Injeção de resíduos plásticos em um alto-forno
Injeção de resíduos plásticos em um alto-forno
A reciclagem de resíduos plásticos (WP) injetando-os em alto-forno (BF) está sendo praticada em poucos BFs principalmente no Japão e na Europa. O uso de plásticos no BF também recupera energia do WP e, portanto, às vezes é considerado como recuperação de energia. Os processos de fabricação de ferro baseados em BF podem utilizar WP por qualquer um dos seguintes métodos.
- Carbonização com carvão para produzir coque.
- Carregamento superior no BF, embora isso gere alcatrão indesejado da decomposição dos plásticos no eixo.
- Gaseificando os plásticos fora do BF. O gás de síntese resultante é então injetado através das ventaneiras.
- Injeção como um sólido através das ventaneiras de forma semelhante ao carvão pulverizado (PC). Normalmente é feito como uma co-injeção de WP e carvão no BF.
A primeira tentativa de injeção de resíduos plásticos (WPI) em uma BF foi feita na Aciaria de Bremen em 1994, com a injeção comercial começando um ano depois. O primeiro sistema integrado para injeção de resíduos plásticos foi na NKK’s (agora JFE Steel) Keihin Works no Japão.
A injeção de WP no BF tem várias vantagens ambientais, operacionais e econômicas. Estes incluem o seguinte.
- Redução na quantidade de resíduos plásticos depositados em aterros ou incinerados.
- Menor consumo de coque e PC, economizando recursos de carvão. No entanto, nem o WP nem o PC podem substituir completamente o coque. A quantidade de coque substituído no BF depende em parte da qualidade do WP.
- Há economia de recursos energéticos. O benefício da economia de recursos do WPI misto é de cerca de 11 giga calorias por tonelada (Gcal/t).
- Há uma diminuição nas emissões de dióxido de carbono (CO2), uma vez que a energia de combustão do WP é geralmente pelo menos tão alta quanto a do PC normalmente injetado, e sua maior proporção de hidrogênio (H2) para carbono (C) significa menos CO2 é produzido dentro do BF a partir dos processos de combustão e redução de minério de ferro.
- O consumo de energia é menor, pois o H2 é um agente redutor mais favorável do que o C. A regeneração do H2 é mais rápida e menos endotérmica do que a regeneração do monóxido de carbono (CO). Assim, o WPI pode reduzir o consumo de energia, o que também significa menores emissões de CO2.
- Existe uma alta eficiência energética que é de pelo menos 80%. Cerca de 60% dos plásticos injetados são consumidos na redução do minério de ferro, e cerca de 20% da energia dos 40% restantes dos gases são utilizados como combustível dentro da siderúrgica. Assim, a utilização do WP é um processo eficiente em um BF.
- WP tem menor teor de enxofre (S) e álcalis do que o carvão. Injetores com baixos teores de S são desejados devido aos efeitos do S na qualidade do metal quente (HM). Os álcalis podem contribuir para a degradação do coque, desintegração do sinter e deterioração do revestimento refratário do forno.
- Há menores emissões de dioxinas e furanos. As emissões de dioxina na Aciaria de Bremen foram de 0,0001 a 0,0005 nanogramas por metro cúbico (ng/cum) de gases de escape, valores bem abaixo das normas. Normalmente, não há contaminação adicional de gás, de modo que o gás BF superior pode ser usado na usina siderúrgica.
As principais desvantagens do WPI são o custo da coleta e tratamento do material. WP vêm de muitas fontes, incluindo famílias, indústria e agricultura e, portanto, são amplamente distribuídos. Assim, a coleta e seu tratamento são caros. Os resíduos são altamente heterogêneos, constituídos por misturas de vários tipos de plásticos. Diferentes resíduos plásticos precisam de processamento diferente. Plásticos com alto teor de cloro (Cl), como policloreto de vinila (PVC), precisam ser desclorados, aumentando os custos de preparação. Os compostos de Cl podem corroer o revestimento refratário BF e as tubulações na planta de limpeza de gás BF superior (GCP). O desempenho do BF é predominantemente governado pela qualidade e consistência do WP, coque e minério de ferro.
A qualidade do WP como PC influencia a qualidade do HM, estabilidade e produtividade do BF e a composição do gás do BF superior. Uma vez injetados, o desempenho de combustão dos plásticos é importante, pois estes podem influenciar negativamente a operação do BF.
Tipos de plásticos
Os plásticos são normalmente feitos de moléculas simples de hidrocarbonetos (monômeros) derivadas de petróleo ou gás. Estes sofrem polimerização para formar polímeros mais complexos a partir dos quais os produtos são fabricados. Aditivos, como antioxidantes, corantes e outros estabilizantes, são adicionados para dar propriedades específicas aos plásticos.
O plástico é um termo geral que descreve uma variedade de materiais e compostos. Existem mais de 20 grupos distintos de plásticos com centenas de variedades. Estes podem ser classificados em dois tipos principais, a saber (i) termoplásticos e (ii) termofixos. O segundo tipo consiste em plásticos que foram endurecidos por um processo de cura. Uma vez endurecidos, não podem ser amolecidos por aquecimento e, portanto, não são adequados para injeção de BF. Estes incluem resinas de poliuretano, epóxi e fenólicas.
Os principais tipos de plásticos indicados para injeção em BF são os termoplásticos, que amolecem quando aquecidos e endurecem no resfriamento. Estes consistem em cinco famílias principais são (i) polietileno (PE), que inclui polietileno de baixa densidade (LDPE) e polietileno de alta densidade (HDPE), (ii) polipropileno (PP), (iii) polietileno tereftalato (PET), (iv ) policloreto de vinila (PVC), e (v) poliestireno (PS), na forma de PS sólido e poliestireno expandido (EPS).
Os BFs onde o WPI foi realizado pela primeira vez utilizaram plásticos de embalagens e recipientes. BFs injetam WP misto, mas isso nem sempre é definido. Uma definição comumente usada é que WP misto inclui todas as embalagens plásticas que não são garrafas.
WP é um material altamente heterogêneo. Consiste principalmente em polímeros de hidrocarbonetos combustíveis e aditivos. Estima-se que apenas 3% do C total usado como agente redutor permanece não oxidado. Os polímeros têm propriedades físicas e químicas diferentes. A composição química dos principais grupos de polímeros é apresentada na Tabela 1. Os injetores consistem em misturas desses grupos de polímeros (e, além disso, podem conter PVC). Assim, a tabela inclui composições típicas do WP. Para fins de comparação, são fornecidas a composição química do PC e do injetor de óleo combustível.
Guia 1 Composição química típica de resíduos de plástico, PC e óleo combustível | |||||||||
Elemento | Unidade | PE | PP | PS | ANIMAL DE ESTIMAÇÃO | PVC | Mistura de resíduos plásticos | PC | Óleo combustível |
Carbono | % | 85,60 | 85,75 | 92,16 | 64,71 | 41,40 | 77,80 | 79,60 | 85,90 |
Hidrogênio | % | 14.21 | 14.15 | 7,63 | 3,89 | 5,30 | 12h00 | 4,32 | 10,50 |
Enxofre | % | 0,03 | 0,90 | 0,97 | 2,23 | ||||
Cinza | % | 0,19 | 0,10 | 0,21 | 0,17 | 0,40 | 4,90 | 9,03 | 0,05 |
Cloro | % | 47,70 | 1,40 | 0,20 | 0,04 | ||||
Potássio | % | 0,05 | 0,27 | 0,001 | |||||
Sódio | % | 0,09 | 0,08 | 0,001 |
O WP misto deve atender a determinados requisitos de especificação. Os valores típicos para estes são 3% ou menos de umidade, 0,4% ou menos de cloretos e 8 mm ou menos de tamanho de partícula. Existem limites para a quantidade de metais pesados e traços de metais na mistura WP, pois estes podem afetar a qualidade do HM. A especificação típica é fornecida na Tab 2.
Tab 2 Especificação típica para metais pesados e oligoelementos em resíduos plásticos | ||
Elemento | Unidade | Valor |
Cloro | % | Menos de 2 |
Enxofre | % | Menos de 0,5 |
Mercúrio | grama/ton | Menos de 0,5 |
Cádmio | grama/ton | Menos de 9 |
Liderar | grama/ton | Menos de 250 |
Zinco | grama/ton | Menos de 1.000 |
Cobre | grama/ton | Menos de 1.000 |
Arsênico | grama/ton | Menos de 5 |
Cromo | grama/ton | Menos de 500 |
Níquel | grama/ton | Menos de 500 |
Em geral, os plásticos usados para WPI no BF têm as seguintes propriedades.
- WP tem alta relação H2/C (normalmente maior que o carvão). A injeção de plásticos aumenta a quantidade de H2 dentro do BF e no gás BF superior. Um aumento no teor de H2 do gás bosh reduz a densidade do gás bosh e, portanto, reduz a queda de pressão ou permite um fluxo de gás maior para a mesma pressão. Como a redução por H2 é menos endotérmica do que a redução direta, há uma diminuição nos requisitos de energia. A capacidade do H2 e do vapor de água (H2O) de difundir para dentro e para fora das partículas de carga de minério individual é significativamente maior do que CO e CO2. A maior difusibilidade promove taxas de redução mais rápidas, especialmente em temperaturas mais baixas. A temperatura ideal de chama adiabática da pista (RAFT) também é menor devido ao maior teor de H2 na pista. No entanto, uma maior concentração de H2 no eixo BF pode levar a quantidades aumentadas de finos de coque no eixo, diminuindo assim a permeabilidade.
- WP tem alto poder calorífico (CV), em muitos casos maior que PC. O CV típico de PE é de cerca de 11 milhões de calorias por quilograma (Mcal/kg), PS é de cerca de 9,7 Mcal/kg, PET é de cerca de 5,6 Mcal/kg e PVC é de cerca de 4,5 Mcal/kg (embora existam grandes variações entre e PVC flexível). Quanto maior o CV, maior a quantidade de calor fornecida pelo material e, portanto, maior a redução no consumo de coque.
- WP tem baixo teor de S e alcalino (geralmente menor que o carvão).
- WP tem baixo teor de cinzas se não houver enchimento de plástico (normalmente menor que o carvão, mas maior que o óleo combustível). , pouca escória adicional é produzida. Mas a injeção de WP levou a um aumento na queda de pressão (queda na permeabilidade do forno), o que tem sido atribuído ao componente de cinzas originário do WP. O alto ponto de fusão (cerca de 1750 graus C) da cinza significa que ela não forma facilmente escória.
- WP tem alto teor de Cl se o PVC estiver presente. Quase todo o cloro sai do BF como ácido clorídrico (HCl), que pode corroer as tubulações através das quais o gás do BF superior flui. O PVC é normalmente removido do WP, embora os processos de descloração tenham sido desenvolvidos. O teor de cloro da mistura WP é normalmente limitado a menos de 2%, ou seja, cerca de 3% de PVC. A preocupação foi expressa sobre a possível formação de dioxinas e furanos através do HCl gerado, mas as medições no gás BF superior mostraram baixos teores.
A força e a dureza do WP podem ser um problema. Plásticos aglomerados de baixa resistência são facilmente quebrados durante o transporte (o que pode levar a problemas de bloqueio e combustão e, portanto, redução da eficiência de combustão (CE) O uso de WP em BF permite a recuperação adicional de materiais ferrosos presentes nos fluxos de resíduos ricos em plástico. A injeção de 1 kg de WP normalmente substitui cerca de 1,3 kg de PC e cerca de 1 kg de óleo pesado em BF. A substituição de coque por WPI é limitada a cerca de 30%, embora valores de 40% tenham sido citados. BF precisa de um injetor consistente qualidade para operação estável, por isso a preparação do WP é um passo essencial.
Preparação de WP para injeção
A qualidade dos injetores WP é importante não apenas em termos de sua utilização no próprio BF, mas também no preparo, manuseio e distribuição dos materiais ao forno. O injetor WP é preparado e transportado para uma tremonha de armazenamento. Em seguida, é transportado pneumaticamente através de tubulações individuais ou por meio de um distribuidor para as ventaneiras individuais.
Dois dos requisitos mais críticos para o uso bem-sucedido do WP em BF são a disponibilidade e os custos de processamento. Os resíduos são muitas vezes altamente heterogêneos e muitas vezes misturados com outros materiais. Assim, a coleta e triagem de resíduos contendo resíduos plásticos é dispendiosa. O objetivo da planta de processamento é fornecer uma matéria-prima de qualidade consistente com o tamanho de partícula necessário e em quantidade suficiente. A extensão do processamento necessário depende da condição em que os resíduos são recebidos.
Materiais estranhos, como metais e areia, precisam ser removidos, pois podem causar problemas, incluindo abrasão nos sistemas de injeção e dos elementos de moagem em moinhos e menor qualidade do HM. Aditivos adicionados a certos produtos plásticos durante a fabricação também podem levar a problemas de abrasão. Pequenas quantidades de papel, pedras e areia incluídas nos plásticos não causam problemas, pois são descarregadas na escória BF.
O material residual contém muitos tipos diferentes de plástico que requerem triagem para tratamento separado. Isso aumenta os custos de preparação. Além disso, os custos são influenciados pelo tamanho de partícula necessário, o que afeta a eficiência de combustão e gaseificação do WP. A automação, sempre que possível, pode ajudar a reduzir esses custos. O material residual coletado é normalmente separado em duas correntes, a saber (i) plástico sólido, que é triturado, os contaminantes metálicos removidos magneticamente e, em seguida, triturados em pedaços de 6 mm a 10 mm, e (ii) filme plástico que é cortado em pedaços , o PVC removido por separação centrífuga, e então fundido e aglomerado pelo uso do calor de fricção para formar pellets com tamanho de partícula de 6 mm a 10 mm.
No caso, o WPI inclui resíduos municipais, então os resíduos são tratados de maneira semelhante (como fluxos de plástico sólido e filme). Pode haver necessidade de uma etapa de descloração. Os pellets de PVC separados são aquecidos com coque em um forno rotativo sob atmosfera de nitrogênio (N2) a cerca de 300°C a 350°C, decompondo-os em hidrocarbonetos e ácido HCl. Os hidrocarbonetos são separados do coque e injetados no BF. O ácido HCl recuperado pode ser usado na siderurgia ou vendido. A resistência dos plásticos aglomerados e sua combustibilidade podem ser melhoradas pela adição de carbonato de cálcio (CaCO3).
Na Europa, foi desenvolvido um processo chamado Redop (REDução de minério de ferro em BF por plásticos de resíduos municipais). A pasta da fração plástica misturada (separada dos resíduos municipais) é aquecida em um reator agitado a uma temperatura de 230°C a 300°C. O ácido HCl liberado é neutralizado pela adição de uma base solúvel em água diluída. Os plásticos desclorados fundem-se em gotículas, cujo tamanho é determinado pela agitação e pelos vestígios de celulose ainda presentes. Após o resfriamento, as gotículas de plástico solidificam em grânulos com mais de 0,15% de Cl que são adequados para injeção em BF.
Sistema de injeção
O sistema de injeção transporta e mede pneumaticamente o WP do silo de armazenamento através do vaso injetor, onde é pressurizado até ou acima da pressão BF, até as lanças de injeção da ventaneira. As lanças injetam o WP em quantidades iguais através das ventaneiras, que são dispostas simetricamente ao redor da circunferência do BF. Um fator crítico no projeto do sistema de distribuição é garantir a alimentação uniforme do redutor para cada ventaneira sem flutuações na rota de entrega do WP. Qualquer interrupção no fornecimento do WP pode levar rapidamente a sérios problemas. Quanto maior a taxa de injeção, mais graves são as consequências de uma interrupção não planejada.
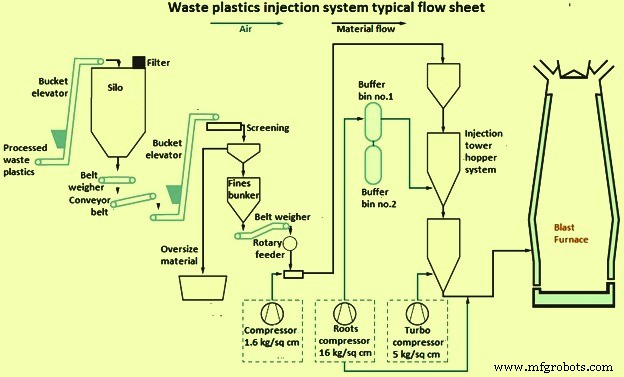
Fig 1 Fluxograma típico para sistema de injeção WP
Caso o WP esteja sendo injetado junto com o PC, ele pode ser transportado (i) através de sistemas de injeção e lanças completamente separados, (ii) através de sistemas de injeção separados para uma lança comum e (iii) como uma mistura. Na maioria dos casos, o carvão e o WP são transportados separadamente por causa de seus diferentes tamanhos de partículas (o carvão é pulverizado enquanto o WP está na faixa de tamanho de 1 mm a 10 mm) e densidades.
São necessários pelo menos dois vasos de injeção para fornecer um fluxo WP contínuo para o BF. Basicamente, seguem-se dois arranjos desses navios.
- Arranjo em série onde o vaso superior reabastece periodicamente o inferior, que é sempre mantido sob pressão, e que injeta o WP continuamente no BF. Assim, os recipientes de injeção são continuamente pesados e a taxa de fluxo do WP é cuidadosamente controlada. Incrustação das caixas por cotão de plástico pode ocorrer.
- Arranjo onde os dois vasos injetam alternadamente. Uma operação de sobreposição é necessária para manter a injeção de WP durante o período de troca.
O WP dos vasos de injeção pode ser transportado (i) por tubulações individuais para cada ventaneira com a quantidade de WP controlada independentemente e carregada em cada tubulação, e (ii) por uma tubulação comum para um distribuidor adjacente ao BF que então divide igualmente o WP nos tubos individuais que levam a cada ventaneira. Uma vantagem do segundo método é que a distância entre a instalação de preparação e o BF pode ser maior do que com o sistema de tubulação individual. Diferenças no encaminhamento dos tubos para as ventaneiras e a inevitável divisão desigual do WP nos pontos de divisão podem resultar em uma alimentação desigual para as ventaneiras. Desequilíbrios também podem causar desgaste desigual nas tubulações e no distribuidor.
Dependendo da proporção de WP para gás de transporte, o WP é transportado pneumaticamente do recipiente de injeção para as ventaneiras em (i) fase diluída ou (ii) fase densa. O gás de arraste para WP é geralmente ar comprimido. A velocidade do gás para WP em sistemas de fase densa é de 3 metros por segundo (m/s) a 8 m/s. Algumas plantas usam o transporte de fase diluída para os pellets de plástico (até 10 mm).
A velocidade do gás de arraste deve ser sempre maior que a velocidade mínima de transporte para evitar bloqueios. Essa velocidade mínima depende de vários parâmetros, incluindo a pressão do sistema e o diâmetro do tubo, e essas variáveis interagem entre si. A baixa velocidade em sistemas de fase densa significa baixo desgaste de tubulações e componentes, enquanto a alta velocidade de sistemas de fase diluída pode levar ao desgaste, principalmente em curvas de tubos. A taxa de desgaste é determinada pela dureza, forma e velocidade das partículas. Os aglomerados de plástico têm um formato de partícula irregular que pode causar erosão, enquanto os pellets de plástico extrudado têm um formato regular. As partículas de plástico trituradas são mais duras do que as pelotas aglomeradas. Revestir as partes dos tubos propensas à erosão com, por exemplo, um material elastômero de uretano proporcionará resistência à abrasão, além de retardar o acúmulo de finos que podem levar a bloqueios.
As propriedades do WP relacionadas a bloqueios de linha de transferência incluem (i) teor de umidade que precisa ser controlado para evitar bloqueios e (ii) a presença de partículas ultrafinas. A distribuição do tamanho das partículas de plásticos misturados aglomerados é importante. A proporção de partículas de tamanho inferior a 250 micrômetros (mícron) deve ser limitada a 1% quando a especificação de tamanho de partícula é de 0 mm a 10 mm e os grânulos são transportados em uma fase diluída. Além disso, para uma injeção estável, é essencial que cerca de 50% dos plásticos injetados tenham um tamanho de partícula superior de 6 mm. O uso de partículas plásticas fibrosas é difícil porque as fibras se aglomeram para formar partículas maiores bloqueando os tubos. Fluff de plástico também pode atolar os canos. Partículas de plástico podem se tornar eletrostaticamente carregadas durante o transporte através de tubulações, fazendo com que elas adiram às paredes. Em casos graves, os tubos podem bloquear, especialmente nas curvas. A adição de um material de granulação fina de fluxo livre pode influenciar o efeito.
Os bloqueios podem ser diminuídos por melhorias no layout da tubulação e nos sistemas de distribuição. O sistema de injeção possui métodos para detectar e eliminar bloqueios. As linhas de transferência incluem portas de purga onde os bloqueios são removidos, normalmente com ar de alta pressão. Um teste simples e prático é necessário para avaliar a fluidez e manuseio do WP. Isso permite que os materiais problemáticos sejam identificados antes de serem utilizados.
A lança de injeção injeta WP no maçarico que leva até a ventaneira. As partículas são imediatamente aquecidas pelo jato quente, inflamadas, gaseificadas e queimadas. O design e a colocação da lança influenciam o CE do WP. Podem ocorrer problemas de bloqueio da lança e da ventaneira e derretimento da ponta da lança. Os bloqueios são principalmente devidos ao aquecimento do WP a uma temperatura em que se tornam pegajosos e aderem à superfície das lanças de injeção e ventaneiras. Existem procedimentos definidos para detectar e eliminar esses bloqueios antes que possam causar problemas.
Combustão
Raceways são regiões vitais do BF, embora seu volume total geralmente não exceda 1% do volume interno do BF. Eles fornecem o processo com calor e agentes redutores. A injeção de WP afeta as condições da pista que, por sua vez, tem consequências fora da pista. Partículas não queimadas que saem da pista podem causar problemas operacionais, como permeabilidade reduzida, distribuição de gases e temperatura indesejáveis, erosão excessiva de coque e aumento do arraste de carvão. A quantidade de carvão não queimado aumenta com o aumento das taxas de injeção. Assim, o comportamento de combustão e gaseificação dos plásticos injetados na pista é um fator importante para a operação estável do forno. O comportamento de combustão de resíduos plásticos é dado na Fig 2.
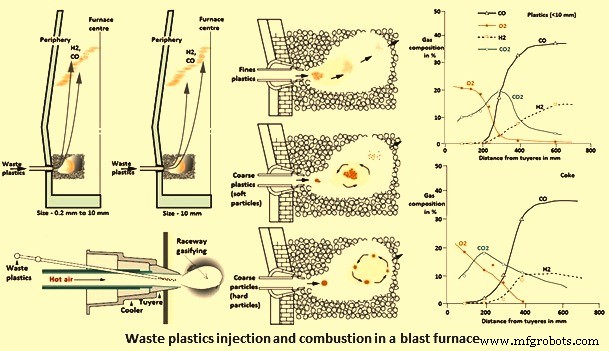
Fig 2 Comportamento de combustão do WP em BF
É óbvio que o BF pode consumir mais WP injetado do que o queimado dentro da pista, uma vez que o material não queimado é consumido em outras partes do BF. A combustão de plásticos segue um caminho semelhante ao PC, exceto que alguns tipos de plástico se decompõem termicamente em um líquido combustível e gás volátil. Menos carvão é formado a partir dos plásticos que têm menor teor de cinzas do que o carvão. Assim, a combustão de gás pode ser mais importante do que a combustão de carvão. As partículas de plástico têm uma baixa condutividade térmica e, portanto, a transferência de calor na pista é alta. O comportamento da combustão depende do tipo de plástico, suas propriedades (como dureza/densidade) e tamanho. Partículas maiores têm um tempo de residência mais longo na pista, por exemplo, cerca de 4 segundos a 6 segundos para partículas de 7 mm.
São as características de combustão do WP, em vez da combustão do coque, que governam a composição do gás e a distribuição de temperatura na pista, uma vez que são queimados preferencialmente. A Fig 2 mostra como a composição do gás (incluindo H2) varia em uma pista simulada (modelo quente) quando os resíduos plásticos são injetados. Para comparação, a Fig. 2 inclui a composição do gás para toda a operação de coque ao soprar apenas ar quente através da ventaneira.
A extensão da combustão (CE) e, portanto, a quantidade de material não queimado transportado para fora da pista, depende de vários fatores que incluem (i) propriedades de WP, como conteúdo de matéria volátil (VM), tamanho de partícula e densidade, e (ii) condições de operação, por exemplo, composição e temperatura do gás BF e posição e projeto da lança. O comportamento de combustão e gaseificação de resíduos plásticos na pista é influenciado por suas propriedades.
Os tipos de plástico variam em composição, estrutura e grau de ordem (cristalinidade). Por exemplo, as estruturas de PP, PS e PVC diferem daquelas de PE, pois contêm metil (CH3), benzeno e Cl, respectivamente, como unidade de repetição. O PE consiste em uma longa cadeia de hidrocarbonetos alifáticos feitos de monômero de etileno. Tanto o HDPE quanto o LDPE têm essencialmente uma estrutura molecular semelhante, exceto a ramificação da cadeia que é responsável pelas diferenças de densidade. Assim, o comportamento de decomposição térmica dos vários constituintes WP difere. A decomposição térmica do PE, por exemplo, favorece maior liberação de H2 em relação ao CO.
A injeção de plásticos reduz o RAFT, pois promove reações endotérmicas. O WPI tem um efeito de resfriamento mais forte que o PCI, e o efeito depende do tipo de plástico. O polibutileno tereftalato (PBT) tem um efeito de resfriamento maior que o PE que, por sua vez, é maior que o PS. Taxas de injeção de 100 kg para plásticos de baixa qualidade e até 170 kg para PS são teoricamente possíveis sob condições de ventaneira constantes sem incorrer em uma queda de temperatura da chama abaixo de 2000 graus C (Fig 3). Aumentar a temperatura de explosão e/ou enriquecimento de O2 e/ou diminuir a umidade de explosão pode compensar o efeito de resfriamento do WP.
Fig 3 Efeitos de plásticos e outros injetores na temperatura da chama
Estudos de análise termogravimétrica (TGA) mostraram que o comportamento de pirólise de PS, PP, PBT, LDPE e HDPE é semelhante, com uma rápida perda de peso de hidrocarbonetos ocorrendo dentro de uma estreita faixa de temperatura de cerca de 80 graus C a 100 graus C. a pirólise do PS começa e termina antes do PP que, por sua vez, começa e termina antes do PE. O comportamento de degradação térmica do PVC é mais complexo. Primeiro o benzeno (C6H6) e depois o Cl são liberados, seguidos pela degradação dos hidrocarbonetos remanescentes que ocorre a uma temperatura semelhante aos outros plásticos. Além disso, o PVC produz uma fração de carvão, ao contrário dos outros plásticos. Tem uma estrutura mais complexa. Em geral, o PE (e alguns outros tipos de plásticos) se decompõe termicamente em um líquido combustível e gás volátil.
Alguns dos estudos mostraram que o PVC produz um carvão ao contrário do LDPE, HDPE, PP e PS (sem corante). O que não é colorido não produz resíduo sólido após a pirólise, gera uma grande quantidade de fuligem. Além disso, o PVC produz muita fuligem seguido, em ordem, por PS, PP e PE. O PVC também mostra uma ignição mais rápida e tempos de pirólise e combustão mais curtos do que PE, PP e PS de tamanho semelhante. A ignição mais rápida é atribuída à menor “energia de ativação para degradação térmica” do PVC (20 kcal/mol a 33,5 kcal/mol para o PVC comparado a 48 kcal/mol a 72 kcal/mol para os outros plásticos). As diferenças no comportamento de pirólise entre os vários plásticos também se devem a diferenças na sua estrutura química que podem alterar a sua reactividade. A reatividade do PS é maior que a reatividade do PP que, por sua vez, é maior do que LDPE e HDPE.
O desempenho de combustão do WP é influenciado pelo tamanho das partículas. Para a conversão completa e, portanto, a utilização efetiva do WP, o aquecimento, desvolatilização, pirólise e combustão das partículas deve ocorrer entre sua entrada no jato quente e o limite da pista.
O comportamento de combustão dos diferentes WP é variável. O PE é regularmente usado como material substituto para investigar WPI em um BF devido à abundância de seus derivados em WP. A temperatura de ignição do PE aumenta com o aumento do tamanho das partículas (360 ° C com 3 mm a 5 mm em comparação com 380 ° C com um tamanho de partícula de 6 mm a 10 mm) quando queimado ao ar. Isso é atribuído à maior área de superfície de contato das partículas mais finas com o O2. Portanto, espera-se que partículas de plástico mais finas tenham um CE mais alto do que as mais grossas.
Uma análise da concentração de CO2 no gás gerado (frequentemente usado como medida de CE) mostra que as partículas maiores de PE sofrem combustão mais longe das ventaneiras e, portanto, levam mais tempo para queimar em BF do que as mais finas. Isso se deve à baixa condutividade térmica dos plásticos. A análise também mostra que, além de possuir menor temperatura de ignição, o PE apresenta menor tempo de queima e maior taxa de queima em relação ao carvão com granulometria de 0,6 mm a 0,7 mm. Isso ocorre porque o PE se decompõe em gás combustível em altas temperaturas. A combustão do gás de pirólise com O2 é uma reação gás-gás, que é uma reação mais rápida.
Um estudo com combustão de PE e WP misto em um forno elétrico sob fluxo de ar quente e medição dos teores de CO e CO2 do gás gerado, mostrou que a taxa de combustão das partículas menores de ambos os materiais é mais rápida que a partículas maiores a 1200°C, mas a 1250°C, o tamanho das partículas teve pouca influência no processo de combustão. Como esperado, CE (denominada razão de combustão e definida como a razão entre o teor de C e o teor de C original) de partículas com o mesmo tamanho é melhor na temperatura mais alta. Partículas menores têm um CE mais alto durante os 200 segundos iniciais a 600 segundos, mas após esse período o CE é revertido em que as partículas maiores tinham um CE mais alto.
A adição de CaCO3 melhora a resistência dos plásticos aglomerados, permitindo que as partículas circulem por mais tempo dentro da pista. Além disso, reduz o ponto de fusão da escória formada, diminuindo assim a queda de pressão no forno causada pela deterioração da permeabilidade.
Um estudo foi realizado na Alemanha para o comportamento de combustão do WP com a mesma composição (76% C, 10% H2, 8% O2 e 5% cinzas) e tamanho de partícula (3 mm a 6 mm), mas preparado de maneiras diferentes . Três tipos de plástico foram estudados. Eles eram aglomerados (fração após esmagamento e remoção de substâncias indesejadas), granulados (após a fundição a 100°C) e regranulados (após prensagem adicional, tendo a maior densidade). O plástico aglomerado (triturado) apresentou o maior CE devido a sua maior área superficial e menor densidade, seguido do granulado e depois do regranulado. A CE de todos os três tipos de plástico foi baixa, uma vez que as partículas grandes não podem queimar completamente no tempo de residência disponível.
O uso efetivo do WP precisa de mudanças operacionais para compensar as alterações nos parâmetros da pista e seus efeitos em outras partes do BF (como o estado térmico, regime de escória e dinâmica dos gases). Não se espera que a injeção de WP de até 10 kg/tHM perturbe a operação do BF. Medidas para intensificar a combustão de WP na região da ventaneira e, consequentemente, aumentar as taxas de injetor, incluem (i) aumento da quantidade de O2 nas ventaneiras e (ii) ajuste da temperatura e umidade da explosão.
O oxigênio pode ser adicionado à ventaneira por (i) enriquecimento do jato de ar quente, (ii) injeção através das lanças WP e (iii) lanças de O2 separadas. A adição de O2 significa que mais O2 está disponível para a participação na combustão do WP na pista. Assim, o CE aumenta. However, the influence of O2 enrichment on the CE is limited.
Oxygen enrichment of the hot air blast produces both a reduction in bosh gas flow and a rise in flame temperature. The former effect can help counteract the increase in burden resistance (lower permeability) and the pressure drop associated with high injection rates. The latter effect can help compensate for the cooling effect of the decomposition of the WP volatiles. The CO and H2 contents also increase with O2 enrichment, resulting in improved reduction of the iron ores in the central shaft. The CV of the top BF gas normally improves with the O2 enrichment. The lower limit of O2 enrichment is generally determined by the amount needed to maintain the required RAFT, with more O2 required as the volatile content of the WP increases. If the flame temperature becomes too high, then burden descent can become erratic. Too low a flame temperature hinders WP combustion and melting of the ore burden. The upper limit is dependent on maintaining a sufficient top gas temperature. As O2 is increased, the gas mass flow within the BF decreases, which decreases the heat flow to the upper region of the BF for drying the burden. The upper limit of the top gas temperature may also be governed by the need to protect the top gas equipment. Other limitations to O2 enrichment include its cost and availability.
The key measure for combustion at high injectant rates is a high blast temperature. O2 enrichment plays a more important role as a means of controlling gas flow in the BF rather than controlling the WP combustion. Generally, a higher hot blast temperature is an inexpensive measure than O2 enrichment since it allows a lower O2 consumption. Increased blast temperatures also reduce coke consumption. WP has a stronger cooling effect on flame temperature than coal.
Although increasing the blast temperature raises the RAFT with waste PE injection, it has been found in a study that regardless of the blast temperature (900 deg C, 1000 deg C, and 1100 deg C) and O2 enrichment (0.7 % and 1.2 %), the maximum RAFT which can be achieved is around 1950 deg C. This suggests that blast temperature and O2 enrichment only affect the combustion kinetics (rates), and not the thermodynamics, as long as the plastic particles start burning, the maximum temperature related to the enthalpy of combustion remains constant.
Lowering blast moisture can help to compensate for the cooling effects of WPI. If the RAFT becomes excessive, then blast moisture can be increased. Raising hot blast moisture means more H2 in the bosh gas for iron ore reduction. The optimum RAFT in the BFs operating with higher H2 contents can be lower than those operating with lower H2. In addition, the blast velocity can be adjusted to not only improve waste plastics combustion, but to maintain the required length of the raceway zone which is critical for obtaining good conditions in the hearth.
Unburnt char
With the increase of the injection rate, the combustibility of WP has a tendency to decrease resulting in unburnt material (char, fines and fly ash) leaving the raceway. Some of this material, along with coke debris, accumulates at the back of the raceway, in the bird’s nest, hampering the rising gas flow and entrained solids in this area. The majority are swept upwards where they can accumulate under the cohesive zone, decreasing permeability and hence BF productivity. Changes in the lower BF zone permeability can also affect the HM quality and slag viscosity.
The unburnt material tends to accumulate at positions where large changes in gas flow occur. Finally it is entrained into the gas flow, passing through the cohesive zone coke slits, and up the BF shaft, where it can influence burden permeability, and is finally released with the top BF gas. Higher WP injection rates also increase the volume of combustion gases, and hence the gas flow, and change the heat load in the lower part of the BF. In addition, more slag is produced.
The deposition of unburnt fine material is a complex phenomenon consisting of several generation mechanisms, reactions, multiphase flow, accumulation and re-entrainment. Different gas flow models have been developed to understand and predict the behaviour of fine material within the BF. With suitable burden charging patterns (such as central coke charging) and the use of stronger coke many of the problems relating to gas flow have been solved.
The experience has shown that most of the unburnt char is consumed within the BF. The three mechanisms for this are (i) gasification with CO2 and H2O, (ii) reaction with liquid iron (carburization), and (iii) reaction with slag. It is advantageous if the unburnt char participates in the ore reduction reactions, thus replacing more of the coke and lowering the amount of unburnt solids in the top BF gas.
The reaction of chars with CO2 and H2O begins in the raceway, but since the residence time for fine particles is very short for appreciable reaction, gasification mainly occurs in the BF shaft. The reactions of char C with CO2 (Boudouard reaction) and H2O are slower than char combustion. The chars resulting from WP and coke compete with each other for CO2 and H2O. Chars from WP are more reactive than those from coke and thus are preferentially gasified. Thus coke degradation by the Boudouard reaction decreases with increasing WPI rates.
It has been reported that the CO2 gasification rate of char from agglomerated WP (particle diameter 400 micron to 500 micron) is around 10 times higher compared to the PC char (50 micron), despite its larger size. The rates have been determined using a thermo-balance. The CO2 gasification rate of PVC char is also slightly higher than PC char. It has also been reported that the reaction rate of unburnt char from WP (300 micron to 400 micron) is around half that of PC char (50 microns). Though WP char has a longer residence time in the packed coke bed due to its larger size, it has a small gasification rate due to its fairly small specific surface area. Hence, it can accumulate in the lower part of the BF, decreasing permeability, unless CE in the raceway is high.
The reactivity of C in the unburnt char to CO2 and H2O is dependent not only on its surface area (particle size) but also on its structure and composition, as well as operating conditions. Also, since the residence time for particles at high temperatures is too short in a BF, char gasification mainly occurs at decreasing temperatures in the furnace shaft. The properties of char change as it moves up the BF, and hence its reactivity to CO2 and H2O. The reacting atmosphere is not uniform, for example, the concentrations of CO, CO2, H2 and H2O vary at different locations within the BF. Normally higher H2 and CO concentrations are found at the periphery compared to the centre of the BF for waste plastics with a particle size of 0.2 mm to 1 mm but the reverse takes place with the injection of larger particles size (less than 10 mm).
Injection of WP increases the bosh gas H2 concentration. Since the chemical reaction rate of H2 reduction is higher than that of CO, the extent of Boudouard reaction reduces as bosh gas H2 increases. CO2 and H2O are present in the upper part of the BF due to the reduction of iron oxides. Under the conditions here, char gasification by CO2 is likely to be controlled by the rate of the chemical reactions. In the lower part of the BF, char gasification is partly diffusion controlled. Hence the overall reaction rate of char gasification is likely to be influenced by the chemical reactivity of char to CO2 in this region. Char reactivity towards CO2 is influenced by its chemical structure, with less ordered structures being more reactive. The char structure from agglomerated WP has an isotropic texture with high CO2 reactivity.
The presence of certain minerals in the char ash, such as Fe and alkalis, can catalyze the CO2 gasification reaction, whereas other minerals, such as silica (SiO2) and alumina (Al2O3), can slow down the reaction. Depending on its composition, ash can also retard the C conversion due to the blockage of char particles as a result of increased proportion of slag formation in the char particle. In the lower part of the BF, condensed alkalis from the recirculating gases can have a catalytic effect. The loss of C by gasification increases the char ash content. In general, WP has a lower ash (mineral) content than PC and thus are more likely to be consumed within the BF.
Carburization of the HM begins in the solid phase within the cohesive zone of the BF, and continues during descent of the metal droplets through the active coke, deadman and hearth zones. Unburnt char and fine material leaving the raceway can contact the dripping liquid metal in the bosh and hearth zones. C and other elements, such as Fe, Si and S, dissolve from the char into the liquid Fe influencing the composition of the HM. The dissolution of C contributes to the carburization of liquid Fe, and commands the level of char consumption by the HM. It is critical where CE is low. If the HM is close to saturation when it reaches the areas of deadman and hearth, the unburnt material cannot be consumed, thus diminishing permeability in these regions. The C comes from unburnt WP materials, as well as coke.
Carbon dissolution from unburnt char into liquid metal is influenced by the operating conditions and the following factors.
- Char particle size – Unburnt chars which maintain their original form react very little with the liquid Fe and slag as they cannot penetrate into the liquids. However, if they are agglomerated into larger particles or captured by the larger pieces of coke, then they behave like bosh coke and carburize the metal up to saturation.
- Char structure – Generally, the rate of dissolution improves as the C structure becomes more ordered.
- Char mineral matter – In general, SiO2, Al2O3, and magnesia (MgO) slow the C dissolution kinetics, while calcium fluoride (CaF2) and Fe oxides enhance the rate. The effect of lime (CaO) is less clear. The reaction of calcium (Ca) with S in the metal produces a CaS (calcium sulphide) layer which hinder C transfer. The ash fusion temperature (AFT) is also one of the controlling mechanisms which limit C dissolution. The formation of an ash layer on the carbonaceous material reduces the surface area available for dissolution, hence retarding C dissolution rates. Low AFT allows easy removal of the ash, in the form of liquid slag. This results in constant exposure of fresh C surface to the HM, permitting the mass transfer of C to the liquid iron.
- Liquid metal composition – It changes over time. The C dissolution rate typically decreases as the C content of the liquid metal increases. Higher S content also retards C dissolution. Combustion of WP and coke releases sulphur oxides (SOx) which can react with the descending liquid metal and slag. This is less of a problem with WP since they typically have a lower S content than coal and coke.
Unburnt char, ash, fines, and coke can interact with the dripping liquid slag. The slag composition changes as it moves down the BF, with the Fe oxide concentration being continuously lowered as it is reduced. The reactions at the interface between the solid char and liquid slag play a major role in char consumption since they influence the kinetics of the reduction reactions and the contact area between the slag and char available for reaction.
Factors influencing unburnt char interactions with the slag include the slag composition, char C content, and char ash content and composition, as well as the operating conditions. Basically, char consumption by slags occurs through the following.
- Reduction of the Fe oxides in slags by C in the char – The wetting characteristics have a significant effect on the dominant reduction mechanism taking place. The wetting characteristics of slags vary with slag composition, temperature, time, and carbonaceous material. Wetting varies as a function of time since the reduction of Fe oxide in the slag by char, and the dissolution of the char ash components into the slag, results in continuous variations in the slag and char compositions. An increase in temperature normally results in improved wettability at the slag/C interface. Reduction rate usually increases with increasing slag FeO (2 % to 10 %) content and with increasing reaction temperature (1300 deg C to 1600 deg C).
- Reduction of SiO2 in slag by C of char – This is a function of temperature. At temperatures less than 1500 deg C, only reduction of Fe oxide occurs. At higher temperatures, both SiO2 and Fe oxides in the slag are reduced, resulting in increased consumption of the char. SiO2 is reduced by C, via gaseous SiO, to Si or silicon carbide (SiC). Self-reduction of SiO2 in the char ash by C can also occur, resulting in further consumption of the char. The reduction kinetics of SiO2 is influenced by the wettability of chars by the slags. Wetting behaviour improves with an increase in slag SiO2 content, and with an increase in temperature (1500 deg C to 1700 deg C). Higher amounts of SiO2 and Fe oxides in the char ash facilitate the slag/C interactions, leading to improved consumption of these oxides through reduction reactions.
- Interaction between components in the slag and char – This interaction leads to the assimilation of char ash components such as S.
In addition, the reduction of MgO in slag by char C can lead to further consumption. Self-reduction of the oxides in the char ash by C can also contribute to char consumption.
The presence of unburnt char in the slag can interfere with tapping by increasing slag viscosity, while assimilation of char normally increases the fluidity of the bosh slag. Changes in slag mobility can affect the position and shape of the fluid and cohesive zones. A high viscosity slag around the tuyeres also leads to serious gas flow problems. Slag viscosity is a complex function of slag composition, temperature and O2 partial pressure. As well as unburnt char and coke, unburnt ash from WP can interact with the slag. All of these carbonaceous materials contribute oxides to the slag. In general, higher amounts of SiO2 or Al2O3 (acidic components) increase slag viscosity, whereas a higher basicity (higher CaO or MgO) lowers slag viscosity because of de-polymerization of the silicate network. Slag viscosity decreases with increasing FeO (0 % to 20 %) content at a fixed basicity. Basicity is generally determined by the CaO/SiO2 ratio. Since the slags do not fully assimilate the char and ash in the bosh region, bosh slag normally has a higher basicity than tapped slag. The addition of fluxes can help solve slag formation problems.
Processo de manufatura
- Geração e uso de gás de alto-forno
- Uso de Nut Coke em um Alto Forno
- Injeção de carvão pulverizado em um alto-forno
- Irregularidades do alto-forno durante a operação
- Sistema de resfriamento do alto-forno
- Sistemas de carregamento de alto-forno
- Química da Ferragem por Processo de Alto Forno
- Revestimento refratário do alto-forno
- Injeção de gás de forno de coque em um alto-forno
- Fatores que afetam a taxa de coque em um alto-forno