Principais características de um alto-forno moderno de alta capacidade
Principais características de um alto-forno moderno de alta capacidade
O desempenho de uma siderúrgica integrada é altamente dependente do desempenho de suas unidades siderúrgicas. Em usinas siderúrgicas integradas, a produção de metal quente (HM) em um alto-forno (BF) é a rota preferida globalmente para a produção de ferro. O custo específico de produção de aço é altamente dependente do custo específico de HM no BF. Assim, BF é uma unidade muito importante de uma siderúrgica.
O BF moderno é um BF de alta capacidade com grande volume útil. Tem muitos recursos tecnológicos avançados. Por conta dos recursos tecnológicos avançados, possui maior vida útil de campanha e melhores índices de produção. Possui maior zona de redução indireta e menor área de superfície específica, o que é benéfico para melhorar a eficiência da utilização do gás, diminuir a perda de calor e reduzir a taxa de combustível. A taxa de coque, taxa de carvão e taxa de combustível do moderno BF de alta capacidade geralmente é baixa, pois possui uma tecnologia integrada para operação de baixo carbono.
O BF moderno de alta capacidade tem maior produtividade determinada pela produção de toneladas de metal quente (tHM) por metro cúbico de volume útil por dia e menor consumo específico de combustível. Por isso, tem menor custo específico de produção de HM e menor investimento por tonelada de capacidade de HM. Isso porque o moderno BF de alta capacidade utiliza diversas tecnologias modernas de última geração e possui recursos para garantir a qualidade da matéria-prima que é carregada no BF, operação mais suave do BF e melhor aproveitamento da energia térmica e química do gás para redução de combustível. avaliar.
O moderno BF de alta capacidade incorpora muitas tecnologias de última geração. Essas tecnologias incluem tecnologias de preparação de matéria-prima e tecnologias relacionadas à melhoria da eficiência de utilização do gás BF. Além disso, os fornos modernos de alta capacidade possuem muitos recursos avançados. As principais tecnologias avançadas e os recursos de um BF moderno de alta capacidade são mostrados na Fig 1 e descritos a seguir.
Fig 1 Principais tecnologias avançadas e os recursos de um alto-forno moderno de alta capacidade
Tecnologias de preparação de matérias-primas
As principais tecnologias de preparação de matérias-primas incluem (i) uso de sinter com baixo teor de sílica e alta redutibilidade, (ii) otimização da mistura de carvão para coqueificação de carvões, (iii) tecnologia de mistura para matérias-primas, (iv) controle da carga de elementos nocivos , (v) tecnologia de peneiramento de matérias-primas, (vi) utilização de menor tamanho de sinter, (vii) utilização de coque de castanha, e (viii) injeção de pó de coque de têmpera a seco.
Uso de sinter com baixo teor de sílica e alta redutibilidade – Sinter com baixo teor de sílica tem alto teor de ferro (Fe) e, portanto, reduz o volume de escória no BF. Possui propriedades metalúrgicas aprimoradas especialmente suas características de amolecimento e seu uso no BF desloca a posição da zona coesiva para baixo e assim reduz a espessura da zona coesiva, promove a redução indireta e melhora a permeabilidade da coluna de carga. Estatisticamente, o teor de sílica do sinter deve ser de cerca de 5% a 5,5%. As tecnologias específicas para a produção de sinter de baixo teor de sílica e alta redutibilidade incluem o seguinte.
O aumento da basicidade do sinter é necessário para o nível desejado. Uma vez que a quantidade de fase de ligação é diminuída devido à redução do teor de sílica, a basicidade binária do sinter deve ser aumentada adequadamente para aumentar o teor de CaO (óxido de cálcio), aumentando assim o teor de ferrita de cálcio, o que é benéfico para manter quantidade necessária de fase de ligação e para melhorar a redutibilidade do sinter.
A melhoria na proporção dos finos e microfinos dos materiais na mistura de sinterização tem um efeito desejável na fase de ligação. A fase de ligação origina-se em finos de pequeno tamanho, que podem promover a reação da fase sólida e a geração da fase líquida de sinterização.
O tipo e as características dos minérios de ferro têm impacto importante na formação da ferrita de cálcio e na compacidade da mistura de sinterização. Com base nos valores das características de sinterização dos minérios de ferro, a fase de sinterização adequada pode ser formada por seleções apropriadas dos tipos de minérios de ferro, que podem satisfazer o requisito de quantidade de fase de ligação para produzir sinter de baixo teor de sílica, atendendo ao requisito de alto teor de sinterização. sinter de redutibilidade.
Aumentar a altura do leito de sinterização na máquina de sinterização tem muitas vantagens. Tem efeito auto-regenerativo do leito de sinterização e, portanto, reduz o consumo de combustível sólido e o consumo geral de calor. Assim, a sinterização a alta temperatura cai, a atmosfera oxidante é reforçada, o teor de FeO da sinterização é diminuído, o teor de ferrita de cálcio é aumentado e a redutibilidade da sinterização é melhorada. Isso é benéfico para melhorar a fração de tamanho do sinter com baixo teor de sílica.
Otimização da mistura de carvão para coqueificação de carvões – O BF moderno de alta capacidade necessita de coque de maior qualidade. Existem vários requisitos para a qualidade do coque necessários para o moderno BF de alta capacidade. As exigências do coque para a manutenção da coluna de carga na zona grumosa e a manutenção da permeabilidade na área da fornalha são materialmente diferentes uma vez que o volume do BF é alto. Com o aumento do volume de BF, o diâmetro do forno é maior, o lote de minério é aumentado, a carga no coque é aumentada e, portanto, é necessário um coque de maior resistência ao frio. A atividade da moderna lareira de BF de alta capacidade tem maior impacto no rendimento, operação suave, injeção de carvão pulverizado e rosqueamento, portanto, os maiores requisitos para melhorar a degradação do coque no BF e para garantir o tamanho do coque que é necessário antes da tuyeres e na área do homem morto.
O aumento das taxas de injeção do carvão pulverizado aumentou drasticamente o tempo de residência do coque no BF. Assim, também aumentou os estresses químicos e físicos no coque. Com taxas de injeção de carvão pulverizado (PCI) de 200 kg/tHM a 250 kg/tHM, o tempo de residência do coque é duas vezes maior em comparação com um caso sem a injeção do carvão pulverizado. Um aumento da porosidade do coque e uma diminuição da resistência nas partes inferiores foram observados ao aumentar as taxas de PCI. Assim, os requisitos para a qualidade do coque são significativamente maiores no BF moderno de alta capacidade com altas taxas de injeção de carvão pulverizado.
Atualmente, para controlar o custo do coque metalúrgico, diversos tipos de carvões com diferentes análises proximais e com diferentes propriedades de coqueificação são utilizados de forma mista para a produção do coque BF. Em algumas usinas, as misturas de carvão contêm até uma pequena quantidade de carvão não coqueificável. Para a produção de coque BF com a resistência e propriedades térmicas exigidas para o BF moderno de alta capacidade, há requisitos a serem atendidos para a seleção de carvões para a mistura de carvão e há a necessidade de uma mistura uniforme de carvões antes a coqueificação da mistura de carvão.
Tecnologia de mistura para matérias-primas – As flutuações no teor de Fe da carga ferrosa e na basicidade da escória causam operação instável do BF e aumenta a taxa de coque e diminui a saída do BF. Atualmente, com o moderno BF de grande capacidade, é construído um pátio de matéria-prima para realizar as funções de armazenamento, mistura e movimentação de granéis para reduzir as flutuações na composição do minério, sinter ou pelota. O teor de umidade e a fração de tamanho das matérias-primas sendo carregadas no BF também devem ser controlados para atender aos requisitos do BF. Além disso, as variedades e a proporção de matéria-prima são ajustadas conforme a necessidade de produção do BF. Além disso, todo o processo de preparação da matéria-prima deve se adaptar às mudanças no fornecimento de matéria-prima. Todo o processo é automatizado utilizando o modelo de minério inteligente. Este modelo programa o plano geral de mistura de minério, alocação dinâmica de matérias-primas em tanques de dosagem e controle inteligente da velocidade de corte das balanças de alimentação constante para garantir a composição uniforme da carga de minério a ser carregada no BF. Os desvios padrão são controlados em porcentagem de sílica em um nível de mais/menos 0,125% e em porcentagem de ferro total em um nível de mais/menos 0,375%.
Controle de carga de elementos nocivos – A carga de elementos nocivos deve ser controlada, pois o acúmulo de elementos nocivos no BF danifica o revestimento refratário. Isso, por sua vez, leva a flutuações frequentes na carga térmica e resulta em um forno instável. Principalmente, os elementos nocivos causam degradação do coque, destroem a função de suporte de carga do coque e resultam em maior taxa de coque. Investigações realizadas em um dos BF de alta capacidade mostraram que sob carga alcalina em torno de 4 kg/tHM e carga de zinco em torno de 280 g/tHM, a taxa de degradação do tamanho do coque localizado de 0,5 m a 2,5 m acima da ventaneira é de cerca de 70 %, o que significa que o coque está altamente degradado. Portanto, atenção especial é necessária em BF de alta capacidade para o controle da carga alcalina para um nível inferior a 2 kg/tHM e a carga de zinco para um nível inferior a 150 g/tHM.
Tecnologia de triagem de matérias-primas – O BF possui uma coluna móvel vertical de matérias-primas que necessita de boa permeabilidade para o bom funcionamento do forno. Assim, a cobrança de multas deve ser controlada pela triagem contínua da carga e isso significa um controle rigoroso sobre a operação de triagem dos materiais de carga do BF. A proporção de materiais com menos de 5 mm na carga de BF não deve exceder 5%. A redução no carregamento de materiais de carga com tamanho inferior a 5 mm também reduz o teor de poeira do gás BF superior. Cada diminuição de 1% na cobrança dos finos no BF reduz a taxa de coque em cerca de 0,5%.
Utilização de tamanho menor de sinter – A utilização de menor tamanho de sinter aumenta o rendimento de sinter e reduz a taxa de combustível na planta de sinter. Além disso, a utilização de sínter de menor tamanho também reduz a carga circulante na planta de sinterização. Normalmente, o sinter é carregado no moderno BF de alta capacidade em duas faixas de tamanho que consistem em (i) maiores que 10 mm e (ii) na faixa de 4 mm a 10 mm. A fração de 4 mm a 10 mm é carregada na periferia para melhor eficiência de utilização do sinter e melhoria na geração de gás, bem como redução na taxa de combustível.
Utilização de coque de nozes – A faixa de tamanho do coque de castanha é geralmente de 10 mm a 25 mm. O coque de noz é normalmente carregado com a carga de minério no BF. O carregamento de coque no BF melhora o aproveitamento da energia na siderurgia. A prática de carregamento de coque de castanha em BF de alta capacidade mostrou que é benéfica para o bom funcionamento do BF e tem efeito distinto na redução da taxa de combustível.
Injeção de pó de coque de têmpera a seco – Uma quantidade substancial de pó de coque é gerada durante a têmpera a seco do coque. Este pó de coque tem valor calorífico (CV) significativamente maior do que o CV do carvão usado para PCI. Cerca de 8% do pó de têmpera a seco de coque pode ser adicionado ao carvão bruto usado para PCI. Isso melhora o teor fixo de carbono do carvão usado para injeção e resulta em redução na taxa de combustível. O consumo de pó de coque em torno de 4-5 kg/tHM pode ser alcançado com ajustes adequados nos processos de pulverização e injeção.
Melhoria da eficiência de utilização do gás BF
O BF é um reator contínuo onde os materiais de carga são carregados em camadas alternadas de minério e coque de forma intermitente. Esta estrutura em camadas é mantida à medida que os materiais de carga descem através do forno. A distribuição de carga refere-se à obtenção do arranjo adequado das camadas de diferentes materiais dentro do forno e principalmente à distribuição radial (já que a simetria axial geralmente é desejada). Os vários materiais de carga carregados no forno são muito diferentes uns dos outros. O minério é cerca de quatro vezes mais pesado que o coque e o tamanho das partículas é de 2 a 4 vezes menor, o que afeta a permeabilidade do gás e o aquecimento das camadas carregadas. À medida que o gás redutor sobe de baixo, ele encontra as camadas de carga que têm níveis muito diferentes de permeabilidade. Assim, a distribuição radial de minério e coque é um fator importante que rege a distribuição do fluxo de gás no forno.
Geralmente, a fração de minério do volume ou massa total é usada para quantificar a distribuição do material. A região (radial) com maior fração de minério resulta em menor fluxo de gás. Em algumas práticas operacionais, é preferível um fluxo de gás mais alto no centro do forno, porque é eficaz na diminuição do movimento descontínuo da carga sólida, resultando em uma operação de BF mais suave. Assim, lotes de coque de grande porte, conhecidos como "centro-coque", ou sinter e minério granulado maiores são carregados perto do centro do forno para melhorar a permeabilidade ao gás na região. BF com carregamento sem sino está equipado para carregar coque diretamente no centro do forno. No entanto, um fluxo de gás mais alto também resulta em temperaturas de gás mais altas, pois o gás não tem tempo suficiente para a troca de calor e a taxa de fluxo térmico (definida como a relação de capacidade de calor entre carga e gás) é baixa.
As regiões com temperatura de gás mais alta geralmente correspondem a um nível de zona coesiva mais alto. Portanto, as leituras de temperatura da sonda de carga acima são indicadores importantes da distribuição de carga dentro do forno. À medida que a carga desce para o forno, o minério é reduzido e por volta de 1200 graus C (dependendo da qualidade do minério), ele começa a amolecer e eventualmente derrete em torno de 1350 graus C. O coque, por outro lado, mantém sua forma (exceto a quantidade consumida pela reação de perda de solução) até atingir o nível da ventaneira. A porção semi-fundida da carga é extremamente impermeável ao fluxo de gás, então o gás tem que fluir por regiões mais permeáveis, fendas de coque, na zona coesiva onde muda para direção mais horizontal, até atingir a zona irregular. Se as fendas de coque estiverem bloqueadas ou não forem suficientemente permeáveis, podem ocorrer irregularidades do forno, como suspensão ou descida irregular da carga. A distribuição de carga tem um papel importante em afetar o tamanho das fendas de coque na zona coesiva. Também influencia a formação da zona morta no forno, bem como a taxa de desgaste do revestimento do forno, controlando o fluxo de gás e, portanto, as perdas de calor. A maioria das práticas de operação de BF de alta capacidade se concentra na crescente falta de materiais de carga de alta qualidade e na melhoria da eficiência do forno. Essas novas práticas exigem um controle muito preciso da distribuição da carga, que é realizado por modelagem precisa e cálculos rápidos. Assim, a simulação da distribuição de carga está se tornando uma necessidade cada vez mais importante para o bom funcionamento do forno. Além disso, altas taxas de injeção de carvão através das ventaneiras em BFs reduzem as taxas de coque no forno, de modo que a espessura das camadas de coque está se tornando cada vez menor. Tudo isso requer um controle preciso da distribuição dos materiais de carga para permitir uma permeabilidade suficiente no forno e uma localização adequada das fendas de coque na zona coesiva.
Em um BF, várias reações estão ocorrendo devido ao movimento em contracorrente dos materiais de carga e dos gases. Assim, o BF opera de forma eficiente quando há movimento descendente suave dos materiais de carga e distribuição equilibrada do fluxo de gás. Isso resulta em melhoria na eficiência de utilização do gás e redução na taxa de combustível. A melhoria da eficiência de utilização do gás pode ser alcançada devido à plena utilização das energias térmica e química dos gases. A eficiência de utilização de gás do moderno BF de alta capacidade é geralmente alta e em muitos dos BFs está acima de 50%. Os meios primários para a melhoria da eficiência de utilização do gás e fundição dos materiais de carga ferrosa no BF são alcançados através da distribuição apropriada da carga no forno que, por sua vez, ajusta a distribuição do fluxo de gás.
Ajuste na parte superior do BF – É alcançado pelo controle da carga dos materiais de carga. O carregamento dos materiais de carga pode ser através de (i) carregamento central, (ii) carregamento periférico ou (iii) carregamento radial controlado para obter uma distribuição racional do fluxo de gás. O controle da cobrança dos materiais de carga constitui (i) modalidade de cobrança, (ii) peso do lote, e (iii) a manutenção do nível da linha de estoque.
O modo de carregamento precisa de regulamentos para melhorar a eficiência da utilização do gás. O lote do material e seu tamanho e sequência de carregamento determinam a profundidade do material no forno. Geralmente, quando a taxa de PCI aumenta, há um aumento na razão minério/coque devido à diminuição do peso do lote de coque, diminuindo assim a janela de coque no forno. Devido a isso, a relação minério/coque no limite da zona grumosa aumenta, afetando a distribuição do fluxo de gás, levando à deterioração da permeabilidade e aumento da diferença de pressão. Assim, para ajustar o fluxo central de gás, o carregamento central de coque precisa ser aumentado e a profundidade da janela de coque precisa ser aumentada. Além disso, na periferia, a carga precisa ser ajustada adequadamente, aumentando a quantidade de coque ou diminuindo a quantidade de minério. No geral, o funcionamento central do forno deve ser melhorado e a restrição da quantidade de minério rolando para o centro deve ser assegurada, para evitar a obstrução do fluxo central de gás, deterioração da operação suave e aumento na taxa de combustível . O carregamento central do coque e a profundidade da janela de coque devem ser determinados de acordo com a condição do BF.
No BF de grande capacidade, o período de fundição se estende e a degradação do coque é mais grave e, por causa disso, o fluxo de gás aumenta. À medida que a área da seção transversal aumenta, o volume da zona de homem morto aumenta e a uniformidade da distribuição do fluxo de gás se deteriora. Portanto, há um requisito para fortalecer o fluxo de gás central e aumentar a altura da zona coesiva em forma de "V" invertido para garantir área suficiente de janela de coque e fluxo de gás suave. O modo de carregamento central de coque pode melhorar e estabilizar o fluxo central de gás, reduzir a perda de solução do coque central, evitar a degradação do coque, aumentar adequadamente a altura da zona coesiva e garantir a distribuição racional do fluxo de gás e operação suave do forno. Assim, o BF de alta capacidade pode adotar o modo de carregamento central de coque quando necessário, mas ao mesmo tempo deve-se prestar atenção para que isso não seja feito em excesso.
As maiores vantagens do modo regulado de carregamento são a maior eficiência de utilização de gás e menor taxa de combustível, mas requer qualidade mais alta e uniforme dos materiais de carga. Enquanto as maiores vantagens do modo de carregamento central de coque é que ele adapta a flutuação na qualidade dos materiais de carga, mas com a grande desvantagem de diminuir a eficiência de utilização do gás, o que resulta em maior taxa de combustível.
O peso do lote de minério tem impacto significativo na distribuição da carga na garganta do forno e tem alguma influência na distribuição do fluxo de gás. O peso do lote tem uma faixa de controle diferente para diferentes BFs. Com o aumento do volume de BF, a área da garganta aumenta e, portanto, o peso do lote de minério precisa ser aumentado de acordo. Portanto, todos os equipamentos do lado de carregamento do BF devem ser projetados e dimensionados para atender ao maior peso do lote de minério. O lote de minério maior é benéfico para a estabilidade do forno, melhora a eficiência de utilização do gás e reduz a taxa de combustível. Assim, do ponto de vista de estabilizar a camada de coque na zona coesiva e reduzir a mudança na distribuição do fluxo de gás, o ajuste superior no BF é estabilizar o peso do lote de coque para uma profundidade de coque adequada e, consequentemente, alterar o peso do lote de minério.
A manutenção do nível da linha de estoque é realizada ajustando a altura de queda da carga para alterar a posição de deposição do pico, e em combinação com o ângulo inicial do chute. Com o nível de linha de estoque diferente, a distribuição de carga na superfície é diferente e isso tem uma grande influência na distribuição do fluxo de gás. O nível da linha de estoque tem relação com o perfil da garganta, perfil do eixo superior e as propriedades dos materiais de carga. Na prática, o controle do nível da linha de estoque deve ser combinado com o ângulo de carregamento do chute sem sino, e o ponto de queda inicial deve estar localizado a 300 mm da parede.
Ajuste na parte inferior do BF – O ajuste na parte inferior do BF é realizado pelo ajuste dos parâmetros de explosão para controlar a zona de combustão da ventaneira que tem efeito na distribuição inicial do fluxo de gás no forno. É crucial para controlar a operação suave do forno, distribuição racional do fluxo de gás e melhoria da eficiência da utilização do gás. Uma distribuição inicial racional do fluxo de gás pode ser alcançada através do ajuste na parte inferior do BF. Isso é feito pelo controle do volume de sopro e controle da energia cinética do sopro de ar quente.
O controle do volume de explosão é feito para influenciar o volume de gás bosh. Quando o volume de gás bosh é pequeno, com o aumento do volume de explosão e o movimento no BF melhora, há diminuição da taxa de combustível e da taxa de coque. Depois que o movimento no BF for alcançado a um certo nível, o volume de gás bosh deve ser restrito. Qualquer aumento adicional no volume da explosão resulta em aumento na taxa de combustível e na taxa de coque. É porque o fluxo de gás é afetado pela permeabilidade da coluna de carga. Qualquer desenvolvimento do fluxo de gás periférico ou fluxo de gás central excessivo leva a diminuir a eficiência de utilização do gás e aumentar a taxa de combustível. No moderno BF de alta capacidade, o volume de explosão é controlado em um nível razoável para garantir a distribuição racional do gás, melhorar a eficiência da utilização do gás e reduzir o coque e a taxa de combustível.
O controle da energia cinética do jato de ar quente é feito para atingir a profundidade ideal ou quase ideal da pista e distribuição racional do fluxo de gás inicial. A zona de combustão da ventaneira é ajustada adequadamente para manter a velocidade do vento e a energia cinética da explosão apropriadas e para evitar a influência da velocidade do vento e da energia cinética da explosão excessivamente altas no coque na pista. O objetivo no moderno BF de alta capacidade é atingir uma energia cinética de explosão em um nível de cerca de 14.000 kg.m/s (kg.m/s) a 15.000 kg.m/s. Para atingir este nível de energia cinética, a primeira medida é manter uma velocidade de vento razoável (normalmente na faixa de 250 metros por segundo a 270 metros por segundo). Se a quantidade de coque na carga for alta, a velocidade do vento pode ser maior e vice-versa. No entanto, a velocidade do vento está sujeita a um teto pela correspondência adequada do volume da explosão, zona de combustão da ventaneira, temperatura da explosão e pressão máxima dentro dos limites razoáveis para alcançar bons índices de produção.
Recursos importantes de um BF moderno de alta capacidade
Algumas das características importantes de um BF moderno de alta capacidade são descritas abaixo.
Alta temperatura de explosão – O calor necessário para realizar o processo de fundição no BF provém principalmente da combustão do combustível (coque + carvão) e do calor físico do jato de ar quente. Geralmente, o calor físico do jato de ar quente é responsável por cerca de 30% da necessidade total de calor no BF. Quanto maior a quantidade de calor físico que é trazido pelo jato de ar quente, menor é o calor necessário para a combustão do combustível. A melhoria na temperatura de jateamento reduz a taxa de combustível e tem uma economia no custo de produção do HM. Isso ocorre porque o calor físico trazido pela explosão quente pode substituir parte do combustível. Além disso, com o aumento da temperatura de explosão, a taxa de PCI pode ser melhorada. O aumento da taxa de PCI substitui um pouco de coque e, portanto, reduz a taxa de coque.
Nos últimos anos, a tecnologia de fogões a quente tem desenvolvimentos significativos. O desenvolvimento da tecnologia de fogões a quente é da combustão interna para a combustão externa e depois para a combustão superior. O gás combustível que normalmente tem sido uma mistura de gás de baixo poder calorífico (CV) geralmente consistindo de gás BF enriquecido com uma parte do gás de alto CV (geralmente gás de coqueria) para apenas gás BF com tecnologia de pré-aquecimento duplo gás-ar para se adequar o requisito de alta temperatura de explosão que também está aumentando ano a ano. A temperatura de explosão de alguns dos BFs de alta capacidade está na faixa de 1.250 graus C a 1300 graus C.
Explosão desumidificada – O alto desumidificado elimina a perda de calor necessária para a decomposição da água no alto-forno. Isso, por sua vez, aumenta a temperatura da chama, promove maior taxa de PCI e, portanto, reduz a taxa de coque. Normalmente, para cada 1 g/Ncum de umidade removida no jato de ar quente, há uma diminuição na taxa de coque na faixa de 0,8 kg/tHM a 1 kg/tHM. Para manter as condições térmicas da lareira, para cada 1 g/N cum remoção de umidade, a taxa de PCI aumenta de 1,5 kg/tHM para 2,0 kg/tHM.
BFs modernos de alta capacidade operam com alta temperatura de explosão e baixa umidade de explosão, ajustando a quantidade de PCI para controlar a temperatura do forno. Em muitos fornos, a temperatura de sopro é estabilizada em 1.230 graus C a 1.250 graus C, e a umidade no sopro é estabilizada em 10 g/N cum a 15 g/N cum.
Alta pressão superior – A melhoria da pressão máxima reduz a velocidade do fluxo de gás, diminui a perda de pressão na carga e promove a operação suave do BF. Além disso, o aumento da pressão máxima reduz a quantidade de poeira, aumenta a eficiência de utilização do coque e do carvão e reduz a taxa de coque e combustível. Atualmente, a melhoria da pressão de topo tornou-se um meio indispensável para a produção normal em um BF. A pressão máxima dos BFs modernos de alta capacidade está normalmente acima de 2,75 kg/sq cm.
Injeção econômica de carvão pulverizado – O objetivo da injeção de carvão pulverizado é economizar coque e reduzir o custo de produção de HM. Apesar da diferença de preço entre carvão e coque, se a razão de substituição de carvão por coque diminuir a um certo nível, aumenta a taxa de combustível e os benefícios econômicos da injeção de carvão pulverizado são compensados. Assim, para a injeção econômica de carvão pulverizado, existe a necessidade de manter uma alta taxa de reposição enquanto aumenta a quantidade de injeção de carvão pulverizado. Se ao aumentar a taxa de PCI, há o aumento da taxa de combustível devido à diminuição da taxa de combustão do carvão e devido à diminuição da taxa de reposição, então não é a injeção econômica de carvão pulverizado. Os BFs modernos de alta capacidade visam a injeção econômica de carvão pulverizado. Os pré-requisitos para a injeção econômica de carvão pulverizado são os seguintes.
- Melhoria na qualidade da carga, incluindo coque, sinter, pellet e minério granulado, para reduzir o volume de escória e melhorar a permeabilidade nas porções superior e inferior do BF.
- A implementação de alto nível de enriquecimento de oxigênio, alta temperatura do jato de ar quente e desumidificação do jato de ar quente é essencial para controlar a temperatura da chama e a quantidade acumulada de carvão pulverizado não queimado e pó de coque na lareira, e aumentar a taxa de combustão do carvão pulverizado injetado. O enriquecimento de oxigênio do jato de ar quente reduz o volume de gás por tonelada de HM, aumenta a temperatura da chama e altera a distribuição de temperatura no BF. A combinação do enriquecimento de oxigênio com a injeção de carvão pulverizado reduz adequadamente a mudança da taxa de fluxo de calor, mantém a temperatura da chama dentro de limites razoáveis e torna a operação do BF estável. Cada aumento de 1% na taxa de enriquecimento de oxigênio resulta em aumento na taxa de combustão do carvão em 1,51%. O alto enriquecimento de oxigênio do jato de ar quente é uma característica dos modernos BFs de alta capacidade. Existem BFs de alta capacidade operando com taxa de enriquecimento de oxigênio superior a 10%. O alto enriquecimento do jato de ar quente também compensa a deterioração da qualidade do coque BF.
- A distribuição racional do fluxo de gás e a operação estável do BF são garantidas quando há um fluxo central de gás adequado na parte inferior do BF. É assegurado pelo ajuste nos parâmetros de jateamento que auxilia na utilização completa do carvão pulverizado não queimado que entra na lareira e assim a eficiência de utilização do carvão aumenta.
- A otimização da mistura de carvões para injeção melhora a propriedade de combustão do carvão misturado, melhorou a taxa de PCI, expande as opções de tipo de carvão e reduz o custo do carvão misturado. Geralmente o carvão antracito com alto teor de C (carbono) fixo e alto CV é misturado com carvões betuminosos com alto teor de matéria volátil (VM) e boa propriedade de combustão. O teor de VM do carvão misturado deve ser controlado na faixa de 15% a 25% e o teor de cinzas deve ser inferior ao do coque (geralmente inferior a 11%).
Produção de HM com baixo teor de silício – A produção de HM com baixo teor de silício resulta na redução da taxa de combustível. A cada diminuição de 0,1% do teor de silício do HM, há uma redução na taxa de combustível de cerca de 4 kg/tHM para 6 kg/tHM. A lareira dos BFs modernos de alta capacidade é normalmente ativa e tem bastante calor, por isso é mais fácil produzir HM com baixo teor de silício. Os requisitos tecnológicos para a produção de HM com baixo teor de silício incluem o seguinte.
- Redução da carga de sílica dos materiais de carga a ser alcançada pela diminuição do teor de cinzas do coque, teor de cinzas do carvão para PCI e teor de sílica do sinter.
- Com os requisitos de garantir calor suficiente na lareira BF para o bom funcionamento, a temperatura da chama pode ser reduzida adequadamente para conter a geração de gás SiO.
- O controle da forma e posição razoáveis da zona coesiva é necessário para reduzir o contato do ferro líquido pingando com o gás SiO. Isso evita a geração do silício.
- A otimização da qualidade da escória é necessária reduzindo a atividade da sílica na escória.
- A operação do BF com alta pressão de topo é necessária para a supressão da geração de gás SiO.
However, the production of HM with low silicon has an impact on the campaign life of the BF since it has a detrimental effect on the erosion of the hearth lining. Hence, the silicon content of the HM is normally not dropped to a very low level and is normally maintained in the range of 0.4 % to 0.6 % in the high capacity BFs.
Control of thermal load of the BF – The heat loss of the BF is reduced mainly by controlling the thermal load on the lining. The thermal load reflects the cooling status of the lining and it is frequently used to know whether there is increase in the peripheral gas flow and erosion of the lining. Thermal load is to be controlled within a certain range, and as far as possible to reduce the heat loss, which is in turn helps in the reduction of the fuel rate. However, too low of thermal load can cause build-up (scaffolding) at the lining. This, in turn, affects the gas flow distribution in the BF. Further, when the build-up falls off, it affects the BF operation and even damages the tuyere, leading to reduction the blast or even shut down of the BF. Hence, control is needed for the balanced thermal load in the BF since it is beneficial for its stable operation and for the control of the fuel rate.
For ensuring the suitable thermal load during the BF operation, one of the measures is the maintenance of the proper gas flow distribution by adjusting the charging regulation. The other measure is the adjustment of the cooling water flow according to the erosion level and temperature of lining for the maintenance of the stable operation profile in the BF. Hence, the adjustment of gas flow distribution is the most important means for the control of the thermal load.
In the modern high capacity BFs, thermal load monitoring is carried out through the partition management along the vertical and horizontal direction. The management standard at different height of the BF is different, and the thermal load along the horizontal direction is to be kept uniform. The control of thermal load is done through the adjustments in the upper and lower parts of the BF in oder to gradually achieve the middle-part (between lower shaft and bosh) management of the BF.
The three-dimensional visual thermal load model (Fig 2), which shows the BF operator display of 3 dimension real-time thermal load, historical trend, video-interaction, and alarm function, is the latest trend in the modern high capacity BFs. Combining of the model with the profile management model determines the reasonable control range of thermal load and provides good guidance for the BF operator.
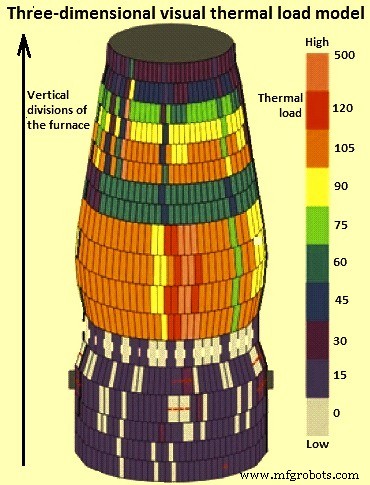
Fig 2 Three-dimensional visual thermal load model
BF operations through visuals
The technology of BF operation by observing the visuals of furnace inside is being followed in the modern high capacity furnaces. This technology of observing the visuals is being used to monitor the distribution of the burden and it helps the BF operator to know what is happening inside the BF. The visuals of the BF inside helps the operator to understand better what is taking place inside of the BF so that proper adjustments can be made in the operating parameters for improving the gas utilization efficiency and thus reducing the fuel rate, and ensuring smooth BF operation. Major implements for the use of this technology are given below.
Use of thermo-vision camera and image processing The video camera at BF top helps the BF operator to observe the movement of the chute, gas flow distribution and the stream of the falling burden materials throughout the whole burden surface. This helps the operator in monitoring of channeling and slipping tendency inside the furnace. Thermo-vision camera is used since during the normal working of the BF, the temperature at the furnace top is normally less than 120 deg C.
Use of laser technology to measure online the surface profile of the burden The laser technology is used to measure the burden surface profile online by installing the burden surface laser detector. These detectors provide the operator the visual burden surface profile image thus helping him in better monitoring of the burden surface profile.
Monitoring of tuyeres by video camera and image processing – With the help of the video camera, the BF operator can observe at the same time the brightness, coke movement and coal stream size at the each tuyere, and timely detect the falling of the scaffolds, skulls, and colder burden in front of the tuyere. By the subsequent image processing, operators can get the quantitative analysis of thermal state and coal stream status at the each tuyere. This helps him in better understanding of the working of the tuyeres and PCI system for taking timely action in case of abnormalities. A video camera with a spectroscope can help the operator in direct observation of the tuyere.
BF filling measurement during BF blow- in using laser technology The use of the laser technology to observe furnace inside during the blow-in of the furnace provides the operator, the filling measurement, the data of burden flow trajectory with different angle of the chute, and the data of burden surface profile after charging. This helps the operator to know the way the burden distribution is done by the charging equipment. This knowledge guides the operator in the charging operation of the BF during the normal operation.
Processo de manufatura
- Geração e uso de gás de alto-forno
- Uso de Nut Coke em um Alto Forno
- Operação de alto-forno e escória de alta alumina
- Injeção de carvão pulverizado em um alto-forno
- Irregularidades do alto-forno durante a operação
- Sistema de resfriamento do alto-forno
- Sistemas de carregamento de alto-forno
- Principais Características de um Moinho Moderno de Barras e Seções Leves
- Principais características de um moderno moinho de fio-máquina
- Principais características de um moderno laminador de tiras a quente