Desenvolvimentos de processos de fabricação de aço
Desenvolvimentos de processos de fabricação de aço
A primeira produção conhecida de aço são peças de ferragens escavadas em um sítio arqueológico na Anatólia e têm quase 4.000 anos, datando de 1800 aC (antes da era comum). Horácio identificou armas de aço como a falcata na Península Ibérica, enquanto o aço Nórico foi usado pelo exército romano.
A reputação de 'ferro sérico' do sul da Índia (aço wootz) entre os gregos, romanos, egípcios, africanos orientais, chineses e do Oriente Médio cresceu consideravelmente. Fontes do sul da Índia e do Mediterrâneo, incluindo Alexandre, o Grande (século III a.C.) relatam a apresentação e exportação de tal aço para os gregos. Os locais de produção de metal no Sri Lanka empregavam fornos eólicos impulsionados pelos ventos das monções, capazes de produzir aço de alto carbono (C). A produção de aço wootz em larga escala em Tamilakam usando cadinhos e fontes de C, como a usina Avaram, ocorreu no século VI aC, o precursor pioneiro da produção moderna de aço e metalurgia. O aço foi produzido em grandes quantidades em Esparta por volta de 650 aC.
Os chineses do período dos Estados Guerreiros (403 aC a 221 aC) haviam temperado aço endurecido, enquanto os chineses da dinastia Han (202 aC a 220 dC) criaram aço fundindo ferro forjado com ferro fundido, obtendo um produto final de carbono -aço intermediário no século I dC (era comum). O povo Haya da África Oriental inventou um tipo de forno que usavam para fazer aço C a 1.800 graus C quase 2.000 anos atrás. O aço da África Oriental foi sugerido por Richard Hooker para datar de 1400 aC.
Evidências da primeira produção de aço com alto teor de carbono no subcontinente indiano são encontradas em Kodumanal em Tamilnadu, Golkonda em Telengana e Karnataka e nas áreas de Samanalawewa no Sri Lanka. Este aço conhecido como aço wootz, produzido por volta do século VI aC foi exportado globalmente. A tecnologia do aço existia antes de 326 aC na região, pois são mencionados na literatura de Sangam Tamil, árabe e latino como o melhor aço (chamado de ferro Seric) do mundo exportado para os mundos romanos, egípcios, chineses e árabes naquela época . Como a tecnologia foi adquirida no sul da Índia, a origem da tecnologia do aço na Índia pode ser estimada de forma conservadora em 500 aC a 400 aC.
Wootz, também conhecido como aço Damasco, é famoso por sua durabilidade e capacidade de manter uma borda. Como é conhecido pelos escritos de Zósimo de Panópolis, este aço foi originalmente criado a partir de vários materiais diferentes, incluindo vários oligoelementos. No entanto, o aço era uma tecnologia antiga na Índia quando o rei Porus apresentou uma espada de aço ao imperador Alexandre em 326 aC. Era essencialmente uma liga complicada com ferro como seu principal componente. Estudos recentes sugeriram que nanotubos de carbono foram incluídos em sua estrutura, o que pode explicar algumas de suas qualidades lendárias, embora, dada a tecnologia da época, tais qualidades tenham sido produzidas por acaso e não por design. Vento natural foi usado onde o solo contendo ferro foi aquecido pelo uso de madeira. Os antigos cingaleses conseguiram extrair uma tonelada de aço para cada 2 toneladas de solo, um feito notável na época. Um desses fornos foi encontrado em Samanalawewa e os arqueólogos conseguiram produzir aço como os antigos faziam.
Vários métodos foram usados para produzir aço no subcontinente indiano. De acordo com textos islâmicos como al-Tarsusi e Abu Rayhan Biruni, três métodos são descritos para a produção indireta de aço. O historiador islâmico medieval Abu Rayhan Biruni (973 dC a 1050 dC) fornece a referência mais antiga da produção de aço de Damasco. Ele descreve apenas três métodos para a produção de aço. Os dois primeiros métodos têm uma longa história na Ásia Central e no subcontinente indiano, enquanto o terceiro é exclusivo do sul da Ásia. Esses três métodos são geralmente considerados originários do subcontinente indiano. O primeiro método e o método tradicional mais comum é a cementação em estado sólido de ferro forjado. Este é um processo de difusão no qual o ferro forjado é embalado em cadinhos ou uma lareira com carvão, depois aquecido para promover a difusão de C no ferro para produzir aço. A carburação é a base do processo wootz do aço (um tipo de processo de cimentação). O segundo método é a descarbonetação do ferro fundido removendo C do ferro fundido (um tipo de processo de cadinho). Outro método indireto usa ferro forjado e ferro fundido. Neste processo, ferro forjado e ferro fundido podem ser aquecidos juntos em um cadinho para produzir aço por fusão. Em relação a este método, Abu Rayhan Biruni afirma:“este era o método usado em Hearth”.
Variações do processo de cofusão foram encontradas preliminarmente na Pérsia e na Ásia Central, mas também foram encontradas em Hyderabad, na Índia. Para o C, uma variedade de materiais orgânicos são especificados pelas autoridades islâmicas contemporâneas, incluindo cascas de romã, bolotas, cascas de frutas como casca de laranja, folhas, bem como clara de ovo e cascas. Lascas de madeira são mencionadas em algumas das fontes indianas, mas significativamente nenhuma das fontes menciona carvão.
O aço para cadinho, formado por aquecimento e resfriamento lento de ferro puro e C (normalmente na forma de carvão) em um cadinho, foi produzido em Merv do século IX ao X dC. No século 11, há evidências da produção de aço na Song China usando duas técnicas, a saber (i) um método "berganesco" que produzia aço inferior, não homogêneo e (ii) um precursor do processo Bessemer que usava desintegração parcial -carbonização através de forjamento repetido sob uma explosão a frio.
A produção de aço pelo processo de cimentação foi descrita em um tratado publicado em Praga em 1574 e estava em uso em Nuremberg a partir de 1601.
Processo de cimentação de fabricação de aço
O processo de cimentação é um método obsoleto de fabricação de aço por cementação de ferro. Ao contrário da siderurgia moderna, aumentou a quantidade de C no ferro. Aparentemente, foi desenvolvido antes do século XVII. O forno de aço Derwentcote, construído em 1720, é o mais antigo exemplo sobrevivente de um forno de cimentação. Dois fornos de cimentação que certamente existiam no início do século XVI foram escavados na Inglaterra.
O processo começa com ferro forjado e carvão. Ele usava um ou mais potes de pedra longos dentro de uma fornalha. Normalmente, cada um tinha 14 pés (4,27 m) por 4 pés (1,22 m) e 3,5 pés (1,07 m) de profundidade. Barras de ferro e carvão são embaladas em camadas alternadas, com uma camada superior de carvão e depois matéria refratária para deixar o pote hermético. Alguns fabricantes usavam uma mistura de carvão em pó, fuligem e sais minerais, chamada cimento em pó. Em obras maiores, foram tratadas até 16 toneladas de ferro em cada ciclo.
Barras de ferro forjado padrão foram colocadas no forno de cimentação para conversão em cimentação ou aço blister. O forno foi construído em arenito na forma de um grande baú com tampa e foi carregado com as barras de ferro colocadas em camadas intercaladas com grandes quantidades de carvão de alta qualidade. Quando totalmente carregado, a tampa foi colocada no lugar e argamassa usada para selar o baú. O aquecimento foi aplicado a partir de um incêndio abaixo do forno, onde um fogo de carvão foi mantido a partir de um poço. O calor foi mantido por até uma semana e mais uma semana foi tomada para que o baú esfriasse antes de ser aberto, esvaziado e recarregado.
O projeto comum dos fornos de cimentação tinha dois baús lado a lado com um furo de fogo no centro dos dois e todo o lote contido dentro de uma estrutura em forma de garrafa, semelhante a 'cones de vidro' e 'fornos de cerâmica', que abrigavam os fornos de o clima e agiu como uma chaminé. A colocação de dois baús de fornalha juntos permitiria que um fogo aqueça o primeiro baú enquanto o segundo estava esfriando e sendo recarregado.
Durante o aquecimento longo e lento, o C do carvão foi absorvido pelas barras de ferro. Quando removido do forno, o aço tinha uma aparência empolada (daí o nome alternativo). Esses blisters continham aço com alto teor de C, enquanto o centro das barras ainda era de ferro forjado com muito pouco C, portanto, o aço blister era de pouca ou nenhuma utilidade até que fosse processado posteriormente.
O aço blister foi aquecido e forjado sob um martelo de tal forma que a barra foi dobrada sobre si mesma. Isso resultou em 'Shear Steel', uma segunda rodada de aço produzido para dobrar e martelar conhecido como 'double shear', um produto de melhor qualidade, mais rodadas de dobra e martelar produziram graus ainda mais altos de aço. Um plano e vista de elevação de um forno de cimentação típico está na Fig 1.
Fig 1 Vista típica de um forno de cimentação
Aço para cadinho
Aço de cadinho é um termo que se aplica ao aço feito por dois métodos diferentes na era moderna, embora tenha sido produzido em locais variados ao longo da história. É feito derretendo ferro e outros materiais em um cadinho e derramando o líquido derretido em um molde. O aço para cadinhos foi produzido no sul e centro da Ásia durante a era medieval. Técnicas para produção de aço de alta qualidade foram desenvolvidas por Benjamin Huntsman na Inglaterra no século XVIII. Seu processo usava ferro e aço como matérias-primas. A estrutura cristalina homogênea deste aço fundido melhorou sua resistência e dureza em comparação com as formas anteriores de aço.
O aço para cadinho é geralmente atribuído a centros de produção na Índia e no Sri Lanka, onde foi produzido usando o processo wootz, e supõe-se que seu aparecimento em outros locais foi devido ao comércio de longa distância. Apenas recentemente ficou claro que lugares na Ásia Central como Merv no Turcomenistão e Akhsiket no Uzbequistão eram importantes centros de produção de aço para cadinhos. Os achados da Ásia Central são todos de escavações e datam dos séculos VIII a XII dC, enquanto o material indiano / do Sri Lanka é de 300 aC. Além disso, o minério de ferro da Índia tinha traços de vanádio (V) e outras terras raras, levando ao aumento da temperabilidade no aço de cadinho indiano, famoso em todo o Oriente Médio por sua capacidade de reter uma borda.
Embora o aço do cadinho seja mais atribuído ao Oriente Médio nos primeiros tempos, espadas foram descobertas na Europa, particularmente na Escandinávia. As espadas em questão têm o nome ambíguo gravado nela, 'Ulberht'. Essas espadas, na verdade, datam de um período de 200 anos, do século 9 ao início do século 11. É especulado por muitos que o processo de fabricação das lâminas se originou no Oriente Médio e posteriormente foi comercializado durante os dias da 'rota comercial do Volga'.
Nos primeiros séculos do período islâmico, surgem alguns estudos científicos sobre espadas e aço. Os mais conhecidos são por Jabir ibn Ayyan (século VIII), al-Kindi (século IX), Abu Rayhan Biruni (início do século XI), Murda al Tarsusi (final do século XII) e Fakhr-i-Mudabbir (século XIII). ). Qualquer um deles contém muito mais informações sobre aços indianos e damascenos do que aparece em toda a literatura da Grécia e Roma clássicas.
Benjamin Huntsman era um relojoeiro em busca de aço melhor para molas de relógio. Ele começou a produzir aço em 1740, após anos de experimentos em segredo. O sistema de Huntsman usava um forno a coque capaz de atingir 1.600 graus C, no qual eram colocados até doze cadinhos de barro, cada um capaz de conter cerca de 15 kg de ferro. Quando os cadinhos ou "vasos" estavam incandescentes, eles eram carregados com pedaços de aço blister, uma liga de ferro e C produzida pelo processo de cimentação e um fluxo para ajudar a remover impurezas. Os potes foram removidos após cerca de 3 horas no forno, as impurezas na forma de escória foram retiradas e o aço líquido despejado em moldes para terminar como lingotes fundidos. A fusão completa do aço produziu uma estrutura cristalina altamente uniforme após o resfriamento, o que deu ao metal maior resistência à tração e dureza em comparação com outros aços fabricados na época.
O aço era produzido em oficinas especializadas denominadas ‘fornos de cadinho’ em Sheffield, Inglaterra, que consistiam em uma oficina no nível do solo e uma adega subterrânea. Os edifícios dos fornos variavam em tamanho e estilo arquitetônico, crescendo em tamanho na última parte do século XIX, à medida que os desenvolvimentos tecnológicos permitiam que vários potes fossem "queimados" de uma só vez, usando gás como combustível de aquecimento. Cada oficina tinha uma série de características padrão, como fileiras de furos de fusão, poços cheios, aberturas de teto, fileiras de prateleiras para os potes de cadinho e fornos de recozimento para preparar cada pote antes da queima. Salas auxiliares para pesagem de cada carga e para a fabricação dos cadinhos de barro eram anexadas à oficina ou localizadas dentro do complexo da adega. O aço, originalmente destinado à fabricação de molas de relógios, foi posteriormente utilizado em outras aplicações, como tesouras, machados e espadas.
Em outro método, desenvolvido nos Estados Unidos na década de 1880, ferro e C foram fundidos diretamente para produzir aço para cadinho. Ao longo do século 19 e na década de 1920, uma grande quantidade de aço de cadinho foi direcionada para a produção de ferramentas de corte, onde foi chamado de aço ferramenta.
O processo de cadinho continuou a ser usado para aços especiais, mas hoje está obsoleto.
Outra forma de aço para cadinho foi desenvolvida em 1837 pelo engenheiro russo Pavel Anosov. Sua técnica dependia menos do aquecimento e resfriamento e mais do processo de têmpera de resfriamento rápido do aço líquido quando a estrutura cristalina correta se formava. Ele chamou seu aço de 'bulat'. O segredo do processo morreu com ele. Nos Estados Unidos, o aço cadinho foi iniciado por William Metcalf. Embora o aço do cadinho fosse de alta qualidade, também era caro; no entanto, um sinal de qualidade foi o uso de aço de cadinho na década de 1950 para usos especializados.
O processo Bessemer trouxe o fim do aço cadinho para usos menos críticos.
O processo Bessemer e a fabricação de aço moderna
A história da siderurgia moderna começou no século 19, quando Reaumur da França em 1772, Kelly dos Estados Unidos em 1850 e Bessemer da Grã-Bretanha em 1856 descobriram como melhorar o ferro-gusa controlando o teor de carbono das ligas de ferro, que assim realmente tornam-se aços. Enquanto Reaumur, um químico, era movido pela curiosidade científica, mas Kerry e Bessemer sendo engenheiros, estavam respondendo à necessidade de maiores quantidades e melhores qualidades de aço que a revolução industrial, com seus teares, máquinas a vapor, máquinas e ferrovias, havia criado . Isso deu início a uma relação dialética entre ciência e tecnologia e os conceitos básicos de refino de metal quente (ferro gusa) pela oxidação de C em um banho líquido foram inventados na época.
O crescimento das ferrovias durante o século 19 na Europa e na América colocou grande pressão sobre a indústria de ferro e aço, que ainda lutava com processos de produção ineficientes. No entanto, o aço ainda não era comprovado como metal estrutural e a produção era lenta e cara. Isso foi até 1856, quando Henry Bessemer encontrou uma maneira mais eficaz de introduzir oxigênio (O2) no ferro líquido para reduzir o teor de C.
A partir de janeiro de 1855, ele começou a trabalhar em uma maneira de produzir aço nas quantidades maciças necessárias para a artilharia e em outubro registrou sua primeira patente relacionada ao processo Bessemer. Bessemer começou a trabalhar com um forno reverberatório comum, mas durante um teste, alguns lingotes de porco caíram ao lado da panela e ficaram acima dela no ar quente do forno. Quando Bessemer foi empurrá-los para dentro da concha, descobriu que eram cascas de aço:só o ar quente havia convertido as partes externas dos lingotes em aço. Essa descoberta crucial o levou a redesenhar completamente seu forno para forçar o ar de alta pressão através do ferro líquido usando bombas de ar especiais. Intuitivamente, isso parece uma loucura porque esfriaria o ferro, mas devido à oxidação exotérmica tanto o silício (Si) quanto o C reagem com o excesso de O2 deixando o ferro fundido circundante ainda mais quente, facilitando a conversão em aço.
Agora conhecido como o processo Bessemer, Bessemer projetou um receptáculo em forma de pêra - conhecido como "conversor" - no qual o ferro pode ser aquecido enquanto o O2 pode ser soprado através do metal líquido. À medida que o O2 passasse pelo metal líquido, ele reagiria com o C, liberaria dióxido de carbono (CO2) e produziria um ferro mais puro.
O processo Bessemer foi o primeiro processo industrial barato para a produção em massa de aço a partir de ferro líquido. O processo recebeu o nome de seu inventor, Henry Bessemer, que obteve uma patente sobre o processo em 1855. O princípio-chave é a remoção de impurezas do ferro por oxidação com ar soprado através do ferro líquido. A oxidação também aumenta a temperatura da massa de ferro e a mantém derretida. O processo é realizado em um grande recipiente de aço ovóide revestido com argila ou dolomita chamado de conversor Bessemer. A capacidade de um conversor era de 8 toneladas a 30 toneladas de ferro líquido com uma carga usual em torno de 15 toneladas. Na parte superior do conversor há uma abertura, geralmente inclinada para o lado em relação ao corpo da embarcação, através da qual o ferro é introduzido e o produto acabado retirado. O fundo é perfurado com vários canais chamados ventaneiras através dos quais o ar é forçado para dentro do conversor. O conversor é girado em munhões para que possa ser girado para receber a carga, virado para cima durante a conversão e depois girado novamente para derramar o aço líquido no final.
O processo de oxidação remove impurezas como Si, C e manganês (Mn) como óxidos. Esses óxidos escapam como gás ou formam uma escória sólida. O revestimento refratário do conversor também desempenha um papel na conversão – o revestimento de argila refratária foi usado no ácido Bessemer, no qual há baixo fósforo (P) na matéria-prima. A dolomita é usada quando o teor de P é alto no Bessemer básico (revestimentos de calcário ou magnesita também são usados às vezes em vez de dolomita). Para dar ao aço as propriedades desejadas, outras substâncias podem ser adicionadas ao aço líquido quando a conversão estiver completa, como spiegeleisen (uma liga de ferro carbono-manganês).
Quando o aço necessário foi formado, ele foi derramado em panelas e depois transferido para moldes e a escória mais leve é deixada para trás. O processo de conversão chamado de 'golpe' foi concluído em cerca de vinte minutos. Durante este período o progresso da oxidação das impurezas foi avaliado pelo aparecimento da chama que sai da boca do conversor. Após o sopro, o metal líquido foi recarburado até o ponto desejado e outros materiais de liga são adicionados, dependendo do produto desejado. O processo Bessemer reduziu para cerca de meia hora o tempo necessário para produzir aço dessa qualidade, exigindo apenas o coque necessário para fundir o ferro-gusa inicialmente. A Fig 2 mostra o conversor Bessemer.
Fig 2 Conversor Bessemer
Bessemer licenciou a patente de seu processo para cinco mestres de ferro, por um total de GBP 27.000, mas as licenças não produziram a qualidade do aço que ele havia prometido e mais tarde ele os comprou de volta por GBP 32.500. Ele percebeu que o problema era devido a impurezas no ferro e concluiu que a solução estava em saber quando desligar o fluxo de ar em seu processo; de modo que as impurezas foram queimadas, mas apenas a quantidade certa de C permaneceu. No entanto, apesar de gastar dezenas de milhares de libras em experimentos, ele não conseguiu encontrar a resposta. A solução simples, mas elegante, foi descoberta pela primeira vez por Robert Forester Mushet, que realizou milhares de experimentos cientificamente válidos. Seu método era primeiro queimar, tanto quanto possível, todas as impurezas e C, depois reintroduzir C e Mn adicionando uma quantidade exata de spiegeleisen. Isso teve o efeito de melhorar a qualidade do produto acabado, aumentando sua maleabilidade e sua capacidade de suportar laminação e forjamento em altas temperaturas e tornando-o mais adequado para uma vasta gama de usos.
O processo Bessemer revolucionou a fabricação de aço ao diminuir seu custo, de GBP 40 por tonelada longa para GBP 6-7 por tonelada longa durante sua introdução, além de aumentar muito a escala e a velocidade de produção dessa matéria-prima vital. O processo também diminuiu os requisitos de mão de obra para a siderurgia.
Antes da introdução do processo Bessemer, o aço era muito caro para fazer pontes ou a estrutura de edifícios e, portanto, o ferro forjado foi usado durante a Revolução Industrial. Após a introdução do processo Bessemer, o aço e o ferro forjado passaram a ter preços semelhantes, e a maioria dos fabricantes se voltou para o aço. A disponibilidade de aço barato permitiu a construção de grandes pontes e permitiu a construção de ferrovias, arranha-céus e grandes navios. A introdução do processo de produção de aço em larga escala, aperfeiçoado pelo inglês Henry Bessemer, abriu caminho para a industrialização em massa observada nos séculos XIX-XX.
A produção comercial de aço usando esse método parou em Workington em 1974. Foi substituído por processos como o processo de oxigênio básico, que oferecia melhor controle da química final. O processo Bessemer foi tão rápido (10 a 20 minutos para um aquecimento) que permitiu pouco tempo para análise química ou ajuste dos elementos de liga no aço. Os conversores Bessemer não removeram P eficientemente do aço líquido; à medida que os minérios com baixo teor de P tornaram-se mais caros, os custos de conversão aumentaram. O processo permitia que apenas uma quantidade limitada de sucata fosse cobrada, aumentando ainda mais os custos. Especialmente quando a sucata era barata, o uso da tecnologia de forno elétrico a arco (EAF) competia favoravelmente com o processo Bessemer, resultando em sua obsolescência.
O processo foi rápido e barato, removendo C e Si do ferro em questão de minutos, mas sofreu por ser muito bem-sucedido. Muito C foi removido e muito O2 permaneceu no produto final. Bessemer finalmente teve que reembolsar seus investidores até encontrar um método para aumentar o conteúdo de C e remover o O2 indesejado.
Processo de forno aberto de fabricação de aço
O processo de forno aberto (OH) de fabricação de aço usa fornos de forno aberto. Devido às suas vantagens logo deslocou o processo Bessemer de fabricação de aço. Em 1908, a produção anual de aço por forno OH ultrapassou a produzida pelo processo Bessemer. A maioria dos fornos de OH foi fechada no início da década de 1990, principalmente por causa de seu funcionamento lento, sendo substituído pelo forno básico de oxigênio (BOF) ou EAF. Ainda existem algumas siderúrgicas no mundo que fabricam aço pelo processo OH. As principais vantagens do processo OH eram que ele não expunha o aço ao nitrogênio excessivo (o que faria com que o aço se tornasse quebradiço), era mais fácil de controlar e permitia a fusão e refino de grandes quantidades de sucata de ferro e aço.
O engenheiro alemão Carl Wilhelm Siemens desenvolveu o forno regenerativo da Siemens na década de 1850 e afirmou em 1857 estar recuperando calor suficiente para economizar 70% a 80% do combustível. Este forno operou em alta temperatura usando pré-aquecimento regenerativo de combustível e ar para combustão. No pré-aquecimento regenerativo, os gases de exaustão do forno são bombeados para uma câmara contendo tijolos, onde o calor é transferido dos gases para os tijolos. O fluxo do forno é então revertido para que o combustível e o ar passem pela câmara e sejam aquecidos pelos tijolos. Por meio desse método, um forno de OH pode atingir temperaturas altas o suficiente para derreter aço, mas a Siemens não o utilizou inicialmente para isso.
Em 1865, o engenheiro francês Pierre-Emile Martin obteve uma licença da Siemens e aplicou pela primeira vez seu forno regenerativo para a fabricação de aço. A característica mais atraente do forno regenerativo Siemens é a rápida produção de grandes quantidades de aço básico. O tamanho usual dos fornos OH varia de 50 toneladas a 500 toneladas.
O processo OH é um processo em lote e um lote é chamado de "calor". O forno é inspecionado primeiro quanto a possíveis danos. Uma vez pronto ou reparado, é carregado com sucata leve, como chapas metálicas, veículos triturados ou resíduos de metal. O forno é aquecido usando gás queimado. Uma vez derretido, é adicionado sucata pesada, como sucata de construção, construção ou usinagem de aço, juntamente com metal quente (HM) do alto-forno (BF). Uma vez que todo o aço tenha derretido, são adicionados agentes formadores de escória, como calcário. O O2 no óxido de ferro e outras impurezas descarbonizam o HM queimando o excesso de C, formando o aço. Para aumentar o teor de O2 do calor, minério de ferro é adicionado ao calor
O processo é muito mais lento que o processo do conversor Bessemer e, portanto, mais fácil de controlar e amostrar para avaliação de qualidade. A preparação de um calor geralmente leva cerca de 8 horas a 9 horas para ser concluída em aço. Como o processo é lento, não é necessário queimar todo o C como no processo Bessemer, mas o processo pode ser encerrado em um determinado ponto quando o conteúdo C desejado for alcançado.
O forno é rosqueado da mesma forma que um BF é rosqueado, ou seja, um furo é perfurado na lateral da fornalha e o aço bruto flui para fora. Uma vez que todo o aço tenha sido perfurado, a escória é retirada. O aço bruto pode ser fundido em lingotes; esse processo é chamado de fervura ou pode ser fundido em uma máquina de lingotamento contínuo.
Os regeneradores são a característica distintiva do forno e consistem em chaminés de tijolos refratários preenchidos com tijolos colocados na borda e dispostos de forma a ter um grande número de pequenas passagens entre eles. Os tijolos absorvem a maior parte do calor dos gases residuais de saída e o devolvem mais tarde aos gases frios de entrada para combustão. A Fig. 3 mostra uma seção transversal de um forno Siemens-Martin de 1895.
Fig 3 Seção transversal do forno Siemens-Martin
O processo Siemens-Martin complementou e não substituiu o processo Bessemer. É mais lento e, portanto, mais fácil de controlar. Também permitiu a fusão e o refino de grandes quantidades de sucata de aço, reduzindo ainda mais os custos de produção de aço e reciclando um material residual problemático. Sua pior desvantagem foi o fato de que derreter e refinar uma carga leva várias horas. Isso foi uma vantagem no início do século 20, pois deu aos químicos das fábricas tempo para analisar o aço e decidir quanto tempo mais para refiná-lo. Mas por volta de 1975, instrumentos eletrônicos como espectrofotômetros de absorção atômica tornaram a análise do aço muito mais fácil e rápida.
Aciaria em forno elétrico
Existem dois tipos de fornos usados para a fabricação de aço elétrico. São eles (i) forno elétrico a arco e (ii) forno de indução. O desenvolvimento histórico da siderurgia por esses dois fornos é apresentado a seguir.
A tecnologia de fabricação de aço EAF tem mais de cem anos. Embora De Laval tenha patenteado um forno elétrico para a fusão e refino de ferro em 1892 e Heroult tenha demonstrado a fusão a arco elétrico de ligas de ferro entre 1888 e 1892, o primeiro EAF industrial para fabricação de aço só entrou em operação em 1900. O desenvolvimento foi rápido e houve um aumento de dez vezes na produção de 1910 a 1920, com mais de 500.000 toneladas sendo produzidas em 1920, embora isso representasse apenas uma porcentagem muito pequena da produção global de aço da época.
Inicialmente, a siderurgia EAF foi desenvolvida para a produção de tipos especiais de aços usando formas sólidas de alimentação, como sucata e ligas de ferro. O material sólido foi primeiramente derretido por fusão direta a arco, refinado através da adição de fundentes apropriados e aproveitado para processamento posterior. Até cerca de trinta a trinta e cinco anos atrás, tempos de tap to tap de mais de três horas eram bastante comuns e o uso específico de energia era muitas vezes bem acima de 700 kWh/ton, quase o dobro do requisito termodinâmico. Durante grande parte do século XX, a fabricação de aço EAF foi vista como um processo caro e lento e adequado apenas para aços especiais e de valor agregado. Desde a década de 1960, a tecnologia passou por um rápido desenvolvimento e se tornou a segunda maior tecnologia de fabricação de aço, atrás da tecnologia básica de fabricação de aço com oxigênio.
Os EAFs são uma parte central da rota de produção que é uma alternativa à rota BF-BOF dominante. Uma vista em planta e em corte transversal de um EAF é mostrada na Fig. 4. Os EAFs são usados para produzir aços C e ligas de aço principalmente por meio da reciclagem de sucata ferrosa. Em um EAF, sucata e/ou unidades de ferro fabricadas (como DRI, ferro-gusa e carboneto de ferro, etc.) são derretidas e convertidas em aço de alta qualidade usando arcos elétricos de alta potência formados entre um cátodo e um (para CC) ou três (para AC) ânodos. A sucata é de longe o recurso mais importante, respondendo por cerca de 80% de toda a matéria-prima de metal EAF globalmente.
Fig 4 Vista da planta e da seção transversal do forno elétrico a arco
O aumento na produção e tecnologia de EAF em todo o mundo deve-se às seguintes razões.
- A descontinuação do processo OH como um processo de fabricação de aço competitivo.
- O desejo de se afastar dos grandes custos operacionais e de capital associados à siderurgia integrada em larga escala em direção a mini usinas siderúrgicas menores e menos intensivas em capital.
- Uma melhoria muito rápida na tecnologia elétrica, reduzindo os custos de equipamentos elétricos de grande escala e também permitindo um controle muito melhor de dispositivos elétricos.
- A pronta disponibilidade de sucata em muitos países combinada com uma forte pressão social para a reciclagem de metais.
- A crescente disponibilidade de fontes alternativas de ferro, especialmente dos países em desenvolvimento.
- Uso de HM e oxicombustíveis nos EAFs.
- Uma grande melhoria na operação, controle, eficiência e qualidade do produto da tecnologia de fabricação de aço baseada em EAF.
O forno de indução (IF) é usado para a fusão de metais ferrosos e não ferrosos. Produz o seu calor de forma limpa e sem combustão. Ele funciona no princípio da indução eletromagnética que foi descoberto por Michael Faraday.
Em 1870, De Ferranti iniciou experimentos na Europa em fornos de indução. A primeira FI para fusão de metais foi patenteada por Edward Allen Colby em 1900. O primeiro aço feito em uma FI nos Estados Unidos da América foi em 1907 em um forno Colby perto da Filadélfia. O primeiro forno trifásico foi construído na Alemanha em 1906 por Rochling-Rodenhauser. Embora os fornos de indução sejam utilizados há muito tempo, a produção de aço macio pela FI é um fenômeno relativamente recente.
O desenvolvimento de fontes de alimentação de indução de frequência média e flexíveis, com rastreamento de energia constante, resultou no uso generalizado dos métodos de fusão em lote. Estas unidades de potência incorporam retificadores controlados de silício para serviço pesado que são capazes de gerar tanto a frequência quanto a amperagem necessária para a fusão em lote e são capazes de atingir níveis de eficiência elétrica superiores a 97%, uma melhoria substancial sobre a eficiência de 85% típica das fontes de alimentação de indução de a década de 1970. Esses novos designs permitem a máxima utilização da potência do forno durante todo o ciclo de fusão com bom controle da agitação. Esquemas de um forno de indução sem núcleo são mostrados na Fig 5.
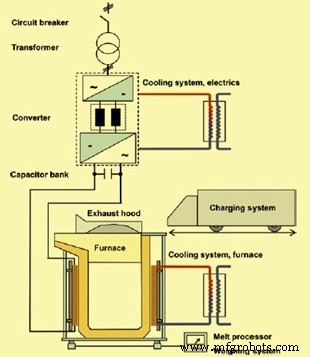
Fig 5 Esquema de um forno de indução sem núcleo
Existem vários tipos de IFs disponíveis, mas todos operam utilizando um forte campo magnético criado pela passagem de uma corrente elétrica através de uma bobina enrolada ao redor do forno. Essa corrente elétrica cria um campo eletromagnético que passa pelo material refratário e se acopla com a carga metálica condutora dentro do forno. The magnetic field in turn creates a voltage across, and subsequently an electric current through the metal to be melted. The electrical resistance of the metal produces heat, which in turn melts the metal and helps it to reach the set point temperature.
IFs are made in a wide range of sizes. Since there is no contact between the charge and the energy carrier, IF is normally suited for the melting of steel, cast iron and non-ferrous metals, so long as a suitable lining material can be found. Products made with the IF melting by the industry include mild steel ingots/billets for structural purposes, stainless steel ingots/billets for making utensils, wire rods and wires, low alloy steel castings for engineering applications, stainless steel castings for heat and corrosion resistant components, and alloy steels for forging industry and grinding media.
In India the use of IFs started in mid-sixties. Imported medium frequency induction furnaces were used from mid-seventies. Induction melting furnaces in India were first installed to make stainless steel from imported stainless steel scrap. During the years 1981-82 some entrepreneurs, who were having small size induction furnaces making stainless steel, experimented in making mild steel from steel melting scrap and they succeeded. Due to this success, sudden growth has taken place in the early eighties to mid-nineties. During this period indigenous manufacture of the induction furnaces also started. Steel making through induction furnace emerged during this period as one of the key driver for steel production growth in the country and is presently accounting for a share of more than 32 % of the total steel production. Today, India is the largest producer of IFs as well as the largest producer of steel with the IF technology. Steel making by IFs has grown not only in terms of overall capacity but also in terms of sizes of furnaces. Today, IFs up to 40 tons capacity are in operation in the country.
Basic oxygen steelmaking
Basic oxygen steelmaking (BOS) is the process of making steel by blowing pure O2 in a liquid metal bath contained in a vessel which is known as basic oxygen furnace (BOF), LD converter, or simply converter.
The concept of BOS goes back to 1856 when Henry Bessemer patented a steelmaking process involving O2 blowing for decarbonizing liquid iron (UK Patent number 2207). At that time there was no method available to supply the quantity of O2 needed for the process. The commercial quantities of O2 were not available at all or were too expensive, and hence the invention of Bessemer remained only on paper and remained unused. The steelmaking by blowing pure O2 became practicable in 1928, when the company Linde succeeded in developing a method (the Linde-Fränkl process) for supplying pure O2 in large quantities. Due to the success of the Linde- Fränkl process, O2 also became very much cheaper, so that both preconditions (availability of large quantities as well as availability of cheap O2) for the introduction of the BOS process were fulfilled.
In both Europe and the USA, experiments with O2 were carried out repeatedly. Among those who worked with high purity O2 was Otto Lellep, but his concept of ‘blowing O2 vertically onto a bath of liquid iron’ proved unsuccessful. As per Hubert Hauttmann, who took part in Lellep’s experiments between 1936 and 1939 at the Gutehoffnungshütte, where he was employed at that time, the intention was to convert liquid iron by blowing in pure O2 through a nozzle in the base of the converter. The steel produced in this way was of miserable quality.
During the World War II, Engineers by names C. V. Schwartz of Germany, John Miles of Belgium, and Durrer Switzerland of and Heinrich Heilbrugge of Germany proposed their versions of O2 blown steelmaking, but only Durrer and Hellbrügge brought it to a level of mass scale production.
Carl Valerian Schwarz submitted a patent application in 1939 for blowing O2 into the bath at supersonic speed. But this method too was ‘not yet capable of producing usable steel’. Although the later Linz- Donawitz (LD) process had similarities with Schwarz’s patent, its typical features were different (for example ‘central, vertical blowing’). It was only due to the outbreak of World War II that the technology described in Schwarz’s patent did not lead initially to any practical applications. It was also at the end of the 1930s that Robert Durrer of Switzerland began experiments of his own.
After the war, Heinrich Hellbrügge and Robert Durrer (Technical director of the Roll’schen Eisenwerke) began further experiments at Roll’schen Eisenwerke in the Swiss town of Gerlafingen. The photograph of the first top blown oxygen converter at Gerlafingen is shown at Fig 6.
Fig 6 First top blown oxygen converter at Gerlafingen and cross sectional views of oxygen converter
It was Durrer who laid down the basic theoretical principles and advised VÖEST to blow the O2 from above in a separate vessel, after a contact had been established between Gerlafingen and VÖEST for an industrial-scale technical cooperation. A series of experiments using a 2 ton experimental converter was started on 3rd June, 1949 on the premises of VÖEST. After the team in Linz had suffered several initial setbacks, a breakthrough was achieved as early as 25th June, 1949, when the O2 pressure was lowered and the tip of the blowing lance was moved farther away from the bath, so that the jet of O2 could not penetrate so far. With this breakthrough, steel was produced that could be rolled into sheet without problems. VÖEST’s experimental department examined this steel and was very positive in its observations. This was the moment when the LD converter steelmaking process was born. The experiments continued until several hundred heats of 2 ton had been produced, after which they were switched to a specially constructed 15 ton experimental converter erected in the open air. The first batch was produced on 2nd October, 1949. The new grade of steel was subjected to continuous metallurgical and other tests.
The key factor for this innovation was the movement of liquid bath. Until then it had been considered impossible to obtain sufficient bath movement without blowing the O2 in at a greater depth. But this movement was achieved in a highly satisfactory way by the formation of CO (carbon monoxide). The principle of ‘soft blowing’ also promoted FeO formation which in turn absorbed the oxidized impurities to form slag. This helped in the production of an excellent new grade of steel.
In addition to the Roll’schen Eisenwerke in Gerlafingen and VÖEST, Mannesmann AG in Duisburg-Huckingen and ÖAMG (i.e. Donawitz) also expressed interest in May 1949 in the O2 blowing process or at least O2 metallurgy in general. During the experiments in Linz and after a demonstration of the process, a precise division of labour was agreed on 17th June, 1949. VÖEST was to continue work with crude steel from Linz in a much larger refining vessel while Mannesmann was to experiment with O2 blowing of Thomas steel, Roll’schen Eisenwerke would investigate the use of O2 in the EAF and ÖAMG would conduct tests with O2 in a low-shaft pig iron furnace. The agreement obliged everyone concerned with this O2 metallurgy ‘not to issue any statement or pass on any information outside their own companies regarding details of O2 refining that came to their notice or conclusions they may have reached during the discussions in Linz on 17th June, 1949.
On the basis of the agreement, it soon became evident from experiments in Donawitz that the use of oxygen in shaft furnaces was valueless, whereupon the company began to explore different approaches. The process developed in Donawitz for the recovery of slag with high manganese content by blowing with O2 led to the awareness that only the use of a blowing process with pure O2 should be considered for the steel production expansion and rationalization plans in Donawitz. Following extensive investigation and successful development work on a 5 ton or 10 ton experimental setup, with oxygen supplied during the first tests from cylinders arranged in series, the company management decided to build a new steelworks, which would be ready for operation in two years. The Donawitz engineers initially named their process ‘SK’, from the German initials for ‘Oxygen Converter’. This term helped distinguish the activities of VÖEST and ÖAMG to a certain extent.
On 9
th
December, 1949 the then managing director of VOEST Heinrich Richter-Brohm took a decision not without risk for the building of the first LD steelworks. Not long after this and after clarification of questions concerning production methods for harder grades of steel, it was decided to build an LD plant in Donawitz as well. The first patents for the process were applied for in 1950.
In the annual research and quality assurance report of 1951, it had been stated that ‘during the review year extensive research work was devoted to the LD steel grades, and a publication was issued. This type of steel is expected to possess great potential in terms of quality, and in particular will permit steel with a high-quality surface combined with good cold formability to be produced. This is especially important for thin sheet metal production, where until now good cold formability was only possible if certain surface flaws were accepted (killed steel grades). But steel with higher yield strength can also be produced extremely advantageously by the O2 refining process.
By 1951 it became possible in Linz to refine hot metal with pure O2 in steelmaking into an innovative, operationally reliable process for the production of bulk quality steel in Linz. Announcement of the new process was made for the first time in December 1951, at the conference ‘Steel Refining with Pure Oxygen’ of Austrian Society for Metallurgy in Leoben. At the conference Robert Durrer stated that the two metallurgical plants (Linz and Donawitz) had developed the concept of blowing high purity O2 onto domestic HM into a viable industrial process, and congratulated them on this great success. With this announcement Austria became the first country to produce steel on an industrial scale from HM by blowing pure O2. The cross section LD converter before and during O2 blowing in the liquid metal bath is shown in Fig 6.
On 27th November, 1952 the first converter was commissioned at LD Steelworks 1 in Linz which was a milestone in the steel production by the O2 blowing principle. On 5th January, 1953 this LD Steelworks, the first in the world, was officially opened. By 17th June, 1953, LD Steelworks 1 in Linz had already produced 100,000 tons of LD steel, and by early December 1953 the 250,000 metric tons of steel was produced. The second LD Steelworks went into operation on May 22, 1953 at the Österreichisch-Alpine Montangesellschaft (ÖAMG) in Donawitz. The process, now developed to full operating maturity, exceeded all expectations in both the quality of the steel it produced and its economic viability. In 2015, 73.4 % of world steel was produced by BOF steel making.
Processo de manufatura