Rebolo
Antecedentes
Os rebolos são feitos de minerais abrasivos naturais ou sintéticos unidos em uma matriz para formar um rebolo. Embora essas ferramentas possam ser familiares para aqueles que trabalham em casa, o público em geral pode não estar ciente delas porque a maioria foi desenvolvida e usada pela indústria de manufatura. Neste setor, os rebolos são importantes há mais de 150 anos.
Para os fabricantes, os rebolos oferecem uma maneira eficiente de modelar e finalizar metais e outros materiais. Os abrasivos costumam ser a única maneira de criar peças com dimensões precisas e acabamentos de superfície de alta qualidade. Hoje, os rebolos aparecem em quase todas as empresas de manufatura nos Estados Unidos, onde são usados para cortar blocos de aço e alvenaria; para afiar facas, brocas e muitas outras ferramentas; ou para limpar e preparar superfícies para pintura ou galvanização. Mais especificamente, a precisão do automóvel árvores de cames e motor a jato os rotores dependem do uso de rebolos. Rolamentos de qualidade não poderiam ser produzidos sem eles, e novos materiais, como cerâmica ou materiais compostos, seriam impossíveis sem rebolos para dar forma e acabamento às peças.
O arenito, um abrasivo orgânico feito de grãos de quartzo mantidos juntos em um cimento natural, foi provavelmente o abrasivo mais antigo; era usado para alisar e afiar a pederneira em machados. No início do século XIX, o esmeril (um mineral natural que contém ferro e corindo) foi usado para cortar e dar forma a metais. No entanto, a qualidade variável do esmeril e os problemas com sua importação da Índia antes de sua descoberta nos Estados Unidos levaram a esforços para encontrar um mineral abrasivo mais confiável.
Na década de 1890, a pesquisa resultou no carboneto de silício, um mineral sintético mais duro que o corindo. Eventualmente, os fabricantes descobriram como produzir uma alternativa ainda melhor, corindo sintético ou óxido de alumínio. Ao criar esse derivado da bauxita, eles desenvolveram um material abrasivo mais confiável do que os minerais naturais e o carboneto de silício. A pesquisa em minerais sintéticos também levou à produção dos chamados superabrasivos. Em primeiro lugar nesta categoria estão os diamantes sintéticos e um mineral conhecido como nitreto de boro cúbico (CBN), perdendo em dureza apenas para o diamante sintético. Hoje, o desenvolvimento continua e um óxido de alumínio em gel semeado acaba de ser introduzido.
Ao longo da história do rebolo, a ligação que mantém os grãos abrasivos juntos provou ser tão importante quanto os próprios grãos. O sucesso dos rebolos começou no início da década de 1840, quando títulos contendo borracha ou argila foram introduzidos e, na década de 1870, um aglomerado com estrutura vitrificada ou semelhante a vidro foi patenteado. Desde então, as ligações usadas em rebolos foram continuamente refinadas.
Os rebolos estão disponíveis em uma ampla variedade de tamanhos, variando de menos de 0,25 polegada (0,63 centímetro) a vários pés de diâmetro. Eles também estão disponíveis em vários formatos:discos planos, cilindros, copos, cones e rodas com um perfil cortado na periferia são apenas alguns exemplos. Embora muitas técnicas, como a colagem de uma camada de abrasivos à superfície de uma roda de metal, sejam usadas para fazer rebolos, esta discussão é limitada a rodas compostas de materiais vitrificados contidos em uma matriz de ligação.
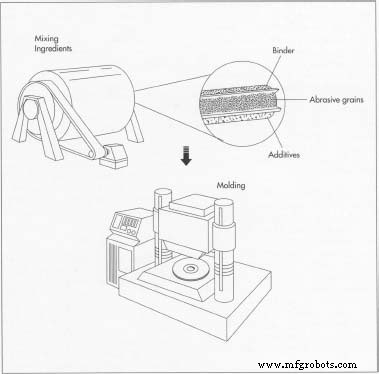
Matérias-primas
Dois componentes importantes, grãos abrasivos e materiais de ligação, constituem qualquer rebolo. Freqüentemente, os aditivos são misturados para criar uma roda com as propriedades necessárias para dar forma a um determinado material da maneira desejada.
Os grãos abrasivos constituem o componente central de qualquer rebolo, e a dureza e a friabilidade dos materiais de esmerilamento afetarão significativamente o comportamento de um determinado rebolo. A dureza é medida em termos de uma escala relativa desenvolvida em 1812 por um mineralogista alemão chamado Friedrich Mohs. Nesta escala, o talco extremamente macio e o gesso representam as durezas de um e dois, e o corindo e o diamante representam a dureza de nove e dez.
Friabilidade se refere à facilidade com que uma substância pode ser fraturada ou pulverizada. As pessoas que projetam rebolos de esmeril consideram a friabilidade de seus abrasivos - que podem diferir com a natureza dos materiais sendo polidos - com muito cuidado. Por exemplo, embora o diamante seja o material mais duro conhecido, é um abrasivo de aço indesejável porque sofre uma reação química destrutiva durante o processo de corte; o mesmo é verdade para o carboneto de silício. Por outro lado, o óxido de alumínio corta ferros e aços melhor do que o diamante e o carboneto de silício, mas é menos eficaz no corte de substâncias não metálicas.
Se selecionado corretamente, um abrasivo escolhido para dar forma a uma determinada substância manterá sua friabilidade quando moído contra essa substância:como a moagem fará com que o abrasivo continue a se fraturar ao longo de linhas nítidas e afiadas, ele manterá uma borda afiada durante todo o processo de moagem. Isso dá ao rebolo a característica única de ser uma ferramenta que se afia durante o uso.
Embora os abrasivos aglomerados tenham começado como ferramentas feitas de minerais naturais, os produtos modernos são feitos quase que exclusivamente com materiais sintéticos. Um material de ligação mantém os grãos abrasivos no lugar e permite um espaço aberto entre eles. Os fabricantes de rebolos atribuem uma dureza ao rebolo, que não deve ser confundida com a dureza do grão abrasivo. As ligações que permitem que os grãos abrasivos se quebrem facilmente são classificadas como ligações do solo. As ligações que restringem a fratura dos grãos e permitem que uma roda suporte grandes forças são classificadas como ligações duras. Geralmente, as rodas de solo cortam facilmente, produzem acabamentos de superfície ruins e têm uma vida útil curta. Por outro lado, as rodas mais duras duram mais e produzem acabamentos de superfície mais finos, mas cortam menos bem e produzem mais calor durante o desbaste.
A matriz de ligação na qual os grãos abrasivos são fixados pode incluir uma variedade de materiais orgânicos, tais como borracha, goma-laca ou resina; materiais inorgânicos como argila também são usados. Ligações inorgânicas com estruturas semelhantes a vidro ou vítreas são usadas nas rodas de afiação de ferramentas para o amolador doméstico, enquanto ligações de resina são usadas em discos de alvenaria ou de corte de aço. Geralmente, ligas vitrificadas são usadas com grãos de tamanho médio a fino em rodas necessárias para trabalhos de precisão. Os títulos de resina são usados geralmente com grãos grossos e para operações de remoção de metais pesados, como trabalhos de fundição.
Além de seus materiais abrasivos e de ligação, os rebolos freqüentemente contêm ingredientes adicionais que produzem poros dentro do rebolo ou auxiliam quimicamente quando um determinado abrasivo é usado para moer um material especial. Um aspecto importante de um rebolo que pode ser criado ou alterado por meio de aditivos é a porosidade, que também contribui para as características de corte do rebolo. Porosidade refere-se aos espaços abertos dentro da ligação que permitem espaço para pequenos fragmentos de metal e abrasivos gerados durante o processo de retificação. A porosidade também fornece caminhos que transportam fluidos usados para controlar o calor e melhorar as características de corte dos grãos abrasivos. Sem a porosidade e espaçamento adequados entre os grãos abrasivos, a roda pode ficar carregada de cavacos e parar de cortar corretamente.
Uma variedade de produtos é usada como aditivo para criar porosidade e espaçamento adequados. No passado, eram usados serragem, cascas de nozes trituradas e coque, mas hoje os materiais que evaporam durante a etapa de cozimento da fabricação (por exemplo, cera naf talina) são os preferidos. Alguns rebolos recebem materiais adicionais que auxiliam no esmerilhamento. Isso inclui compostos de enxofre e cloro que inibem a soldagem microscópica de partículas de metal e geralmente melhoram as propriedades de corte de metal.
O processo de fabricação
A maioria dos rebolos são fabricados pelo método de prensagem a frio, no qual uma mistura de componentes é moldada em temperatura ambiente. Os detalhes dos processos variam consideravelmente dependendo do tipo de roda e das práticas de cada empresa. Para a produção em massa de pequenas rodas, muitas partes do processo são automatizadas.
Misturando os ingredientes
- 1 A preparação da mistura do rebolo começa com a seleção de quantidades precisas de abrasivos, materiais de ligação e aditivos de acordo com uma fórmula específica. Um aglutinante, normalmente um agente umectante à base de água no caso de rodas vitrificadas, é adicionado para revestir os grãos abrasivos; esse revestimento melhora a adesão dos grãos ao ligante. O aglutinante também ajuda o rebolo a reter sua forma até que a ligação se solidifique. Alguns fabricantes simplesmente misturam todos os materiais em um único misturador. Outros usam etapas separadas para misturar grãos abrasivos com aglutinante.
Os fabricantes de rodas freqüentemente despendem esforços consideráveis para desenvolver uma mistura satisfatória. A mistura deve fluir livremente e distribuir os grãos uniformemente por toda a estrutura do rebolo para assegurar ação de corte uniforme e vibração mínima conforme o rebolo gira durante o uso. Isso é particularmente importante para rodas grandes, que podem ter vários metros de diâmetro, ou para rodas que têm um formato diferente do conhecido disco achatado.
Moldagem
- 2 Para o tipo mais comum de disco, um disco anular, uma quantidade predeterminada de mistura de rebolo é derramada em um molde que consiste em quatro peças:um pino circular do tamanho do orifício do mandril do disco acabado (seu orifício central); uma concha com uma parede de 1 polegada (2,5 centímetros), cerca de duas vezes mais alta que a espessura do rebolo desejado; e dois planos,
Após a moldagem e a conformação final, a roda é queimada em um forno ou fornalha. A queima derrete o aglutinante em torno dos abrasivos e o converte em uma forma que resiste ao calor e aos solventes encontrados durante a moagem. As etapas de acabamento que seguem o disparo podem incluir alargar o orifício da árvore (centro) para o tamanho adequado, corrigir a espessura dos lados da roda, equilibrar a roda e adicionar etiquetas. placas circulares com diâmetros e tamanhos de orifícios iguais aos da roda. Vários métodos são usados para distribuir a mistura uniformemente. Normalmente, uma borda reta gira em torno do pino da árvore central para espalhar a mistura por todo o molde.
- 3 Usando pressões na faixa de 100 a 5.000 libras por polegada quadrada (psi) por 10 a 30 segundos, uma prensa hidráulica compacta a mistura na forma final do rebolo. Alguns fabricantes usam blocos padrão entre as duas placas frontais para limitar seu movimento e estabelecer uma espessura uniforme. Outros controlam a espessura da roda monitorando de perto a consistência da mistura e a força da prensa.
- 4 Após o molde ter sido removido da prensa e a roda retirada do molde, a roda é colocada em um suporte plano e resistente ao calor. A moldagem final da roda pode ocorrer neste momento. Todo o trabalho nesta fase deve ser feito com muito cuidado porque a roda é mantida unida apenas pelo aglutinante temporário. Rodas mais leves podem ser levantadas manualmente nesta fase; os mais pesados podem ser içados com uma talha ou cuidadosamente colocados em um transportador para serem transportados ao forno.
Demissão
- 5 Geralmente, o objetivo da queima é derreter o aglutinante em torno dos abrasivos e convertê-lo em uma forma que resista ao calor e aos solventes encontrados durante a moagem. Uma ampla variedade de fornos e fornos são usados para queimar rebolos, e as temperaturas variam amplamente dependendo do tipo de ligação. As rodas com ligação de resina são disparadas normalmente a uma temperatura de 300 a 400 graus Fahrenheit (149 a 204 graus Celsius), e as rodas com ligações vitrificadas são disparadas a temperaturas entre 1700 e 2300 graus Fahrenheit (927 a 1260 graus Celsius).
Acabamento
- 6 Após o disparo, as rodas são movidas para uma área de acabamento, onde os orifícios do mandril são alargados ou fundidos no tamanho especificado e a circunferência da roda é feita concêntrica com o centro. Podem ser necessárias etapas para corrigir a espessura ou o paralelismo dos lados da roda ou para criar contornos especiais nas laterais ou na circunferência da roda. Os fabricantes também equilibram rodas grandes para reduzir a vibração que será gerada quando a roda for girada em uma retificadora. Assim que as rodas receberem etiquetas e outras marcações, elas estarão prontas para envio ao consumidor.
Controle de qualidade
Não existem padrões de desempenho claros para rebolos. Com exceção daqueles que contêm abrasivos caros, como diamantes, os rebolos são itens consumíveis e as taxas de consumo variam consideravelmente dependendo da aplicação. No entanto, uma série de padrões nacionais e globais são aceitos, voluntariamente, pelos fabricantes.
Organizações comerciais, que representam alguns fabricantes no altamente competitivo mercado dos EUA, desenvolveram padrões que abrangem questões como dimensionamento de grãos abrasivos, rotulagem de produtos abrasivos e o uso seguro de rebolos.
A extensão em que a qualidade do rebolo é verificada depende do tamanho, custo e eventual uso dos rebolos. Normalmente, os fabricantes de rodas monitoram a qualidade das matérias-primas que chegam e seus processos de produção para garantir a consistência do produto. Atenção especial é dada a rodas com mais de 15 centímetros de diâmetro, porque elas têm o potencial de prejudicar pessoas e equipamentos se quebrarem durante o uso. Cada grande roda vitrificada é examinada para determinar a resistência e integridade do sistema de colagem, bem como a uniformidade do grão em cada roda. Os testes acústicos medem a rigidez da roda; os testes de dureza garantem a dureza correta das ligações; e os testes de rotação garantem a resistência adequada.
O Futuro
Mudanças nas práticas de fabricação determinarão a demanda por vários tipos de rodas no futuro. Por exemplo, a tendência da indústria do aço para o lingotamento contínuo como forma de fazer aço reduziu muito o uso de alguns tipos de rebolos nessa indústria. Um impulso para maior produtividade por parte dos fabricantes é responsável por projeções de mercado que mostram uma mudança de rodas feitas de abrasivos de óxido de alumínio tradicionais para rodas feitas de formas mais novas de abrasivos sintéticos, como o óxido de alumínio em gel semeado e nitreto de boro cúbico. Além disso, o uso de materiais avançados, como cerâmicas e compostos, aumentará a demanda por novos tipos de rebolos. A transição para novos minerais abrasivos, no entanto, está sendo impedida pelo fato de que muitos equipamentos de manufatura e muitos procedimentos industriais ainda são incapazes de fazer uso eficaz dos produtos mais novos (e mais caros). Apesar das tendências, os abrasivos tradicionais devem continuar servindo a muitos usos.
No entanto, é provável que a competição de várias tecnologias alternativas cresça. Os avanços nas ferramentas de corte feitas de materiais policristalinos superabrasivos - materiais cristalinos de grãos finos feitos de diamante ou nitreto de boro cúbico - tornarão essas ferramentas uma opção viável para moldar materiais duros. Além disso, os avanços na deposição de vapor químico de filmes de diamante afetarão a necessidade de abrasivos, prolongando a vida útil das ferramentas de corte e estendendo suas capacidades.
Processo de manufatura
- Roda giratória
- Roda gigante
- Lucratividade de fabricação por meio de ferramentas de corte bem mantidas
- Corte e polimento de uma roda de moagem | Indústrias | Metalurgia
- Teoria do rebolo | Metais | Indústrias | Metalurgia
- Lixamento de superfície à moda antiga
- Introdução à retificadora de superfície PLC
- Quatro tipos de retificadoras e seus usos
- Entendendo os volantes de automóveis
- Fundamentos da retificação OD