Um guia do gerente de manutenção para criar e usar FMEAs
Um violento ataque de ransomware atingiu a cidade de Atlanta em março de 2018. Acabou sendo uma das violações mais caras da última década. Os serviços públicos foram interrompidos. Os departamentos foram forçados a fazer a papelada essencial manualmente. E custou ao governo municipal US $ 17 milhões.
Quando a poeira baixou, uma coisa ficou clara:a cidade não estava preparada para esse desastre. Uma auditoria feita dois meses antes da violação encontrou 2.000 vulnerabilidades no sistema de TI da cidade. Foi um bom passo, mas era muito pouco, muito tarde.
O que aconteceu em Atlanta é um conto de advertência com uma grande lição - o risco nunca pode ser eliminado, mas pode ser administrado. Isso é especialmente verdadeiro na manutenção. A falha do equipamento é inevitável. Mas saber como reduzir a probabilidade de falha e como reagir quando isso acontecer é fundamental para o sucesso.
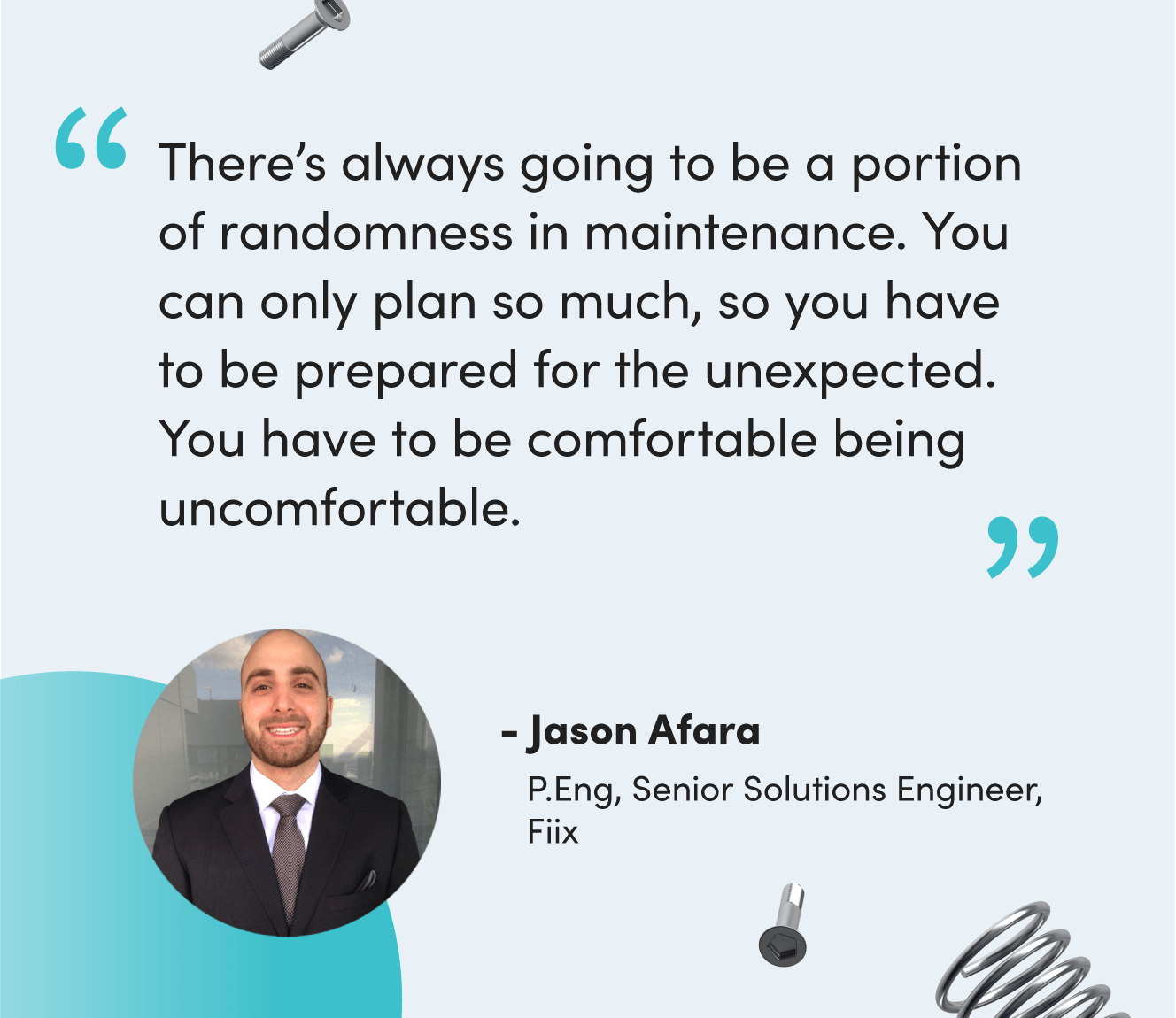
Uma análise de efeitos e modos de falha (FMEA) é uma ferramenta para compreender e antecipar falhas, de forma que você possa limitar seu impacto. Neste artigo, você aprenderá:
- O que é um FMEA
- Os diferentes tipos de FMEAs
- Como criar um FMEA
- E como as equipes de manutenção podem usar um FMEA
O que é FMEA?
Uma análise de efeitos e modos de falha, ou FMEA, identifica e documenta todas as maneiras pelas quais um equipamento pode falhar e o impacto potencial dessas falhas. Descreve:
- Modos de falha para componentes individuais
- As consequências do fracasso na produtividade e segurança
- Um plano para prevenir ou reagir a esses problemas
Construir FMEAs é um componente chave da manutenção centrada na confiabilidade (RCM).
Existem três objetivos principais de um FMEA:
- Evite quebras futuras, reduzindo a probabilidade de falhas comuns e críticas usando manutenção planejada e procedimentos operacionais padrão
- Reduza os tempos de resposta, diminua o tempo de inatividade e melhore a saúde e a segurança quando ocorrer falha de ativo
- Priorizar a manutenção preventiva e corretiva em situações não emergenciais
Quais são os diferentes tipos de FMEA?
FMEAs podem ser categorizados em subtipos com base no tipo de risco que estão avaliando e no impacto que têm. Aqui está um rápido resumo de cada tipo de FMEA:
- FFMEA (modo de falha funcional e análise de efeitos) :Um FFMEA analisa os riscos que afetam o funcionamento de um sistema. O objetivo de um FFMEA (às vezes chamado de modo de falha do sistema e análise de efeitos) é prevenir essas falhas antes que aconteçam.
- DFMEA (modo de falha de projeto e análise de efeitos) :Um DFMEA avalia os riscos de um ativo na fase de projeto. O objetivo desta análise é encontrar e corrigir possíveis problemas com um ativo antes de ser implantado para aumentar sua confiabilidade, reduzir a quantidade de manutenção necessária e estender o ciclo de vida do ativo.
- PFMEA (modo de falha de processo e análise de efeitos) :Um PFMEA busca possíveis falhas em um processo. A diferença entre um PFMEA e outros tipos de FMEAs é que ele se concentra no que pode dar errado durante a operação e manutenção de um sistema.
- FMECA (modo de falha, efeitos e análise de criticidade) :Um FMECA (ou análise de criticidade) analisa os modos de falha e o nível de risco associado a esses modos de falha.
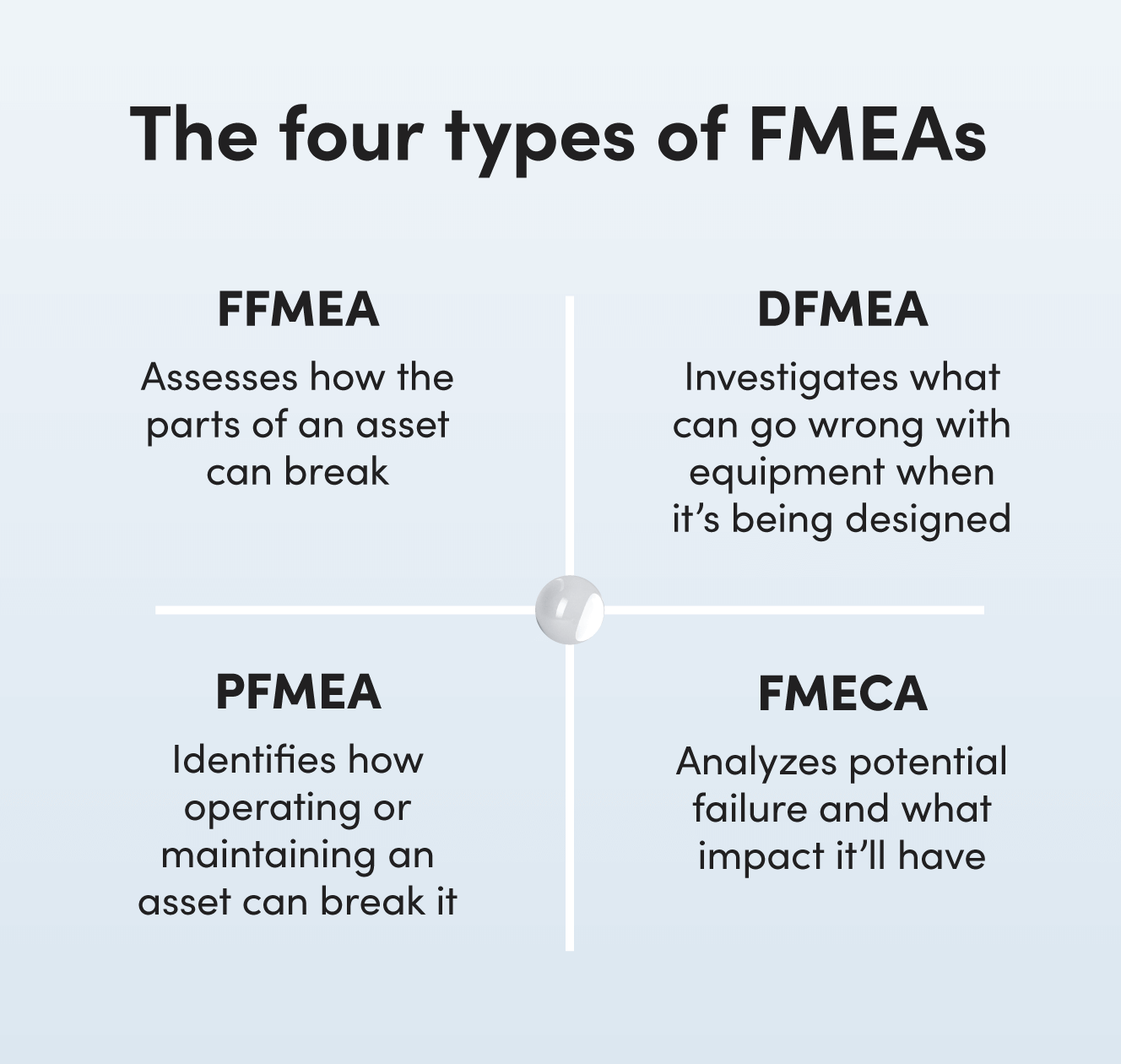
Qual é a diferença entre um modo de falha e um código de falha?
Um modo de falha é um erro ou defeito que causa mau funcionamento do sistema. Um exemplo de modo de falha em um transportador de transferência de velocidade variável pode ser um rolamento emperrado. Um rolamento quebrado fará com que o transportador diminua a velocidade ou pare de funcionar.
Um código de falha é um modo de falha representado por uma etiqueta alfanumérica. Os códigos de falha são frequentemente usados no software CMMS como uma forma de transmitir informações rapidamente e classificar ou relatar falhas. Os códigos de falha geralmente são suportados por três informações contextuais. Um exemplo de código de falha é parecido com este:
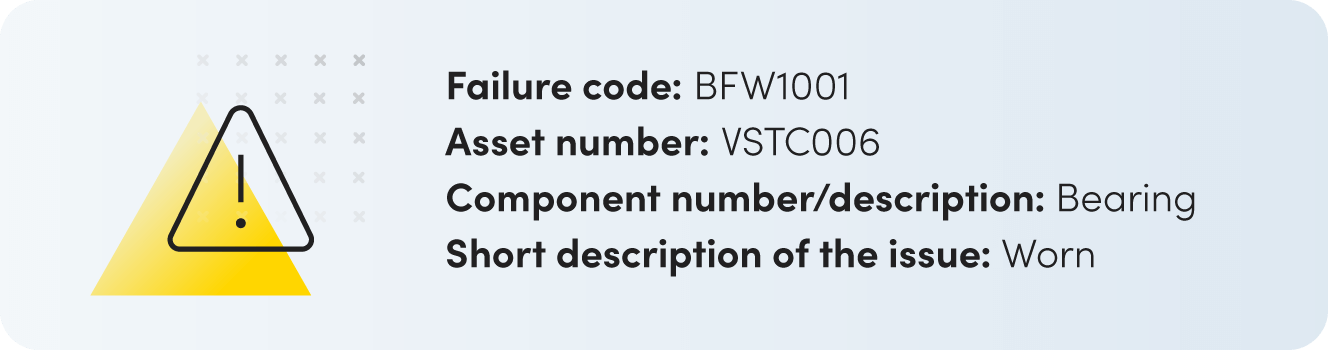
Qual é a diferença entre FMEA e FRACAS?
Uma análise de efeitos e modo de falha descreve uma possível falha, suas causas e seu impacto. É um processo que lista possíveis incidentes futuros e suas prováveis causas raiz. É uma medida proativa.
Um sistema de relatório de falha, análise e ação corretiva (FRACAS) é um sistema de relatório de circuito fechado que analisa falhas que já ocorreram. Ele examina as falhas do passado para descobrir por que aconteceram e qual o impacto que tiveram para que possam ser evitadas no futuro. É uma medida reativa.
Criar FMEAs para manutenção é uma parte fundamental da construção de um FRACAS. Na verdade, é a primeira etapa do processo. Um FMEA é uma linha de base para falhas, bem como para o desempenho da equipe e do equipamento. Você pode basear decisões, como quais relatórios criar ou quais falhas direcionar, com base nessas informações.
Como você pode usar FMEAs para manutenção
Existem três maneiras principais pelas quais as equipes de manutenção podem usar um modo de falha e análise de efeitos:
- Para criar um cronograma de manutenção preventiva que reduza a probabilidade de falha do ativo e otimize os recursos
- Para se preparar para a manutenção de emergência para que os ativos possam ser reparados rapidamente e o tempo de inatividade possa ser minimizado
- Para priorizar a manutenção corretiva e o backlog de manutenção
Usando FMEAs para construir um cronograma de manutenção preventiva
Existem três maneiras de usar FMEAs para executar um programa de manutenção preventiva de classe mundial:
- Crie novas tarefas de manutenção preventiva
- Priorize a manutenção preventiva
- Otimize a manutenção preventiva
Baixe este modelo para criar um cronograma de manutenção preventiva
A primeira etapa na criação de um programa de manutenção preventiva é entender quais falhas podem ocorrer e com que frequência. Um FMEA descreve essas informações. Por exemplo, se um novo ativo está sendo projetado, um FMEA permite que você descubra quais PMs são necessários para evitar possíveis modos de falha e com que frequência eles precisam ser feitos. Isso permitirá que você mapeie as entradas que vão para a criação de novos PMs, incluindo quem será atribuído ao trabalho, o que irá desencadear o trabalho, quanto custará e quanto tempo levará.
O sucesso de seu programa de manutenção preventiva depende de quantas falhas você encontra e interrompe e do impacto dessas falhas. Se você evita 100 pequenas avarias, mas não detecta as cinco ou seis falhas que custam milhões de dólares à sua empresa, seu programa falha. Um FMEA tem todas as informações de que você precisa para priorizar os PMs e direcionar as avarias mais prováveis e perturbadoras.
Embora FMEAs forneçam uma linha de base para a criação de um cronograma de manutenção preventiva, seus planos não durarão para sempre. Sua operação está mudando o tempo todo. Sua programação de PM precisa mudar com isso. Usar ordens de serviço e históricos de reparo para atualizar FMEAs ajuda a otimizar sua programação e manter o ritmo com outras mudanças. Por exemplo, um modo de falha pode não acontecer com a frequência que você previu. Esses dados podem levá-lo a reduzir a frequência da MP destinada a evitar esse modo de falha. Você pode então colocar esses recursos em outra tarefa de manutenção.
Usando FMEAs para se preparar para a manutenção de emergência
Nenhuma quantidade de manutenção eliminará totalmente a falha. O melhor que você pode fazer é planejar as avarias de alto risco e alto impacto para que sua equipe possa consertá-las em uma hora em vez de duas. Um FMEA é uma ferramenta valiosa para implementar essas medidas de emergência.
Comece observando as falhas que têm o maior impacto e acontecem com mais frequência. Nessa lista, escolha os modos de falha que são difíceis de detectar. Você vai acabar com modos de falha que são difíceis de detectar e causam a maior bagunça. Elabore um plano de resposta de emergência para essas avarias.
Seu plano de resposta a emergências deve incluir qualquer informação que reduza os tempos de resposta e reparo. Deve também levar em consideração a saúde e a segurança. Isso pode incluir o seguinte:
- Peças do kit para reduzir o tempo gasto na recuperação de peças sobressalentes essenciais e equipamentos de proteção pessoal (Baixe um modelo de kit de peças)
- Criação de uma lista de tarefas detalhada ou dicas para solução de problemas
- Anexar diagramas, manuais, fotos e outros recursos visuais a ordens de serviço
- Descrever uma lista de técnicos ou empreiteiros que podem concluir o reparo
- Estabelecer uma maneira de se comunicar com os técnicos rapidamente, como o software CMMS
Usando FMEAs para priorizar a manutenção corretiva e carteira de manutenção
Detectar falhas precocemente é útil, mas não significa nada se você não tiver um processo para corrigir essa falha de forma rápida e eficaz. Um FMEA o ajuda a construir esse processo.
A primeira etapa é identificar os modos de falha com uma pontuação de severidade alta (ou seja, ativos que custarão mais à sua empresa se forem desativados). A ação corretiva deve ser realizada neste equipamento o mais rápido possível. Essa lista permitirá que você crie materiais de treinamento e planos de resposta para que todos saibam como reagir a falhas.
Você pode empregar uma abordagem semelhante ao priorizar o backlog de manutenção, exceto por uma etapa extra. Depois de classificar o trabalho adiado por gravidade, observe o trabalho restante por frequência de falha. Compare isso com o atraso do trabalho. Se um modo de falha tiver uma taxa de frequência excedendo o número de inspeções perdidas, esse trabalho deve ter prioridade, pois a probabilidade de falha é maior.
Este modelo gratuito ajudará você a priorizar sua carteira de manutenção
Como criar um FMEA
O modelo FMEA abaixo o ajudará a identificar o risco em sua operação e tomar medidas para evitá-lo.
Baixe seu próprio modelo FMEA aqui
Mas primeiro, veja como obter dados para seu FMEA
Bons FMEAs dependem de bons dados. Sem dados, você construirá seu programa de manutenção com base em suposições e suposições. Mas como você encontra as informações necessárias para um FMEA? As três fontes abaixo fornecem uma ótima base:
- Diretrizes do OEM:este é o seu ponto de partida. Estas diretrizes fornecem uma linha de base para o preenchimento de um FMEA se você não tiver outros dados.
- Entrevistas com operadores e técnicos:aproveite a experiência de quem trabalha com equipamentos todos os dias. Eles fornecerão informações que você não encontrará em nenhum outro lugar, como se um componente precisa de duas vezes mais lubrificação do que o sugerido ou se a frequência de uma falha aumentou porque as especificações da máquina mudaram.
- Dados da ordem de serviço:suas ordens de serviço revelam o desempenho do equipamento e são uma grande fonte de informações para ajustar e melhorar seus FMEAs. Procure por falhas comuns, quais ações foram tomadas para encontrar e corrigir a causa raiz, o que atrasou um reparo e como foi fácil detectar uma falha.
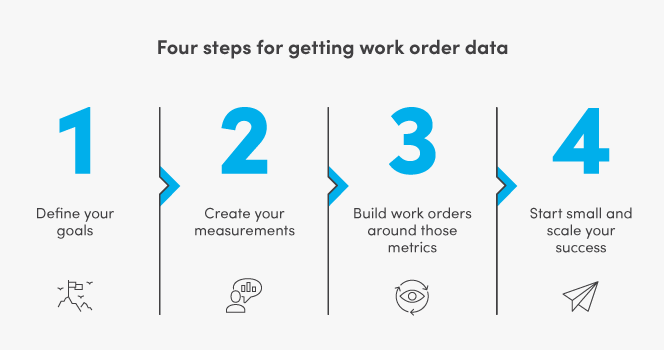
Nenhuma dessas fontes funciona sozinha. Combine-os para obter uma imagem completa de como seu equipamento opera, como ele pode falhar, o impacto da falha e o que deve ser feito a respeito.
Um modelo FMEA
1. Identifique os componentes do ativo
Documente cada componente do ativo que pode quebrar ou degradar. Por exemplo, os componentes de uma linha de engarrafamento podem incluir caixas de engrenagens, motores, rodas dentadas, rolamentos e bicos.
Comece com seu equipamento mais crítico e comece a partir daí. Este é um ótimo momento para criar convenções de nomenclatura claras e uma hierarquia de ativos, caso ainda não tenha.
2. Identifique os modos de falha em potencial
É hora de identificar como esses componentes podem falhar. Se um único componente tiver vários modos de falha, liste cada modo de falha de acordo. Por exemplo, os modos de falha de um rolamento podem incluir desalinhamento, corrosão ou contaminação.
3. Liste os efeitos potenciais da falha
Descreva o resultado de uma falha e como isso afeta a produção e a segurança da equipe. Por exemplo, um rolamento desalinhado desligará uma linha até que ela possa ser substituída (cerca de três horas), com uma perda potencial de 1.800 unidades.
4. Pontuação de gravidade
Esta é uma medição do impacto de uma falha na produção e segurança. É pontuado em uma escala de 1 a 10, sendo 1 um evento de baixo impacto e 10 um evento de alto impacto. Considere o estado do ativo ao pontuar. Por exemplo, um carro com pneu estourado em baixa velocidade terá problemas menores de direção, mas um vazamento em alta velocidade é muito mais perigoso.
Comece a calcular a pontuação de gravidade de um ativo com este modelo de análise de criticidade
5. Liste as causas potenciais
Liste todos os motivos possíveis para a ocorrência de uma falha. Vá além de uma causa direta. Por exemplo, um rolamento corroído pode acontecer porque os suprimentos estavam etiquetados incorretamente ou as instruções não eram claras, levando à lubrificação inadequada.
Chegue ao fundo da falha com este prático (e gratuito!) tempalte de análise de causa raiz
6. Pontuação de frequência esperada
Esta é uma medida de quão comum é um modo de falha. É pontuado em uma escala de 1 a 10, onde 1 representa um evento que ocorre raramente e 10 representa um evento que ocorre com muita frequência.
7. Liste os controles de processo atuais
Documente todas as medidas em vigor para prevenir ou detectar uma falha. Os controles de processo podem incluir inspeções de manutenção preventiva semanais, substituições mensais de peças e o uso de sensores para detectar níveis perigosamente altos de vibração.
8. Pontuação de detecção
Esse número determina como é fácil detectar um problema antes que ele cause uma falha total. É pontuado em uma escala de 1 a 10. Uma pontuação de 1 é dada a um evento que nunca pode ser detectado. Uma pontuação de 10 é atribuída a um evento que pode ser detectado quase todas as vezes. Por exemplo, um pneu furado às vezes pode ser detectado em seus estágios iniciais, então ele teria uma pontuação de 5. Um pára-brisa lascado é muitas vezes causado por eventos imprevisíveis, o que significa que é difícil de detectar e receberia uma pontuação de 9.
9. Número de prioridade de risco
O número de prioridade de risco calcula os modos de falha que têm o maior impacto e são os mais evitáveis. Para encontrar o RPN, multiplique as pontuações de gravidade, frequência e detecção. Por exemplo, se um modo de falha tem uma pontuação de gravidade de 8, uma pontuação de frequência de 5 e uma pontuação de detecção de 10, o RPN seria 400. Quanto maior o número, mais recursos devem ser colocados na prevenção dessa falha.
10. Determine a ação recomendada
Estabeleça um plano para reduzir a probabilidade de falha ou aumentar as chances de detecção precoce. Isso pode incluir aumentar a frequência de PMs em um componente ou investir em equipamentos de monitoramento de condição.
Como gerenciar FMEAs
FMEAs são documentos vivos que devem ser regularmente revisados e atualizados. Aqui estão alguns eventos que podem desencadear uma revisão de um FMEA:
- Um novo ativo é projetado ou instalado em suas instalações
- Um novo técnico ou operador se junta à equipe
- Uma alteração é feita no modo de operação da máquina (ou seja, ela é executada com mais frequência ou as especificações mudam)
- Um modo de falha está ocorrendo com mais frequência
- Uma nova tecnologia é implementada para ajudá-lo a detectar ou prevenir falhas mais facilmente
- You find a new failure mode or reason for an existing failure
- The impact of failure changes (ie. a new product using more expensive material is being produced)
Both maintenance and operations staff should be involved in modifying and adding to a failure mode and effects analysis. The diversity of perspectives and experiences with equipment helps to avoid gaps in your FMEAs.
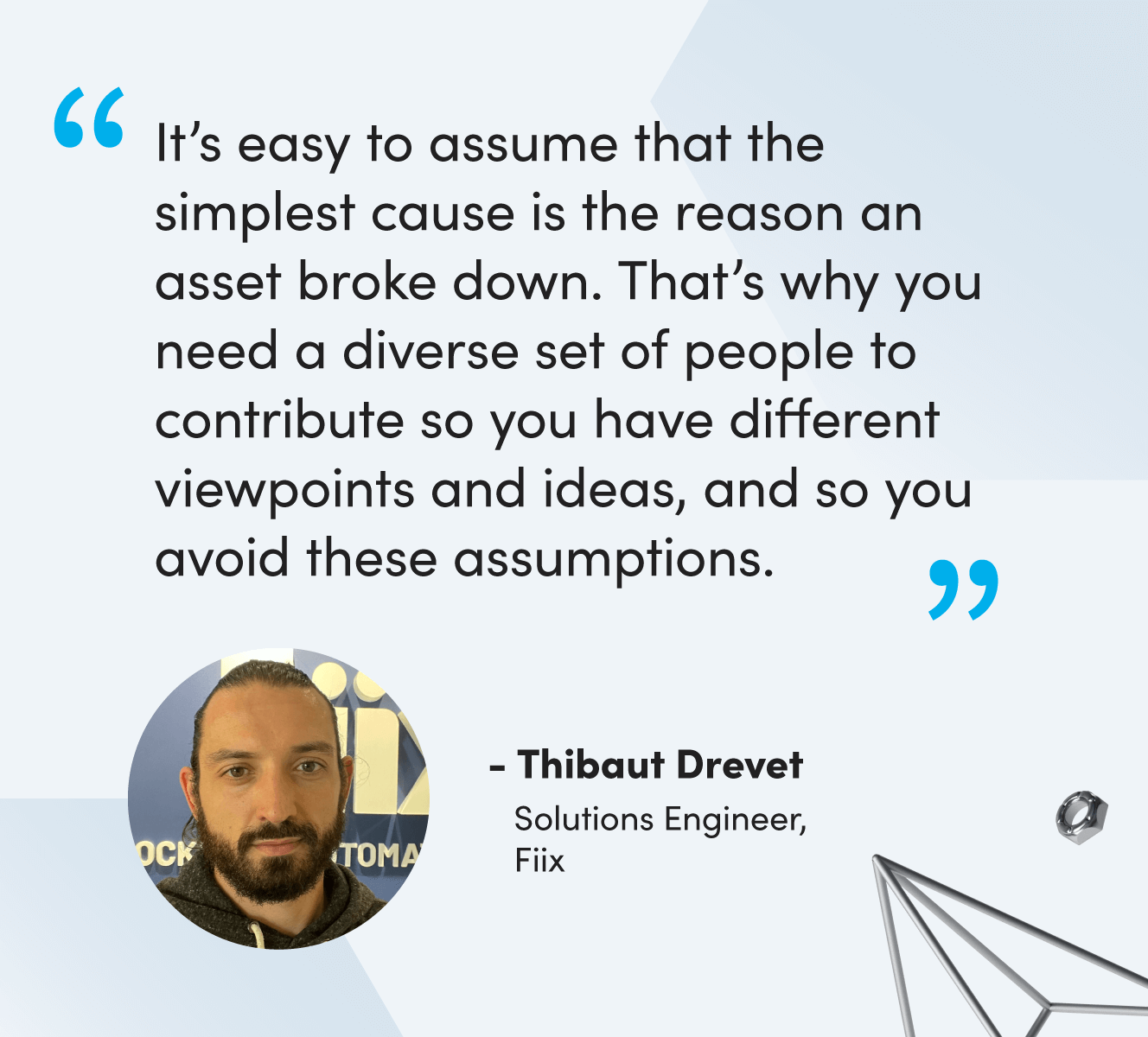
FMEAs are a long-term investment in success
A failure mode and effects analysis is not a band-aid fix or a troubleshooting tool. It’s a continuous activity with the goal of preventing failure where possible and mitigating its effects when it’s not. It’s a planning resource and a safeguard against financial loss and safety risks.
While creating FMEAs involves a considerable time investment, it will pay you back in the long term by helping you plan ahead, prevent reactive maintenance, and track team success.
Manutenção e reparo de equipamentos
- Como manter a manutenção em modo proativo
- Guia rápido para desenvolvimento e execução de PM
- Melhor desempenho em manutenção e confiabilidade
- Detalhes são importantes na manutenção e confiabilidade
- Mantenha a manutenção simples:use os sentidos e a sensibilidade
- 5 causas de falha do equipamento (e o que você pode fazer para evitá-lo)
- Tempo é dinheiro:dicas para usar software de manutenção para economizar tempo e gastar com mais eficiência
- Simplifique o relatório de falhas na manutenção
- Um guia para manutenção e peças de teleférico
- Seu guia para operação e manutenção de guindastes