Uma revolução de confiabilidade do redemoinho
A Whirlpool Corporation opera em círculos familiares. Mecanicamente, o funcionamento interno das máquinas de lavar louça e máquinas de lavar desta empresa gira em torno de água e detergente para limpar sua cozinha e bagunça de roupas.
Financeiramente, é uma empresa de US $ 13 bilhões por ano que por décadas ocupou um lugar de prestígio na lista da Fortune 500 (nº 79 no ranking de 2005).
Socialmente, é uma das marcas mais reconhecidas do mundo. E socialmente, tem status de superioridade sobre seus conhecidos companheiros de eletrodomésticos - General Electric, Maytag e Frigidaire.
Familiaridade é um dos maiores ativos da Whirlpool, mas também é um grande desafio.
“O mercado está mudando e sendo liderado por empresas sobre as quais não sabemos tanto”, diz Larry Dunfee, gerente de Manufatura Centrada no Consumidor da unidade da Whirlpool em Findlay, Ohio, a maior fábrica de lava-louças do mundo.
Isso não é spin. Se você ainda não ouviu falar de empresas como Shian Jing, Wenling Changtian e Naiko Asia - fabricantes de eletrodomésticos da China e Taiwan - você ouvirá em breve.
“Estamos acostumados a competir com fabricantes norte-americanos de lava-louças. Nós os conhecemos e eles nos conhecem ”, diz Dunfee. “Todos nós estamos no mercado norte-americano de alto custo de mão de obra. Todos nós podemos fazer melhorias, mas ninguém tem uma vantagem forte sobre os outros. Mas agora, estamos começando a ver outras empresas vindo de países com salários baixos. Eles estão começando a comercializar seus produtos na América do Norte a um preço competitivo. Vemos as possibilidades deles usando a vantagem que têm do ponto de vista do custo do trabalho. Isso nos colocará em uma posição difícil de competir, a menos que façamos as coisas de maneira diferente. ”
A resposta da Whirlpool é uma revolução. Embora ainda consolidada como o jogador número 1 no setor, a empresa agitou as águas e buscou maneiras de:
-
maximizar seus ativos mecânicos; e,
-
maximizar as contribuições de sua força de trabalho.
A revolução resultou em maior tempo de atividade, produtividade e qualidade. Isso impacta positivamente a receita, a lucratividade e o preço das ações.
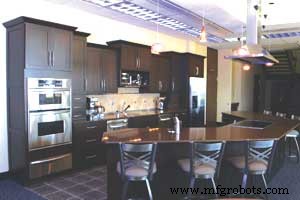
As peças se encaixam
Os 2.000 funcionários da instalação de 1 milhão de pés quadrados da Whirlpool em Findlay, Ohio, não são estranhos aos conceitos de confiabilidade e autonomia da máquina.
O gerenciamento de manutenção, em conjunto com os líderes de produção e operações, introduziu a Manufatura Produtiva Total (TPM) e a Manutenção Centrada na Confiabilidade (RCM) na fábrica em meados e no final da década de 1990. E desde o início, os funcionários do chão de fábrica desempenharam papéis-chave na implementação de projetos de melhoria.
A diferença, comparando 2005 com 1995, é a coesão. As ferramentas de melhoria da Whirlpool agora se encaixam em vez de, em alguns casos, funcionar paralelamente umas às outras. E os trabalhadores de manutenção e produção adotam de maneira mais uniforme a visão de que "todos nós somos responsáveis pelo equipamento".
TPM + RCM =Resultados
TPM (também conhecido como Manutenção Produtiva Total) é uma abordagem baseada em equipe para manter a condição do equipamento. Seus componentes principais são a propriedade do equipamento pelo operador, a identificação e implementação contínuas de melhorias e o desenvolvimento da manutenção planejada.
A Whirlpool coloca aproximadamente 10 operadores de área e pessoal de manutenção em vários turnos em uma equipe TPM. Nos anos de formação do TPM na Whirlpool, uma equipe era liderada por um engenheiro de processo ou supervisor de área. Após receber instruções sobre os princípios de TPM e eficácia geral do equipamento (OEE é uma métrica que rastreia as fontes de perda operacional, incluindo disponibilidade, desempenho e qualidade do equipamento), cada equipe começou a identificar oportunidades em sua área funcional. A equipe então buscou e implementou soluções para eliminar as fontes de perda identificadas.
Hoje, os trabalhadores horistas compartilham papéis de liderança em cada uma das 32 equipes da fábrica. Em outro ponto de partida do passado, o RCM se tornou uma parte importante do currículo do TPM. Todas as equipes agora são expostas antecipadamente a uma análise de RCM.
O engenheiro elétrico Tom Jones (à direita)
trabalha em estreita colaboração com os trabalhadores de produção .
RCM vincula um processo de pensamento estruturado ao conhecimento de uma equipe multifuncional. Em um período de três a cinco dias, a meta é desenvolver uma estratégia completa de manutenção para um processo ou peça de equipamento.
Durante um evento RCM recente, por exemplo, o engenheiro de confiabilidade sênior Richard Word serviu como facilitador de um grupo multifuncional de 12 membros que incluía dois operadores, dois eletricistas, um supervisor de operações, um engenheiro de operações, um técnico de moldagem de plástico, um técnico de qualidade analista de processo, um millwright, um engenheiro de manutenção, um supervisor de manutenção e um representante do fornecedor.
Este grupo analisou meticulosamente os componentes de uma prensa de plástico vertical (trocador de calor hidráulico, válvula de controle de fluxo, cortina de luz, etc.), localizou todos os modos e efeitos de falha e implementou uma estratégia de manutenção para cada componente para tornar a prensa geral mais robusto.
Engenheiro sênior de confiabilidade Richard Word (sentado no meio)
está flanqueado pelos membros de sua equipe RCM recente.
No total, eles seguiram um processo analítico de 14 etapas:
- Revise o histórico operacional do equipamento.
- Detalhe os parâmetros de probabilidade de falha.
- Detalhe os parâmetros de conseqüência da falha.
- Liste as funções principais.
- Liste as subfunções.
- Liste os modos de falha.
- Liste os efeitos da falha.
- Liste o tempo de inatividade.
- Liste a consequência.
- Navegue por uma árvore de decisão.
- Determine a tarefa de manutenção adequada.
- Determine a necessidade de estocar uma peça sobressalente.
- Revise se a análise está completa para o tempo programado.
- Faça uma verificação da realidade.
“O RCM é um bom pontapé inicial para a equipe TPM”, afirma o gerente de manutenção e ferramentas John Siefker. “Eles realmente revisam o processo e o equipamento. É um exercício de aprendizagem de como realmente funciona. Quando você tem um operador ao lado de um técnico de manutenção e um engenheiro, eles começam a conversar sobre os diferentes componentes e o que fazem. Todos fornecem sua perspectiva do mundo real. De repente, as lâmpadas se acendem. Isso dá a todos uma melhor compreensão do processo total e qual é o resultado final. ”
Até o momento, mais de 20 por cento dos trabalhadores da fábrica Findlay participaram de um evento RCM.
Até alguns anos atrás, as análises de RCM funcionavam principalmente de forma independente de outros projetos de melhoria. Em grande parte, eles agora existem para fornecer perspectiva e tarefas de trabalho para equipes de TPM.
A maior parte da implementação do RCM envolve a revisão e a transferência de uma tarefa de manutenção detalhada para o sistema de manutenção preventiva (PM). As tarefas de PM, que costumavam ser de natureza altamente genérica, agora são pesadas em informações. Cada tarefa inclui o status do equipamento (em execução, a qualquer momento ou inativo), um verbo de ação (verificar, medir, inspecionar), o componente específico (motor principal), a condição específica (quantificável sempre que possível) e uma referência a um padrão de monitoramento de condição ( se disponível ou necessário).
A responsabilidade por lidar com essas tarefas de PM é geralmente dividida 50/50 entre os operadores e técnicos de manutenção.
“TPM e RCM não são mais entidades separadas”, diz Word. “Eles sempre se complementaram, mas chegamos ao ponto em que eles se encontram e se cruzam.”
Líderes de fábrica, incluindo gerente de engenharia de instalações
Randy Statzer (à esquerda) O gerente de manufatura, Centrado no consumidor, Larry Dunfee, e o facilitador da TPM, Jim Dray, ajudam a supervisionar o progresso das iniciativas de confiabilidade.
‘Somos todos responsáveis’
Transferir muitas das funções de manutenção para os operadores permitiu que os operadores tomassem mais "posse" do equipamento.
“Originalmente, os operadores pensavam que seu trabalho era fabricar componentes ou montar máquinas de lavar louça”, diz o facilitador do TPM Jim Dray. “Isso mudou. Ressaltamos que você é o responsável pela saúde e produtividade dos equipamentos. É o seu trabalho. É trabalho de todos nesta fábrica. ”
Propriedade significa que os operadores realizam tarefas de PM, como limpeza e lubrificação do maquinário, troca de correias e mangueiras e monitoramento de tiras de calor e fita indicadora. Isso também significa que eles lidam com muitas tarefas de manutenção preditiva.
“Distribuímos algumas armas infravermelhas portáteis. Também temos equipamentos de ultrassom que nossos operadores de configuração de equipamentos podem usar ”, diz Dray.
Tudo isso permite que os técnicos de manutenção se concentrem mais nas atividades que realmente previnem as falhas mecânicas.
“A prevenção está no topo da nossa lista agora”, diz o engenheiro elétrico Tom Jones. “É melhor prevenir o fracasso do que predizê-lo.”
Por exemplo, representantes de manutenção e engenharia trabalham com fornecedores de equipamentos e fornecem ideias, feedback e histórico de desempenho de equipamentos semelhantes atualmente em uso. O resultado final é um equipamento mais robusto e confiável antes mesmo de ser instalado no chão de fábrica da Whirlpool.
Essa relação de compartilhamento continua após a instalação. Por exemplo, um representante da Battenfeld, fabricante de máquinas de moldagem por injeção, atuou no recente projeto RCM.
“Ainda estamos explorando maneiras de alcançar e envolver nossa base de suprimentos”, disse Dunfee. “Esta é uma área de oportunidade.”
Ao se concentrar na prevenção em vez de se estabelecer para a detecção, Word diz que a planta foi capaz de ultrapassar a marca de 90 por cento em tempo de atividade. Além disso, as atividades de manutenção não planejada representaram apenas 13,4 por cento das ordens de serviço documentadas durante um período recente de 30 dias.
Aproximando-se do prato
A prevenção de falhas e a propriedade unificada de equipamentos também são evidentes no impulso da fábrica para desenvolver as habilidades de resolução de problemas de seus trabalhadores. Esta é mais uma prova da natureza integrada das ferramentas de melhoria da Whirlpool.
Os membros da equipe TPM, os mesmos que passam por uma análise RCM, recebem treinamento em conceitos adicionais de “manufatura enxuta”, como Melhoria Contínua. O processo de CI ataca áreas de oportunidade com uma metodologia formal de solução de problemas de sete etapas.
As etapas incluem:
-
Indique o problema inicial (geral, não específico).
-
Esclareça o problema. (Qual é o defeito específico? O que é padrão x real? Qual é o alvo para o problema específico?)
-
Identifique os processos atuais que contribuem para o problema. (Que ação ou ações específicas causaram a condição não padrão?)
-
Identifique a causa raiz do problema. (A causa real costuma estar oculta por trás de sintomas mais óbvios.)
-
Sugira contramedidas para garantir que o problema não aconteça novamente. (Estas são ideias para atacar a causa raiz.)
-
Crie planos para implementar as contra-medidas. (Obtenha o plano de batalha formal para atacar a causa raiz.)
-
Implemente contramedidas e faça um acompanhamento. (As contramedidas foram eficazes? Se sim, continue monitorando e assegure-se de que a solução seja pega. Se não, volte e desenvolva novas contramedidas.)
“Esta é uma abordagem disciplinada para a resolução de problemas, em oposição a atirar na cabeça”, diz Jones, explicando que os métodos tradicionais podem ou não abordar a causa raiz ou podem se concentrar nas questões “triviais” em oposição ao “significativo alguns."
Em uma reunião recente do Comitê de Direção do TPM, as equipes apresentaram estudos de caso sobre como resolveram problemas relacionados a vedações de console não encaixadas, desempenho inconsistente em pistolas de montagem de aparafusamento e visibilidade prejudicada de luzes indicadoras de ciclo.
Esses exercícios de solução de problemas são necessários para que as equipes de TPM obtenham e mantenham um status de certificação da Whirlpool (consulte a barra lateral para obter as diretrizes de certificação).
Além da CI, a planta também incorpora o pensamento enxuto em uma prática chamada caminhadas de “gemba”. (Gemba é um termo japonês que se traduz aproximadamente como "o lugar onde o valor é agregado".) Aqui, líderes de manutenção e produção, trabalhadores horistas e até mesmo o vice-presidente de divisão John Haywood percorrem uma área específica da instalação e identificam áreas de resíduos, atividades sem valor e questões ergonômicas ou de segurança.
A eliminação de resíduos é um grande impulso. Como um sinal na fábrica afirma:“Se não agregar valor, é desperdício! O que você está fazendo para reduzir o desperdício? Você, como cliente, está disposto a pagar por superprodução, estoque, longas trocas, busca de ferramentas / peças, tempo de inatividade não planejado, retrabalho / sucata, longas distâncias desnecessárias ou manter ideias para você? ”
Uma das métricas usadas pela fábrica para registrar os níveis de desperdício é o rendimento do processo crítico. O CPY é responsável por muitas fontes de perdas. Ele começa com uma linha de base da taxa de produção máxima teórica e, em seguida, todas as fontes de perda são calculadas e deduzidas para fornecer a porcentagem da capacidade máxima teórica. Em um alto nível, as fontes de perda incluem disponibilidade, desempenho e qualidade. À medida que o número CPY aumenta, também aumenta a produtividade.
Antes da maturação e coesão das ferramentas de melhoria da Whirlpool, os ativos da planta Findlay produziam de 60 a 70 por cento de sua capacidade. Os benchmarks indicaram que 85 a 90 por cento era possível. Nos últimos anos, a média do CPY da planta aumentou para 79 por cento em 2003, 84 por cento em 2004 e 85 por cento nos primeiros três meses de 2005.
“Se estivermos tomando as decisões certas e fazendo a manutenção certa, tudo se encaixará e teremos algumas garantias”, diz Jones. “Tudo isso coloca menos estresse em mim e em todos os outros.”
Evolução da revolução
Esta fábrica de Findlay, Ohio, é um exemplo brilhante do que pode acontecer quando pessoas energizadas e ferramentas poderosas se unem para impulsionar a melhoria.
A Whirlpool viu os benefícios. Ele sabe que este modelo permite enfrentar melhor os desafios e desafios presentes e futuros. Portanto, está trabalhando para espalhar a notícia. Word está visitando sites irmãos na América do Norte este ano para ensinar estratégias para implementação de RCM. Dray fez o mesmo com o TPM nos anos anteriores.
Em Findlay, porém, ninguém está descansando sobre os louros.
“Quando seu objetivo final é a melhoria contínua, você nunca chega lá”, diz Dray. “É um processo sem fim. Isso é difícil para algumas pessoas. Eles dizem:‘Dê-me um objetivo. Eu vou conseguir. Terminei. O que vem a seguir? 'Com isso, não há fim. ”
Ele simplesmente gira e gira ... como um círculo.
Diretrizes de certificação de TPM
-
Implemente um sistema para medir o progresso da equipe TPM.
-
Limpe e inspecione.
-
Crie uma lista abrangente de peças de reposição e torne-a amplamente disponível.
-
Identifique e documente todos os pontos de lubrificação.
-
Elimine fontes de problemas e áreas inacessíveis.
-
Elabore cronogramas de limpeza, lubrificação e inspeção.
-
Implementar inspeções de negócios qualificados.
-
Defina operador, negócios qualificados e tarefas compartilhadas.
-
Treine operadores e ofícios especializados.
-
Comunique o progresso da implementação a toda a equipe.
-
Procure a melhoria contínua.
-
Revisão de certificação.
-
Certificação.
Manutenção e reparo de equipamentos
- O que é cultura de confiabilidade?
- Qual é a função do engenheiro de confiabilidade?
- A grandeza da confiabilidade é o objetivo da Raytheons
- Planeje um caminho claro para melhorias de confiabilidade
- Melhor desempenho em manutenção e confiabilidade
- A chave nº 1 para o sucesso da confiabilidade
- Vendas centradas na confiabilidade?
- Confiabilidade orientada para a família
- Confiabilidade é uma iniciativa verde
- Revolução Industrial 4.0