Como implementar um programa eficaz de monitoramento do desgaste da corrente
O monitoramento do desgaste da corrente faz parte dos programas de confiabilidade do equipamento desde que o primeiro elo foi forjado. É uma parte tão integrante do programa de confiabilidade de uma organização que se tornou parte da gíria da indústria como na frase:"Uma rede é tão forte quanto seu elo mais fraco."
As correntes fazem parte de quase todos os processos industriais. Eles são encontrados no sistema de transporte de manuseio de materiais de uma planta, componentes-chave na operação de talhas e guindastes, ou como parte da conexão que controla um dispositivo de parada de segurança.
Independentemente de sua função, a falha de qualquer componente que compõe uma cadeia é onerosa para o proprietário, senão desastrosa. Mesmo que todos concordemos que uma falha de corrente é indesejável, o monitoramento do desgaste da corrente da indústria moderna permaneceu variado em sua abordagem e frequência.
Normalmente, as inspeções de confiabilidade da cadeia são aplicadas por meio de um procedimento de amostragem de inspeção periódica ou programação de substituição. As inspeções visuais são comumente aplicadas à inspeção da corrente para identificação de desgaste, o que é demorado para realizar com tremenda dependência da experiência do inspetor, atitude e conhecimento de processamento.
Existe tecnologia que faz com que essa abordagem cara não seja mais a única via disponível para o monitoramento da corrente para os departamentos de manutenção de hoje. A aplicação de sistemas ópticos fotoelétricos infravermelhos permite inspeções que são mais precisas, menos caras e resultam em informações de tendência para reduzir as oportunidades de falha.
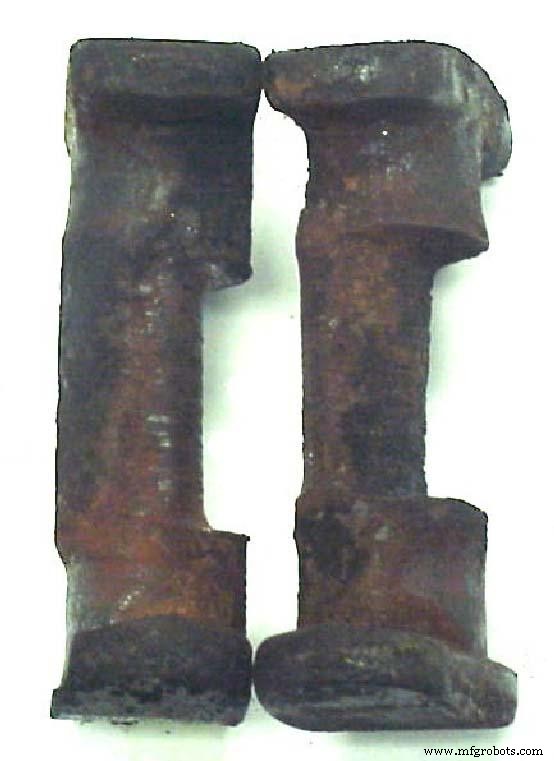
Exemplos de pinos de corrente gastos identificados através do uso de um sistema de monitoramento de desgaste fotoelétrico infravermelho.
Explicação do processo fotoelétrico
A tecnologia fotoelétrica infravermelha é utilizada em muitos aspectos de nossas vidas diárias, sem que a maioria de nós tenha consciência de sua existência. Exemplos de detectores fotoelétricos incluem os componentes do sensor nos tipos mais avançados de sistemas de segurança, controles de segurança em sistemas de fechamento de portas para elevadores e sistemas de trânsito e até mesmo como monitores de nível de enchimento de garrafas em sistemas de engarrafamento de alta produção.
As aplicações desta tecnologia são certamente vastas e variadas por natureza. O princípio básico se baseia em uma fonte de luz infravermelha (transmissor) que gera um feixe de infravermelho pulsado para uma série de sensores infravermelhos (receptor), que por sua vez monitoram esse feixe. A combinação do transmissor e do receptor é chamada de detector fotoelétrico.
O transmissor e o receptor são instalados em lados opostos da área a ser monitorada e um sinal é gerado quando o receptor detecta a obstrução do feixe infravermelho pulsado. Um farol de carro e uma fotocélula poderiam ser usados em um projeto científico para criar um detector fotoelétrico muito rudimentar.
A adição de luz infravermelha a este processo se deve ao aumento da sensibilidade e penetração do receptor. A luz infravermelha é uma forma de radiação eletromagnética semelhante aos sinais de rádio, luz visível e raios-X. Enquanto a energia infravermelha é semelhante à luz visível e compartilha muitas de suas características, a energia infravermelha é invisível ao olho humano devido à sua diferença nos comprimentos de onda. A energia infravermelha tem comprimentos de onda de 0,75 mícrons a 1 milímetro.
As tampas dos detectores fotoelétricos são feitas de materiais especiais projetados para bloquear a luz visível e, ao mesmo tempo, permitir a máxima penetração da energia infravermelha. É o que permite o uso de detectores fotoelétricos infravermelhos em um chão de fábrica bem iluminado ou mesmo sob luz solar direta.
Perspectiva Histórica
Se a maioria das empresas documentasse seus programas de monitoramento de corrente, você não ficaria surpreso ao encontrar afirmações como, "Substitua a corrente quando o transportador apresentar mau funcionamento durante a produção" ou "A última substituição da corrente foi há cerca de cinco anos, e é o devido". Mesmo o que é visto como um programa proativo para monitoramento do desgaste da corrente tem historicamente usado o método de escolher uma amostra arbitrária de uma seção nominal de 10 pés da corrente e medi-la fisicamente para alongamento, o que indicaria desgaste. Obviamente, existe um grau significativo de risco no uso dessa abordagem.
Os planos de amostragem dependem da amostra fornecer informações que sejam consistentes com a condição de todo o sistema. Limitar a inspeção a uma seção de 3 metros de corrente dentro de um sistema de 300 metros de comprimento cria uma situação em que a probabilidade de realmente amostrar a área de pior desgaste fornece “chances” de detecção que até mesmo um jogador de Las Vegas consideraria inaceitáveis.
Outra preocupação é a precisão com que as medições estão sendo produzidas quando o dispositivo de medição é uma fita métrica com qualidade de hardware padrão. A alternativa histórica - a inspeção visual da corrente - pode certamente identificar o desgaste da corrente, mas mais uma vez o cronograma de produção pode tolerar as paradas extremas de uma abordagem tão trabalhosa, que precisa de uma corrente estacionária para fazer uma inspeção adequada? Muitos tipos de corrente são lubrificados ou pintados, e os mesmos revestimentos que protegem a corrente do desgaste e da máscara de corrosão indicadores de desgaste típicos ao realizar inspeções visuais.
A última abordagem frequentemente usada é a substituição periódica com base na idade da cadeia. Este sistema de garantia da confiabilidade da corrente pode ajudar a reduzir o tempo de inatividade da produção, mas o custo de substituir a corrente confiável apenas porque é devido nunca pode ser recuperado.
Monitoramento do desgaste da corrente fotoelétrica infravermelho
Os instrumentos fotoelétricos infravermelhos projetados especificamente para o monitoramento do desgaste da corrente normalmente usam tecnologia referenciada para medir com precisão a distância entre as bordas de cada elo central da corrente. Com medições link-a-link precisas, esses monitores podem identificar facilmente links ou pinos individuais que mostram sinais de desgaste anormal.
A unidade ilustrada abaixo é um dispositivo portátil operado por bateria capaz de monitorar todas as combinações de correntes de 3, 4 e 6 polegadas. Estão disponíveis unidades alternativas que são projetadas para correntes de passo único. Esses monitores são capazes de monitorar a corrente em movimento para permitir que a inspeção seja realizada sem interrupção da produção.
Se forem utilizadas unidades instaladas permanentemente, o monitoramento contínuo da cadeia pode ser realizado instantaneamente, identificando quaisquer elos da cadeia que excedam os limites programados. Tanto as unidades de monitoramento de status quanto as unidades instaladas permanentemente identificam qualquer link que esteja fora dos comprimentos de tamanho predefinidos por meio da iluminação das luzes de alarme que identificam a área específica do problema. A maioria das unidades fornecerá ao operador opções de como os dados podem ser processados, incluindo caminhos alternativos para monitoramento, revisão de dados e identificação de áreas problemáticas.
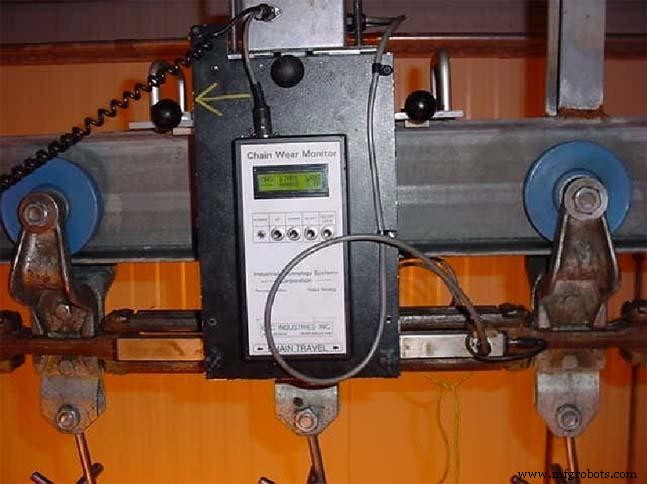
Um sistema de monitoramento de desgaste fotoelétrico infravermelho portátil montado em um transportador.
Os sistemas automatizados de identificação e marcação de anormalidades identificam cada elo que está acima do limite de desgaste e, se combinados com o monitoramento do software de análise de tendências, a varredura periódica ou contínua permitirá a substituição planejada da corrente apenas quando for realmente necessária. O software de tendências requer um ponto de início / parada definido para permitir comparações precisas. Isso geralmente é realizado por meio de um link identificado exclusivamente instalado no sistema.
Uma opção para iniciar / parar a identificação do link pode ser realizada montando permanentemente um conjunto de ímã na própria corrente, que sinalizará automaticamente a unidade para iniciar e parar as sessões de registro de dados cada vez que o ímã passar pelos sensores da unidade. Esta opção fornece uma apresentação de dados facilmente compreensível.
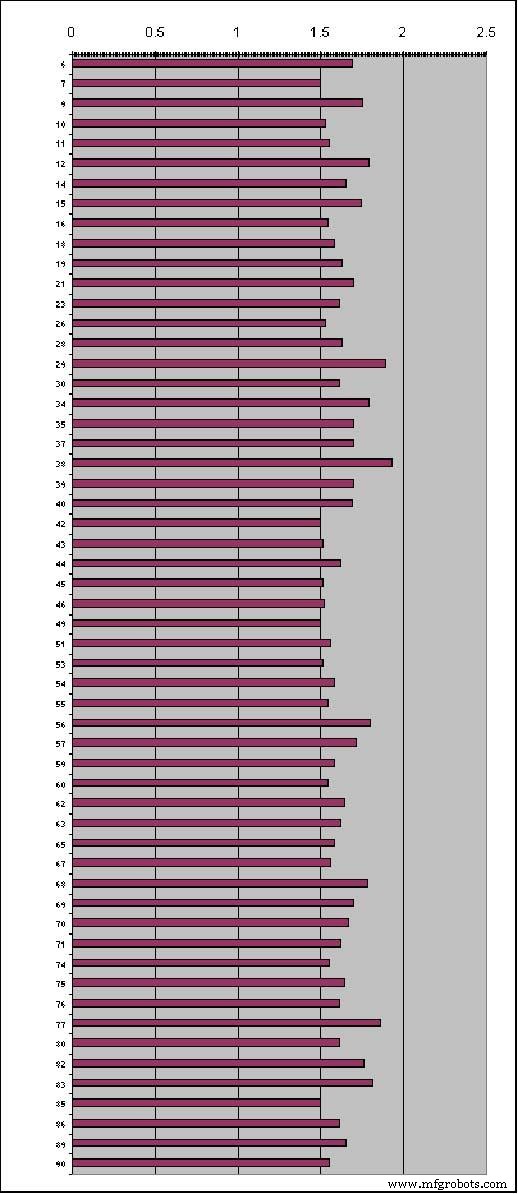
Um exemplo de software de relatório mostrando um gráfico de barras de medições de conjunto de links.
Vários recursos exclusivos que podem ser obtidos a partir de um software especialmente projetado permitem valiosas ferramentas de análise, como critérios de aceitação de comprimento de span ajustável, faixas de medição de registro de dados (link individual, conjuntos de links individuais ou seções de 10 pés), sobreposição de tendências e opções de gráficos.
Precisão
Na corrente de uso normal, a maior parte do desgaste da corrente ocorre nos pontos de fricção. Os pontos de fricção são as áreas onde o pino engata no elo central. O desgaste ocorre no próprio pino central, no interior do elo central ou, na maioria dos casos, uma combinação de ambos. Os fabricantes fornecem gráficos de crescimento de substituição que fornecem um valor para determinar o comprimento máximo de “crescimento da corrente” que é recomendado como uma diretriz para a substituição da corrente. Isso geralmente é baseado em dados de inspeção que são coletados da técnica de medição nominal de 10 pés comumente realizada. Um exemplo seria que uma seção de 10 pés de uma nova corrente medida em 120 polegadas deveria ser substituída quando atingir 124 a 124,5 polegadas de comprimento.
Uma preocupação que deve ser reconhecida é que o desgaste pode ou não ser uniformemente distribuído por aquela seção medida da corrente. O desgaste em um link pode ser muito mais severo do que em um link adjacente. Este tipo de condição apresenta a possibilidade de uma corrente à beira da falha medindo bem dentro de tolerâncias aceitáveis.
O uso da tecnologia de medição de elo individual elimina esse tipo de erro, aumentando a confiabilidade da inspeção e reduzindo o risco de falha catastrófica da corrente. Um sistema fotoelétrico infravermelho de varredura fornece precisão de 0,02 polegadas. Isso é ainda mais significativo quando o usuário lembra que está sendo medido na corrente em movimento.
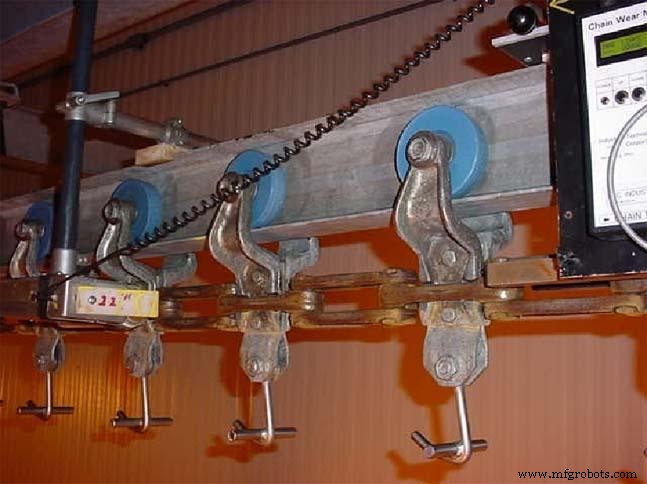
Este sistema está equipado com um sistema automático de marcação por pulverizador de tinta projetado para marcar links individuais que não estejam dentro dos limites de tolerância aceitáveis.
Pessoal operacional
Embora a operação de sistemas de monitoramento de cadeia fotoelétrica infravermelho padrão não seja muito mais difícil do que a operação de um computador pessoal de mesa típico, há considerações que devem ser avaliadas ao operar esse tipo de sistema. O primeiro e mais importante é a segurança. Sempre que o pessoal é obrigado a trabalhar fisicamente em torno do equipamento industrial em movimento, há questões de segurança que precisam ser monitoradas cuidadosamente. No mínimo, o treinamento de segurança deve incluir treinamento de segurança OSHA e revisão de segurança específica da planta. Os procedimentos de bloqueio e etiquetagem também devem ser seguidos para evitar o movimento da corrente durante a instalação e remoção do monitor.
Dependendo do tipo de unidade que está sendo inspecionada, o treinamento do operador precisa abordar a operação da unidade de corrente elétrica (transportadores, guindastes, elevadores, etc.), instalação da unidade, requisitos de inspeção da linha, operação de software, armazenamento e recuperação de arquivos e interpretação de dados. Freqüentemente, o acesso dos dois lados à corrente não é possível e pode exigir recortes visuais. Esta operação requer um indivíduo que entenda os requisitos de carga de vários tipos de unidades para evitar o enfraquecimento estrutural dos suportes necessários. Uma vez que este tipo de inspeção é baseado na confiabilidade e não é um código, os critérios de aceitação de requisitos precisam ser estabelecidos a fim de fornecer dados úteis.
O desenvolvimento de tolerâncias máximas de crescimento requer indivíduos com experiência em seu desenvolvimento. O treinamento e a experiência recomendados podem variar, mas uma boa diretriz incluiria 30 horas de treinamento em sala de aula cobrindo todos os assuntos relacionados e um mínimo de seis meses de experiência prática antes de considerar um indivíduo qualificado para realizar inspeções de forma independente.
A utilização da tecnologia fotoelétrica infravermelha para realizar o monitoramento da cadeia é um grande salto de melhoria nesta parte importante do programa de confiabilidade de uma empresa. A economia de custos por si só justifica a pesquisa quanto à aplicabilidade desta tecnologia.
Um exemplo recente de economia de custos foi desenvolvido por uma empresa de processamento de carne que usou a técnica de medição nominal de 10 pés para inspeção antes da implementação desta tecnologia. Ao longo de um período de dois anos, seus incidentes de paralisação foram reduzidos em 100% (de uma média de sete paralisações por período de 12 meses para zero paralisações não programadas).
Foi calculado que cada avaria custou à empresa $ 2.416 em custos de reparação de manutenção, $ 3.765 em tempo de trabalho perdido e $ 1.184 em receitas de produção. O custo total para a empresa foi de $ 51.555 anualmente. Economias de custo adicionais foram obtidas na extensão da vida útil da corrente, redução do estoque de peças de reposição, programação de manutenção planejada e substituição da corrente estendida.
Este é apenas um dos muitos exemplos em que, se a confiabilidade da cadeia for crítica para a produção da planta ou para a segurança do pessoal, a utilização de métodos de inspeção de elos individuais são autofinanciados em sua aplicação.
Manutenção e reparo de equipamentos
- Parte do infravermelho da estratégia PM eficaz em Weyerhaeuser
- Como Obter um Planejamento de Manutenção Eficaz
- Um programa de PM eficaz requer uma base sólida
- Como o monitoramento de condição aprimora um programa PdM
- Como implementar a manutenção produtiva total
- Como construir um programa de manutenção elétrica
- Como o programa baseado em confiabilidade melhora a segurança?
- Como sustentar a mudança em um programa de confiabilidade
- Como iniciar um programa de confiabilidade
- Como implementar um programa de aprendizagem de manufatura