Processo HYL para Redução Direta de Minério de Ferro
Processo HYL para redução direta de minério de ferro
O processo HYL é projetado para a conversão de minério de ferro (pellet/minério granulado) em ferro metálico, pelo uso de gases redutores em um reator de leito móvel de gás sólido. O oxigênio (O2) é removido do minério de ferro por reações químicas à base de hidrogênio (H2) e monóxido de carbono (CO) para a produção de ferro reduzido direto altamente metalizado (DRI)/ferro briquetado a quente (HBI). O processo HYL é atualmente comercializado sob a marca 'Energiron'.
O processo HYL para redução direta de minério de ferro foi fruto de esforços de pesquisa iniciados pela Hojalata y L.mina, S.A. (mais tarde conhecida como Hylsa), no início da década de 1950. Após a avaliação inicial do conceito, decidiu-se instalar um processo utilizando um forno túnel e várias corridas foram realizadas. O primeiro lote foi feito em um antigo forno (que havia sido construído para aquecer placas) no dia 5 de julho de 1950. Uma parte do minério britado de tamanho variando de 12 mm a 25 mm foi misturada com 40% de coque brisa e 15 % de calcário de mesma granulometria do minério. Essa mistura foi colocada em cadinhos de barro e em 2 tubos de ferro, cada um com 100 mm de diâmetro e 1 metro de comprimento. Foram produzidos 20 kg de DRI de boa qualidade.
A primeira planta a gás, com capacidade projetada de 50 toneladas por dia, não conseguiu atingir níveis aceitáveis de metalização. Durante os 18 meses de operação, passou por diversas mudanças, incluindo a instalação de um reformador de gás natural com o objetivo de aprimorar o gás redutor. Finalmente, sua operação foi suspensa no início de 1955. Após essa tentativa desanimadora, vários experimentos foram realizados e uma planta piloto foi montada para testar as novas idéias. Quando esta planta piloto entrou em operação, ela começou a produzir com sucesso ferro reduzido de boa qualidade a uma taxa de 30 toneladas por dia. Logo atingiu uma produção sistemática de quase 60 toneladas diárias.
Com o sucesso da produção de ferro reduzido direto com o processo de redução direta HYL à base de gás, foram iniciados os estudos para o projeto da primeira planta comercial com capacidade diária de 230 toneladas de DRI. A primeira planta de redução direta em escala industrial entrou em operação em 5 de dezembro de 1957. A planta Hylsa Monterrey 1-M, um reator de leito fixo ou processo em lote, tinha uma capacidade inicial de 75.000 toneladas por ano de DRI. Permaneceu em operação contínua até 1991, pouco antes de completar 35 anos de produção. Em 1978, a American Society for Metals designou a Hylsa' HYL Process Plant 1-M como um marco histórico por ter sido a primeira implementação industrial bem-sucedida da tecnologia de produção de ferro com redução direta. No entanto, a competitividade desta tecnologia foi limitada devido à sua natureza de lote.
No final de 1970, a produção total mundial de DRI para 1970 atingiu 790.000 toneladas, das quais 680.000 toneladas foram produzidas em plantas de processo HYL. No entanto, foi previsto pela HYL que a competitividade desta tecnologia seria limitada devido à sua natureza de lote. Por esta razão, um programa de pesquisa foi iniciado em 1967 para desenvolver um processo contínuo (leito móvel), iniciando a primeira planta industrial em maio de 1980 em Hylsa Monterrey, México, 23 anos após o sucesso de sua primeira planta HYL. O novo processo de forno de poço contínuo foi chamado de HYL III. O novo conceito de processo levou a uma maior produtividade da planta, qualidade DRI superior, menor consumo de energia e operação mais simples da planta.
O nome HYL III foi escolhido, representando a terceira geração da tecnologia HYL. A segunda geração (HYL II) foi basicamente uma modificação do processo original de leito fixo projetado para melhorar a eficiência e reduzir o consumo de gás natural. Durante esta etapa de desenvolvimento do processo foram feitas duas modificações importantes a saber:(i) uso de tubo de liga de alta temperatura no forno de reaquecimento do gás redutor, que permitia aquecer o gás até a temperatura mais alta, e (ii) redução no número de aquecimento forno das quatro unidades originais para duas unidades. No processo HYL II, foi gerado gás redutor (rico em CO e H2), tipicamente por reforma catalítica à base de níquel. No entanto, o processo HYL II nunca foi comercializado, pois o surgimento do processo HYL III ofereceu vantagens significativas.
Desde então, várias melhorias foram incorporadas no processo de leito móvel HYL III. Em 1986 foi incorporado um sistema de remoção de CO2 no circuito de gás redutor, o que resultou em melhorias significativas na produtividade, consumo de energia e qualidade DRI. O consumo de gás reformado foi reduzido em cerca de 50% e a produtividade do forno de cuba também aumentou em cerca de 50%.
Em 1995, a tecnologia de combustão parcial foi incorporada nas plantas HYL através da injeção de O2 na linha de transferência entre o aquecedor a gás redutor e a entrada do forno de cuba. Este esquema permitiu um aumento importante na temperatura do gás redutor, bem como a reforma in situ. Isso diminuiu o consumo de gás reformado em cerca de 25% e aumentou a produtividade do forno de cuba. Em 1988, a alimentação total de gás natural e a injeção de O2 no forno de cuba (reator de redução) levaram ao “esquema de auto-reforma HYL”, onde a composição do gás reformado foi reduzida a zero. Este esquema sem reformador foi denominado processo HYL ZR e foi aplicado com sucesso na planta Hylsa 4M em abril de 1998 e na planta Hylsa 3M5 em julho de 2001.
O uso de revestimento de minérios granulados para redução direta foi introduzido em 1988. O sistema de transporte pneumático (tecnologia Hytemp) e alimentação DRI quente para o EAF foi introduzido em 1993. Durante 1994, a HYL começou a produzir DRI de alto carbono (C) com 3% a 5% de teor de C. O primeiro projeto de planta de descarga dupla (DRI e HBI) do mundo foi colocado em operação em 1997.
O uso de 100% de carga de minério granulado foi feito com sucesso de forma rotineira durante o ano de 2000. Durante 2001, a planta de micromódulos (200.000 toneladas por ano) baseada em HYL ZR (reformador zero) foi introduzida com menos tecnologia de reformador. Plantas de processo HYL ZR baseadas em gaseificação de carvão e gás de coqueria (COG) foram introduzidas. Além disso, a planta DR com capacidade projetada de 2,5 milhões de toneladas por ano em um único módulo foi fornecida durante o ano. Entre o micro módulo e o módulo único de capacidade de 2,5 milhões de toneladas por ano, existem módulos disponíveis com capacidades anuais de 500.000 toneladas, 800.000 toneladas, 1,2 milhão de toneladas e 1,6 milhão de toneladas.
O trabalho de desenvolvimento inicial foi feito pela Hylsa. Em 1977, a Hylsa criou uma nova divisão operacional (tecnologias HYL) com o objetivo de desenvolver e comercializar formalmente as tecnologias de redução direta. Em 2005, Techint Technologies adquiriu tecnologias HYL. Mais tarde esta divisão foi chamada Tenova HYL. Em 2006, uma aliança estratégica foi formada por Tenova e Danieli para o projeto e construção de plantas DR baseadas em gás sob a nova marca 'Energiron'. Energiron é a inovadora tecnologia de redução direta HYL desenvolvida em conjunto pela Tenova e Danieli, e cujo nome deriva do produto exclusivo DRI que distingue esta tecnologia de outros processos disponíveis.
Planta e equipamentos
A planta de redução direta HYL consiste principalmente nas seguintes instalações e equipamentos, juntamente com suas características.
- Um forno de poço de redução que mantém o leito móvel. Este forno de poço possui um sistema de carga de carga de ferro e um sistema de descarga de produto.
- Um circuito de gás redutor, composto por um aquecedor de gás de processo, recuperador de calor de gás superior, unidade de têmpera/depuração de gás superior, compressor de reciclagem de gás redutor, torre de umidificação e tambores de desativação.
- A operação do forno é realizada com consumo mínimo de gás natural e água, além de injeção de O2.
- O sistema de descarga do produto pode ter (i) um resfriador para a produção de DRI a frio, (ii) máquina de briquetagem a quente para a produção de HBI e/ou (iii) sistema de transporte pneumático Hytemp para transferir DRI quente diretamente do eixo forno ao forno elétrico a arco (EAF).
- Um circuito externo de gás de resfriamento, que consiste em uma unidade de têmpera/depuração e um compressor de reciclagem de gás de resfriamento.
- Um sistema de adsorção, baseado em PSA (adsorção por oscilação de pressão), para remoção de dióxido de carbono (CO2) do fluxo de gás redutor.
- Equipamentos de manuseio de minério de ferro, incluindo silo de minério de ferro, transportadores de transferência, estação de triagem, sistema de revestimento de pellets, transportador de alimentação, juntamente com unidades de amostragem e pesagem.
- Sistema de manuseio DRI composto por transportadores e equipamentos relacionados para o transporte de DRI frio.
- Torre de resfriamento junto com equipamentos de filtragem e bombas.
- Sistema de resfriamento de água de processo, baseado em circuito fechado para minimizar o consumo de água, com decantador e lagoas de decantação.
- Um sistema de instrumentação e controle de processo, usando controle distribuído baseado em microprocessador.
- Subestação elétrica, motores elétricos e iluminação.
- Sistema de gás inerte normalmente baseado em gás nitrogênio (N2).
- Um compressor de ar
Descrição do processo
O processo de redução direta Energiron (processo HYL) usa um forno de redução de eixo para produzir DRI. Ele é projetado para converter pelotas/minério de ferro em ferro metálico pelo uso de gases redutores em um forno de poço de leito móvel de gás sólido. O O2 é removido do minério de ferro por reações químicas baseadas em H2 e CO, para a produção de DRI altamente metalizado.
O fluxo de processo esquemático do processo de redução direta é mostrado na Fig 1.
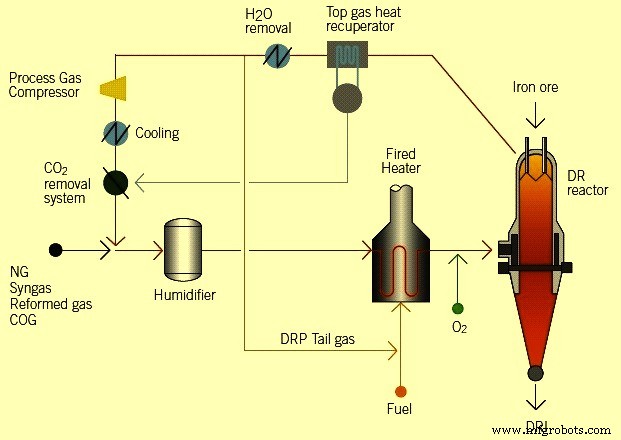
Fig 1 Fluxo esquemático do processo de redução direta
As principais características do processo HYL consistem em (i) utilização de gases redutores ricos em H2 com razão H2/CO superior a 4, (ii) alta temperatura de redução geralmente superior a 930°C e (iii) alta pressão de operação geralmente em a faixa de 5 kg/sq cm a 8 kg/sq cm. A pressão de operação mais alta tem muitas características que incluem (i) menor velocidade do gás, (ii) menor força de arrasto, (iii) menor transporte de poeira, (iv) menor consumo de materiais de rolamento de ferro, (v) maior relação capacidade da planta/ tamanho, e (vi) menor consumo de energia devido ao menor fator de compressão. A alta pressão de operação no forno de cuba também resulta em uma alta produtividade do forno que é de cerca de 9 toneladas por hora por metro quadrado de área.
O processo é flexível para produzir três formas diferentes de produtos, dependendo das necessidades específicas de cada usuário. As três formas de DRI são DRI frio, HBI ou DRI quente (ferro ‘Hytemp’). A descarga DRI a frio é normalmente usada em uma aciaria adjacente próxima à planta de redução direta. Também pode ser embarcado e exportado, desde que sejam seguidos alguns procedimentos e tomados os devidos cuidados para evitar a reoxidação. HBI é o DRI que é descarregado a quente, briquetado e depois resfriado. É um produto comercial geralmente destinado à exportação para o exterior. O ferro Hytemp é o DRI descarregado a quente, transportado pneumaticamente da planta DR para uma aciaria adjacente para sua alimentação direta no forno elétrico a arco (EAF). As opções de descarga para os três produtos, bem como o esquema de fluxo para o ferro Hytemp, são mostrados na Fig 2.
Fig 2 Opções de descarga para os três produtos e o esquema de fluxo para o sistema de ferro Hytemp
A configuração básica do processo é caracterizada por sua flexibilidade para processar diferentes análises de gás. Os gases redutores podem ser gerados (i) diretamente, por reforma in situ de gás natural dentro do forno de poço, (ii) em um reformador externo de gás natural/vapor, (iii) como gás de síntese da gaseificação de combustíveis fósseis, biomassa, etc. , (iv) do gás de exaustão do processo de redução de fundição, como Corex, ou (v) de fontes de gás de forno de coque (COG). Em todos os casos, a configuração do processo corresponde aos mesmos esquemas básicos de reformador zero, ajustando os tamanhos relativos dos equipamentos para a aplicação específica. Para as alternativas de reforma in situ e a vapor, a análise de gás natural (conteúdo de hidrocarbonetos pesados) não é um fator limitante. O gás de "composição" pode ser de qualquer mistura de H2, CO, CO2 e hidrocarbonetos em qualquer proporção.
Uma das características inerentes ao fluxo do processo Energiron que tem grande importância ambiental é a eliminação seletiva dos subprodutos gerados no processo de redução, nomeadamente água (H2O) e CO2. Esses subprodutos são eliminados por meio de sistemas de depuração de gás superior e remoção de CO2, respectivamente. A remoção seletiva de H2O e CO2 otimiza os requisitos de maquiagem. A água produzida durante o processo de redução é condensada e removida da corrente de gás e a maior parte da poeira transportada com o gás também é separada. O gás depurado é então passado através do compressor de reciclagem de gás de processo, onde sua pressão é aumentada. O gás comprimido, depois de enviado para a unidade de remoção de CO2, é misturado com o make-up de gás natural, fechando assim o circuito de gás redutor.
Um fator chave do processo HYL é sua operação pressurizada. O uso de O2 depende do teor de hidrocarbonetos. A metalização DRI e C são controladas independentemente.
Três tipos de reações químicas ocorrem durante o processo. São elas (i) reações parciais de oxidação e reforma, (ii) reações de redução e (iii) reações de cementação. Estas reações são dadas abaixo.
Oxidação parcial e reações de reforma
2CH4 + O2 =2CO + 4H2
CH4 + H2O =CO + 3H2
2H2 + O2 =2H2O
CO2 + H2 =CO + H2O
Reações de redução
Fe2O3 + 3 H2 =2 Fe + 3 H2O
Fe2O3 + 3 CO =2 Fe + 3 CO2
Reações de carburação
3 Fe + CH4 =Fe3C + 2 H2
3 Fe + 2 CO =Fe3C + CO2
3 Fe + CO + H2 =Fe3C + H2O
A reforma do gás natural requer (i) um certo nível de oxidantes (H2O e CO2), que devem ser cuidadosamente controlados, (ii) uma alta temperatura, como resultado da combustão parcial, e (iii) um catalisador ativo, que é fornecido pelas unidades de ferro metálico a partir do minério de ferro já reduzido. Os oxidantes produzidos pelas reações de redução são parcialmente consumidos pelas reações de reforma. Desta forma, uma vez em contato com o material sólido dentro do forno de cuba, ocorre a reforma do metano in situ devido ao efeito catalítico do ferro metálico (Fe). Nestas condições, o metano está sempre em contato com o novo catalisador (Fe metálico em DRI) uma vez que o DRI está sendo continuamente removido do forno de cuba. Portanto, a geração e a redução de gás redutor in situ ocorrem em um ambiente altamente eficiente. Este processo de reforma é altamente endotérmico e continua até o ponto em que a temperatura ainda é alta o suficiente. Uma vez que a temperatura cai abaixo de um certo nível, a reforma in-situ não ocorre e apenas a redução do minério de ferro ocorre. A maior parte da carburação DRI ocorre por craqueamento do metano (CH4) para produzir carboneto de ferro (Fe3C).
O processo Energiron ZR diminuiu o tamanho e melhorou a eficiência das plantas de redução direta HYL. Os gases redutores são gerados in situ no forno de cuba de redução, através da alimentação de gás natural como complemento do circuito de gás redutor e injeção de O2 na entrada do forno de cuba. No processo, a eficiência de redução ideal é alcançada, uma vez que os gases redutores são gerados na seção de redução. Por isso, não é necessário um reformador de gás redutor externo. Normalmente, a eficiência energética geral do processo ZR é superior a 80%, o que é otimizado pela reforma in situ dentro do forno de cuba. O produto leva a maior parte da energia fornecida ao processo, com perdas mínimas de energia para a atmosfera.
O impacto no tamanho da planta da eliminação do reformador de gás externo é significativo. Para uma capacidade de 1 milhão de toneladas por ano, a necessidade de área reduz em cerca de 60%. Isso também facilita a localização da planta DR adjacente à aciaria.
Vantagem adicional do processo ZR é a flexibilidade para a cementação do DRI, que permite atingir níveis de C de até 5%. Isso se deve ao potencial de cementação aprimorado dos gases dentro do eixo, que permitem a produção principalmente de Fe3C. O DRI com alto teor de Fe3C tem uma reatividade muito menor do que o DRI normal, pois é necessário maior calor de dissociação para Fe3C.
O processo Energiron também pode utilizar a reforma convencional do gás natural por vapor, que caracteriza o processo HYL há muito tempo. Outros gases como H2, gás de síntese obtido da gaseificação de carvão, coque de petróleo e combustíveis fósseis similares, gás de coqueria (COG), entre outros, também são possíveis fontes de gás redutor, dependendo da situação específica e da disponibilidade do gás. Essa flexibilidade está disponível, pois o processo Energiron ZR é independente da fonte de gás redutor, sem a necessidade de recircular os gases de volta para um reformador para completar o ciclo químico do processo.
Gases redutores quentes são alimentados dentro do forno de cuba na zona de redução. Esses gases fluem em contracorrente ascendente para o leito móvel da carga de ferro. A distribuição do gás é uniforme e há um alto grau de contato direto entre gás e sólidos. O gás de exaustão (gás superior) sai do forno de poço a cerca de 400°C e passa pelo recuperador de calor do gás superior, onde o calor do gás é recuperado para produzir vapor. Alternativamente, o calor do gás de exaustão pode ser utilizado para pré-aquecer a corrente de gás redutor e, em seguida, o gás de exaustão pode ser resfriado através do processo de têmpera/depuração.
Para DRI frio, um gás de resfriamento é alimentado na parte cônica inferior do forno de cuba a cerca de 40°C, fluindo em contracorrente ascendente para o leito móvel DRI. A distribuição do gás é uniforme e há um alto grau de contato direto entre o gás e o sólido, sem restrições físicas ao fluxo de sólidos ou gases no interior do forno.
O DRI quente é descarregado por meio da válvula rotativa do forno de cuba, através da válvula desviadora, que fornece o material para o sistema Hytemp ou para um resfriador externo alternativo (para produção de DRI a frio). O transporte pneumático é normalmente realizado na mesma taxa que a taxa de produção do forno de cuba.
Para a produção de HBI, o DRI quente é continuamente descarregado a uma temperatura superior a 700 graus C para as máquinas de briquetagem a quente dispostas abaixo. O HBI é resfriado em esteiras vibratórias de resfriamento usando água de resfriamento e depois descarregado na esteira de transporte HBI.
O ferro Hytemp utiliza sistema pneumático para o transporte de DRI quente para o forno elétrico a arco (EAF). Ele usa nitrogênio (N2) ou gás de processo como gás de transporte. É um processo ecologicamente correto, pois o DRI é mantido fechado desde o momento da descarga do forno de cuba de redução até o momento em que é descarregado no EAF. O sistema tem a flexibilidade de alimentar dois EAFs a partir de um forno de eixo único. Na parte inferior do forno de cuba, o DRI é descarregado para o sistema de transporte pneumático onde circula o fluxo de gás quente proveniente do aquecedor a gás e é utilizado para transportar o DRI. Para evitar a degradação, o DRI é transportado pelo aumento da pressão em vez da velocidade do gás. Quando o DRI quente atinge as caixas de armazenamento na parte superior do EAF, o DRI e os gases são separados. O gás é enviado para um purificador para limpeza e resfriamento. Em seguida, é comprimido e aquecido para reciclagem. Antes de entrar no aquecedor a gás, o gás de compensação é adicionado para compensar as perdas ao separar o DRI do gás de transporte. O DRI quente separado do gás de transporte é enviado para uma caixa de transição para passar da pressão do sistema de transporte para a pressão atmosférica. Da caixa de transição DRI vai para a caixa de armazenamento para ser alimentada no EAF por gravidade. O DRI quente também pode ser enviado do forno de cuba para um resfriador externo quando a aciaria não estiver pronta para usar ou armazenar o DRI quente. O cooler externo normalmente tem capacidade para resfriar toda a produção de DRI.
Em uma configuração de processo HYL III típica, o calor sensível do gás reformado quente e dos gases de combustão do reformador é usado principalmente para geração de vapor. Os requisitos de vapor para a planta de processo DRI são para dois usuários finais:(i) vapor para reforma e (ii) vapor de exaustão para o sistema de absorção de CO2 no circuito de redução. A quantidade e a pressão do vapor produzido são especificadas para atingir um ótimo equilíbrio térmico e mecânico da planta. Normalmente, o vapor é produzido em alta pressão (63 kg/sq cm), a fim de aproveitar ao máximo a entalpia do vapor para geração de eletricidade em um único turbogerador de alta eficiência, antes de ser usado para reforma e no stripper de CO2 re -caldeira. Desta forma, a necessidade total de energia elétrica para a planta pode ser gerada dentro da planta. A capacidade do turbogerador é de cerca de 90 kWh/ton em caso de descarga a frio ou 105 kWh/ton HBI em caso de descarga a quente, o que é suficiente para atender a necessidade total de energia elétrica da planta.
Uma característica importante da planta de redução direta Energiron é a possibilidade de projetar o processo para uma necessidade zero de água de reposição. Isso é possível principalmente porque a água é um subproduto da reação de redução, uma vez que é condensada e removida da corrente de gás. Como consequência, com a adoção de um sistema de água de circuito fechado baseado no uso de trocadores de calor de água em vez de torres de resfriamento convencionais, não há necessidade de água fresca de reposição e, na verdade, um pequeno fluxo de água fica disponível na bateria limite.
Parâmetros operacionais e consumos específicos
As características típicas do produto do processo Energiron ZR são dadas na Tab 1.
Guia 1 Características típicas do produto | |||||
Sl.Nº | Item | Unidade | DRI | HBI | Hytemp ferro |
1 | Metalização | % | 92 – 95 | 92 – 95 | 92 – 95 |
2 | Carbono | % | 1,5 – 5,5 | 1,5 – 2,5 | 1,5 – 5,5 |
3 | Temperatura | Grau C | 40 | 40 | > 600 |
4 | Densidade de massa | toneladas/cum | 1,60 | 2,50 | 1,60 |
5 | Densidade aparente | toneladas/cum | 3,20 | 5,00 | 3,20 |
6 | Tamanho nominal | mm | 6 – 15 | 110 x 60 x 30 | 6 – 15 |
7 | Fe3C | % | 25 – 60 | 25 – 30 | 25 – 60 |
Os parâmetros operacionais típicos e os consumos específicos para o processo Energiron ZR são apresentados na Tab 2.
Tab 2 Parâmetros operacionais típicos e consumo específico para o processo HYL ZR | |||||||
Sl. No. | Item | Unidade | DRI frio | HBI | DRI quente | ||
1 | Carbono | % | 4,5 | 2,5 | 2,5 | 4,5 | 4,5 |
2 | Metalização | % | 93 | 93 | 93 | 93 | 93 |
3 | Temperatura DRI | Grau C | 40 | 40 | 700 | 700 | 700 |
4 | Carga de ferro | toneladas/tonelada | 1,36 | 1,39 | 1,41 | 1,36 | 1,39 |
5 | Gás natural | Gcal/ton | 2,25 | 2,20 | 2,23 | 2,35 | 2,25 |
6 | Eletricidade | kWh/ton | 65 | 65 | 80 | 65 | 65 |
7 | Oxigênio | N cum/ton | 42 | 53 | 53 | 48 | 53 |
8 | Água | Goma/ton | 0,8 | 0,8 | 1.1 | 0,8 | 0,8 |
9 | Nitrogênio | N cum/ton | 12 | 12 | 19 | 18 | 18 |
As emissões típicas do processo Energiron ZR são fornecidas na Tab 3.
Tab 3 Emissões típicas do processo HYL ZR | ||||
Sl. No. | Emissões | Unidade | Valor | |
1 | NOx com queimadores de NOx ultrabaixos | mg/N cum | 50 – 80 | |
2 | NOx com remoção catalítica seletiva | mg/N cum | 10-50 | |
3 | CO | mg/N cum | 20-100 | |
4 | Poeira da pilha do aquecedor/reformador | mg/N cum | 1 – 5 | |
5 | Poeira do despoeiramento do manuseio de materiais | mg/N cum | 5 – 20 | |
Processo de manufatura
- Ferro para roupas
- Ferro
- O processo de sinterização de finos de minério de ferro
- Processo Finex para Produção de Ferro Líquido
- Processo HIsmelt de fabricação de ferro
- Processo HIsarna para fabricação de ferro
- Processo CONARC para Siderurgia
- Beneficiamento de Minérios de Ferro
- Processo de Laminação para Aço
- Entendendo o processo de fundição de minério de ferro