Siderurgia Verde
Fabricação de aço verde
A temperatura média anual da Terra está aumentando desde a revolução industrial. Isso se deve principalmente à queima de combustíveis fósseis que aumentam as emissões de dióxido de carbono (CO2) na atmosfera. Antes da revolução industrial, 280 ppm (0,028%) do ar atmosférico consistia em CO2, e isso aumentou para cerca de 413 ppm (0,0413%) no início de 2019. A Fig 1 mostra o aumento global da temperatura anual e da concentração de CO2 na Terra durante os últimos 800.000 anos. Os dados de CO2 atmosférico são fornecidos pela Administração Nacional Oceânica Atmosférica dos EUA (NOAA). Uma vez que não existem medições diretas, as respectivas informações foram derivadas de testemunhos de gelo através do Projeto Europeu de Extração de Gelo na Antártida (EPICA).
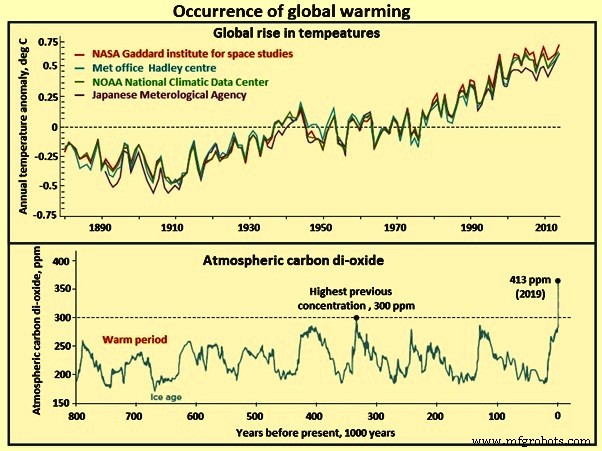
Fig 1 Ocorrência do aquecimento global
O aquecimento global, na verdade, é o resultado de “muito de uma coisa boa”. Sem a atmosfera, a superfície da Terra estaria praticamente congelada. À medida que a luz solar entra na atmosfera, ela é absorvida pelos oceanos e continentes, que se aquecem. Grande parte do calor é então irradiado de volta para o espaço na forma de luz infravermelha rica em energia. É aqui que entram os “gases de efeito estufa”. Esses gases que consistem principalmente em vapor de água, CO2 e metano interagem com a luz infravermelha e impedem que ela deixe a atmosfera enquanto se dirige para o espaço. Como consequência, a “coisa boa” acontece e a atmosfera retém o calor. É só que muito do efeito de aquecimento tem efeitos negativos de tornar a atmosfera muito quente.
A Figura 1 mostra que a quantidade de CO2 na atmosfera aumentou de 280 ppm para 413 ppm desde a revolução industrial. A datação por carbono mostra que esse aumento está ligado à queima de combustíveis fósseis (carvão, petróleo e gás natural). Durante o mesmo período, as temperaturas médias globais aumentaram 1°C. Embora 1°C não pareça ser alto, acredita-se que qualquer aumento adicional pode ter consequências graves, como o desaparecimento do gelo marinho, o recuo das geleiras, resultando em um aumento do nível do mar, que atualmente é medido em 3,3 milímetros por ano em média. Para evitar os efeitos nocivos da chance climática, o aquecimento global deve ser mantido abaixo dos 2 graus C.
A indústria siderúrgica é o maior setor em termos de emissões totais globais fósseis e industriais, representando cerca de 7% a 9% das emissões de gases de efeito estufa (GEE). É o maior emissor industrial e atualmente responsável por cerca de 8% da demanda final global de energia. Por isso, é um foco principal para os governos. Por outro lado, o aço é vital para as economias modernas e, portanto, espera-se que a demanda global por aço cresça para atender às crescentes necessidades de bem-estar social e econômico. É também um insumo crítico para a transição para a energia limpa. A geração e o uso de eletricidade dependem em parte das propriedades ferromagnéticas do aço e suas ligas. O aço é um importante insumo para turbinas eólicas, infraestrutura de transmissão e distribuição, usinas hidrelétricas e nucleares, entre outros ativos críticos do setor de energia.
Embora seja um facilitador da transição para energia limpa, o aço também é um grande contribuinte para o atual desafio que o mundo enfrenta para cumprir as metas climáticas. As emissões diretas de CO2 do setor giram em torno de 2,6 giga toneladas de dióxido de carbono (Gt CO2) por ano, ou cerca de um quarto das emissões industriais de CO2, devido à sua grande dependência do carvão e do coque como combustíveis e agentes redutores. Mais 1,1 Gt CO2 de emissões são atribuíveis ao uso de seus gases de escape, juntamente com outros combustíveis, para gerar a eletricidade e o calor importado que consome.
A alta dependência do carvão na atual produção de aço primário, ativos de capital de longa duração e a exposição do setor ao comércio internacional e à competitividade tornam desafiadora essa transição para emissões quase zero de CO2. É por estas razões que o setor é por vezes referido como um dos “difíceis de diminuir”.
O atendimento da demanda de produtos siderúrgicos apresenta desafios para o setor siderúrgico, que busca traçar um caminho mais sustentável, mantendo-se competitivo. Assim, os produtores de ferro e aço têm a grande responsabilidade de reduzir o consumo de energia e as emissões de gases de efeito estufa, desenvolver produtos mais sustentáveis e aumentar sua competitividade por meio da inovação, implantação de tecnologia de baixo carbono e eficiência de recursos.
Estudos recentes estimam que a indústria siderúrgica global pode encontrar cerca de 14% do valor potencial das organizações siderúrgicas em risco se não conseguirem diminuir seu impacto ambiental. Assim, a descarbonização deve ser uma prioridade para se manter economicamente competitivo e manter a permissão de operação do setor. Além disso, longos ciclos de investimento de 10 a 15 anos, necessidades de financiamento multibilionárias e capacidades limitadas de fornecedores tornam essa questão ainda mais relevante e garantem prazos significativos para enfrentar o desafio da descarbonização.
A indústria de ferro e aço reconheceu que são necessárias soluções de longo prazo para combater as emissões de CO2 produzidas durante a produção de aço. Como resultado, a indústria siderúrgica tem sido altamente proativa na melhoria do consumo de energia e na redução das emissões de CO2. As melhorias na eficiência energética levaram a reduções de cerca de 50% na energia necessária para produzir uma tonelada de aço bruto desde 1975 na maioria dos principais países produtores de aço. Outras melhorias na eficiência energética estão sendo feitas, fazendo o máximo uso possível das tecnologias de ponta.
A siderurgia verde consiste na utilização daqueles processos que resultam na redução das emissões de CO2. O trabalho de desenvolvimento dos processos de siderurgia verde está sendo feito na União Européia, EUA, Canadá, Brasil, Japão, Coréia do Sul, Austrália e China. Para o desenvolvimento das tecnologias para a siderurgia verde, cinco direções-chave estão sendo exploradas. Essas orientações são (i) tecnologias envolvendo uso de carvão, (ii) tecnologias envolvendo uso de hidrogênio, (iii) tecnologias envolvendo elétrons, (iv) tecnologias envolvendo uso de biomassa e (v) tecnologias envolvendo captura, uso e/ou carbono armazenamento (CCUS). Os caminhos para as tecnologias inovadoras para reduzir as emissões de CO2 das rotas de produção de aço à base de minério são mostrados na Figura 2.
Fig 2 Caminhos para tecnologias inovadoras para a fabricação de aço verde
Na União Européia, as tecnologias inovadoras estão sendo desenvolvidas sob o programa ULCOS (Ultra-Low CO2 Steelmaking). Sob este programa, o trabalho de desenvolvimento está sendo realizado para (i) 'alto-forno de reciclagem de gás superior' (TGR-BF) com captura, uso e/ou armazenamento de CO2 (CCUS), (ii) processo HIsarna com CCUS envolvendo redução de fundição , (iii) ULCORED com CCUS que envolve um novo conceito de redução direta (DR), e (iv) eletrólise. Além disso, a ULCOS também está trabalhando no uso de carbono de biomassa sustentável, bem como na fabricação de aço à base de hidrogênio.
Nos EUA, o trabalho de desenvolvimento está sendo realizado com “parceria público-privada” entre o American Iron and Steel Institute (AISI) e o Departamento de Energia dos EUA (DOE) e o Office of Industrial Technology. Dois projetos representam passos significativos. Esses projetos são (i) redução de hidrogênio em suspensão do concentrado de óxido de ferro e (ii) eletrólise de óxido fundido (MOE). No curto prazo, o trabalho de desenvolvimento está sendo feito pelos membros da AISI para “o forno de fornalha reta emparelhada”, um processo DRI à base de carvão e metal fundido para substituição de longo alcance de altos-fornos e fornos de coque.
No Japão, o trabalho de desenvolvimento é realizado sob o programa COURSE50 envolvendo seis organizações de aço e engenharia, a Federação Japonesa de Ferro e Aço e a Organização de Desenvolvimento de Novas Energias e Tecnologia Industrial. As metas de pesquisa e desenvolvimento do programa são (i) redução das emissões de CO2 da redução do minério de ferro do alto-forno com outros agentes redutores (hidrogênio), (ii) reforma do gás de coqueria visando aumentar o teor de hidrogênio utilizando o calor residual, ( iii) coque de alta resistência e alta reatividade para redução com hidrogênio. O trabalho de desenvolvimento também está sendo realizado para a captura de CO2 do gás de alto-forno envolvendo (i) absorção química e física para capturar, separar e recuperar CO2, e (ii) redução da necessidade de energia para captura, separação e recuperação usando calor residual da siderúrgica.
Na Coréia do Sul, o trabalho de desenvolvimento é realizado envolvendo POSCO, RIST, POSLAB e POSTECH. Três rotas promissoras de soluções inovadoras de CO2 foram identificadas. São eles (i) siderurgia enxuta de carbono, consistindo no processo FINEX enxuto de carbono, e pré-redução e recuperação de calor da sinterização a quente, (ii) captura e armazenamento de carbono da siderurgia por absorção de CO2 usando solução de amônia e sequestro de CO2 em campo de gás oceânico, e (iii) siderurgia a hidrogênio por redução de minério de ferro no processo FINEX utilizando gás de síntese enriquecido com hidrogênio e processo de alto-forno enriquecido com hidrogênio.
As tecnologias emergentes para redução ou eliminação das emissões de carbono do processo siderúrgico podem ser divididas em duas categorias distintas:(i) captura, uso e/ou armazenamento de carbono (CCUS) e (ii) redução alternativa de minério de ferro. O CCUS emprega diferentes métodos para capturar as emissões de CO2. Ele os armazena (por exemplo, em formações geológicas, como reservatórios de gás submarinos esgotados) ou processa as emissões para utilização posterior. Sozinho, o CCUS não pode alcançar a neutralidade de carbono. Mas pode resultar em um balanço negativo de CO2 se os combustíveis fósseis usados no processo siderúrgico forem substituídos pela biomassa.
O segundo tipo de tecnologias potenciais envolve a substituição de coque ou gás natural por agentes redutores alternativos para o minério de ferro. Estes incluem hidrogênio e corrente elétrica direta. A vantagem dessas tecnologias é que teoricamente elas podem tornar a produção de aço totalmente verde. No entanto, a maioria deles provavelmente precisa de ainda mais tempo e fundos para configurar em comparação com o CCUS.
A mais promissora das novas tecnologias de redução CCUS e alternativas, bem como a tecnologia de redução direta baseada em hidrogênio, são discutidas abaixo.
Tecnologias com CCUS
Nessas tecnologias, o CO2 emitido durante o processo de operação é separado dos demais gases e capturado. O CO2 capturado é então transportado através de um duto ou enviado para um local de armazenamento onshore ou offshore ou usado. Os processos para CCUS incluem captura pós/pré-combustão, compressão, transporte e armazenamento/uso. A Figura 3 mostra o esquema CCUS para a rota de aciaria de alto-forno simplificado – forno básico a oxigênio (BF-BOF).
Fig 3 Esquema CCUS para rota BF-BOF simplificada
A principal vantagem é que os sistemas CCUS podem ser facilmente integrados em plantas industriais convencionais existentes. E como a tecnologia não é específica da siderurgia, outras indústrias também podem dividir os custos de desenvolvimento e infraestrutura. Além disso, os custos operacionais futuros são amplamente previsíveis.
A principal desvantagem é que o CCUS não é totalmente neutro em carbono, pois o processo de captura de carbono por si só captura apenas cerca de 90% do CO2. Além disso, existem alguns outros desafios. A aceitação pública do armazenamento de carbono não é certa, o que coloca os pioneiros em uma posição desvantajosa. Além disso, atualmente, com exceção de locais de armazenamento em terra menores, o mar oferece o único local de armazenamento grande e adequado, e isso requer esforços consideráveis de transporte. Além disso, a utilização de emissões também é para garantir que não haja liberação de carbono em um estágio posterior para que o processo seja neutro em carbono. Além disso, o equipamento CCUS aumenta a carga de manutenção e os tempos de desligamento com um impacto significativo nos custos operacionais.
Existem alguns projetos-piloto que foram adotados para o processamento de emissões, como o CO2, para produzir combustível sintético. Mas, no momento, isso não é neutro em carbono, pois o CO2 é emitido em um estágio posterior.
Fabricação de ferro à base de biomassa com CCUS
A ideia básica por trás dessas tecnologias é que a biomassa neutra em carbono substitui parcialmente os combustíveis fósseis no pré-processamento ou como agente redutor do minério de ferro. Os exemplos são “carvões” ricos em carbono feitos de biomassa bruta (algas brutas, grama, madeira etc.) Os processos baseados nessas tecnologias incluem pirólise e carbonização hidrotérmica. Os sistemas CCUS cuidam de quaisquer emissões de carbono restantes.
A biomassa sozinha pode reduzir até 40% a 60% das emissões de CO2 e em combinação com o CCUS pode alcançar uma produção de aço neutra em carbono. No curto prazo, a biomassa é uma substituição parcial instantânea dos combustíveis fósseis, permitindo reduções de emissões de ganhos rápidos nas usinas existentes. O CO2 das emissões também pode ser reciclado usando CCUS para produzir biomassa fresca.
No entanto, o cultivo de biomassa é difícil. Ambientalmente, pode levar ao desmatamento, poluição e redução da biodiversidade, e socialmente afeta os preços dos alimentos e o uso da terra agrícola. Portanto, a aceitação política e social tem um alto risco. Além disso, a biomassa tem um poder calorífico inferior aos combustíveis fósseis, limitando seu uso em grandes altos-fornos ou resultando em redução de eficiência. Além disso, devido ao seu alto teor de água, também pode ser muito pesado para uso em grandes altos-fornos.
Um estudo sobre o uso do grupo de pesquisa sueco SWEREA em uma usina siderúrgica da SSAB em Lulea identificou potencial para uma redução de 28% nas emissões de CO2 com a fabricação de ferro à base de biomassa.
Forno de cuba à base de hidrogênio para ferro reduzido direto
No processo, em vez de um agente redutor de carbono, como o gás natural reformado, o hidrogênio é usado para reduzir pelotas de minério de ferro a “ferro reduzido direto” (DRI ou ferro esponja). A reação ocorre em um forno de cuba. O DRI produzido é então alimentado em um forno elétrico a arco e pela adição de carbono; é transformado em aço por processamento adicional. O DRI também pode ser alimentado em um alto-forno na forma de “ferro briquetado a quente” (HBI). Isso aumenta significativamente a eficiência do alto-forno e reduz o consumo de coque. As tecnologias de processo semelhantes mais comuns são os processos Midrex e Energiron.
Na redução à base de hidrogênio, o minério de ferro é reduzido por meio de uma reação gás-sólido, semelhante à rota de produção DRI. O único fator de diferenciação é que o agente redutor é hidrogênio puro em vez de gás monoóxido de carbono, gás de síntese ou coque. A redução do minério de ferro pelo hidrogênio ocorre em duas ou três etapas. Para temperaturas superiores a 570°C, o minério de hematita (Fe2O3) é primeiro transformado em magnetita (Fe3O4), depois em wustita (FexO) e finalmente em ferro metálico, enquanto em temperaturas abaixo de 570°C, a magnetita é transformada diretamente em ferro, pois a wustita não é termodinamicamente estável.
As reações de redução envolvidas na redução do minério de ferro por hidrogênio são representadas pelas equações (i) 3 Fe2O3 + H2 =2 Fe3O4 + H2O, (ii) x Fe3O4 + (4x-3) H2 =3 FexO + (4x-3 ) H2O, e (iii) FexO + H2 =x Fe + H2O onde x é igual a 0,95. Conforme indicado por essas reações, a redução do minério de ferro com hidrogênio libera vapores de água inofensivos (H2O) em vez do gás de efeito estufa CO2. A reação global para a redução do minério de hematita com H2 é Fe2O3 + 3H2 =2Fe + 3H2O que é uma reação endotérmica com um calor de reação, delta H a 298 graus C =95,8 kJ/mol, que é negativo para o balanço de energia do processo e demanda um acréscimo de energia com a mistura gás de redução/gás injetada. O foco no desenvolvimento da linha de produção é a otimização baseada na temperatura de redução, cinética da reação, composição do pellet e tecnologia de pré-aquecimento do gás de redução.
O consumo estequiométrico de H2 para redução de minério de hematita (Fe2O3) é de 54 kg por tonelada de ferro. Assim, uma usina siderúrgica de 1 milhão de toneladas por ano precisa de uma usina de hidrogênio com capacidade de até 70.000 cum/hora de hidrogênio em temperatura e pressão padrão (STP). Com o hidrogênio como gás de redução, é importante antecipar a mudança no comportamento do reator em relação ao reator com misturas de hidrogênio-monóxido de carbono como gás de redução. Vários fatores podem interagir de diferentes maneiras, como cinética, termodinâmica, transferência de calor e fluxo de gás.
O processo faz com que toda a rota primária de fabricação de aço seja neutra em carbono e livre de combustível fóssil, caso a eletricidade verde seja totalmente usada para o processo. Outra vantagem para o processo é a alta flexibilidade de produção. O processo é fácil de iniciar e parar, e a capacidade da tecnologia de usar unidades menores permite maior escalabilidade. Além disso, a capacidade de alimentar DRI como HBI em um alto-forno – sistema básico de produção de aço com forno a oxigênio significa que as plantas convencionais existentes podem ser usadas enquanto a produção de forno de poço / EAF é aumentada.
O processo ainda precisa de pelotas de minério de ferro, e produzi-las pode causar emissões significativas dependendo da fonte de calor da planta de pelotização. Fornecer a quantidade necessária de hidrogênio também é um problema e eletrolisadores eficientes em larga escala precisam ser desenvolvidos. Além disso, como o processo depende de grandes quantidades de energia verde barata, os países produtores de aço devem importar hidrogênio ou ferro pré-processado, prejudicando suas cadeias de valor, se não conseguirem aumentar significativamente sua própria produção de energia verde. Há também incerteza em torno dos custos operacionais futuros relacionados aos preços do hidrogênio e da eletricidade. A Fig. 4 mostra um forno de cuba à base de hidrogênio para ferro reduzido direto.
Fig 4 Forno de cuba à base de hidrogênio para ferro reduzido direto
O processo HYBRIT usa forno de cuba à base de hidrogênio para a produção de DRI. HYBRIT é a abreviação de 'tecnologia de fabricação de ferro HYdrogen BReakthrough'. Em 4 de abril de 2016, as três empresas suecas – SSAB, LKAB e Vattenfall AB lançaram um projeto destinado a investigar a viabilidade de um processo de produção DRI baseado em H2, com eletricidade livre de emissões de CO2 como fonte de energia primária. Uma empresa de joint venture foi formada, HYBRIT Development AB, com as três empresas sendo proprietárias. Isso deu acesso total à competência superior em toda a cadeia de valor, desde produção de energia, mineração, beneficiamento de minério e produção de pelotas, redução direta, fusão e produção de aço bruto. Em 2017, foi realizado um estudo de pré-viabilidade de redução direta baseada em H2. O estudo concluiu que a rota de processo proposta é tecnicamente viável e, tendo em vista as tendências futuras de custos de emissões de CO2 e eletricidade, também é economicamente atraente para condições em norte da Suécia / Finlândia.
O processo HYBRIT substitui o carvão por hidrogênio para a redução direta do ferro, combinado com um forno elétrico a arco. O processo é quase completamente livre de combustível fóssil e resulta em uma redução substancial em suas emissões de gases de efeito estufa. O processo está entre as várias iniciativas que usam uma configuração de redução direta de hidrogênio / forno elétrico a arco, combinando a redução direta de minério de ferro pelo uso de hidrogênio com um forno elétrico a arco para posterior processamento em aço. O produto do processo de redução direta de hidrogênio é DRI ou ferro-esponja, que é alimentado em um forno elétrico a arco, misturado com partes adequadas de sucata e posteriormente processado em aço.
O fluxograma principal do processo de produção HYBRIT é mostrado na Figura 5. As principais características do processo são (i) combustíveis não fósseis são usados na produção de pellets, (ii) hidrogênio é produzido com eletrólise usando eletricidade livre de fósseis, (iii) armazenamento de hidrogênio em uma unidade especialmente projetada é usado como um amortecedor para a rede, (iv) um forno de poço é usado para redução de minério de ferro, (v) pelotas feitas sob medida são usadas como alimentação de minério de ferro, (vi) o gás de redução / mistura gasosa é pré-aquecida antes da injeção no poço, (vii) o produto pode ser DRI ou HBI isento de carbono ou carburado, e (viii) o DRI/HBI é fundido junto com sucata reciclada em um forno elétrico a arco.
Fig 5 Fluxograma de princípios do processo de produção HYBRIT
O uso do hidrogênio produzido por eletrólise da água usando eletricidade livre de fósseis para reduzir pelotas de minério de ferro em um forno de poço é a principal alternativa escolhida para a iniciativa HYBRIT. Sob esta iniciativa, uma conversão para uma cadeia de valor livre de fósseis da mina para o aço acabado inclui muitas questões a serem desenvolvidas, levando em consideração também o mercado local e as condições geográficas. A Suécia tem uma situação única com excesso de capacidade de energia elétrica na parte norte do país, proximidade de minas de minério de ferro, bom acesso de biomassa e siderurgia e uma forte rede entre indústria, institutos de pesquisa e universidades.
O processo HYBRIT se enquadra em uma categoria de conceitos tecnológicos substancialmente mais próximos da implantação comercial. Baseia-se na utilização do hidrogénio como agente redutor, sendo o hidrogénio produzido por eletrólise com base em eletricidade renovável. Do ponto de vista ambiental, a vantagem mais importante disso é que o escape desse processo é água (H2O) em vez de CO2, com conseqüente redução das emissões de GEE. Assim como na fabricação de aço DRI convencional, o ferro produzido usando a rota DRI à base de hidrogênio pode ser processado em aço usando a tecnologia de forno elétrico a arco disponível comercialmente. A produção de hidrogênio e as etapas de fabricação de aço com forno elétrico a arco podem ser feitas sem carbono se a energia elétrica e o hidrogênio forem produzidos usando fontes renováveis, como eletrólise solar / eólica / hidrelétrica fotovoltaica, produção fotoquímica de hidrogênio ou energia solar. separação da água termal.
Processo de leito fluidizado à base de hidrogênio para redução direta de ferro
Assim como na versão de forno de poço, essa tecnologia usa hidrogênio para reduzir o minério de ferro e produzir DRI para alimentar um forno elétrico a arco. As diferenças são que a redução ocorre em um leito fluidizado ao invés de um forno, e finos/concentrados de minério de ferro finamente processados são usados em vez de pelotas. Leitos fluidizados são câmaras de reator que podem misturar continuamente matérias-primas sólidas com um gás para produzir um sólido. Os processos semelhantes são FINEX e Circored.
O uso de finos sobre pelotas de ferro tem a vantagem de eliminar a necessidade de pelotização e, assim, reduzir os custos e as altas emissões de CO2 envolvidas no processo. Além disso, os reatores de leito fluidizado apresentam menos problemas de aderência interna do que os fornos de cuba, alcançando maior metalização (cerca de 90% a 95%).
O processo compartilha as mesmas questões em relação ao fornecimento de hidrogênio, eletrolisador e custo operacional que o método do forno de cuba. O fornecimento de eletricidade também deve ser 100% verde para alcançar a neutralidade de carbono. Além disso, o uso de reatores de leito fluidizado na siderurgia é menos desenvolvido do que os fornos de cuba e, portanto, necessita de maior investimento. A Fig. 6 mostra o processo de leito fluidizado à base de hidrogênio para ferro reduzido direto.
Fig 6 Processo de leito fluidizado à base de hidrogênio para redução direta de ferro
A redução de minério fino à base de hidrogênio (ou HYFOR para abreviar) é o primeiro processo de redução direta do mundo para concentrados de minério de ferro do beneficiamento de minério que não precisa de nenhum pré-processamento do material, como sinterização ou pelotização. Isso reduz os custos de CAPEX e OPEX. O processo é capaz de processar uma grande variedade de minérios, e. hematita e magnetita.
O processo HYFOR foi desenvolvido pela Primetals Technologies. A nova tecnologia pode ser aplicada a todos os tipos de minério beneficiado. Funciona com granulometria inferior a 0,15 mm para 100% da matéria-prima, permitindo, ao mesmo tempo, granulometria máxima de 0,5 mm. Devido à grande superfície das partículas, o processo atinge altas taxas de redução em baixas temperaturas e pressões.
Como agente redutor primário, o novo processo usa hidrogênio. O hidrogênio pode ser de energia renovável ou, alternativamente, gases ricos em hidrogênio de outras fontes de gás, como pirólise de gás natural ou reformadores a vapor convencionais. Como outra alternativa, o HYFOR pode funcionar com gases residuais ricos em hidrogênio. Dependendo da fonte do hidrogênio, isso leva a uma emissão de CO2 baixa ou mesmo zero para o DRI resultante.
Uma planta piloto para fins de teste foi comissionada em abril de 2021 voestalpine Stahl Donawitz, Áustria. A planta apresenta um design modular com capacidade nominal de 250.000 toneladas por módulo por ano, tornando-a adequada para todos os tamanhos de plantas siderúrgicas. O objetivo da planta piloto é fornecer evidências práticas para esse processo inovador e servir como uma instalação de testes, coletando dados suficientes para montar uma planta em escala industrial em um estágio posterior.
Os primeiros testes foram executados com sucesso em abril de 2021 e maio de 2021. A escala de um teste está na faixa de processamento de 800 kg de minério de ferro. A planta piloto HYFOR será operada por pelo menos 2 anos em várias campanhas para testar vários tipos de minério e avaliar os parâmetros de processo ideais para a próxima etapa de expansão. Assumida operação suave, uma unidade de briquetagem a quente será adicionada para verificar a etapa de briquetagem a quente, bem como a qualidade HBI que se espera da tecnologia HYFOR.
O processo HYFOR reduz drasticamente as emissões de CO2 e ajuda os produtores a lidar efetivamente com o desafio da redução da qualidade do minério de ferro, que se tornou mais agudo ultimamente, resultando em uma maior necessidade de beneficiamento dos minérios. A crescente demanda por pelotas de minério de ferro para altos-fornos e plantas de redução direta levou a preços mais altos para o minério de ferro, especialmente pelota premium. Com o processo HYFOR, é possível usar minério fino granulado diretamente e se beneficiar da crescente oferta global de ultrafinos.
A planta piloto HYFOR na voestalpine Donawitz consiste em três partes, a saber (i) uma unidade de pré-aquecimento-oxidação, (ii) uma planta de tratamento de gás e (iii) o núcleo que é a nova e única unidade de redução. Na unidade de pré-aquecimento-oxidação, o concentrado de minério fino é aquecido a cerca de 900°C e alimentado na unidade de redução. O gás de redução é 100% hidrogênio, fornecido por um fornecedor de gás localizado fora dos limites da planta. Um sistema de recuperação de calor residual que aproveita o calor do gás de exaustão garante o uso ideal de energia e um sistema de despoeiramento a seco cuida das emissões de poeira dos processos. O ferro reduzido direto a quente (HDRI) sai da unidade de redução a uma temperatura de cerca de 600 graus C antes de ser resfriado e descarregado da planta piloto HYFOR.
O ferro reduzido direto a quente que sai da unidade de redução a uma temperatura de cerca de 600°C pode ser posteriormente transportado diretamente e alimentado em um forno elétrico a arco ou usado para produzir ferro briquetado a quente. Ferro briquetado a quente é para fornecimento ao mercado. O próximo passo será a adição de uma instalação de teste de briquetagem a quente para testar as características do ferro briquetado a quente.
O objetivo da planta piloto HYFOR é verificar este processo inovador e servir como uma instalação de teste para fornecer a base de dados para aumentar o tamanho da planta para uma planta protótipo em escala industrial como a próxima etapa de desenvolvimento.
Fabricação de ferro com suspensão
A fabricação de ferro com suspensão também é conhecida como “tecnologia de fabricação de ferro flash”. Este processo começa com a moagem ultrafina de minério de ferro de baixo teor para produzir concentrado de minério de ferro. O minério de ferro deve ser moído em partículas de menos de 100 micrômetros de diâmetro. Os ultrafinos são então reduzidos usando hidrogênio em um reator ‘flash’ de alta temperatura por apenas alguns segundos, produzindo ferro diretamente uma vez que o carbono é adicionado. O concentrado de minério de ferro também pode ser pré-reduzido a uma temperatura mais baixa em um reator separado antes de ser adicionado ao reator flash. A Fig. 7 mostra o princípio de fabricação de ferro com base em suspensão.
Fig 7 Fabricação de ferro com suspensão
A tecnologia de transformação flash de fabricação de ferro está sendo desenvolvida por um consórcio de organizações e institutos nos EUA sob o apoio financeiro do American Iron and Steel Institute. Esta tecnologia baseia-se na redução gasosa direta do concentrado de óxido de ferro em um processo de redução instantânea. A tecnologia tem o potencial de reduzir o consumo de energia de 32% a 57% e as emissões de CO2 de 61% a 96% em comparação com a operação média atual baseada em BF. Esta tecnologia é adequada para uma operação industrial que converte concentrado de minério de ferro (menos de 100 mícrons) em aço sem tratamento adicional.
Esta tecnologia produz ferro ao mesmo tempo que ignora a pelotização ou sinterização, bem como as etapas de fabricação de coque. Além disso, o processo é intensivo devido ao fato de que as partículas finas do concentrado são reduzidas a uma taxa rápida de 1.150 graus C a 1.350 graus C. Assim, os tempos de residência necessários neste processo são da ordem de segundos, em vez do minutos e horas necessários para pelotas e até mesmo finos de minério de ferro. As reduções de 90% a 99% ocorrem em 2 segundos a 7 segundos a 1.200 graus C a 1.500 graus C. A necessidade de energia do processo com H2 como gás redutor é de 5,7 GJ (1.360 Mcal)/ton de ferro líquido.
A redução direta de minério de ferro para aço em um reator elimina a necessidade de fabricação de ferro e sinterização ou pelotização. Tem custos consideráveis e benefícios de emissão. Também produz aço "mais limpo", pois as altas temperaturas e os tempos de reação rápidos garantem menos impurezas.
Com o H2 como gás redutor, as emissões de CO2 são de 0,04 toneladas de CO2 por tonelada de ferro líquido. Essas emissões são 2,5% das emissões da rota BF de siderurgia. O processo de ferro flash é realizado a uma temperatura alta o suficiente para que as partículas individuais tenham energia suficiente para fechar os poros criados pela remoção do oxigênio. Assim, as partículas individuais são muito menos suscetíveis a pegar fogo por oxidação rápida. A Universidade de Utah realizou pesquisas em pequenas amostras de pó e determinou que elas não são pirofóricas.
O processo deve ser aplicado à produção de ferro como alimentação para o processo de fabricação de aço ou como parte de um processo de fabricação de aço direto contínuo. Justified by experimental data obtained during the previous phase of the project, scale-up development work is presently ongoing at the University of Utah. Testing in a laboratory flash furnace has resulted in the establishment of a kinetics database over wide ranges of operating conditions and a complete design of a more advanced bench reactor. With an objective to develop an industrially viable flash iron technology, a comprehensive bench scale testing campaign is planned. The deliverables from this phase of the project are expected to be the determination of the scalability of the process, substantive process simulation results, and fundamental engineering data leading to the design and construction of an industrial pilot plant. The flowsheet of the flash ironmaking technology is given at Fig 8.
Fig 8 Flowsheet of flash ironmaking Technology
Plasma direct steel production
In the plasma direct steel production process iron ore, raw or in the form of fines or pellets, is reduced using hydrogen plasma in a plasma steelmaking reactor. At the same time, carbon is added to the reactor to produce steel. Hydrogen plasma is hydrogen gas which has been heated or electrically charged to separate, or ionize, it into its constituent particles. The process can use either thermal plasma (produced by directly heating hydrogen) or non-thermal plasma (produced by passing a direct current or microwaves through the hydrogen).
The process removes the need for pre-processing of iron ore and allows for lower reactor temperatures. It is also highly integrated, with some methods (for example, hydrogen plasma smelting reduction) needing only a single step. This makes it commercially attractive. The technology has the potential to reduce costs considerably. It also offers higher product quality and better production flexibility.
The technology is at a very early stage of development, with an optimal process and full reactor design yet to be developed. Its commercial feasibility is also still to be proven. As part of its Sustainable Steel (SuSteel) project, the Austrian steelmaker voestalpine has built a small pilot hydrogen plasma reduction reactor at its Donawitz site. Plasma direct steel production process is shown in Fig 9.
Fig 9 Plasma direct steel production process
Electrolytic processes
There are two types of electrolytic processes. These are (i) electrolysis, and (ii) electro-winning. These two process variants are called as ULCOWIN and ULCOLYSIS under the ULCOS programme. ULCOWIN process operates slightly above 100 deg C in a water alkaline solution populated by small grains of ore. In this process iron ore is ground into an ultrafine concentrate, leached and then reduced in an electrolyzer at around 110 deg C. The resultant iron plates are fed into an electric arc furnace, which turns it into steel. ULCOLYSIS operates at steelmaking temperature (around 1,550 deg C) with a molten salt electrolyte made of a slag (pyro-electrolysis). This process transforms iron ore at into liquid steel using electricity as a reducing agent. Fig 10 shows electrolytic processes for steel production.
Fig 10 Electrolytic processes for steel production
The electrolysis process has been developed from scratch within the ULCOS programme and, hence, is still operating at laboratory scale. Although it holds the promise of zero emissions, if it has access to green electricity, time is needed to scale it up to a commercial size (10 to 20 years). ULCOWIN process consists of alkaline electrolysis of iron ore. Electrolysis is normally used to produce metals other than steel and needs large amounts of electricity. The process is to depend on a CO2-lean electricity source such as renewable power, hydro power, or nuclear power. ULCOLYSIS is the molten oxide electrolysis. Molten oxide electrolysis works by passing an electric current through molten slag fed with iron oxide. The iron oxide breaks down into liquid iron and oxygen gas. No CO2 is produced. Process emissions are further reduced with a CO2-lean electricity source.
Since the electrolytic processes skip the upstream stages needed in other production routes, such as producing coke or H2 as reducing agents, these processes have the potential to become the most energy-efficient steelmaking technologies, especially electrolysis. They also promise to significantly lower CAPEX as, in the case of electrolysis, only very few equipments are needed. The process is also relatively inflexible compared to the hydrogen direct reduction process since it cannot be stopped easily.
Processo de manufatura