Forno de Indução e Aspectos Operacionais Importantes
Forno de indução e aspectos operacionais importantes
O desenvolvimento do forno de indução para siderurgia tem sido uma benção para os pequenos produtores de aço. Esses fornos são fáceis de instalar, operar e manter. Esses fornos são menores em tamanho de calor com um investimento de baixo custo e preferidos por usinas siderúrgicas de menor capacidade. Nesses fornos, o aço é produzido pela fusão do material de carga usando o calor produzido pelo campo eletromagnético.
O forno de indução é composto basicamente por um cadinho, bobina indutora e casca, sistema de refrigeração e mecanismo de inclinação. O cadinho é formado de material refratário, com o qual as bobinas do forno são revestidas. Este cadinho contém o material de carga e, posteriormente, o fundido. A escolha do material refratário depende do tipo de carga e consiste basicamente em refratários ácidos, básicos ou neutros.
A bobina do indutor é uma bobina de cobre tubular com número específico de voltas. Uma corrente alternada (AC) passa por ele e o fluxo magnético é gerado dentro do condutor. O fluxo magnético gerado induz correntes parasitas que possibilitam o aquecimento e posteriormente o processo de fusão no cadinho.
A casca é a parte externa do forno. Este abriga o cadinho e as bobinas do indutor, e tem maior capacidade térmica. É feito de paralelepípedo retangular com chapa de aço de baixo carbono e unidos nos cantos por suportes de borda de peças angulares e tiras de metal não magnético.
O sistema de resfriamento é normalmente um sistema de fluxo unidirecional com as bobinas tubulares de cobre conectadas à fonte de água através de mangueiras de borracha flexíveis. O processo de resfriamento é importante porque o circuito do forno parece resistivo, e a potência real não é consumida apenas no material carregado, mas também na resistência da bobina. Esta perda da bobina, bem como a perda de calor conduzida da carga através do cadinho refratário, requer que a bobina seja resfriada com água como meio de resfriamento para evitar o aumento indevido da temperatura das bobinas de cobre.
Matérias-primas e fonte de energia
Sucata de fundição de aço, ferro reduzido direto e ferro gusa/ferro fundido são as matérias-primas de entrada para um forno de indução. A proporção desses itens e a tecnologia de fusão desses insumos varia de acordo com a disponibilidade de matéria-prima e localização da planta. Outras matérias-primas selecionadas são necessárias para a produção de aço de qualidade específica. Para melhor e eficiente operação de fusão em forno de indução, a carga de matéria-prima deve atender aos seguintes critérios.
- Deve ser o mais denso possível. A compactação da sucata é importante para garantir um aquecimento uniforme e rápido, bem como para a economia de energia.
- Deve estar limpo. Ferrugem, óleo, graxa e areia etc. devem ser preferencialmente zero.
- Deve ser metalurgicamente limpo, ou seja, livre de grumos de escória, óxidos etc., principalmente para ferro reduzido direto, crânio e ligas de ferro.
- Não há bordas pontiagudas ou menos afiadas, principalmente no caso de sucata pesada e volumosa.
- Deve ser segregado de ingredientes nocivos, como explosivos, recipientes fechados, substâncias evaporativas e prontamente disponível em tamanhos carregáveis no chão de fábrica.
A eletricidade é a única fonte de energia para a fusão do aço no forno de indução. O forno de indução deve funcionar na potência máxima desde o início. Existem alguns equívocos sobre o funcionamento do forno em uma torneira baixa inicialmente e depois aumentar gradualmente para uma torneira mais alta. A entrada máxima de energia aumenta a taxa de fusão e, portanto, reduz o tempo de ciclo de um calor. Fator de potência a ser mantido próximo de um.
Queda de tensão da fonte também deve ser monitorada para melhor eficiência energética. A taxa de consumo de energia adicional depende do tamanho do forno e é reduzida à medida que a capacidade do forno aumenta aproximadamente até 15 a 17 toneladas e, posteriormente, a taxa de consumo permanece quase constante em cerca de 600 kWh/ton.
Aspectos importantes da operação
Como o aço líquido é excitado pela corrente oposta à corrente que flui na bobina de indução, ele é agitado para elevar sua superfície no centro. A superfície do aço líquido aumenta à medida que a frequência se torna mais baixa, ou seja, a agitação do aço líquido ocorre mais forte no forno de baixa frequência do que no forno de alta frequência. Este efeito de agitação permite garantir a uniformidade da temperatura do aço líquido e sua qualidade uniforme, bem como promover o aprisionamento do material carregado e a fusão dos agentes de ajuste da composição química, especialmente a adição de carbono. Por outro lado, a agitação excessiva pode causar problemas como o desgaste oxidativo do aço líquido e a fusão dos refratários ou o perigo de respingos do aço líquido.
Uma vez que a fusão está completa, a escória é desnatada. A escória gerada durante a fusão tem tendência a grudar na parede do forno. Isso reduz o volume do forno, portanto, reduz a produção de metal por calor. O superaquecimento do metal é feito em temperatura mais alta e mantido por alguns minutos. Isso inibe o depósito de escória no revestimento do forno, mantendo o forno limpo com volume total.
A composição da escória varia dependendo do processo específico que está sendo usado e do tipo de aço que está sendo produzido. As composições de escórias de forno e concha são muitas vezes muito complexas. A escória que se forma é o resultado de reações complexas entre sílica, óxido de ferro da sucata de aço, outros produtos de oxidação da fusão e reações com revestimentos refratários. A escória consiste em uma fase líquida complexa de óxidos de ferro, manganês, magnésio e silício, silicatos e sulfetos, além de uma série de outros compostos, que podem incluir alumina, óxidos e sulfetos de cálcio, óxidos e sulfetos de terras raras etc.
Ao produzir o aço, a química do produto final é controlada. A análise química de todos os materiais de entrada é feita para se ter uma decisão sobre a mistura de cargas. Depois de completar 50% de carga dos materiais de entrada, uma amostra de banho é analisada quanto à composição química. Com base na análise química da amostra do banho, nesta etapa são feitos cálculos para novas adições dos metálicos. Se a amostra de banho neste estágio apresentar alta porcentagem de carbono, enxofre e fósforo, então o teor de ferro reduzido direto da carga é aumentado. A amostra final do banho é coletada quando a fusão de 80% estiver completa. Com base na análise dessa amostra, outro ajuste é feito na carga. O menor teor de carbono na amostra é corrigido aumentando a quantidade de gusa/ferro fundido na carga. Silício e manganês no metal são oxidados pelo óxido de ferro do ferro reduzido direto. O enxofre também é diluído pelo ferro reduzido direto. Devido ao uso de ferro reduzido direto, os oligoelementos no aço feito no forno de indução permanecem sob controle.
O aço líquido é a saída desejada do forno de indução. A quantidade depende da capacidade do forno e a qualidade depende das matérias-primas e da composição do aço. A temperatura de vazamento depende do tipo de aço e do superaquecimento necessário no aço líquido para seu uso final. O rosqueamento de aço em altas temperaturas aumenta a erosão refratária e o consumo de energia.
O superaquecimento desnecessário de aço líquido a altas temperaturas custa energia significativamente. Minimizar o superaquecimento do banho fundido economiza energia. Dependendo da especificação do aço e da perda de temperatura durante a transferência do aço líquido para a máquina de lingotamento contínuo, a temperatura de superaquecimento deve ser decidida. Em cada aquecimento, a temperatura do banho de aço líquido deve ser medida e monitorada para obter uma ótima economia de energia. Sistemas adequados de controle de potência com ajuste de potenciômetro precisam ser fornecidos para minimizar as perdas de energia devido ao superaquecimento.
A inclinação do forno é para efetuar o vazamento do fundido é uma última atividade operacional antes do vazamento. O forno é normalmente inclinado para atingir um ângulo de 90 graus ou mais para o vazamento completo do aço líquido.
Outros aspectos da fabricação de aço em forno de indução
Dependendo da densidade de potência instalada e da prática de fusão, a eficiência térmica do forno de indução pode exceder 80%, mas geralmente está na faixa de 60% a 78%.
Os fornos de indução são normalmente mantidos abertos durante todo o processo de fusão, onde os trabalhadores se dedicam à escumação da escória e ao monitoramento da qualidade do banho fundido. No entanto, isso leva a uma perda de calor significativa e, portanto, é necessário instalar tampas ou tampas especiais para reduzir as perdas de calor. Em particular, reduzir o tempo em que a tampa é mantida aberta durante o derretimento pode levar a economias substanciais de energia.
O requisito teórico de energia para o ferro fundido é de apenas 340 kWh por tonelada, enquanto a potência real necessária é de cerca de 600 kWh. Essa diferença se deve a dois fatores, a saber (i) inerente ao princípio de fusão em um forno de indução que inclui a ineficiência nas perdas de barramento elétrico, perdas por correntes parasitas, perdas refratárias e perdas de água de resfriamento etc., e (ii) a perdas operacionais que se devem em grande parte à retenção desnecessária e excessiva de aço líquido no forno de indução.
Os equipamentos do forno de indução devem ser colocados com distância mínima entre cada equipamento para reduzir as perdas na fiação. Para reduzir notavelmente as perdas na fiação, é essencial diminuir a distância entre o corpo do forno e o capacitor, melhorando o fator de potência, pois uma corrente muito grande flui entre eles.
A eficiência do forno de indução é expressa como um total, deduzindo as perdas elétricas e de transferência de calor. O diagrama de equilíbrio térmico típico do forno de indução tipo cadinho de alta e média frequência é mostrado na Fig. 1. As perdas elétricas consistem em transformador, conversor de frequência, condensador, fiação, cabo, bobina, etc. A perda na bobina é um fator essencial, no qual o forno capacidade depende. As perdas de calor no forno de indução consistem em perda de condução de calor que escapa da parede do forno para o lado da bobina, perda de radiação de calor liberada da superfície do fundido, perda de absorção na capa do anel, perda de fusão da escória, etc. As bobinas do forno são resfriadas a água, o que também resulta na perda de calor. A eficiência térmica dos fornos de alta e média frequência (60% – 78%) é ligeiramente maior do que a do forno de baixa frequência (58% – 71%).
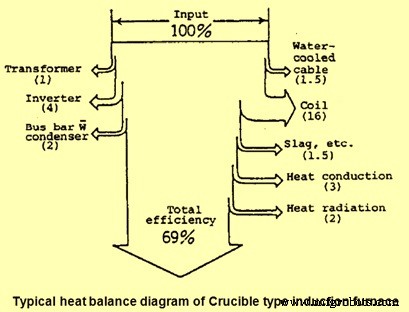
Fig 1 Diagrama de equilíbrio térmico típico do forno de indução de cadinho
Um dos problemas mais críticos com o processo de fabricação de aço em forno de indução é sua limitação para refinar o aço para reduzir o teor de fósforo abaixo dos limites desejados. O fósforo mais alto e a captação de nitrogênio durante a fusão por indução tornam o produto final duro e quebradiço e inutilizável para muitas aplicações críticas. Além disso, a qualidade do ferro-esponja, proveniente principalmente de unidades de produção baseadas em carvão, também é de baixa qualidade, principalmente em termos de metalização e teor de fósforo. Devido a essas desvantagens, o maior uso de DRI no forno de indução resulta em baixo rendimento e maior consumo de energia/energia, bem como maior fósforo no aço.
Emissões ambientais
Como nenhum carvão ou combustível é queimado no forno de indução e nenhum procedimento de refino é executado, as emissões dependem exclusivamente da limpeza e da composição do material carregado. Duas grandes categorias de emissões podem ser distinguidas. A primeira e principal categoria refere-se à limpeza da carga, por ex. ferrugem, sujidade, areia de fundição, tinta, óleo, metal galvanizado ou soldado, todos eles elementos que originam a emissão de poeiras e fumos (orgânicos ou metálicos). A segunda categoria refere-se a reações químicas em altas temperaturas (por exemplo, enquanto se mantém ou ajusta a composição do metal), que pode dar origem a fumos metalúrgicos devido à oxidação.
Além disso, o revestimento refratário (SiO2 ácido, Al2O3 neutro ou MgO básico) pode adicionar uma pequena quantidade de partículas de poeira à emissão. É difícil obter dados de emissão média, pois a limpeza da carga, que é o principal contribuinte para as emissões, varia muito de unidade para unidade.
A taxa de emissão de um forno de indução depende do material de carga que novamente depende do produto que está sendo feito desse forno. Se o produto que está sendo feito for uma fundição de boa qualidade, as emissões são da ordem de 1 a 2 kg/ton de carga de metal, mas se for lingote/tarugo, as taxas de emissão da ordem de 10 a 20 kg/ton de carga de metal são normais . As maiores taxas de emissão ocorrem durante o carregamento e no início do ciclo de fusão. Os tamanhos das partículas variam de 1 a 100 micrômetros, com mais de 50% sendo menores que 10 a 20 micrômetros. O carregamento de sucata oleosa ou perfurações em um forno frio leva à presença de vapores orgânicos nos gases de exaustão.
Enormes quantidades de fumaça e gases quentes são liberadas dos vasos abertos do forno durante as operações do forno de indução e se espalham pelo chão de fábrica, afetando a saúde dos trabalhadores.
Com relação ao potencial poluidor dos fornos de indução, observa-se que o volume, a quantidade e a emissão nociva de contaminantes sólidos e gasosos são bastante baixos quando comparados aos fornos elétricos a arco. O equipamento não precisa ser tão elaborado quanto o forno elétrico a arco para torná-lo rentável para unidades de forno de indução de pequena escala. Ao mesmo tempo, os poluentes emitidos devem estar em conformidade com os regulamentos.
As etapas envolvidas no controle da poluição incluem a captura de fumaça por um mecanismo de capô de sucção projetado adequadamente. A coifa deve aspirar todos os gases de exaustão que devem ser limpos por separador de ciclone. A limpeza adicional de partículas mais finas é realizada por meio de um filtro de mangas ou em um purificador úmido e, em seguida, liberando gases limpos para passar para a atmosfera. O mecanismo do capô de sucção pode ser do tipo capô lateral, giratório ou dossel. O último passo é a eliminação de matéria sólida deixada como lodo ou poeira.
A concentração de partículas na emissão de um forno de indução para a produção de aço líquido não deve exceder 100 mg/cum, expressa em condições de referência de 0 graus C, 101,325 kPa e condições secas sem correção para teor de oxigênio, e compensado por qualquer efeito de ar de diluição para a concentração.
Fornos de indução e de segurança
Trabalhar com metal fundido sempre foi um trabalho perigoso. Os fornos de indução de alta eficiência atuais melhoraram as condições de trabalho, tornando as aciarias locais de trabalho mais frios, limpos e geralmente menos hostis, uma vez que o ruído do calor e os fumos associados aos fornos de combustão não estão lá. No entanto, esses fornos não eliminaram os perigos inerentes ao trabalho próximo ao metal líquido.
Os motivos da maioria dos acidentes nas aciarias com fornos de indução são (i) a introdução de metal úmido ou úmido no fundido, causando uma explosão de água/metal, (ii) falta de habilidade do operador durante a medição de temperatura, amostragem ou adição de ferro ligas, causando respingos de metal, (iii) queda de grandes pedaços de material de carga no banho fundido, causando respingos de metal, (iv) atenção inadequada ao carregamento causando ação de ponte, (v) falha em ficar atrás das linhas de segurança, causando uma situação de aprisionamento , (vi) entrar em contato com condutores elétricos, ignorar chaves de intertravamento de segurança ou entrar em contato com capacitores descarregados incompletamente, causando choques elétricos ou eletrocussão, e (vii) falta de treinamento adequado do operador.
Processo de manufatura
- 5 usos importantes do níquel
- Aspectos importantes do projeto de alto-forno e equipamentos auxiliares associados
- Inclusões em siderurgia e siderurgia secundária
- Forno de indução e siderurgia
- Geração e uso de gás de alto-forno
- Fornos de reaquecimento e seus tipos
- Aspectos Metalúrgicos da Galvanização do Aço
- Eficiência Energética e Produção de Ferro e Aço
- Alto-forno e seu projeto
- Entendendo as operações da planta de sinterização e sinterização