5 maneiras pelas quais as usinas de energia podem reduzir os custos indiretos de fabricação de equipamentos por meio do gerenciamento de manutenção
A falta de manutenção regular apresenta riscos significativos para as usinas, como riscos de segurança e avarias inesperadas que exigem reparos dispendiosos. As quebras de equipamentos também podem resultar em interrupções na produção de energia, o que afeta o resultado final. A manutenção de equipamentos no setor elétrico é complexa, dadas as muitas variáveis que podem impactar no desempenho dos equipamentos. Falhas em sistemas de controle, válvulas com vazamento, operação inadequada, exposição excessiva a cargas térmicas e até mesmo projeto defeituoso podem ter consequências caras se não forem detectadas e corrigidas precocemente.
Como resultado, o gerenciamento de manutenção é igualmente complexo, exigindo processos de gerenciamento robustos e personalizados para as necessidades exclusivas da planta. Embora não haja uma solução única para todos, um programa abrangente de gerenciamento de manutenção de usinas elétricas oferece economias substanciais nos custos indiretos de fabricação de equipamentos. Aqui está uma olhada em algumas das maneiras pelas quais as usinas de energia podem reduzir a sobrecarga de fabricação de equipamentos com um gerenciamento de manutenção eficaz.
Aprimorando a segurança da planta
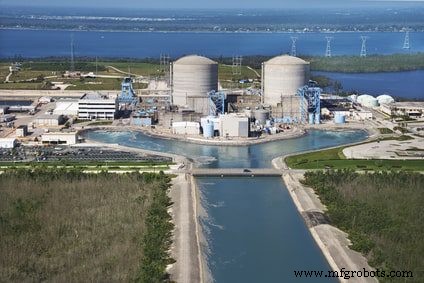
O mau funcionamento do equipamento da usina pode representar sérias preocupações de segurança. Embora trabalhar em uma usina seja inerentemente perigoso, a maioria das usinas prioriza a segurança – mas, apesar de tomar as precauções de segurança recomendadas, o mau funcionamento do equipamento tem sido associado a explosões, eletrocussão, incêndios e outros perigos. Em muitos casos, esses incidentes são atribuídos a fatores como a pressão da caldeira que excede amplamente sua pressão de operação, falhas nos mecanismos de desligamento de emergência ou operação inadequada, como trabalhadores que deixam de desligar uma unidade antes de realizar determinadas atividades de manutenção.
Embora o gerenciamento de manutenção não possa evitar todos os acidentes e lesões nas usinas, ele pode reduzir a probabilidade de incidentes resultantes de problemas de pressão operacional e outras variáveis, detectando esses problemas antes que eles atinjam um ponto de ruptura.
O valor da segurança da usina de energia excede em muito o valor em dólares, mas também há um benefício financeiro para a segurança. O custo de danos e limpeza pode ser significativo, e os acidentes também podem levar a custos de seguro mais altos. Isso sem mencionar o dano à reputação que a empresa sofrerá após um grande incidente.
Aproveitando o rastreamento de equipamentos para manter o controle das atividades de manutenção
A implementação de soluções de rastreamento de equipamentos, como etiquetas de código de barras, combinadas com uma solução CMMS, é a melhor maneira de garantir que os cronogramas e procedimentos regulares de manutenção preventiva sejam rigorosamente cumpridos. Os ativos de equipamentos são facilmente identificados por meio da digitalização de uma etiqueta de código de barras CMMS, permitindo que os trabalhadores iniciem ordens de serviço facilmente.
As etiquetas de código de barras também são usadas para identificar pontos de medição e atividades de medição de data e hora para monitoramento de condições, auxiliando as operações da usina para criar uma trilha de auditoria precisa das condições do equipamento e identificar flutuações de desempenho que podem indicar um problema iminente. As etiquetas LDAR e as etiquetas de purga de vapor podem ser usadas para detecção e reparo de vazamentos em ambientes de fabricação difíceis, simplificando o gerenciamento dos testes de detecção de vazamentos necessários e registrando informações adicionais sobre reparos de vazamentos. Ao alavancar soluções eficazes de rastreamento de equipamentos, as usinas de energia podem eliminar erros na identificação, marcação e monitoramento de possíveis pontos de vazamento em toda a instalação, evitando não conformidades e multas dispendiosas.
Manter os equipamentos com desempenho operacional máximo
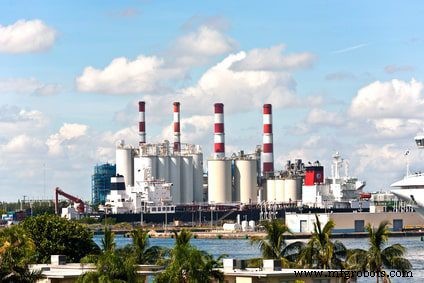
O objetivo do gerenciamento de manutenção é encontrar o equilíbrio que forneça o máximo benefício, ou saída, do equipamento, com o menor custo possível. Isso requer a identificação do nível aceitável de risco (o menor risco possível) para atingir determinados objetivos operacionais ou de produção.
Equipamentos que não estão operando com desempenho máximo não significam menos despesas gerais; na verdade, geralmente significa mais custos indiretos em termos de manutenção e reparos inevitáveis que serão necessários como resultado do estresse do equipamento. Mesmo que seu equipamento esteja se arrastando, os custos indiretos para mantê-lo funcionando são os mesmos que seriam se estivesse operando com desempenho máximo. A diferença é que você não está obtendo tanto disso, em termos de produção, o que significa menos receita.
O gerenciamento de manutenção ajuda os operadores de usinas a manterem-se atualizados sobre as atividades de manutenção preventiva, o que mantém os equipamentos operando com desempenho operacional máximo por mais tempo. Equipamentos que funcionam em níveis ideais significam que as usinas de energia estão mais aptas a cumprir as metas de produção, o que tem um impacto direto no resultado final da empresa.
Reduzindo avarias e interrupções de produção
A manutenção preventiva e o monitoramento da condição do equipamento permitem que os operadores identifiquem problemas de desempenho e tomem medidas para corrigi-los antes que se tornem grandes riscos de segurança ou interrompam a produção com uma falha total do equipamento.
A manutenção preventiva normalmente envolve procedimentos de manutenção planejados em intervalos definidos, independentemente da condição do equipamento. As peças são substituídas à medida que se aproximam do fim de sua vida útil, antes de atingirem um ponto de desgaste que prejudique o desempenho operacional. A desvantagem dessa abordagem de gerenciamento de manutenção é que ela pode levar a manutenção desnecessária, o que pode aumentar os custos gerais gerais do equipamento. Dito isto, a manutenção preventiva aumenta a segurança da planta.
A manutenção baseada em condições, por outro lado, requer monitoramento cuidadoso e contínuo dos ativos do equipamento para identificar defeitos antes que eles se tornem prejudiciais ao desempenho ou à segurança. As soluções CMMS e etiquetas de código de barras para monitoramento de condições tornam os rigorosos requisitos de monitoramento mais gerenciáveis para usinas de energia de todos os tamanhos.
Prolongamento da vida útil do equipamento
O equipamento que está operando em condições abaixo do ideal resulta em desgaste adicional de peças e componentes, bem como do ativo do equipamento como um todo. Ao permitir que o equipamento opere em condições de risco por longos períodos de tempo – uma caldeira operando sob pressão excessiva por várias semanas, por exemplo – essas condições podem sobrecarregar o equipamento e reduzir sua vida útil. Isso pode significar a substituição de um equipamento caro anos antes do prazo para substituição em circunstâncias normais.
O gerenciamento de manutenção também pode ajudar a fazer determinações de substituição versus reparos. Se um ativo de equipamento está chegando ao fim de sua vida útil esperada, reparos caros, peças de reposição ou componentes nem sempre fazem sentido financeiro. Ao ter um registro completo do histórico de manutenção de um ativo, desempenho ao longo do tempo, avarias, as usinas de energia podem estimar a vida útil restante prevista do ativo e tomar decisões mais inteligentes quando se trata de reparar ou substituir equipamentos.
Ao aproveitar as etiquetas de código de barras e uma solução CMMS para rastreamento de equipamentos, você obterá mais do seu programa de gerenciamento de manutenção. Como resultado, você se beneficiará de custos indiretos de fabricação de equipamentos mais baixos, obtendo o máximo desempenho de cada ativo, reduzindo avarias e reparos dispendiosos e estendendo a vida útil de seus ativos – tudo isso enquanto melhora a segurança de sua planta.
Tecnologia industrial
- 6 maneiras de reduzir custos de fabricação com impressão 3D
- Reduza os custos de manutenção com manutenção preditiva
- Três maneiras que as equipes de aquisição podem reduzir os custos da empresa
- A Importância da Manutenção de Equipamentos na Fabricação
- 8 passos para reduzir os custos de gerenciamento de manutenção
- 5 principais maneiras de reduzir os custos de manutenção de equipamentos
- 8 maneiras eficazes de reduzir o desperdício de fabricação
- 5 maneiras de reduzir os custos de fabricação
- O software de gerenciamento de equipamentos de cinco maneiras ajuda na manutenção preventiva de equipamentos
- Dicas para reduzir os custos de inatividade hidráulica