Processo direto de fundição de minério de ferro para fabricação de ferro
Processo direto de fundição de minério de ferro para fabricação de ferro
O processo de fundição direta de minério de ferro (DIOS) é um processo de redução de fundição para a produção de metal quente (ferro líquido). É um processo de duas etapas que foi desenvolvido no Japão. Utiliza carvão não coqueificável em pó ou granulado para fundir finos de minério de ferro em ferro líquido (metal quente) e, portanto, não há necessidade de uma planta de coqueria e uma planta de sinterização. Os finos de minério são pré-reduzidos em um forno de leito fluidizado e são carregados no forno de redução de smelting juntamente com carvão não-coque e fundentes. O oxigênio é soprado no forno de redução de fundição.
As duas etapas do processo DIOS consistem em (i) pré-redução do minério de ferro em forno de redução preliminar (PRF), e (ii) redução final e fusão no forno de redução de smelting (SRF). A pré-redução do minério é realizada em duas etapas utilizando o gás de exaustão do SRF. Cada uma das etapas utiliza um reator de leito fluidizado que é projetado como um forno vertical.
O desenvolvimento do processo DIOS começou em 1988 no Japão como um projeto de pesquisa conjunto entre oito empresas de fabricação de ferro que, antes de 1988, estudavam individualmente o processo de redução de fundição. Este projeto foi patrocinado pelo MITI, o Ministério Japonês de Comércio Internacional e Indústria. As empresas japonesas e a Japan Iron and Steel Federation (JISF) apoiaram ativamente o desenvolvimento do processo durante o período de 1988 a 1996.
O estudo da tecnologia central necessária para a construção da planta piloto foi feito durante o período de 1988 a 1990. Durante este período, as tecnologias centrais foram estabelecidas. Essas tecnologias principais incluem (i) um aumento na eficiência térmica de um SRF, (ii) a tecnologia a ser integrada a um PRF, (iii) a tecnologia para a descarga de escória líquida e (iv) a ampliação do SRF. Uma planta piloto de 500 toneladas por dia de capacidade com base no conceito de processo foi construída e comissionada em 1993 na fábrica de Keihin da NKK Corporation (agora parte da holding JFE). Para o teste da planta piloto, o SRF utilizado foi um forno de oxigênio básico modificado de 250 t.
Os testes da planta piloto foram realizados no período de 1993 a 1995. A possibilidade de utilização direta de pó de minério de ferro, minério granulado e carvão foi confirmada durante os testes da planta piloto. No entanto, durante os dois anos de teste, muitas experiências valiosas foram adquiridas, a maioria delas positivas e algumas negativas. As experiências negativas testemunhadas durante os testes da planta piloto foram as seguintes.
- Houve baixo nível de pré-redução, geralmente abaixo de 30%. Isso trouxe muita pressão sobre a SRF.
- A movimentação do minério de ferro no leito fluidizado não foi suave e foi observado problema de aderência no leito fluidizado do PRF.
Durante os testes da planta piloto, foram determinadas as especificações dos equipamentos necessários. Com diversas matérias-primas, foram determinados os equipamentos e especificações operacionais para alcançar alta eficiência térmica, como alternativa ao alto-forno. Além disso, a tecnologia para resfriamento a água do corpo do forno foi estabelecida. Foi realizado um projeto conceitual e uma avaliação econômica (estudo de viabilidade) para instalações comerciais. Foram esclarecidas as condições das instalações e das operações para comprovar a superioridade em relação ao alto-forno, conforme demonstrado nos resultados da pesquisa.
Com base nos dados do avião piloto, foi realizado um estudo de viabilidade no Japão juntamente com os parâmetros de desempenho para a planta comercial de 6.000 toneladas por dia (capacidade anual de 2 milhões de toneladas). O fluxograma para esta planta está na Fig 1. Quando comparado com a produção de 2 milhões de toneladas de metal quente pelo processo de alto-forno, percebeu-se que (i) o custo de investimento é reduzido em 35%, (ii) o custo de produção de metal quente é reduzido em 19%, (iii) o consumo de carvão está na faixa de 730 kg/tHM a 750 kg/tHM (tonelada de metal quente), que é equivalente ao do processo de alto-forno, (iv) o consumo líquido de energia é reduzido em 3 % a 4 %, e (v) as emissões de CO2 no processo de fabricação do ferro são reduzidas em 4 % a 5 %.
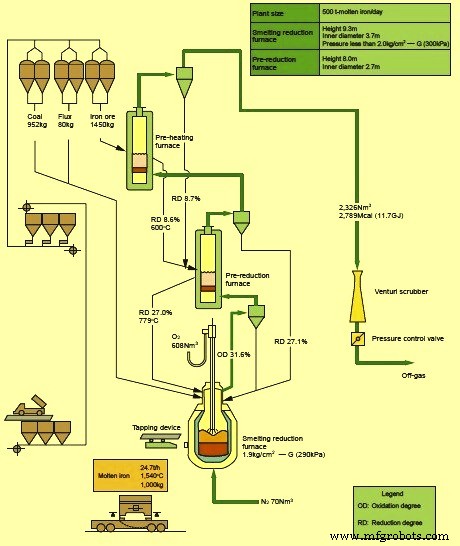
Fig 1 Folha de fluxo de 6.000 toneladas por dia planta DIOS
Descrição do processo
O processo DIOS tem as características de (i) minério de ferro e finos de carvão podem ser usados diretamente, (ii) não há exigência de coque e, portanto, não há restrição quanto ao tipo de carvão usado no processo, (iii) processo pode ser parado e reiniciado facilmente e, portanto, boa flexibilidade e (iv) a intensidade de agitação do banho pode ser otimizada para maior grau de pós-combustão e para melhor eficiência de transferência de calor.
Os finos de minério de ferro (tamanho 0-8 mm) sem sinterização são pré-aquecidos a cerca de 500°C na primeira etapa da pré-redução e reduzidos em cerca de 5% no primeiro de dois reatores de leito fluidizado operando em série e ainda pré-reduzidos para cerca de 15% a 25% no segundo reactor. Para esta pré-redução, é usado gás de exaustão limpo do SRF. A temperatura do minério de ferro atinge cerca de 800 graus C durante a segunda etapa de pré-redução. O minério pré-reduzido é transferido para o SRF para redução final e fusão.
A maior parte do carvão não coqueificável (tamanho inferior a 25 mm) necessário para o processo é carregado por gravidade no SRF. O oxigênio é injetado no SRF a partir do topo para combustão do carvão primário, bem como para pós-combustão. A lança de oxigênio é projetada para fornecer oxigênio de alta velocidade para oxidação de carbono (sopro forte) e oxigênio de baixa velocidade para pós-combustão na borda livre (sopro suave) simultaneamente. O monóxido de carbono (CO) gerado é utilizado para pré-reduzir o minério de ferro na PRF. A temperatura no SRF é de cerca de 1500 graus C. O nitrogênio é soprado no fundo do SRF para agitação do banho.
A redução de óxidos de ferro fundido em SRF é promovida pelo carvão carbonizado que é char, e contendo carbono no ferro. Três camadas de material existem dentro do SRF. Essas camadas são (i) camada superior consistindo de mistura de carvão e minério parcialmente reduzido, (ii) camada intermediária consistindo de escória fundida contendo carvão e minério fundido, e (iii) camada inferior consistindo de metal quente. A poeira removida dos gases de exaustão do SRF e os finos removidos dos gases que saem dos reatores de leito fluidizado (ambos dos PRFs) são injetados de volta no SRF. Além disso, uma pequena quantidade de finos de carvão, da ordem de 50 kg por tonelada de produção de metal quente, é injetada no gás de exaustão da SRF para resfriar o gás de exaustão. O carbono deste carvão reage com o CO2 do gás de exaustão para dar CO, enquanto a dissociação da matéria volátil do carvão fornece CO e H2. Essa quantidade adicional de CO e H2 auxilia na pré-redução de minério em PRF.
O objetivo do processo é atingir uma pós-combustão de cerca de 40% e uma pré-redução de cerca de 20% a 30%. Nestas condições espera-se que o consumo de carvão seja de cerca de 700 kg/tHM a 800 kg/tHM dependendo do tipo de carvão não coqueificável. Normalmente, o consumo de carvão é maior com carvões com alta matéria volátil.
O processo DIOS opera a uma pressão de 1 kg/sq cm a 2 kg/sq cm e usa top feed de carvão e minério. Utiliza uma lança superior para injeção de oxigênio e possui sistema de leito fluidizado para pré-redução de minério de ferro. No SRF, a maior parte da redução ocorre em uma camada de escória espumosa. O poder calorífico do gás de exportação é de cerca de 1000 -1100 kcal/N cum. Este gás pode ser usado para geração de energia.
Para que o processo DIOS seja bem-sucedido, existem seis elementos básicos do processo que devem ser controlados. Além disso, há necessidade de controlar a interação entre esses seis elementos. Esses seis elementos básicos do processo DIOS são apresentados a seguir.
- Grau de pré-redução – maior é o grau de pré-redução, menor é a carga no SRF.
- Taxa de pós-combustão – A taxa de pós-combustão determina o grau de pós-combustão dos gases em evolução no SRF. É utilizado para a avaliação do potencial de geração de calor do SRF, e também significa o potencial redutor dos gases de escape na fase de pré-redução. Praticamente, é determinado pela análise dos gases de escape. Se a taxa de pós-combustão for alta, o gás de exaustão que sai do SRF tem mais CO2 e H2O, diminuindo assim seu potencial como gás redutor. Observa-se que com cerca de 50% pós-combustão e um nível de pré-redução de 25% a 30%, pode-se obter uma boa eficiência do SRF. O alto valor de pós-combustão leva à utilização do valor combustível de CO e H2 mais no próprio reator de fundição. Assim, reduz o consumo de carvão.
- Cinética da reação – Devido ao sopro de oxigênio no SRF, o tempo para que o processo seja concluído é bastante curto e a cinética da reação é importante. A taxa de produção em SRF depende da cinética da reação.
- Eficiência de transferência de calor ou eficiência energética – A eficiência de transferência de calor é definida como a razão entre o calor efetivamente usado na fundição e o calor total gerado na SRF. Para uma melhor eficiência do combustível, é necessário que o calor gerado na pós-combustão seja efetivamente transferido para a escória e o metal quente para sustentar as reações endotérmicas que ocorrem ali e também para combater as perdas de calor.
- Custo de produção – Para que o processo seja competitivo, o custo de produção deve ser controlado de forma que seja inferior ao custo de produção do gusa produzido pelo processo de alto-forno.
- Aspectos ambientais – As emissões do processo devem ser controladas de forma que ofereça vantagens em relação à rota do alto-forno.
Parâmetros de processo e consumos específicos
Os valores típicos para os parâmetros do processo e consumo específico são fornecidos na Tab 1.
Tab 1 Valores típicos para parâmetros de processo e consumo específico | |||
Sl. No. | Parâmetro | Unidade | Valor |
1 | Análise típica de carvão não coqueificável | ||
Matéria volátil | % | <40 | |
Carvão fixo | % | 60-88 | |
Umidade | % | 4-6 | |
Cinza | % | 8-12 | |
Enxofre | % | <0.6 | |
Tamanho da partícula | % | <30 | |
2 | Pré-redução de minério | % | 20-30 |
3 | Consumo de oxigênio | N cum/tHM | Cerca de 500 |
4 | Consumo de carvão | kg/tHM | 700-800 |
5 | Consumo de eletricidade | kWh/tHM | Cerca de 75 |
6 | Consumo de vapor de baixa pressão | kg/tHM | Cerca de 80 |
7 | Gás de escape | ||
Quantidade | N cum/tHM | Por volta de 1800 | |
Valor calórico | kcal/N cum | 1000-1100 | |
8 | Saída de energia | M cal/tHM | Por volta de 1850 |
9 | Geração de vapor de baixa pressão | kg/tHM | Cerca de 700 |
10 | Geração de eletricidade | kWh/tHM | Cerca de 30 |
11 | Composição típica dos gases de escape | ||
H2 | % | 15 | |
CO | % | 30 | |
CO2 | % | 20 | |
N2 | % | 15 | |
H2O | % | 20 |
A qualidade típica do metal quente produzido pelo processo DIOS consiste em C- cerca de 3,5 %, Si - menos de 0,05 %, S - menos de 0,05 % e P - 0,10 %. Tanto o metal quente quanto a escória são vazados através de um orifício de torneira.
A comparação do processo DIOS e do processo BF em relação ao balanço de energia e emissões de CO2 é mostrada na Fig 2.
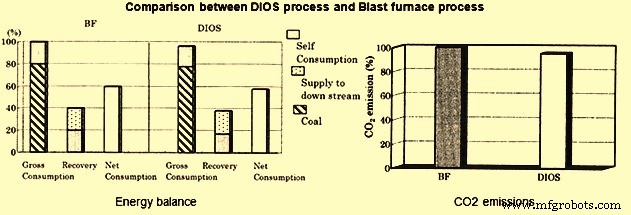
Fig 2 Comparação entre o processo DIOS e o processo BF
Vantagens e limitações do processo
DIOS tem as seguintes vantagens.
- Ele utiliza matérias-primas e combustível baratos (carvão não coqueificável, poeira interna etc.).
- O processo elimina a necessidade de uma planta de sinterização e uma planta de coqueria.
- Baixo custo de operação.
- Baixo consumo direto de energia elétrica.
- Tem menor consumo líquido de energia.
- É flexível em relação ao uso de matérias-primas e variações na taxa de produção, bem como em relação à parada e partida da planta.
- É compacto e precisa apenas de um pequeno investimento incremental.
- Os custos de investimento são estimados em cerca de 65% da produção equivalente de metal quente pelo processo de alto-forno.
- É estável e produz fornecimento de metal quente de alta qualidade.
- Contribui para o uso eficaz da energia do carvão.
- A coprodução fácil de energia (cogeração) é viável.
- Tem baixa carga ambiental (baixo SOx, NOx, CO2, geração de poeira, sem vazamento de gás de coqueria).
O processo DIOS tem as seguintes limitações.
- A temperatura da torneira está alta. Está na faixa de 1750 graus C a 1800 graus C.
- O desgaste dos refratários é alto devido às altas temperaturas. Por causa disso, há alto consumo de refratários e alto tempo de inatividade do processo necessário para o reembasamento.
- Devido ao uso de três reatores (2 números PRFs e um número SRF) no processo, os controles do processo são um pouco complexos.
- Como o nível de pré-redução é baixo (menos de 30%), a carga no SRF é alta, tornando a operação do SRF muito crítica para o sucesso do processo.
- Experiência na operação de uma planta de expansão está faltando na ausência de investimento na planta de expansão.
Processo de manufatura
- O processo de sinterização de finos de minério de ferro
- Processo Finex para Produção de Ferro Líquido
- Processo HIsmelt de fabricação de ferro
- Processo HIsarna para fabricação de ferro
- Processos FASTMET e FASTMELT de fabricação de ferro
- Processo CONARC para Siderurgia
- Beneficiamento de Minérios de Ferro
- Processo de Laminação para Aço
- Pelotas de minério de ferro e processo de pelotização
- Entendendo o processo de fundição de minério de ferro