Fabricação de fossos em nanoescala com alto rendimento em filme fino de polímero usando litografia de aragem dinâmica baseada em ponta de AFM
Resumo
Nós mostramos que uma abordagem de litografia de aragem dinâmica (DPL) baseada em microscópio de força atômica (AFM) pode ser usada para fabricar poços em nanoescala com alto rendimento. O método se baseia em arranhar com uma velocidade relativamente grande sobre uma superfície de amostra no modo de vazamento, que é responsável pela distância de separação de poços adjacentes. Os testes de raspagem são realizados em uma película fina de poli (metacrilato de metila) (PMMA) usando uma ponta de revestimento de carbono semelhante a diamante. Os resultados mostram que 100 μm / s é o valor crítico da velocidade de raspagem. Quando a velocidade de raspagem é maior que 100 μm / s, estruturas de poço podem ser geradas. Em contraste, os nanogrooves podem ser formados com velocidades menores do que o valor crítico. Devido à dificuldade de quebrar a cadeia molecular do polímero em estado de vidro com uma carga de alta frequência aplicada e dissipação de baixa energia em uma interação da ponta e da amostra, um poço requer 65-80 penetrações para ser alcançado. Posteriormente, o processo de formação da cava é analisado em detalhes, incluindo três fases:deformação elástica, deformação plástica e escalada sobre o empilhamento. Em particular, 4800–5800 poços podem ser obtidos em 1 s usando este método proposto. Ambos os experimentos e análises teóricas são apresentados que determinam totalmente o potencial deste método proposto para fabricar poços de forma eficiente.
Histórico
O recente e rápido desenvolvimento da nanotecnologia tem atraído cada vez mais atenção para a aplicação de nanoestruturas em vários campos, como sistemas nanoeletromecânicos, nanosensores e nanofotônicos. Em particular, os nanopontos, definidos como nanoestruturas unidimensionais, são amplamente utilizados nas áreas de armazenamento de alta densidade e preparação de pontos quânticos [1]. No entanto, a fabricação eficiente de nanopontos ainda enfrenta enormes desafios. Muitos estudiosos propuseram vários métodos para fabricar nanopontos em uma ampla variedade de materiais. Dentre eles, o método de síntese química é amplamente utilizado para obter nanopontos para a maioria dos dispositivos de detecção de propriedades e em nanoescala [2]. No entanto, é difícil determinar as dimensões e distribuição espacial dos nanopontos usando este método. Isso resulta em mais esforço necessário para localização e manipulação em processos subsequentes. Assim, muitos estudiosos têm dedicado recursos para explorar métodos mais controláveis para obter estruturas de nanopontos com dimensões de vários nanômetros, como litografia por feixe de íons focado [3], litografia por feixe de elétrons [4] e litografia por nanoimpressão [5]. No entanto, a complexidade, os rígidos requisitos ambientais e / ou o alto custo dificultam muito a aplicação dessas técnicas.
Desde que o microscópio de força atômica (AFM) foi inventado em 1986, ele tem sido comumente utilizado como um perfilador de superfície de alta precisão [6]. Quando a força de interação entre a ponta de AFM e a amostra é aumentada para um valor relativamente grande, como várias centenas de nanonewtons ou mesmo várias centenas de micronewtons, o material da amostra pode ser removido pela ponta afiada plasticamente, semelhante a uma pequena ferramenta de corte [7 ] As energias química e térmica também foram introduzidas no sistema AFM através da oxidação local [8] ou aquecimento da amostra [9] para auxiliar na remoção dos materiais da amostra. Portanto, resulta em alguns novos métodos de fabricação para estender o escopo dos métodos existentes de nanolitografia com base em ponta de AFM (TBN). Dentre todos os métodos de TBN, a abordagem de remoção mecânica é a mais fácil e flexível [10]. Este método consiste primeiro em indentação e subsequentes ações de raspagem em vários materiais, nos quais a interação ponta-material é fortemente dependente do tipo de material, como metais [11], semicondutores [12, 13] e polímeros [14]. Ao controlar com precisão a interação do material da ponta na nanoescala, nanoestruturas complexas e de alta precisão, como nanopontos, nanogrooves e até mesmo nanoestruturas 3D, foram fabricadas com sucesso. Em particular, alguns estudiosos realizaram processos de nanoindentação com base na ponta de AFM na superfície de materiais semicondutores para obter estruturas de nanoponto [15, 16]. Em seus estudos, os defeitos cristalinos causados por nanoindentação foram determinados como locais de nucleação para nanoestruturas de InAs. No entanto, a dureza relativamente grande dos materiais semicondutores pode resultar em sério desgaste da ponta. Assim, alguns pesquisadores propuseram realizar o processo de nanoindentação em materiais mais macios, como a resina de filme fino de polímero, para fabricar primeiro estruturas de nanoponto. Essas estruturas de nanoponto podem então ser transferidas para materiais semicondutores por corrosão iônica reativa (RIE) ou processos de corrosão úmida [17]. Por causa de sua baixa dureza e espessura ultrafina, a camada resistente pode ser penetrada com uma carga normal relativamente pequena. Alguns estudiosos propuseram uma abordagem de arranhão em duas etapas para obter matrizes de nanopontos em uma superfície de policarbonato [18]. Este método se baseia nas ondulações dos materiais formados pelo processo de arranhamento constante da força com base na ponta AFM. No entanto, o espaçamento entre os nanopontos adjacentes depende apenas da geometria da ponta de AFM, e o mecanismo de formação dos nanopontos permanece obscuro.
Por outro lado, o baixo rendimento é um fator crítico que impede o desenvolvimento de métodos de nanofabricação baseados em ponta de AFM. Foi demonstrado que o processo de nanoindentação com base na ponta de AFM é demorado para a obtenção de estruturas de nanoponto em grande escala [19]. Para resolver esse problema, Vettiger et al. apresentou o conceito de “Milípede”, que emprega grandes arranjos de micro-cantilevers operando em paralelo para atingir capacidade de usinagem de ultra-alta densidade [20]. Considerando o sério desgaste da ponta após um processo de arranhão em grande área, alguns estudiosos propuseram uma nova operação no modo de contato intermitente para reduzir a força de interação ponta-amostra, diminuindo assim o desgaste da ponta [21, 22]. No entanto, os grandes arranjos de micro-cantiléveres usados nesta abordagem precisam de processos de projeto e produção complicados, e um processo tedioso é necessário para ajustar a posição de todas as pontas em uma sonda para garantir o contato com a amostra. Portanto, alguns pesquisadores modificaram o sistema comercial AFM, incluindo hardware e software, para promover a capacidade de usinagem de alta velocidade [23,24,25]. Nestes métodos, foram utilizadas pontas com um cantilever. No entanto, apenas nanogrooves podem ser fabricados usando essas abordagens de forma eficiente, e arranhar com grandes velocidades também pode levar a um sério desgaste da ponta. Além do processamento estático com uma ponta AFM, a litografia de aragem dinâmica (DPL) baseada na ponta AFM também tem atraído cada vez mais atenção recentemente; este processo é conduzido com o modo de rosqueamento do sistema AFM. Ao aumentar a amplitude de acionamento do cantilever, a ponta do AFM pode penetrar na superfície da amostra para realizar o processo de usinagem [26,27,28]. Por causa do contato intermitente entre a ponta e a amostra na abordagem DPL, o desgaste da ponta pode ser reduzido, semelhante aos métodos propostos nas Refs. [21, 22]. A profundidade usinada obtida pelo método DPL é normalmente da ordem de alguns nanômetros, o que é adequado para a fabricação de nanoestruturas em filme fino, como resistências de filme fino de polímero e materiais bidimensionais [29]. Além disso, no método DPL, o cantilever da ponta do AFM poderia ser acionado para oscilar a vários milhares de hertz, o que resultaria na interação da ponta com a superfície da amostra muitas vezes em um curto período. Assim, o método DPL pode ser uma abordagem potencial para fabricar estruturas de poço em nanoescala em uma superfície de amostra de filme fino de forma eficiente.
Neste estudo, um método de nanolitografia de varredura rápida (FSN) é apresentado com base na abordagem de fabricação DPL e empregando um sistema comercial AFM. A Figura 1a mostra um esquema do processo de nanorriscagem com uma ponta de revestimento de carbono semelhante a diamante, que ilustra uma vista da ponta em contato com um filme fino de poli (metacrilato de metila) (PMMA) em um substrato de silício. O cantilever é acionado perto de sua frequência de ressonância para gerar contato intermitente entre a ponta e a superfície da amostra. A amplitude de acionamento da ponta é mantida em um valor constante pelo sistema de controle (AM-AFM). O módulo Nanoman equipado no sistema AFM é usado para todos os processos de usinagem, e a direção de arranhão é escolhida como paralela ao longo eixo do cantilever. O efeito da velocidade de raspagem nas nanoestruturas usinadas é estudado. Além disso, o mecanismo de formação da estrutura do poço também é investigado.
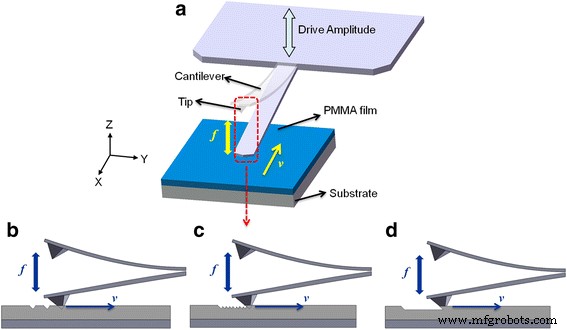
a Esquema do processo de riscar de linha na superfície do filme de PMMA com o método FSN. O cantilever está oscilando em sua frequência de ressonância f na direção vertical. A velocidade de arranhar v é modificado ao longo da direção da varredura rápida. Vários intervalos de velocidade de raspagem são descritos: b alta velocidade de raspagem, c velocidade de raspagem média e d baixa velocidade de coçar
Métodos
A concentração da solução de PMMA é de 1,25% em peso, preparada pela dissolução do pó de PMMA com peso molecular Mw =120.000 em clorobenzeno. Os filmes de PMMA são preparados girando a solução em um pedaço de substrato de Si de cristal único, que é limpo por sucessivos banhos ultrassônicos em acetona e álcool por aproximadamente 10 min. A velocidade de rotação escolhida é de 6000 rpm nos experimentos para gerar filmes com espessuras de várias dezenas de nanômetros. Seguindo o processo de revestimento, os filmes de PMMA são pós-cozidos a 125 ° C, que é próximo à temperatura de transição vítrea do PMMA, por 30 min.
Os experimentos são operados com um AFM comercial (Dimension Icon; Bruker Corporation, EUA). Uma ponta de silicone é selecionada com uma constante de mola nominal de 42 N / me frequência de ressonância de 320 kHz, fornecida pelo fabricante (TESPD; Bruker Corporation, EUA). O lado da ponta do cantilever é endurecido com um revestimento de carbono tipo diamante (DLC) para prolongar a vida útil da ponta. A medição de nanoestruturas na superfície do PMMA é definida para o modo de toque com uma taxa de varredura de 1 Hz e uma linha de varredura de 256. O sistema cantilever deve ser ajustado ao usar uma sonda diferente. O ponto de ajuste é ajustado em torno de 300 mV neste estudo. As imagens são processadas por nivelamento de primeira ordem usando o software Nanoscope Analysis fornecido pela Bruker Company.
O módulo Nanoman equipado no sistema AFM é utilizado para o processo de raspagem neste estudo, que é amplamente adotado para projetar a trajetória da ponta para obter estruturas desejáveis, como retângulos ou círculos, na superfície da amostra. Para modificar a superfície, o valor da amplitude da unidade da ponta deve ser aumentado para V w (escrita), onde a interação entre a ponta e o filme de PMMA é promovida para garantir que a ponta penetre na superfície da amostra. Após o processo de raspagem, o valor da amplitude de acionamento da ponta é imediatamente mergulhado para V r (leitura) sem mudar o cantilever. Em comparação com o método de litografia de aragem estática, o desgaste da ponta é provado ser muito pequeno com DPL e, portanto, pode ser desprezado. Ao evitar mudar a sonda e procurar a localização da nanoestrutura, este método de imagem in situ pode melhorar a eficiência do processo de raspagem. Todos os experimentos são operados em temperatura ambiente.
Resultados e discussão
Considerando a limitação de velocidade do AFM PZT, velocidades de raspagem na faixa de 0,1 a 1000 μm / s são selecionadas nos testes experimentais. A Figura 1 mostra um esquema do processo de nanomáquina, incluindo três faixas de velocidade. Ao riscar a uma velocidade relativamente grande (cerca de várias centenas de micrômetros por segundo), poços separados podem ser formados, como mostrado na Fig. 1b. Quando a velocidade de raspagem diminui para um valor médio (cerca de 100 μm / s), os poços podem se sobrepor uns aos outros, como mostrado na Fig. 1c. Conforme mostrado na Fig. 1d, quando a velocidade de raspagem atinge um valor relativamente pequeno (dezenas de micrômetros por segundo), os poços podem ser transformados em nanogrooves. Este resultado indica que a distância entre os dois poços fabricados é dependente da velocidade de raspagem, que tem uma grande influência nos nanopadrões fabricados.
Neste estudo, quatro direções típicas de arranhar são escolhidas, conforme mostrado na Fig. 2a. V 1 e V 3 representam arranhões ao longo do eixo longo do cantilever; V 2 e V 4 são definidos como arranhões perpendiculares ao longo eixo do cantilever. As trajetórias de ponta são obtidas controlando o AFM PZT. A Figura 3 mostra imagens AFM de nanoestruturas de linha quadrada fabricadas com diferentes velocidades de raspagem e as seções transversais correspondentes das nanoestruturas riscadas com a direção V 1 , quando a frequência de ressonância do cantilever é 380 kHz. Com uma velocidade de raspagem relativamente grande de 200 μm / s, poços contínuos podem ser formados, como mostrado na Fig. 3a. Para quatro direções de raspagem definidas com antecedência, os poços seriam formados imediatamente com muito menos de 1 s, mesmo que a velocidade de raspagem diminua no ponto de viragem das duas direções. Com uma velocidade de raspagem média (100 μm / s), nenhum poço óbvio pode ser encontrado ao longo do caminho de usinagem e nanoestruturas flutuantes são formadas, como mostrado na Fig. 3b. Apenas um poço com uma profundidade muito maior pode ser observado na intersecção dos dois caminhos de arranhão adjacentes, o que pode ser explicado a seguir. Durante o período da transformação entre os dois caminhos de arranhão adjacentes, a velocidade de arranhão deve diminuir para 0 e a ponta pode pressionar na superfície da amostra mais vezes do que no caso de arranhão, o que pode ser a possível razão para gerar uma profundidade maior do poço. A velocidade de raspagem de 100 μm / s pode ser considerada um valor crítico para a fabricação de poços contínuos em um filme fino de PMMA. A Figura 3c mostra os nanogrooves usinados com uma velocidade de raspagem de 50 μm / s. A partir da seção transversal da nanogroove usinada, pode ser observado que a parte inferior da nanogroove é relativamente plana e uma profundidade óbvia da nanogroove pode ser formada. Além disso, como mostrado na Fig. 3, como a ponta sulca no filme de PMMA, não há cavacos formados durante o arranhão e apenas empilhamento podem ser formados, em um lado ou em ambos os lados da ranhura. Além disso, os perfis de lados diferentes das nanoestruturas obtidas são inconsistentes ao arranhar com direções diferentes, o que é semelhante aos resultados usando litografia estática com ponta assimétrica. Para outros materiais resistentes, como SU-8 ou poliestireno (PS), os valores de limiar da velocidade de raspagem serão diferentes do filme de PMMA, devido aos diferentes módulos de relaxamento de tensão. No entanto, seus valores de limite podem ser obtidos por meio do experimento de arranhão, seguindo a mesma abordagem deste estudo.
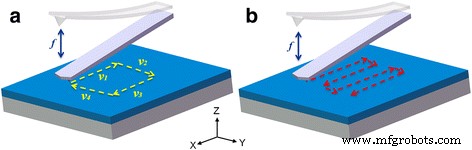
a Quatro direções típicas de arranhar ( V 1 , V 2 , V 3 e V 4 ) são escolhidos para fabricação de nanomáquina neste estudo. b A trajetória da ponta com o feed para padrões de grandes áreas
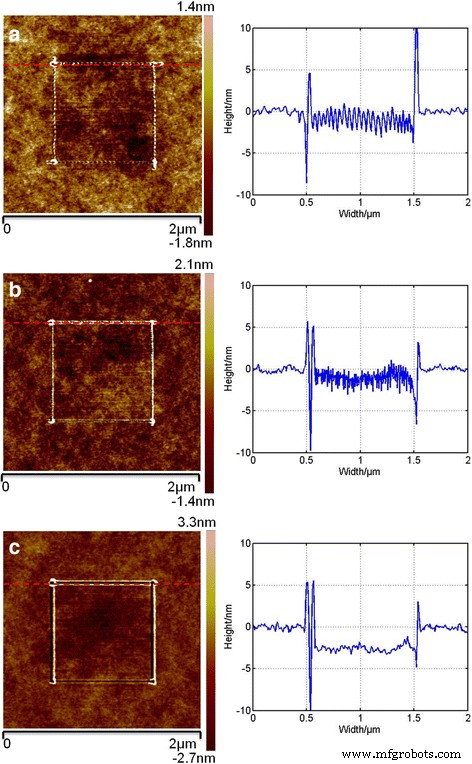
Imagens AFM de três tipos de nanoestruturas e suas seções transversais com velocidades de arranhamento de a 200 μm / s, b 100 μm / s e c 50 μm / s
Com velocidades de raspagem menores que 100 μm / s, nanogrooves com boa qualidade podem ser obtidos. A Figura 4 mostra a relação entre a profundidade usinada do nanogroove e a velocidade de raspagem com as diferentes direções de raspagem mostradas na Fig. 2a. Para cada nanogroove, a profundidade experimental é calculada pela média de cinco valores de profundidade em cinco locais diferentes. As distâncias de scratch para todas as direções de scratch são iguais - 1 μm neste estudo. Pode-se observar que a profundidade usinada diminui com o aumento da velocidade de raspagem em todas as direções de raspagem. Uma possível razão pode ser explicada da seguinte maneira. Para uma distância de raspagem de 1 μm, conforme selecionado neste estudo, o número de operações de prensagem sob velocidades de raspagem de 100 μm / se 1 μm / s será 3870 e 387.000, respectivamente. Para a mesma distância de arranhão, um grande número de operações de prensa pela ponta AFM pode levar a uma porcentagem relativamente grande de sobreposição entre as operações de prensa adjacentes, o que pode resultar em uma maior profundidade usinada do nanogroove. Além disso, como mostrado na Fig. 4, as profundidades dos nanogrooves riscados em todas as direções são consistentes quando a velocidade de raspagem é inferior a 5 μm / s, enquanto a profundidade do nanogroove usinado na direção V 3 torna-se muito menor do que as profundidades usinadas obtidas por outras direções com velocidades de raspagem maiores que 5 μm / s. Além disso, as barras de erro das profundidades usinadas obtidas na direção V 3 são muito maiores quando a velocidade de raspagem é inferior a 5 μm / s do que para outras. Uma possível razão pode ser explicada da seguinte maneira. A sonda de AFM geométrica usada neste estudo é assimétrica, e uma inclinação da sonda causada pela inclinação típica do cantilever de 12 °, usada para garantir que apenas a ponta do AFM toque a superfície da amostra, pode resultar em uma diferença da área de contato entre a ponta e a superfície da amostra com diferentes direções de arranhão. Para uma velocidade de raspagem de menos de 5 μm / s, a área de sobreposição das operações de prensa adjacentes é muito grande. Assim, a área de contato entre a ponta e a superfície da amostra também é extremamente grande. A influência da direção do risco na profundidade usinada pode, portanto, ser desprezível. No entanto, o empilhamento formado ao longo da superfície da ponta também depende da direção do risco, que é semelhante ao processo de raspagem estático. Portanto, a pilha não pode ser formada de forma constante no V 3 direção coçando. As figuras inseridas na Fig. 4a, b são as seções transversais de nanogrooves típicos usinados com velocidades de raspagem de 0,5 e 50 μm / s, respectivamente. A partir da seção transversal do nanogroove usinado com uma velocidade de raspagem de 0,5 μm / s, a parte inferior do nanogroove é flutuante ao riscar no V 3 direção, o que pode resultar em uma barra de erro relativamente grande para a profundidade usinada. Para arranhar com uma velocidade maior que 5 μm / s, a área de sobreposição com operações de prensa adjacentes torna-se pequena. Assim, a direção do risco desempenha um papel importante, o que pode resultar em uma profundidade usinada relativamente pequena obtida no V 3 direção coçando.
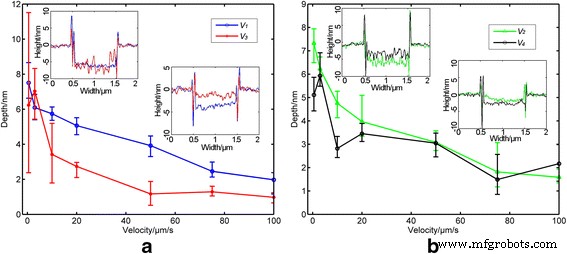
Dependência da profundidade do sulco na velocidade de raspagem nas direções típicas de raspagem: a V 1 e V 3 , paralelo ao longo eixo do cantilever; b V 2 e V 4 , perpendicular ao longo eixo do cantilever. As inserções mostram a seção transversal de nanogrooves para velocidades de raspagem de 0,5 e 50 μm / s
Um filme fino de PMMA é um tipo de material viscoelástico dependente do tempo. Assim, a carga periódica aplicada pela ponta de AFM pode ter uma influência no módulo de Young da amostra. A representação geral para o módulo de relaxamento de tensão G é definido por G 1 e G 2 [30]:
$$ G \ left (\ omega \ right) ={G} _1 \ left (\ omega \ right) + {iG} _2 \ left (\ omega \ right) $$ (1) $$ {G} _1 \ left (\ omega \ right) =\ left [{G} _r \ right] + {\ int} _ {- \ infty} ^ {+ \ infty} \ frac {H \ left (\ tau \ right) {\ omega} ^ 2 {\ tau} ^ 2} {1 + {\ omega} ^ 2 {\ tau} ^ 2} d \ left (\ ln \ tau \ right) $$ (2) $$ {G} _2 \ left ( \ omega \ right) ={\ int} _ {- \ infty} ^ {+ \ infty} \ frac {H \ left (\ tau \ right) \ omega \ tau} {1 + {\ omega} ^ 2 {\ tau} ^ 2} d \ left (\ ln \ tau \ right) $$ (3)
onde G r é uma constante e ω está relacionado com a frequência. H ( τ ) é o espectro de tempo de relaxamento que contribui para o relaxamento do estresse, que tem relação com os tempos de relaxamento entre ln τ e ln τ + d (ln τ ) Quando a frequência de excitação é definida para um valor próximo à frequência de ressonância do cantilever, que é 387 kHz, o módulo pode atingir um valor alto. A partir do cálculo usando as equações mencionadas acima, o filme fino de PMMA apresenta-se como um estado de vidro com uma carga de alta frequência aplicada [30]. Como o modo de rosqueamento é usado em todo o processo de usinagem, a força de interação e a dissipação de energia entre a ponta AFM e a superfície da amostra durante o processo de arranhão são relativamente pequenos, e até mesmo a amplitude de acionamento V w / V r é definido para um valor relativamente alto, variando de 10 a 20. Com essas condições de usinagem, por causa da propriedade semelhante a vidro do filme fino de PMMA e uma carga aplicada relativamente pequena pela ponta de AFM, as cadeias entre as moléculas de polímero não podem ser É difícil gerar deformação quebrada e plástica para modificar a superfície da amostra em um ciclo da operação de prensa. No entanto, a ponta tem energia suficiente (> 1 ~ 2 eV) para realizar isso durante as primeiras 20-30 vezes da operação de injeção [27]. Assim, as ligações da cadeia entre as moléculas de polímero podem ser cortadas para gerar deformação plástica na superfície do filme fino.
A distância de espaçamento entre as operações de prensa adjacentes é um parâmetro crítico que tem uma relação com a velocidade de raspagem e a frequência de oscilação da ponta. A distância de uma linha de fosso ( L ) pode ser obtido pelo tempo usado para uma linha de poço ( t ) multiplicado pela velocidade de raspagem ( v ) O número total de oscilações de ponta AFM em uma linha de poço ( N ) pode ser calculado usando a frequência de oscilação do cantilever ( f ) multiplicado pelo tempo ( t ) Assim, o espaçamento entre as operações de impressão adjacentes ( D ) pode ser obtido pela Eq. 4
$$ D =\ frac {L} {N} =\ frac {v} {f} $$ (4)
A frequência natural de vibração do cantilever selecionado neste estudo é de aproximadamente 387 kHz. A frequência de transmissão do sistema AFM é escolhida para estar próxima a este valor. Conforme mencionado acima, a velocidade de raspagem deve ser selecionada na faixa de 200 a 900 μm / s para garantir a formação dos poços. Assim, o espaçamento entre as operações de impressão adjacentes ( D e ) durante o processo de raspagem pode ser calculado no intervalo de 0,52 a 2,33 nm, que é denotado como a curva vermelha na Fig. 5a. A curva azul na Fig. 5a representa a relação entre a distância de espaçamento entre poços adjacentes ( D ) obtidos a partir dos experimentos e da velocidade de raspagem. As imagens AFM inseridas são obtidas para poços usinados com três velocidades de raspagem típicas de 400, 600 e 800 μm / s. Portanto, o número de operações de prensa para uma formação de poço pode ser calculado como a razão de D para D e mostrado na Fig. 5b. Assumindo que a velocidade de raspagem é um valor constante, 4800-5800 poços podem ser gerados em um filme fino de PMMA em 1 s, conforme calculado a partir do comprimento de raspagem ( L ) e a distância de espaçamento ( D ) Da Fig. 5b, pode ser observado que o número de operações de prensagem para uma formação de poço aumenta com o aumento da velocidade de raspagem e está principalmente na faixa de 65 a 80. Considerando que o terreno nivelado entre os dois poços é quase igual às dimensões de poços, apenas aproximadamente 32-40 operações de prensagem são necessárias para quebrar as cadeias de polímero para gerar deformação plástica da superfície da amostra, o que é consistente com a conclusão de Cappella [27]. Além disso, pode-se concluir que é mais fácil quebrar as cadeias de polímero ao arranhar com uma velocidade relativamente pequena. Neste estudo, a constante da mola do cantilever é idêntica. Um cantilever mais rígido pode ser usado para a fabricação de poços, o que resulta em uma força aplicada maior e uma frequência de ressonância mais alta. Se uma força maior for aplicada à superfície da amostra, a entrada de energia é aumentada em cada ciclo. Mais dissipação de energia é, portanto, contribuída para a deformação do filme de PMMA. Portanto, um poço pode ser gerado com ciclos reduzidos. No entanto, se a frequência de ressonância for aumentada para o sistema de oscilação, o ciclo da operação de prensa entre a superfície da amostra e a ponta é aumentado. Além disso, a dissipação de energia seria aumentada em um ciclo, devido ao ponto de ajuste diminuído nos experimentos. A velocidade crítica pode ser determinada pelo valor do ponto de ajuste. Com base nas discussões acima, o valor limite da velocidade pode ser influenciado pela força aplicada, a frequência de ressonância do sistema cantilever e o ponto de ajuste, que será o foco de investigações futuras.
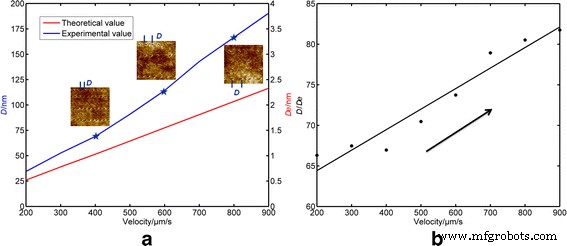
a Variação de D e D e com velocidade de raspagem (200–900 μm / s); as inserções mostram os resultados de fabricação para várias velocidades de raspagem. b Proporção de D para D e
O processo de formação da fossa é demonstrado na Fig. 6, incluindo três fases:deformação elástica, deformação plástica e escalada sobre a pilha. De acordo com a discussão acima, durante o arranhão da ponta ao longo da distância da Fig. 6a, b, o número de operações de prensagem não é grande o suficiente para quebrar as cadeias de polímero do filme fino de PMMA e gerar deformação plástica da superfície da amostra. Foi demonstrado que a ponta oscilante penetra na amostra de polímero gradualmente durante as primeiras 40-50 operações [27]. Comparado com o processo de indentação na Ref. [27], pressionando com uma velocidade lateral poderia gerar uma distância entre duas penetrações adjacentes. No entanto, a distância entre duas penetrações adjacentes (na faixa de 0,52 a 2,33 nm) é muito menor do que o raio da ponta do AFM (aproximadamente 15 nm). Assim, a situação neste estudo é semelhante ao caso do processo de indentação. Devido à falta de acúmulo de energia durante as penetrações iniciais de 30–40, nenhuma deformação plástica óbvia pode ser encontrada na região de usinagem. Esse resultado indica que o mecanismo dominante de dissipação de energia é a deformação elástica no primeiro estágio de riscar. Assim, a ponta do AFM desliza em contato contínuo com a superfície da amostra durante o período de tempo entre as Fig. 6a e b. Quando o número de penetrações conduzidas pela ponta do AFM atinge um valor crítico (40 vezes neste estudo), as cadeias poliméricas começam a se quebrar e ocorre a deformação plástica, conforme mostrado na Fig. 6c. Ao mesmo tempo, haveria uma tensão normal e de cisalhamento ocorrendo na superfície de interação entre a face frontal da ponta de AFM e o material de amostra; assim, um empilhamento pode ser gerado na frente da face frontal da ponta do AFM. Ocorreria uma deformação (Δ), atribuída ao movimento da ponta lateral contra o empilhamento. Isso resultaria em uma tensão dentro do filme de polímero, que poderia ser liberada pela propagação da trinca [31]. A taxa de liberação de energia de deformação V s pode ser descrito como:[32].
$$ {V} _s =E \ frac {h} {2} {\ left (\ frac {\ varDelta} {L} \ right)} ^ 2 $$ (5)
onde E é o módulo de Young do material polimérico e L é o comprimento do defeito interno. h representa a profundidade total de penetração na superfície livre da amostra. O termo de energia superficial W controla o processo de defeito interno, que é igual à taxa de liberação de energia de deformação por meio do equilíbrio termodinâmico. O termo de energia superficial é dependente da velocidade de propagação do defeito interno ( v L ), que é fornecido por [33].
$$ W ={W} _0 \ left (1+ \ alpha {v} _L ^ n \ right) $$ (6)
onde v L é igual a d L / d t e α é um valor constante relacionado ao material de amostra. n também é um parâmetro relacionado ao material. Uma força tangencial aplicada no ápice da ponta pode ser gerada pela energia elástica armazenada no substrato de polímero, que pode ser expressa como [32]:
$$ {F} _t =\ frac {Eah} {2} \ frac {\ varDelta} {L} $$ (7)
onde a representa o raio da área de contato entre a ponta e a amostra. Como a rigidez da sonda é muito maior do que a rigidez da amostra, o material pode ser removido do orifício formado [31]. No entanto, Mindlin definiu um valor crítico da força que poderia resultar no deslizamento da ponta na superfície do substrato [34]. A força tangencial crítica ( F tc ) para o movimento de deslizamento pode ser determinada como uma função da força adesiva e da carga normal, expressa como [35,36,37,38]:
$$ {F} _ {tc} =\ mu \ left (P + 3 \ pi RW + \ sqrt {6 \ pi RW P + {\ left (3 \ pi RW \ right)} ^ 2} \ right) $$ ( 8)
onde μ é o coeficiente de atrito. P é o normal, e R representa o raio da ponta AFM. Quando F t atinge o valor crítico F tc , a ponta do AFM deslizará sobre o empilhamento do material em vez de empurrar o material para fora do orifício produzido pela ponta. O contato se rompe a cada ciclo e, assim, o escorregamento pode ocorrer mais facilmente a cada ciclo no modo de rosqueamento. Embora o ponto de ajuste não esteja próximo a 100% da redução da oscilação da ponta, um período de tempo de contato pode ocorrer durante um ciclo e o travamento pode ocorrer durante este período de tempo.
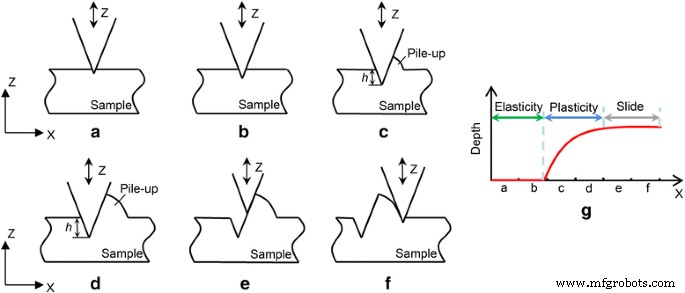
Esquema da formação do poço com a , b estágio de elasticidade, c , d estágio de plasticidade, e , f estágio de slides e g diagrama de precedência da formação do poço
Conforme mostrado na Fig. 6d, neste estudo, a profundidade que a ponta de AFM penetrou na superfície da amostra torna-se maior devido à diminuição da área de contato ponta-amostra quando a ponta de AFM sofre uma velocidade lateral. A altura do empilhamento também é aumentada. Isso pode contribuir para equilibrar a carga normal aplicada pela ponta do AFM. Ao mesmo tempo, a força tangencial aplicada no ápice da ponta descrita na Eq. 7 também pode ser aumentado. Com o aumento da profundidade de penetração, a força tangencial pode atingir o valor crítico F tc given in Eq. 8. The AFM tip starts to slide on the formed pile-up without modifying the material. Because of the characteristics of the tracking sample surface of the AFM system, the AFM tip would rise to climb over the pile-up, as shown in Fig. 6e. After the AFM tip moved over the pile-up, one pit could be achieved and another pit would be fabricated by repeating the above steps. The corresponding deformation mechanism of each stage of pit formation can be found in Fig. 6g.
According to the previous experimental results, the scratching velocity should be set to larger than 100 μm/s. As shown in Fig. 2b, scratching directions V 1 e V 3 are selected and a feed perpendicular to the scratching direction is conducted to achieve pit arrays with a large dimension of 5 μm. Figure 7a shows the pit arrays obtained with a scratching velocity of 400 μm/s. Figure 7b, c shows the local and 3D AFM images of the machined pits, respectively. Because the scratching velocity slows down to 0 near the transition point of two different scratching directions, the depths of the first and last pits of one horizontal scratching path are much larger than the pits in the middle. One possible reason is explained above. As shown in Fig. 7b, c, the pits in the middle of the scratching path are distributed evenly, which may result from the constant velocity. Moreover, it can be observed from the cross-section of the pits shown in Fig. 7d that the depths of the pits are approximately 2.5 nm. In addition, because of the opposite scratching directions of the adjacent paths, the geometries of the pits in adjacent lines are different. As shown in Fig. 8a, with a scratching velocity of 200 μm/s, the spacing distance between the adjacent pits is relatively small and the geometries of the pits are close to circular. From the fast Fourier transform (FFT) image of the pits, high-density pits can be obtained with a scratching velocity of 200 μm/s. When scratching with a velocity of 900 μm/s, as shown in Fig. 8b, the spacing distance is nearly 100 nm and differences between pits obtained with different scratching directions can be clearly observed. Also from the FFT image of the pits, with a scratching velocity of 900 μm/s, only low-density pits can be achieved.
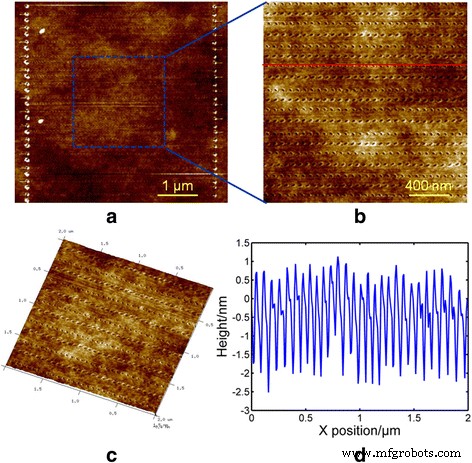
AFM images of an array of pits with a scratching velocity of 400 μm/s, a a dimension of 5 μm, b a portion of a with a dimension of 2 μm, c a 3D AFM image of b , e d a cross-section of pits for the red line in b
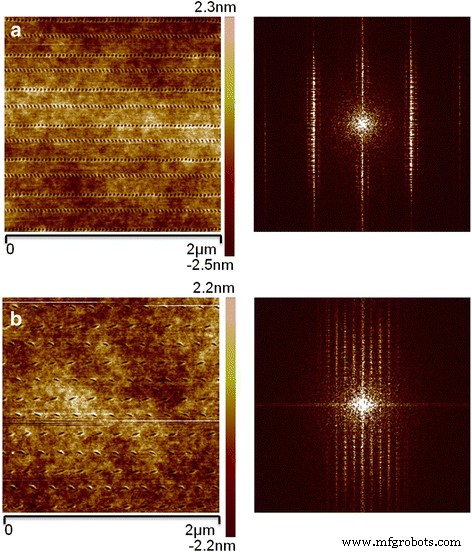
AFM image of pit arrary with a dimension of 2 μm and FFT image of the morphology. The scratching velocities are a 200 μm/s and b 900 μm/s
Conclusões
To improve the fabrication efficiency with the tip-based DPL method, a scratching velocity that ranges from 0.1 to 1000 μm/s is investigated and demonstrated based on the commercial AFM tapping mode. In the present study, results demonstrate that 100 μm/s is the critical value of the scratching velocity for the formation of pits. Nanogrooves with a pile-up can be obtained with scratching velocities less than the critical value. With scratching velocities greater than 5 μm/s, the machined depths are consistent in all typical directions except the V 3 direction, in which the machined depth becomes much smaller. In contrast, the depth is independent of the scratching direction. Separate pits can be generated with scratching velocities larger than the critical value of 100 μm/s. The total number of fabricated pits can reach nearly 4800–5800 in 1 s, when the scratching velocity is a constant value ranging from 200 to 900 μm/s. According to the stress relaxation modulus theory, the polymer surface is in the condition of a glass state when applying a high-frequency load. The energy applied on the sample surface is not large enough to break PMMA molecular chains during one penetration of the AFM tip. To form one pit, 65 to 80 penetrations are required. For the initial stage of penetration, elastic deformation is the dominant material removal mechanism. When the number of penetrations reaches 40 times, the polymer chains start to break and plastic deformation occurs. With increasing penetration depth, the height of the material accumulated beside the machined pit becomes larger, which will lead to an increase in the tangential force applied on the tip apex. This is the possible reason for the AFM tip sliding over the pile-up, after which one pit is created. Finally, pit arrays with dimensions of 5 μm, spacing distance of 70 nm, and machined depth of 2.5 nm are achieved successfully. FFT images are used to reveal the relationship between the density of pits and the scratching velocity.
Nanomateriais
- Pioneiros do AFM reconhecidos com o Prêmio Kavli
- Fabricação em lote de microlentes planas metálicas de banda larga e suas matrizes combinando automontagem de nanosfera com fotolitografia convencional
- Fabricação de nanopadrão ordenado usando copolímero tribloco ABC com sal em tolueno
- Fabricação de alto rendimento de nanofibras de qualidade usando eletrofiação de superfície livre modificada
- Fabricação de padrões de comutação ótica com microfibras estruturais coloridas
- Litografia de difração baseada em máscara de uma etapa para a fabricação de estruturas suspensas 3D
- Uma referência de voltagem sem resistor de baixa potência em nanoescala com alto PSRR
- Ge pMOSFETs de alta mobilidade com passivação de Si amorfo:impacto da orientação da superfície
- Fabricação de chips nanofluídicos de polidimetilsiloxano sob o processo de nanomilling baseado em ponta de AFM
- Tinta polimérica estável com alta condutividade