Laminação de Chapas de Aço em Laminador de Chapas
Laminação de chapas de aço em um laminador de chapas
A chapa de aço é definida como um produto plano, laminado ou tratado termicamente, com espessura de pelo menos 5 mm e largura de pelo menos 1.200 mm. A chapa de aço é um produto de aço amplamente utilizado. Ele se enquadra normalmente nas categorias de aço carbono, aço de baixa liga de alta resistência (HSLA) e aço liga. Para aplicações estruturais, chapas de aço normalmente não excedem 0,3% de carbono e 1,5% de manganês. Placas de aço de maior espessura são necessárias para arranha-céus, plataformas de perfuração em alto mar, pontes com vãos gigantes, aerogeradores delgados, gasodutos, gasodutos com enormes pressões, escavadeiras, guindastes móveis, navios porta-contêineres e navios de luxo etc. Essas aplicações precisam de alta qualidade e alta resistência nas placas para confiabilidade.
A tendência mais importante na chapa de aço é a demanda por chapas com resistências cada vez maiores, alta tenacidade, dureza e boa soldabilidade. A primeira qualidade em termos de espessura, largura, perfil, planicidade, retangularidade e uma microestrutura homogênea também são esperadas com todos os tipos de aço e até dimensões extremas. Ao mesmo tempo, tolerâncias cada vez mais estreitas estão sendo exigidas em relação à precisão dimensional e planicidade. Para atender a esses requisitos, os laminadores de chapas grossas devem ter a capacidade de uma grande variedade de mix de produtos com uma alta proporção de chapas de alta resistência a serem produzidas e, portanto, novos laminadores de chapas grossas são projetados para uma grande variedade de tecnologias de produção. Além disso, exige-se a compilação irrestrita das campanhas de laminação com grandes variações de espessura, largura e tipos de aço de uma chapa para outra sem efeitos negativos na produtividade (laminação sem programação).
Os requisitos que são normalmente feitos em chapa grossa são (i) Deve possuir as dimensões especificadas dentro de tolerâncias estreitas e com boa planicidade (as espessuras podem variar de 5 mm a 500 mm e larguras de cerca de 1.200 mm a 5.500 mm), ( ii) é possuir os valores de limite de escoamento e resistência à tração necessários pelos projetistas (limites de escoamento variando de cerca de 235 MPa a acima de 1.100 MPa), (iii) é possuir os valores de tenacidade necessários pelos projetistas mesmo, em muitos casos , tenacidade a baixas temperaturas, (iv) deve possuir boa trabalhabilidade (como deformabilidade e soldabilidade), e (v) se necessário, deve possuir resistência à corrosão resultante, por exemplo, do ataque pelo hidrogênio contido no H2S- gases de rolamento (gás azedo) ou uma certa resistência à corrosão atmosférica (resistência às intempéries). Para a fabricação de chapas de aço para tubulações em serviço com gás ácido, a resistência a trincas induzidas por hidrogênio é o fator mais importante. Para aplicações marítimas offshore, especialmente nas regiões onde as temperaturas caem muito baixas durante o inverno, as chapas de aço precisam ter propriedades como maior resistência, maior espessura da chapa e tenacidade a temperaturas ultrabaixas (excelentes características da junta de solda em baixas temperaturas) etc. Essas propriedades são, em alguns casos, contraditórias e tornaram-se alcançáveis, em uma combinação extrema de tecnologias de liga e processamento. No passado recente, várias tecnologias para o controle de propriedades das chapas de aço foram desenvolvidas para os laminadores de chapas grossas para atender aos requisitos de maior resistência e tenacidade das chapas.
Para atender a demanda de uma grande variedade de produtos com uma grande proporção de chapas de alta resistência a serem produzidas, os modernos laminadores de chapas grossas são normalmente projetados com capacidades para uma grande variedade de tecnologias de produção. A produção de chapas grossas de alta resistência tem implicações para todas as seções de um laminador de chapa grossa. Os suportes de laminação e os sistemas de resfriamento de chapas, bem como todas as seções de laminação a jusante, devem ser projetados de forma que chapas de alta resistência possam ser produzidas e processadas para obter produtos finais de alta qualidade. Isso exige que o laminador de chapas grossas tenha tecnologias aprimoradas de laminação, resfriamento, nivelamento e cisalhamento com vistas a atingir altos padrões de qualidade. Os processos de produção reprodutíveis e uma alta taxa de produção também precisam de alto grau de automação. Os modernos laminadores de chapas grossas são projetados para ter soluções integradas, incluindo equipamentos mecânicos, elétricos e de automação e, portanto, as condições para o controle ideal do processo.
Além disso, para a produção da chapa grossa, há requisitos de operadores qualificados, instalações de plantas eficientes e sistemas de controle e instrumentação adequados para todas as etapas do processo. Procedimentos sistemáticos baseados no know-how atualizado e quantidades consideráveis de energia (gases de aquecimento, energia para sistemas de acionamento, etc.) placas, dados de processo abrangentes registrados para fins de monitoramento e avaliação de qualidade e de amostras de teste para testes mecânicos e tecnológicos pelo pessoal de inspeção de aceitação. A Fig. 1 mostra um layout típico de um laminador de chapas grossas.
Fig 1 Layout típico de um laminador de chapas grossas
Equipamento de laminação
Os principais equipamentos do laminador de chapas grossas são apresentados a seguir.
Os fornos de reaquecimento são utilizados para o aquecimento das lajes inspecionadas e condicionadas recebidas do pátio de lajes a serem laminadas. Nas usinas modernas, os fornos de reaquecimento do tipo feixe ambulante são os preferidos, pois são eficientes em termos energéticos e garantem um aquecimento uniforme das lajes. O forno de reaquecimento deve ter todas as instalações para a recuperação de calor residual. Deverá também ser equipado com os controles de combustão necessários para o controle da temperatura da laje, bem como outros controles necessários para seu funcionamento eficiente. Normalmente existem dois ou três fornos. Cada forno está equipado com um dispositivo de carga e descarga. Um modelo matemático é usado para controlar os queimadores para alcançar a curva de reaquecimento ideal para cada grau de aço. Na saída do forno, as placas aquecidas passam por uma mesa de rolos até o laminador de chapas grossas através de um desincrustante de alta pressão.
A unidade de descalcificação destina-se à remoção da incrustação primária com o uso de jatos de água de alta pressão. Para permitir uma pressão de impacto constante na superfície da laje, um sistema de macaco é normalmente empregado para adaptar a posição do cabeçalho superior à espessura de entrada da laje.
O elemento central do laminador de chapas grossas é composto por cadeiras de laminação de quatro alturas com controle de processo por computador, nas quais a laminação é realizada em passes de alargamento e alongamento. O laminador de chapas grossas tem uma configuração de suporte único ou de dois suportes. No caso de configuração de duas bancadas, as duas bancadas de rolos são conhecidas como bancada de desbaste e bancada de acabamento. Os suportes possuem um sistema de aparafusamento mecânico rápido, além do sistema hidráulico de ajuste de folga de rolo. Uma biseladora vertical na extremidade de saída dos suportes garante o ajuste preciso da largura da chapa. O comprimento do rolo decide a produção das larguras de chapa correspondentes. As bancadas estão equipadas com sistemas de acionamento de alta potência com motores síncronos trifásicos.
Os suportes de laminação podem ter as carcaças de moinho de peça única comprovadas ou carcaças baseadas no conceito de design de várias peças soldadas. No caso de carcaças de moinho aparafusadas de peças múltiplas, os garfos e postes da carcaça do moinho usinados com acabamento são conectados por hastes de tensão fortes. Essa abordagem simplifica a fundição da carcaça do moinho e, ao mesmo tempo, a pré-carga controlada das hastes de tensão garante uma deformação menor da carcaça do moinho sob carga e, portanto, um deslocamento muito bom da placa e uma excelente geometria da placa. As carcaças do moinho são equipadas com controle automático de medidor hidráulico (HAGC), mecanismos eletromecânicos ou hidráulicos de rosca e células de carga. Os descalcificadores de água de alta pressão são instalados em ambos os suportes de laminação na entrada e na saída para obter uma qualidade de superfície ideal.
O nivelador a quente é instalado antes do equipamento de processamento térmico para o achatamento da chapa de aço antes do resfriamento. O nivelador a frio é instalado após a seção de termoprocessamento para o achatamento da placa para retificar a forma deteriorada pelo resfriamento para facilitar a transferência para o processo subsequente. Os niveladores são normalmente hidráulicos, de 4 alturas, 9 rolos com cassetes intercambiáveis.
O sistema de resfriamento é necessário para o desenvolvimento das propriedades do material das placas de alta resistência. Normalmente é projetado para atingir altas taxas de resfriamento (até 80 graus C por segundo), necessárias para chapas de aço de alta resistência. Combina o resfriamento por spray com o resfriamento laminar comprovado. O resfriamento por spray é instalado a montante da seção laminar. O sistema de resfriamento por spray atinge taxas de resfriamento muito altas devido a uma poderosa estação de água de alta pressão em combinação com bicos especiais. Para obter uma boa planicidade da placa também no resfriamento por spray nas taxas de resfriamento mais altas, rolos de pressão são instalados entre os coletores de resfriamento para regular o fluxo de água na placa e, assim, melhorar a distribuição de temperatura e a eficiência de resfriamento.
O sistema de resfriamento é separado em duas zonas para resfriamento direto ou resfriamento acelerado. O sistema de têmpera direta consiste em vários coletores de alta pressão (5 bar) colocados na parte superior e inferior da mesa de rolos e separados por rolos de pressão. A taxa de resfriamento varia de 80 graus C por segundo a 3 graus C por segundo. O sistema de resfriamento acelerado consiste em vários coletores de tubo em U na parte superior da placa e cabeçotes de pulverização na parte inferior. A taxa de resfriamento varia de 40 graus C por segundo a 2 graus C por segundo. A temperatura da placa e a taxa de resfriamento adequada sob o sistema de resfriamento são definidas para garantir as características metalúrgicas dos produtos finais. O modelo de resfriamento é baseado no mapeamento de processos físicos e controla o processo de resfriamento de forma que as propriedades metalúrgicas nas placas sejam alcançadas com precisão.
A linha de cisalhamento e acabamento é projetada para aparar lateralmente e cortar chapas de comprimento normalmente de até 50 mm de espessura. Todas as tesouras são geralmente do tipo oscilante, o que garante tolerâncias dimensionais finais ideais e qualidade superior da aresta. A linha de acabamento também inclui leitos de resfriamento, estação de inspeção ultrassônica, leitos de inspeção de superfície, dispositivo de torneamento de chapas, marcação e estampagem, empilhamento de chapas e instalações de manuseio.
A elétrica e automação inclui todos os sistemas de automação básicos e tecnológicos de Nível 1 e Nível 2, juntamente com modelos matemáticos para controle superior de perfil e planicidade, proporcionando assim um sistema de automação altamente integrado e otimizado que garante resultados precisos e reprodutíveis em termos de qualidade do produto e melhoria eficiência da planta.
Processo contínuo
As placas após a inspeção são aquecidas em um forno de reaquecimento a temperaturas de cerca de 1.200 graus C, o que é adequado para a deformação plástica do aço e, portanto, para a laminação do aço no laminador. A remoção de incrustações de alta pressão é realizada antes da laminação.
A placa aquecida é então laminada no laminador de chapas grossas. O laminador de chapas grossas é normalmente um laminador reversível de quatro alturas com uma configuração de suporte único ou com configurações de dois suportes. No caso de configuração de dois suportes, os dois suportes de laminação são o suporte do laminador de decapagem e o suporte do laminador de acabamento. Os carrinhos de laminação normalmente possuem rolos de borda para controlar a largura da chapa. As chapas são normalmente laminadas na espessura prescrita na mesa de laminação reversa (ou seja, passando repetidamente a chapa para frente e para trás através da mesa de laminação) enquanto reduz progressivamente a folga entre os rolos superior e inferior de maneira gradual, e normalmente precisa de um número de passes rolantes. A ação de passar uma placa através da folga do rolo é chamada de passagem, e a quantidade de redução da espessura da placa em cada passagem é chamada de redução de laminação. A redução de espessura durante a laminação é distribuída em vários passes de laminação. O processo pelo qual o número de passes e a redução de laminação em cada passe da espessura da laje para a espessura do produto são decididos no cronograma de passes de laminação. A temperatura de laminação de acabamento afeta o número de passes necessários devido às propriedades do material, onde o material mais frio fica mais duro.
No caso de produtos de espessura normal (ou seja, chapas planas), a mesma espessura é obtida em todo o comprimento, controlando o laminador para que a folga entre os rolos superior e inferior não se altere durante uma passada de laminação.
Para a laminação da chapa fina, o laminador de chapas grossas deve estar equipado com recursos para controle automático de forma, controle de planicidade e controle de bitola. A fábrica precisa de um instrumento de medição on-line para medição de espessura. As temperaturas de início e término da laminação determinam a estabilidade do processo, onde o material mais frio precisa de mais força de laminação do que o mais quente. Assim, chapas finas com maior taxa de resfriamento do que chapas grossas podem tornar o processo de laminação instável, especialmente para chapas de baixa espessura onde a queda de temperatura é alta.
Os suportes de laminação e os sistemas de resfriamento de chapas, bem como todas as seções de laminação a jusante, devem ser projetados de forma que chapas de alta resistência possam ser produzidas e processadas para obter produtos finais de alta qualidade. Parafuso e controle automático de folga são as partes principais do laminador para ajustar a folga do rolo de acordo com a espessura definida. Cada um dos tamanhos de chapa tem seu próprio cálculo de programação de passagem, incluindo a folga do rolo, a força do rolo e o módulo do moinho apropriados.
A chapa laminada é submetida a nivelamento em nivelador a quente antes de entrar na seção de termoprocessamento e em nivelador a frio após a seção de termoprocessamento. A boa planicidade de uma placa de aço é desejada, pois durante o processo de resfriamento, a planicidade influencia a distância para a água colidir com a placa de aço e influencia o fluxo de água na placa de aço. A função do nivelador a quente instalado antes do equipamento de processamento térmico é aplainar a chapa de aço antes do resfriamento. Por outro lado, o nivelador a frio instalado após a seção de termoprocessamento destina-se a alisar a placa para retificar a forma deteriorada pelo resfriamento para facilitar a transferência para o processo subsequente.
A seção de processamento térmico é muito importante na produção e no processamento da chapa de aço, pois as propriedades finais do aço são alcançadas durante o processamento da chapa nesta seção. Após a chapa ter sido submetida ao processamento térmico necessário para alcançar as propriedades desejadas de resistência, dureza e tenacidade, a chapa de aço é endireitada novamente no nivelador a frio e, em seguida, as atividades de acabamento como cisalhamento e corte, corte de amostra, teste e inspeção e, se necessário, jateamento e revestimento e tingimento são realizados conforme mostrado no fluxograma. A placa é submetida à inspeção final antes de sua expedição.
Durante o teste, todos os testes necessários de acordo com as normas devem ser realizados para garantir que as placas estejam em conformidade com os valores especificados na norma com relação às dimensões, tolerâncias dimensionais, microestrutura, resistência, dureza e tenacidade. O laboratório do laminador deve ser equipado com todos os testes necessários e instalações de inspeção para que os testes e inspeção necessários das chapas laminadas possam ser realizados. O fluxograma de laminação e processamento de chapas de aço em um laminador de chapas grossas é mostrado na Figura 2.
Fig 2 Fluxograma de laminação e processamento de chapas de aço em um laminador de chapas grossas
Tecnologias usadas em laminadoras de chapas grossas
O processo de produção de chapa grossa inclui diversas combinações potenciais de estágios de processo. Durante a laminação de chapas, há um grande número de parâmetros que têm impacto na qualidade da chapa. Estes incluem a deformação do equipamento de laminação, temperatura, força de laminação e velocidade de laminação, etc. A partir de composições de aço definidas, são necessários mecanismos metalúrgicos que permitam a obtenção das propriedades mecânicas e tecnológicas. Esses mecanismos devem ser ativados em uma série de diferentes etapas do processo. As etapas metalúrgicas relevantes são as que contribuem não apenas para a conformação (geometria) da chapa grossa, mas também para suas propriedades mecânicas e tecnológicas, por meio da modificação de sua estrutura. Algumas das principais tecnologias desenvolvidas para o controle dos parâmetros de laminação são apresentadas a seguir.
O controle da espessura da chapa é realizado pelo sistema de controle automático de bitola (AGC). Em um sistema típico, o monitoramento do AGC é feito usando um medidor de espessura de raios gama aproximado. As cargas geradas pela laminação e as mudanças na folga do rolo causadas por essas cargas (flexão do rolo, deformação da carcaça do moinho, etc.) precisão. Alterações na folga do rolo devido a flutuações de carga durante a laminação são corrigidas pelo AGC, reduzindo os desvios na espessura da chapa e a diferença entre a espessura alvo e a espessura medida imediatamente após a laminação ser realimentada na folga do rolo, possibilitando o controle da comprimento total da placa para a espessura alvo.
A obtenção de alta precisão na planicidade (controle de forma) das chapas é uma tarefa importante durante a laminação de chapas em um laminador de chapas grossas. O controle rigoroso da coroa da chapa em cada passe de laminação é necessário para controlar a planicidade das chapas de aço. Em laminadoras de chapas grossas que não possuem sistema de controle de forma, a maior parte do controle de coroamento de chapas é realizada utilizando o perfil do cilindro de trabalho e o controle da distribuição da redução em cada passe. As tecnologias utilizadas para o controle de forma das placas são coroa variável contínua (CVC) juntamente com dobra de rolo de trabalho e dobra de rolo de apoio. A tecnologia de controle de forma também faz uso de software/sensores que consistem em (i) um modelo de coroa de alta precisão que considera a deformação tridimensional do material rolante, (ii) sensor de planicidade próxima e (iii) controle de avanço/retrocesso com base na planicidade medida.
A austenitização, incluindo a homogeneização e a dissolução de elementos de microliga, ocorre durante o aquecimento da placa até uma temperatura definida na faixa de 1.050°C a 1.200°C. Dependendo do regime de temperatura selecionado, um certo fortalecimento e refinamento de grão da estrutura ocorre durante o processo de laminação e é ainda mais intensificado como resultado dos processos de transição da estrutura e precipitação durante a fase de resfriamento subsequente, dependendo da taxa de resfriamento. As placas são normalmente empilhadas a quente na faixa de resfriamento inferior para garantir a efusão do hidrogênio. Modificações estruturais definidas podem ser realizadas através da aplicação de etapas de tratamento térmico dos mais diversos tipos.
As propriedades melhoradas das chapas são alcançadas com a adoção de diferentes tecnologias de laminação. Essas tecnologias são laminação controlada e resfriamento acelerado. No processo de laminação convencional sem requisitos específicos de temperatura, também conhecido como “laminação normal”, a laminação é usada apenas como um processo de conformação. A placa aquecida a altas temperaturas é convertida na geometria da placa em uma fase de laminação e o resfriamento é realizado ao ar.
No processo normal de laminação de chapas nos laminadores de chapas grossas, não há controle especial de temperatura do processo de laminação. Neste processo, a chapa grossa é entregue na condição não tratada termicamente, ou 'como laminada' sem qualquer modificação adicional da estrutura por meio de tratamento térmico. No entanto, uma estrutura com uma combinação típica de propriedades da chapa laminada pode ser alcançada por meio de processos tecnológicos que consistem na combinação de tratamento em temperaturas especificadas e resfriamento. Há uma série de processos tecnológicos empregados nos laminadores de chapas grossas para a laminação de chapas grossas para atender aos requisitos de propriedades para diferentes especificações de chapas grossas. A Figura 3 resume esses processos.
Fig 3 Processos tecnológicos do laminador de chapas
A laminação normalizada consiste em laminação normal com tratamento térmico que consiste em aquecer a placa até a temperatura de austenitização (superior a Ac3, em torno de 900°C) e depois resfriar ao ar. Isso é realizado em fornos de dimensões correspondentes, seja continuamente (por exemplo, forno de feixe duplo) ou estacionário (por exemplo, forno de carregamento lateral). O resultado é uma estrutura composta predominantemente por ferrita poligonal e perlita. Com este tratamento, limites de escoamento e resistência à tração mais altos podem ser alcançados essencialmente para aços normalizados apenas por meio de teores de elementos de liga mais altos. Há, portanto, limites nas possíveis combinações de propriedades que podem ser alcançadas na chapa grossa usando este processo. Um estado equivalente pode ser alcançado por meio de laminação normalizada, isto é, laminação com deformação final na faixa de temperatura de normalização.
Uma das variantes da laminação normalizadora é com têmpera e revenimento. Isso consiste em aquecer a placa até a região de austenitização (superior a Ac3) e então a têmpera em água. Este processo é realizado em combinação de forno de rolos e têmpera de rolos, ou de forma estacionária em caixas de têmpera. Devido à taxa extremamente alta de resfriamento da placa, o resultado é uma estrutura dura composta predominantemente por martensita e bainita. A tenacidade da estrutura é aumentada modificando as zonas de martensita originalmente duras e quebradiças por meio de revenimento subsequente (em outro forno de rolos), por exemplo, a temperaturas em torno de Ac1 menos 100 graus C, ou seja, cerca de 600 graus C. Isso dá uma estrutura tratada termicamente com uma combinação de uma dureza ou resistência ao escoamento ainda relativamente alta e resistência à tração com uma tenacidade sistematicamente ajustada. As chapas de aço temperadas e temperadas são usadas principalmente onde os requisitos de resistência ou resistência ao desgaste são especialmente altos.
Outra variante é o rolamento com temperatura controlada. A laminação controlada é amplamente praticada para aumentar a resistência e melhorar a tenacidade do entalhe de chapas de aço. É uma prática de laminação de chapas que adapta o processo de deformação tempo-temperatura controlando os parâmetros de laminação. Os parâmetros de importância primordial são (i) a temperatura para início da laminação controlada na bancada de acabamento, (ii) a redução percentual desde o início da laminação controlada até a espessura final da chapa e (iii) a temperatura de acabamento da chapa. A laminação controlada envolve a deformação em temperaturas de laminação de acabamento muito mais baixas do que a laminação a quente, normalmente na faixa de 705 graus C a 815 graus C. Em contraste, uma prática normal de laminação a quente aproveita a melhor trabalhabilidade a quente do material em temperaturas mais altas . As chapas laminadas a quente são acabadas o mais rápido possível, frequentemente em temperaturas de 1.000 graus C e acima. Para laminação controlada, normalmente é necessário um tempo de espera ou atraso para que a laje parcialmente laminada atinja a temperatura intermediária desejada antes do início da laminação final.
As práticas de laminação controlada (Fig 4) são projetadas especificamente para uso com classes de microligas, que aproveitam a influência do elemento de liga na recristalização e no crescimento de grãos, em combinação com o cronograma de redução específico. Devido a considerações práticas, principalmente a carga do moinho e os tempos de atraso, as chapas laminadas de controle não são normalmente produzidas acima de 25 mm de espessura.
O termo “laminação com temperatura de acabamento controlada” é usado para diferenciar do termo “laminação controlada”. A laminação com temperatura de acabamento controlada é uma prática muito menos severa do que a laminação controlada e visa principalmente melhorar a tenacidade do entalhe para chapas de espessura de até 75 mm. As temperaturas de acabamento nesta prática (em torno de 870°C) são mais altas do que as exigidas para laminação controlada. No entanto, como placas mais pesadas estão envolvidas, os atrasos do moinho para atingir a temperatura desejada ainda são encontrados. Ao controlar a temperatura de acabamento, o tamanho do grão fino pode ser obtido com excelente tenacidade ao entalhe resultante.
O resfriamento acelerado é um ciclo de resfriamento controlado (resfriamento a água a uma temperatura em torno de 540°C a 600°C, seguido de resfriamento a ar) imediatamente após a operação de laminação final (Fig. 4). O resfriamento acelerado após laminação controlada ou laminação com temperatura de acabamento controlada leva a um refinamento estrutural adicional e, portanto, a uma melhor combinação de propriedades. O resfriamento acelerado pode melhorar as propriedades das chapas na faixa de espessura aproximada de 12 mm a 100 mm.
Fig 4 Processos convencionais de laminação, laminação de controle e resfriamento acelerado
No cenário atual, a laminação termomecânica é o processo produtivo mais importante para a fabricação de chapas de alta resistência. Este processo é utilizado para atender a demanda de alto rendimento e outras resistências em tubos de linha de grande diâmetro (baixa espessura de parede e altas pressões de transporte no caso de gás natural), combinado com alta tenacidade a baixas temperaturas e boa soldabilidade. A laminação termomecânica pode ser agrupada sob o termo genérico "Processo de controle termomecânico" (TMCP). A diferença essencial com os outros processos de laminação descritos acima é o fato de que a laminação é usada não apenas como um processo de modelagem, mas também sistematicamente para obter a combinação específica de propriedades exigidas. A laminação termomecânica pode, portanto, ser definida como um processo que visa obter uma estrutura com um tamanho de grão eficaz fino, permite uma combinação favorável de propriedades de serviço e é adaptado à composição do aço. O processo é composto por uma sequência das seguintes etapas controladas em termos de tempo e temperatura.
- O reaquecimento da placa no forno de reaquecimento é com uma temperatura de saída definida.
- A rolagem é baseada em uma sequência de passagem especificada com rolagem de acabamento na austenita não recristalizante ou na zona de duas fases (alfa mais gama).
- O resfriamento é no ar ou na pilha, ou de forma acelerada na linha de resfriamento, até uma temperatura de resfriamento final definida.
- Possivelmente, é feito um tratamento térmico adicional (têmpera).
Esta breve definição precisa de mais explicações. Os benefícios essenciais da laminação termomecânica são baseados nos efeitos da micro-liga, por exemplo, nióbio, que atinge seu efeito total mesmo em níveis de baixo teor de 0,02% a 0,05%. O nióbio retarda ou suprime a recristalização da austenita (reforma dos grãos entre os passes individuais de laminação). O efeito de deformação de um grande número de passes em temperaturas em torno de menos de 850°C é assim acumulado, permitindo a formação de grãos muito finos durante a transformação. Durante o curso do processo, o nióbio forma precipitações de nitreto de carbono que bloqueiam os deslocamentos na rede atômica e, assim, resultam em aumentos no limite de escoamento e na resistência à tração.
Esses dois efeitos do nióbio podem ser explorados por meio da adaptação do processo e permitem reduzir os teores de elementos de liga e o teor de carbono de tal forma que altos valores de tenacidade e boa soldabilidade podem ser alcançados com limite de escoamento e resistência à tração idênticos ou superiores. A exploração de mecanismos de reforço para melhor atingir o perfil de propriedade especificado por meio de "melhoramento de microestrutura" pode ser realizada por meio de uma gama apropriada de equipamentos no laminador. Além disso, neste método, as temperaturas são especificadas e ajustadas exatamente para laminação de acabamento e para resfriamento nos sistemas de resfriamento de placas.
O controle cuidadosamente direcionado dos processos complexos acima requer uma interação próxima entre o equipamento mecânico e os sistemas de automação.
Automação e controle de processos
O laminador de chapas grossas é controlado pelos sistemas elétricos, instrumentais e de automação. Os sistemas elétricos, instrumentais e de automação incluem os sistemas tecnológicos de medição, instrumentos, sistemas sensoriais, sistemas de automação Nível 1 e Nível 2 com modelos de processo e a IHM (interface homem-máquina) para toda a fábrica. A parte elétrica inclui a tecnologia de acionamento completa com transformadores, conversores, acionamentos principais e auxiliares, bem como os motores da mesa de rolos.
Os elementos essenciais para a automação do laminador de chapas grossas são (i) o rastreamento do material desde o forno de reaquecimento até o empilhador de chapas grossas, (ii) o ritmo do laminador para um rendimento ideal, (iii) o cálculo do cronograma de passagem para as bancadas de desbaste e acabamento, (iv) sistemas de controle tecnológico como controle de largura e espessura para as bancadas do moinho, (v) modelo de set-up, controle de volume de refrigerante e mascaramento de bordas para resfriamento de chapas, e (vi) modelo de set-up e ajuste de rolos niveladores hidráulicos para o e niveladores de placa fria (controle de acionamento). Os modelos tecnológicos de processos são cruciais para a produtividade e qualidade do produto. Os principais modelos tecnológicos são o modelo de cálculo de cronograma de passagem, modelo de controle de perfil e planicidade e os modelos de resfriamento e nivelamento.
A operação completa do laminador de chapas grossas é controlada pela aplicação de modelos físico-matemáticos que descrevem com precisão os diversos processos. O rastreamento do material torna a logística dentro da usina, ou seja, desde a laminação até a linha de acabamento, perfeitamente transparente. Combinado com o modelo de cronograma de passagem, bem como o controle de perfil e planicidade, facilita a laminação termomecânica na operação multiplaca. Isso garante alta produtividade do laminador. A mesa de controle do laminador normalmente tem design ergonômico. Os sistemas IHM são organizados para corresponder à visão do operador, dando a ele uma representação orientada para a produção do processo, mostrando todos os sistemas relevantes.
O processo de laminação de chapas passa por várias etapas. Inicialmente, uma placa é reaquecida até a temperatura de recristalização (cerca de 1.200°C) no forno, e é laminada até uma chapa alvo final após várias passagens no laminador de chapas grossas. Então, a microestrutura da placa é controlada pela transformação de fase da austenita durante os processos de resfriamento. Após a extração da placa do forno de reaquecimento, as sequências de operação na seção de laminação são determinadas por um algoritmo de cálculo de passadas, que calcula as sequências de operações de laminação necessárias e prevê as características da chapa após cada passada. Fig 5 shows the rolling sequences in each pass which consists of three steps namely (i) the before calculation step, (ii) the real-time control step (or rolling phase), and (iii) the after calculation step.
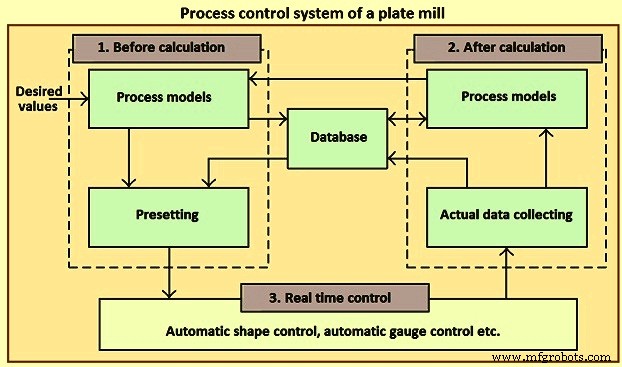
Fig 5 Process control system of a plate mill
The plate rolling process is a complicated process with multiple variables, nonlinearity, and strong coupling. Because of the complexity of rolling environment, such as the changes of material constant, friction coefficient, surface roughness of roller, roll wear, oil film thickness, and lubrication condition, the set calculation results of the rolling force, rolling torque, front slide, and deformation resistance are different from the actual rolling process. The rolling force is the most important equipment parameter and technological parameter of the rolling mill, for it is the important basis of plastic processing technology, equipment optimization design, and process control. The calculation accuracy of the rolling force directly affects the setting accuracy of the rolling schedule. Besides, it is the key to make full use of the regulatory capacity of the thickness and the steel head.
As the conventional rolling force is calculated by the rolling force mathematical model based on experience and statistics, there are some defects in the process of using. Firstly, for the purposes of online control, the general mathematical model is simplified under certain assumptions, so it cannot provide sufficiently accurate predictive value. Secondly, because of the variation of the measurement errors and system characteristics, the parameter errors of model are also great. Therefore, in order to improve the accuracy of rolling force setting, adaptive and self-learning methods based on instant information are used to modify the model.
Rolling schedule plays an important role in the process of plate rolling production. And an excellent rolling schedule is the basic guarantee for the production capacity of rolling mill, for it can improve the quality of products. The medium and thick plate rolling schedule mainly includes the reduction (load) system, the speed system, the temperature system, and the roller type system. Based on the technical requirements of steel, raw material conditions, temperature conditions, and the actual situation of production equipment, rolling schedule design can make artificial calculation or computer calculation to determine the actual reduction, no-load roll gap, rolling speed, and other parameters with the use of mathematical formulas or charts; in the meanwhile, according to the adaptive correction and processing under condition of actual rolling, rolling schedule design can give full play to the equipment potential, increase production, guarantee quality, make operation easy, and make equipment safe.
For the development of the correct rolling schedule, a reasonable reduction (load) distribution is to be determined. Because of the characteristics of the plate rolling, whether it is the traditional optimization method or intelligent optimization method, the whole process of optimization is normally summarized as four steps namely (i) determination of the objective function of rolling load distribution according to the actual production conditions, (ii) determination of the constraint conditions according to the actual production conditions, (iii) choosing of the appropriate optimization method, and (iv) deriving the extreme value of the objective function and obtaining the process parameters when the objective function reaches its extreme value.
Processo de manufatura