Planejamento e programação de manutenção:o novo centro de lucro
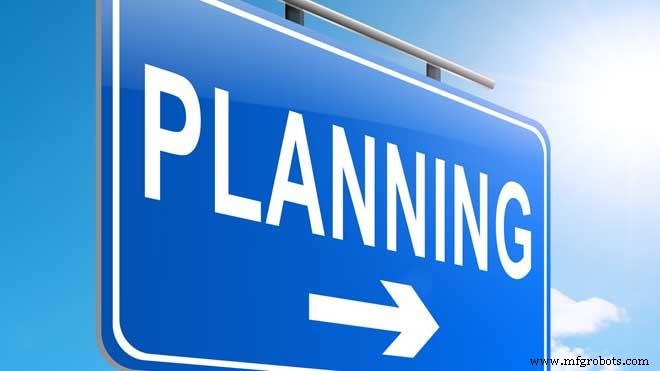
Como indústria, estamos enfrentando circunstâncias muito diferentes das que já enfrentamos. Novos produtores de baixo custo e um mercado mundial cada vez menor deixaram as velhas fábricas dominantes lutando pela sobrevivência. Nenhuma pedra fica sobre pedra na busca de melhorias que permitam a uma usina permanecer economicamente viável nestes tempos difíceis.
Uma área de foco crescente é a manutenção de nossas instalações. No passado, o departamento de manutenção era visto como um "mal necessário". Eles eram os torneiros-chaves caros que se sentavam na oficina e esperavam que o equipamento falhasse. Na história mais recente, estamos encontrando maneiras de prevenir nossas falhas antes que elas ocorram. Ferramentas como análise de vibração, imagem infravermelha, teste acústico e manutenção preventiva nos ajudam a maximizar os lucros, minimizando o tempo de inatividade.
Para realmente realizar esses aumentos potenciais nos lucros, deve-se dar um passo adiante no planejamento e programação da manutenção. Além de identificar falhas em potencial, devemos também concentrar nossos recursos para corrigi-las antes que a falha ocorra. Com a diminuição da força de trabalho e o aumento das responsabilidades daqueles que ficaram nas instalações, a eficiência de nossos recursos torna-se facilmente uma segunda prioridade.
Isso se torna uma ladeira escorregadia à medida que menos trabalho é concluído, mais falhas ocorrem e nosso tempo é gasto reparando as falhas, não em prevenir que elas aconteçam. A única maneira de quebrar esse ciclo é abordar o planejamento e a programação da manutenção como um novo centro de lucro. Para fazer isso, devemos desenvolver uma abordagem nova e disciplinada para identificar, priorizar e concluir o trabalho de manutenção.
A fábrica deve entender que um planejamento de manutenção eficaz e programa de programação produzirá uma força de trabalho mais eficiente e diminuirá o tempo de inatividade geral para manutenção. Isso equivale a maiores margens de lucro para a fábrica e, por sua vez, aumenta a capacidade de sobrevivência da instalação.
O que é planejamento e programação?
O planejamento e a programação são uma abordagem disciplinada para utilizar os recursos de manutenção existentes para reduzir o tempo de inatividade da área e minimizar os custos gerais de produção. Isso é realizado por meio de:
-
Priorizando o trabalho
-
Desenvolver as etapas físicas para concluir o trabalho
-
Aquisição de ferramentas e materiais necessários
-
Agendar o trabalho a ser feito
-
Concluindo trabalho
-
Identificar qualquer trabalho adicional a ser concluído no equipamento
-
Arquivar documentação escrita para o histórico do equipamento
O que isso traz para mim?
A resposta óbvia é melhorar a viabilidade de suas instalações a longo prazo, devido ao custo reduzido associado à manutenção e ao tempo de inatividade do equipamento. Para o homem nas trincheiras, isso geralmente significa muito pouco. Quantas vezes você já foi chamado no meio da noite para vir tratar de uma falha de equipamento? Ou as férias foram canceladas devido a problemas de capacidade de execução? Melhores práticas de planejamento e programação reduzirão a frequência dessas falhas catastróficas.
Olhando no espelho
É muito fácil sentar, fazer o papel de vítima e alegar que não há pessoas suficientes para manter a área funcionando. O fato é que, se você não tem um sistema disciplinado, não sabe quantas pessoas realmente são necessárias para manter seu equipamento.
O primeiro passo para estabelecer um programa eficaz de planejamento e programação é identificar as práticas atuais de planejamento e programação. Isso significa ir para as áreas operacionais e falar com supervisores, planejadores e funcionários horistas de manutenção e operações.
Você provavelmente vai se deparar com muitas frustrações em torno do que está em vigor. Você também terá a oportunidade de ouvir uma infinidade de desculpas explicando por que isso não funciona, mas continue procurando informações para ajudar a construir um sistema de sucesso. Aqui estão algumas coisas que você deve procurar:
-
A sua carteira de trabalhos de manutenção é extremamente grande?
-
Você parece realizar muito pouco com as pessoas que tem?
-
Você tem as mesmas falhas continuamente?
-
Todos os trabalhos são programados usando o método Noah’s Ark? (2x2, dois homens, duas horas; 2x4, dois homens, quatro horas; etc).
-
As peças estão no trabalho antes de ser iniciado?
-
Os funcionários entendem o que se espera deles?
Todos esses são sintomas de um sistema de planejamento e programação que não está funcionando bem.
Fazendo um pequeno morro de uma montanha
Vamos enfrentá-lo, planejamento e programação não é ciência do foguete. O objetivo é concluir as tarefas mais críticas da maneira mais eficiente. Pense nas últimas três vezes em que sua fábrica tentou um projeto de planejamento e programação. Por que falhou? Aprenda com esses erros e siga por um caminho diferente.
Na fábrica da International Paper em Augusta, Geórgia, nossos problemas no passado se concentravam na falta de um sistema escrito e funções e responsabilidades definidas. Assim que o homem com a pasta saiu, rapidamente voltamos ao conforto de como era feito no passado.
Para garantir que a mais nova variação de um programa de planejamento e agendamento permanecesse, tivemos que levar a sério a criação de funções e responsabilidades claras para todos na organização. Isso incluiu todos, desde a mecânica até o gerenciamento superior da fábrica.
Nosso próximo desafio foi garantir que as novas funções se tornassem parte da maneira como fazemos negócios. Isso significava uma abordagem realista do que poderia ser sustentado com nossos atuais níveis de recursos. O sistema também precisava ser flexível o suficiente para acomodar o conjunto de habilidades e os recursos de cada área.
O lançamento (lá vamos nós de novo!)
Quantas vezes você já viu o “programa do mês” falhar quando se deparou com a mentalidade “não isto de novo” da força de trabalho? Já choramos tantas vezes ao implementar esses tipos de sistemas que a maioria da força de trabalho parou de ouvir. Antes de implantar o sistema, certifique-se de documentar por que você falhou no passado e o que fará de diferente para ter sucesso agora.
Para conduzir uma avaliação completa, forme uma equipe multifuncional em torno da fábrica ou apenas conduza algumas pesquisas informais. Descubra qual é a percepção dos sistemas de planejamento e agendamento atuais e anteriores. Faça anotações sobre esses pontos fracos e trate-os especificamente em seu plano de implementação.
Na Augusta, optamos por desenvolver uma equipe multifuncional composta por gerentes de nível médio, supervisores de linha de frente e até mesmo alguns funcionários horistas. Os colaboradores selecionados foram os integrantes mais influentes e respeitados de suas áreas. A equipe foi encarregada pela gerência da fábrica de desenvolver o sistema e um cronograma de implementação.
A implementação incluiu funções e responsabilidades definidas, métricas apropriadas, frequências e agendas de reuniões e planos de sustentabilidade. Tiramos a equipe do local por uma semana e trabalhamos em todo o sistema. Às vezes, havia uma discussão muito acalorada sobre o que funcionaria ou não; mas, no final, chegamos a um consenso sobre o sistema.
A próxima etapa é apresentar as conclusões e planos da equipe para a gerência da fábrica para aprovação. Esta é uma etapa crucial porque sem o apoio da alta administração, o sistema nunca será sustentável.
Em Augusta, não apenas nos reunimos com a equipe de gestão da fábrica e revisamos nossa proposta, mas também fizemos com que cada membro da equipe de gestão assinasse a capa para indicar seu apoio e comprometimento. Isso era algo que nunca havia sido feito no passado e ajudou a definir a expectativa de que o sistema fosse implementado em toda a fábrica.
Uma vez que você tenha um documento acordado sobre como a fábrica irá planejar e programar o trabalho de manutenção, o trabalho real começa! Recursos dedicados serão necessários para implantar o sistema com sucesso. Em Augusta, a equipe de desenvolvimento era responsável pelos rollouts das áreas individuais. Esse foi um dos principais motivos pelos quais selecionamos os membros mais influentes e respeitados de cada área.
Agora que desenvolveram o sistema e criaram propriedade, eles poderiam ser os impulsionadores no nível mais baixo. Os membros da equipe de área realizaram reuniões de meio dia com suas áreas para revisar o sistema, incluindo uma leitura linha por linha do manual e uma seção de perguntas e respostas.
Algumas questões tiveram que ser apresentadas à equipe como um todo para obter uma decisão consensual, mas a maioria foi tratada no documento tal como estava. No final, descobrimos que essa é uma forma muito eficaz de manter a integridade do sistema em toda a fábrica.
Sustentabilidade:Mudando sua cultura e lucros
Assim que o sistema for implementado, o foco principal deve ser a sustentabilidade. Os primeiros seis meses são o prazo crucial para estabelecer uma base na cultura da fábrica. Cada área deve sentir uma presença constante para garantir que o sistema se torne uma segunda natureza. Em Augusta, a equipe de implantação foi encarregada de participar de pelo menos uma reunião diária para cada área uma vez por semana. Também realizamos reuniões mensais da equipe para discutir questões e avanços.
Ao compartilhar aberta e regularmente, pudemos tomar decisões sobre o andamento do sistema. Também ajudou os membros da equipe a ficarem cientes de como o sistema estava progredindo e até inspirou alguma competição entre as áreas para tentar ser o melhor.
Como outra forma de garantir a sustentabilidade, instituímos auditorias de sistema pela equipe de gestão da fábrica. Desenvolvemos uma lista de verificação de perguntas que devem ser respondidas ao participar de uma reunião de planejamento e outra lista de verificação para ajudar a identificar trabalhos bem planejados na carteira. Isso se torna uma ferramenta real quando você vê uma área começando a deslizar um pouco.
É sempre incrível ver um grupo perceber quando o gerente da fábrica entra em uma reunião de planejamento de nível inferior apenas para ver como as coisas estão indo. Algumas perguntas bem colocadas sobre alguma parte do sistema que está faltando sempre ajudam muito a mostrar à equipe que as expectativas são reais e serão seguidas.
Por fim, desenvolvemos métricas para medir o impacto do sistema. A equipe de implementação manteve um scorecard da área com métricas acordadas para medir a utilização do sistema em toda a fábrica. Eles eram obrigados a trazer essas métricas para uma reunião de gerenciamento da fábrica e discutir os resultados mensalmente. Assim como as auditorias, isso ajudou muito a manter os membros da equipe na busca ativa das metas que estabelecemos.
Também adicionamos algumas dessas métricas aos scorecards de todos na fábrica. Augusta usa o scorecard como uma ferramenta de discussão para análises individuais mensais entre os funcionários e seus supervisores diretos. Essas métricas mantiveram as metas de planejamento e programação à sua frente e afetaram diretamente os aumentos por mérito no final do ano.
Preguiça, a VERDADEIRA mãe da invenção
Depois que seu sistema for implementado e as pessoas entenderem que ele não vai desaparecer, você verá que coisas incríveis começarão a acontecer. As pessoas adaptam o sistema e começam a encontrar formas de torná-lo mais fácil de usar em suas áreas. Você verá um cruzamento de responsabilidades e os membros da equipe aprimorarão o sistema para tornar seu trabalho mais fácil.
Por exemplo, um planejador de Augusta decidiu que, nas paralisações, ele iria a campo e marcaria cada trabalho com uma etiqueta de papel que identificava os mecânicos atribuídos ao trabalho, onde as peças estavam localizadas e quaisquer notas específicas para o trabalho. Isso ajudou a reduzir a “corrida matinal” de um desligamento quando os supervisores estão correndo para colocar os mecânicos em seus respectivos trabalhos e responder a quaisquer perguntas.
Os mecânicos horistas deram um feedback muito positivo sobre o sistema e até deixaram notas nas etiquetas de papel com o que encontraram e o trabalho de acompanhamento necessário. Exemplos como esse foram vistos em toda a fábrica, uma vez que cada área assumiu a propriedade do sistema e se tornou parte da cultura cotidiana.
Assim que começar a ver as pessoas levando o sistema para o próximo nível, você terá sucesso em sua implementação inicial. Agora é hora de começar de novo. Olhe novamente no espelho, encontre seus pontos fracos e concentre-se em maneiras de continuar a melhorar. Aqueles que não continuarem a melhorar serão deixados para trás.
Os conceitos de um sistema eficaz de planejamento e programação já existem há anos. A tarefa hoje é desenvolver e implantar com sucesso um sistema que se tornará parte da maneira como sua fábrica faz negócios nos próximos anos. Em um mundo onde apenas os fortes sobrevivem, é imperativo que nos concentremos nos custos que estão sob nosso controle. Ao mudar a percepção de que o planejamento e a programação são apenas um exercício de futilidade para um centro de lucro que pode realmente reduzir o custo da fábrica por tonelada, você ajudará a garantir que sua fábrica continuará a sobreviver.
Sobre o autor:
Chris Hykin é o diretor de confiabilidade orientada pelo operador da International Paper em Augusta, Geórgia.
Manutenção e reparo de equipamentos
- O lado desconfortável, imprevisível e aleatório da manutenção
- Reuniões matinais:planejamento e programação de manutenção
- Siga estes princípios de planejamento e programação
- A necessidade de programação de manutenção
- Trabalho em equipe, planejamento e programação
- Deming, Drucker e um caso para planejamento e programação
- A morte do departamento de manutenção e o que podemos fazer a respeito
- UT renomeia o programa como Centro de Confiabilidade e Manutenção
- Extensão de controle para planejadores de manutenção e outros
- Manual de planejamento e programação de manutenção 4ª edição