Injeção de carvão pulverizado em um alto-forno
Injeção de carvão pulverizado em um alto-forno
A injeção de carvão pulverizado (PCI) é um processo que envolve a injeção de grandes volumes de partículas finas de carvão na pista do alto-forno (BF). O carvão pulverizado é um importante combustível auxiliar utilizado na siderurgia BF. PCI fornece combustível auxiliar para substituição parcial de coque e provou ser economicamente e ambientalmente favorável. Pode resultar em melhoria substancial na eficiência do BF e, assim, contribuir para a redução do consumo de energia e das emissões ambientais.
Quando o carvão pulverizado é injetado no BF através de maçaricos e ventaneiras, o carvão é fonte de calor e redutor, devido às reações de desvolatilização, gaseificação e combustão, bem como a formação de carvão não queimado. No ambiente atual, o carvão pulverizado é amplamente utilizado em BFs como substituto parcial do coque metalúrgico. PCI é uma tecnologia bem estabelecida hoje para a produção de metal quente (HM) em um BF. É praticado na maioria dos BFs e todos os novos BFs são normalmente construídos com capacidade PCI. A composição e as propriedades do carvão utilizado para injeção podem influenciar a operação, estabilidade e produtividade do BF, a qualidade do HM e a composição do gás BF.
No cenário atual, existem muitos critérios que são usados para medir o desempenho do PCI. A primeira é a pulverização e manuseio. Os principais custos operacionais do PCI, além dos custos de carvão, estão relacionados à pulverização e distribuição do carvão ao BF. A segunda diz respeito ao funcionamento do BF. A qualidade do carvão injetado pode influenciar a qualidade do HM, a estabilidade do BF e a composição do gás de topo. A cinza do carvão injetado (i) pode atuar como um inibidor do processo oxidante, (ii) é o principal distribuidor de álcalis indesejáveis e (iii) consome energia de fusão. A terceira diz respeito ao benefício econômico. O principal custo benefício é a substituição do carvão coqueificável de alto custo acrescido dos custos operacionais de coqueificação, embora outros benefícios como a melhoria da produtividade também tenham sido observados, essa melhoria é dependente da qualidade do coque. Os importantes benefícios econômicos e operacionais do uso de PCI em BF incluem o seguinte.
- Menor consumo de carvões de coque caros. A substituição do coque BF por coque suave ou carvão térmico mais barato reduz os custos com redutores.
- Vida estendida do forno de coque, pois é necessário produzir menos coque. Isso é importante porque muitos fornos de coque estão chegando ao fim de sua vida útil e é necessário um investimento significativo para substituí-los ou mantê-los.
- O sistema PCI é mais barato do que o custo de uma bateria adicional de forno de coque. Menor custo de capital significa menor depreciação e juros a serem cobrados no HM.
- Maior produtividade de BF, ou seja, maior quantidade de HM produzida por dia (em conjunto com outras mudanças operacionais).
- Maior flexibilidade na operação BF. Por exemplo, o PCI permite que a temperatura da chama seja ajustada e a condição térmica no BF pode ser alterada muito mais rapidamente do que é possível ajustando a carga de carga na parte superior do forno.
- Consistência aprimorada na qualidade do HM e seu conteúdo de silício.
- Emissões gerais reduzidas da siderurgia, em particular, emissões mais baixas da produção de coque devido à diminuição dos requisitos de coque.
Histórico
A injeção de carvão pulverizado foi desenvolvida no século XIX, mas não foi implementada para uso industrial. No início da década de 1960, o PCI foi implementado com sucesso na AK Steel dos EUA e na Shougang na China. Embora os testes em vários países naquela época tivessem provado que a tecnologia de transporte pneumático e injeção de carvão estava disponível, a economia e a relativa facilidade do processo eram tais que a injeção de petróleo e gás natural se tornou mais popular. Na década de 1980, o interesse no PCI aumentou, impulsionado principalmente por aumentos dramáticos no preço do óleo combustível em 1973 e novamente em 1979, e seu potencial como substituto do coque começou a ser realizado. No início da década de 1980, instalações de injeção de carvão foram instaladas em toda a Europa e Japão, com taxas de injeção normalmente entre 40 kg/tHM e 90 kg/tHM e com taxas de reposição de coque da ordem de 0,9 kg de coque/kg de carvão. Este processo se desenvolveu muito rápido desde então e na segunda metade da década de 1980 houve práticas bem-sucedidas de injeções de carvão em taxas que variam de 180 kg/tHM a 200 kg/tHM. Nos anos noventa, as tecnologias PCI amadureceram. Mas a verdadeira mudança para o PCI ocorreu apenas quando o custo do coque metalúrgico começou a subir devido ao aumento da demanda global.
Carvão para PCI
A importância relativa de diferentes aspectos da qualidade do carvão para o PCI variou, à medida que a tecnologia de injeção melhorou e a taxa de injeção aumentou. No final da década de 1970, desencadeada pela crise do petróleo, o interesse pelo PCI foi renovado e o carvão foi considerado um combustível substituto econômico do petróleo. Como a combustibilidade era considerada importante, os carvões usados para PCI eram principalmente carvões térmicos. Naquela época, os carvões térmicos estavam prontamente disponíveis e tinham um custo muito menor do que os carvões de coque duro e semi-soft.
Após o foco inicial na combustibilidade do carvão injetado, o foco foi direcionado para o entendimento do impacto da qualidade do carvão na substituição do coque. Durante este período, verificou-se que carvões de baixa volatilidade (LV) deram melhores taxas de substituição do que carvões de alta volatilidade (HV).
No que diz respeito à pulverização de carvão, os quatro principais parâmetros operacionais do pulverizador são (i) taxa de alimentação, (ii) vazão de ar, (iii) ajuste do classificador composto por ciclone e filtro de mangas e (iv) pressão de moagem (carga em rolo/bola). A taxa de alimentação, a pressão de moagem e o ajuste do classificador têm influência direta na carga do pulverizador e, portanto, na potência necessária. A vazão de ar influencia indiretamente a potência do pulverizador, pois impacta na eficiência do classificador.
As características de moagem de carvões são tipicamente descritas pelos resultados de um pequeno número de testes analíticos padrão. Com base nestes resultados, são feitas previsões quanto ao comportamento de moagem antecipado dos carvões. Há uma tendência geral de reduzir uma avaliação do comportamento de moagem de carvões para o HGI (Índice de Moagem Hardgrove), que é uma medida para a moagem de carvão. A moagem é um índice e, portanto, não tem unidade. Quanto menor o HGI, mais difícil é a textura do carvão e menos retificável é o carvão. A moagem é um fator importante para a pulverização do carvão no pulverizador. Influencia a finura do produto, o consumo de energia e o rendimento.
O teor de umidade do carvão tem influência na pulverização do carvão. É necessário reduzir a umidade total contida no carvão em torno do nível de umidade de equilíbrio para reduzir os problemas de manuseio dentro do moinho pulverizador, bem como nos bunkers. O teor de umidade do carvão que sai do pulverizador deve ser dois terços do nível de umidade de equilíbrio. A quantidade de umidade que deve ser removida no pulverizador é dada pela equação 'umidade removida no pulverizador =(como umidade recebida) - 2/3 (umidade de equilíbrio)', onde a umidade de equilíbrio para o sub-betuminoso e superior rank carvões é aproximadamente dada pela equação 'umidade de equilíbrio =0,69 + 0,84 x (ar morreu umidade) + 0,18 x quadrado de (ar morreu umidade). O teor de umidade de equilíbrio varia com a classificação do carvão, composição maceral e teor de cinzas.
O tipo de carvão e sua umidade superficial governam os requisitos de secagem por pulverização. A capacidade de secagem de um determinado projeto de pulverizador depende da extensão da carga circulante dentro do pulverizador, da capacidade de misturar rapidamente os retornos do classificador seco com a alimentação de carvão úmido de entrada e da proporção de ar e da temperatura de entrada de ar que o projeto específico do pulverizador deve tolerar .
O sistema de processo PCI
O sistema de processo PCI consiste em uma série de subsistemas desde o recebimento de carvão até a injeção de carvão pulverizado em cada ventaneira para atender aos requisitos do PCI. Constitui seis números de subsistemas a saber (i) armazenamento e descarga do carvão bruto, (ii) pulverização e secagem do carvão bruto, (iii) transporte, armazenamento e fornecimento do carvão pulverizado para o sistema de injeção, (v ) distribuição uniforme de carvão pulverizado para cada ventaneira, (v) combustão de carvão pulverizado e (vi) instalações de prevenção de explosão. As características importantes do sistema de processo PCI são descritas abaixo.
O tanque reservatório é projetado para ter alta capacidade de forma que mesmo que uma das linhas de pulverização pare de operar, a injeção de carvão possa continuar até a correspondente alternância de condições operacionais, como a redução da quantidade de minério carregado no forno ou preparações para soprar são tomadas.
Existem três tanques de alimentação, um tanque de onde o carvão está sendo descarregado, o segundo tanque em stand-by para descarga e o terceiro tanque na fase de redução de pressão, enchimento de carvão pulverizado e pressurização após a conclusão do carregamento.
O duto de transporte, composto por um duto de fase densa e um duto de fase diluída, garante o transporte suave do carvão com pequenas perdas de pressão. A tubulação de alta pressão entre o tanque reservatório e as ventaneiras não possui partes móveis, exceto as válvulas de fechamento, o que garante alta disponibilidade e facilita o controle e a manutenção.
Para os processos de pulverização e armazenamento, um sistema confiável de prevenção de explosão é estabelecido através da instalação de supressores de explosão, extintores de incêndio etc.
Para uma operação bem-sucedida do sistema PCI, atenção deve ser dada a vários fenômenos que ocorrem no BF. Entre esses fenômenos destacam-se (i) grau de combustão do carvão injetado ou comportamento dos finos de carvão não queimados no leito de coque que afeta a distribuição do fluxo de gás na região de carga, (ii) comportamento das cinzas de carvão fundido ou possibilidade de sua deposição no maçarico -zona de ventaneira, (iii) permeabilidade ou distribuição de fluxo de gás na zona de carga afetada pela razão minério/coque aumentando com o aumento da taxa de injeção de carvão e (iv) propriedades térmicas representadas pela temperatura do gás de bosh ou a razão de fluxo de calor que afeta as reações ocorrendo na parte inferior do BF.
O posicionamento da lança de injeção no maçarico é importante e deve ser tal que assegure a combustão completa do carvão injetado dentro da zona da canaleta e ao mesmo tempo evite o depósito de cinzas de carvão na extremidade do maçarico. O fluxograma típico do processo PCI é mostrado na Fig 1.
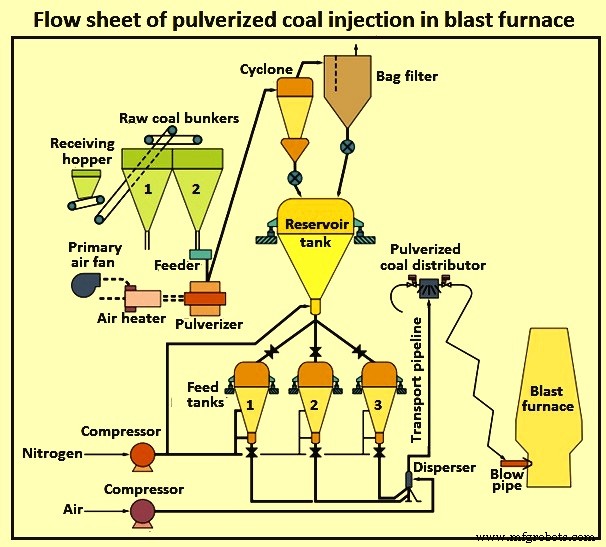
Fig 1 Fluxograma típico de injeção de carvão pulverizado em alto-forno
O processo de injeção de carvão
O processo PCI é baseado no conceito simples de transportar o carvão seco finamente moído (pulverizado) por um gás de transporte (normalmente nitrogênio) para o BF onde é distribuído para diferentes ventaneiras e injetado através de uma lança no tubo de sopro. No tubo de sopro, ele é misturado com ar quente de sopro enriquecido com oxigênio e então fornecido ao BF na pista.
O carvão bruto é recebido na tremonha de recebimento. Ele é peneirado e processado para remover materiais residuais e é armazenado em bunkers de carvão bruto. O carvão bruto é pulverizado, seco e então transportado pneumaticamente para o classificador em um sistema de passagem única. O carvão é completamente seco para evitar assoreamento e compactação. O carvão pulverizado é depositado em um único tanque reservatório onde é armazenado em condições inertes.
O carvão pulverizado é alimentado por gravidade do tanque reservatório para os tanques de alimentação que são então pressurizados com gás inerte como parte de um processo em lote no qual os tanques de alimentação estão enchendo, alimentando, ventilando ou retendo para fornecer um fluxo contínuo de carvão pulverizado no BF. A vazão do carvão pulverizado é regulada pela pressão do gás inerte em função da variação do peso do tanque de alimentação. O fluxo único de carvão de fase densa de um tanque de alimentação é combinado com o gás de transporte (nitrogênio) no T de mistura.
Um único tubo de transporte transporta a mistura carvão/gás para um distribuidor de carvão localizado no BF (Fig. 2). No distribuidor, o fluxo único de mistura de carvão/gás é dividido automaticamente em vários fluxos iguais e transportado por um tubo em cada ventaneira para injeção no BF. Um sistema detector de blocos protege contra o bloqueio da ventaneira.
Fig 2 Tipos de distribuidores
Existem várias características importantes do processo PCI. No sistema de circuito fechado, o gás emitido pelo filtro é parcialmente recirculado para a entrada do pulverizador. Isso cria uma condição inerte que minimiza o teor de oxigênio no sistema e reduz as chances de explosão de pó de carvão.
O gás residual do fogão BF juntamente com o gás BF (em caso de necessidade) é utilizado como fonte de energia para a secagem do carvão reduzindo assim o consumo de energia primária. A umidade do carvão pode ser removida do sistema de forma muito eficaz sem o uso de um resfriador de gás ou um condensador. O uso de gás inerte durante a operação do tanque reservatório reduz o risco de incêndio e explosão.
O peso total do carvão injetado é controlado com precisão por um sistema de célula de carga que se ajusta continuamente para atender ao ponto de ajuste. Os arranjos paralelos dos tanques de alimentação garantem o fluxo contínuo do carvão para o BF. O sistema de distribuição de carvão é simples e eficaz, sem partes móveis.
A taxa de injeção é normalmente controlada pela modulação da posição de uma válvula dosadora montada na descarga dos tanques de alimentação. O sistema garante uma distribuição uniforme do carvão injetado entre o número total de ventaneiras e tem capacidade inerente de redistribuir automaticamente o total de carvão injetado no BF caso a injeção seja interrompida em uma ou mais ventaneiras por qualquer motivo.
O nitrogênio pressurizado é usado para injeção de carvão pulverizado do tanque de alimentação na tubulação de transporte. Com uma pequena quantidade de gás de transporte adicional, o carvão pulverizado é transportado e injetado no BF em condições de fase densa. Nessa condição, o carregamento de cerca de 40 kg a 50 kg de carvão por kg de gás é obtido na tubulação de transporte de carvão.
O carvão é transportado na tubulação a uma velocidade de apenas alguns metros por segundo. A baixa velocidade de transporte do carvão reduz o desgaste na tubulação aumentando assim sua vida útil. O sistema de transporte denso é poderoso e pode transportar o carvão pulverizado a longas distâncias.
A distribuição uniforme de carvão pulverizado para ventaneiras é muito importante. Para operar o BF com alta eficiência, a distribuição uniforme da carga e do fluxo de gás na direção circunferencial é essencial. Nesse sentido, a taxa de carvão pulverizado a ser injetado em cada ventaneira deve ser o mais uniforme possível. Alta precisão de distribuição de cerca de 1,5% é desejada (a precisão de distribuição normal do jato de ar quente é de cerca de 2,5%) que está sendo obtida usando um distribuidor (Fig 2). O esquema de injeção de carvão na ventaneira e na pista é mostrado na Fig 3.
Fig 3 Esquema de injeção de carvão pulverizado na ventaneira e na pista
Operação BF e PCI
Observou-se que em taxas de PCI, superiores a 140 kg/tHM, ocorrem mudanças na operação do BF. Algumas dessas mudanças incluem (i) redução na relação coque/minério, (ii) o tamanho da pista, (iii) redução da permeabilidade do coque ao redor da pista, (iv) mudanças na distribuição de temperatura na pista, (v ) degradação mecânica do coque na pista e (vi) diminuição da temperatura de homem morto. Todas essas mudanças são interdependentes e são influenciadas pelas propriedades e quantidade de carvão injetado, qualidade do coque e condições de explosão.
Permeabilidade – Os fluxos de gás, fluxos de líquido e descida de carga dentro do BF são dinâmicos, levando ao aparecimento e desaparecimento de zonas não ativas no bosh, deadman ou stack. Para alta produtividade e operação de BF estável com altas taxas de PCI, um requisito crítico é o fluxo de carvão consistente e as propriedades do carvão através de cada uma das ventaneiras. A qualidade consistente do carvão pode ser controlada pela mistura de carvões PCI e fluxo de carvão por controles individuais em cada ventaneira. As propriedades do carvão podem afetar os fluxos complexos de gás, líquido e sólido na zona inferior do BF (Fig. 4), mas esse impacto não é significativo se o fluxo estável e a qualidade do carvão forem alcançados. O carvão injetado pode influenciar a permeabilidade na zona inferior pelas seguintes razões.
- Combustibilidade que afeta a quantidade de material não queimado (carvão e fuligem) que sai da pista.
- A geração de finos de coque dentro da pista é devido à energia transmitida ao coque pelo impulso da explosão. A quantidade de finos gerados depende da qualidade do coque. O momento da explosão é influenciado pelo grau de combustão que ocorre dentro da ventaneira.
- A viscosidade da escória influencia o fluxo de escória e HM através da zona de homem morto e a penetração de gases quentes da pista na zona de homem morto, o que reduz ainda mais a viscosidade da escória dentro da zona de homem morto.
Mudanças operacionais podem ser feitas para tratar a permeabilidade reduzida em altas taxas de injeção. Por exemplo, o carregamento central de coque aumenta a permeabilidade do eixo BF e o aumento da profundidade da pista melhora a permeabilidade e reduz as perdas de carga de calor. Algumas das influências do PCI na operação do BF são mostradas na Figura 4.
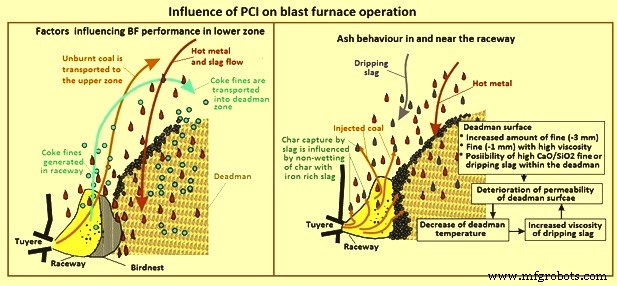
Fig 4 Influência do PCI na operação BF
Impacto do caractere não queimado – Em baixas taxas de PCI, os finos de coque gerados na pista são consumidos pela combustão, perda de solução e outras reações na zona inferior do BF. Com o aumento das taxas de PCI, observou-se que há um aumento no arraste de finos do topo do BF, bem como um aumento na profundidade física da pista e na instabilidade do BF. No entanto, o aumento do transporte de carbono é coque fino com algumas pequenas quantidades de fuligem e carvão não queimado insignificante. O carvão não queimado pode ser benéfico, pois na presença de carvão a resistência ao desgaste do coque é aumentada. Este comportamento parece estar limitado ao coque de baixa reatividade e alta resistência.
Combustibilidade do carvão – Observa-se que a combustibilidade do carvão injetado ao nível da ventaneira diminui com o aumento da taxa de injeção ou diminuição da matéria volátil do carvão. No entanto, a combustibilidade do carvão a 700 mm acima da ventaneira é superior a 95% para todos os carvões devido à reação de perda de solução do carvão não queimado. O carvão não queimado não consumido pela reação de perda de solução fica preso no BF ou sai como poeira. Estimou-se que a taxa de injeção máxima que pode ser obtida é de 230 kg/tHM com uma eficiência de combustão de 75%.
A intensa condição de combustão dentro da ventaneira e da pista leva a uma maior liberação de voláteis. Ao avaliar as características de carvões de baixa volatilidade, verificou-se que a proporção de voláteis liberados para a matéria volátil próxima (VM) do carvão aumentou significativamente com a classificação (conteúdo de carbono) do carvão em altas taxas de aquecimento. Há uma clara evidência da fragmentação de partículas em chamas. O fluxo de carvão não queimado da pista tem impacto na permeabilidade da zona inferior e da zona de homem morto do BF.
A fragmentação da partícula de carvão pode ocorrer durante a desvolatilização (fragmentação primária) e durante a combustão do carvão (fragmentação secundária). A fragmentação primária é influenciada pela VM do carvão. Grandes partículas de carvão produzem muito mais partículas de cinzas volantes do que pequenas partículas de carvão. A classificação de carvão também tem uma grande influência. A extensão da fragmentação tende a aumentar com o aumento do teor de carvão e tende a diminuir com o aumento do carregamento de cinzas.
No BF, a taxa de aquecimento rápida, altas temperaturas, oxigênio enriquecido e geralmente carvões de classificação mais alta usados para PCI, todos contribuem para a fragmentação primária dentro de uma ventaneira. Sob essas condições, a superfície externa de uma partícula pode endurecer devido à reação com oxigênio ou recozimento térmico antes da desvolatilização completa do núcleo interno da partícula. Isso leva à fragmentação explosiva da partícula.
A reatividade do carvão aumenta com o teor de VM do carvão devido a mudanças na morfologia do carvão, no entanto, nas temperaturas elevadas relacionadas à combustão do carvão na pista, a reatividade química tem muito pouco significado, pois as taxas de combustão são limitadas pela taxa de difusão do oxigênio para a partícula e os tempos de queima dependem mais do tamanho da partícula e da concentração de oxigênio. O alto teor de cinzas no carvão influencia negativamente o comportamento da combustão. A combustibilidade do carvão de baixa tensão pode ser aumentada pela mistura com um carvão de alta tensão, pois o carvão de alta tensão diminui o tempo de ignição e aumenta a temperatura dentro da ventaneira.
A composição das cinzas do carvão não queimado pode influenciar o efeito catalítico da reação de perda de cinzas para solução. Dependendo de sua composição, a cinza também pode retardar a conversão de carbono devido ao bloqueio dos poros do carvão como consequência do aumento da proporção de formação de escória nas partículas de carvão. Embora grande parte do carvão seja consumido por reações no forno devido à reatividade significativamente maior do carvão em comparação com a do coque, normalmente acredita-se que o carvão não queimado desempenha um papel significativo na desativação do homem morto, reduzindo a permeabilidade do carvão. deadman ao fluxo de gás e líquido. Considera-se que a redução da permeabilidade aumenta com o aumento da taxa de injeção à medida que a combustibilidade do carvão diminui devido à diminuição da relação de excesso de ar. Parte do carvão não queimado pode ser capturado pela escória gotejante, embora a quantidade desse carvão capturado seja influenciada pelo comportamento não molhante do carvão com escórias ricas em ferro.
A fragmentação do carvão/carvão e a combustão sendo controlada por difusão são as principais razões pelas quais o VM tem pouco efeito sobre a combustibilidade dos carvões PCI.
Deposição de char não queimado no BF – A deposição de finos de carvão e coque não queimados nas zonas mais baixas do Bf é um fenômeno complexo que consiste em vários mecanismos de geração, como reação, fluxo multifásico, acumulação e reentrada. Foi demonstrado tanto por medição dentro de um BF quanto numericamente que a forma e o tamanho da pista mudam dinamicamente com o acúmulo e re-arrastamento de pó na zona inferior. Essas mudanças têm aproximadamente dois períodos, o menor período são as flutuações usuais dentro da pista e o maior período corresponde à grande mudança com vazão devido ao acúmulo de pó. É a grande mudança no fluxo de gás que pode levar a altas velocidades de gás perto da parede do BF, resultando em maior perda de calor e desgaste das paredes do BF.
O acúmulo de pó em um leito compactado foi examinado experimentalmente e numericamente. O trabalho experimental em leito empacotado bidimensional utilizando partículas de 3 mm e pó de 0,075 mm mostrou a influência da carga de pó e da velocidade superficial do gás no acúmulo de pó em uma região correspondente ao piso e ninho da pista. A influência de diferentes formas de zonas coesivas no acúmulo de partículas também foi demonstrada experimentalmente. A análise numérica é capaz de mostrar muito do mesmo comportamento de acumulação que os dados do teste experimental. Esta análise numérica também mostrou a influência significativa do tamanho do pó no acúmulo de pó na zona de homem morto.
A análise numérica da influência do pó fino (carvão não queimado e coque fino) que foi conduzida mostrou que o carvão não queimado e o coque fino com diferentes diâmetros e densidades têm diferentes padrões de fluxo, áreas de acumulação e zonas de reação. A densidade do pó gerado tem um efeito significativo no padrão de fluxo do pó, especialmente para as partículas maiores. À medida que as partículas de pó se tornam maiores que 1 mm, sua tendência é assentar do gás que flui para cima e descer para o homem morto, deteriorando sua permeabilidade. Qualquer carvão não queimado é preferencialmente transportado com o fluxo de gás para a região superior do BF onde reage com o gotejamento de HM e/ou gás. Existem alguns indícios da existência de um ninho de pássaro com um teor muito elevado de finos. A quantidade de multas depende da qualidade do coque e dos níveis de PCI. Os finos de coque grandes e mais pesados tendem a deixar a corrente de gás e se acumulam na zona de homem morto, tendo um efeito adverso de menor permeabilidade da zona.
A recente análise numérica e amostra física confirmaram que a quantidade de carvão não queimado acumulado na zona de deadman é relativamente pequena e não aumenta com o aumento da taxa de PCI. Assim, o carvão não queimado tem pouca influência na parte inferior do forno e no aumento da resistência à permeabilidade. É mais provável que a deposição de coque fino tenha uma influência mais significativa na permeabilidade do BF do que o carvão não queimado.
Influência das propriedades do coque – Afirma-se frequentemente que a necessidade de sínter e coque de alta qualidade são essenciais para alcançar altas taxas de PCI e manter alta produtividade. É muito importante melhorar a permeabilidade geral do BF para alcançar alta produtividade com altas taxas de PCI. Normalmente, os BFs com altas operações de PCI usam coque de alta resistência (em termos de índice de tambor) e sinter de baixo SiO2 e baixo AL2O3 com excelentes propriedades de redução de alta temperatura. Vários BFs asiáticos estão alcançando altas produtividades com taxas de PCI superiores a 200 kg/tHM usando matérias-primas de alta qualidade.
Com base na experiência industrial, verificou-se que o tamanho do coque bosh aumenta com a resistência a frio (I40), aumenta com a resistência a quente (CSR), aumenta com o tamanho do coque grosso e diminui com a taxa de PCI. Os resultados do raking de tuyere em 'Corus Ijmuiden BF' mostraram que um ponto I40 resulta em 1,5% a mais de coque bosh acima de 40 mm quadrados. Verificou-se que não há relação entre a taxa de injeção de carvão e a quantidade de coque fino no nível da ventaneira. Os dados para injeção e I40 sugerem que há degradação máxima do coque em torno da taxa PCI de 120 kg/tHM.
Um estudo que examinou o comportamento do coque na zona inferior do BF sob altas taxas de PCI descobriu que o carvão é consumido preferencialmente. Isso diminui a concentração de CO2 ao redor da partícula de coque e expande a camada de reação do coque ao redor da superfície e para o interior da partícula. Na presença de carvão injetado, a resistência ao desgaste do coque aumentou e o volume total de poros no coque aumentou. Esta maior resistência à abrasão com maiores taxas de PCI pode ser a razão para o aumento do tamanho do coque bosh em altas taxas de PCI.
A análise de amostras de coque coletadas no nível da ventaneira mostrou que, em altas taxas de PCI, as propriedades de alta temperatura (CSR e CRI) têm um efeito positivo maior na permeabilidade do que as propriedades de resistência ao frio. Parece que a permeabilidade não melhora após um valor de CSR de cerca de 65% a 70%.
Em um estudo com os dados de vários BFs com taxas de PCI acima de 170 kg/tHM, os BFs apresentam índice de coração (HI =CRI – 2,5 x CSR + 100 %) acima de 97 %, embora nenhuma relação clara entre HI e taxa de injeção tenha foi encontrado. Também foi observado que a produtividade aumenta com o HI. Também foi sugerido que em altas taxas de PCI o coque resiste à abrasão (baixo I10) e tem alto CSR.
Em um estudo que examinou a influência da qualidade do coque na produtividade do BF, foi desenvolvido um índice global de qualidade do coque. Este índice dá uma indicação da variação de calor na parte inferior do BF e, portanto, uma ideia da permeabilidade da fornalha e do fuste do BF. Este índice global de qualidade de coque foi definido pela equação Iglobal.coke =0,5 x [(I40 – 3,42 x I10 + 100) + (CSR – 2,6 x CRI + 100)]. A variação na variação de calor no fundo do BF pode ser explicada pela variação no Iglobal.coke. Este índice está sendo utilizado em algumas usinas para determinar a estratégia operacional dos BFs, se Iglobal.coke for baixo a taxa de injeção de carvão e a produção diminuir. Considerou-se que a adição de carvão não queimado aos finos de coque existentes leva a uma menor permeabilidade na zona de homem morto, resultando em estabilidade reduzida do leito de coque.
No entanto, a permeabilidade diminui com o aumento do teor de VM e a faixa de tamanho mais fina do carvão pulverizado. Uma explicação para isso é que à medida que a combustibilidade do carvão é aumentada (aumento do teor de voláteis e/ou moagem mais fina), há maior combustão dentro da ventaneira dando um maior volume de gases sendo injetados na canaleta, levando a um maior momento de explosão. Este maior momento de explosão causa o aumento da profundidade da pista e aumento da degradação do coque da pista, o que leva ao aumento do arraste de finos de coque.
Em um estudo examinando a influência da energia da explosão na formação da pista, foi observada uma relação linear entre a energia da explosão e a profundidade da pista. Um modelo bidimensional da pista mostra a relação linear entre a velocidade de explosão e a profundidade da pista para tamanho de coque constante e dimensões de BF. O aumento da instabilidade do homem morto e degradação do coque devido ao aumento do momento da explosão foi modelado por outros estudos. Esses modelos mostram que a profundidade da pista aumenta linearmente com a velocidade de explosão para uma força de coque constante.
Usando os dados de vários estudos, estima-se a variação do momento da explosão com o teor de carbono do carvão injetado. Isso é capaz de mostrar como a classificação do carvão injetado influencia na geração de finos de coque. Um carvão de alto VM típico produz até duas vezes mais finos de coque que um carvão de baixo VM PCI devido ao aumento do momento de explosão resultante da combustão dos voláteis dentro da ventaneira. Os dados operacionais mostram que, com taxas de injeção em torno de 170 kg/tHM, a permeabilidade e a produtividade aumentam quando a profundidade da pista é aumentada (maior momento de explosão). A expansão da pista reduz a área de homem morto e, portanto, aumenta a área onde o HM e a escória podem descer e onde o fluxo de gás pode subir.
Na Europa, a resistência do coque a frio e no Japão, a resistência do coque a quente é usada como parâmetro do coque para monitorar a qualidade do coque por muitas usinas que operam com altas taxas de PCI. Há evidências de que a resistência do coque por si só não é suficiente para prever a degradação do coque devido a mecanismos físicos e químicos.
Influência da química das cinzas de carvão na viscosidade da escória – The viscosity of the slag can influence the BF productivity since the productivity is related to the flooding phenomenon which can occur in the lower zone of the BF. The slag viscosity can adversely influence the permeability and the liquid flooding factor. Tuyere samples from a Japanese BF has given a valuable insight into the influence of the ash from injected coal on the physical properties of the dripping slag and the permeability of the region surrounding the raceway for a high productivity and operations with high PCI rates.
In recent years, there have been several studies into to the prediction of slag viscosities due to its importance to the flow behaviour of slag in the BFs. In one of the study, a quasi-chemical viscosity model has been developed for fully liquid slags in the Al2O2-CaO-FeO-MgO-SiO2 system, which has shown good agreement between experimental data and predictions over the whole compositional range. The composition of the slag influences the liquidus temperature in SiO2-CaO-MgO-Al2O3 systems. A slag critical temperature at which the viscosity of the slag abruptly changes has been described. At a basicity of less than 1.3, the critical temperature is around 1340 deg C and at a basicity of over 1.3, the critical temperature is around 1380 deg C. Lowering the MgO content of the slag decreases the slag viscosity but the temperature of the slag is the major factor.
A laboratory study has shown that mixing of pulverized fluxes with ash from coke and coal reduces the melting point of the tuyere slag by more than 200 deg C. At the same time slag viscosity is highly improved. In another study the reactions at the interface of unburnt char and iron have been examined. It has been found that the dissolution of carbon into the liquid iron is influenced more by the chemistry of the ash layer that formed at the interface than other factors. An increase in silica content slows the carbon dissolution. Silicon vaporization can occur in some coals. Further, it has been shown that the formation of ferritic iron at the surface can also slow the carbon dissolution.
The alkalis from coke or PCI which are of the most interest to BF operators are Na2O and K2O. Within the BF there is a re-circulation of the alkalis as the alkali vapours produced in the lower section of the furnace are condensed in the upper region of the furnace. High alkali load can lead to the formations of scabs (skulls) on the BF wall leading to BF irregularities like hanging and slipping. The chlorine content of the injected coal can increase the recirculation of alkalis within the BF. The level of re-circulating load can be controlled by adjusting slag volume and the chemistry.
The results of a study into the influence of alkalis in BFs indicate that decreased slag basicity, decreased hearth temperature, increased top gas temperatures, use of low alkali-burden are important factors in the control of alkalis in the BF. The most effective control is to limit alkali input to 2.0 kg/tHM to 2.5 kg/tHM. The main interaction of alkalis with coke occurs as the coke passes through the re-circulating zone becoming enriched in alkalis. This weakens the coke and makes it more susceptible to breakage. The extent of this effect probably depends on the type of carbon texture. The coke loses its alkalis as it proceeds down the furnace through the high temperature zone near the raceway.
With PCI the alkalis from the injected coal evaporate in the raceway and then due to the temperature drop condense in the deadman zone. The peak values of alkalis contents are around 2 m from the tuyere nose. The build-up of alkalis within deadman zone can lead to permeability problems associated with the HM flow to the hearth. In one of the studies on the effect of chlorine and alkali on BF operation, it has been found that a reduction of chlorine and alkali inputs improved BF permeability.
Processo de manufatura
- Geração e uso de gás de alto-forno
- Uso de Nut Coke em um Alto Forno
- Irregularidades do alto-forno durante a operação
- Sistema de resfriamento do alto-forno
- Sistemas de carregamento de alto-forno
- Química da Ferragem por Processo de Alto Forno
- Revestimento refratário do alto-forno
- Injeção de gás de forno de coque em um alto-forno
- Fatores que afetam a taxa de coque em um alto-forno
- Alto-forno e seu projeto