Processo Redsmelt para fabricação de ferro
Processo de fundição vermelha para fabricação de ferro
Redsmelt é um novo processo de fabricação de ferro baseado em duas etapas de redução. Estes são (i) pré-redução de materiais de suporte de ferro em um forno rotativo (RHF), e (ii) fundição do ferro pré-reduzido a quente (DRI, ferro reduzido direto). Originalmente, um forno de arco submerso (SAF) foi usado para a segunda etapa. O SAF agora foi substituído por um conversor de carvão e oxigênio (reator oxi-carvão) conhecido como “Nova Tecnologia de Fundição” (NST). O RHF reduz as pelotas verdes feitas de minério de ferro, finos redutores e ligantes para produzir DRI metalizado a quente, que é cobrado do NST para sua fundição em metal quente.
O processo Redsmelt foi concebido para consistir numa tecnologia económica e amiga do ambiente. Os destaques importantes do processo são os seguintes.
- O processo não precisa de nenhum material de cobrança preparado
- O processo não necessita de energia elétrica, pois a fundição DRI é feita com energia química
- A fundição está tendo alta produtividade, resultando em um custo de investimento limitado
- O processo pode utilizar praticamente todos os resíduos gerados durante os diversos processos da siderurgia (incluindo lodos e carepas oleosas), resolvendo assim a crescente questão do tratamento de resíduos de aço
- O efluente proveniente do reator de fundição é usado como combustível no RHF, com otimização da utilização geral de energia. Isso resulta em redução efetiva no consumo de energia
Uma planta de demonstração Redsmelt com processo de redução de fundição em duas etapas foi construída e testada na fábrica de Piombino (Itália) para a produção de metal quente. A planta de demonstração foi comissionada no ano de 2003. As duas etapas de produção na planta de demonstração foram baseadas na pré-redução de materiais contendo ferro em um RHF e na fundição do DRI quente em um conversor de oxi-carvão. A planta foi projetada para processar até 65.000 toneladas por ano de matérias-primas (em base seca) com uma produção nominal de metal quente de 30.000 toneladas por ano a 35.000 toneladas por ano.
A tecnologia do processo Redsmelt foi desenvolvida para atender à crescente demanda por uma alternativa de fabricação de ferro de baixo custo ambientalmente amigável à rota tradicional de alto-forno em usinas siderúrgicas integradas de grande escala. A planta com este processo pode ser projetada para uma capacidade de produção de 0,3 milhão de toneladas por ano a 1,0 milhão de toneladas por ano de metal quente. O processo foi projetado principalmente para duas aplicações básicas, a saber (i) para converter subprodutos contendo ferro da planta em metal quente valioso e (ii) para produzir metal quente em escala média baixa (tipicamente em torno de 500.000 toneladas por ano), a fim de combinar com o conceito de mini-mill onde o metal quente é usado como substituto de sucata.
O conceito do processo Redsmelt é mostrado na Fig 1.
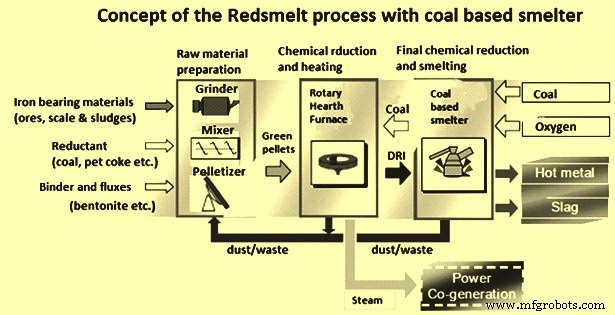
Fig 1 Conceito do processo Redsmelt
O processo
O processo consiste em várias etapas, conforme indicado abaixo.
Preparação de materiais – Para a preparação de pellets verdes, são utilizados materiais de suporte de ferro finamente moídos e um redutor à base de carbono, como carvão ou coque de petróleo. O processo de peletização requer materiais com granulometria o mais próximo possível do ótimo que é 80% abaixo de 100 micrômetros e 100% abaixo de 250 micrômetros. Uma mistura úmida é preparada em um misturador onde esses materiais são cuidadosamente dosados com adição de água e uma pequena quantidade de ligante (bentonita). A mistura preparada é peletizada em um disco peletizador com adição de mais água. Os pellets verdes produzidos são então peneirados para remover a fração subdimensionada que é reciclada, enquanto o produto dimensionado é carregado em um secador de esteira metálica.
Secador de pellets verdes – As duas finalidades do secador de pellets verdes são (i) evitar problemas de aderência no sistema de alimentação RHF e (ii) evitar a decrepitação de pellets verdes no RHF. O calor necessário para a secagem dos pellets verdes é fornecido pelo gás de exaustão do RHF. Isso também resulta na melhoria da eficiência energética geral do processo.
Forno de lareira rotativa – A fornalha anular rotativa é colocada em uma câmara do forno coberta por um teto tipo suspenso. As paredes laterais, o teto e a lareira do RHF são revestidos de refratário para permitir uma temperatura de operação de até 1450 graus C. Os pellets verdes secos são carregados no RHF através de um alimentador vibratório e distribuídos ao longo da lareira como uma camada uniforme de cerca de 20 mm (um a três pellets) em toda a largura da lareira.
O gás combustível e o ar de combustão são introduzidos através de vários queimadores laterais agrupados em três zonas de controle. Em cada zona de queima as vazões de combustível e ar são controladas individualmente pelo sistema de controle, a fim de obter a temperatura desejada e a composição do gás (CO e O2). Nas zonas 1 e 2, o ar secundário é introduzido através de entradas de ar separadas para a combustão do CO liberado pelo processo de redução. Os pellets, após o carregamento, são aquecidos rapidamente até a temperatura de redução. O tempo total de residência varia de 10 minutos a 18 minutos na lareira do RHF para atingir um grau de metalização final de 70% a 90%. Dependendo das propriedades das diferentes matérias-primas, a produção específica do DRI varia na faixa de 60 kg/m² h a 100 kg/m² h.
O calor necessário para o processo é fornecido por quatro fontes de energia diferentes, a saber (i) combustão do combustível auxiliar (gás rico em CO do vaso do reator NST), (ii) combustão do CO resultante da redução do óxido de ferro, (iii) combustão de voláteis liberados pelo redutor (carvão), e (iv) combustão de uma fração do próprio redutor (queima de carbono). A utilização dessas fontes de energia está claramente em competição com o fenômeno indesejado da reoxidação do ferro. O projeto do RHF visa especificamente otimizar este complexo sistema gás-dinâmico. Inclui queimadores e entradas de ar especiais, para a injeção de ar de combustão secundária, capazes de ajustar o grau de turbulência adequado em cada zona e em cada nível da câmara do forno. Outro fator crítico necessário para um bom projeto de RHF é a necessidade de um controle de temperatura extremamente preciso em toda a área da lareira para obter propriedades mecânicas e químicas consistentes dos pellets produzidos. O sistema de queimadores geralmente é projetado para atender a todos esses objetivos e garantir a formação mínima de NOx.
Os pellets DRI produzidos são descarregados através de um parafuso resfriado a água em uma calha e, em seguida, movidos por um transportador de correia metálica contínua (projetado para transporte DRI quente) para o forno de fundição. O transportador metálico é feito de material resistente ao calor e fechado em um eixo estanque ao gás. O gás de saída que sai do RHF e do secador é descarregado na atmosfera após pós-combustão, diluição do ar, injeção de água e despoeiramento através de um filtro de mangas.
Parte da energia do gás residual do RHF é usada para secar as pelotas verdes. A energia do gás residual também é usada para pré-aquecer o ar de combustão e fornecer calor para a secagem de matérias-primas. Em usinas de grande porte, a energia do gás residual também pode ser usada para produzir vapor por uma caldeira de calor residual.
Forno de fundição – No conceito original do processo Redsmelt, um forno a arco submerso foi incluído para a fundição e redução final do DRI. No entanto, na demonstração do Redsmelt em Piombino, o forno de fundição NST foi usado para a fundição e redução final do DRI.
O forno de fundição NST consiste em um vaso reator vertical não basculante. Sua parte inferior (lareira) é equipada com um sifão semelhante aos adotados em mini-alto-fornos ou cúpulas (separação de escória e gusa com skimmer). O Hot DRI é carregado por gravidade a partir do topo por uma calha refrigerada a água, colocada no centro da embarcação. Uma cortina de ar ao redor da ponta da lança minimiza a transferência de DRI diretamente com o fluxo de gás residual. Os fluxos em tamanhos de pedaços são carregados através de uma porta de alimentação separada. O resfriamento do vaso do reator na área de interface escória e metal-escória é realizado por elementos de resfriamento especiais de cobre. O teto do vaso do reator e o duto de gás são feitos de paredes de água com soldagem tubo a tubo.
O reator de fundição está equipado com dois níveis de lanças laterais (três lanças por nível) para injetar oxigênio e carvão. A posição e a orientação dessas lanças visam gerar as condições químicas e fluidodinâmicas adequadas ao processo. Particularmente, o sistema é projetado para melhorar a transferência de calor entre a zona oxidante superior, onde ocorre a pós-combustão do gás CO, e a zona redutora, onde ocorre a redução direta de óxidos de ferro e outras reações endotérmicas. As lanças superiores injetam oxigênio no nível da emulsão para promover a pós-combustão na zona de transição, enquanto as lanças inferiores injetam oxigênio e carvão no banho de metal quente. Com este arranjo a injeção de gás promove uma turbulência de escória que é suficiente para transportar a energia térmica necessária da zona exotérmica (pós-combustão) para a zona endotérmica (fusão) onde ocorre a redução direta do FeO. O carvão relativamente grosso é utilizado para reduzir as perdas de carbono e melhorar a carburação do metal quente. O gusa produzido é fundido em ferro gusa em moldes de areia ou em máquina de lingotamento dependendo da capacidade da planta.
O topo da fundição tem um teto refrigerado a água para evitar o desgaste refratário devido às altas temperaturas resultantes da pós-combustão. Depois disso, um duto resfriado a água coleta e resfria o gás de exaustão da fundição até a temperatura adequada para entrar no sistema de têmpera. O gás de saída é resfriado e limpo sem combustão e é enviado para um pequeno reservatório de gás para estabilizar sua pressão e então utilizado no RHF como combustível do queimador.
Sistema de condicionamento sem gás – A linha de condicionamento de efluentes é composta por duto de pós-combustão revestido de refratário, extintor de gás com jatos de água, estação de diluição de ar e filtro de mangas. Devido à combinação dos gases RHF e NST em um sistema de sucção comum, o projeto adequado do sistema é importante, especialmente o duto de gases RHF.
O gás de exaustão deixa o RHF a uma temperatura em torno de 1100 graus C e não é completamente oxidado. Em seguida, é transportado para um duto revestido de refratário. Bocais adequados para injeção de ar fresco estão localizados após a entrada de gás no duto revestido de refratário para queimar compostos como CO e limitar a temperatura abaixo do valor em que as cinzas volantes começam a derreter. As condições adequadas para atingir a combustão completa do gás de escape são (i) nível de oxigênio livre superior a 3%, (ii) alto grau de turbulência e (iii) um tempo de residência acima de 1 segundo. Os bicos de injeção de ar são distribuídos homogeneamente ao longo do duto para minimizar a formação de NOx.
Em comparação com o gás de saída do RHF, o gás de saída proveniente da fundição tem uma temperatura mais alta (cerca de 1700°C) e um grau de pós-combustão mais baixo com o consequente teor de compostos não queimados (CO+H2 é superior a 30%) . O gás de exaustão da fundição é transportado para um duto resfriado a água, onde o ar de pós-combustão é injetado. Os parâmetros de combustão (tempo de residência, oxigênio, turbulência e temperatura) são os mesmos usados para o tratamento de efluentes de RHF.
Os gases RHF e de fundição a uma temperatura não superior a 950 graus C são então transportados para o mesmo quencher, para reduzir a temperatura dos fumos para cerca de 320 graus C. Os bicos do tipo 'spill-back' permitem a nebulização completa das gotas de água e uma redução rápida da temperatura do gás.
Uma pilha de emergência equipada com uma válvula de sangria (auto-abertura em caso de emergência) é colocada na parte superior do quencher. O primário RHF, o primário da fundição e o ar de despoeiramento secundário são finalmente enviados para a planta de despoeiramento.
O fluxograma do processo Redsmelt com forno a arco submerso é dado na Fig 2.
Fig 2 Fluxograma do processo Redsmelt com forno a arco submerso como unidade de fundição
Processo de manufatura
- Processo Finex para Produção de Ferro Líquido
- Processo HIsmelt de fabricação de ferro
- Processo HIsarna para fabricação de ferro
- Tecnologias para Melhoria no Processo de Sinterização
- Química da Ferragem por Processo de Alto Forno
- Processos FASTMET e FASTMELT de fabricação de ferro
- Processo CONARC para Siderurgia
- Processo de Laminação para Aço
- Processo de Produção para Refratários Moldados
- Processo de Laminação a Quente e Frio