Tipos de manutenção:uma comparação
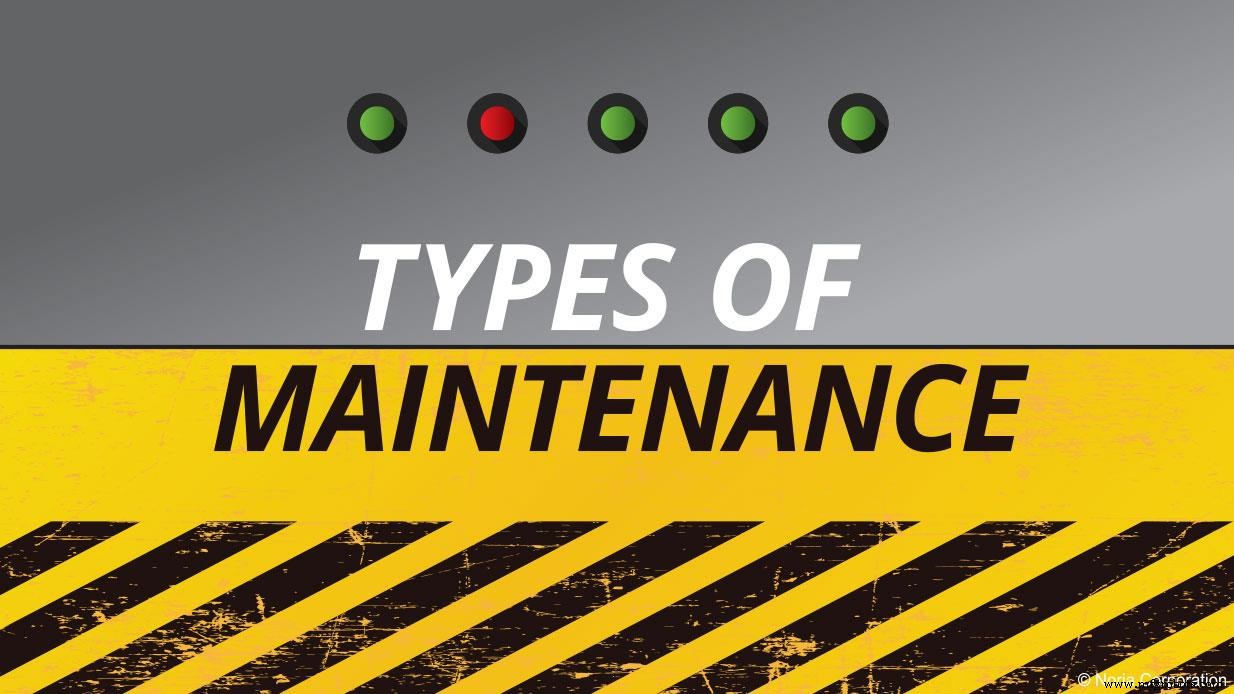
Tipos de manutenção
É bem sabido que bilhões de dólares são perdidos a cada ano devido ao tempo de inatividade não programado e à baixa qualidade dos ativos. Em uma batalha sem fim para combater essa estatística, as organizações implementam um dentre uma variedade de tipos de manutenção, geralmente combinando dois ou mais. As definições dos tipos de manutenção variam em todo o setor, o que pode tornar bastante confuso diferenciar itens como manutenção preventiva e preditiva, entre outros.
A maioria dos tipos de manutenção se enquadra em duas categorias principais:preventiva e corretiva. Manutenção preventiva é quando você inicia tarefas e planos de manutenção de forma proativa para evitar a ocorrência de falhas. Além de prevenir falhas, a manutenção preventiva pode ter o objetivo de minimizar a (s) consequência (s) da falha ou determinar o risco da falha acontecer.
Manutenção corretiva acontece depois que a falha ocorreu. Sua equipe está basicamente colocando o ativo de volta em funcionamento neste ponto. Para esclarecer, a manutenção corretiva pode ser deliberada na forma de uma estratégia de manutenção executar até a falha, que será discutida abaixo.
Vamos examinar os tipos mais comuns de manutenção usados nas indústrias de manufatura e de processo.
- Manutenção preventiva. A manutenção preventiva é uma rotina estabelecida de inspecionar o equipamento periodicamente, perceber pequenos problemas e corrigi-los antes que se transformem em problemas maiores. O principal objetivo da manutenção preventiva é o tempo de inatividade zero. Essa meta é buscada por meio de três objetivos:aumentar a vida produtiva do equipamento, reduzir as quebras críticas do equipamento e minimizar a perda de produção devido à falha do equipamento.
Existem alguns tipos de manutenção que se enquadram na categoria de manutenção preventiva. Esses incluem:
- Manutenção baseada no uso, que usa gatilhos com base no uso real de cada ativo. O rastreamento do uso de ativos com monitores de equipamentos permite que os gerentes de manutenção estabeleçam um cronograma de manutenção preventiva de acordo com os parâmetros predefinidos.
- Manutenção prescritiva assemelha-se muito à manutenção preventiva, mas aproveita o software de aprendizado de máquina, como inteligência artificial (IA) e a Internet das coisas (IoT), para ajudar a agendar tarefas de manutenção preventiva.
Para uma análise aprofundada dos tipos de manutenção preventiva, como projetar um programa de manutenção preventiva, ferramentas de manutenção preventiva e muito mais, verifique o link no início desta seção.
- Manutenção preditiva. A manutenção preditiva é aquela que monitora o desempenho e a condição do equipamento durante as condições normais de operação para reduzir a probabilidade de falhas. Semelhante à manutenção preventiva (algumas pessoas até a categorizam como um tipo de manutenção preventiva) e intimamente relacionada à manutenção baseada na condição (CBM) , o objetivo da manutenção preditiva está no nome:primeiro prever quando as falhas podem ocorrer e, em seguida, evitar a falha por meio da manutenção corretiva programada.
Embora muitas organizações empreguem manutenção preditiva e preventiva (76 por cento usam preventiva, enquanto 65 por cento usam preditiva, de acordo com uma pesquisa recente da Reliable Plant), existem algumas diferenças importantes. Mais notavelmente, a manutenção preventiva não requer o aspecto de monitoramento de condição que a manutenção preditiva exige. Isso significa que a manutenção preditiva utiliza tecnologias baseadas em condições, como termografia infravermelha, monitoramento acústico, análise de vibração e análise de óleo. Outra diferença importante é a manutenção preventiva que envolve a inspeção e execução de manutenção em ativos, independentemente de o equipamento precisar de manutenção (o cronograma de manutenção é baseado em um gatilho). A manutenção preditiva não.
Abaixo está um gráfico que mostra como a manutenção baseada em condições se relaciona com a manutenção preditiva e proativa. Aqui, a manutenção preditiva é um dos dois lados decorrentes do CBM:um lado proativo que se concentra em encontrar a causa raiz de uma falha e um lado preditivo que se concentra nos sintomas e falhas de falha.
Para obter mais detalhes sobre manutenção preditiva, tecnologia de manutenção preditiva e muito mais, clique no link no início desta seção.
- Manutenção centrada na confiabilidade (RCM). A manutenção centrada na confiabilidade é o processo de identificar problemas em potencial com seu equipamento e determinar o que você deve fazer para garantir que esses ativos continuem a produzir na capacidade máxima. Em outras palavras, você analisa avarias para descobrir métodos de manutenção adequados e programações de manutenção personalizadas para cada ativo individual.
A manutenção centrada na confiabilidade às vezes é confundida com a manutenção preventiva, mas há uma diferença fundamental:a manutenção preventiva não é seletiva como a RCM, tornando-a menos eficiente. Como o RCM analisa cada ativo individualmente, a ineficiência é reduzida atribuindo tarefas de manutenção personalizadas para cada peça do equipamento.
A manutenção centrada na confiabilidade usa um fluxo de trabalho geral de quatro etapas:Escolha o ativo, avalie o ativo, determine o tipo de manutenção e repita o processo. Os critérios de avaliação para a implementação de um programa RCM fazem sete perguntas:
- Qual deve ser o desempenho deste equipamento?
- De que maneiras este equipamento pode falhar?
- O que causa cada falha?
- O que acontece quando ocorre uma falha?
- Por que cada falha é importante?
- Quais tarefas (proativas) devem ser realizadas para evitar que essas falhas aconteçam?
- O que deve ser feito se uma tarefa preventiva adequada não for encontrada?
Clique no link no início desta seção para ler mais sobre a manutenção centrada na confiabilidade, incluindo como implementar RCM, estudos de caso do mundo real de organizações que implementaram um programa RCM e muito mais.
- Manutenção produtiva total (TPM). A manutenção produtiva total é o processo de utilização de máquinas, equipamentos, funcionários e processos de apoio para manter e melhorar a integridade da produção e a qualidade do sistema. O objetivo de um programa TPM é melhorar a eficácia geral do equipamento (OEE), formando pequenas equipes multidisciplinares para abordar áreas essenciais como manutenção preventiva e autônoma, treinamento de operadores de máquinas e padronização de processos de trabalho. A manutenção produtiva total concentra-se em todos os departamentos de uma organização, garantindo o uso eficiente e eficaz dos meios de produção.
A manutenção produtiva total é considerada mais um processo do que um programa, bem como um processo de melhoria de operações, em vez de um programa de manutenção completo. Também não é uma solução rápida, pois leva anos para obter o máximo benefício de um processo de TPM de alta qualidade; no entanto, você pode ver os resultados imediatamente.
A manutenção produtiva total incorpora a manufatura enxuta e as técnicas do Sistema 5-S de sua referência internacionalmente aceita composta de oito pilares:manutenção autônoma, melhoria focada, manutenção planejada, manutenção de qualidade, gestão inicial de equipamentos, treinamento e educação, segurança, saúde e meio ambiente, e TPM na administração.
A implementação do TPM envolve cinco fases:
- Identifique uma área piloto
- Restaure o equipamento às melhores condições de operação
- Medir OEE
- Resolva / reduza as grandes perdas
- Implementar manutenção planejada
Clique no link no início desta seção para ler mais sobre o TPM, incluindo os oito pilares do TPM, como implementá-lo, como manter um processo de TPM e muito mais.
- Manutenção autônoma. A manutenção autônoma é uma estratégia de manutenção que consiste em treinar os operadores para monitorar continuamente seus equipamentos, fazer ajustes e realizar pequenas tarefas de manutenção para aumentar a eficiência. Isso é feito em vez de dedicar técnicos de manutenção para realizar a manutenção programada regularmente, liberando-os para tarefas de manutenção mais importantes e urgentes.
A manutenção autônoma tem dois princípios básicos:prevenir a deterioração do equipamento por meio de operação adequada e trazer o equipamento e mantê-lo em "estado de novo" por meio de restauração e gerenciamento adequado. Isso requer que os operadores dominem habilidades, como detectar anormalidades ao compreender os componentes da máquina, fazer melhorias, identificar problemas de qualidade e descobrir o que causou os problemas de qualidade.
A implementação da manutenção autônoma envolve sete etapas:aumento do conhecimento do operador, limpeza e inspeção inicial da máquina, remoção da causa da contaminação e melhoria do acesso, desenvolvimento de padrões para lubrificação e inspeção, inspeção e monitoramento, padronização da manutenção visual e melhoria contínua.
Para uma visão mais aprofundada da manutenção autônoma, como implementá-la e como sustentá-la, clique no link no início desta seção.
- Manutenção run-to-fail (RTF). A manutenção de execução até a falha é um tipo de manutenção não planejada e reativa que geralmente é uma estratégia deliberada projetada para minimizar custos. As organizações podem optar por adotar um plano de RTF para coisas como ativos descartáveis (máquinas com peças descartáveis destinadas a serem trocadas em vez de reparadas), ativos não críticos como ferramentas, ativos duráveis ou ativos que não estão sujeitos a desgaste ou provavelmente não sofrerão falham em condições normais de operação ou ativos que mostram padrões de falha aleatórios que não podem ser previstos.
A advertência para a manutenção do RTF é que ela requer bom senso. Saber quando rotular algo como uma falha geral em vez de consertar faz parte do conjunto de habilidades que acompanha a manutenção do RTF. Isso pode representar algum risco, uma vez que os ativos não estão sendo monitorados, fazendo com que a organização enfrente o barril de tempo de inatividade não planejado quando algo quebra.
No entanto, quando implementado nos ativos certos com planejamento inteligente para lidar com falhas inevitáveis, o RTF pode economizar tempo e dinheiro ao não substituir equipamentos inteiros.
Manutenção da máquina e o paralelo do corpo humano
Quando se trata de tipos, técnicas e custos de manutenção, os tipos primários de manutenção podem ser comparados ao corpo humano para obter um instantâneo da tarefa de "manutenção corporal" equivalente. A tabela abaixo usa um exemplo de ativo de geração de energia e o compara com o coração humano.
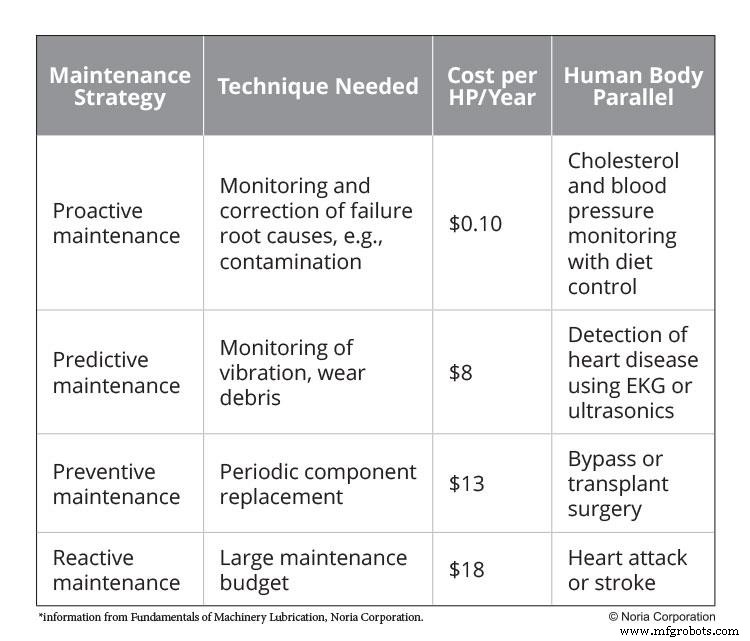
Tipos de gatilhos de manutenção
Os gatilhos de manutenção podem ser definidos e usados com vários tipos de manutenção. Os gatilhos de interrupção são usados com planos de manutenção de operação até a falha ou reativos. A manutenção preditiva usa coisas como gatilhos baseados em tempo na forma de alertas para tentar prevenir a ocorrência de uma falha. Outros gatilhos que serão discutidos incluem gatilhos baseados em evento, uso e condição.
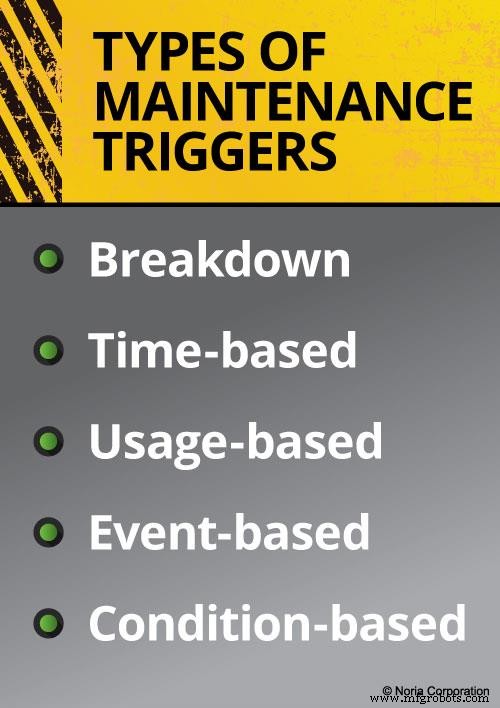
- Disparadores de detalhamento. Conforme mencionado anteriormente, os gatilhos de interrupção são usados com programas de manutenção operacional até a falha ou reativos. Quando um ativo para de funcionar, um alerta é disparado, o que agenda uma ordem de serviço de manutenção para reparar o ativo e restaurá-lo à condição operacional normal.
Normalmente, os gatilhos de interrupção só são úteis quando uma organização está operando um grupo de equipamentos de baixo custo e fáceis de substituir e tem peças e unidades de reposição em estoque que podem ser trocadas de maneira fácil e rápida, minimizando o tempo de inatividade tanto quanto possível. Usar gatilhos de quebra é semelhante a um jogo de gato e rato; não ter que planejar a manutenção permite um orçamento de manutenção menos caro, mas também significa que você deve ter peças sobressalentes e equipamentos disponíveis o tempo todo, bem como pessoal para resolver os problemas. Manter ações como este vai contra princípios enxutos como Just in Time (JIT), que são projetados para reduzir o estoque retido.
- Gatilhos baseados em tempo. Talvez os gatilhos de manutenção mais comumente usados sejam baseados no tempo. Eles estão ligados a um software de planejamento de manutenção como um sistema de gerenciamento de manutenção computadorizado (CMMS) e alerta com base em um intervalo de tempo predefinido. Gatilhos baseados em tempo são usados em programas de manutenção preditiva e preventiva para tarefas simples, como lubrificar engrenagens ou agendar uma inspeção. Por exemplo, quando um ativo atinge um tempo de execução de 14 dias, um alerta é acionado para que ele seja atendido. Fora do ambiente de fabricação, um gatilho baseado no tempo mudaria os filtros de ar da sua unidade de aquecimento, ventilação e ar condicionado (HVAC) a cada três meses.
- Acionadores com base no uso. Semelhante aos gatilhos baseados em tempo, os gatilhos baseados em uso contam com uma métrica predeterminada com base no uso do ativo em questão, independentemente do período de tempo. Ao contrário dos gatilhos baseados no tempo, que são realizados regimentalmente, independentemente da condição da máquina, os gatilhos baseados no uso significam que um ativo só está recebendo manutenção depois de concluir uma quantidade específica de serviço.
Assim como seu carro muda o óleo a cada 5.000 milhas, qualquer máquina que execute operações com restrição de tempo ou quantidade pode ser configurada com um gatilho baseado no uso. As leituras do medidor podem ser adicionadas a um CMMS e usadas para definir alertas quando uma quantidade ou valor desejado é alcançado. Os gatilhos baseados no uso são uma ótima maneira de manter o equipamento sujeito a horários irregulares e são mais frequentemente usados com programas de manutenção preditiva ou preventiva.
- Acionadores baseados em eventos. Os gatilhos de eventos podem ser usados para responder e avaliar equipamentos ou instalações após a ocorrência de um evento, como incêndio ou inundação. Por exemplo, a necessidade de agendar e realizar verificações do sistema elétrico e da infraestrutura após uma enchente pode ser acionada por um CMMS, com o sistema alertando a equipe de manutenção sobre tais tarefas. Embora os gatilhos baseados em eventos ocorram após a ocorrência de um evento, eles podem não estar todos diretamente conectados ao próprio evento. A maioria dos gatilhos baseados em eventos agem como verificações de acompanhamento de um evento.
- Gatilhos baseados em condições. Os gatilhos baseados em condições são empregados de acordo com uma avaliação de um ativo individual. A avaliação é usada para determinar se é aceitável que o ativo continue em execução ou se a manutenção é necessária. Esta é uma opção mais aprofundada porque requer que o pessoal de manutenção tenha conhecimento prático do ativo para tomar uma decisão informada sobre sua condição.
A condição do equipamento também pode ser avaliada remotamente. Sensores colocados em um ativo para monitorar parâmetros como temperatura, vibração e ruído podem ser usados como alertas acionados por condição. Por exemplo, se um sensor perceber um pico de temperatura que ultrapassa uma faixa predeterminada, um alerta é enviado para agendar uma inspeção.
Tecnologia de manutenção moderna
Uma das maiores chaves para os fabricantes se destacarem na manutenção operacional é usar os dados fornecidos pela tecnologia moderna. Para fazer isso, uma nova solução de manutenção é quase necessária para manter ativos, funcionários e processos organizados e funcionando perfeitamente.
Os avanços tecnológicos são mais prevalentes no monitoramento com base na condição na forma de manutenção proativa e preditiva. Sob esses tipos de manutenção, tecnologias como análise de óleo, análise de vibração, termografia e análise de corrente do motor podem ajudar a determinar as causas raízes e os sintomas de falha, buscar benefícios como extensão da vida útil da máquina e detecção precoce de falhas e reduzir o número e o impacto das falhas.
A revolução tecnológica de hoje na indústria de manufatura levou a menos erros e defeitos, produção otimizada e custos de mão de obra reduzidos. Sensores automatizados que podem monitorar continuamente as máquinas estão entre as maiores melhorias. Eles não apenas podem ser empregados em vários tipos de manutenção, mas também podem gerar uma grande quantidade de dados que podem ser analisados e usados para melhorar os processos.
As soluções de CMMS podem ajudar a controlar todos esses dados e integrá-los a quatro aspectos principais para uma estratégia de tecnologia de manutenção moderna:usar manutenção preditiva, enfocar dados e IoT, gerenciar inventário e melhorar os ciclos para o sucesso contínuo.
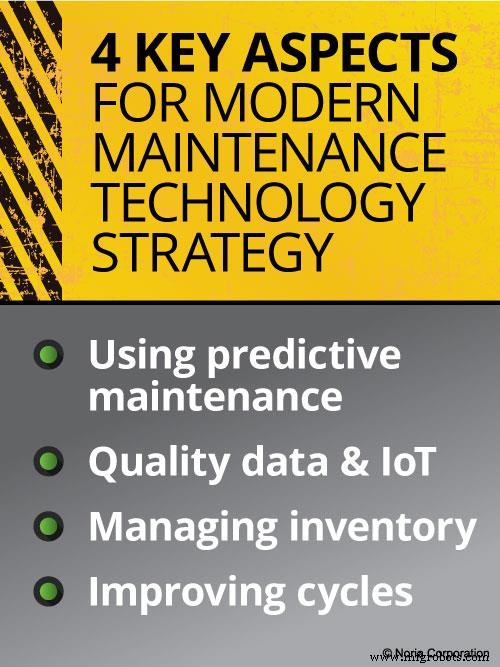
- Usando manutenção preditiva: Embora a manutenção preventiva seja uma boa maneira de evitar que você falhe e reduza o tempo de inatividade, a próxima etapa é implementar a manutenção preditiva para coletar e analisar com eficiência os dados que suas máquinas estão gerando.
- Dados de qualidade e IoT: É importante ter um CMMS que possa lidar com a grande quantidade de dados que está sendo produzida em sua planta. Você vai querer integrar dados de sensores básicos auto-instalados a sensores embutidos e tudo mais. Isso geralmente significa que você deve procurar um CMMS com uma estratégia de IoT para não se casar com um único tipo de hardware.
A IoT é empregada para integrar sem fio os dados coletados de ativos no chão de fábrica a um CMMS utilizado em toda a organização. Isso exigirá a configuração de gatilhos e alertas discutidos anteriormente para criar ordens de serviço automaticamente sem interação humana.
- Gerenciamento de estoque: Uma pesquisa recente da Plant Services revelou que quase 29% dos entrevistados tinham uma carteira de tarefas de manutenção de três a quatro semanas. Sempre adotar uma abordagem reativa para manutenção apenas faz com que sua carteira aumente, o que significa que seus ativos não estão recebendo a manutenção adequada de que precisam. O rastreamento de tarefas pendentes em um CMMS ajuda a identificar problemas, causas e soluções e leva você a adotar uma cultura mais proativa para reduzir o atraso.
- Ciclos de melhoria: Aproveitar os dados de uma configuração de chão de fábrica modernizada e integrá-los por meio de um CMMS coloca você no caminho para melhorar seu ciclo de manutenção, manter a economia e aumentar a eficiência.
Tendências da tecnologia de manutenção moderna
- Internet das coisas industrial: Conforme discutido anteriormente, a internet das coisas, e mais especificamente a internet das coisas industrial (IIoT), é uma forma moderna de coleta automatizada de dados por meio do uso de uma rede de sensores sem fio. Hoje, sensores multifuncionais de baixo custo estão mais disponíveis do que nunca. Eles podem ser configurados em diferentes redes de sensores em vários ativos industriais e usados para coletar dados de manutenção automaticamente. Isso elimina a necessidade de dados manuais caros e demorados, que estão sujeitos a erro humano.
- Realidade Aumentada (AR): A manutenção e o treinamento remotos estão começando a se beneficiar da RA graças à capacidade de oferecer instruções remotas. Essa abordagem personalizada permite que as tarefas de manutenção sejam personalizadas de acordo com a compreensão e o nível de habilidade do funcionário. A realidade aumentada pode facilitar o treinamento fornecido por um fornecedor de equipamento ou pessoal de manutenção de nível sênior por meio de uma apresentação cibernética que mostra como realizar uma tarefa.
Embora ainda seja uma tendência emergente, o uso de RA para treinamento está ganhando popularidade devido à crescente complexidade dos equipamentos industriais. A realidade aumentada pode aliviar a carga do pessoal de manutenção que tenta acompanhar as variações nos novos equipamentos, incluindo recursos tecnologicamente avançados que acompanham cada ativo. Já existem vários fornecedores que oferecem soluções de AR em grande escala para tarefas de manutenção e fornecedores de IIoT que fornecem AR como parte de um pacote agrupado.
- Manutenção como serviço (MaaS): MaaS é um paradigma relativamente novo para o mundo da manutenção. Basicamente, envolve a entrega de serviços de manutenção sob demanda. Com o MaaS, um fornecedor pode cobrar de um operador de fábrica de acordo com os serviços de manutenção que ele realmente usa, em vez de uma taxa fixa de serviço. Os fornecedores fazem isso coletando e processando grandes quantidades de dados, armazenando-os na nuvem e agendando tarefas com base nesses dados. Os serviços incluem:
- prever a vida útil de um ativo ou oferecer informações sobre os intervalos de manutenção ideais;
- fornecendo manuais de serviço, vídeos e realidade virtual (VR) e suporte interativo de AR;
- configurar tecnologia da informação (TI) e outros sistemas dentro de uma planta com base em resultados analíticos; e
- fornecendo estatísticas detalhadas e relatórios sobre o maquinário.
Os primeiros estágios dos programas MaaS estão começando a ser disponibilizados pelos fornecedores. Os elevadores ThyssenKrupp agora vêm com um programa de manutenção proativa que prevê os problemas antes que eles ocorram e notifica os indivíduos apropriados para realizar uma inspeção. A BMW também está planejando levar o MaaS ao consumidor em um futuro próximo, oferecendo programas que permitirão aos proprietários de automóveis saber o melhor momento para fazer a manutenção em seus veículos.
Manutenção e reparo de equipamentos
- Diferença entre manutenção preventiva e preditiva
- Otimizando a manutenção preventiva usando um CMMS
- Manutenção preventiva vs manutenção preditiva:de volta ao básico
- Manutenção preventiva:uma visão geral
- Usando software de manutenção preventiva para fabricação
- Como fazer a manutenção preventiva planejada (PPM)
- Como agendar ordens de serviço de manutenção preventiva
- Principais benefícios do software de manutenção preventiva
- O que é Manutenção Preventiva?
- 5 tipos de manutenção para conhecer