Transferência de calor durante o lingotamento contínuo de aço
Transferência de calor durante a fundição contínua de aço
Durante o lingotamento contínuo (CC) do aço, o controle cuidadoso do resfriamento do cordão e do crescimento da casca ao longo da máquina CC é de grande importância. Esses fatores desempenham um papel importante na formação de trincas e outros defeitos que podem ser formados no produto de aço fundido. Para garantir produtos de aço fundido sem defeitos, o cordão deve ser resfriado de acordo com um padrão que depende do tipo de aço, dimensões do produto de aço, velocidade de fundição e projeto da máquina CC. Por outro lado, o controle do comprimento da poça de líquido é um elemento chave para otimizar a velocidade de lingotamento com relação a uma boa produtividade. Assim, a transferência de calor desempenha um papel muito importante na operação das máquinas CC, especialmente na fundição de aços sensíveis a trincas. De fato, muitos fenômenos diversos controlam simultaneamente a complexa sequência de eventos que governam a transferência de calor no processo CC.
A temperatura do aço líquido no distribuidor é tipicamente 30°C a 50°C mais alta que a temperatura liquidus. No início do processo de lingotamento contínuo, o aço líquido é resfriado em um molde resfriado a água para formar uma casca solidificada que pode suportar a poça de líquido na saída do molde. A temperatura típica no final do molde é de 1100°C e a do centro do cordão é de 1550°C. Como o aço não solidifica a uma temperatura fixa, mas em uma faixa de temperatura, há uma região pastosa onde o aço é nem completamente sólido nem completamente líquido. Os graus de aço usados no lingotamento contínuo são completamente sólidos abaixo de uma temperatura que varia de 1350 graus C a 1500 graus C, e a solidificação começa a uma temperatura que varia de 1450 graus C a 1525 graus C. Isso depende fortemente do conteúdo dos elementos de liga em o aço.
A transferência de calor no produto de aço CC em solidificação ocorre de forma complexa, uma vez que o calor a ser extraído é proveniente de mudanças de entalpia no fio de aço, tanto por diminuições de temperatura quanto por mudanças de fase. O primeiro é referido como mudança de calor sensível e o último como calor latente. Além disso, as mudanças de fase envolvem não apenas as mudanças entre as fases sólidas, mas também as condições produzidas pela solidificação de uma liga. Por exemplo, existe uma zona pastosa entre as temperaturas liquidus e solidus que dependem do teor de carbono do aço. Além disso, a resistência térmica aumenta à medida que a espessura da casca do aço aumenta do menisco até o fundo do molde. A transferência de calor nesta região é por condução.
A solidificação do aço no processo de lingotamento contínuo começa no molde, segue nas zonas secundárias de resfriamento e termina sob condições de resfriamento ao ar. A tecnologia de fundição requer uma transferência de calor muito eficaz da superfície do cordão para os sistemas de resfriamento a água.
A ocorrência de transferência de calor durante os estágios de resfriamento primário (aço líquido para molde), secundário (zonas de pulverização) e terciário (radiação livre) é o principal fenômeno relacionado ao lingotamento contínuo de aço líquido. Tanto a previsão do comportamento térmico quanto a determinação de tais sistemas de transferência de calor são importantes, pois influenciam diretamente na solidificação, principalmente durante a fase inicial de formação da casca sólida no interior do molde.
O resfriamento e a solidificação no lingotamento contínuo ocorrem principalmente nas seções de molde e resfriamento secundário. O resfriamento que ocorre no molde deve ser suficiente para resfriar o aço líquido até o ponto em que se forme uma camada sólida na superfície com espessura suficiente para suportar mecanicamente a poça de aço líquido dentro do invólucro de aço ao sair do molde. O processo de resfriamento secundário, por outro lado, deve ser suficiente para completar o processo de solidificação iniciado no molde. A velocidade de resfriamento também é um parâmetro crítico por outras razões, uma vez que uma taxa de resfriamento excessivamente grande tende a produzir rachaduras na zona de flexão do produto de aço fundido e uma taxa de resfriamento excessivamente lenta resulta em uma poça de líquido excessivamente longa.
Os processos que influenciam a transferência de calor no processo CC do aço líquido são condução e convecção na área do aço líquido, condução na casca solidificada, transporte de calor entre a camada externa da casca solidificada e a superfície da parede do molde, condução de calor na o molde, transferência de calor no molde entre as paredes do canal e a água de resfriamento, transferência de calor dentro da zona de resfriamento secundária por convecção e radiação, transferência de calor entre o cordão de solidificação e os rolos por condução. Além disso, os efeitos térmicos relacionados às transformações de fase que acompanham a solidificação têm uma influência significativa na transferência de calor.
O controle da transferência de calor no molde e nas zonas de resfriamento secundário desempenha um papel essencial na solidificação do aço líquido. A troca de calor limita a velocidade de fundição e influencia essencialmente a formação da casca sólida.
Transferência de calor no molde CC
A transferência de calor no molde CC é crítica e é governada por muitos fenômenos complexos. A modelagem matemática e computacional é normalmente utilizada no desenvolvimento de uma maior compreensão das condições térmicas do molde e para auxiliar no projeto adequado e nas práticas operacionais. A transferência de calor transversal predominante pode ser considerada como um fluxo de energia térmica através de uma série de resistências térmicas, desde a fonte de alta temperatura do núcleo de aço líquido no molde até o sumidouro de água de resfriamento do sistema de resfriamento do molde. As resistências térmicas de transferência de calor são dadas abaixo.
- Transferência de calor através da casca de solidificação
- Transferência de calor da superfície do invólucro de aço (pele) para a superfície interna do revestimento de cobre
- Transferência de calor através do molde de cobre
- Transferência de calor da superfície externa do revestimento de cobre para a água de resfriamento do molde
Na região do molde, a transferência de calor é controlada pelo seguinte. (Figura 1)
- Convecção de superaquecimento líquido para a superfície da casca
- Solidificação (evolução de calor latente na zona pastosa)
- Condução através da casca sólida
- O tamanho e as propriedades da interface entre o shell e o molde
- Condução através do molde de cobre
- Convecção para a água de resfriamento do molde
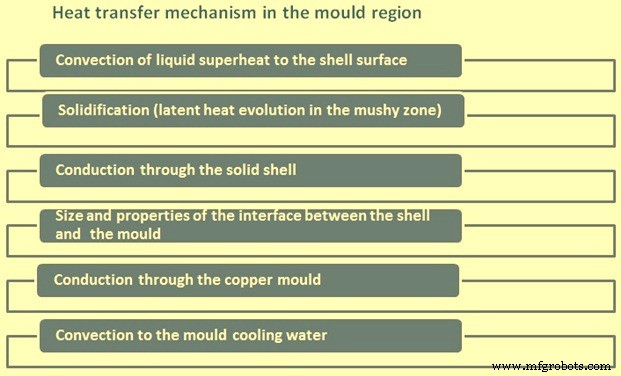
Fig 1 Mecanismo de transferência de calor na região do molde
A transferência de calor da superfície do invólucro de aço para a superfície interna do revestimento de cobre é a mais complexa e é a etapa de controle no molde. Envolve principalmente dois mecanismos de transferência de calor:(i) condução e (ii) radiação. A característica saliente desta etapa de transferência de calor é o encolhimento do aço solidificado (que é uma função do grau do aço e das condições de operação da máquina CC), e a tendência resultante para a formação de um espaço de ar entre o invólucro de aço e a superfície do molde.
A formação do entreferro é complexa e pode variar tanto na direção transversal quanto na longitudinal. Assim, tem um efeito variável no mecanismo de transferência de calor, bem como na magnitude do fluxo de calor. Por exemplo, à medida que o entreferro é formado, a transferência de calor ocorre principalmente da condução para a radiação com uma diminuição resultante no fluxo de calor. Em geral, esta etapa de transferência de calor representa a maior resistência térmica de todas as quatro etapas, principalmente no que diz respeito à transferência de calor através do revestimento de cobre e deste último para a água de resfriamento do molde.
Todo o padrão de remoção de calor no molde é dependente da dinâmica da formação de fendas. Em geral, a largura da fenda tende a aumentar com o aumento da distância do menisco à medida que a casca de aço se solidifica e se afasta da superfície do molde. Além disso, à medida que a espessura da casca aumenta com a distância do menisco, ela tende a resistir ao efeito de abaulamento oposto da pressão ferrostática para reduzir a folga.
Depois que o aço próximo à superfície do molde foi resfriado abaixo da temperatura solidus, o desenvolvimento da folga começa. A determinação do tamanho real da folga é difícil devido a três fatores, a saber (i) o movimento oscilante do molde, (ii) o movimento do produto de aço fundido no molde relacionado à velocidade de fundição e (iii) o movimento aleatório do produto de aço fundido no plano que é perpendicular à direção de fundição. A presença de pó de molde junto com gases na abertura é o fator adicional, o que torna a transferência de calor mais complexa. Como resultado, a resistência térmica no intervalo é difícil de ser determinada com precisão. Depois de sair do molde, a superfície da laje é resfriada com spray de água e ao ar. O fluxo de calor que é então levado da superfície do cordão de resfriamento é proporcional à diferença de temperatura da superfície do cordão e à temperatura do meio de resfriamento. A área de transferência de calor no molde pode ser dividida em três zonas (i) a zona de contato direto do aço líquido com as paredes do molde, (ii) a zona intermediária onde aparece uma camada de aço solidificado e (iii) a zona com o entreferro em desenvolvimento. O desenvolvimento do entreferro causa um gradiente de temperatura muito alto entre a casca do cordão solidificado e a parede do molde. A mudança nos parâmetros do gap tem uma influência significativa no curso do processo de cristalização e constitui uma fonte potencial de distúrbios para o curso estável do processo de fundição. Portanto, para a avaliação da estabilidade do sistema considerado é vital conhecer a influência da geometria da folga no funcionamento térmico do molde.
A transferência de calor na superfície interna do cobre é ainda mais complicada pelos efeitos da lubrificação do molde. Outro fator que influencia a transferência de calor nesta superfície do molde é a conicidade do molde, que tende a aumentar a transferência de calor porque se opõe ao efeito da formação de fendas.
Em geral, o fluxo de calor local ao longo do comprimento do molde atinge um valor máximo ou logo abaixo do menisco de aço líquido e diminui ao longo do comprimento do molde. O fluxo de calor médio para todo o molde aumenta com o aumento da velocidade de fundição.
A transferência de calor através do revestimento de cobre é por condução. Depende da condutividade térmica do cobre e de sua espessura; quanto maior a espessura, maior a temperatura da face quente do revestimento de cobre. A transferência de calor da superfície externa do revestimento de cobre para a água de resfriamento do molde é realizada por convecção forçada. Embora a temperatura geral da água de resfriamento, tipicamente cerca de 40°C, esteja geralmente abaixo de sua temperatura de saturação a uma determinada pressão da água, a ebulição ainda é possível em regiões locais na superfície externa do molde se a temperatura local dessa superfície for suficientemente alta para bolhas de vapor de água se nucleam na superfície, passam para a água de resfriamento a granel mais fria e se condensam. Este efeito aumenta a transferência de calor. A ebulição de nucleotídeos pode resultar em ciclos do campo de temperatura através do molde de cobre (tanto na face fria quanto na face quente) e pode resultar na deterioração da qualidade do produto de aço fundido. A ebulição pode ser suprimida aumentando a velocidade da água no sistema de refrigeração ou aumentando a pressão da água. A ebulição incipiente é mais provável em moldes de tarugos, que têm temperaturas de face fria mais altas do que os moldes de placas por causa de suas espessuras de parede mais finas. Os valores típicos para a temperatura da face fria estão na faixa de 150°C para os moldes de tarugos e 100°C para os moldes de placas.
O controle da transferência de calor no molde é realizado por um sistema de água de resfriamento por convecção forçada, que normalmente é projetado para acomodar as altas taxas de transferência de calor resultantes do processo de solidificação. Em geral, a água de resfriamento entra no fundo do molde, passa verticalmente através de uma série de canais de água paralelos localizados entre a parede externa do molde e uma camisa de contenção de aço e sai na parte superior do molde. Os parâmetros de controle primários são os seguintes.
- O volume de água na temperatura, pressão e qualidade da água necessária.
- A velocidade do fluxo de água uniformemente através das passagens ao redor do perímetro do revestimento do molde.
Normalmente, é empregado um sistema de circuito fechado de recirculação pressurizado. A taxa de fluxo de água deve ser suficiente para absorver o calor do fio sem um aumento excessivo na temperatura da água em massa. Um grande aumento na temperatura pode resultar em uma diminuição na eficácia da transferência de calor e temperaturas mais altas do molde. Por esta mesma razão, a temperatura da água de entrada no molde também não deve ser excessiva. Também é necessária uma pressão de água do molde adequada. Pressões de água mais altas tendem a suprimir a ebulição, mas pressões excessivamente altas podem causar deformação mecânica do molde.
A qualidade da água é um fator importante no que diz respeito à deposição de incrustações no revestimento do molde. A deposição de incrustações pode ser um problema sério porque causa uma resistência térmica adicional na interface da água de resfriamento do molde que aumenta a temperatura da parede do molde levando a efeitos adversos como geração de vapor e redução na resistência do revestimento de cobre. O tipo e a quantidade de incrustação formada dependem principalmente da temperatura e velocidade da água de resfriamento, da temperatura da face fria do molde e do tipo de tratamento da água.
Para atingir a velocidade de fluxo adequada, o sistema de resfriamento é projetado de modo que a velocidade seja alta o suficiente para produzir um coeficiente de transferência de calor efetivo na interface da água de resfriamento do molde. Uma velocidade de fluxo muito baixa produz uma maior resistência térmica nesta interface, o que pode levar à ebulição e seus efeitos adversos. Em geral, quanto maior a velocidade da água de resfriamento, menor é a temperatura do molde. O sistema de resfriamento também deve ser projetado para manter a distribuição de velocidade de fluxo necessária uniformemente ao redor do molde e maximizar a área das faces que são refrigeradas diretamente a água. A distribuição uniforme do fluxo pode ser alcançada pelo desenho geométrico adequado das passagens de água com o uso de coletores e placas de fardos.
O monitoramento dos parâmetros operacionais do sistema de resfriamento do molde permite uma avaliação do processo de fundição. Por exemplo, com uma vazão de água de resfriamento constante, o calor removido de uma face do molde está diretamente relacionado à diferença entre a temperatura da água de entrada e saída (delta T). Assim, um delta T excessivamente grande indica uma taxa de fluxo anormalmente baixa para uma ou mais faces do molde, enquanto um delta T excessivamente pequeno indica um acúmulo de escala anormalmente grande para uma ou mais faces do molde. Um delta T desigual para faces opostas resulta de um fluxo de vazamento assimétrico, distorção do molde ou desalinhamento do cordão.
Transferência de calor na seção de resfriamento secundária da máquina CC
Abaixo do molde, a transferência de calor ocorre pelo contato direto da carcaça de aço com o meio de resfriamento, água ou mistura água-ar dos bicos de pulverização. O resfriamento nesta seção é frequentemente referido como resfriamento secundário. Nesta seção de resfriamento secundário, o calor é extraído devido à alta pressão dos jatos de água atomizada de ar, radiação e contato com os rolos de apoio e guia. Nesta zona, a transferência de calor é caracterizada pelo coeficiente de transferência de calor combinado. Aqui, o calor é transferido em todos os três modos de transferência (condução, convecção e radiação). Mas também os rolos e especialmente os rolos de suporte resfriados internamente dissipam muito calor do fio.
Na área de resfriamento secundário, o fluxo de calor removido da superfície do aço fundido pode ser expresso por
q =K (Ts – Tw) + qR
Onde q é o fluxo total de calor, K é o coeficiente de transferência de calor, Ts é a temperatura da superfície, Tw é a temperatura da água de resfriamento e qR é o fluxo de calor por radiação.
A principal variável que influencia o resfriamento secundário é a temperatura da superfície. O termo teórico "temperatura Leidenfrost" tem um impacto muito prático na operação e no design da máquina CC. A eficiência do resfriamento por pulverização depende fortemente da temperatura da superfície. Camada de vapor estável pode ser formada na superfície resfriada. A camada de vapor estável protege a superfície do contato direto com o refrigerante e o resfriamento é de baixa intensidade. A estabilidade da camada de vapor é acoplada à temperatura da superfície. Quando a temperatura diminui e a camada de vapor colapsa, o resfriamento cresce instantaneamente.
A temperatura real da superfície e a 'temperatura Leidenfrost' para as condições relevantes de fundição e resfriamento secundário podem alterar significativamente a intensidade do resfriamento. A temperatura Leidenfrost é um termo teórico, que tem um impacto muito prático no lingotamento contínuo. Não existe nenhum método teórico para prever a temperatura Leidenfrost. Só pode ser obtido por medição.
A intensidade de resfriamento pode ser dez vezes maior na região de baixa temperatura em comparação com a intensidade na região de alta temperatura. A fronteira entre essas duas áreas de temperatura é a temperatura Leidenfrost.
As principais funções de transferência de calor do sistema de spray de água são fornecer o seguinte.
- A quantidade adequada de água para obter a solidificação completa sob as restrições da operação CC, ou seja, grau de aço, velocidade de fundição, etc.
- A capacidade de regular as condições térmicas do cordão desde abaixo do molde até a operação de corte, ou seja, temperatura da superfície do cordão e gradientes térmicos no cordão
- Funções auxiliares, como resfriamento dos rolos de contenção.
É necessário controlar tanto os níveis de temperatura quanto os gradientes térmicos no cordão para evitar a ocorrência de defeitos superficiais e internos, como forma inadequada e trincas. Em alta temperatura, as propriedades de resistência da casca de aço desempenham um papel crítico na capacidade da casca de suportar as forças externas e internas impostas pela operação do CC. As forças primárias são aquelas exercidas pela pressão ferrostática do núcleo líquido e pela tração da operação de retirada. Em particular, a ductilidade do aço próximo à temperatura solidus é baixa e a casca é suscetível à formação de trincas. É importante controlar os gradientes de temperatura porque podem ser causadas deformações térmicas que excedem a resistência do aço, resultando em trincas. Deformações térmicas excessivas resultam de mudanças na taxa de extração de calor tanto por super-resfriamento quanto por sub-resfriamento. As últimas condições ocorrem devido ao reaquecimento, que é causado quando o resfriamento por spray é encerrado de forma inadequada e o cordão reaquece por transferência de calor do interior com um aumento de temperatura antes de decair por transferência de calor por radiação para o ambiente. Sob essas condições, podem ocorrer tensões e rachaduras excessivas. Este efeito pode ser reduzido estendendo e variando a operação de resfriamento por spray de água para proporcionar uma transição suave com a área de resfriamento por radiação.
Assim, no projeto de um sistema de resfriamento secundário, as condições térmicas ao longo do cordão devem ser estabelecidas que satisfaçam a integridade e a qualidade do produto. Por exemplo, as temperaturas da superfície ao longo do cordão são especificadas. Eles geralmente estão na faixa de 700°C a 1200°C. Com base nesta informação, as taxas de resfriamento ao longo do cordão são determinadas a partir de equações de transferência de calor. Parâmetros importantes nesses cálculos incluem o coeficiente de transferência de calor por convecção dos jatos de água e o fluxo de água (a quantidade de água por unidade de área de contato da superfície). O tipo de bico de pulverização, a posição do bico em relação à superfície do fio, o número de bicos e a pressão da água são selecionados para fornecer o fluxo de água necessário e a distribuição em todo o setor de resfriamento secundário. Múltiplos bicos são normalmente usados em cada nível ao longo do cordão que tem um padrão de sobreposição.
Geralmente, uma série de zonas de resfriamento é estabelecida ao longo do cordão, cada uma com as mesmas configurações de bocal e características de transferência de calor. Como as taxas de resfriamento necessárias diminuem ao longo do comprimento do cordão, seu fluxo de água em zonas sucessivas diminui.
Durante a operação, as mudanças no fluxo de água são feitas para compensar as mudanças nas condições de fundição, como velocidade de fundição, temperatura da superfície do cordão, temperatura da água de resfriamento e grau do aço.
Três formas básicas de transferência de calor, ou seja, radiação, condução e convecção ocorrem na região de resfriamento secundária.
A radiação é a forma predominante de transferência de calor nas regiões superiores da câmara de resfriamento secundária e é descrita pela equação a seguir.
Q =KEA (Ts? -Ta?) (os valores de Ts e Ta estão na potência 4)
Onde K é a constante de Stefan-Boltzmann bem estabelecida, E é a constante de emissividade (tipicamente 0,8), A é a área da superfície e Ts e Ta são a superfície do aço e as temperaturas ambiente, respectivamente.
À medida que o produto passa pelos rolos, o calor é transferido através da casca por condução e também pela espessura dos rolos, como resultado do contato associado. Esta forma de transferência de calor é descrita pela lei de Fourier.
Q=kA (Ti-To)/delta X
Para a transferência de calor por condução através da casca de aço, k é a condutividade térmica da casca, enquanto A e delta X são a área da seção transversal e a espessura da casca de aço, respectivamente, através da qual o calor é transferido. Ti e To são as temperaturas da superfície interna e externa da casca, respectivamente. Essa forma de transferência de calor também ocorre através dos rolos de contenção.
A convecção é o mecanismo de transferência de calor que ocorre movendo rapidamente gotículas de água pulverizada ou névoa dos bicos de pulverização, penetrando na camada de vapor próxima à superfície do aço, que então evapora. Este mecanismo convectivo é descrito matematicamente pela lei de resfriamento de Newton pela seguinte equação.
q=hA (Ts-Tw)
onde o coeficiente de transferência de calor 'h' (uma constante) é determinado experimentalmente para fluxos de água selecionados, tipos de bicos, pressão da água de pulverização (e pressão do ar se for utilizada névoa de ar) e, finalmente, temperaturas da superfície do aço. A é a área da superfície. Ts e Tw são as temperaturas da superfície do aço e da água de pulverização, respectivamente.
Especificamente, a transferência de calor de resfriamento secundário atende às seguintes funções.
- Aprimore e controle a taxa de solidificação e, para alguns rodízios, atinja a solidificação total nesta região
- Regulação da temperatura do cordão através do ajuste da intensidade da água de pulverização
- Resfriamento de contenção de máquina CC
O papel do sistema de resfriamento secundário é controlar o estado térmico do cordão desde a saída do molde até sua completa solidificação. Para garantir produtos de aço CC livres de defeitos, o cordão deve ser resfriado de acordo com um padrão que depende da classe do aço, tamanho do cordão, velocidade de fundição e projeto da máquina CC. Normalmente, grandes flutuações de temperatura devem ser evitadas, bem como altas taxas de resfriamento ou reaquecimento. O reaquecimento da superfície leva a tensões térmicas na área próxima à frente de solidificação, e isso pode levar, dependendo da quantidade de reaquecimento e do grau do aço, a trincas na face média ou trincas a quente em geral. Também é importante que a temperatura da superfície do cordão na área de dobra ou endireitamento esteja fora da faixa de baixa ductilidade do aço a ser fundido. Caso contrário, existe o risco de rachaduras na superfície.
Transferência de calor além da seção de resfriamento secundário
Do final da seção de resfriamento secundária até a seção de corte, o cordão é resfriado principalmente ao ar apenas por convecção e radiação.
Processo de manufatura
- Inclusões em aço fundido contínuo e sua detecção
- Automação, Instrumentação e Modelagem de Lingotamento Contínuo de Aço
- Resfriamento por névoa de ar em lingotamento contínuo
- Pós para moldes de fundição contínua
- Tundish e seu papel na fundição contínua de aço
- Fundamentos de Fundição Contínua de Aço
- Agitação Eletromagnética no Processo de Fundição Contínua
- Papel do Molde na Fundição Contínua de Aço
- Transferência de Calor PCB
- Processo de tratamento térmico do aço