Deposição de vapor químico aprimorada por plasma de acetileno em catalisadores bimetais codificados, aumentando a continuidade da folha de grafeno sob condições de crescimento a baixa temperatura
Resumo
Aqui, relatamos um novo método para a síntese de baixa temperatura de grafeno monocamada a 450 ° C em um catalisador de Ni-Au bimetal policristalino. Neste estudo, a síntese de deposição química de vapor de grafeno em baixa temperatura foi realizada a 450 ° C em Ni-Au codificado, que mostra a formação de grafeno em monocamada bem-sucedida sem um processo de recozimento extra. Os resultados experimentais sugerem que a codeposição do feixe de elétrons do catalisador bimetálico é o procedimento chave que permite a eliminação do recozimento pré-crescimento a alta temperatura do catalisador antes da síntese do grafeno, um processo indispensável, utilizado em relatórios anteriores. A formação foi ainda melhorada pelo crescimento assistido por plasma no qual o plasma acoplado indutivamente ioniza os precursores de carbono que interagem com o catalisador Ni-Au codificado de 50 nm de espessura a 450 ° C. Essas condições de crescimento combinadas aumentam drasticamente a uniformidade da folha de grafeno e a conectividade de área de 11,6% para 99%. Estes parâmetros de fabricação permitem a formação de grafeno que muda de um modelo de crescimento baseado em difusão em massa para uma reação baseada em superfície. A técnica relatada aqui abre a oportunidade para o crescimento de grafeno em baixa temperatura para uso potencial em futuras aplicações CMOS.
Introdução
Já se passaram mais de 10 anos desde o isolamento do grafeno [1], uma única camada de átomos de carbono em uma rede hexagonal; no entanto, este material 2D exclusivo ainda precisa ser incorporado industrialmente a um nível em que esteja beneficiando os bens de consumo. O grafeno é um material especialmente promissor para a indústria de semicondutores devido às suas notáveis propriedades eletrônicas [2, 3]. Como uma barreira de difusão atomicamente fina [4], o grafeno é um recurso poderoso na corrida para criar espaçamentos de transistores cada vez mais pequenos e dar continuidade ao reinado da Lei de Moore. No entanto, suas aplicações na indústria de semicondutores foram seriamente prejudicadas pelas altas temperaturas geralmente exigidas para sintetizar o grafeno - na faixa de 800 ° C ~ 1000 ° C [5] - e pelo fato de que o processo de transferência de grafeno é limitado a geometrias planas . O crescimento direto do grafeno em circuitos integrados contornaria o processo de transferência do grafeno, outro processo destrutivo, de um catalisador de crescimento para o dispositivo. Atualmente, é possível crescer em catalisadores de Cu e Ni (metais comuns em circuitos integrados), mas estes requerem altas temperaturas de crescimento [5], o que pode danificar as estruturas já existentes de um circuito integrado. Muita pesquisa tem sido focada na redução das temperaturas de síntese de grafeno e tem havido um sucesso recente. Weatherup et al. [3] mostraram que é possível cultivar grafeno a 450 ° C adicionando uma camada termicamente evaporada de 5 nm de Au no topo de um catalisador de Ni policristalino de 550 nm de espessura depositado por pulverização catódica, mas um pré-recozimento de 600 ° C de as camadas de Au e Ni são necessárias para produzir uma liga de Ni-Au. Um mecanismo proposto é que a adição de Au ao catalisador de Ni auxilia na limitação da absorção de carbono durante a exposição ao precursor de carbono e reduz a nucleação de grafeno e locais de difusão externa, como bordas de degraus e contornos de grão [3]. Embora tenha havido progresso para reduzir a temperatura de síntese para a faixa de 400-600 ° C [3, 6, 7], os impactos prejudiciais da transferência da folha de grafeno também devem ser superados. Crescimento direto em Si ou SiO 2 é outro alvo desejado para folhas de grafeno, mas isso não foi relatado na região de 400 ° C ~ 500 ° C necessária para processos semicondutores de fim de linha (BEOL). Enquanto crescimento direto de grafeno em Si ou SiO 2 ainda não foi alcançado, a síntese de grafeno em catalisadores mais finos representa um passo substancial em direção a este objetivo. Em um catalisador mais fino, a camada de grafeno resultante está cada vez mais perto do substrato alvo. Isso cria o potencial para desenvolver um processo de transferência que é menos prejudicial ao grafeno, minimizando a quantidade de manipulação manual do grafeno devido à sua proximidade com o substrato alvo. Embora o grafeno seja comumente sintetizado usando técnicas de deposição química de vapor (CVD), a adição de um plasma remoto pode ajudar a reduzir as temperaturas de síntese. O crescimento do plasma energiza os gases precursores por meio da ionização, superando a energia térmica que é perdida ao crescer na faixa de 400 ° C ~ 500 ° C em comparação com a faixa de 800 ° C ~ 1000 ° C. As vantagens de um plasma acoplado indutivamente remoto são duas:o plasma é criado longe do catalisador de crescimento, o que reduz o dano do bombardeio de íons na superfície de síntese, e o plasma é produzido por meio de bobinas de indução que estão fora da câmara de crescimento de grafeno, onde o catalisador substrato está localizado. Em um sistema de plasma capacitivo típico, o estágio de síntese é entre duas placas de metal dentro da câmara de vácuo com um potencial elétrico entre elas que expõe a superfície de crescimento a qualquer material estranho da fonte de plasma. Usando a bobina de indução externa enrolada ao redor do tubo de fluxo de gás, ionizamos os gases precursores criando um campo eletromagnético alternado dentro do tubo. Isso remove completamente a fonte de plasma da câmara, o que não permite que materiais estranhos da fonte de plasma contaminem potencialmente o catalisador de crescimento. Aqui nós relatamos a síntese de grafeno monocamada (MLG) a 450 ° C usando deposição de vapor químico de plasma indutivamente acoplado (ICPCVD) em catalisador Ni-Au fino (50 nm) codificado pela técnica de evaporação por feixe de elétrons.
Métodos Experimentais
Preparação do catalisador
Dois métodos de preparação de catalisador foram usados para este estudo para comparar os efeitos de Ni-Au versus Ni puro, e todas as deposições de catalisador foram realizadas em uma ferramenta Kurt J. Lesker Physical Vapor Deposition (PVD) separada. Para experimentos de crescimento de grafeno de Ni puro, o catalisador de Ni foi preparado por pulverização catódica de magnetron sobre SiO 2 / Si wafers para a espessura desejada (50 nm). Para a preparação do catalisador Ni-Au, pelotas de Au e Ni foram primeiro misturadas por aquecimento de feixe de elétrons, onde o sistema de feixe de elétrons direciona um feixe de elétrons para um cadinho contendo pelotas de metal de Au e Ni. A deposição de feixe de elétrons foi preferida aqui devido ao fato de permitir o controle preciso da porcentagem em peso de Au na mistura. O feixe de elétrons aquece e mistura as pelotas, e a mistura resultante é então codificada por evaporação em SiO 2 / Si wafers como esquematicamente ilustrado na Fig. 1. Este processo de liga remota produz um catalisador que expõe Ni ao precursor de hidrocarboneto enquanto implanta Au no volume de Ni e na superfície do catalisador. A preparação do catalisador que foi usada na literatura relatada [3] deposita metais usando um método de estratificação no qual vários metais são depositados uns sobre os outros. As camadas devem então ser recozidas a 600 ° C para formar uma liga ou mistura. A técnica de codeposição aplicada neste estudo teve como objetivo eliminar o processo de recozimento do catalisador e obter a formação de grafeno em baixa temperatura usando um catalisador de liga de Ni-Au pré-fabricado antes da deposição. A natureza do estado pré-misturado do catalisador codificado evita a necessidade de um pré-recozimento de mistura para formar um catalisador válido. Para fins de simplicidade neste relatório, chamamos esse processo de deposição de catalisador de “codeposição” porque o Ni e o Au são codificados no substrato. Para nossos experimentos, optamos por depositar uma liga de 1% em peso de Au que se mostrou mais eficaz na síntese de grafeno em baixa temperatura [3]. Ambos os catalisadores de Ni e Ni-Au puros foram depositados em uma espessura de 50 nm devido ao nosso interesse no crescimento de catalisadores mais finos. Descobrimos que essa espessura está dentro dos intervalos relatados anteriormente para crescimento à base de níquel [8, 9], embora estes estivessem em temperaturas muito superiores a 450 ° C, ainda que nosso catalisador Au-Ni de 50 nm é uma ordem de magnitude mais fino do que o relatado Crescimento de grafeno em multicamadas (MLG) a 450 ° C [3].
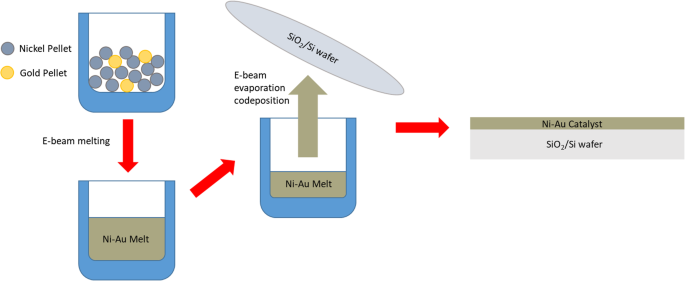
Diagrama esquemático da técnica de codeposição de feixe de elétrons no qual vemos as pelotas de Ni e Au são remotamente misturadas em um cadinho antes de serem evaporadas no substrato. Este processo serve para remover completamente a necessidade de recozimento pré-crescimento usado na literatura anterior e permite uma síntese completa de grafeno em monocamada a 450 ° C
Crescimento do grafeno
Nossos regimes de crescimento de grafeno foram realizados em uma câmara ICPCVD de parede fria construída sob encomenda. As temperaturas foram medidas por meio de um medidor de termopar afixado à superfície da amostra para detectar temperaturas de superfície precisas in situ. Os gases foram lançados na câmara através de um chuveiro. As amostras foram colocadas em um palco radiante aquecido cerca de 25 cm abaixo do chuveiro de gás. Os catalisadores preparados foram inseridos na câmara ICPCVD e bombeados a uma pressão de base de 1 × 10 −6 Torr após o qual H 2 foi introduzido a 15 sccm quando a amostra foi aquecida à temperatura do processo de 450 ° C. Uma vez que as amostras alcançaram a temperatura do processo, o H 2 o fluxo foi interrompido e a câmara foi purgada usando Ar. Depois que a pressão de base foi restabelecida, Ar foi interrompido e C 2 H 2 foi voado a 0,1 sccm trazendo a pressão da câmara para 6 × 10 −6 Torr. Para o crescimento intensificado por plasma, a potência de RF variando de 0 a 10 W foi introduzida para diferentes amostras de crescimento. Dez watts foram a potência de RF mais alta que poderia ser fornecida ao mesmo tempo em que se mantinha um plasma indutivamente acoplado (ICP) remoto e estável desde C 2 tão baixo H 2 à pressão, a resistência do gás é muito alta e a corrente induzida começa a fluir em outro lugar com potências de plasma mais altas. Uma vez que a duração de crescimento desejada foi alcançada (7 min para crescimentos CVD e 30 s para crescimentos ICPCVD), C 2 H 2 o fluxo foi interrompido, seguido por outra purga de Ar para liberar os gases restantes do processo para fora da câmara. O aquecedor da amostra foi então desligado, permitindo que a amostra esfriasse até a temperatura ambiente.
Caracterização do grafeno
Após a síntese, as amostras de grafeno foram revestidas por rotação com PMMA. As bolachas foram então colocadas em FeCl 3 para gravar o Ni, seguido por iodo / iodeto de potássio (40 mL H 2 O / 4 g KI / 1 g I 2 ) solução para gravar o Au restante. O filme resultante foi então transferido para limpar SiO 2 / Si wafers, e o PMMA foi removido com acetona. A análise espectroscópica de grafeno foi realizada usando um espectrômetro Horiba Jobin Yvon HR800 UV Raman com um laser de 532 nm para identificar os principais picos espectrais esperados para filmes finos de grafeno. As razões de intensidade de pico D:G e D:D '( I D:G , eu D:D ’ ) fornecem informações sobre a densidade e o tipo de defeito no grafeno, respectivamente. O 2D:intensidade de pico G ( I 2D:G ), bem como a largura total do pico 2D na metade do máximo (FWHM) fornecem informações sobre o número total de camadas de grafeno. Monocamadas de grafeno sem defeitos I D:G de aproximadamente 0, no entanto, quando os defeitos estão presentes um I 2D:G > 1.0 e FWHM 2D <100 cm −1 são indicativos de grafeno monocamada [10]. A imagem de superfície foi realizada usando um Zeiss Sigma VP FEG SEM configurado com um detector de elétrons secundário In-Lens, que permite a visualização dos tamanhos de grãos e morfologias do catalisador após a formação do grafeno. ImageJ foi usado para realizar cálculos de porcentagens de folha maiores que I 2D:G =1 que sugere a porcentagem de grafeno monocamada produzida, e os picos Raman foram ajustados e analisados usando um programa escrito em R para identificar razões de pico e FWHM.
Resultados e discussão
Aqui, é mostrado que o uso de codeposição de Ni-Au como uma técnica de preparação de catalisador erradica o processo anteriormente necessário de pré-recozimento de 600 ° C para ligar o catalisador de Ni-Au, comparando com um catalisador de controle apenas de Ni de base e com o anterior relatórios [3]. Para comparar os efeitos do Ni-Au com o Ni puro, a Fig. 2 exibe um espectro Raman médio de grafeno transferido crescido via CVD térmico a 450 ° C com um C 2 de 7 min H 2 exposição em (a) Ni puro e (b) o catalisador de Ni-Au codificado sem recozimento, em contraste com a literatura anterior [3]. O modelo de crescimento de catalisador de Ni puro CVD aceito para grafeno [11] sugere que os precursores de hidrocarbonetos são absorvidos no volume de Ni e desidrogenados, já que C mostra alta difusão em Ni. Durante o resfriamento, os átomos de C individuais se difundem do volume de Ni para a superfície e formam o grafeno [12]. A Figura 2a exibe um filme fino de carbono amorfo e o espectro correspondente (inserção) que é típico para crescimento catalisado por Ni puro em baixa temperatura. O catalisador de Ni policristalino contém muitas bordas de degrau e limites de grão na superfície como resultado da deposição de pulverização catódica que agem como locais que têm uma alta probabilidade de difusão de C e, portanto, como locais de nucleação de grafeno durante o resfriamento, o que permite que os átomos de C se difundam do volume em muitos locais causando sobreposição. No entanto, com a adição de 1% em peso de Au, na Fig. 2b, uma melhoria drástica no espectro Raman é observada. O espectro mostra picos D, G e 2D bem definidos com I 2D:G =1.2 e FWHM 2D =48,5 cm −1 o que sugere a formação de grafeno monocamada com defeitos. Existe um I relativamente grande D:G =0,68 e um I correspondente D:D ’ =5,0, o que sugere que os tipos de defeito de vacância e incompatibilidade de rede estão presentes [13], no entanto, observe em ambas as Fig. 2a, b, filmes finos inteiros foram produzidos. Com base na literatura, o carbono não se difunde prontamente em Au [14], e isso sugere que o Au poderia reduzir o número de locais de nucleação de grafeno bloqueando bordas de degraus e contornos de grão [3] se localizado nessas regiões produzindo menos números de camada por limitando a absorção de C e difusão externa. Para ilustrar o mecanismo de crescimento para esta formação, a Fig. 3 mostra um conjunto de diagramas esquemáticos comparando os modelos de crescimento de Ni puro vs Ni-Au para crescimentos de CVD térmicos, onde a síntese típica de grafeno Ni desenvolve grafeno multicamadas devido à incapacidade de estrangular a absorção de C e difusão externa (Fig. 3a), porém a adição de Au ajuda no controle da absorção e difusão de C no Ni (Fig. 3b). Esses resultados mostram que a adição de Au é eficaz na produção de grafeno em baixas temperaturas, o que é consistente com os resultados relatados por Weatherup et al. [3]. Mais importante, no entanto, nossos resultados demonstram que o uso de codeposição elimina completamente o recozimento de 600 ° C necessário para produzir uma liga de Ni-Au, tornando esta uma síntese verdadeiramente de 450 ° C ligando remotamente o catalisador de Ni e Au antes da deposição em vez de durante o receita de crescimento.
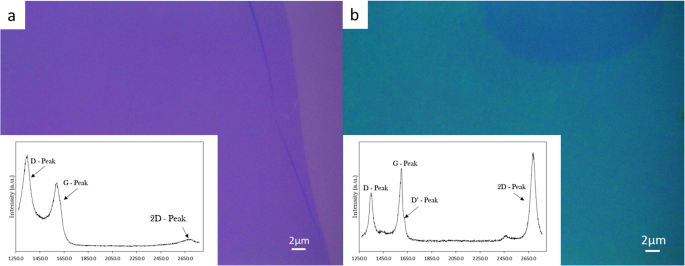
Imagens ópticas e espectros Raman (inserções) de a carbono amorfo como resultado de uma tentativa de síntese de grafeno por 7 min C 2 H 2 exposição em catalisador de Ni puro de 50 nm a 450 ° C e b síntese de grafeno bem-sucedida seguindo os mesmos parâmetros de a no catalisador Ni-Au codificado, observe a mancha escura no topo da imagem b é uma área de grafeno multicamadas e foi capturada para adicionar contraste e ajudar a identificar a área circundante da monocamada. Há uma melhoria óbvia criada pela adição de 1% em peso de Au, pois esta é a única variável alterada para permitir a mudança drástica do carbono amorfo para o grafeno. Rotulado em a são os principais picos usados para a caracterização do grafeno. Para b , calculamos eu 2D:G =1,2, FWHM 2D =48,5, eu D:G =0,68, e I D:D ’ =5.0
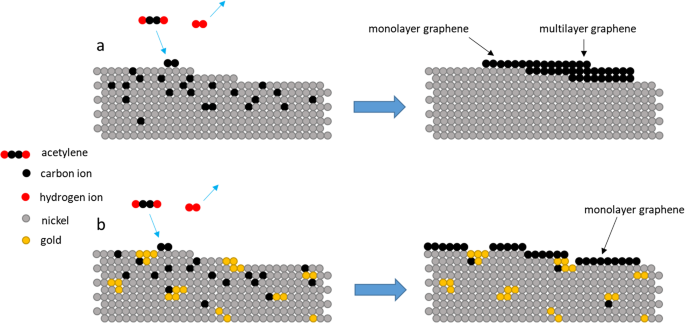
Diagrama esquemático do crescimento do grafeno em a catalisador de Ni puro em que o grafeno de poucas camadas (FLG) é produzido devido à absorção não controlada de C e difusão externa em locais de alta energia, como bordas de etapa em comparação com b síntese de Ni-Au codificada em que o Au atua como um limitador de absorção de C, bem como reduz os altos níveis de produção de grafeno, bloqueando pontos de nucleação, como bordas de degrau
Embora o Ni-Au codificado produza filmes de grafeno, é crucial ser capaz de produzir grandes áreas de grafeno contínuo e uniforme para aplicações práticas. Para resolver este problema, três crescimentos em Ni-Au codificado foram realizados para comparar os efeitos da incorporação de um plasma remoto com três diferentes potências de plasma no crescimento. A Figura 4a-c mostra um Raman I 2D:G mapa de grafeno crescido de Ni-Au codificado via ICPCVD (0 W, 5 W e 10 W respectivamente) com 30s C 2 H 2 período de exposição. A Figura 4a é um mapa Raman de síntese realizado sem a adição de potência de plasma de RF que exibe um padrão quadriculado que é o resultado de pequenas áreas de espessura alternada da camada de grafeno. A adição de potência de plasma RF de 5 W na Fig. 4b e 10 W na Fig. 4c mostra porções maiores de camadas mais uniformes conectadas exibidas por um aumento na área do uniforme I 2D:G , representado por grandes áreas de cores uniformes, com aumento da potência de RF. Isso mostra que a adição de plasma auxilia na criação de uma folha de grafeno maior e mais uniforme, que é ainda suportada pelo gráfico de dados na Fig. 4d. A tendência é que conforme o plasma RF é aumentado para 10 W, há um aumento em I 2D:G , uma diminuição em I D:G , e uma diminuição em FWHM 2D em que todos são significativos de grafeno monocamada. Para explorar visualmente a continuidade do filme fino de grafeno, a Fig. 5a mostra uma imagem SEM de grafeno pré-transferido crescido via 10 W ICPCVD, onde vemos uma folha de 15 μm de largura de grafeno de monocamada contínua (MLG) com algumas ilhas de grafeno de poucas camadas (FLG ) Há uma mancha visível na superfície na Fig. 5a, mas isso é atribuído à estrutura de grão subjacente do catalisador, uma vez que esta é uma imagem de grafeno crescido e nosso catalisador policristalino não foi removido ainda, o que é detalhado na Fig. . 5b, bem como correlacionar espectros Raman para o grafeno de multicamadas (MLG) e grafeno de poucas camadas (FLG) na Fig. 5c. Nossos resultados sugerem, como representado pela Fig. 6, que os íons C desidrogenados produzidos pelo plasma de RF alcançam a superfície do catalisador e atuam como locais de nucleação de alta energia para o crescimento e a semente. Embora haja absorção no Ni, esses íons C têm uma alta probabilidade de se ligar a íons C adicionais na superfície, produzindo dímeros e moléculas maiores que são muito menos propensas a serem absorvidas pelo catalisador de Ni. Uma vez que vemos maior uniformidade ao aplicar plasma ao crescimento, e não uniformidade no crescimento de CVD térmico, conforme exibido na Fig. 4, isso sugere que, durante a síntese de ICPCVD, o catalisador não é superabsorvido para produzir grafeno multicamadas. Em vez disso, o crescimento foi deslocado para um mecanismo dominado pela superfície. Este movimento em direção a um crescimento dominado pela superfície também apóia nossa abordagem de utilizar um catalisador fino que saturaria ainda mais rápido do que os catalisadores mais espessos.
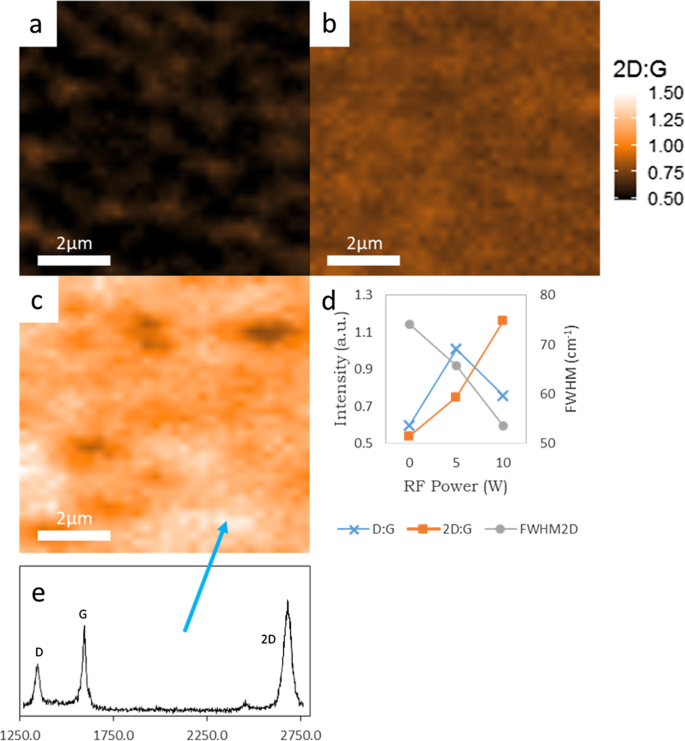
Mapas Raman de grafeno cultivado em Ni-Au codificado de 50 nm com 30s C 2 H 2 tempo de exposição via a CVD, b ICPCVD com plasma 5 W e c ICPCVD com plasma de 10 W. O eu 2D:G , eu D:G e FWHM 2D para cada potência de plasma são mostrados em d onde é aparente que 10 W serve como o melhor devido ao seu I mais alto 2D:G , inferior I D:G , e menor FWHM 2D em comparação com os outros, e um espectro representativo retirado da região mais brilhante de c é mostrado em e
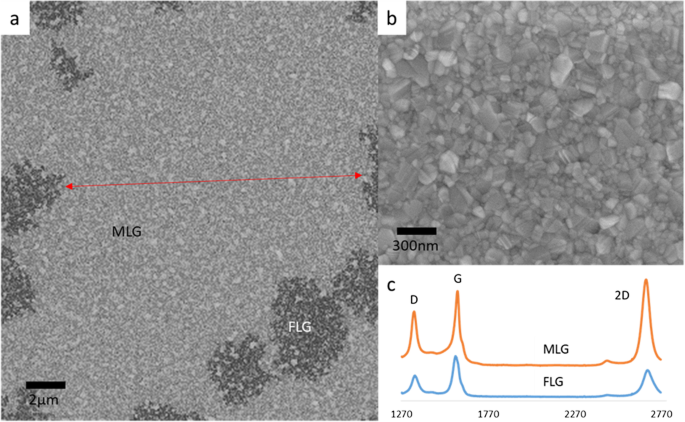
Imagens de microscópio eletrônico de varredura de grafeno conforme crescido em catalisador de Ni-Au codificado cultivado a 450 ° C via ICPCVD de 10 W que mostram a uma seção de 15 μm de largura de grafeno de monocamada contínua (MLG) (seta vermelha) com ilhas de grafeno de poucas camadas (FLG) (escuro) (espectros Raman médios correspondentes em c ) e b alta ampliação da área de grafeno monocamada onde o grafeno é formado na parte superior dos grãos de catalisador
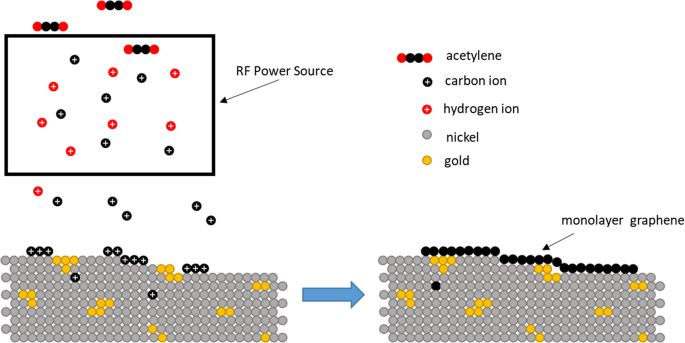
Diagrama esquemático do crescimento do ICPCVD no qual vemos uma mudança em direção a um mecanismo dominado pela superfície. Esta mudança é causada pela ionização de átomos de C que agem como locais de nucleação de grafeno de alta energia, uma vez que atingem a superfície do catalisador e permite o uso de um catalisador mais fino, pois há menos absorção que leva à superprodução de grafeno durante o resfriamento
Os benefícios do ICPCVD sobre o CVD também podem ser vistos ao comparar a cobertura multicamadas (MLG). Um conjunto de amostras de ambas as sínteses de ICPCVD e CVD foi comparado e os resultados são mostrados na Fig. 7 que exibe mapas Raman de (a) crescimento de CVD de 7 min versus (b) crescimento de ICPCVD de 30s com potência de RF de 10 W em Ni codificado Au. Com base em nosso cálculo do mapa Raman, estimamos que o crescimento de CVD de 7 minutos exibe uma cobertura de 11,6% de I 2D:G > 1.0, enquanto o crescimento do ICPCVD dos anos 30, por outro lado, exibe uma cobertura de 99% de I 2D:G > 1.0. Isso sugere que o plasma desempenha um papel importante na conectividade e uniformidade do grafeno em um catalisador fino e evita a absorção de grandes quantidades de C no catalisador, em oposição ao crescimento de CVD em que a superabsorção de C leva à superprodução de grafeno e, portanto, menos uniformidade .
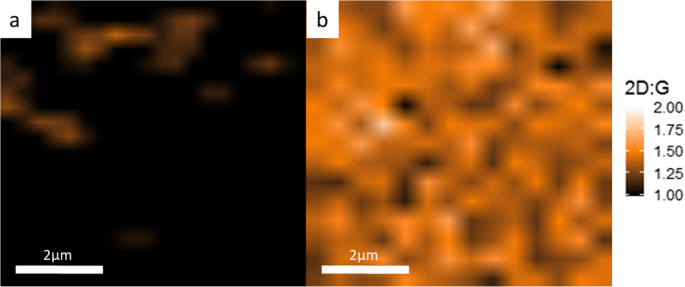
Mapas Raman mostrando I 2D:G > 1.0 para a Síntese CVD com 7 min de tempo de exposição versus b Síntese de 10 W ICPCVD com tempo de exposição de 30s. Ambos os crescimentos são de 450 ° C no catalisador Ni-Au codificado. A adição de plasma aumenta a uniformidade da camada de 11,6% ( a ) a 99% ( b )
Conclusões
Nós demonstramos a validade da codeposição como uma técnica única de preparação de catalisador que efetivamente remove a necessidade de recozimento para catalisadores de Ni-Au, pré-ligando remotamente o catalisador durante a evaporação de feixe de elétrons e produzindo um catalisador imediatamente capaz para crescimento de grafeno a 450 ° C. A adição de usar um plasma acoplado indutivamente durante o crescimento serve para aumentar a área de filme fino de grafeno e uniformidade de camada, mudando o processo de síntese para um mecanismo de superfície dominado que é benéfico quando catalisadores finos são usados para o crescimento. O estudo apresentado aqui demonstrou o progresso significativo do uso de CVD aprimorado por plasma e catalisador fino de Ni-Au codificado para cultivar grafeno com qualidade aprimorada em baixa temperatura. No entanto, os parâmetros de crescimento precisam ser ajustados e otimizados com relação às aplicações específicas. Por exemplo, o projeto e a otimização do catalisador para aumentar ainda mais o tamanho do grão de grafeno sob as condições de crescimento de baixa temperatura e o crescimento direto de grafeno nos substratos desejados. Essas são as questões que serão abordadas nas investigações em andamento.
Disponibilidade de dados e materiais
Todos os dados estão disponíveis com os autores por meio de uma solicitação razoável.
Abreviações
- 2D:
-
Bidimensional
- BEOL:
-
Fim da linha
- CVD:
-
Deposição de vapor químico
- FLG:
-
Grafeno de poucas camadas
- FWHM:
-
Meio máximo de largura total
- ICPCVD:
-
Deposição de vapor químico de plasma indutivamente acoplado
- MLG:
-
Grafeno monocamada
- PVD:
-
Deposição física de vapor
Nanomateriais
- O que é deposição de vapor químico?
- Tecnologias de Deposição de Camada Atômica Avançada para Micro-LEDs e VCSELs
- Investigações de Estruturas de Vacância Relacionadas ao Seu Crescimento na Folha h-BN
- Crescimento autocatalisado de nanofios de GaSb verticais em hastes de InAs por deposição de vapor químico orgânico-metálico
- As Nanofibras Hierárquicas de Poliamida 6-ZnO Antibacteriana Fabricadas por Deposição de Camada Atômica e Crescimento Hidrotérmico
- Propriedades fotocatalíticas de pós de TiO2 revestidos com Co3O4 preparados por deposição de camada atômica aprimorada com plasma
- Filme WS2 de área grande com grandes domínios únicos cultivados por deposição de vapor químico
- Avaliação de estruturas de grafeno / WO3 e grafeno / CeO x como eletrodos para aplicações de supercapacitor
- Redução do óxido de grafeno a baixa temperatura:Condutância elétrica e microscopia de varredura de força de sonda Kelvin
- Espectroscopia Raman de Grafeno Multi-Camada epitaxialmente cultivado em 4H-SiC por Joule Heat Decomposition