TPM com RCM forma uma combinação poderosa
Duas filosofias complementares formam uma combinação poderosa para mudar a cultura organizacional e estabelecer um processo de melhoria contínua. A abordagem de Manutenção Produtiva Total (TPM), baseada em pessoas e processos, transforma a cultura e a forma como vemos nossos ativos.
A abordagem de Manutenção Centrada em Confiabilidade (RCM) pode ser assustadora, embora estabeleça uma base sólida para uma estratégia de manutenção. Individualmente, ambos têm sido abordagens monumentais para a excelência da manutenção, mas quando combinados, comprovadamente reduzem o tempo de inatividade e aumentam a produtividade.
A SKF decidiu mudar a maneira como vê seus ativos. Nossos ativos - como os seus - são inestimáveis. Poderia ser tão simples quanto tomar uma decisão de mudança?
Filosofias Complementares
Ao apoiar o processo de TPM, em particular os pilares de Manutenção Planejada e Manutenção Autônoma, a metodologia RCM solidificará ainda mais a base de gerenciamento de manutenção e facilitará a melhoria contínua.
Você pode obter de forma conclusiva um programa de manutenção com base nas metas gerais de negócios da organização. O que todos nós devemos primeiro entender é que antes que alguém vá a qualquer lugar (ou seja, produção e manutenção de "classe mundial") ou faça qualquer coisa (ou seja, "trabalhar de forma mais inteligente em vez de arduamente") - uma decisão deve ser tomada em todos os níveis da organização para mudança.
A SKF aprendeu isso em primeira mão em uma de nossas fábricas da Divisão Automotiva na América do Sul. Num mercado altamente competitivo, esta fábrica teve dificuldades em obter vantagem competitiva com o comportamento tradicional de produção e manutenção.
Quando confrontados com o fechamento que se aproximava nos anos seguintes, eles decidiram fazer uma mudança. Para permanecer aberta e salvar nobremente muitos empregos no processo, esta fábrica escolheu o TPM como o catalisador para a mudança.
Algum tempo depois, a SKF adotou essa filosofia como uma de suas maneiras de construir uma base para a Excelência em Fabricação de Classe Mundial.
Desde a adoção do TPM, a SKF começou a perceber o ingrediente que faltava, o pensamento de confiabilidade. A adaptação foi pensada inicialmente para ser RCM, mas mais tarde descobriu-se que era mais adequada para usar o processo SKF SRCM.
Por quê? O RCM é particularmente útil e viável para manutenção de instalações idênticas (como aeronaves), mas dado o contexto operacional e a manutenibilidade de nossos ativos, não era o caso.
Outro problema era que um certo nível de maturidade de manutenção é necessário para garantir dados de ativos precisos e completos. Era difícil avaliar e garantir que todos estivessem em níveis equivalentes. Com base na irregularidade dos ativos e na maturidade irresoluta da manutenção, a SKF escolheu o SKF SRCM.
SKF SRCM é um processo de revisão de estratégia de manutenção que fornece virtualmente os mesmos resultados que o RCM clássico, mas usa um processo eficiente para definir necessidades e concentrar esforços apropriados em equipamentos, funções e sistemas críticos e não críticos.
Tanto o TPM quanto o SKF SRCM foram integrados, e o pilar de manutenção planejada do TPM foi redesenhado. Os impactos não afetam apenas o pilar de manutenção planejada, mas têm um efeito cascata em todos os pilares que a SKF optou por implementar.
Os pilares escolhidos, sem ordem específica, são Melhoria Focada, Treinamento e Educação, Manutenção Planejada e Manutenção Autônoma com base 5-S.
Manutenção produtiva total
TPM, uma filosofia japonesa usada em muitas facetas da indústria, busca aumentar a produtividade eliminando qualquer desperdício de esforço. O TPM é atraente para muitos setores diferentes, mas provou ser bom na fabricação em linha e em lote.
A ideia começou em 1951 quando a manutenção preventiva foi introduzida no Japão a partir dos EUA. A Nippondenso, parte da Toyota, foi a primeira empresa no Japão a introduzir a manutenção preventiva em toda a fábrica em 1960. (5)
Depois que algumas conclusões foram feitas, a carga de trabalho era muito grande para a manutenção sozinha. Foi implementada uma relação de manutenção compartilhada entre os operadores e a manutenção, denominada manutenção planejada e autônoma.
Desde então, isso cresceu nos oito pilares que comumente conhecemos hoje como Kobetsu Kaizen, Manutenção Autônoma, Manutenção Planejada, Treinamento e Educação, Gestão de Equipamentos Antecipados, Segurança, Higiene e Meio Ambiente, Manutenção de Qualidade e TPM no Escritório.
Muitas organizações diferentes alteram o TPM e o tornam único para as filosofias de sua empresa; no entanto, o conceito e as progressões internas permanecem basicamente os mesmos.
Manutenção centrada na confiabilidade
O RCM pode ser explicado resumidamente como um processo estruturado, originalmente desenvolvido na indústria de aviação, para determinar as estratégias de manutenção de equipamentos necessárias para qualquer ativo físico para garantir que ele continue a cumprir suas funções pretendidas em seu contexto operacional atual.
Os ativos são decompostos, extensivamente analisados e descritos, modos de falha e análises de efeitos (FMEA) são feitas para os componentes mais críticos, e a organização e os processos de manutenção são cuidadosamente (re) definidos. (1)
Para fazer uma declaração austera, RCM foi derivado de um processo para ajudar a evitar que aviões caiam do céu e para fazer com que as usinas nucleares sejam o próximo desastre semelhante ao de Chernobyl.
O RCM foi desenvolvido na indústria de aviação comercial dos EUA no final dos anos 1960. O RCM foi então adotado pelo Departamento de Defesa dos Estados Unidos na década de 1970. O RCM foi identificado pelo USA Electric Power Research Institute (EPRI) em 1984 como um candidato para aplicação em usinas nucleares. Além disso, três aplicações piloto foram patrocinadas pelo EPRI de 1985 a 1987; todos eles eram estudos de sistema único que foram iniciados.
Para esclarecer ainda mais o que RCM é e não é, um padrão da Society of Automotive Engineers foi desenvolvido, conhecido como SAE JA10112, e pode ser encontrado em www.SAE.org. Esta norma fornece um critério de avaliação para eliminar quaisquer questões de se o assim chamado processo RCM é ou não verdadeiro em suas raízes para garantir que o ativo continue a cumprir suas funções pretendidas em seu contexto operacional atual.
Os sete critérios simplificados são os seguintes:
- Quais são as funções e o contexto operacional?
- Como ele pode deixar de cumprir essas funções?
- O que torna uma falha de função uma realidade?
- Qual é o resultado deste verdadeiro fracasso?
- Qual é o resultado do resultado e seu significado definido?
- O que deve ser feito para eliminar o fracasso?
- O que deve ser feito se o fracasso não puder ser eliminado?
Primeiros passos primeiro
A SKF decidiu fazer uma mudança e escolheu um veículo. Em seguida, alteramos esse veículo para atender às nossas necessidades e atender à cultura. TPM simples e SKF SRCM foram os métodos patrocinados. Esses dois métodos, quando combinados, seriam apenas o ponto de partida para a Excelência em Fabricação de Classe Mundial.
Muitas outras áreas, como Six Sigma, eficiência energética, etc., precisam ser polvilhadas e todas devem estar bem equilibradas entre si. Razões proprietárias restringem algum conteúdo de como, mas se focar apenas no pilar Manutenção Planejada do TPM, os pontos principais podem ser destacados e transmitidos.
Essa mudança não era necessária apenas no chão de fábrica, mas também na equipe de gerenciamento. A SKF precisava abrir os olhos para ver de uma maneira diferente. O benchmarking foi a primeira métrica principal.
Avaliar nosso desempenho em comparação com outras indústrias de manufatura em todo o mundo foi vital. A SKF tinha bolsões de “melhores práticas” internamente, mas seria mais poderoso comparar organizações externas. Isso ajudaria a levar para casa a necessidade de mudança.
Cinco maneiras principais de melhorar a SKF
A visita a empresas como Bosch, Tetra Pak, Fiat e Unilever (entre outras) deu a base para criar uma análise de lacunas para medir com precisão nossa situação atual em comparação com a visão da SKF. A análise de lacunas, bem como a Análise de necessidades do cliente (CNA) da SKF, são as ferramentas usadas. A SKF precisava medir a maturidade da produção e manutenção.
Essas ferramentas são fáceis o suficiente para transmitir informações entre as instalações de manufatura individuais em todo o mundo para um local centralizado. As análises de lacunas e o CNA são um esforço contínuo que geralmente é realizado com uma frequência anual para verificar o progresso e abordar as áreas fragilizadas.
A estrutura organizacional era muito necessária. Por quê? Em uma organização global, é impraticável ter um grupo pequeno ou grande localizado centralmente para fazer mudanças globais.
Demorou algum tempo para configurar a estrutura organizacional mais adequada. Normalmente não há maneira certa ou errada, mas certamente há subprodutos de uma estrutura organizacional deficiente.
Uma abordagem de baixo para cima era a forma preferida. A SKF descobriu que deve mudar constantemente para resolver novos problemas e promover melhorias contínuas. O diagrama abaixo descreve a abordagem de baixo para cima e onde o suporte foi alinhado para a melhoria contínua.
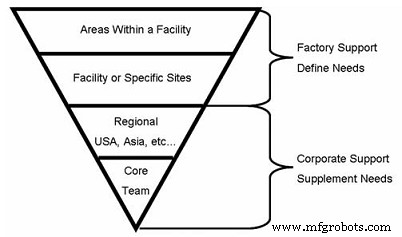
Figura 1. Abordagem de cima para baixo para estrutura organizacional .
Consultoria é uma área chave que continua a fazer a diferença. Quando a SKF não tem os recursos ou disponibilidade interna, deve ser complementado. Convocamos consultores de TPM, bem como outros especialistas em conteúdo, para fornecer assistência à SKF a fim de se transformar globalmente.
Devido à natureza dos consultores, seus produtos correspondem exatamente às necessidades da organização. Consultores de boa qualidade são essenciais para que a SKF compreenda melhor sua situação atual e obtenha vantagem competitiva sobre o destino da oposição.
O Business Process Management (BPM) é algo que surgiu recentemente no contexto dos sistemas BPM. Os sistemas BPM permitem que a gerência e os engenheiros analisem e avaliem a eficácia dos processos de negócios.
Usando um sistema BPM rudimentar, a Divisão Industrial e a Divisão de Serviços da SKF uniram forças e sobrepuseram a Otimização de Eficiência de Ativos (AEO) usando o processo SRCM da SKF e o pilar de Manutenção Planejada de TPM. Seis características fundamentais foram identificadas no contexto da manutenção planejada:
- Avalie o estágio atual (KPIs e alinhamento de metas de negócios)
- Repare ativos e melhore os pontos fracos
- Organizar o sistema de gerenciamento de manutenção de computadores (CMMS)
- Desenvolva estratégia de manutenção
- Implementar estratégia de manutenção
- Avaliar e sustentar a estratégia de manutenção
A última área-chave que a SKF conseguiu explorar é como e quando usar quais tecnologias e técnicas. A SKF Asset Management Services trabalha em estreita colaboração para prescrever o medicamento certo para um diagnóstico preciso. Isso, é claro, no contexto do gerenciamento de manutenção. Está comprovado que ganhar uma vitória rápida é apenas isso - uma vitória rápida e curta.
Parte do processo de tomada de decisão, conforme discutido acima, é decidir se melhorias sustentadas ao longo do tempo são apropriadas ou se é mais astuto obter algumas vitórias rápidas a fim de ganhar impulso. A SKF escolheu melhorias sustentadas ao longo do tempo.
Em conclusão, é bastante simples decidir fazer qualquer coisa. Seguir e melhorar continuamente é o que a maioria não consegue fazer. Estabelecer sistemas e processos e colocá-los em funcionamento é o que mais importa para a melhoria contínua.
Poderia ser tão simples quanto tomar uma decisão de mudança? A resposta, em minha opinião, é não; é o que é o conteúdo e o que fazemos. Não é apenas sobre o que falamos, mas sim sobre ações. Isso é o que é necessário para alcançar a visão geral.
A SKF continua obtendo resultados como redução do tempo de inatividade, melhor rendimento, maior eficiência e satisfação do funcionário devido a essa decisão. Além disso, a escolha é sua. O que você vai decidir?
Referências
- Glossário do Aptitude Exchange www.aptitudexchange.com
- Emitido em agosto de 1999. Critérios de avaliação para processos de manutenção centrada em confiabilidade (RCM), SAE JA 1011. www.sae.org
- Nowlan FS, Heap HF ,. 1978. Reliability Centered Maintenance, National Technical Information Service, U.S. Department of Commerce, Springfield, Va.
- Roberts J. 1997. "Total Productive Maintenance (TPM)," Departamento de Tecnologia Industrial e de Engenharia Texas A&M University-Commerce; A interface de tecnologia. http://et.nmsu.edu/~etti/fall97/manufacturing/tpm2.html
- Venkatesh J. revisado em 28 de outubro de 2007. Uma introdução à manutenção produtiva total (TPM) http://www.plantmaintenance.com/articles/tpm_intro.shtml
Manutenção e reparo de equipamentos
- 5 maneiras de reduzir o uso de energia com boa manutenção
- Implementação da manutenção preditiva com a ajuda da manutenção preventiva
- Minimize os resíduos com um fluxo de trabalho suave
- Aumente o tempo de atividade com a manutenção adequada da correia
- Formulários de manutenção do gerador de turbina da consolidação
- SKF assina contrato de manutenção com Valero Energy
- Por que as iniciativas TPM às vezes falham
- Luminant renova contrato de manutenção com Fluor
- Lidando com uma equipe de manutenção reduzida
- Resolvendo problemas de manutenção com colaboração móvel