribuição mais famosa do Japão para as práticas de fabricação, JIT (fabricação just-in-time), decorre e depende dos princípios e práticas do TPM.
A Manutenção Produtiva Total hoje pode ser dividida em duas seções, primeiro a base 5S e depois os oito pilares. Vale a pena passar por cada parte para ter uma ideia de como o sistema funciona como um todo. Os objetivos do TPM combinam perfeitamente com alguns dos principais objetivos de cada departamento de manutenção:
- menos tempo de inatividade
- mais tempo de atividade
- menos estresse
- maior segurança
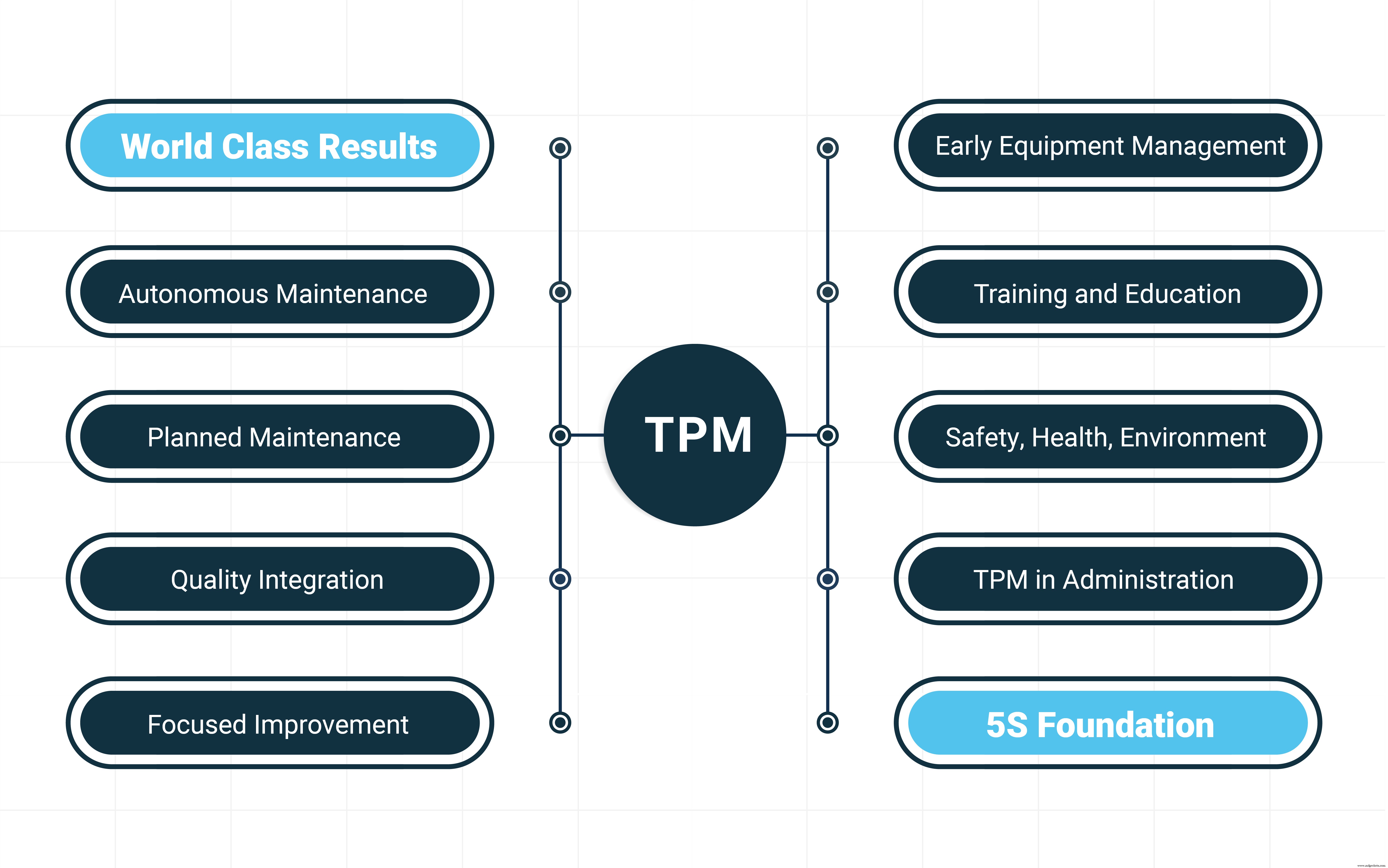
Fundação 5S
Embora as palavras originais sejam japonesas e haja mais de uma tradução possível para cada uma, elas tendem a ser apresentadas como:
- Classificar
- Coloque em ordem
- Brilho
- Padronizar
- Sustentação/Autodisciplina
Vejamos cada um. Tenha em mente que eles são sequenciais e auto-referenciais. Você precisa fazê-los em ordem, e as etapas posteriores referem-se às anteriores.
Classificar
Aqui, você está passando e basicamente classificando as coisas em duas pilhas, uma das coisas para manter na área e uma das coisas para mover ou jogar fora.
Isso torna tudo menos confuso, e a desordem deixa você mais lento. Quando você procura uma peça, pode encontrá-la mais rapidamente quando há menos outras peças ao seu redor. Por que é tão difícil encontrar uma agulha no palheiro? É por causa de todo o feno.
Além de deixar tudo mais rápido, pode deixar tudo mais seguro também. Se o piso ao redor de um ativo estiver limpo, você notará vazamentos muito mais rapidamente. As inspeções visuais são mais fáceis e os problemas se tornam detectáveis mais cedo quando há menos coisas ao redor, bloqueando sua visão.
Coloque em ordem
Depois de se livrar de todas as coisas que você não precisa, você precisa organizar as coisas que você faz. Você precisa colocar ferramentas e materiais em locais que suportem seu fluxo de trabalho. Por exemplo, coloque as ferramentas na bancada na ordem em que você as usará. Se você nem sempre estiver usando as mesmas ferramentas na mesma ordem, posicione-as para que sejam fáceis de encontrar.
Uma grande vantagem disso é que fica muito fácil ver quando algo está faltando. Se todas as suas chaves estiverem dispostas ao longo de uma parede em ordem de tamanho, você saberá instantaneamente quando estiver faltando uma.
Basicamente, esta etapa é sobre “Um lugar para tudo e tudo em seu lugar”.

Brilho
Agora que você configurou tudo bem, você precisará lutar para mantê-lo assim. A etapa de brilho consiste em reservar um tempo regularmente para limpar e garantir que tudo esteja onde deveria estar. Durante a limpeza, você também deve inspecionar as ferramentas e máquinas para garantir que tudo esteja funcionando corretamente.
Padronizar
Aqui você vai dar um passo adiante para garantir que seu trabalho árduo não seja desfeito com o tempo, criando políticas formais e um cronograma definido para as três primeiras etapas. Por exemplo, você pode definir políticas sobre quem é responsável por quais áreas e depois agendar os últimos 15 minutos de cada turno para “brilhar”.
Sustentação/Autodisciplina
A gestão de cima para baixo pesada tende a funcionar até o gerente ir para casa para o dia. Para que o sistema 5S realmente funcione, você precisará da adesão dos funcionários. Nesta etapa, você pode organizar sessões de treinamento que ajudam os funcionários a entender os benefícios do sistema. Você também pode coletar informações de funcionários; os trabalhadores ficarão mais entusiasmados com a implementação de um sistema que ajudaram a desenvolver.
Agora que temos a base, vamos olhar para os oito pilares. Eles são um pouco menos interconectados que os 5Ss. Você pode fazer qualquer um sem os outros, e você pode fazê-los basicamente em qualquer ordem.
Oito pilares da Manutenção Produtiva Total
Se o TPM é o telhado e os 5Ss são a fundação, as próximas partes dos pilares ficam na fundação, sustentando o telhado.
Manutenção autônoma
Olhando para a frase agora, você pensaria que era sobre inteligência artificial em CMMS e robôs pensantes. Mas lembre-se de que o sistema foi formalizado na década de 50 e, na época, referia-se à prática dos operadores assumirem a responsabilidade pela limpeza de rotina, inspeção e lubrificação de seus equipamentos. Em vez do departamento de manutenção, os operadores eram responsáveis por todas as pequenas MPs associadas aos equipamentos.
Uma grande vantagem é aumentar o conhecimento dos operadores sobre as máquinas em que trabalham. É importante saber que a expectativa não é que eles se tornem especialistas. Pensando nisso em termos de possuir um carro, eles saberiam como verificar o óleo (mas não trocá-lo) e adicionar ar aos pneus. Então, se algo der errado com o equipamento, eles perceberão rapidamente. Além disso, por serem capazes de cuidar das pequenas coisas, os técnicos do departamento de manutenção, que são especialistas reais, gastam seu precioso tempo em reparos mais importantes e complexos. De volta à analogia do carro, seu mecânico deve verificar as vedações e ajustar a marcha lenta. Se você os fizer aspirar o banco de trás e colocar ar nos pneus, estará desperdiçando seu tempo e talento. Você também está desperdiçando seu dinheiro.
Manutenção planejada
Este é fácil de explicar. É apenas manutenção preventiva com outro nome.
Um dos benefícios é que você pode planejar a manutenção preventiva em horários de pico. Em vez de fazer a linha parar no meio do primeiro turno com uma falha catastrófica, você pode cuidar de suas inspeções e substituições de rotina entre o segundo e o terceiro turno, quando as coisas estão relativamente mais tranquilas.
Outros incluem:
- Tempo de inatividade reduzido
- Aumento do tempo de atividade
- Controle de estoque mais fácil
- Menos ordens de serviço sob demanda
Manutenção de qualidade
Uma grande parte deste é a análise de causa raiz. Em vez de apenas corrigir um problema, você também descobre o que o causou para poder evitá-lo no futuro.
Normalmente, você ouvirá as pessoas falando sobre os 5 porquês ao fazer esse tipo de análise. É importante lembrar que não existem 5 Porquês. Em vez disso, a ideia é perguntar “por que” cinco vezes para chegar à raiz do problema. E precisamos encontrar a raiz; caso contrário, estamos apenas perdendo nosso tempo trabalhando em uma lista interminável de sintomas recorrentes.
Por exemplo, digamos que o problema é que seu carro não liga.
Um:“Por que o carro não pega?”
Resposta:A bateria está descarregada.
Dois:“Por que a bateria está descarregada?”
Resposta:O alternador não está funcionando.
Três:“Por que não estava funcionando?”
Resposta:O cinto estava quebrado.
Quatro:“Por que o cinto quebrou?”
Resposta:Já passou da sua vida útil.
Cinco:“Por que uma correia velha ainda estava no alternador?”
Resposta:O carro não estava sendo mantido de acordo com as recomendações do fabricante.
São sempre cinco? Nem sempre; cinco é apenas uma boa regra geral.
Melhoria focada
Honestamente, não sei por que isso é chamado de melhoria focada. Pode ser porque o trabalho é feito por pequenos grupos de funcionários. Talvez seja daí que vem a ideia de foco.
No entanto, faz muito sentido chamá-lo de “melhoria generalizada”. As equipes podem ser compostas por funcionários de cima e para baixo na escada corporativa. Outras duas palavras importantes são incremental e proativo. O progresso não acontece em trancos e barrancos gigantes. Em vez disso, pequenas mudanças são feitas constantemente, sendo analisadas e testadas. Além disso, as equipes estão procurando melhorar os processos antes que surjam problemas.
Gerenciamento antecipado de equipamentos
Quando é mais caro operar uma máquina? Está perto do fim de sua vida útil? Isso faz sentido porque é quando você provavelmente terá muitos reparos caros.
Mas também é caro logo no início. Tem o custo de instalação. Depois, há o custo das avarias causadas por erro do operador. Lembre-se, novas máquinas levam tempo para descobrir. E também leva tempo para descobrir como corrigi-los, então qualquer trabalho feito logo após o lançamento será um pouco lento. E tempo é dinheiro.
O gerenciamento inicial de equipamentos tenta antecipar esses custos trabalhando com operadores e departamentos de manutenção para desenvolver máquinas fáceis de consertar e fáceis de usar. Algo tão simples quanto a colocação de painéis de acesso pode economizar inúmeras horas ao longo da vida útil de um ativo ou equipamento.
Educação e treinamento e TPM administrativo e de escritório
Para economizar tempo e espaço, vamos combinar esses dois em um. Basicamente, a ideia aqui é difundir os conceitos e práticas do TPM entre a equipe de linha de frente e de escritório. Ao garantir que todos conheçam os conceitos, você aumenta suas chances de aplicá-los.
Condições ambientais de saúde e segurança
Aqui está outro que é fácil de adivinhar apenas olhando para o nome. As equipes trabalham juntas para aumentar a segurança e reduzir o risco nas instalações. Não apenas as máquinas ficam mais seguras com proteções e interruptores de interrupção, mas também os operadores e técnicos ficam mais seguros com proteção pessoal, como capacetes.
O que tudo isso significa para mim?
Pode ser pouco ou muito. Embora você precise abraçar todos os aspectos do TPM para obter o máximo benefício, também é possível vê-lo como um restaurante buffet. Quando se trata de software de manutenção preventiva, pegue o que lhe agrada e não se preocupe com o resto.
Por exemplo, da próxima vez que sua empresa estiver planejando investir em novos ativos ou equipamentos, você pode garantir que o departamento de manutenção tenha uma palavra a dizer no processo de seleção. Ou, como outro exemplo, você pode aplicar todos ou alguns dos 5Ss na sala onde guarda suas peças sobressalentes. Cabe a você encontrar e aplicar as ideias que funcionam melhor para sua situação atual.
Você também pode simplesmente adotar o espírito da Manutenção Produtiva Total, que é a ideia de que o progresso contínuo é possível e que é mais provável que você tenha sucesso quando diferentes departamentos trabalham juntos.
Tecnologia industrial
- Circuitos do divisor atual e a fórmula do divisor atual
- Estudo de caso de manutenção produtiva total
- As diferenças entre os despachantes aduaneiros do México e dos Estados Unidos
- Quais são as diferenças entre manutenção e reparos?
- Qual é a diferença entre a Indústria 4.0 e a Indústria 5.0?
- Manutenção produtiva total e IoT industrial
- Diferenças entre manutenção preventiva e corretiva
- Manutenção Produtiva Total:uma alavanca de desempenho?
- As diferenças entre fresamento CNC e torneamento CNC
- Torneamento e Fresamento CNC:Você Entende a Diferença Entre Eles?