Alcoa busca excelência em confiabilidade

Se você não aguenta o calor, é melhor não procurar emprego na fábrica de Metais Primários da Alcoa no sul de Indiana.
Cabos de cubas cuspidoras de fogo e cadinhos cheios de metal derretido podem empurrar a temperatura ambiente do chão de fábrica para quase três dígitos. O calor irradia visivelmente da maquinaria. Riachos de suor escorrem pelas bochechas e costas dos trabalhadores. Pausas frequentes para beber água e Gatorade são uma necessidade.
É um ambiente fisicamente exigente, mas o calor real mencionado no primeiro parágrafo está mais relacionado à posição desta planta em particular na indústria de fundição de alumínio. Este site, parte das enormes operações Warrick da Alcoa, foi construído no final dos anos 1950 e começou a produzir alumínio bruto para a indústria de folhas de latas no início dos anos 1960.
É uma fábrica antiga em uma indústria sensível a idade e tecnologia. Havia 33 fundições americanas operando em 1980. Hoje, são 13. Apenas 6% da capacidade mundial de alumínio será produzida este ano em fundições com mais de 50 anos. O tempo está passando.
Para este estado, adicione:
-
25 por cento da força de trabalho da fábrica é atualmente elegível para aposentadoria por idade ou anos de serviço;
-
os salários pagos pela fábrica estão entre os mais altos do setor; e,
-
há alguns anos, os custos de manutenção dessa fundição por tonelada métrica de alumínio produzida eram os segundos mais altos do sistema Alcoa global.
Você pode sentir o calor? Cada funcionário desta fábrica tem. Mas, em vez de esperar uma morte que parecia iminente, o pessoal de manutenção e operações deu um passo à frente e entrou em ação.
“Temos que engatá-lo se quisermos manter esse padrão de vida e a fábrica viva”, diz o gerente do Alcoa Business System, da fundição, Mark Keneipp. “Esta é a nova realidade. Você apenas tem que lidar com isso."
Tudo começa com uma olhada no espelho.
“Nosso desafio era e é ser competitivo em termos de custos, apesar da nossa idade avançada”, diz Keneipp. “Não estamos mais na frente da curva de idade. Devemos ter um horizonte de 15 a 20 anos para atrair capital dentro da Alcoa. Se for de 25 a 30 anos, isso seria ótimo. Para fazer isso, temos que nos provar continuamente como uma planta enxuta, com custo competitivo, estável e eficiente. ”
Este não é um ambiente para os fracos. Mas, por meio de trabalho árduo e perseverança, as recompensas são amplas.
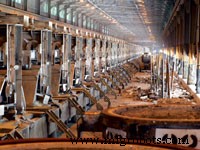
Tempo limite de chamada
Os esforços para sustentar a presença da Alcoa Metais Primários na comunidade de manufatura do sul de Indiana começaram em nível corporativo.
Em 1997, o CEO da Alcoa, Alain Belda, começou a levar os princípios do Sistema Toyota de Produção (TPS) para as 250 unidades globais de sua empresa.
Gerente de produção da fábrica de alumínio Rodney Cunningham (à esquerda), coordenador de processo Larry York e sênior O engenheiro de processos da equipe, Brian Audie, está dentro de um tanque vazio de alumina no terreno das Operações Warrick da Alcoa. O local tradicionalmente usava quatro desses tanques como recipientes para alumina, um ingrediente chave no processo de fundição de alumínio. As iniciativas de manufatura enxuta e o pensamento crítico levaram a fábrica a reduzir o tamanho para dois tanques, economizando uma grande soma de dinheiro para a empresa.
TPS é uma filosofia de manufatura enxuta baseada na produção “just-in-time”, eliminação de desperdícios e solução rápida de problemas. No entanto, a fundição de Indiana fez uma descoberta importante ao implementar o sistema.
“TPS e flow e lean não funcionam se você tiver equipamentos instáveis e imprevisíveis”, diz Keneipp.
A manutenção eficiente, simplificada e econômica da fábrica e a confiabilidade do maquinário devem vir em primeiro lugar.
Para ilustrar seu ponto de vista, Keneipp oferece um diagrama chamado “o iceberg da manutenção”. Acima da água estão os custos diretos de manutenção vinculados a materiais, mão de obra, horas extras, serviços de contrato e despesas gerais e benefícios. Sob a superfície, se escondem os custos indiretos vinculados ao tempo de inatividade, configuração e inicialização, cronogramas perdidos, excesso de estoque, gerenciamento de crise, compras de emergência e um efeito cascata geral na produção.
“Os componentes indiretos são reféns dos equipamentos e processos instáveis de uma planta”, diz ele.
Todo esse desperdício obstrui o sistema e aumenta os custos de operação e manutenção.
O mecânico geral Dick Day liderou iniciativas de organização, padronização e redução de custos no berço de ferramentas centralizado da fábrica .
Em 2002, essa planta de fundição teve custos totais de manutenção superiores a US $ 35 milhões. Sua proporção “dolorosamente alta” de mais de US $ 137 em custos de manutenção para cada tonelada métrica de alumínio produzida (consulte “Apenas os fatos” para tonelagem anual) a coloca em penúltimo lugar entre as usinas de fundição da Alcoa em todo o mundo. A média global em 2002 foi de US $ 90 por tonelada métrica.
Essa fábrica da Alcoa e seus líderes tinham duas opções.
“O gerente da fábrica, Royce Haws, disse que reduziríamos nossos custos. Não era uma opção ficar onde estávamos. Isso ia acontecer ”, diz Keneipp. “Podemos fazer isso da maneira inteligente ou da maneira míope. Quando você fica míope, esses são dias assustadores. É difícil atrair capital para a fábrica para ir atrás das coisas que precisam ser feitas quando você apenas adia a manutenção. Ninguém se sente bem com essa abordagem. Essa é a motivação para as pessoas buscarem algo melhor. ”
Sherman Clark dá uma mão enquanto uma ponte rolante move a parte superior do cadinho no lugar.
Pegando as ondas
Se você ainda não adivinhou, a fábrica da Alcoa escolheu a abordagem inteligente para reduzir os custos de manutenção. Os líderes de manutenção se uniram a consultores da Life Cycle Engineering (LCE) e do Ron Moore Group no início de 2003 para criar uma abordagem chamada Processo de Excelência de Confiabilidade, que foi implantado em três "ondas". O processo é baseado na crença de que uma parceria formalizada e bem definida é imprescindível entre a manutenção e a operação. Nessa parceria, a operação é proprietária do equipamento e tem como principal interesse a confiabilidade. A manutenção é um parceiro igual, dedicado a fornecer métodos, habilidades, experiência e suporte oportunos e eficazes.
“Essa é uma grande mudança”, disse o superintendente de engenharia de confiabilidade Joseph Motz. “Costumava ser um ambiente de silo com muitas acusações.”
O metal fundido é derramado de um cadinho
no Departamento de Lingotes de a fábrica da Alcoa.
Alguns exemplos:
Um operador percebeu um problema potencial. Nenhuma correção foi agendada ou feita. A máquina quebrou. Quem foi o culpado?
Ou a manutenção apareceu para um trabalho de manutenção preventiva de duas horas. Enquanto estava na máquina, ele encontrou problemas adicionais e concluiu o trabalho de PM oito horas depois, impactando assim a produção. Quem foi o culpado?
A resposta nesses casos era tanto a manutenção quanto as operações.
“Tínhamos que perceber que estávamos todos no mesmo time”, diz Motz. “Estamos todos aqui para fazer alumínio. Se seguirmos direções diferentes e não trabalharmos juntos, o processo não funcionará. ”
A Onda 1 na abordagem de três ondas começou em junho de 2003.
“A onda 1 foi Ron Moore”, diz Keneipp. “Nós o trouxemos para falar com os principais líderes da fábrica. Ele desafiou os antigos paradigmas. ‘Você precisa adotar mais uma filosofia de proprietário de ativos.’ ‘Você está desperdiçando dinheiro’. Ele sacode as coisas e abre os olhos. ”
A Onda 2 chegou em agosto com uma avaliação completa de Excelência de Confiabilidade pela LCE. Ao longo de um período de duas semanas, a empresa conduziu longas entrevistas com 90 funcionários de operações e manutenção (horários e salários), bem como com o controlador da planta.
As informações levaram a:
-
uma análise financeira detalhando o valor estimado para fechar as lacunas para a excelência em confiabilidade em comparação com o custo de implementação (apresentado como um cálculo de retorno sobre o investimento);
- um plano mestre preliminar que descreve os processos e metodologias necessários para fechar as lacunas.
“Queríamos olhar nossa condição atual e identificar uma condição-alvo”, diz Keneipp. “A diferença entre os dois é a sua dor ou ganho. Vale a pena o esforço para preencher a lacuna? Tínhamos que provar esse valor para a alta administração. Tínhamos que provar que havia méritos em colocar dinheiro na antiga fábrica.
“Diante de todos os fatos, era prudente conseguir a aprovação do dinheiro o mais rápido possível para prosseguir.”
A onda 3 começou em setembro. Líderes de operações e manutenção:
-
implementou o plano diretor
-
educou todos os funcionários sobre suas novas funções e responsabilidades relacionadas ao aumento da confiabilidade do equipamento
-
conduziu workshops sobre técnicas adequadas de aumento de confiabilidade
-
estabeleceram processos definidos e medidas eficazes de progresso
“Isso não é fácil. Nada disso é ”, diz o gerente de produção da sala de cubas, Rodney Cunningham. “Mas se você tem compromisso de gestão e parceria entre manutenção e operação, suas chances de sucesso aumentam. Sem essas coisas, você não vai conseguir. ”
Elevando a fasquia
O estabelecimento de definições em uma variedade de áreas ajudou a desencadear melhorias. O foco principal foi definir "o que é possível?" e "o que é progresso?"
Uma resposta veio ao aceitar a eficácia geral do equipamento (OEE) como uma métrica chave em toda a fábrica. O OEE rastreia fontes de perda operacional, incluindo disponibilidade, desempenho e qualidade do equipamento, e é expresso como uma porcentagem do desempenho ideal.
“É basicamente definido por algum melhor desempenho anterior”, gerente de produção de eletrodos, Tom Svoboda. “Você viu isso acontecer. Não era fictício ou hipotético. Se o equipamento estava funcionando extraordinariamente naquele mês ou se você estava realmente no topo do processo, aconteceu. A questão é, se você fez isso durante aquele período de tempo, por que não pode fazer isso o tempo todo? ”
Usando uma analogia esportiva para ilustrar a importância do OEE de 100 por cento, se um saltador em altura normalmente pula 6 pés e 6 polegadas, mas estabelece um recorde pessoal de 7 pés, o que especificamente levou a esse desempenho de 100 por cento máximo. Ele treinou de forma diferente? Ele mudou sua dieta antes do encontro? Ele usava sapatos diferentes? Ele literalmente levantou a barra. O que pode ser aprendido e o que pode ser feito para atingir essa marca repetidamente?
A manutenção e as operações trabalharam juntas para definir o desempenho máximo para as funções da planta (por exemplo, montagem do ânodo), processos (descarregamento do minério), resultados (sucata) e peças individuais do equipamento (forno de anel). Ao compilar essas informações, determinou-se que $ 8,3 milhões em economia de custos anuais eram possíveis como resultado do cumprimento das metas de OEE.
Com as informações básicas, os estados atuais foram definidos e as condições-alvo estabelecidas. Atividades - projetos de trabalho utilizando ferramentas de manufatura enxuta, como Kaizen e Melhoria Contínua - ocorreram. O progresso foi medido e analisado. E, benefícios tangíveis foram calculados.
Em 2004, US $ 2,4 milhões em melhorias foram vinculadas aos ganhos do OEE.
Olhar mais a fundo e tomar medidas também resultou na redução dos gastos com manutenção na planta de fundição. No primeiro ano após o início da iniciativa de confiabilidade, as despesas caíram US $ 1,9 milhão, de um valor básico de US $ 32 milhões para US $ 30,1 milhões. Em 2004, o valor caiu mais US $ 700.000. A proporção de despesas de manutenção por tonelada métrica produzida também caiu para US $ 109 em 2004.
O plano ‘planejado’
Um grande esforço também foi feito para definir melhor os elementos de manutenção. Especificamente, neste sistema de confiabilidade liderado pelo operador, "como o trabalho é planejado?" e "como o trabalho é feito?"
“Olhando para trás, estávamos nos enganando pensando que éramos saudáveis”, disse o gerente de manutenção Danny Reyes. “Muitas de nossas métricas antigas estavam fora de alcance. Achamos que nosso ‘percentual de trabalho planejado e programado’ estava em 85 por cento e nosso ‘percentual de conclusão de PM’ estava em 90 por cento. ”
O LCE informou à planta que estava usando as definições erradas.
“A‘ porcentagem de trabalho planejado e programado ’foi realmente apenas‘ porcentagem programada ’. O planejamento era muito limitado”, diz Reyes. “Era o cumprimento do cronograma. Provavelmente 10 por cento desses trabalhos foram planejados. ”
A proporção de 35 para 1 de pessoal artesanal (140) para planejadores (quatro) era o ponto crucial do problema.
“Não funcionou muito bem”, disse o planejador de manutenção Larry McCubbins. “Havia muito pouco tempo para planejar. Você se tornou um planejador, e não muito bom nisso. ”
Um ambiente reativo prospera neste cenário. “Estávamos fazendo a‘ abordagem de manutenção doméstica ’”, diz Keneipp. “É assim que você e eu lidamos com projetos em uma manhã de sábado. É realmente não planejado e ineficiente. ”
Desde então, a planta adicionou três planejadores para um total de sete, proporcionando uma proporção mais gerenciável de 20 para 1.
“Isso permite que esses caras montem, organizem o trabalho, planejem, programem com os centros de produção, certifiquem-se de que todas as peças estejam lá, garantam que o equipamento esteja desligado e que o tempo seja concedido”, diz o superintendente de manutenção da fundição Scott Deon.
Outras chaves para um melhor planejamento:
-
Um documento formal agora descreve os componentes de um trabalho planejado (consulte a barra lateral na página 14). “Os quatro pobres planejadores que tínhamos tentando fazer tudo não faziam as coisas da mesma maneira”, diz Deon. “Esse novo formato agora padroniza a execução do trabalho.”
-
Uma área formal e segura agora é usada pelos planejadores para kits de trabalho. No passado, as peças e os materiais necessários eram despachados aos poucos para um local de trabalho. A pilha pode permanecer por semanas até que todos os itens cheguem. Durante o tempo de espera, não era incomum que peças ou ferramentas fossem movidas, perdidas ou usadas para outro trabalho.
“Conforme o planejador planeja o trabalho, ele encomenda todos os materiais e os entrega aqui , ”Diz McCubbins. “Quando tudo para o trabalho está aqui, nós reunimos em um palete ou dois. O artesanato então vem e leva para o local de trabalho e executa o trabalho. ”
-
Comunicação eficaz.
“Eu costumava pensar que sabia o que as pessoas queriam. Esse processo me ensinou que não ”, diz McCubbins. “Eu não sabia o que eles queriam e o que era certo para eles. No passado, planejava o trabalho e não fazia perguntas. ”
Deon acrescenta:“ Com a responsabilidade compartilhada com a produção, agora sabemos qual trabalho vem primeiro. O proprietário do equipamento deve saber o que é mais crítico. Antes, não acho que estávamos adivinhando. Mas estávamos 100 por cento? Provavelmente não."
-
Reuniões semanais focadas e eficazes.
“Os proprietários de ativos presidem as reuniões e os planejadores / programadores de manutenção da área são facilitadores”, diz Keneipp. “Se for uma reunião de planejamento, discutiremos como faremos isso. Se for uma reunião agendada, nós estabelecemos a programação. ”
Ainda em relação à forma de execução do trabalho, a fábrica tomou medidas para documentar o histórico dos equipamentos e padronizar as instruções das tarefas de manutenção.
“No início, você podia obter registros, mas depois a documentação parou”, diz o engenheiro de energia da estação retificadora Dan Decastra. “Então, criamos um local no servidor e começamos a documentar. Para esta estação, criamos uma lista de ‘bad boy’. Selecionamos os grandes problemas e começamos por aí. Agora, você pode voltar a 2001 e ver um histórico das chaves de ar, contatos, transformadores e skids. ”
Jonathan Fulton, engenheiro de confiabilidade, acrescenta:“Talvez um terço de nossa força de trabalho de manutenção pudesse se aposentar amanhã, se quisesse. Esse é um grande risco potencial para nós. E é difícil conseguir um artesão de qualidade de fora. Para resolver isso, estamos padronizando os processos de trabalho e desenvolvendo o histórico dos equipamentos. Fazendo isso, podemos fazer com que as pessoas com conhecimento técnico possam trabalhar rapidamente. ”
Notas do berço
Um exemplo de melhoria final é como a fábrica definiu melhor quem compra produtos de manutenção e como o dinheiro é gasto em ferramentas e materiais de consumo.
No passado, diversos funcionários de manutenção na usina de fundição compravam ferramentas manuais, ferramentas elétricas, produtos de segurança, produtos de limpeza, produtos de manuseio de materiais e uma centena de outros itens necessários. Os produtos adquiridos eram armazenados em berços de ferramentas descentralizados ao redor da instalação e em uma série de pontos de retenção não oficiais (armários, baús e cubículos).
“À medida que a fábrica foi se expandindo, áreas foram adicionadas. Eles tinham um pequeno grupo e alguém fazia os pedidos e eles juntavam seus suprimentos aqui e ali ”, diz o mecânico geral Dick Day. “Estávamos gastando muito dinheiro tentando alimentar esses berços satélites. Eles não foram gerenciados. As pessoas compravam coisas, mas não eram realmente acessíveis. ”
Se um mecânico precisasse de uma ferramenta específica, ele iria caçá-la. Estava em algum lugar. Se ele não conseguisse encontrar, ele encomendaria um. Essa ferramenta comprada pode desaparecer antes de chegar até ele. Isso levou a gastos desnecessários e redundantes.
Para resolver isso, um berço centralizado foi construído e todos os itens do berço satélite e cubículos foram trazidos para esta área fechada e segura.
Entrou o inútil.
“Percebemos que tínhamos muito material obsoleto - algo para um equipamento que podemos ter retirado há 10 anos”, diz Keneipp.
E, veio o valioso.
“Foi incrível tudo o que saiu da madeira. Alguém trouxe um armário com mais de $ 38.000 em bombas e macacos ”, disse Day, que se tornou o principal atendente do berço central. “Começamos a usar o que tínhamos. Para alguns materiais, não tivemos que pedir nada por um ano. ”
Hoje, Day é responsável pela compra desses produtos relacionados à manutenção. Ele recebe as compras, armazena os itens e os dispensa conforme a necessidade.
“Sabemos o que temos e onde está localizado”, diz ele.
Day também criou um sistema mínimo / máximo para uma variedade de produtos e empreendeu esforços para padronizar as marcas de ferramentas elétricas e suprimentos de soldagem.
“Com as ferramentas elétricas, padronizamos principalmente o DeWalt e estamos investindo fortemente em suas ferramentas sem fio”, diz ele. “Para suprimentos de soldagem, padronizamos nossas pistolas de alimentação de arame e as peças de reposição para essas pistolas.”
Ele faz sua lição de casa e encontra maneiras inovadoras de cortar custos.
Alguns exemplos são:
Luvas :“Costumávamos comprar uma marca de luvas que tinha uma pequena aba por US $ 12 o par. Isso é o que todo mundo ‘tinha que ter’ ”, diz ele. “Você poderia comprar as mesmas luvas com um pouco de elástico por US $ 2,67 o par. As pessoas gostaram deles. ”
Óleo hidráulico :“Nós o compramos por galão por US $ 8 o pop. Comprando a granel, agora economizamos $ 3 por galão. Eu despejo o óleo em potes reutilizáveis que custam 57 centavos cada. ”
Mangueira de acetileno :“Costumávamos comprar pré-embalado em carretel. Agora, nós o compramos em um rolo de 150 metros e cortamos o que a pessoa precisa. Economizamos 25%. ”
Day diz que tudo é bom senso.
“Eu vejo isso como meu dinheiro”, diz ele. “Se este for meu negócio, é assim que eu o administraria.”
Fazendo-os suar
Por meio de trabalho árduo, parceria, propriedade e pensamento inovador, esta unidade de fundição da Alcoa se tornou mais estável, enxuta, previsível, confiável e com custo competitivo.
Os benefícios de custo do OEE são de US $ 4,4 milhões anualizados para 2005 no acumulado do ano, em comparação com o valor da linha de base de 2003.
As despesas de manutenção acumuladas em 2005 são de $ 27,1 milhões anualizadas e refletem uma redução de $ 4,9 milhões em relação ao número da linha de base de 2003.
Os custos de manutenção para o segundo trimestre de 2005 foram de $ 96 por tonelada métrica produzida e as expectativas são de alcançar $ 87 em um futuro próximo.
Uma avaliação de acompanhamento do LCE colocou a planta na categoria de “condições proativas” e o trabalho está em andamento para elevá-la à categoria de “excelência”.
Existe otimismo e ímpeto.
“Quando fui contratado, há 15 anos, dissemos:‘ Somos uma tecnologia antiga. Não podemos competir com algumas das instalações mais modernas '”, diz Fulton. “Para mim, a recompensa é nos ver competir e ter maior eficiência. Estamos produzindo melhor com nossa tecnologia de 40 ou 50 anos do que em locais construídos há 10 ou 20 anos. ”
Embora o calor nunca vá embora completamente para esta planta, ela está fazendo o que pode para fazer a competição suar.
Quais são as características de um trabalho planejado?
-
Há uma estimativa de tempo precisa para o trabalho de forma que o supervisor tenha uma expectativa razoável de quando ele ou ela poderia atribuir a tarefa.
-
Há uma estimativa precisa dos recursos necessários em termos de pessoal de artesanato, peças de reparo / substituição, ferramentas, equipamento de apoio, etc.
-
Todas as informações necessárias (plantas, licenças, relacionadas à segurança, etc.) são obtidas.
-
A sequência de etapas do trabalho, procedimentos e instruções para realizar o trabalho são estabelecidos.
-
Todas as peças e materiais necessários estão equipados.
-
Como uma verificação integrada para garantir um trabalho planejado de qualidade, discuta periodicamente a natureza do trabalho com um supervisor e / ou o artesão designado para concluir o trabalho. Assegure-se de que haja um entendimento completo do escopo do trabalho e que o pacote de trabalho preparado esteja completo.
Manutenção e reparo de equipamentos
- O que é cultura de confiabilidade?
- Qual é a função do engenheiro de confiabilidade?
- Uma revolução de confiabilidade do redemoinho
- Melhor desempenho em manutenção e confiabilidade
- A chave nº 1 para o sucesso da confiabilidade
- Como a Excelência em Confiabilidade acelera os benefícios do Lean?
- Confiabilidade orientada para a família
- Gerenciamento da cadeia de suprimentos:indo além da excelência em confiabilidade
- Por que a excelência em confiabilidade é fundamental para a segurança
- Confiabilidade é uma iniciativa verde