Um Guia do Gerente de Manutenção para Manutenção Centrada em Confiabilidade (RCM)
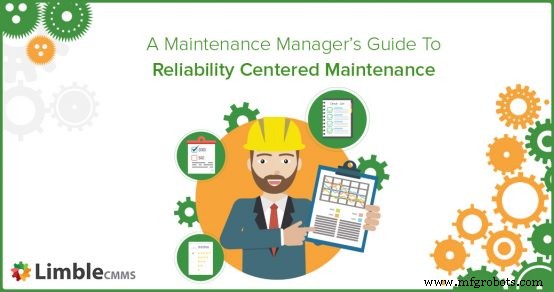
Você tem dúvidas se o seu equipamento está funcionando da melhor maneira possível? Você se pergunta se pode encontrar maneiras de melhorar a produtividade e reduzir os custos de manutenção otimizando sua manutenção? Então você pode querer investigar a Manutenção centrada em confiabilidade (RCM) .
O que é manutenção centrada na confiabilidade?
Muitos jargões são usados quando se trata de Manutenção Centrada em Confiabilidade - mas, simplesmente, o RCM é um processo estruturado que identifica problemas que, quando resolvidos, aumentam a produtividade de seus equipamentos e ativos, reduzindo os custos de manutenção. A manutenção centrada na confiabilidade não é necessariamente um método de manutenção, é um critério de avaliação para identificar quais métodos de manutenção funcionarão melhor para cada peça do maquinário.
Quando feito corretamente, o RCM pode afetar os resultados financeiros da sua empresa de uma forma enorme.
A Ebsco relatou um retorno de 63% sobre o investimento após iniciar um programa de manutenção centrado na confiabilidade.
Como realizar a análise RCM
Se você deseja realizar uma análise de manutenção centrada em confiabilidade, há um conjunto padrão de perguntas para ajudá-lo. Essas perguntas são oferecidas pela SAE (Society of Automotive Engineers), a organização reguladora sobre RCM e outras normas de engenharia. As perguntas abaixo são listadas como parte do padrão JA1011 da SAE.
Nós respondemos a essas perguntas e as simplificamos neste guia com um exemplo de empilhadeira real
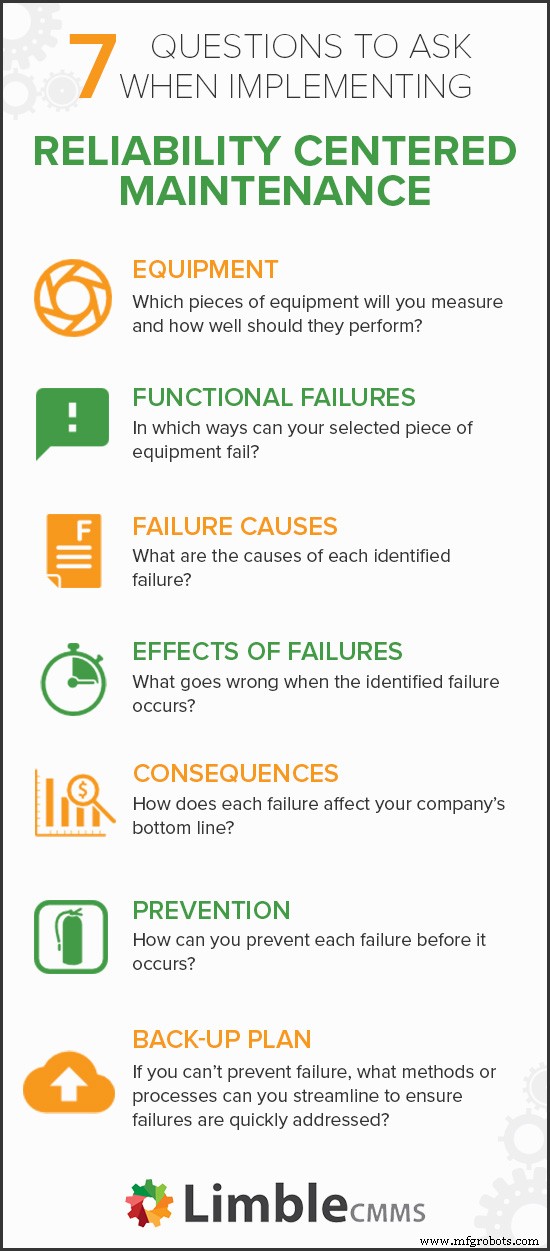
Pergunta 1: Quais são as funções e os padrões de desempenho desejados associados do ativo em seu contexto operacional atual (funções)?
Que boca cheia. Não se preocupe, vamos dividir para você.
A) Antes de respondermos a essa pergunta, precisamos selecionar qual equipamento você vai analisar com RCM.
Ao decidir com qual equipamento começar, você deve considerar qual equipamento é mais valioso e causa mais problemas para sua organização quando há uma pane.
Isso permitirá que você colha as maiores recompensas por seus esforços.
B) Precisamos descobrir a parte “funções e padrões de desempenho desejados associados”.
Simplificando, o que o equipamento selecionado faz e qual é o desempenho desejado? Para entender os níveis mais altos de produtividade do equipamento, consulte sua equipe de produção para obter os dados de produtividade.
C) Precisamos descobrir a parte “em seu contexto de operação atual (funções)”.
Para compreender o contexto de operação atual do equipamento, você precisará consultar seu CMMS para obter dados sobre as operações de manutenção. Se você não tem um CMMS, pode encontrar esses dados em seus registros em papel. Se você não conseguir encontrar esses números em nenhum dos locais, outro gerenciamento de manutenção pode ajudá-lo.
Sua resposta pode ser mais ou menos assim:
Empilhadeira nº 3 pode mover 18 paletes por hora ao operar em níveis de pico. Atualmente, o tempo médio entre reparos (MTBR) é de 800 horas com um tempo médio de inatividade de 6 horas. Se operamos nossa empilhadeira 40 horas por semana, a cada 20 semanas (800/40) temos uma avaria crítica e perdemos a capacidade de mover 108 paletes (18 paletes * 6 horas). Com base nos dados do seu CMMS ou outros gerentes de manutenção, uma empilhadeira deve ter um MTBR de 1200 horas. Se pudermos aumentar nosso MTBR em% 50 para o MTBR médio, ganharemos a capacidade de mover mais 54 paletes a cada 20 semanas.
Isso lhe dará uma boa visão de onde você pode ser capaz de melhorar.
Se você não consegue encontrar todos os dados, está tudo bem. Construa-o da melhor maneira possível.
Pergunta 2: De que forma ele pode deixar de cumprir suas funções (falhas funcionais)?
Agora que sabemos onde estamos e o resultado desejado que esperamos alcançar, precisamos identificar a origem das avarias (falhas).
Com isso em mente, examine seus registros ou pense sobre as avarias recentes e o que pode tê-las causado.
Usando uma empilhadeira como exemplo, sua resposta pode ser mais ou menos assim:
- Erro humano
- Mau funcionamento da forquilha
- Mau funcionamento do motor
Pergunta 3: O que causa cada falha funcional (modos de falha)?
Você pode aproveitar a lista anterior de falhas para expandir e responder à pergunta 3:
- Erro humano - causado por treinamento insuficiente
- Mau funcionamento da forquilha - causado por má manutenção e / ou mau comportamento do operador
- Mau funcionamento do motor - causado por má manutenção do motor (mudanças de óleo, etc.)
Pergunta 4: O que acontece quando cada falha ocorre (efeitos de falha)?
Esta pergunta é muito simples - sua resposta deve refletir os efeitos negativos das falhas que você descreveu. Pode ser parecido com isto - Modo de falha e análise de efeitos (fmea)
- Erro humano - acidentes (quebra, derramamento, lesão humana), diminuição da produtividade, etc.
- Mau funcionamento do garfo - dano ao equipamento, ciclo de vida, acidentes (quebra, derramamento, ferimento humano), aumento dos custos de trabalho e reparo, diminuição da produtividade, etc.
- Mau funcionamento do motor - danos ao equipamento, aumento dos custos de mão de obra e reparo, diminuição da produtividade, etc.
Pergunta 5: De que forma cada falha é importante (consequências da falha)?
Isso é muito semelhante à pergunta anterior, embora você vá dividi-la pelos efeitos negativos devido ao fato de uma falha pode ter vários efeitos negativos.
- Aumento dos custos de mão de obra e reparo - $ 25 por hora e $ 500 em média em peças
- Danos no equipamento - $ 800 cada incidente devido à redução da vida operacional das empilhadeiras
- Diminuição da produtividade - $ 300 por hora devido à interrupção da produção
- Acidentes (quebra, derramamento, lesão humana) - Potenciais violações de segurança, lesão de funcionário e mercadoria danificada. Potencialmente milhares de dólares por incidente.
Dividir isso em números reais permitirá que você estime e preveja os custos associados às falhas.
Por exemplo, digamos que ocorreu um mau funcionamento do motor que causou um tempo de inatividade de 6 horas. A conta total seria de $ 150 para mão de obra, $ 500 para peças, $ 800 devido a uma vida útil reduzida e $ 1800 para redução de produtividade. Isso totaliza $ 3.250 colossais para uma única avaria em um único equipamento .
Pergunta 6: O que deve ser feito para prever ou prevenir cada falha (tarefas proativas e intervalos de tarefas)?
É aqui que entendemos por que o RCM é importante. Você pode implementar manutenção preventiva ou preditiva para evitar grandes custos e interrupções inesperadas? Vale a pena e, se não, você deve usar uma estratégia de execução até a falha?
Usando o exemplo da Pergunta 5, o que poderia ter sido feito para evitar o colapso de $ 3.250?
Depois que seu técnico corrigir o problema, eles saberão o que causou a falha. Saber a causa da falha permite que você planeje e programe a manutenção para evitar mais interrupções.
Por exemplo, digamos que um filtro entupido causou danos ao motor que levaram à quebra. Agora sabemos o que fazer. Substitua o filtro da empilhadeira a cada 3 meses, juntamente com a troca do óleo para que o ar possa fluir livremente através do motor da empilhadeira, o que deve evitar que ele se deteriore e quebre.
A solução nem sempre é tão clara quanto alterar um filtro, mas fazer a análise RCM permite que você obtenha os dados para tomar a decisão se gastar recursos em manutenção preventiva vale a pena prevenir as avarias . Se não for, uma estratégia de execução até a falha (reativa) pode atender melhor às suas necessidades.
Pergunta 7: O que deve ser feito se uma tarefa pró-ativa adequada não puder ser encontrada (ações padrão)?
Esta pergunta parece mais confusa do que realmente é.
Aqui está outra maneira de formular:
Se você não pode implementar planos de manutenção preventiva ou preditiva para resolver o problema, há mais alguma coisa que pode ser feita?
Claro, isso. Basta um pouco de pensamento criativo.
Por exemplo, digamos que você tenha uma empilhadeira velha e decida que a melhor escolha seria deixá-la funcionar até morrer. Você pode evitar o tempo de inatividade da produção causado quando a empilhadeira finalmente quebra, colocando em prática um processo para alugar uma empilhadeira ou emprestar uma empilhadeira de um departamento diferente para que você não perca produtividade. Encontrar essas soluções geralmente é melhor quando você faz um brainstorming com outras pessoas de sua equipe (ou seja, técnicos, gerenciamento, equipe de produção, outros departamentos).
Esta é uma situação em que o colapso inesperado não é tão inesperado, então você pode preparar a solução com antecedência.
Como sua empresa pode implementar mudanças com base na análise de RCM?
Depois de responder às perguntas acima, é hora de começar a implementar as mudanças com base nos resultados de sua análise RCM.
A partir daqui, você determinará qual plano é necessário. Aqui está uma análise de algumas das estratégias de manutenção mais comuns e como implementá-las.
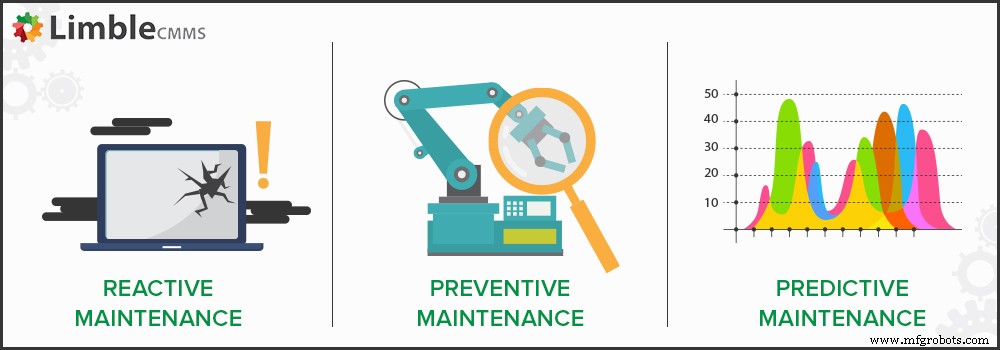
Manutenção run-to-fail / reativa
Definição: Reparando o equipamento conforme ele falha.
Exemplo: Se você esperar que a placa de circuito falhe antes de enviar um técnico para repará-la, você está contando com a manutenção corretiva. Esse tipo de manutenção tende a ser mais caro, mas nunca totalmente evitável. Dito isso, a manutenção corretiva tem seu tempo e lugar e devido à sua análise de Manutenção Centrada em Confiabilidade, você saberá quando utilizá-la corretamente.
Manutenção preventiva
Definição: Trabalho executado regularmente de forma programada para diminuir a probabilidade de falha do equipamento. A manutenção preventiva é realizada enquanto o equipamento ainda está em condições de funcionamento para evitar quebras inesperadas.
A manutenção preventiva pode ter retornos de até 545%. Veja como você pode implementar seu próprio plano:
Etapa 1. Selecione máquinas que requeiram manutenção regular e tenham altos custos de reposição / reparo. O agendamento da manutenção preventiva desses ativos proporcionará à sua empresa o maior retorno.
Etapa 2. Determine um cronograma de manutenção com base nos requisitos do ativo
Com que frequência cada máquina requer cuidados preventivos de rotina? - Essas informações podem ser encontradas no manual da máquina. Se você não conseguir encontrar o manual, visite o site do fabricante, pois eles geralmente têm uma cópia online.
Etapa 3. Reúna informações relevantes de seus colegas e supervisores. Você pode precisar falar com membros da equipe de produção ou outra equipe para ter uma boa noção de como você pode implementar da melhor forma um plano preventivo e quando é a melhor maneira de fazer a manutenção do equipamento.
Etapa 4. Implemente sua manutenção preventiva. Agora você precisa decidir se deseja executar seu plano manualmente ou se deseja implementar um sistema CMMS que pode automatizar os processos.
Depois que o plano de manutenção preventiva estiver funcionando perfeitamente, comece lentamente a adicionar outros ativos que se beneficiarão de um bom cronograma de manutenção preventiva. Antes que você perceba, todos os seus equipamentos estarão no seu plano de manutenção preventiva e você começará a ver os benefícios.
Para obter um guia mais detalhado sobre como implementar com sucesso uma estratégia de manutenção preventiva, verifique nosso Como mudar de manutenção reativa para manutenção preventiva ou como fazer.
Manutenção preditiva
Definição: Determina a condição do equipamento enquanto está em uso por meio de hardware e software projetado para medir a funcionalidade ou anormalidades. O retorno sobre o investimento é obtido sabendo exatamente quando os serviços são necessários e apenas fazendo a manutenção do equipamento quando for necessário. Quando implementada corretamente, a manutenção preditiva é muito econômica.
Estudos independentes do ISI (Institute for Scientific Information) mostraram que a manutenção preditiva pode reduzir as tarefas de manutenção preventiva em 15% e ter um efeito geral no tempo de inatividade de 1-2%.
Exemplo: Digamos que você use equipamento de imagem térmica para determinar quando as placas de circuito precisam de reparos. As inspeções visuais não detectarão problemas como o superaquecimento da placa de circuito. Esta é a manutenção preditiva porque você está reparando o equipamento apenas quando ele precisa de um reparo em vez de depender do tempo ou do uso por meio de um plano de manutenção preventiva.
Etapas para implementar a manutenção preditiva:
A manutenção preditiva requer hardware e software. Em nosso exemplo acima, uma câmera de imagem térmica e um software de imagem térmica seriam necessários para determinar se as placas de circuito precisam ser reparadas. Freqüentemente, os investimentos em hardware e software podem ser caros. Felizmente, empresas de manutenção preditiva surgiram em todo o país e são bastante acessíveis.
Se você está preparado para fazer o investimento necessário em hardware e software, obtenha uma lista de equipamentos nos quais gostaria de implementar a manutenção preditiva. Depois disso, faça uma pesquisa online ou entre em contato com o fabricante para descobrir o que você precisa para empregar a manutenção preditiva para aquele equipamento.
Além disso, configurar sensores em seu equipamento e sincronizá-los com seu CMMS pode reduzir muito os custos gerais, embora o investimento inicial ainda tenda a ser grande.
Se o seu CMMS tiver as integrações corretas, ele será capaz de se comunicar com os sensores e avisá-lo quando e com que freqüência você precisa realizar essas tarefas de manutenção preditiva.
Para uma visão aprofundada do que é um CMMS, confira nosso guia O que é um sistema CMMS e como funciona.
Em conclusão
A Manutenção Centrada na Confiabilidade pode ajudá-lo a ver a importância das decisões sobre a manutenção de seus ativos. Esse método comprovado de análise ajudará sua empresa a economizar tempo, dinheiro e recursos, o que, por sua vez, aumentará seus lucros.
Se você estiver interessado em melhorar suas operações de manutenção, confira Limble CMMS para saber como podemos ajudar.
2 comentários
-
Edward J Turk 9 de setembro de 2018, 17h09
Compare RCM com manutenção preditiva para mim.
Obrigado ed
Responder -
David 20 de setembro de 2018, 13h55
A manutenção preditiva é um processo ou método estruturado no qual a RCM é empregada para cumprir sua teoria de aumentar a produtividade de seus equipamentos e ativos. É como comparar a curva em um cruzamento e compará-lo a dirigir.
Responder
Manutenção e reparo de equipamentos
- Guia para KPIs de Fabricação
- O que é confiabilidade?
- Em manutenção. Aumente a confiabilidade.
- O que é cultura de confiabilidade?
- Manutenção baseada em condição:um guia completo
- Melhor desempenho em manutenção e confiabilidade
- Detalhes são importantes na manutenção e confiabilidade
- Confiabilidade orientada para a família
- 5 Chaves para Manter a Confiabilidade do Equipamento
- Como implementar a manutenção centrada na confiabilidade (RCM)