Os fundamentos (e benefícios) da manutenção produtiva total
Adotar um modelo de manutenção preventiva para suas instalações e praticar seus princípios de acordo com uma rotina regular pode aumentar a produção geral de sua empresa, manter os equipamentos funcionando em um nível ideal e aliviar o tempo de inatividade. A manutenção produtiva total (TPM) está entre os métodos mais populares usados para atingir esses objetivos:A abordagem é altamente focada na capacitação dos funcionários e ajuda a garantir maior disponibilidade, desempenho e qualidade.
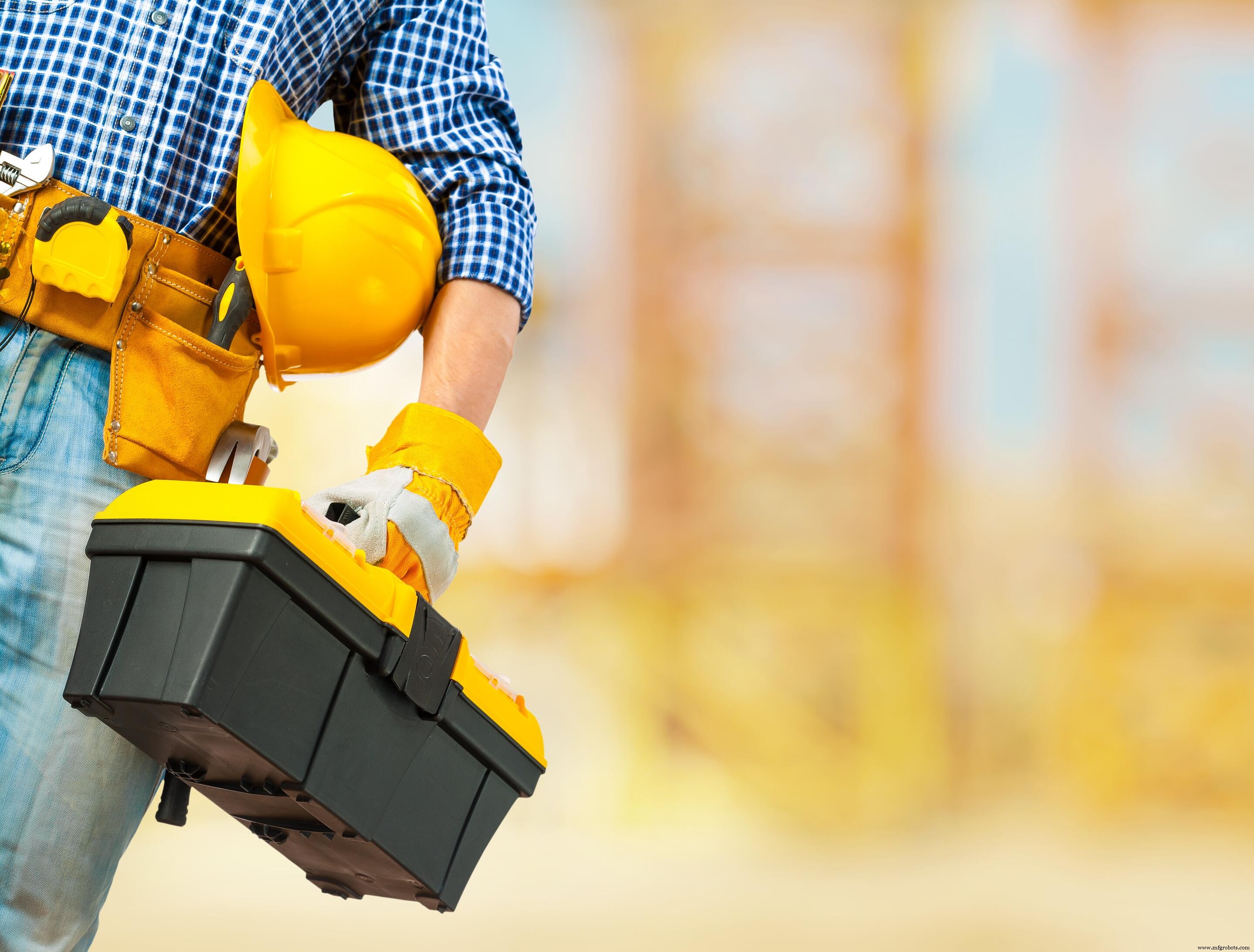
O desempenho é otimizado minimizando a probabilidade de quebras e garantindo que lentidão ou pausas operacionais sejam o menos frequentes possível. Isso, por sua vez, reduz significativamente a chance de defeitos do produto, o que pode ajudar a melhorar a qualidade de seus produtos acabados. Além disso, a implementação da estratégia de TPM pode gerar economias de custo notáveis ao longo do tempo, aumentando a eficiência geral do equipamento:de acordo com Mark Jolley, diretor de serviços de fabricação da consultoria do Marshall Institute, é possível ver os custos de manutenção caírem de 25 a 30% e os custos de conversão diminuirem em 20-25% em cinco anos.
Aqui, vamos explorar o que o TPM realmente envolve e também examinar mais de perto como ele beneficia fabricantes, empresas de serviços de alimentação, fornecedores de energia e empresas de vários outros setores industriais pesados.
Os fundamentos da manutenção produtiva total
Em sua essência, a abordagem TPM é sobre a maximização da produtividade – bem como a vida útil do equipamento – permitindo que os trabalhadores assumam mais responsabilidade por esses problemas no dia-a-dia. Isso é conseguido das seguintes maneiras:
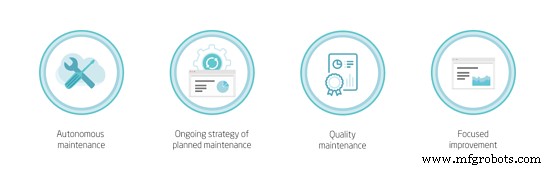
1. Manutenção autônoma
O TPM atribui as responsabilidades pelas tarefas de manutenção de rotina do equipamento, como lubrificação, limpeza e inspeção, aos operadores regulares de várias máquinas em toda a instalação. Os trabalhadores, portanto, não podem simplesmente deixar seus equipamentos em mau estado ou em mau estado, contando com a intervenção de técnicos de manutenção dedicados para trazê-los de volta ao funcionamento. (Pense desta forma:se eles foram para adotar essa abordagem despreocupada, o que você ganha quando a equipe de manutenção não está disponível por qualquer motivo? Tempo de inatividade não planejado, que nenhuma empresa pode suportar por muito tempo – ou, em alguns casos, até mesmo.)
Há muitos benefícios nessa técnica de manutenção proativa. Por um lado, a equipe de manutenção tem mais tempo para lidar com tarefas de nível superior – ou seja, lidar com falhas de equipamentos de produção realmente inesperadas e urgentes. Mas enquanto os operadores podem inicialmente estar menos entusiasmados em ter mais responsabilidades, o processo TPM aumenta seu grau de familiaridade com o equipamento ao longo do tempo, e isso facilita seu trabalho a longo prazo. Também garante que esses funcionários estejam mais bem equipados para identificar quaisquer pequenos problemas com o maquinário à medida que eles surgem e resolvê-los sem ter que trazer a equipe de manutenção para a cena.
2. Uma estratégia contínua de manutenção planejada
O TPM normalmente envolve o agendamento de tarefas de manutenção com base em taxas de falhas medidas e/ou previstas. Isso reduz os casos de paradas não planejadas, permite que os equipamentos sejam atendidos fora do horário de trabalho e reduz o estoque (através do controle aprimorado de peças propensas a falhas e propensas a desgaste). Nesse sentido, é a antítese da manutenção reativa, onde os reparos são feitos apenas quando absolutamente necessários – geralmente por causa de falha total ou quase catastrófica de uma máquina ou sistema.
3. Manutenção de qualidade
A implementação de uma estratégia de TPM pode ajudar uma organização a incorporar práticas de detecção e prevenção de erros no ciclo geral de produção. Isso decorre da base da metodologia nos princípios de análise de causa raiz (RCA):Observar a manutenção de uma perspectiva de RCA evita o exame de dinâmicas simples de causa e efeito no interesse de rastrear exatamente como um processo, sistema ou dispositivo falhou. Fazer isso equipa melhor os trabalhadores para determinar a resposta mais eficaz a um problema.
Como uma estrutura de TPM baseada em RCA geralmente se concentra na eliminação das causas dos defeitos que levam ao mau funcionamento ou falha do equipamento, ela melhora lenta mas seguramente a qualidade de várias operações. Além disso, ajuda a reduzir os custos aumentando as chances de que as falhas sejam descobertas precocemente, antes que possam causar muitos danos e exigir reparos caros ou tarefas de substituição.
4. O impulso para a melhoria focada
Esse aspecto do TPM é ter grupos menores de funcionários trabalhando juntos de forma proativa para alcançar melhorias sistemáticas e incrementais na operação da máquina. Dessa forma, você evita que os indivíduos fiquem presos à responsabilidade exclusiva de manter as coisas funcionando sem problemas com seus equipamentos e o caos que resulta de ter "cozinheiros demais na cozinha".
Aqui, equipes pequenas, mas multifuncionais, podem identificar e resolver problemas recorrentes. Também combina um conjunto de talentos dentro da empresa, e isso catalisa ainda mais a melhoria contínua.
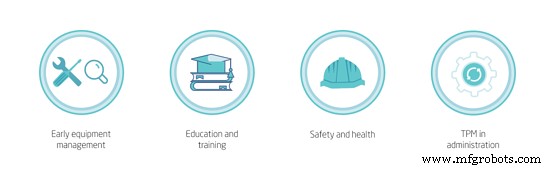
5. Gerenciamento antecipado de equipamentos
A compreensão e o conhecimento prático de máquinas de processamento adquiridos através da abordagem TPM são direcionados para a melhoria e projeto de novos equipamentos neste princípio. Como há menos problemas de inicialização quando o TPM é implementado e executado corretamente, o novo maquinário pode atingir seu nível de desempenho ideal mais rapidamente. Além disso, a manutenção do equipamento e outras atividades de manutenção são muito mais fáceis e robustas como resultado do envolvimento dos funcionários e da revisão prática antes da instalação.
6. Educação e treinamento
O TPM depende de preencher quaisquer lacunas de conhecimento que impeçam sua empresa de atingir as principais metas de manutenção. Isso se aplica a gerentes, pessoal de manutenção e operadores:
- Os gerentes treinam nos princípios de TPM juntamente com seus subordinados, funcionários laterais e superiores. Isso os ajuda a entender melhor como as partes interessadas em toda a organização lidam com os problemas de manutenção de seus pontos de vista distintos.
- O pessoal de manutenção aperfeiçoa as técnicas necessárias para a execução adequada das estratégias de gerenciamento proativo e preventivo de equipamentos.
7. Segurança e saúde
A manutenção de um ambiente de trabalho saudável e seguro deve ser uma preocupação fundamental para qualquer empresa onde máquinas pesadas (ou outros equipamentos que podem ser perigosos fora de seu contexto operacional adequado) são necessárias regularmente. Fazer isso é do melhor interesse tanto da simples decência humana quanto das complexidades da conformidade regulatória.
O TPM coloca essas preocupações na frente e no centro. Ele ajuda a eliminar potenciais riscos contínuos de segurança e saúde, ao mesmo tempo em que minimiza a possibilidade de acidentes repentinos e catastróficos.
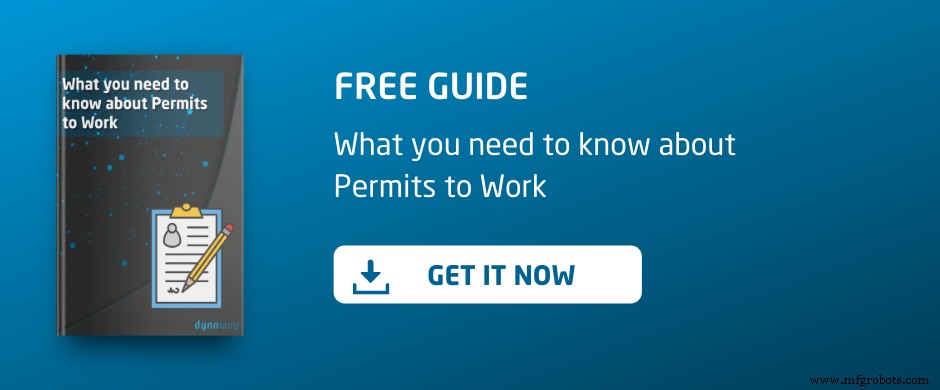
8. TPM na administração
Esse fundamental envolve a aplicação de técnicas de TPM às funções administrativas da empresa. Ele estende os benefícios da abordagem além do chão de fábrica da instalação, abordando qualquer tempo ou esforço desperdiçado no curso das operações executivas e gerenciais. Adotar esses princípios pode ser especialmente importante para melhorar a aquisição, programação, processamento de pedidos e gerenciamento de ativos.
Principais benefícios do processo TPM
Ao envolver os operadores no desempenho das tarefas de manutenção – e planejar e programar essas atividades para garantir uma supervisão consistente dos principais equipamentos – sua organização tem o potencial de obter os seguintes benefícios:
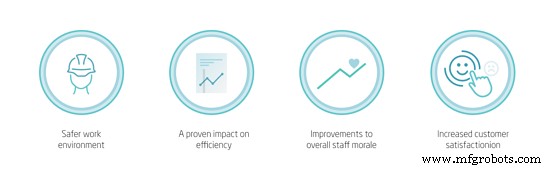
1. Ambientes de trabalho mais seguros
Além de frameworks como RCA, o TPM também é baseado no sistema de gestão estruturado comumente conhecido como método 5-S para suas etapas aliterativas:Ordenar, Colocar em ordem, Brilhar, Padronizar e Sustentar.
Todos os S's apontam para a ideia de que manter equipamentos e maquinários limpos, organizados e saudáveis pode melhorar a segurança no ambiente de trabalho. O foco do TPM na manutenção proativa e preventiva aumenta a vida útil do equipamento, além de reduzir a desordem no local de trabalho. Também facilita projetos que maximizam a produtividade, eficiência e fluxo. Todas essas qualidades formam a base da segurança dos trabalhadores em todos os níveis.
2. Um impacto comprovado na eficiência
O principal objetivo da abordagem TPM é alcançar uma condição às vezes chamada de "produção perfeita". Em outras palavras, qualquer fabricante que considere o TPM visa atingir zero defeitos, avarias ou acidentes. Isso significa que você pode ter que se concentrar na qualidade sobre a quantidade, ao mesmo tempo em que prioriza a eficiência sobre a produção.
Você pode medir o TPM usando a escala de classificação de eficiência geral do equipamento (OEE) — geralmente considerada o padrão-ouro para quantificar a produtividade no processo de fabricação. A classificação se aplica a configurações de processo e produção discreta. Ele facilita a melhoria identificando rapidamente quaisquer áreas de perda, comparando o progresso e melhorando a produtividade do equipamento — tudo com base em dados abrangentes. Métricas sólidas falam muito e, com o OEE, você pode comparar a instalação com os padrões do setor e confirmar se o programa de melhoria do TPM que você está usando está funcionando.
3. Melhorias no moral geral da equipe
Para implementar totalmente a manufatura enxuta, você precisa de funcionários em toda a organização em todos os níveis para comprar a ideia de todo o coração. Se apresentar resultados positivos, a equipe pode ser menos propensa a resistir inerentemente às mudanças.
O TPM é semelhante em muitos aspectos:por meio de seus princípios, os funcionários são capacitados com a responsabilidade de cuidar de seus equipamentos. Consequentemente, eles podem tender a ter orgulho e propriedade em seu trabalho. As medidas preventivas inerentes ao TPM resultam em menos casos de falha do equipamento e um mínimo de tempo de inatividade frustrante. Esses sucessos apenas aumentarão o comprometimento de seus funcionários com a filosofia TPM.
4. Maior satisfação do cliente
Um local de trabalho seguro, moral dos funcionários e produção eficiente são todos os principais benefícios da manutenção produtiva. No entanto, muitos argumentam que a experiência e a satisfação do cliente são ainda mais importantes a longo prazo. O pilar TPM de manutenção da qualidade permite a integração de melhorias de qualidade no processo de produção. Como resultado, geralmente há uma redução nos retrabalhos e defeitos e um aumento na produção e na qualidade. Isso, juntamente com máquinas confiáveis que experimentam menos tempo de inatividade, pode ajudar a aumentar o número de clientes satisfeitos e a repetir negócios.
Um programa TPM é ideal para o seu negócio?
Muito pouco é cortado e seco nos vários setores industriais e de manufatura, e cada empresa é diferente. Embora o TPM possa ser benéfico para qualquer empresa em teoria, na prática pode não ser o sistema perfeito para sua organização. Talvez valha a pena implementá-lo em uma escala menor, ou como um programa piloto, e observar os resultados por um período finito (vários meses ou mais) antes de se comprometer com ele como uma solução permanente.
A manutenção baseada em condições é semelhante ao TPM, mas alcança seu monitoramento contínuo de equipamentos por meio da implementação e alavancagem de estruturas de Internet das Coisas Industrial (IIoT). Isso pode ser preferível se você se sentir mais confortável em atribuir a supervisão da eficiência do equipamento à tecnologia de ponta (e totalmente objetiva). Dito isto, como o TPM, pode ser caro de implementar e mantê-lo também não é barato. Se você estiver realmente sem dinheiro, pode até ser necessário manter um modelo reativo por enquanto – mantendo o TPM em mente como um sistema ao qual aspirar.
Como você elabora a melhor estratégia de manutenção para o seu equipamento?
Você também pode considerar não escolher um modelo de manutenção específico em detrimento de outros:Em vez disso, você pode combinar elementos de vários métodos, criando um modelo exclusivo para as necessidades específicas de sua organização. Por exemplo, não seria irracional adotar uma abordagem reativa para equipamentos de baixa prioridade ou com risco reduzido de quebra. Ao mesmo tempo, você faria com que seus operadores adotassem uma abordagem prática de propriedade de tecnologia operacional crítica, como seu sistema de controle industrial (ICS). Essa diversidade de estilos levaria tempo para que os funcionários se acostumassem a ela, portanto, é melhor proceder gradualmente.
A manutenção produtiva – seja na estrutura TPM ou em outro formato – visa melhorar a confiabilidade dos equipamentos, inspirando os funcionários a se orgulharem de sua manutenção. Se bem feita, a abordagem pode trazer benefícios mensuráveis e duradouros, como cultura proativa da empresa, rotatividade reduzida, produção de melhor qualidade e maior satisfação do cliente.
A solução de gerenciamento de ativos corporativos (EAM) da Dynaway é ideal para facilitar a implementação de TPM, manutenção baseada em condições e estruturas preventivas semelhantes. Integrada no Microsoft Dynamics 365 Business Central, a solução simplifica os processos, incluindo ordem de serviço e gerenciamento de ativos, inventário, análise de falhas e registro de manutenção, para uma eficiência ideal em toda a instalação. Deixe para trás as dificuldades de lidar com ferramentas integradas de vários terceiros e centralize a supervisão das instalações e o EAM em uma plataforma de ponta.
Manutenção e reparo de equipamentos
- Navegando na modernização da manutenção e gestão de instalações
- Compreendendo os benefícios da manutenção preditiva
- Como implementar a manutenção produtiva total
- Aproveite os benefícios da manutenção planejada de forma eficiente
- Os benefícios da gestão estratégica de ativos
- Vodcast:Uma introdução à Manutenção Produtiva Total
- TOTAL desenvolve estratégia de manutenção e inspeção
- Os fundamentos e benefícios da manutenção baseada em condições
- Manutenção produtiva total e IoT industrial
- Manutenção Produtiva Total:uma alavanca de desempenho?