Laminação de aço em laminador de tiras a quente
Laminação de aço em laminador de tiras a quente
Os laminadores de tiras a quente atualmente são laminadores de tiras a quente convencionais ou laminadores de tiras para laminação de placas finas. A principal função do laminador de tiras a quente convencional (HSM) é reaquecer o aço semi-acabado as chapas (laminadas ou fundidas continuamente) às temperaturas de laminação e depois lamina-las mais finas e longas através de uma série de carrinhos de laminação acionados por grandes motores e finalmente enrolando a chapa de aço alongada para seu fácil manuseio e transporte. diâmetro interno de 750 mm nas bobinadeiras, com diâmetro externo de até 2400 mm e com limitações de peso da bobina de até 220 kg por cm de largura. O laminador de tiras a quente fornece bobinas para laminadores a frio, unidades de corte e cisalhamento de tiras como bem como um produto acabado para envio direto aos clientes.A maior parte do material é transportada para fora da área da fábrica por um sistema automatizado de manuseio de bobinas para o corredor de armazenamento.
Os atributos conferidos à tira pelo laminador de tiras laminadas a quente incluem qualidade da superfície, espessura, largura e controle de planicidade, bem como o perfil da tira.
A laminação de placas de aço em laminador de tiras a quente consiste em vários subprocessos e ao final deles é produzido o produto final ‘bobina laminada a quente’. Os principais subprocessos são (i) aquecimento de placas de aço no forno de reaquecimento, (ii) desincrustação da placa aquecida e sua colagem em prensa de colagem, (iii) laminação no desbaste e desincrustação secundária, (iv) laminação em o laminador de acabamento, (v) controle de resfriamento da tira laminada a quente e (vi) bobinamento da tira laminada.
Reaquecimento da laje
Crítico para o laminador de tiras a quente é o forno de reaquecimento. Os modernos laminadores de tiras a quente são equipados com fornos de reaquecimento de viga móvel de última geração que substituíram e superaram os fornos de reaquecimento mais antigos do tipo empurrador. Esses fornos de reaquecimento são nominalmente classificados para produzir placas aquecidas na faixa de 250 toneladas por hora a 300 toneladas por hora, com capacidade de produzir até 25% a mais de sua saída nominal com algum sacrifício na uniformidade da temperatura da placa. O forno precisa de cerca de 350.000 kcal de gás combustível por tonelada de placa para o aquecimento da placa desde a temperatura ambiente até uma faixa de temperatura de 1100 graus C a 1250 graus C. As placas inspecionadas conforme cronograma de laminação são colocadas uma de cada vez no mesa de rolos de carregamento do forno no pátio de lajes e posicionado em frente à porta de carga no forno de reaquecimento. Quando há espaço disponível no forno, os braços empurradores empurram a placa para dentro do forno. Uma vez no interior, as lajes são suportadas cerca de 2,5 m acima do piso do forno por tubos refrigerados a água e revestidos com refratários chamados “skids”. Para minimizar os pontos frios ('marcas de deslizamento') deixados nas lajes, o espaçamento de deslizamento muda em alguns projetos dos fornos de reaquecimento em cerca de dois terços do caminho através do forno. Dois conjuntos independentes de patins, um fixo e outro móvel, revezam-se apoiando a laje enquanto ela passa pelo forno por uma subestrutura maciça energizada por um par de grandes cilindros hidráulicos. Dependendo do projeto do forno, o interior do forno é dividido em várias (cinco a dez) zonas para controle de temperatura. As zonas de pré-aquecimento e aquecimento queimam uma mistura de gás combustível e ar de combustão pré-aquecido com os queimadores no teto e nas paredes laterais do forno, acima e abaixo dos skids, para aquecer a laje quase até sua temperatura de descarga.
A maior parte do pré-aquecimento da laje de aço é conseguida pelos gases quentes de exaustão que passam pelas lajes a caminho dos recuperadores. Qualquer que seja o calor que resta nos gases de escape, pré-aquece o ar de combustão de entrada para cerca de 500°C a 550°C nos recuperadores. Na zona de aquecimento, o aço é aquecido principalmente por radiação pelas paredes quentes do forno. Na zona de imersão, os tamanhos e localizações dos queimadores são tais que mantêm uma temperatura uniforme dentro das zonas para equilibrar quaisquer pontos frios nas lajes.
Divisores refratários ajudam a distinguir fisicamente as zonas, e os sensores de temperatura termopares em todo o forno interagem com os sistemas de controle automático do queimador para manter as temperaturas alvo em cada zona. Modelos de computador complexos calculam a temperatura de saída do moinho de desbaste para obter uma temperatura de destino de descarga do forno. Estimando continuamente o perfil de temperatura através da espessura de cada placa no forno, o computador ajuda o operador a selecionar a taxa de produção e os pontos de ajuste da zona que maximizam a produção de placas de aço aquecidas uniformemente até o mais próximo possível da temperatura alvo . Após o início do processo de laminação, à medida que o aço sai do desbaste, sua temperatura é realimentada ao forno, atualizando os modelos computacionais e informando ao operador do forno quanto à uniformidade da temperatura.
Quando a placa atinge a 'porta de descarga' na extremidade de saída do forno e o computador determina que a placa foi suficientemente aquecida, a porta se abre e os braços do extrator alcançam abaixo da placa, levante-a do skid suportes e puxe-o para fora da fornalha. O forno de reaquecimento geralmente tem dois extratores. Esses extratores podem atuar independentemente um do outro para remover as placas duplamente carregadas uma de cada vez ou em combinação para extrair as placas mais longas. A placa a quente é colocada na mesa de rolos de entrada que a transporta para o desbaste através de um descalcificador.
Descalcificação e dimensionamento de laje
A desincrustação de placas aquecidas é uma obrigação no laminador de tiras a quente para obter uma boa qualidade superficial da tira laminada a quente. A operação do descalcificador precisa ser otimizada para garantir a remoção máxima de incrustações e, portanto, limpeza aprimorada com resfriamento mínimo da placa aquecida.
Depois de deixar o forno de reaquecimento, a placa passa a uma velocidade que varia de 0,15 m/s a 2,0 m/s por uma unidade de descalcificação, um invólucro que emprega dois pares de cabeçotes de pulverização. Estes cabeçotes de pulverização são de design simples e de fácil manutenção e pulverizam água de alta pressão (pressão de água de até 400 kg/sq cm) na laje para remover a camada de ferro oxidado que se forma na superfície da laje na atmosfera rica em oxigênio de o forno de reaquecimento. Esses cabeçalhos geralmente são equipados com bicos avançados para pulverizar água de forma eficaz. O descalcificador é normalmente de design fechado para evitar que a água escape e há um fluxo de água otimizado dentro do descalcificador. O consumo de água para descalcificação varia de 200 cum/h a 700 cum/h.
Os modernos laminadores de tiras a quente são equipados com uma prensa de colagem no lugar de uma biseladora. A vantagem tecnológica essencial da prensa de colagem é que além de resultar em uma grande redução de largura (até 350 mm) em uma passagem, ela produz nitidamente melhor através da formação da placa bem no centro. A prensa de colagem de placas produz "ossos de cachorro" mais planos, levando a um espalhamento reduzido e a uma maior eficiência de colagem. A prensa de colagem oferece uma vantagem distinta de muito mais flexibilidade na produção de tiras a quente. A redução da largura do passe da prensa de colagem permite que o número de tamanhos no lingotamento contínuo seja padronizado para algumas larguras, o que, por sua vez, ajuda no aumento da produtividade na máquina de lingotamento contínuo. Um modo especial de curso curto na cabeça da laje e nas extremidades traseiras resulta em menos perdas de colheita e maior rendimento.
Fresa de desbaste e descalcificação secundária
No laminador de tiras a quente semicontínuo, o laminador de desbaste consiste geralmente em uma ou duas bancadas de desbaste em que a placa é laminada a quente de forma reversível. A placa é laminada em moinho de desbaste 5 ou 7 vezes repetidamente para atingir o requisito de espessura mínima de cerca de 30 mm. O moinho de desbaste também contém rolos de borda que são usados para rolar a borda da placa e centralizá-la.
O laminador de tiras a quente pode ser um laminador de alto desempenho ou um laminador compacto. A diferença entre os dois tipos de laminador é a caixa de bobinas que, nos laminadores a quente compactos, é instalada entre o desbaste e o laminador de acabamento. Ele equaliza as temperaturas da barra de transferência de modo que com apenas seis suportes de acabamento podem ser alcançadas bitolas finais de 1,2 mm. A espessura da barra de transferência que a caixa de bobina pode manipular varia geralmente de 20 mm a 40 mm e a velocidade de bobinagem é de cerca de 5,5 m/s. A capacidade de produção de um laminador a quente compacto está normalmente na faixa de 3,5 milhões de toneladas por ano, enquanto os laminadores de alto desempenho podem atingir até aprox. 5,5 milhões de toneladas por ano.
O alto rendimento para o HSM exige um número mínimo de passes no desbaste, o que é de particular importância para o HSM semicontínuo. Isso significa alta redução por passagem, que só é possível com excelente comportamento de rolagem. É bem conhecido que a mordida do rolo é melhorada com menor teor de carboneto e menor dureza da superfície de trabalho dos rolos de trabalho.
Em um HSM contínuo, o laminador de desbaste é geralmente composto de seis carrinhos de laminação independentes, os últimos quatro a cinco dos quais incorporam pequenos laminadores verticais chamados edgers. As lajes aquecidas são roladas em um suporte de cada vez para produzir as chamadas barras de transferência adequadas para laminação de acabamento. Os bicos de jato de água de alta pressão limpam o ferro oxidado, ou incrustação, da superfície ao longo do caminho. À medida que a barra de transferência sai da última bancada do desbaste, a espessura da borda de ataque da barra é estimada. Da mesma forma, um pirômetro mede o perfil de temperatura da barra da cabeça à cauda e uma câmera especial fotografa ambas as extremidades. Dependendo da bitola, largura e grau do produto a ser laminado, a temperatura média da barra ao sair do último desbaste normalmente varia de 1050°C a 1150°C. Esses dados são coletados em antecipação à laminação de acabamento.
As últimas quatro a cinco fresas de desbaste incorporam bordas para controle de largura. Os moinhos de desbaste individuais são espaçados cada vez mais para acomodar o alongamento das barras de transferência à medida que são laminadas cada vez mais finas. Nas temperaturas muito altas em que o aço é laminado no desbaste, ele é muito plástico e “flui” facilmente. Consequentemente, à medida que a laje é reduzida, a barra tende a se espalhar no sentido da largura em suas extremidades. As biseladoras servem para manter uma largura uniforme ao longo do comprimento da barra.
Os requisitos do moinho de desbaste com relação às propriedades do rolo de trabalho para suportes de desbaste estão resumidos a seguir.
- Alta mordida de rolo com base no alto coeficiente de atrito, permitindo altas reduções por passagem sem trepidação ou deslizamento e, consequentemente, maior rendimento com redução da perda de calor do produto.
- Alta resistência do material da carcaça contra desgaste, fadiga térmica e oxidação/corrosão, resultando em desgaste baixo e homogêneo, permitindo campanhas de rolamento mais longas e tempo de inatividade reduzido.
- Alta resistência ao calor e a rachaduras por fogo, o que significa uma rede de rachaduras de fogo minúscula e suave, evitando altos danos causados por barracas de fábrica.
- Qualidade perfeita da superfície do rolo em tiragens longas, o que está relacionado à ausência de descascamento, formação de faixas e microescamação durante um período de campanha.
- Alta segurança contra falhas de rolo geradas por qualquer tipo de condição de operação, incluindo incidentes no moinho, altas cargas térmicas e mecânicas etc.
Como um cabeçote quadrado é fundamental para rosquear adequadamente as fresas de acabamento e as bobinadeiras, e porque um cabeçote desigual pode danificar as superfícies do cilindro de trabalho ou causar problemas de rosqueamento para o próximo processo de produção, os cabeçotes e extremidades de quase todos os barras de transferência são cortadas por um par de grandes tambores de aço, cada um com uma lâmina de cisalhamento que se estende ao longo de seu comprimento. Com a barra rastejando ao longo da mesa do rolo a cerca de 30 m/min, os sensores detectam sua posição e velocidade para cronometrar os tambores de corte para otimizar a quantidade cortada; uma vez que as barras de transferência têm cerca de 30 mm de espessura, cada colheita extra significa perdas de colheita bastante caras.
Entre a tesoura de corte e a primeira mesa de laminação do laminador de acabamento há normalmente um segundo desincrustante, cuja tarefa é a remoção final da carepa. Pulverizações de água acima e abaixo da barra de transferência a cerca de 200 kg/sq cm de pressão quebram a incrustação que se formou novamente (incrustação secundária), bem como qualquer incrustação que tenha persistido através de operações anteriores de descalcificação. O ajuste de nível dos cabeçotes de pulverização superiores e dos coletores de água permite uma adaptação ideal da barra de transferência que está sendo manuseada. Devido ao arranjo especial do bocal, os diferentes graus de resfriamento na parte superior da barra de transferência são minimizados.
Após a descalcificação secundária, a barra é comprimida por um par de rolos acionados pneumaticamente para soltar mecanicamente qualquer incrustação remanescente, que, à medida que as temperaturas de processamento esfriam, torna-se cada vez mais pegajosa, mesmo quando retorna cada vez mais lentamente às superfícies da peça ainda vermelha. aço quente.
Fábrica de acabamento
O laminador de acabamento da HSM geralmente possui de cinco a sete carrinhos de rolos de acabamento, que reduzem a espessura da barra de transferência até a bitola necessária. A velocidade de laminação é ajustada para permitir que o último suporte realize a redução final na temperatura de acabamento, entre 820°C a 900°C, de modo a alcançar certas propriedades mecânicas na tira laminada a quente. Os laminadores de acabamento rolam a barra de transferência em conjunto, o que significa que cada barra é rolada por todos os suportes de acabamento de uma só vez. O aço a quente é bastante frágil, pois é laminado e a tensão entre as bancadas do laminador de acabamento deve ser controlada de perto em níveis muito baixos para evitar esticar ou rasgar a tira.
Os ajustes são feitos conforme necessário para garantir que a tira passe corretamente por cada um dos moinhos sem enrolar e dobrar ou esticar e rasgar. A posição de cada rolo é realimentada para o sofisticado sistema de automação do laminador de acabamento que, juntamente com as informações das células de carga que monitoram a força de laminação e do medidor de raios X que mede a espessura final da tira, trabalham para ajustar suavemente as folgas e velocidades dos rolos para manter a laminação estável da tira até a espessura necessária, apesar das variações de temperatura presentes em cada barra.
Uma vez que a barra é enfiada entre cada par sucessivo de moinhos, um laçador engata a tira para monitorar a tensão entre os suportes. Os laçadores dispostos entre os suportes de acabamento do HSM garantem o controle correto do fluxo de massa e, portanto, contribuem para a laminação estável da tira acabada até a espessura final da tira. Os loopers são acionados por cilindros hidráulicos.
Para a laminação da tira ultrafina, laçadeiras com medição de tensão diferencial são usadas para detectar diferenças de tensão da tira entre o acionamento e os lados do operador, que podem ser eliminadas girando o conjunto de rolos superiores. Pequenas diferenças de tensão contribuem para um desenroscamento confiável e ajudam a evitar colisões na extremidade traseira.
A função do tensor looper é medir a distribuição das tensões de tração ao longo da largura da tira, o que representa um pré-requisito essencial para o controle automático de planicidade online. Um tensiômetro é preferencialmente disposto entre os dois últimos suportes.
As instalações entre estandes são de vital importância para a produção de tiras laminadas a quente com qualidade superficial superior. Equipamentos importantes incluem (i) guias de entrada e saída, (ii) sistema de resfriamento do rolo de trabalho, (iii) dispositivo anti-descascamento, (iv) sistema de lubrificação da folga do rolo e (v) sistemas de resfriamento e descalcificação entre suportes. A interação próxima de todas essas facilidades é essencial para alcançar um resultado ideal. A proteção lateral com ajuste hidráulico da largura garante o posicionamento exato em um tempo mínimo. As áreas de guia de tiras são projetadas para que todas as peças de desgaste possam ser substituídas rapidamente. A eficiência de resfriamento é melhorada pela seleção e disposição otimizadas dos bicos.
A combinação de resfriamento do intervalo do rolo, lubrificação do intervalo do rolo e sistemas aprimorados de resfriamento do lado de saída reduzem a temperatura do rolo. Isso resulta em uma camada de óxido mais fina na superfície do rolo com menos descamação do rolo de trabalho como consequência. A lubrificação dentro da folga do rolo minimiza o atrito, permitindo assim uma redução da força de rolamento de 20% a 30%. Desta forma é possível redistribuir a força de laminação para otimizar o cronograma de passes e bitolas de tiras finais mais finas. Além disso, são evitadas vibrações ou vibrações no suporte, o que leva a uma vida útil mais longa do rolo.
Uma profunda transformação metalúrgica na estrutura cristalina ocorre à medida que o material esfria, que, dependendo da química específica do material, normalmente está entre 800 graus C e 850 graus C. Além disso, as propriedades mecânicas do produto final respondem em algum grau à temperatura específica na qual o passo final de redução é realizado.
Conseqüentemente, é especificada uma temperatura de acabamento para cada produto e a automação do moinho ajusta a velocidade da primeira bancada do laminador de acabamento com base em sua temperatura e na medida em que se espera que a barra resfrie ao passar por cada bancada, a fim de permitir a tira que sai dos suportes de acabamento para atingir a temperatura alvo. A última operação de trabalho a quente é geralmente realizada acima da temperatura crítica superior de 787,8°C, que permite que o aço laminado passe por uma transformação de fase após todo o trabalho a quente ter terminado. Isso produz um grão uniformemente fino e equiaxial em todo o aço. Se parte da laminação a quente for realizada em aço que já foi parcialmente transformado em ferrita, os grãos de ferrita deformados irão engrossar durante o auto-recozimento que ocorre durante o resfriamento do aço bobinado. Esta condição pode limitar a adequação do aço para algumas aplicações de trefilação severas.
Uma vez que cada barra de transferência passa aproximadamente um minuto no laminador de acabamento, da cabeça à cauda, a temperatura do aço que entra nas bancadas de acabamento é significativamente menor, talvez 100 graus C, no momento em que a extremidade final é laminada em comparação com o cabeceira. Conseqüentemente, uma vez que os primeiros 150 m da tira tenham sido rolados na velocidade da rosca e uma bobina descendente tenha sido rosqueada, o laminador começa a acelerar a uma taxa de 'zoom' que foi calculada a partir do perfil de temperatura da barra quando ela saiu o último moinho de desbaste. Velocidades máximas de até 20 m/s são alcançadas pela automação do moinho buscando manter a temperatura de acabamento especificada em todo o produto final. Um pirômetro colocado após o último estande atualiza os modelos computacionais da usina de acabamento e permite a adição dessa temperatura para registros de qualidade da tira.
Com as tremendas forças de laminação presentes em um laminador, não é suficiente simplesmente ajustar a folga entre os cilindros de trabalho para a espessura desejada e esperar que a tira saia do outro lado nessa espessura. Com forças de laminação regularmente superiores a 3.000 toneladas nas primeiras bancadas de acabamento, pode-se esperar que as carcaças do moinho estiquem até 10 a 15 mm após a barra entrar na mordida ao laminar produtos largos, rígidos e/ou de bitola leve. Ao ajustar as folgas dos rolos para rosqueamento, é fundamental que este fator seja compensado em cada uma das bancadas da fresadora; para isso, modelos sofisticados são usados pela automação do moinho para estimar a força de laminação para cada barra de transferência em cada estande com base, entre outras coisas, na espessura de entrada e saída, largura, grau de aço e temperatura instantânea estimada. Os modelos empregados pela automação da usina são atualizados com os parâmetros de laminação e medições do produto a cada nova laminação de uma nova placa, otimizando continuamente as configurações de automação das usinas. A qualidade do produto e o rendimento da produção se beneficiam da programação de produtos com bitola e classe semelhantes para laminação sucessiva, permitindo que a automação implemente o modelo de laminação utilizado mais recentemente.
Além do grau em que o moinho se estica sob cargas de laminação, os rolos defletem, ou dobram, sob carga, uma vez que estão sendo forçados a se separar no meio pela tira, mas são apoiados nas extremidades pelos rolamentos. Esta deflexão é a fonte do atributo de tira comumente referido como coroa. A coroação de tiras é iniciada nos laminadores de desbaste e continua em cada suporte de laminação sucessiva. A coroa da tira é medida na extremidade de saída dos laminadores de acabamento por um segundo medidor de raios-X de varredura que atravessa para frente e para trás ao longo da largura da tira à medida que o aço é laminado. A espessura medida é comparada com a espessura medida pelo raio-X primário que monitora o medidor da linha central ao longo do comprimento da tira e a diferença é então plotada como um registro de qualidade do produto. Normalmente, o HSM produz material com entre 0,025 mm e 0,075 mm de coroa, dependendo de vários fatores que incluem a bitola, a largura e o grau do produto acabado.
Os operadores de qualquer suporte de rolos têm um grau de controle sobre a forma da folga dos rolos, ajustando os parafusos para aumentar ou diminuir a força de rolo presente naquele suporte, influenciando o grau de deflexão dos rolos. Os últimos quatro carrinhos de acabamento geralmente incorporam dobramento hidráulico do cilindro de trabalho para dar aos operadores controle adicional sobre a forma da folga do cilindro carregado. Os operadores ajustam a flexão do rolo de trabalho nesses suportes para influenciar a coroa no produto final. A dobra do cilindro de trabalho na bancada de acabamento final é usada exclusivamente para criar uma forma de intervalo de rolo que corresponda ao perfil da tira que sai do laminador de acabamento anterior para produzir um produto final plano.
As tecnologias incorporadas em um moderno laminador de tiras a quente para melhorar a qualidade do produto são (i) controle automático de bitola, (ii) controle automático de largura, (iii) dobra de cilindro de trabalho, (iv) coroa variável contínua (CVC), (e v ) compensação de excentricidade de rolo. O CVC é uma forma de alterar o perfil da tira usando rolos com perfil. A folga entre os rolos pode ser alterada por deslocamento axial dos rolos. A técnica CVC também é conhecida como técnica de deslocamento de rolo. A técnica CVC tem uma dinâmica mais lenta, mas um alcance mais amplo do que a flexão do rolo de trabalho. Como o CVC e a dobra de cilindros de trabalho se complementam, ambas as técnicas são normalmente usadas nos modernos laminadores de tiras a quente.
Nos últimos anos, há uma demanda crescente no perfil, espessura, planicidade e superfície da tira quente. Para atender a essa demanda, a tecnologia CVC foi atualizada. As melhorias são tanto no equipamento mecânico quanto no modelo de processo.
Controlar o resfriamento
Depois de sair dos laminadores de acabamento, a tira é transportada por um grande número de rolos acionados individualmente através de quatro a 12 bancos de sprays de água de baixa pressão e alto volume que resfriam a tira incandescente a uma temperatura de bobinamento especificada entre 400 graus C e 900 graus C e em bobinas descendentes. Guias laterais em ambos os lados da mesa de saída procuram manter a ponta da tira apontada para as bobinas; a seção final de guias na frente de cada bobinadeira se ajusta para corresponder à largura da tira e apresenta um sistema pneumático de fechamento rápido que permite ao operador centralizar a extremidade da cabeça da tira quando a bobinagem começa.
Metalurgicamente crítica para as propriedades do aço laminado a quente é a temperatura de bobinagem, pois a bobina esfria dessa temperatura para a temperatura ambiente ao longo de três dias. Essencialmente, um tratamento térmico comparável ao recozimento, as tensões transmitidas ao aço durante a redução da espessura da laje até o calibre da tira quente têm a oportunidade de aliviá-las à medida que a bobina esfria. Embora o aço esteja continuamente recristalizando durante a laminação a quente, reduções na espessura às vezes superiores a 99% e ocorrendo em menos de dez minutos estressam consideravelmente o aço; A temperatura de bobinagem é especificada pelos metalúrgicos do produto para aproveitar e manipular esses níveis de tensão em busca de propriedades mecânicas ideais. O resfriamento da tira laminada a quente após sua laminação na última bancada de acabamento é mostrado na Fig 1.
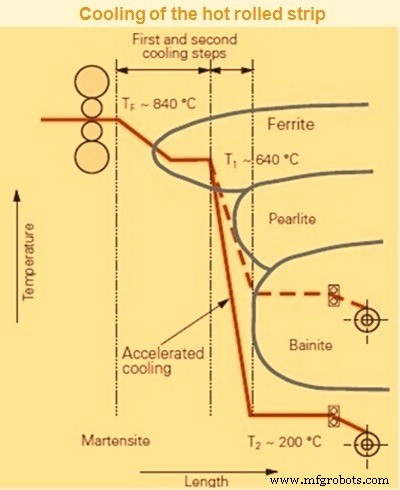
Fig 1 Resfriamento da tira laminada a quente
A área de saída localizada entre o laminador de acabamento e o bobinador do laminador de tiras a quente é necessária para o transporte do material e ajuste da temperatura do material e, portanto, para obter as propriedades mecânicas. A seleção dos espaçamentos dos rolos em função da faixa de espessura da tira garante um transporte confiável, especialmente da cabeça da tira.
Em conjunto com um modelo de resfriamento altamente eficiente, o sistema de resfriamento laminar disposto nesta área garante a temperatura de bobinagem desejada, bem como o resfriamento para alcançar as propriedades mecânicas desejadas do material laminado.
A combinação de sistema de resfriamento laminar e sistema de mascaramento de bordas evita o resfriamento excessivo das bordas da tira, minimizando assim as diferenças de tensão ao longo da largura da tira. Como resultado, a planicidade da tira a frio é melhorada.
O produto vendido como laminado a quente e laminado a quente decapado e lubrificado para ser cortado a laser por um cliente é enrolado a temperaturas relativamente altas para tentar relaxar o aço o máximo possível, de modo que as peças cortadas da bobina fiquem planas mesmo depois que as tensões residuais se resolverem em torno da configuração da peça. Por outro lado, o enrolamento a uma temperatura relativamente fria permite que os aços de qualidade física retenham níveis mais altos de tensão interna e limite o tamanho dos cristais individuais e dos carbonetos que se formam dentro e entre os cristais; cada um desses fatores contribui para níveis de resistência mais altos na tira laminada a quente acabada.
Arrefecer o aço a 200 graus C, à medida que passa a velocidades de até 20 m/s, requer enormes quantidades de água, portanto, um grande número de 152 cabeçotes de pulverização, individualmente valvulados e controlados pelo sistema de automação, encharca o aço de cima e de baixo com cortinas de água. O computador estima, com base na velocidade de rosca da tira e na temperatura de acabamento alvo, quanta água é necessária para resfriar o cabeçote, e a precisão dessa estimativa é confirmada por um pirômetro na frente das bobinadeiras. Como é necessário ajustar o número de sprays em uso, o computador liga e desliga os sprays para atingir a temperatura desejada ao longo do comprimento da bobina. Como os laminadores de acabamento aceleram uma vez que a bobinadeira é rosqueada para continuar a fazer a temperatura de acabamento, cada vez mais sprays são ativados à medida que o aço é laminado para compensar o tempo reduzido que ele passa na mesa de saída.
Até 300 metros cúbicos de água são bombeados a cada minuto em todo o HSM para resfriar tiras laminadas com acabamento, skids de fornos, cilindros laminadores e componentes de bobinas e para desincrustar barras de transferência. Toda a água é reciclada através de um sistema de poços de coleta de incrustações/lodo, através do sistema de resfriamento laminar e de volta para uma das duas torres de resfriamento dedicadas.
Enrolando
A operação de bobinagem começa com um par de rolos de pressão que prendem a extremidade do cabeçote da tira e estabelecem a tensão através da mesa de saída e de volta para os laminadores de acabamento. A extremidade da cabeça é desviada por um portão até o mandril associado ao bobinador e é guiado em torno do mandril por rolos de empacotamento acionados pneumaticamente ligados por aventais.
Uma guia de entrada ajustável hidráulica fornecida na extremidade terminal da mesa de saída serve para centralizar a tira antes que ela entre na estação de bobinagem. A tira que corre na velocidade de laminação final é seguramente agarrada pela unidade de rolo de aperto e direcionada para o mandril da bobina. Um rolo de retenção no lado de entrada da unidade de rolo de pressão evita que a tira (especialmente a tira de calibre pesado) fique saliente à frente do rolo de pressão.
Uma vez que o head-end está em toda a volta do mandril, as voltas começam a se formar ao redor do mandril, forçando os rolos do invólucro. Uma vez que a extremidade da cabeça está firmemente presa e a fricção e a tensão evitam que os envoltórios de aço deslizem em relação ao mandril, os rolos de envoltório se desprendem da bobina crescente de aço. Depois que a tira termina no laminador de acabamento, os rolos de pressão continuam a reter a tensão para evitar que a bobina se desfaça; antes que a ponta da tira seja puxada pelos rolos de pressão, os rolos de embalagem são reengatados. Um carro de bobina hidráulica se move para baixo da bobina e, depois de se levantar para suportar o volume da bobina, retira a bobina do mandril e a coloca em posição para transporte para a máquina automática de encadernação e etiquetagem.
Tendo em vista a ampla faixa de tamanhos das tiras laminadas a quente com espessuras de 1,5 mm a 20 mm, largura de 750 mm a 2200 mm, bem como as condições e custos de manutenção da estação de bobinadeira, uma bobinadeira de três ou quatro rolos oferece um grande número de benefícios práticos.
Processo de manufatura
- Tipos de aço laminado a quente
- Decapagem de tiras laminadas a quente de aço carbono em linhas de decapagem
- Fornos de reaquecimento e seus tipos
- Principais características de um moderno laminador de tiras a quente
- Processo de Laminação para Aço
- Noções básicas de laminação de aço
- Materiais necessários para a Produção de Aço em Forno Básico de Oxigênio
- Laminação Rolls and Roll Shop
- Um guia rápido para a linha de corte de tiras de aço
- Processo de Laminação a Quente e Frio