Linguagem de manutenção baseada na condição de navegação com sucesso
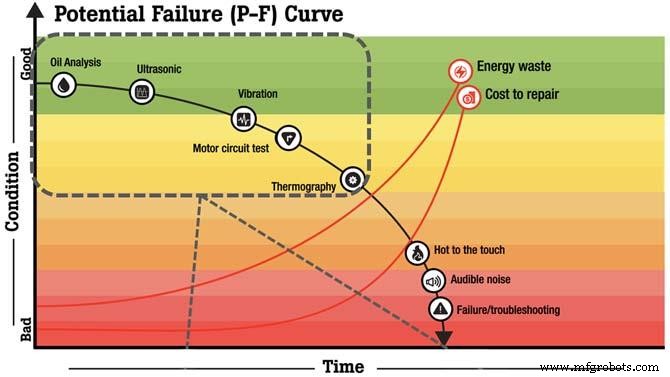
A estratégia de confiabilidade de manutenção ideal não é uma abordagem de tamanho único. Para ter o maior impacto, você deve analisar cada ativo e traçar o caminho que produzirá os melhores resultados para sua organização. Os profissionais de manutenção estão se voltando cada vez mais para técnicas de manutenção preditiva (PdM) e monitoramento de condição (CdM) para ajudá-los a alcançar o sucesso nesta jornada.
Para navegar com eficácia no cenário de manutenção, primeiro precisamos usar a linguagem correta. A manutenção preditiva (PdM) e o monitoramento de condição (CdM) são técnicas e ferramentas de manutenção dentro de uma estratégia de manutenção baseada em condição (CBM). Essas técnicas e ferramentas são usadas para detectar sintomas de falhas potenciais do equipamento; eles não são estratégias em si.
A manutenção baseada em condição reúne informações de condição de ativos de manutenção preditiva e técnicas de monitoramento de condição para determinar o momento ideal para realizar a manutenção para condições atenuantes que levam à falha.
O objetivo da manutenção baseada em condições é garantir que cada ativo esteja disponível quando solicitado e evitar realizar a manutenção muito cedo ou muito tarde na curva P-F. A ideia é mover para a esquerda na curva P-F, detectando falhas potenciais mais cedo ou mais tarde.
É aí que está o desafio. Encontrar o momento ideal para a manutenção tem confundido os profissionais de manutenção há décadas.
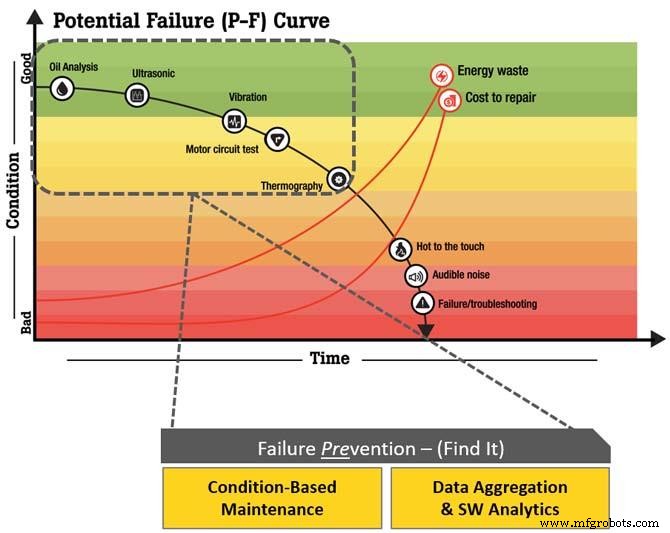
Mudança para uma mentalidade da indústria 4.0 (IIoT)
Até anos recentes, as estratégias de manutenção eram principalmente uma combinação de direcionada pelo tempo e execução até a falha. As decisões de manutenção foram amplamente baseadas em técnicas baseadas em observação humana e captura empiricamente de informações de saúde de ativos após o fato.
As instalações esperariam até que um motor, bomba ou transportador falhasse antes de agir. Na época, era praticamente a única escolha que eles tinham, porque as ferramentas e os dados não estavam prontamente disponíveis para encontrar com segurança as condições adversas com rapidez suficiente para evitá-las.
A ascensão da automação e dos dados digitais alinhados com o Industry 3.0 forneceu às equipes de manutenção métodos de observação tecnológica para ajudá-los a prever as condições que podem resultar em falha do ativo. Entre no mundo do software de sistema de gerenciamento de manutenção computadorizado (CMMS). Isso permitiu que eles estabelecessem uma estratégia digitalizada de manutenção preventiva baseada no tempo (PM) para cada ativo.
Os profissionais de manutenção mediam regularmente os indicadores-chave em equipamentos críticos para descobrir as falhas potenciais e, em seguida, agendavam o tempo de inatividade para reparar ou substituir componentes em um cronograma definido (muitas vezes especificado pelo fabricante do equipamento original), independentemente da condição real do ativo. Isso geralmente reduzia a taxa de falha, mas era trabalhoso e caro devido ao tempo de inatividade adicional e, às vezes, substituição desnecessária de componentes.
Agora, à medida que avançamos com a Indústria 4.0 e os sistemas autônomos inteligentes dentro da Internet das Coisas Industrial (IIoT), muitas instalações estão usando dados de condição de ativos em tempo real (ou quase em tempo real) para otimizar as atividades de manutenção.
Essa estratégia de manutenção baseada em condições envolve a captura de dados de uma variedade de fontes, incluindo sensores, ferramentas de diagnóstico portáteis, SCADA e outros sistemas de aquisição de dados. Os dados são agregados, analisados e transformados em inteligência acionável por meio de um CMMS, que então direciona os recursos de manutenção onde são mais necessários. Portanto, em vez de apagar incêndios, os profissionais de manutenção podem trabalhar na digitalização de processos.
Manutenção preditiva? Monitoramento de condição? Qual é a diferença?
A manutenção preditiva e o monitoramento de condição são semelhantes, pois ambos usam métodos de observação tecnológica para capturar dados de condição de ativos. Além disso, ambos são participantes completos desses métodos, pois estão totalmente imersos no ambiente.
As diferenças entre a manutenção preditiva e o monitoramento de condição são mínimas; eles são, na verdade, complementares. Portanto, em vez de escolher um ou outro, a maioria dos programas de manutenção os combina para fornecer um quadro de confiabilidade de manutenção mais abrangente.
Juntas, as técnicas de manutenção preditiva e monitoramento de condição fornecem os meios para capturar e registrar os dados empíricos de que você precisa para tomar melhores decisões sobre onde aplicar os recursos de manutenção para obter o melhor retorno.
Manutenção preditiva
As ferramentas e técnicas de manutenção preditiva empregam tecnologia ultrassensorial, como termografia, análise de vibração, análise de óleo e medição de som ultrassônico, para obter um instantâneo da integridade do ativo. Como você está capturando um breve período de tempo, é importante também registrar o contexto operacional das leituras, como há quanto tempo o componente está em execução e outros dados operacionais que podem afetar (ou avaliar melhor) a integridade de seu desempenho.
Uma advertência sobre a manutenção preditiva é que ela não prevê a longevidade ou o ponto exato de falha funcional de um ativo. Em vez disso, ele fornece dados de observação tecnológica para ajudá-lo a programar a manutenção de um ativo com mais precisão, eficácia e responsabilidade fiscal para fornecer um grau mais alto de disponibilidade e garantia de capacidade.
Monitoramento de condição
As ferramentas e técnicas de monitoramento de condição também fornecem dados tecnológicos de observação; mas, em vez de apenas capturar um instantâneo, eles coletam dados de integridade de ativos contínuos por meio de sensores e outros sistemas de aquisição de dados.
As técnicas de monitoramento de condição são ideais para ativos de difícil acesso ou em ambientes perigosos. Instalar sensores para detectar vibração excessiva ou superaquecimento do rolamento, ou problemas de qualidade de energia do motor, fornece informações críticas sobre a condição dos ativos sem colocar os funcionários em risco ou exigir paradas de produção.
Dependendo do sistema, os dados podem ser coletados em intervalos que variam de segundos a horas e dias. A ascensão da IIoT, os avanços na tecnologia de sensores e as reduções nos custos estão fazendo com que o volume de dados cresça a uma taxa exponencial. Aplicar inteligência artificial e aprendizado de máquina a esse volume crescente de dados de condição de tendência está ajudando os profissionais de manutenção a identificar com mais precisão o ponto ideal na curva P-F para aplicar medidas preventivas.
Mitigando Falhas Aleatórias
As falhas aleatórias são classificadas como tal porque resultam de causas desconhecidas. Uma das áreas em que as ferramentas e técnicas de manutenção preditiva e monitoramento de condições têm maior impacto é na identificação das causas raiz de falhas aleatórias.
Isso significa que os profissionais de manutenção devem observar tudo, de um ponto de observação tecnológica, como vibração, termografia e qualidade de energia, entre outros. Executar todas essas inspeções usando atividades de manutenção orientadas pelo tempo repetitivas pode consumir muito tempo e recursos.
Agora, a manutenção preditiva e as técnicas de monitoramento de condição podem frequentemente identificar condições que levam a falhas aleatórias, classificá-las na curva de falha adequada, resolver a causa com mais eficácia e, em seguida, aplicar a estratégia de manutenção atenuante correta.
Ao ajudar os profissionais de manutenção dessa forma, essas técnicas podem ajudar a eliminar muitas falhas anteriormente classificadas como aleatórias. Em termos simples, não sabemos o que não sabemos. Usar dados de observação tecnológica derivados de manutenção preditiva e técnicas de monitoramento de condição ajuda a tornar o desconhecido conhecido para que possamos mover a curva P-F ainda mais para a direita e, assim, ganhar mais tempo operacional entre as falhas.
Desenvolvimento de uma estratégia de ação preventiva eficaz
A progressão das estratégias de manutenção tende a passar da manutenção direcionada pelo tempo para a manutenção direcionada para a condição e (eventualmente) para a manutenção direcionada pelos dados. Mas nem todo ativo precisa seguir esse caminho.
A verdade é que a maioria das instalações usa uma combinação dessas estratégias de manutenção com base na criticidade e no custo do ativo em questão. Embora a tendência seja para estratégias de manutenção baseadas em condições e direcionadas por dados, muitas organizações desenvolvem um plano de ação preventiva híbrido que inclui tudo, desde procedimentos de manutenção direcionados por tempo até procedimentos de manutenção direcionados por dados. O segredo é encontrar a combinação certa.
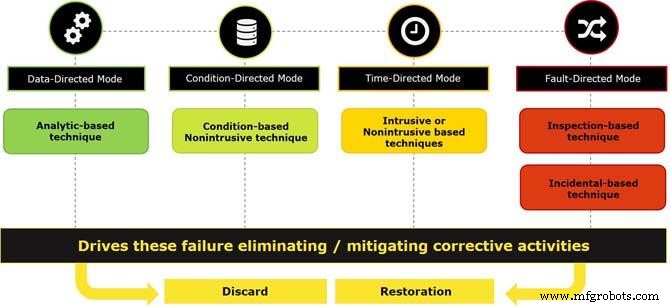
Embora a manutenção orientada pelo tempo tenha caído em desuso nos últimos anos, há casos em que o descarte programado ou as tarefas de restauração associadas à manutenção preventiva tradicional são mais eficazes. Para aplicações de missão crítica, onde uma falha pode causar danos físicos ou ambientais generalizados, como no processamento de petróleo e gás ou usinas nucleares, a combinação de estratégias de manutenção baseadas em condições com direcionadas por dados é uma abordagem preferida.
Após a criticidade do ativo, o orçamento e a disponibilidade de recursos humanos e tecnológicos desempenham papéis essenciais na decisão de qual técnica de manutenção usar.
Você não quer "correr atrás de um centavo com um dólar" implantando técnicas de manutenção preditiva e monitoramento de condição quando as abordagens direcionadas ao tempo padrão - ou mesmo executar até a falha - são mais eficazes. Em alguns casos, é mais barato e rápido substituir um ativo do que detectá-lo ou conduzir MPs regulares nele.
Igualmente importante é a sensibilidade ao tempo e a frequência de coleta dos dados de condição do ativo. Por exemplo, um modo de falha de rolamento com uma curva P-F de seis meses pode não precisar que dados de condição sejam coletados a cada minuto, hora ou segundo. Talvez semanalmente esteja bom. Por outro lado, esse mesmo rolamento em uma operação de missão crítica, como uma usina nuclear, pode precisar de monitoramento constante.
Principais considerações ao projetar uma estratégia de manutenção eficaz
Criar a melhor estratégia de manutenção para sua organização é um processo de decisão financeira e logística. Aqui estão alguns fatores importantes a serem considerados:
-
Decida se é mais barato e rápido substituir um ativo de vez em quando do que enviar um profissional de manutenção para verificá-lo em intervalos regulares.
-
Determine quais ativos são tão críticos para manter as coisas em movimento que o custo de adicionar monitoramento de condição vale a pena, não importa o custo.
-
Lembre-se de que há uma diferença entre estratégias e técnicas e ferramentas :
-
Manutenção baseada em condição (CBM), manutenção centrada em confiabilidade (RCM), manutenção baseada em confiabilidade (RBM), manutenção projetada (DOM) e até mesmo operação até a falha (RTF) são todas estratégias.
-
A manutenção preditiva e o monitoramento de condições descrevem técnicas e ferramentas usado na estratégia de manutenção baseada em condições .
-
Direcionado pelo tempo, direcionado pela condição e direcionado pelos dados são classificações procedimentais. Eles classificam as tarefas que os profissionais de manutenção implantam em um plano de ação preventiva para eliminar e / ou mitigar os modos de falha.
-
Ferramentas de manutenção baseadas em confiabilidade, como modo de falha e análise de efeitos (FMEA) ou modo de falha, efeitos e análise de criticidade (FMECA), ajudam a determinar as estratégias de manutenção mais prudentes e etapas de procedimento para identificar, mitigar ou eliminar as possíveis causas de falha .
No final, dois ROIs devem ser considerados. Um é o tradicional retorno sobre o investimento com o aumento da eficiência com os recursos existentes. O outro é o seu retorno à integridade. Como um profissional de manutenção, sua integridade - e a de toda a organização - gira em torno da manutenção da disponibilidade de ativos e garantia de capacidade. As ferramentas, técnicas e estratégias de manutenção que você escolher devem dar suporte a esse objetivo.
Sobre o autor
Gregory Perry, CMRP, CRL, é consultor sênior de garantia de capacidade da Fluke Reliability. Ele é um Líder Certificado de Confiabilidade com quase duas décadas de experiência em manutenção e melhores práticas operacionais e tem uma ampla base de experiências em MRO e depósitos, princípios de manutenção de classe mundial e consultoria e liderança em CMMS de classe mundial. Além de fornecer serviços de implementação e consultoria para clientes, Perry também apresenta sessões de melhores práticas de manutenção em conferências líderes do setor e é autor de vários webinars online de melhores práticas.
Manutenção e reparo de equipamentos
- Navegando na modernização da manutenção e gestão de instalações
- Como a integração com SensrTrx ajuda os clientes Fiix a conquistar a manutenção baseada em condições
- Estratégia e soluções do Exército para manutenção baseada em condições
- Melhorando a manutenção proativa com monitoramento de lubrificação em tempo real
- GE, Boeing implementa o padrão de manutenção com base na condição
- Navegando na limitação de capacidade com sistemas de manutenção digital
- A manutenção baseada na condição é adequada para o seu equipamento eletrônico industrial?
- Os fundamentos e benefícios da manutenção baseada em condições
- Manutenção baseada em condições:o que é e suas vantagens
- Estratégias de manutenção baseadas em condições minimizam falhas de equipamentos